CNC ミリングのヒント:ダウンミリングとダウンミリングをいつ使用するかを学びます。バックミーリング
専門家は、機械加工される部品のサイズ、形状、機能、および材料に応じて、数え切れないほどの CNC フライス加工技術を使用して、CNC マシンを最大限に活用します。機械加工業界で採用されているこれらの技術の 1 つは、さまざまな切削アプローチ、つまりダウン フライス加工とバック フライス加工の利用です。特定の用途に適したタイプの切削アプローチを使用することは、加工を成功させる上で重要な役割を果たします。まず全体像を把握するために、それぞれの定義を以下に示します:
ダウンミリング
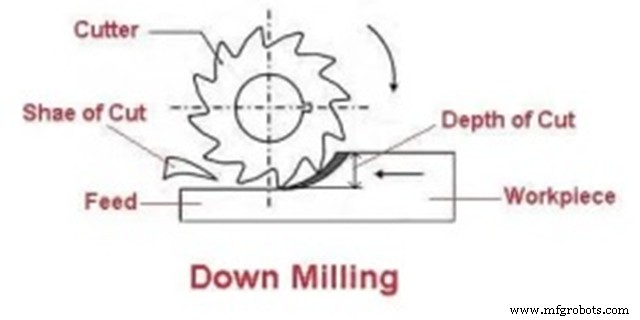
ダウンカットとも呼ばれます。このアプローチでは、切削工具の回転と同じ方向にワーク パーツを送り、下向きの切削力を発生させます。入口でのワーク パーツとのカッターの噛み合わせは、最大の材料を切削し、カッターが回転するにつれて徐々にゼロに到達します。送り方向と切削工具の回転方向を同じにすることで、カッターとワークピース間の抵抗が少なくなります。これは、機械加工プロセス中の発熱が少ないことを意味します。
バックミリング
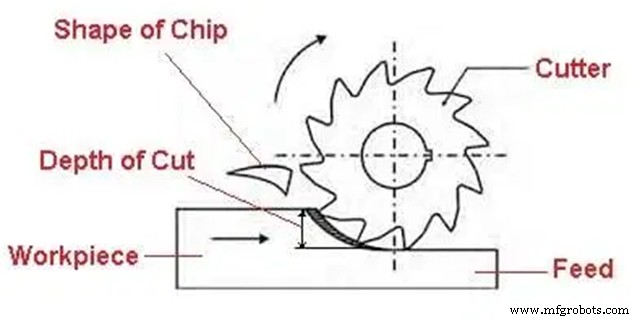
フライス加工とも呼ばれます。切削工具の回転方向とは逆方向にワークを送り、上向きの切削力を発生させる従来のフライス加工です。ここで、切削工具は、それが係合するときにワークピースに押し付けられ、比較的高い摩擦を生成し、次に、より高い量の熱を生成します.アップミリングでは、ダウンミリングとは対照的に、カッターは最小材料を差し引き始め、回転しながら徐々に最大材料を切削します。
WayKen はさまざまな を提供します フライス加工、旋盤加工、EDM、ワイヤー EDM、表面研削などの CNC 機械加工サービス。
アップミリングとダウンミリングの違いは何ですか?
