放電加工:構造、用途、長所と短所
放電加工は、スパーク加工とも呼ばれ、CNC 旋削やフライス加工などの従来の加工プロセスとは大きく異なるプロセスです。後者のプロセスでは、機械加工されるワーク パーツから材料を除去できるように、鋭利な切削工具が必要です。旋削やフライス加工とは異なり、EDM プロセスは一連の放電による金属の浸食を利用します。
以下を読んで、EDM 製造に関連する基本的な概念について詳しく学んでください。
EDM の仕組み
放電加工では、放電加工機で電気火花を使用してワークピースの一部を侵食します。これらの「電気火花」は、実際には、互いに近接した 2 つの通電導体間に形成される電気アークです。電気アークは、導電性材料を溶かして蒸発させる極度の熱を発生させる原因となります。 EDM プロセスのシステム内では、ワークピースはプラス端子またはアノードに接続され、材料を侵食するツールはマイナス端子またはカソードに接続されます。
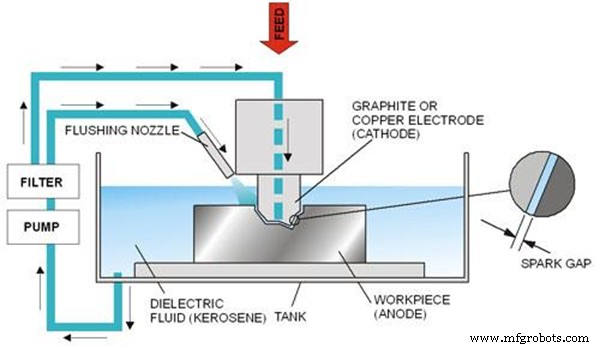
EDM システムの基本構成
動作原理をさらに詳しく説明するために、以下に放電加工 (EDM) システムの基本構造の内訳を示します。
<強い>1. DC パルス発生器
このコンポーネントは、AC 電源を、侵食ツールとワーク パーツの間に火花を発生させるのに十分な高さの脈動 DC 電源に変換します。
<強い>2.電極ツール
システムのこの部分は、刃物台に取り付けられた状態で電源のカソードに接続されます。ツールのプロファイルは、ワーク パーツに残されたプロファイルとまったく同じになります。プロセス中、アーク ギャップと呼ばれる非常に小さなギャップ (製造技術者が特定) が、電極ツールとワーク パーツの間に維持されます。電極に使用される最も一般的な材料は、銅、タングステン合金、黒鉛、鋼、および鋳鉄です。
<強い>3.サーボモーター機構
このメカニズムは、EDM マシンの工具の送りと動きを制御します。前述のアーク ギャップは、プログラムされたサーボ モーター機構によって厳密に制御されます。
<強い>4.スパークジェネレーター
このコンポーネントは、スパークの生成と放電の維持に必要な適切な量の電圧を供給します。 1 秒間に 10 万個の火花を生成することで、ワーク パーツから材料を大幅に削減することができます。
<強い>5.誘電流体
電極工具と加工部品の両方を誘電性流体に浸し、その間、工具と加工部品の間の隙間に流体を供給する。また、加工液は一定圧力で循環するように設定し、被加工物から侵食された金属部品を吹き飛ばす必要があります。液圧が高すぎると、金属チップがすぐに除去され、切削動作が遅くなる可能性があります。液圧が弱すぎると、浸食プロセス中に排気されていない切りくずが原因で、システム内で短絡が発生する可能性があります。
このプロセスで使用される最も一般的な誘電性流体は、脱イオン水、グリコール、およびシリコン オイルです。
<強い>6.ワーク
作業部分が陽極に接続されているため、これで放電加工機のエコシステムが完成します。プロセスを可能にするには、ワーク パーツが良好な導電体である必要があります。
EDM プロセスの種類
