OOA注入ウィングボックスを前進させる
航空宇宙産業はCOVID-19のパンデミックからの回復を期待しているため、これまでの高率生産の推進は、地球と人々に対する環境への脅威を減らすための緊急の推進力に軸足を移しました。この取り組みには、温室効果ガス(GHG)排出量、エネルギーと水の使用量の制限、およびリサイクルできない廃棄物の作成が含まれます。これらのイニシアチブはCOVID以前に進行中でしたが、複合構造を製造するためのはるかに低いコストの必要性と同様に、現在それらの重点が高まっています。 Clean Sky 2汎ヨーロッパ航空プログラムは、これらすべての分野の研究開発に資金を提供し、さまざまな繊維強化複合技術を大幅に進歩させました。
Clean Sky 2の7回目の提案募集(CFP07、2017年10月)には、自動ファイバーを使用して高度に統合されたウィングボックスフライングデモンストレーターを製造するための革新的で柔軟なパイロットプラントに対するエアバスディフェンスアンドスペース(エアバスDS、カディス、スペイン)の要求が含まれています。配置(AFP)および液体樹脂注入。
2013年にGKNAerospace(Redditch、UK)によって発表されたOOA「ブレンデッド」ウィングボックスを含む、他の樹脂注入および/または脱オートクレーブ(OOA)ウィングボックスのデモンストレーターがありました。北アイルランドのSpiritAeroSystemsBelfastがオートクレーブ内の樹脂移送注入を使用して製造したエアバスA220翼。 MS-21 用にAeroComposit(モスクワ、ロシア)が製造したOOAウィング ジェット旅客機。ただし、これらはすべて、機械的な留め具を使用して、個別の複合ストリンガーで補強されたスキンとスパーを組み立てています(「最小限の留め具でOOAウィングへの道」を参照)。
クリーンスカイ2のエアバスDSが要求したウィングボックスは、補強された下部スキンを補強された前方および後方スパーと統合することで一歩前進し、 なしでより完全なモジュールを可能にすることでした。 残りの翼コンポーネントとの組み立てのために転送されるファスナー。
このウィングボックスは、幅の狭い(幅0.25インチまたは0.5インチ)ドライカーボンファイバーテープと高温(180°CT g )も使用します。 )硬化樹脂ですが、省エネで低コストの加熱システムとセンサーベースのデジタル制御およびシミュレーションにより、処理を予測および管理し、開発中の試行錯誤のループを短縮し、製造担当者の迅速なトレーニングを可能にします。このデジタル化は、ユーザーマニュアルとメンテナンスマニュアル、プロセスシーケンスの定義、ペーパーレスプロセスとパーツの追跡、およびパーツへのCATIAモデルの投影を提供する、拡張現実モバイルアプリケーション(アプリ)を含むように進化し、補強材プリフォーム、ツーリングインサートの正確な配置を支援します。および炭素繊維強化ポリマー(CFRP)コールプレート。
