表面仕上げを改善するための 5 つの研削考慮事項
精密な CNC 生産研削は、部品が厳しい幾何公差と高品質の表面仕上げを必要とする場合に威力を発揮します。通常、32 マイクロインチ Ra から 4.0 マイクロインチ Ra までの範囲の表面仕上げ、またはそれ以上の値を達成する必要があります。それに比べて、従来のフライス加工または旋削加工では、約 125 マイクロインチから 32 マイクロインチ Ra の仕上げが可能です。
目標が現在の表面仕上げを 20 マイクロインチ Ra から 17 マイクロインチ Ra に改善することである場合は、砥石速度を上げたり、送り速度を少し下げたりするだけで十分かもしれません。ただし、より細かい表面仕上げが必要な場合は、これらの 5 つの要因に対処する必要があります。
1) 研削操作パラメータ
研削パラメータを調整することは、部品の表面仕上げを改善するための最も簡単で最速のソリューションです。これを成功させるための重要なパラメーターと推奨されるアクションを次に示します。
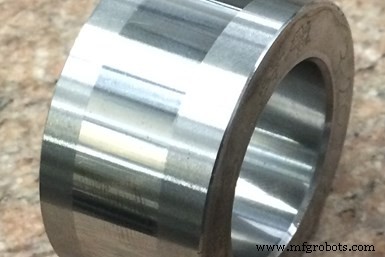
このコンポーネントは、3.0 マイクロインチ Ra の表面仕上げに研磨されています。この仕上げは、超砥粒ホイールを使用し、この記事に記載されているすべての推奨事項に対処するなど、プロセスを最適化することによって達成されました。写真クレジット:ノートン |サンゴバンの研磨剤。
クリープフィード/平面研削:
- 車輪の速度を上げる。 これは良い出発点です。ただし、ホイールが新しい速度で動作する定格であることを確認してください。最高動作速度 (MOS) はホイールの側面に記載されています。
- 送り速度を下げる
- 切り込みを減らす
- スパーク アウト パスの数を増やします。
外径(OD)/内径(ID)研削:
- 車輪の速度を上げる。前述のように、ホイールは新しい速度で動作するように定格されている必要があります。最大動作速度は、ホイールの側面に記載されています。
- 1 回転あたりの切り込み深さを減らします。
- 作業速度 (rpm) を下げる:1 回転あたりの深さを維持するために、送り速度を調整する必要がある場合があります。
- ドエル/スパークアウト時間を増やす
- オシレーションを使用します (プランジ ID 研削の一般的な方法)。
今日の多くの研削盤には可変速度コントローラーが搭載されているため、CNC プログラムを編集するか、スピンドル速度コントローラーを調整するだけで砥石の速度を変更できます。他の機械では、プーリーとベルトを手動で交換する必要がある場合があります。
送り速度を下げることは、CNC プログラムを編集するか、送り速度制御を調整することによっても実行できます。ただし、このアプローチではサイクル タイムが長くなる可能性があり、特にサイクル タイムが重要な生産オペレーションでは、必ずしも適切なオプションとは限りません。サイクル タイムが重要でないアプリケーションでは、送り速度を下げることが、ワークピースの表面仕上げを改善するための良いオプションになる場合があります。
砥石速度を上げて切込みと送り速度を下げると、砥石が鈍くなることがあります。これにより、ワークピースへの熱損傷の可能性が高まり、研削力が増加する可能性があります。したがって、これらのパラメーターを調整するときは、プロセスに他の問題を持ち込まないように注意する必要があります。
2) 砥石ドレッシング
従来の砥石と超砥粒砥石の両方のドレッシング条件を操作して、表面仕上げを改善することができます。これは