放電加工は、使用する工具の形状やアプローチによって、いくつかのタイプに分類されます。業界で一般的な 3 種類の放電には、ワイヤ EDM、シンカー EDM、および穴あけ EDM が含まれます。
1.ワイヤー放電加工機
名前が示すように、EDM ワイヤ切断では、ダイヤモンド ガイドで保持された非常に細いワイヤ (通常は 0.004 インチから 0.0006 インチの薄さの銅または真鍮合金) を使用して、3D ワークピースの 2 次元形状を正確に切断します。パスは、複雑な形状を簡単に切断できるようにする CNC プログラムによって制御されます。切断は、帯鋸やチーズカッターの切断送りにたとえることができます。このプロセスは通常、金属の押出ダイ、パンチ、およびプレートの切断に使用されます。
2.シンカーEDM
ラム EDM とも呼ばれるこのタイプの EDM プロセスでは、グラファイトまたは銅の電極を逆の形状に形成して、ワーク パーツに空洞を切削します。使用するツールは、ワークピースに残す目的の形状の逆の形に加工されます。
シンカー EDM は、複雑なキャビティ形状が必要な鋳造や射出成形に使用される金型の加工に最適です。
3.穴あけEDM
このタイプの EDM プロセスでは、電極ツールを使用して、従来のドリルでは不可能な非常に薄くて深い穴を開けます。このプロセスのツールは、誘電性液体が穴から直接供給されるように設計されているため、中空電極になります。穴あけ放電加工は従来の機械加工ではないため、加工品にバリが発生しません。穴あけ EDM は、さまざまなタービン ブレード、金型、金型に小さな逃げ穴を加工するために使用されます。
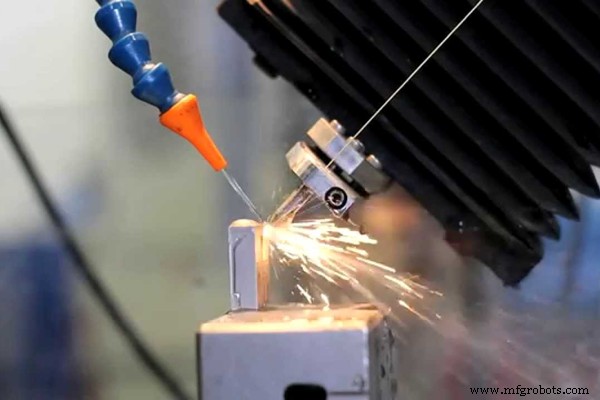
EDM 加工の用途は?
EDM 加工は、複雑な形状や形状を作成する能力が非常に高いです。
そのため、一般的に放電加工は、従来の加工では不可能な高精度の用途に使用されます。以下は、EDM 加工の最も一般的な用途です:
小さな穴あけ
多くの製造業者は、非常に小さな穴をあける際に EDM 加工を使用することを選択しています。 EDM 加工穴は構造が非常に小さい場合があり、タービン ブレードのエッジ、燃料システム コンポーネントの微細なオリフィスなどに見られます。
金型と金型の製作
EDM 加工は、金型の製造において、従来の機械加工に加えて、補完的なプロセスとしてよく使用されます。前述のように、ワイヤーカットタイプは金型のブランクを形成するために一般的に使用され、シンカータイプはキャビティの複雑な形状を形成するために使用される場合があり、ホールドリルタイプは圧力解放穴を作成するために使用される場合があります。
構成要素の分解
EDM マシンは、通常の方法では除去できない加工部品内の固着した金属を除去するためにも使用されます。付着したコンポーネントを分解することは、材料を破壊または除去することを意味します。状況によっては、ねじ穴のせん断ボルト、機械加工部品の工具の吸引、または非常に貴重な部品にピンが刺さっているなどがあります。コンポーネントを分解することで、再利用する部品に損傷を与えることなく、付着した金属を取り除くことができます.