おそらく最も要求の厳しいこのプロジェクトでは、すべての工具および製造装置が持ち運び可能で柔軟性があり、どの製造現場でも簡単に展開でき、より高度な工具、加熱、複合材料4.0プロセス制御技術が利用可能になったときに他の部品設計やアップグレードに適応できる必要がありました。
エアバスDSの複合開発エンジニアリング-テクノロジーおよびプロセスの責任者であるトピックマネージャーのルイス・ルビオは、次のように説明しています。環境フットプリントは、同様の設計公差と品質レベルを達成できます。」
MTorres(Torres de Elorz、スペイン)は、パートナーなしで申請しました。 「社内には、AFP、注入、ドライテープ材料、自動化などのすべての機能がありました」と、MTorresの複合材料技術のシニアマネージャーであるSebastianDiaz氏は説明します。同社は、助成金契約No820845に基づく欧州連合のHorizon2020プログラムを通じて資金提供された、革新的な輸液機体製造システム(IIAMS)プロジェクトを受賞し、2018年10月に作業を開始しました。
外翼ボックスのデモンストレーター
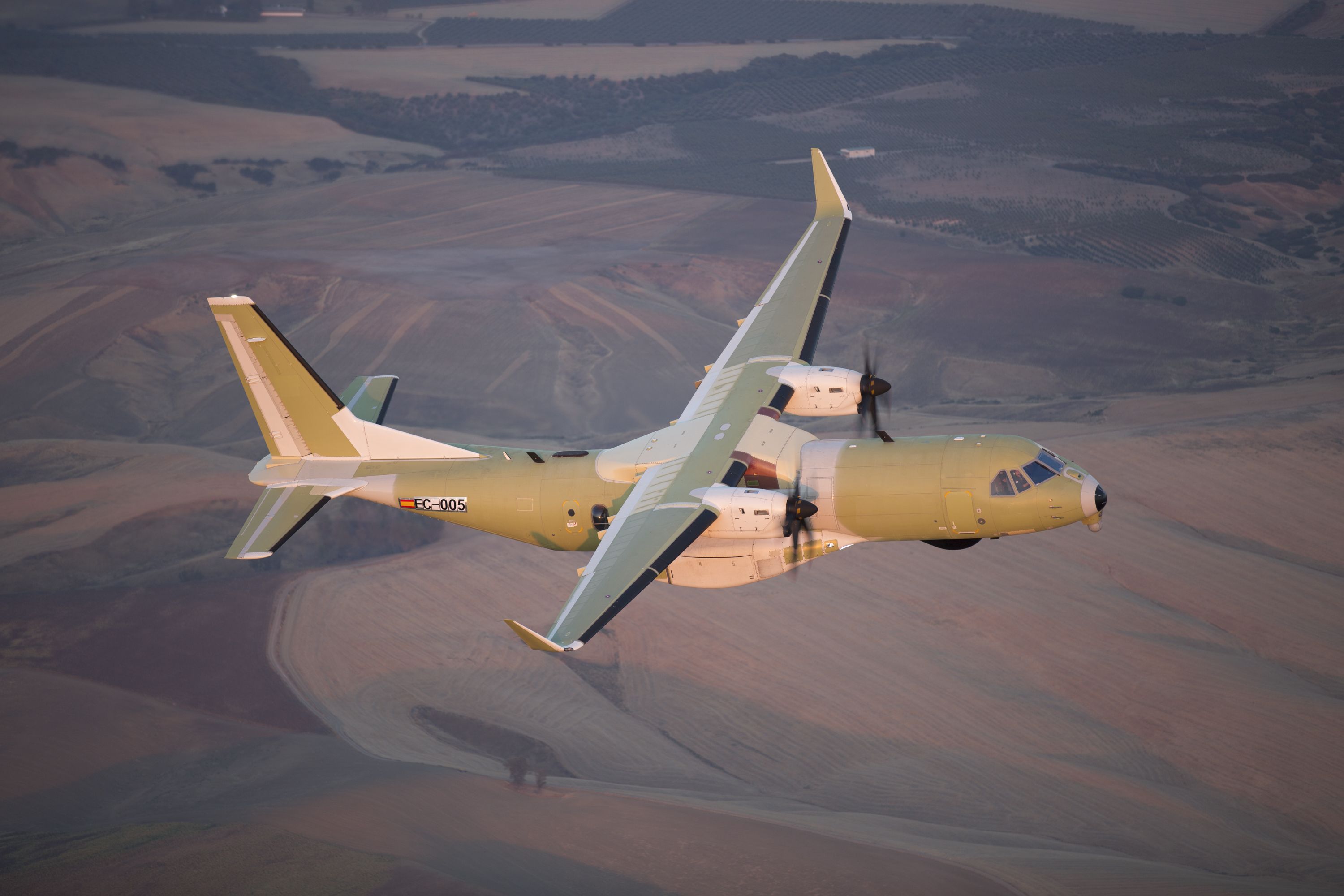
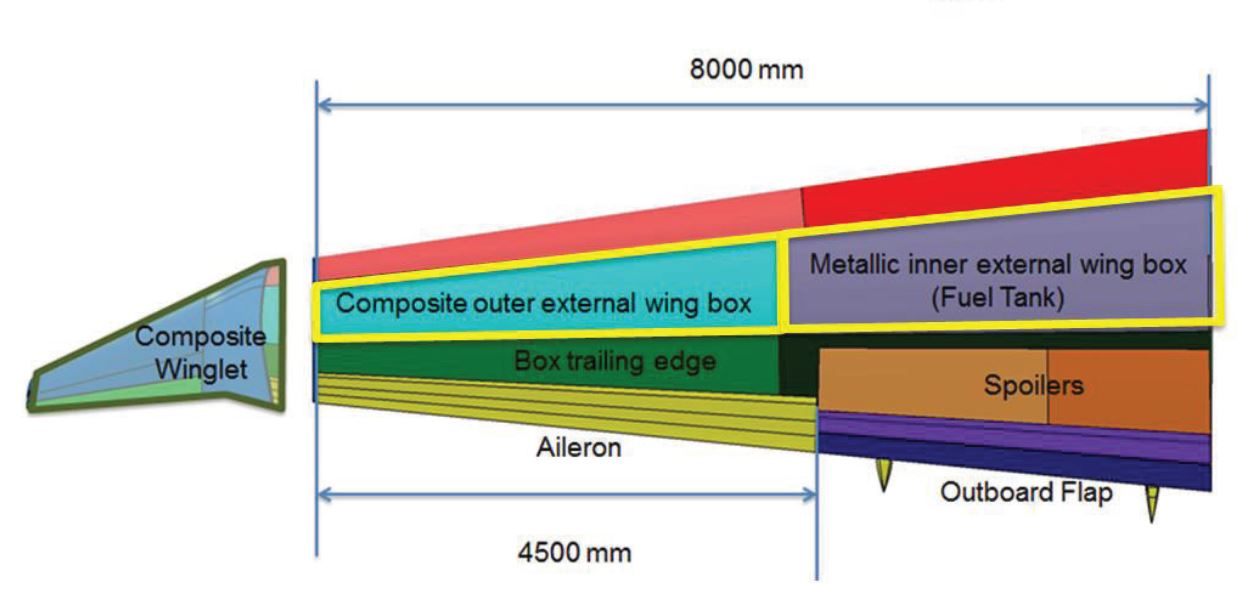
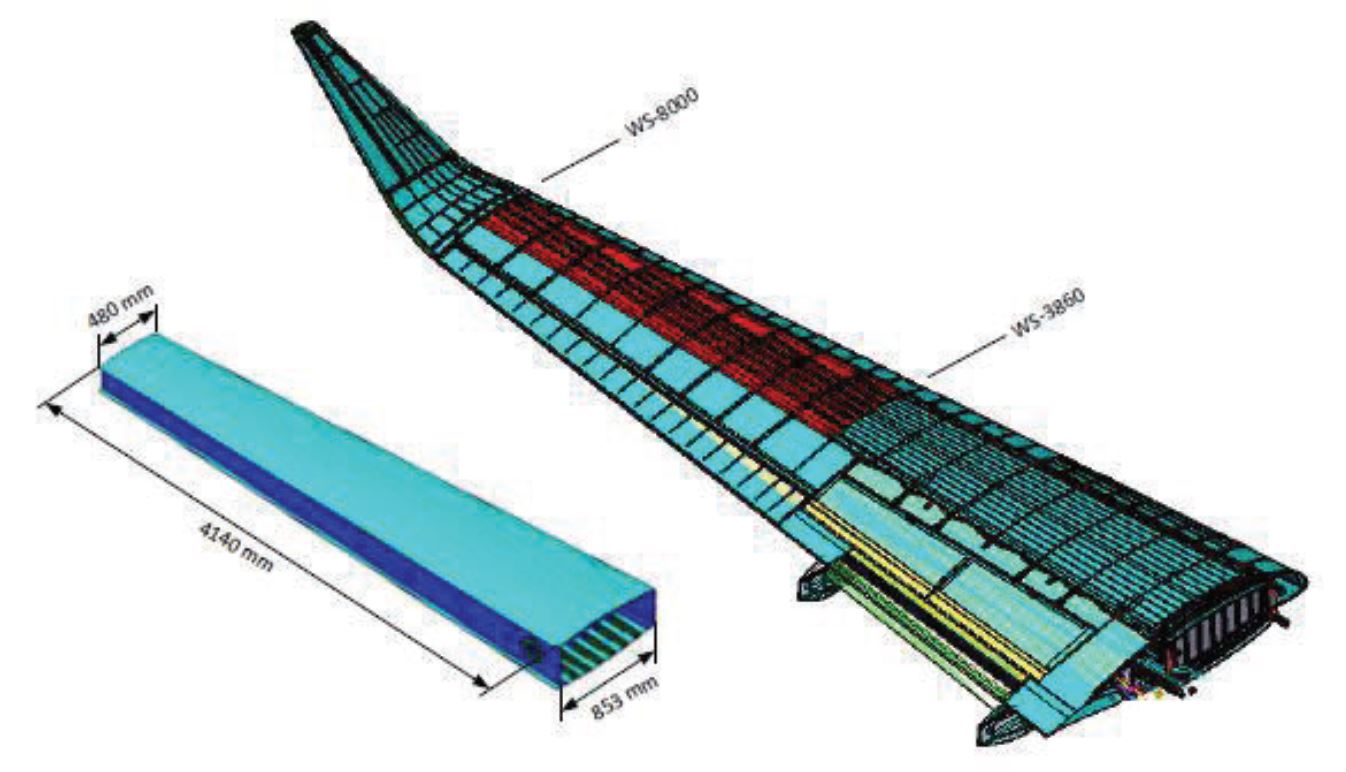
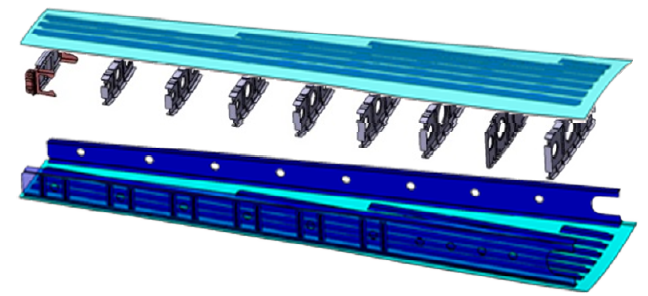
エアバスDSが選んだデモンストレーターは、スペインのセビリアのサンパブロで生産されたC-295ツインターボプロップ軍用輸送機(図1)をベースにした外翼ボックスでした。この4.14メートルの長さの複合船外トルクボックスは、船内金属に結合します。 トーションボックス。複合ウィングボックスは、ウィングレット、前縁、後縁にも取り付けられます。
「私たちは、飛行中の試験のために設置される、2つの長さ4メートルのデモンストレーター、右翼と左翼を製造することになっていました」とディアスは言います。 「製造は一回限りのプロセスであり、二次的な結合はありませんでした。 6つのストリンガーと両側にスパーが組み込まれた下部スキンで構成される「U」のみを作成しました。スキン、ストリンガー、スパーはすべて厚さが異なります。スパーのJ字型と補強材の統合は、製造が非常に困難でした。また、この製造プロセスで厳しい公差と正確な形状を維持する方法という課題にも直面しました。この精度は、特に内側のウィングボックスに組み立てるためのルートで、次にウィングレットでも重要です。」
革新的な工業製造の設計はMTorresで開発され、AirbusDSは部品設計仕様を提供しました。 「私たちは簡単に協力して最高の製造プロセスを設計し、この設計が私たちのプロセスで製造できること、およびその逆が可能であることを確認しました」とディアス氏は言います。
自動注入センター(ACTI)