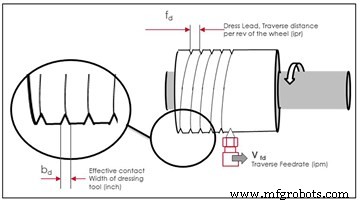
ドレス リードは車輪が移動する距離です
これは通常、ドレス トラバース速度を遅くするか、ドレス中のパスあたりの深さを減らすことによって達成されます。ドレッシングの深さを減らすと、ドレッシング動作の積極性が低下し、砥石面がより滑らかになり、通常はワークピースの表面仕上げが向上します。ドレストラバース速度を下げると、ドレスリード(砥石が 1 回転する間に移動する距離)が減少します。ドレスリードは、ドレスツールが砥石面を横切るあらゆるドレスプロセスに適用できます。ただし、ドレス リードは、プランジ ドレス作業には適用されません。リードを調整することは、既存のプロセスの表面仕上げを改善する良い方法です。
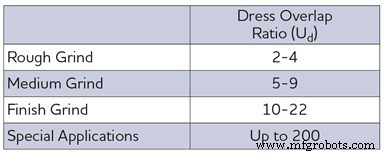
表 1. 考慮すべきガイドラインは次のとおりです。オーバーラップ率を選択するとき。
新規工程の開発時やドレスツールの種類変更時には、ドレスオーバーラップ率(ドレッサー幅を考慮したもの)を算出するのがベストです。オーバーラップ率は、ドレッサーが砥石を横切って移動する際に、砥石面の任意の 1 点がドレッサー面に接触する回数です。
砥石面の表面状態はドレスオーバーラップ率で決まります。これにより、ワークピースの表面粗さが決まります。オーバーラップ率が高くなると、ドレッサーが砥石に同じ砥粒を何度も当てることになり、砥石表面に細かい凹凸ができます。これにより、砥石面が鈍く閉じた状態になり、ワークピースの表面仕上げが細かくなります。
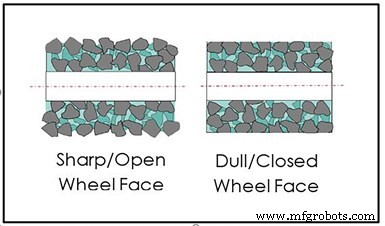
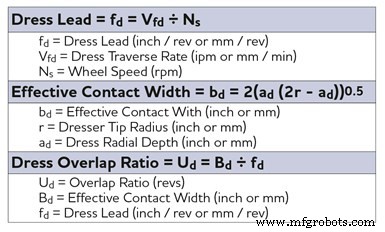
表 2. リード率とオーバーラップ率を決定する式は次のとおりです。
ただし、非常に細かいドレッシングを行った後は、砥石面が閉じすぎないように注意する必要があります。砥石の面が閉じていると、砥石の表面がくすんでいるため、研削力が高くなり、ワークピースの熱損傷を引き起こす可能性があります。表 2 は、リード率とオーバーラップ率を決定するための式を示しています。
3) 砥石組成:粒度
砥石の粒度は、表面仕上げに直接影響します。粒度が大きいほど仕上がりが粗くなります。ワークピースの仕上げ要件に基づいて、正しいグリットサイズを選択することが重要です。表 3 は、さまざまな仕上げ要件に対するグリットの種類、サイズ、および推奨事項を示しています。
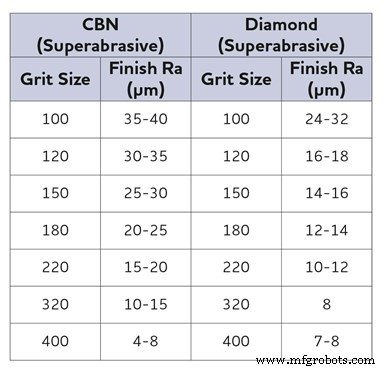
表 3.砥石は、表面仕上げを改善する 1 つの方法です。この表は、CBN およびダイヤモンド砥石の目的の仕上げに関連して、どの粒度を使用するかを示しています。
グリットサイズを変更する前に、あまり積極的でないパラメーターを使用して砥石をドレッシングすることをお勧めします。グリットサイズを小さくすると、送り速度を下げる必要があり、その結果、サイクル時間が長くなる可能性があります。グリットサイズが小さいと、グリットサイズが粗いほど高い除去速度で材料を除去できません。また、より小さいグリットサイズを使用すると、ワークピースに熱損傷が誘発される可能性があります。
従来の砥石砥石の構成には、砥粒の種類とサイズ、砥石の構造(粒子間隔)、グレード(ボンド硬度)、およびボンドの種類が含まれます。超砥粒砥石の組成には、砥粒の種類とサイズ、砥粒の濃度、ボンドのグレードと種類が含まれます。従来の研磨剤には、酸化アルミニウム、炭化ケイ素、セラミック研磨剤が含まれます。超砥粒には、ダイヤモンドと立方晶窒化ホウ素 (cBN) が含まれます。