医療用部品
EDM 機械加工製品は、製造時にバリが形成されないため、さまざまな医療用インプラント コンポーネントの作成に最適です。
航空宇宙部品
航空宇宙部品には、一部の標準的な切削工具では作成できない多くのフィーチャがあり、そこで EDM 機械加工の出番です。EDM 機械加工は、タービン ローター ディスク、細いスロット、鋭く四角い形状など、困難なフィーチャを作成することができます。穴、および非常に厳しい深い穴の要件。
EDM が好まれる理由
複雑なプロファイルの加工に高い能力
EDM の切断の自由度は、従来の機械加工操作よりも制約が少なくなります。この工程では、エンドミルやドリルでは不可能に近いさまざまな形状を簡単に切削できます。これらの機能には、複雑なポケット、細かい深い穴、薄い壁、およびその他の不規則な形状のジオメトリが含まれます。
高精度
EDM 技術で機械加工された部品は、金属製造業界で使用される最小公差まで正確にすることができます。これが可能なのは、EDM 加工のエコシステムが加工部品に高い応力を導入せず、積極的な振動がないためです。これとは別に、精度と正確性を高めるためにスキミング プロセスが行われることもあります。
バリのない表面仕上げ
EDM 加工で製造された加工部品は、加工部品からの侵食された金属がほとんど崩壊して微粒子になり、その後洗い流されるというプロセスの性質により、バリのない状態になります。最も重要なことは、EDM 切断にはエンドミル、のこぎり、ドリルなどの鋭利な切断工具が含まれていないため、このプロセスで加工部品にバリが発生しない理由です。
硬い金属を切断できます
EDM 加工は、導電性がある限り、低力で最小限の労力で硬質金属を切断することができます。切断される材料の硬度は、プロセス全体に影響しません。
低ストレス
EDM プロセスで使用される工具は、切削工具が切削面に接触する他の機械加工方法とは異なり、工作物に触れません。これは、ワークピースに導入される応力が最小限であることを説明しています。
高度にスケーラブルな製造
EDM 加工プロセスは、生産規模に関しては非常に汎用性が高く、少量から大量生産に適しています。これらのプロセスは再現性が高く、一貫した品質で複数の部品を製造できます。
Lorem ipsum dolor sit amet, consectetur adipiscing elit. Ut elit tellus, luctus nec ullamcorper mattis, pulvinar dapibus leo.
EDM プロセスの制限事項は何ですか?
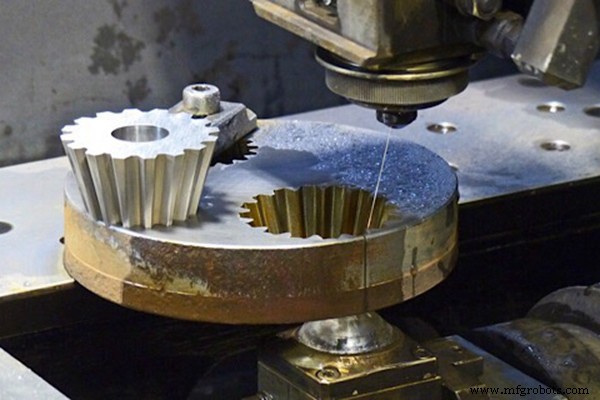
導電性材料にのみ適用
加工部品の材料を侵食する熱は、放電の導入に依存しているため、EDM 加工は、複合材、プラスチック、その他の誘電体材料などの非導電性材料には適合しません。
材料除去率が低い
前述のように、放電加工は徐々に材料を侵食します。そのため、フライス加工や旋削加工などの従来の機械加工プロセスよりも材料除去速度が大幅に遅くなります。
高価な制作費
EDM を使用して部品を製造するためのコストには、高電力消費、過度の工具摩耗、長い加工時間など、さまざまな要因が関係しています。
まとめ
放電加工は、さまざまな従来の CNC 加工プロセスに追加するのに非常に便利です。フライス加工や旋削加工では実現が難しい特殊な機能を生み出すことができるという点で、その強みを発揮します。これに加えて、EDM プロセスは、非常に硬い導電性金属を切断する場合でも卓越した精度を発揮し、さらに加工中の歪みが少なくなります。
CNCマシン