エアバスDS仕様に従い、ウィングボックスの製造に使用されるすべての工具および製造装置は、持ち運び可能で、標準的な車両で他の施設に輸送でき、特別な措置を講じることなく迅速にセットアップできる必要があります。これは、ストリンガーとスパーのホットドレープ成形を実行する熱注入用自動センター(ACTI)の開発につながりました。ストリンガー、スパー、スキンの注入。と硬化サイクル。ホットドレープフォーミング(HDF)—航空構造の加熱デバルキングおよび航空宇宙外の加熱プリフォーミングとして開発—レイアップのボイドを取り除き、ストリンガーとスパーの2Dブランクを成形プリフォームに変換します(「ホットドレープフォーミング」を参照)。
ACTIの有効な内部領域は約5.5x 2.2メートルで、従来のHDFシステムに似ています。鉄骨フレームと上半分が電子的に上下し、ロックやその他の安全装置が備わっています。硬化ツールと複数のホットドレープ形成ツールがACTI内に配置されています。 「圧力はかけられず、真空だけが加えられます」とディアスは言います。 「ACTIは、ホットドレープ形成プロセスと注入プロセスの両方で高速熱伝達を提供するように定義された空気流を備えた加熱空気を使用します。」
彼はまた、システムがセルフレベリングであると述べています。 「ACTI構造(および硬化ツール)の剛性は、2つのサポートセクションのみで単純にサポートされた状態での操作負荷の下での許容誤差に準拠するように設計されています」とDiaz氏は説明します。 「これは、床に置いたときに寸法精度が維持されることを意味し、それ以上のレベリングやその他の幾何学的調整は必要ありません。 ACTIは、低エネルギーと低製造コストも特徴としています。」
後者は、主に、複数の硬化部品のアセンブリが複数のプリフォームのアセンブリに置き換えられ、それらが注入されて単一の統合構造に硬化されるためです。 「硬化ツールは組み立てツールでもあります」とDiaz氏は言います。 「すべての要素は、硬化ツールに組み立てられたドライプリフォームであり、シングルショットプロセスで一緒に注入されます。」組み立て治具は不要で、工具の革新的な要素によって厳しい公差が実現されます。
このアプローチのもう1つの重要な側面は、破壊検査と非破壊検査(NDT)を削除することです。代わりに、さまざまな製造ステップで収集されたプロセスデータに依存して、プロセスの品質を検証し、仕様外のパラメーターにフラグを立てます。 ACTIで使用されるセンサーは、温度、真空、樹脂の流れ、および硬化状態を収集します。 「気温と部品温度の両方が監視されます」とDiaz氏は言います。 「金型には、金型と部品表面の温度を追跡する熱電対が組み込まれています。」すべてのデータは記録、分析され、グラフを印刷し、製造上の決定を導くために使用されます。
「IIAMSと将来のプロジェクトの両方で、データは初期段階でのプロセス設定の改善に役立ちます」とディアス氏は説明します。樹脂の流れと硬化状態は、CFRP硬化ツールに直接取り付けられたNetzsch(Selb、ドイツ)誘電体センサーを使用して監視されます。 「樹脂とカビが直接接触しないため、皮膚に非接触センサーが必要でした」とディアス氏は言います。 「センサーは、樹脂が到着したときの誘電体フィールドの変化を監視し、硬化中に固体になります。このデータを使用して、硬化サイクルを短縮しました。」