より小さいグリット サイズの砥石を注文する前に、砥石メーカー/販売業者に連絡して、用途に最適な砥石構成を見つけることをお勧めします。
4) クーラントの配送
クーラントの適用が不十分な場合、研削チップが研削ゾーンに再導入される可能性があります。切りくずはワークピースにスクラッチを引き起こす可能性があり、これは ID 研削でよく発生します。
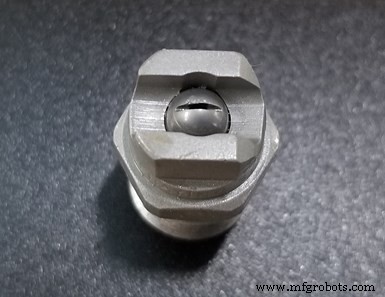
スクラバー ノズルは通常高圧 (500 -1,000 psi)、ホイール構造から切りくずを除去するために研削ゾーンの後にターゲットを絞った低流量ノズル。
クーラント ノズルが適切に研削ゾーンに向けられており、十分なクーラント フローと圧力があり、切りくずをその領域から洗い流します。研削ゾーン全体を正確にターゲットにすることは、部品全体で一貫した表面仕上げを達成するための鍵となります。一部の高除去率プロセスでは、部品の焼損を避けるために、砥石速度に合わせてクーラント圧を調整する必要がある場合があります。これは、研削ゾーンから切りくずを取り除くのにも役立ちます。
場合によっては、切りくずが砥石に付着することもあります。これは、より積極的な研削や、砥石にくっつきやすい特定の金属を研削するときに発生する可能性があります。これらのアプリケーションでは、スクラバー ノズルを実装する必要がある場合があります。スクラバー ノズルは通常、高圧 (500 ~ 1,000 psi) の低流量装置で、研削ゾーンの後にホイール構造から切りくずを除去することを目的としています。
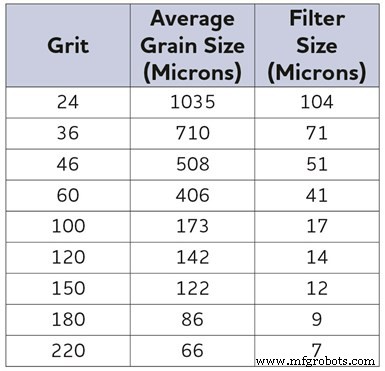
表 4. カーバイド研削の一般的な経験則は、ホイールのグリット サイズの 10% を超える粒子を捕捉するフィルターを使用することです。
ただし、部品のボア内のスペースが限られているため、スクラバー ノズルが ID 研削の答えになる可能性は低いです。このような場合は、フラッドクーラントを使用する必要があります。ただし、OD およびクリープフィード/表面研削の場合、多くの場合、部品や治具に干渉することなくスクラバー ノズルを実装できます。
クーラントのろ過が不十分だと、表面仕上げに悪影響を及ぼしたり、部品の表面に傷がついたりする可能性もあります。粒子がろ過されない場合、粒子はクーラントと一緒に粉砕ゾーンに戻されます。傷や仕上がり不良の原因としてフィルタリングが疑われる場合は、より小さなミクロン フィルターを使用する必要がある場合があります。たとえば、カーバイド研削の一般的な経験則は、少なくとも砥石のグリット サイズの 10% を超える粒子をろ過するフィルターを使用することです (表 4 を参照)。
クーラントの種類も表面仕上げに影響を与える可能性があります。これは、通常、潤滑性がホイールの摩耗に影響を与えるためです。ストレート オイル クーラントは通常、ホイールの摩耗を抑え、より一貫した表面仕上げを促進します。
5) 機械の状態
研削盤関連の要因は、ワークピースの表面仕上げに影響を与える可能性があります。これらには以下が含まれます:
ホイール/ハブ アセンブリのバランス: 砥石アセンブリのバランスが許容レベルに達していないと、びびりや粗い表面仕上げが発生する可能性があります。バランシングは、静的バランサー、動的/手動バランサー、またはマシンに取り付けられたオートバランサーなどの機器を使用して実行できます。必要なワークの精度と表面仕上げによって、使用する装置のタイプが決まります。