これらの 2 つの方法は、餌の与え方が異なります。さらに説明するために、以下は、歯のかみ合い、切りくず排出、切削力、カッターの摩耗、および冷却の違いを比較したものです。
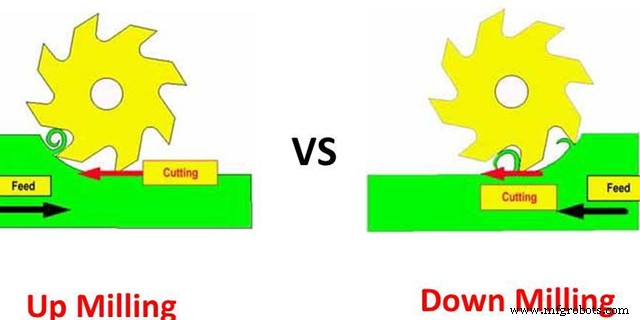
1.歯のかみ合い
バックミーリングでは切削方向が逆であるため、切りくずが刃にかかる負荷は最小限に抑えられます。これは、歯がワークピースと噛み合うにつれて、切りくずの幅がゼロから最大まで増加することを意味します。ダウンミリングでは、切削工具の刃が材料の切りくずを最大からゼロまで切削し始め、各刃がワークピースと噛み合います。
理想的には、優れた表面仕上げを確保するには、切削終了時の切りくず厚さを可能な限り薄くすることを考慮することが不可欠です。これが、荒加工にはバック フライス加工が好まれ、仕上げ加工にはダウン ミリングが好まれる理由です。
2.チップの排出
これら 2 つのフライス加工のアプローチについて学ばなければならないもう 1 つの違いは、得られる切りくずがワーク パーツから異なる方法で分離されることです。バックミリングプロセス中の切りくずは上向きに投げられますが、ダウンミリングプロセスでは、切りくずは下方向に分離します。これは、アップフライス加工では、切りくずが切削領域に蓄積する傾向があり、フライス加工中にチョークしたり、切削刃で運ばれたりして、表面仕上げが損なわれる可能性があることを意味します。一方、ダウンミーリングでは、切りくずは切削をあまり妨げずに簡単にワークピースから離れます。そのため、切りくず処理にはダウンミリングが適していると考えられています。
3.切削抵抗
両方のアプローチにおける切削工具の入口と出口に関連して、両方のフライス加工方法の切削力も異なります。バックミーリングの切削抵抗はゼロから最大まで、ダウンミーリングでは最大からゼロまでです。ダウン フライス加工で材料を切断する方法により、CNC フライス加工では比較的低い電力消費を実現できます。
これに加えて、バックフライス切削力は反対側に向けられ、ワークピースをクランプから持ち上げる傾向があります。一方、ダウンミーリングでは切削力が下向きになるため、ワークのクランプが確実になり、ワークの抜けが少なくなります。
4.カッターの摩耗
バックミーリングは反対方向に切削するため、摩擦が大きくなり、カッターの刃先が摩耗する可能性が高くなります。ダウンミリングでは、送りと同じ方向に材料を切削するため、工具の摩耗が比較的最小限に抑えられます。
バックミリングとアップミリングはいつ使用するのですか?
CNC フライス加工では、特定の状況と用途において、ダウン ミーリングとバック ミーリングの両方が利点を提供します。以下に、それらの利点と、どのような状況で最もよく使用されるかについて説明します:
バックミリングの利点
バックラッシュまたはアップミリングは、マシンがまだバックラッシュエリミネータを備えていなかったときの伝統的なバックミリング方法です。このアプローチの相反する力は、機械のバックラッシュが引き起こす可能性のあるエラーを取り除きます。
このフライス加工のアプローチは、強靭で脆い材料 (硬化、鋳造、鍛造など) のワーク パーツを荒削りするという過酷な要求に対処する場合に適しています。粗加工の用途に加えて、機械工は、薄肉で拡張された表面を切削する場合、切削アプローチをバック フライス加工に設定する傾向があります。この理由は、切断中の反対の力によりたわみが最小限に抑えられるためです。
ダウンミリングの利点
時が経つにつれて、CNC フライス盤の背後にある技術が進化し、バックラッシュ エリミネータがメカニズムに組み込まれ、機械工がプロセスでダウン フライス加工を使用できるようになりました。
ダウン フライス加工は、一般的に次の理由により、通常の状況で部品を加工する際に最も効率的な方法と考えられています。
● 刃先からの負荷が少ないため、工具の摩耗が少なく、工具寿命が長くなります。
●切削方式(厚→薄)で滑らかな表面に仕上がります。
●バックミーリングより発熱量が少ない。
● 重要度の低い作業保持治具が必要です。
● 切りくず排出性が向上します。
これらすべての利点があるにもかかわらず、ダウンミリングにはまだ注意すべき点があります。これらは、機械のバックラッシュと、カッターまたはワーク パーツの両方のたわみです。
結論:
ダウンミリングとバックミリングは、CNC フライス加工サービスを提供する際に使用される異なるアプローチであり、どちらも特定の状況またはアプリケーションで利点を提供します。これら 2 つの基本的な違いは、切断方向と送り方向です。ダウンミリングでは、材料は切削工具の回転と同じ方向に供給されます。一方、バックミーリングでは、材料は切削工具の回転とは逆方向に送られます。
上記の議論から、次の結論を得ることができます:
● 滑らかな表面仕上げが必要な場合はダウン ミリングが、荒加工が目的の場合はバック ミリングが推奨されるプロセスです。
● ダウンミーリングは、発熱が良く、負荷が少なく、切りくず排出が良好です。
● 機械のバックラッシュとたわみを最小限に抑えるには、バック フライス加工が適しています。
CNCマシン