プロジェクトの後半で、センサーとACTIは、MTorresによって開発されたヒューマンマシンインターフェイス(HMI)と組み合わされました。これにより、真空や温度、フィードバルブを介した樹脂の流れなど、コンピューターからの真のプロセス制御が可能になります。 Airbus DSによると、目標は、プロセスをより合理化およびインテリジェント化することにより、統合された複合一次構造の大量生産を促進することです。
軽量のツールと携帯性
MTorresは、右翼用と左翼用の2セットの金型を製造しました。 「補強材のように、同じ形状の部品には1つのセットしかありませんでした」とDiaz氏は述べています。 「可能であれば、他のツールを共有しました。」
単一のワンピース硬化ツールを使用して、皮膚の3D形状を形成し、その上に他のすべてのプリフォームを配置しました。長さ約4.5メートルのこのツールの左右のバージョンはCFRPを使用して作られました、とディアスは言います。 「これにより、部品と同じレイアップと処理で工具を設計したため、公差を維持しやすくなり、CTEは最終部品のCTEに非常に近くなります。これらのCFRP硬化ツールも軽量で、約200 kgであるため、小さな電動フォークリフトで移動できます。長さ4.5メートルの工具に金属を使用した場合、これは不可能です。」
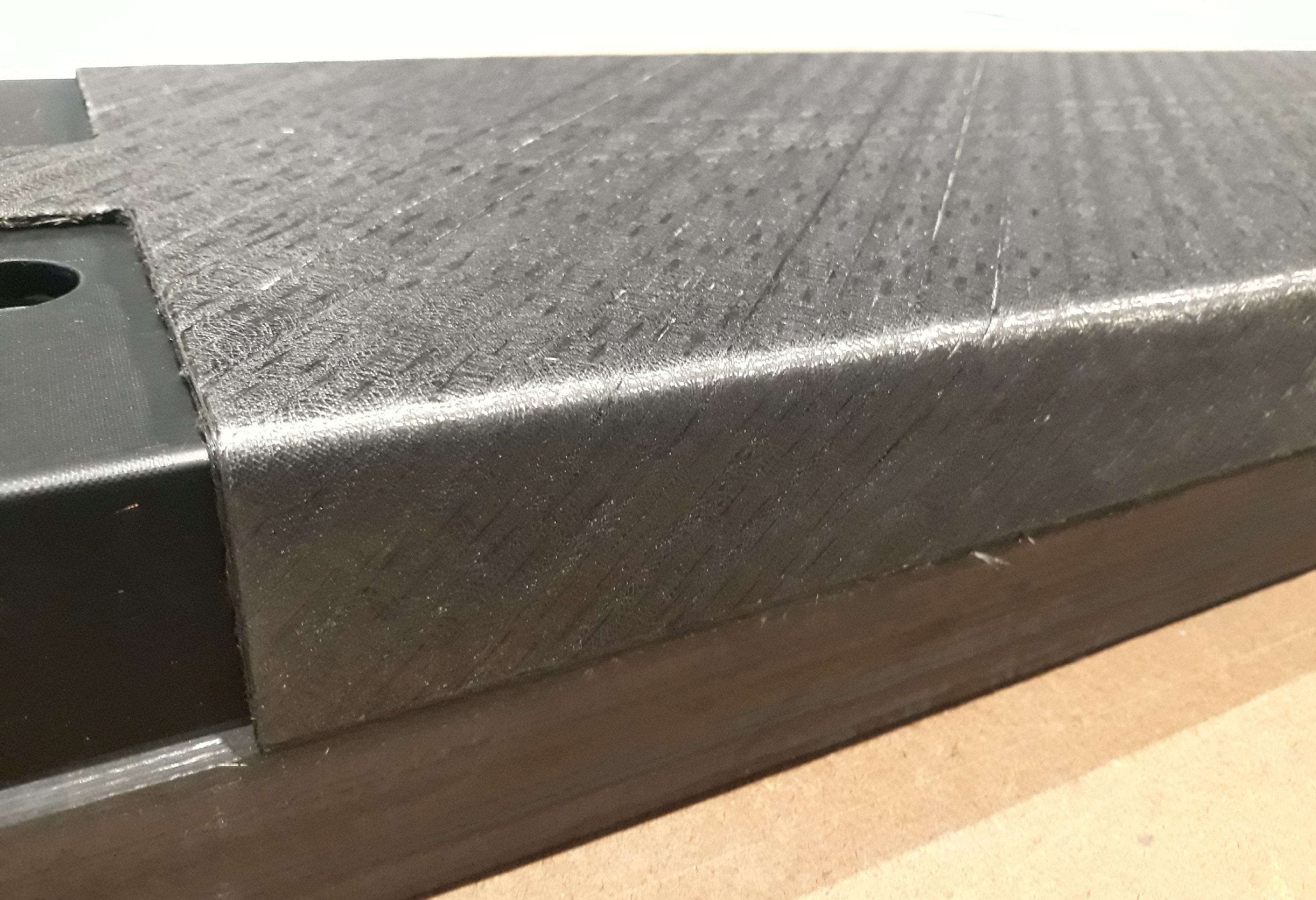
残りの工具(コール、ポジショナー、HDFツール)は手作業で簡単に管理できました。ストリンガー、スパー、スパー補強材のプリフォームのHDFは、同じくCFRP製のオス(IML)ツールを使用していました。使用中、これらはアルミニウム製のテーブルに取り付けられ、ACTI内に設置されました。
新しいドライファイバーテープを使用したAFP
ウィングボックスのすべての構造要素(スキン、ストリンガー、スパー、スパー補強材)は、乾式繊維テープ用のMTorresAFPテクノロジーを使用して製造されました。 「提案の呼びかけは、速くて安い材料を使うと言われました」とディアスは言います。 「しかし、特に大規模なサプライヤーから市販されている乾式繊維テープは、購入がそれほど簡単ではなく、独自の材料を作成する専門知識がありました(「液体成形複合材料用の新しい乾式テープ」を参照)。そこで、三菱レイヨン(東京、日本)の50K高強度(HS)繊維から作られた、幅0.5インチ、1平方メートルあたり300グラム(gsm)の乾燥炭素繊維テープを使用しました。私たちのテープは、注入中だけでなく、AFPヘッドを使用したレイアップ中にも容易に機能するように設計されています。 AFPレイアップ、ホットドレープフォーミング、樹脂注入のすべてのパラメーターを知っています。小さな変更が必要な場合は、テープ製造ラインが利用可能だったので、それが可能でした。」
MTorresはまた、中間弾性率(IM)ファイバーから作られたHexcel(LesAvenières、フランス)の200gsmテープを使用してウィングボックスの製造プロセスをテストしました。 「私たちのプロセスは両方のタイプのテープでうまく機能しますが、開発段階では、市販の材料よりも私たちの材料を敷設する方が簡単で安価でした。幅と剛性は、テーブルへのスプールはスムーズで高速でした。また、すぐに利用できました。」