研削スピンドルに直接取り付けられた自動バランサ システムは、最適なバランス調整オプションです。このシステムは、ハブ内のウェイトを自動的に動かして、ホイールとハブの不均衡を相殺します。オートバランサーは、クリープフィードや OD 型などの大型の機械に限定されているため、小径ホイールには実用的ではありません。
バランシングの次善の方法は、すべてのタイプの機械で使用できる動的/手動タイプのバランシング システムです。ホイール/ハブ アセンブリのバランスをマシン上で直接調整しますが、バランス ウェイトを手動で動かす必要があります。
最後に、マシンから離れて実行されるスタティック バランスには、達成できるバランス レベルに関して制限があります。ただし、バランスを取らないよりはましで、アプリケーションによっては問題なく動作します。
とはいえ、すべてのホイールにバランスが必要なわけではありません。質量の小さい小さなホイールの中には、問題のある不均衡を引き起こす重量がないものがあります。したがって、これらの小さなホイールが非常に高速で動作している場合や、機械/システム (クイル) が硬くない場合を除き、バランスを取る必要はありません。また、精度の低い用途や荒削り用途に使用される砥石は、バランス調整が不要な場合があります。
機械の剛性: 機械の剛性が低いと、加工品の品質が低下する可能性があります。時間の経過とともに、スピンドル ベアリングが摩耗して緩むことがあります。機械がクラッシュした場合、ベアリングも損傷する可能性があります。可能であれば、振動分析装置を使用して、スピンドル ベアリングを定期的または継続的にチェックする必要があります。この装置は、ワークピースの品質低下につながるスピンドル ベアリングの問題を予測するのに役立つ優れたツールです。治具やクランプ方法が不十分だと、振動やたわみが発生し、最終的には表面仕上げが損なわれる可能性があります。
ドレッシング システム: ホイールを正しくドレッシングすることは、良好な表面仕上げを達成するために重要であるため、ドレッシング システムを良好な状態にする必要があります。固定ツールが損傷または摩耗している場合は、交換する必要があります。研削スピンドルなどの回転工具は、過度の振動、振れ、動きがないかチェックする必要があります。
工作機械のメンテナンス: 圧縮空気を監視しながら、定期的な機械注油について工作機械サプライヤーの指示に従うことが重要です
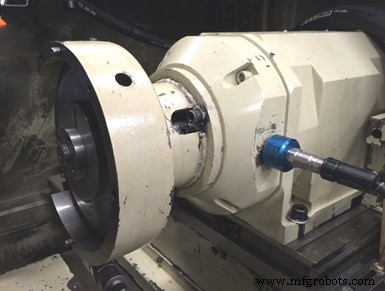
加速度計は研削スピンドルに取り付けられています。振動レベルをチェックします。
品質、フィルター交換頻度など。ホイールハブとアーバー、固定具、振れ止め、テールストックセンターなどに損傷がないか検査する必要があります。これらの機械部品の検査は、ショップの日常の予防保守ルーチンの一部である必要があります。
定期的なメンテナンスに加えて、現在、多くの企業がコンディション ベース モニタリング (CBM) などのメンテナンス プログラムを実施しています。CBM では、加速度計、温度計、圧力計などのセンサーによって機械が監視されます。この予知保全では、センサーから収集されたデータを使用して傾向を確立し、故障を予測して、ベアリングなどのコンポーネントをいつ交換する必要があるかを判断します。
ノートン|サンゴバン研磨剤 | nortonabrasives.com/en-us
著者について
John Hagan はシニア アプリケーション エンジニア、Mark Martin は Norton|Saint-Gobain Abrasives のアプリケーション エンジニアです。
産業機器