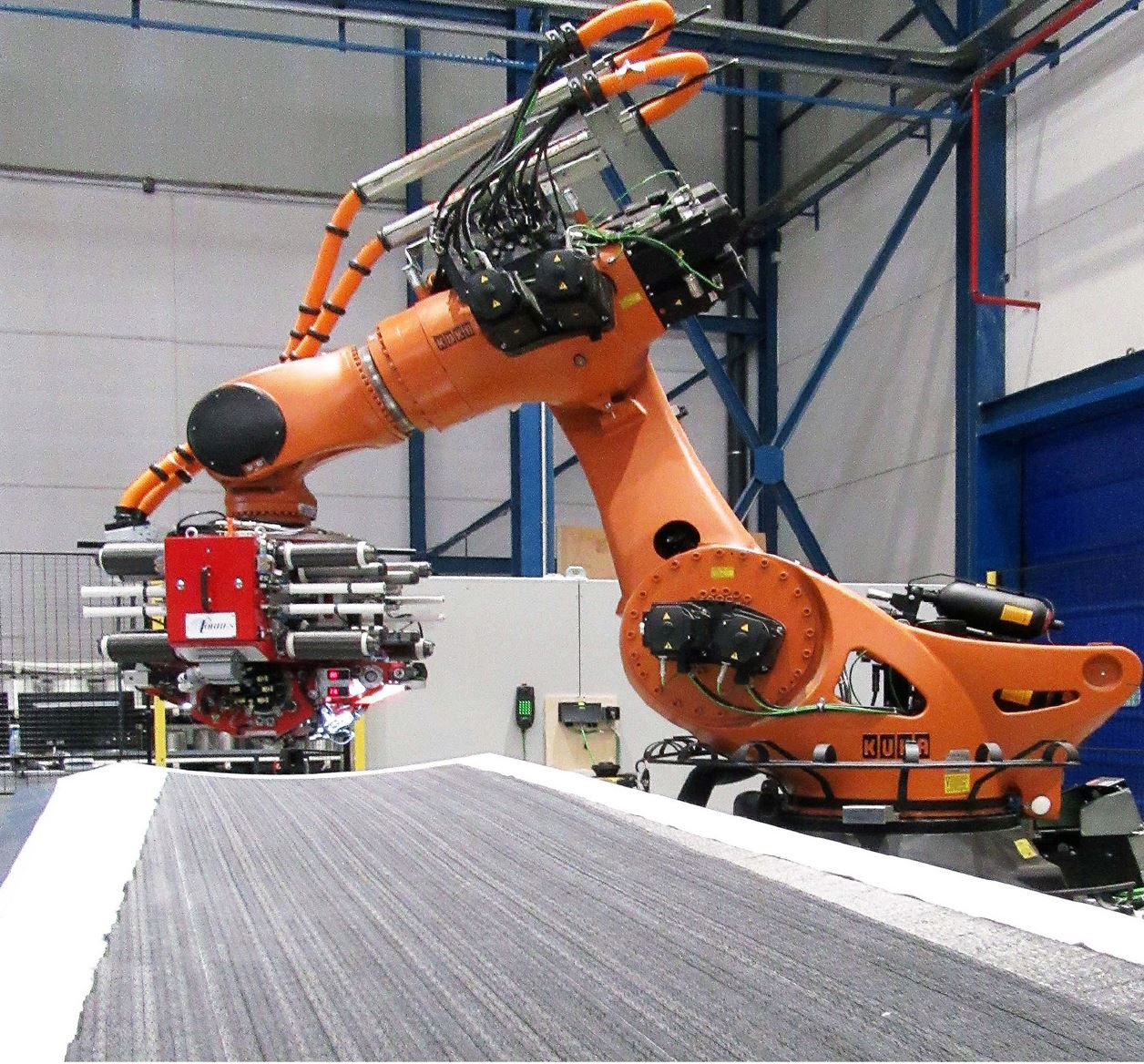
ステップ1。 AFPは、ウィングボックススキン(ここに表示)と、ストリンガー、スパー、およびスパー補強材用の2Dブランクをレイアップするために使用されました。 写真クレジット、すべての手順: IIAMSプロジェクト、エアバスディフェンスアンドスペース、MTorres。
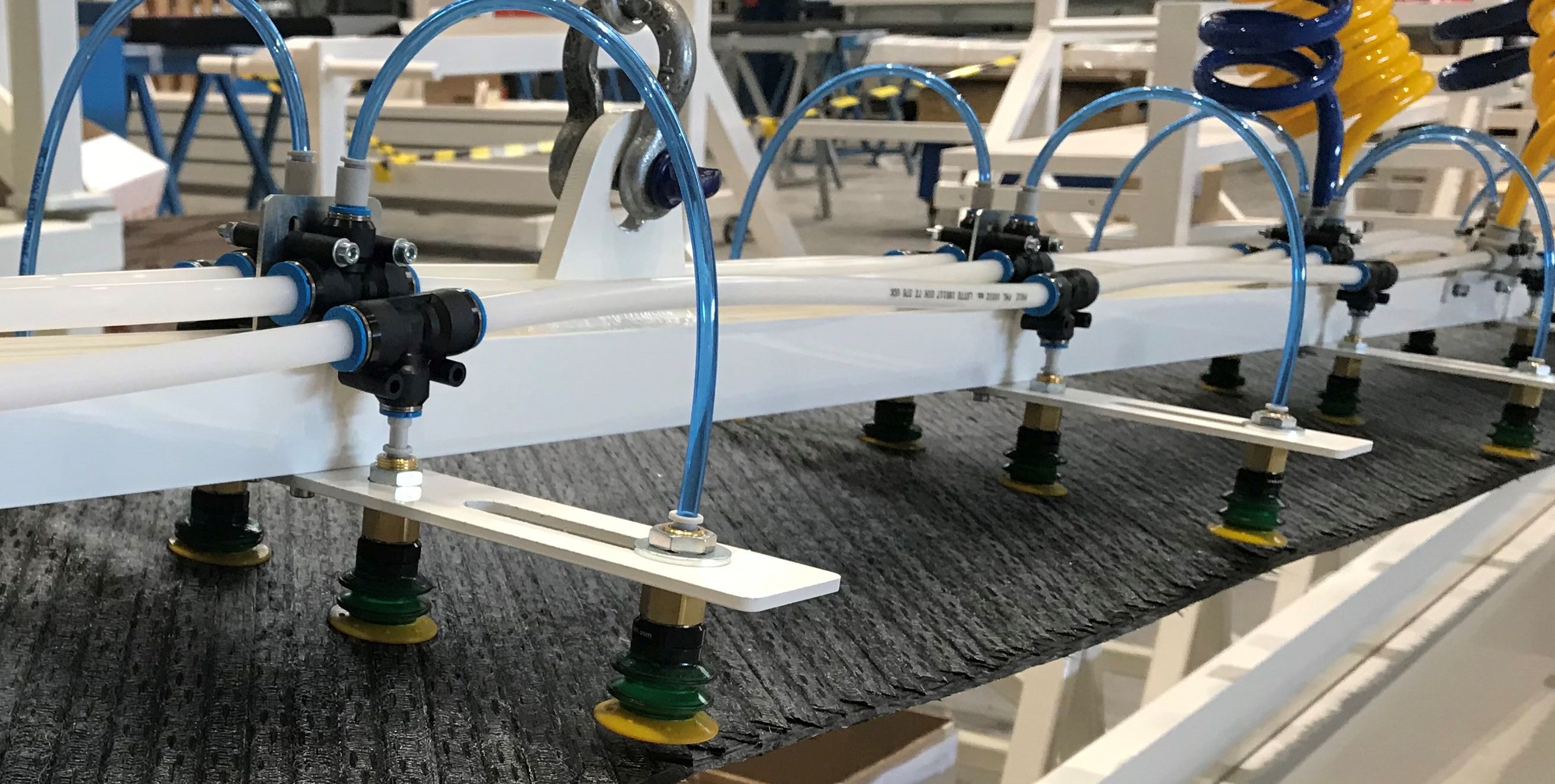
ステップ2。 フラットテープブランクは、レイアップテーブルからホットドレープ成形ツールに運ばれました。
彼は、AFPには2つの戦略が採用されたと述べています。1つは下部スキン用で、もう1つはストリンガー、スパー、スパー補強材用です。 を使用して、硬化ツール(ステップ1)の上にスキン(厚さ3〜6ミリメートル)を最終的な3D形状に配置しました。 半透膜—エアバスが真空支援プロセス(VAP)注入で特許を取得しています。ストリンガー、スパー、スパー補強材をフラットブランク(2D)として真空テーブルに置き、HDFツールに移動して、最終的な3D形状を実現しました(ステップ2)。
加熱された予備成形
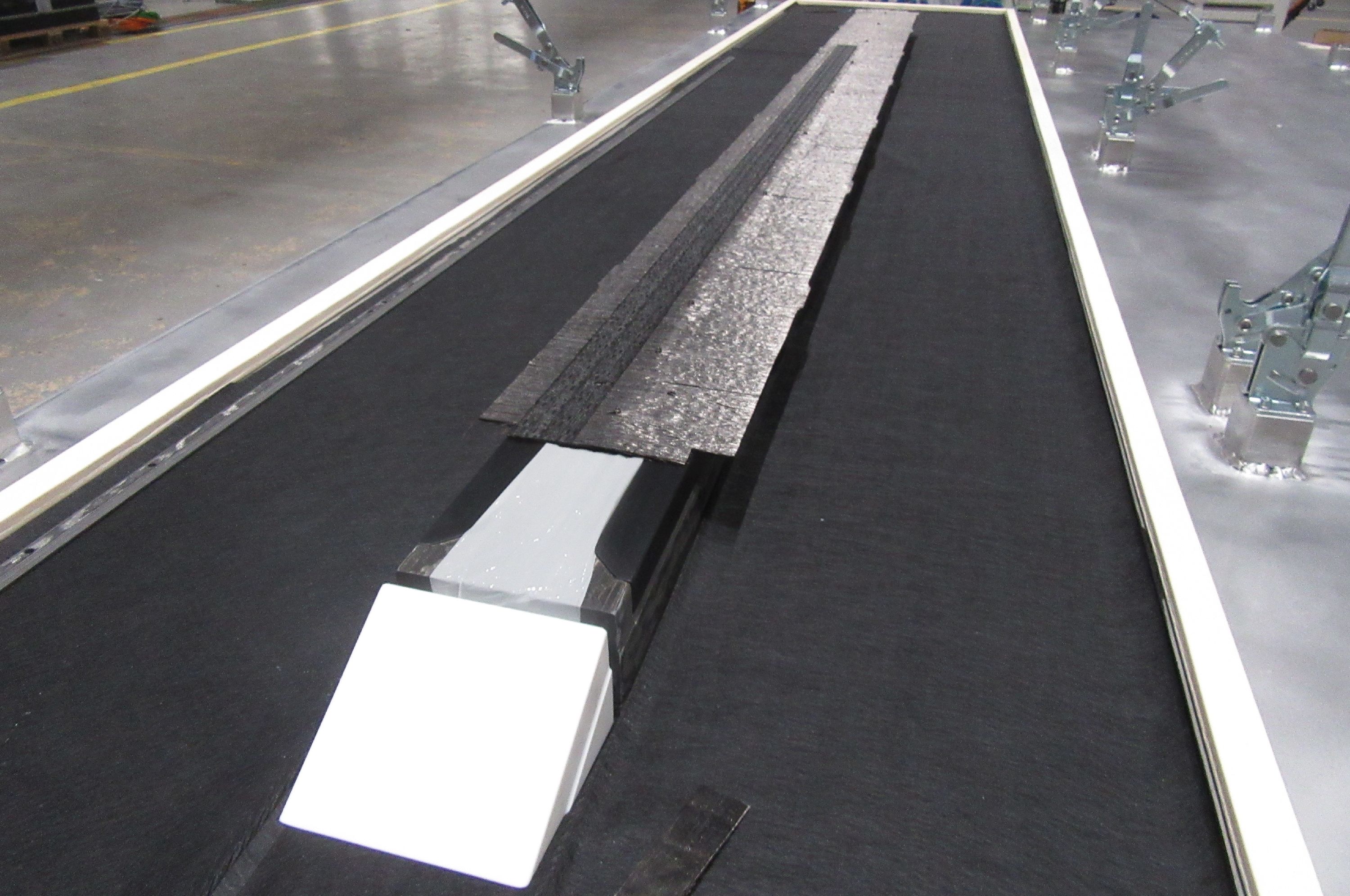
ステップ3。 ストリンガーブランクは、オスのHDFツールの上に配置されます。
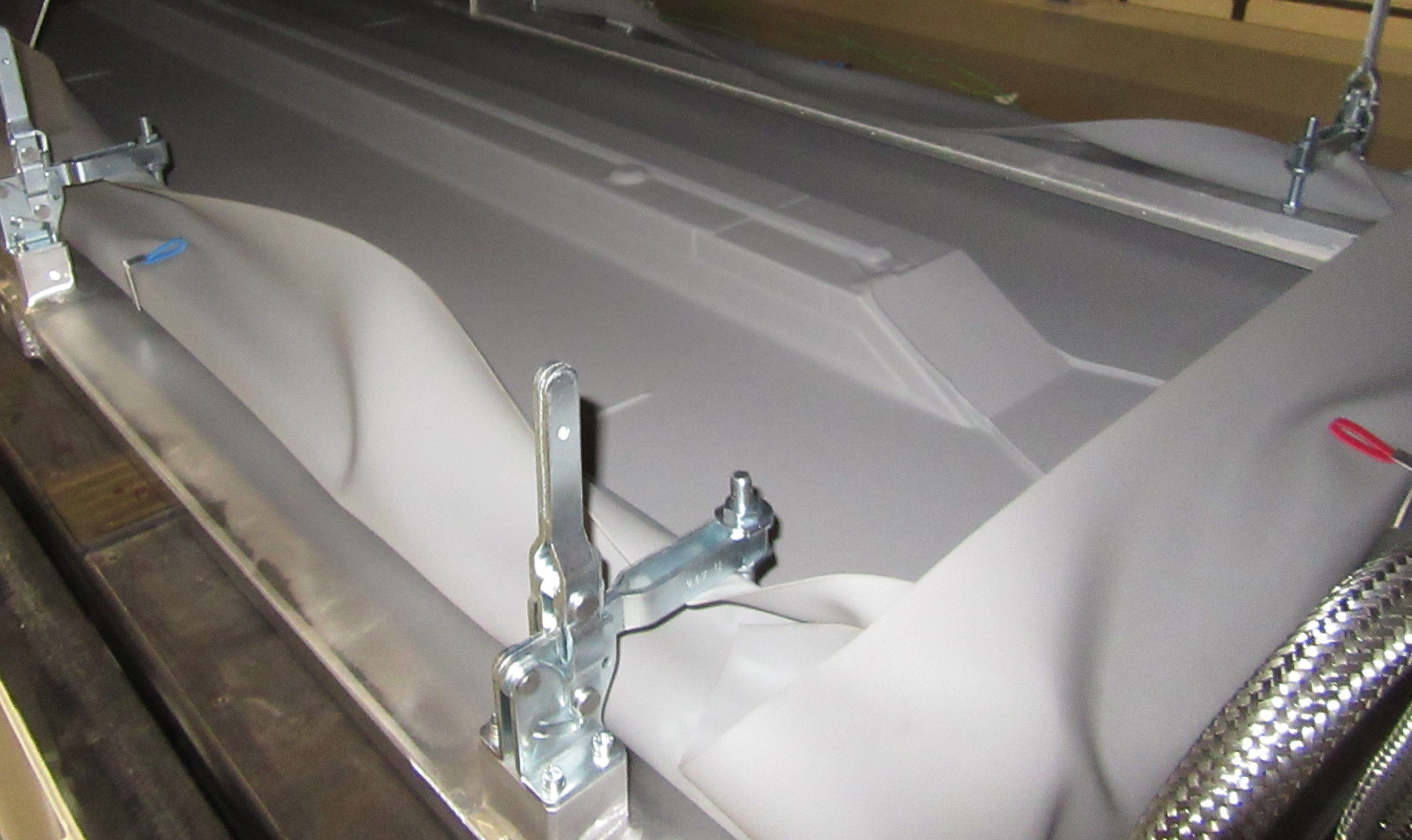
「ストリンガー、スパー、スパー補強材のフラットブランクを、真空グリッパー付きのガントリーを使用して、レイアップテーブルから熱間成形ステーションに移動しました」とDiaz氏は説明します。 「自動化されたシステムは、ブランクを平らな状態で動かし、しわを作ることなくオス成形ツールに配置することができます[ステップ3]。」成形工具は、ACTIに配置されたアルミニウム成形テーブルに取り付けられました。再利用可能なシリコン真空バッグ(Mosites Rubber Co.、Fort Worth、Texas、U.S。)をブランクの上に置き、ACTIで130°Cに加熱し、真空圧を使用して成形しました(ステップ4)。 「温度設定値に達したときに、制御バルブを使用して事前定義されたランプに従って真空がスムーズに適用されました」とDiaz氏は言います。
彼は、ドライテープはプリプレグ/ホットドレープフォームの方が簡単であると述べています。「層間の結合がプリプレグよりも柔らかいためです。乾燥した素材であるにもかかわらず、 テープに含まれているバインダーのおかげで、得られたプリフォームが形状を維持するHDF /加熱デバルキング。」
ストリンガーとスパー補強材の場合、ブランクを2つのLに成形し、硬化ツールに背中合わせに配置してTストリンガー/補強材を形成しました。 6つのスキンストリンガーはそれぞれ異なり、プリフォームを作成するには異なる形状のブランクが必要です。 24個のスパー補強材もそれぞれ長さが異なります。
フロントとリアのJスパーは、ウィングボックスの内側を向くCに形成された1つのブランクと、外側を向いたZに形成されたもう1つのブランクで構成されます。2つは背中合わせに配置されます。スパーには、ウィングボックスの外側に正弦波状の脚があります(ステップ7の矢印)。 「ブランクを成形ステーションに移動する前に、フラットレイアップテーブルでスパーフィートの形状をカットしました」とDiaz氏は言います。 「このエリアでは、後でトリミングやフライス盤を作ることはできませんでした。ブランクは、スパーフィートがツールの左側にあり、上部フランジが右側にある状態で、オス成形ツールにまっすぐに配置されました。」
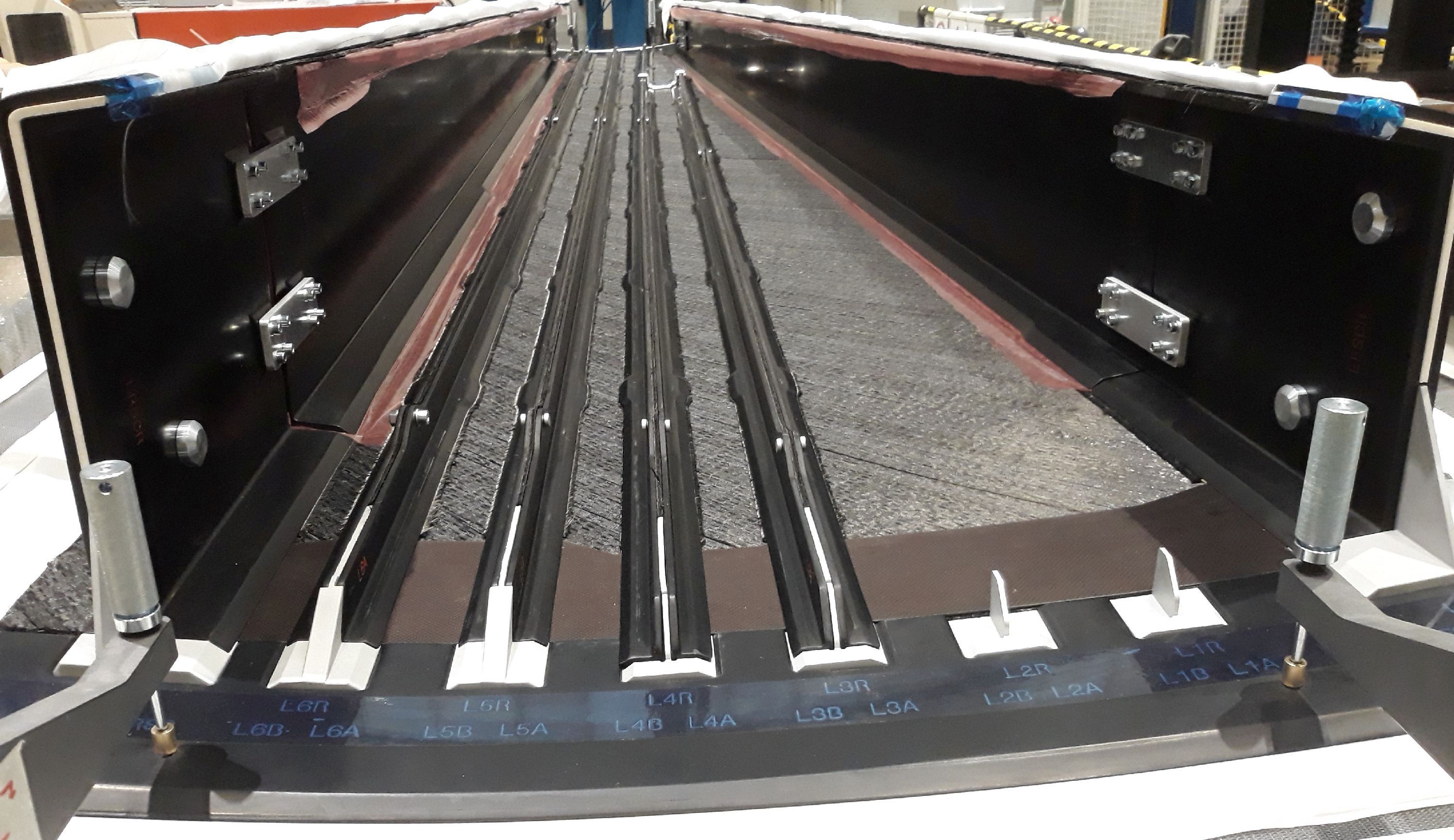
図。 3.正確なプリフォームの配置。 Jスパーとストリンガーのプリフォームは、2つの金属シリンダー(左端と右端に表示)、白いポジショナー、ストリンガー/ポジショナー用の切り欠きのあるCFRPコールを使用して配置されました。 写真クレジット: IIAMSプロジェクト、エアバスディフェンスアンドスペース、MTorres。
ワンショット注入
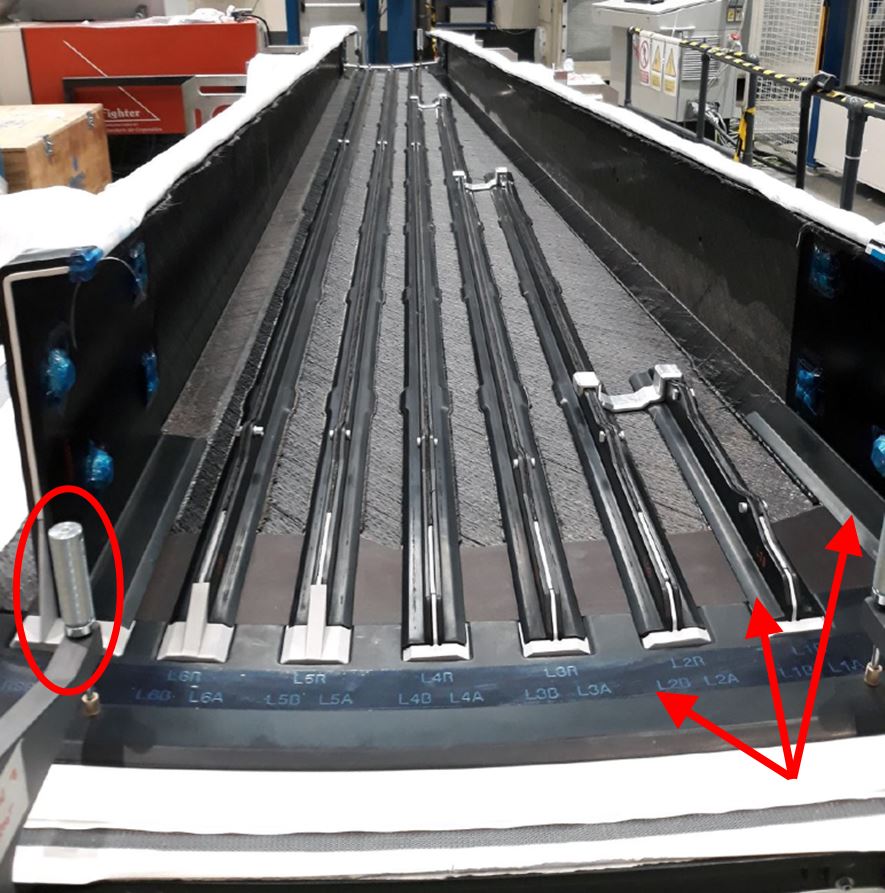
ステップ5。 ストリンガーとスパーのプリフォームは、円筒形(丸で囲まれた)の助けを借りて、下の皮膚に配置されました。 )と白いポジショニング要素。黒のCFRPコール(矢印 )は、ストリンガーの配置を支援するためにも使用されました ストリンガーとJスパーの上に配置されます。
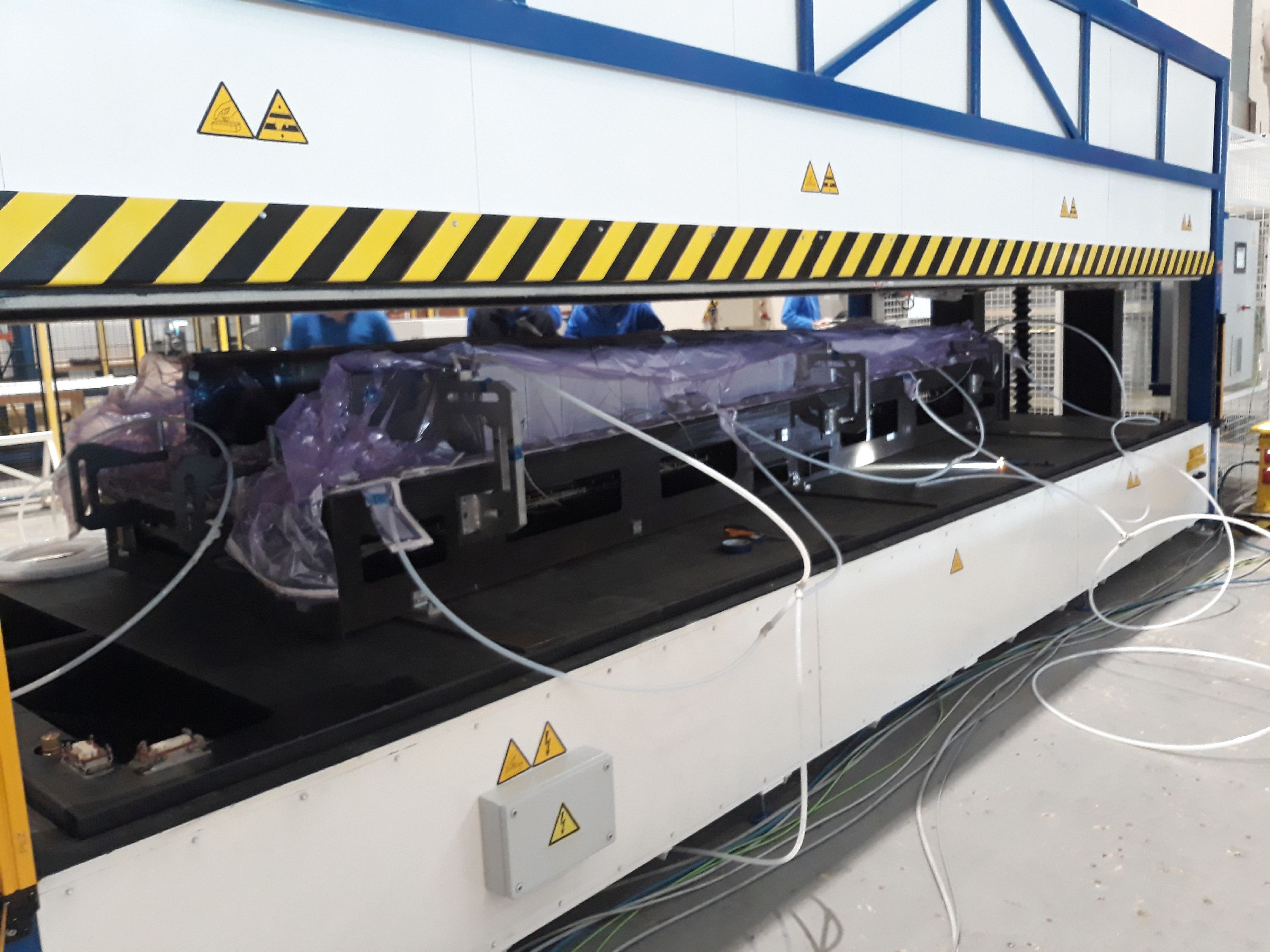
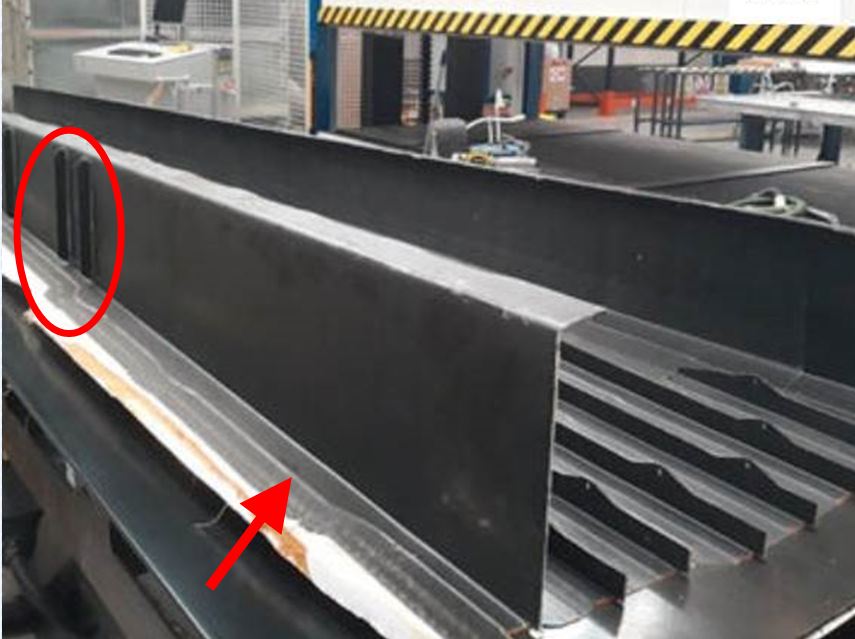
ステップ7。 MTorresで完成した最初のデモンストレーターは、2つのリブ補強材を備えたJスパーを示しています(丸で囲んだ )とその正弦波の足(矢印 。
次のステップは、ストリンガー、スパー、スパー補強材のプリフォームを、すでに敷設されている下翼の外板に配置することでした(ステップ5)。 「各プリフォームをスキンアンドキュアツールに配置するときにインデックスを作成していました」とDiaz氏は言います。位置要素として機能するシリンダーは、ステップ5の左側の桁の端と、図3の両方の桁の端に表示されます。これらの画像は、ストリンガーとJ桁の白い位置決め装置も示しています。最終的なプリフォームアセンブリにはこれらのポジショナーが13個あり、それぞれが異なっていました。
コールプレートは、プリフォームの配置および配置システムの重要な部分でもありました。それらは、複雑なレイアップおよび/または形状の領域全体で均一な圧力と温度を維持するという従来の目的を果たしましたが、以下で説明するように、注入の鍵にもなります。ステップ5と図3のストリンガーとスパーの端に、ストリンガープリフォーム用の切り欠きのある黒いCFRPコールプレートがあります。
「ストリンガープリフォームの位置は、そのコールの位置によって異なります」とディアス氏は説明します。 「製造プロセスを監視および制御するために開発したデジタルテクノロジーには、CATIAモデルをレイアップに投影する拡張現実アプリが含まれていました。これは、コールプレート、位置決め要素、およびプリフォームの配置をガイドするために使用されました。また、実行する次のステップも示しました。このアプリでは、タブレットコンピューターでのセルフサポートが可能であるため、すべての従業員がすべての情報に簡単にアクセスできます。」
次に、黒のCFRPコールプレートの最終セットを、TストリンガーのLプリフォームの上に配置し、各Jスパーの内側と外側に沿って配置し、フランジまで上に、外側の足まで下に伸ばしました。ステップ5と図3に示すように、ウィングボックス。「スパーは、接合部の精度を高めるために、端の内側にある種のコールプレートも使用します」とDiaz氏は言います。 「これらのコールプレートはすべて、HDFプロセス中に使用され、レイアップによってプリフォームに取り付けられたままでした。」
次に、コールプレートを備えた完成したドライプリフォームアセンブリを、ピールプライと真空バッグフィルムで覆った。次に、スキン、ストリンガー、スパーのアセンブリ全体をACTIに配置し、工具を120°Cに加熱しました。 Hexcel RTM6エポキシ樹脂を70°Cに加熱し、脱気してから、単一の樹脂供給場所から注入しました。 「ACTIは4つの場所から樹脂を供給する準備ができていましたが、広範なシミュレーションとテストの結果、単一の樹脂注入口を使用する方が簡単で安価であると判断しました。」
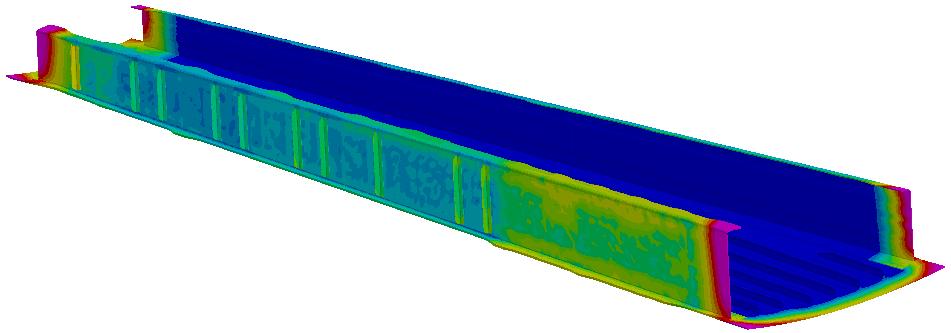
単一の注入口でも、注入プロセスは非常に複雑で、3つの異なるモードで構成されていました。 「最初に、PAM-RTMソフトウェア[ESI Group、パリ、フランス]を使用して流体シミュレーションを実行しました」とDiaz氏は言います。 「完全なウェットアウトに必要なフローフロントとパラメータの複雑な組み合わせがありました。たとえば、ウィングボックスの中央では樹脂の流れが速くなりましたが、すべての補強材を濡らすのは困難でした。」
半透膜を備えたVAPは下層の皮膚にうまく機能しましたが、これはストリンガーに沿ったスパーの内側の高温フローメッシュと交換されました。 「コーナーは濡れるのが最も難しい領域でした」とディアスは言います。「しかし、コーナーは、エッジに沿ってだけでなく、組み立ての公差を保持するためにも最も重要でした。」これは、図4のフローシミュレーションの赤い領域で確認できます。「これらの領域では、必要な正確な寸法を実現するためにカスタマイズされたアプローチが開発されました」と彼は説明します。また、周囲に沿って、スパーの上部に真空ポートを使用しました。」
シミュレーションで予測されたように、注入は比較的迅速で、その後、加熱された工具ではなく、熱風のみを使用して、180°Cで2時間硬化しました。型から外された後、各ウィングボックスのデモンストレーターは超音波探傷試験(UT)を使用して検査されました。これは、デモ参加者の質を分析するために、IIAMSプロジェクトの成果物の一部として行われました。ただし、このプロセスを産業用に適用すると、従来のNDTが削減され、デジタルセンサーと、ビジョンシステムなどのより高速なインライン検査ツールが採用されます。
Diazによると、注入硬化サイクルはオートクレーブ硬化プリプレグウィングボックスの場合と同様でしたが、全体的なサイクル時間は短くなるはずです。 「その後、アセンブリのほとんどを排除しました。また、プリプレグのようにシムをかける必要もありませんが、品質は同じです。たとえば、スキンの最後の層とストリンガーの最初の層の間の結合は、機械的特性を改善し、公差を説明するために、中央に接着フィルムを必要としません。」これは明らかにより効率的ですが、彼は部品生産率が最初は推進要因ではなかったと述べています。 「この方法は、個々の部品の製造と競合するのではなく、完成したウィングボックスアセンブリと競合します。」
完全なデモンストレーター、認定への道
「このプロジェクトを完了するのにたった18か月しかありませんでした。これには、プロセスとツーリングの設計、ツーリングとデモンストレーターの製造が含まれていました」とDiaz氏は言います。 「14か月目までに、2020年2月下旬にJECで最初のデモンストレーターを展示する準備が整いました[ステップ3]が、その後、パンデミックのためにJECはキャンセルされました。プロジェクトは2020年9月下旬に終了しましたが、COVID-19で作業できなかった月を差し引くと、実際には16か月で終了しました。社内の設計能力と能力により、この非常にタイトなスケジュールを維持することができました。 AFPおよびCNCミリングマシンを使用してツーリングプロトタイプを製造します。」
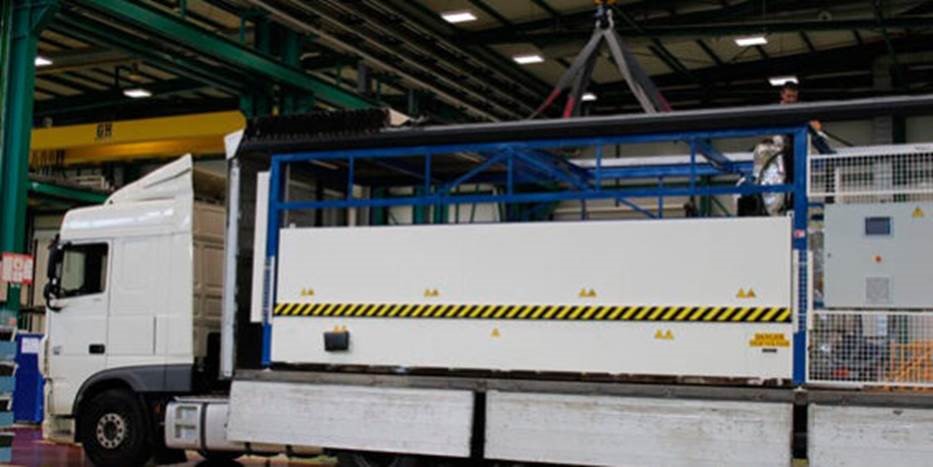
ステップ8。 ACTI成形/硬化装置とウィングボックスツールは、標準の移動トラックに持ち上げられ、スペインのカディスにあるエアバスDSに移転されました。
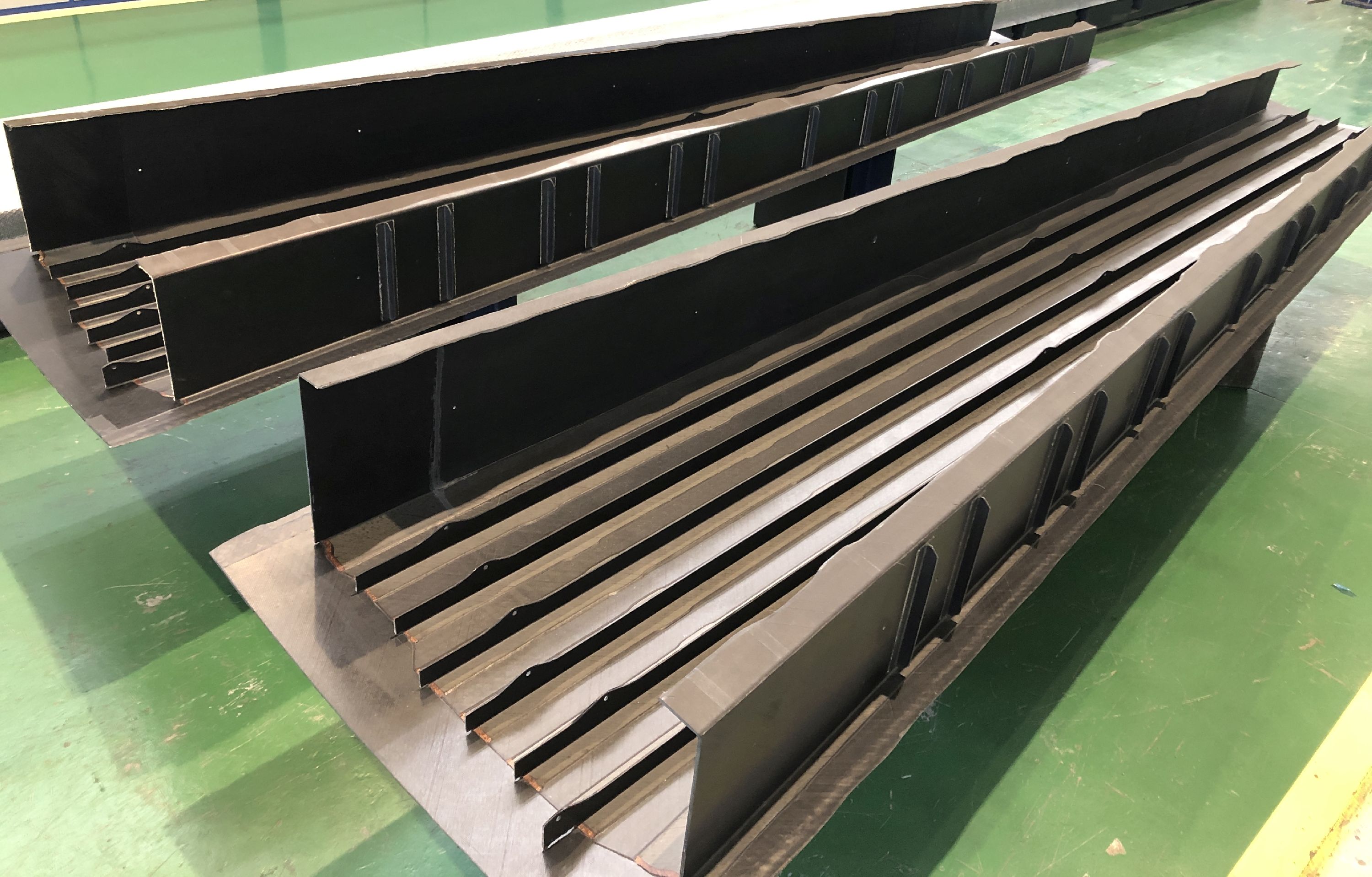
すべてのプロセスパラメータをチェックするために、MTorresで簡略化された長さ1メートルのデモンストレーターが作成されました。その後、初の実物大デモンストレーターが製作されました。その後、工具および製造装置はカディスのエアバスDSに移され(ステップ8)、そこで最終的なデモンストレーターが製造されました。これもプロジェクトの成果物の一部であり、機器を簡単に輸送して複数の場所に設置できることを証明しました。
サイドバーの「IIAMSウィングボックスの認定へのロードマップ」で説明されているように、エアバスDSは、クリーンのグリーンリージョナル航空機(GRA)統合技術デモンストレーター(ITD)の共同リーダーから発展し、クリーンスカイプログラムで重要な役割を果たしました。 Sky、AIRFRAME ITDの共同リーダー、およびClean Sky 2内の地域統合航空機デモンストレータープラットフォーム(IADP)の飛行テストベッド2(FTB#2)のリーダー。FTB#2には他のコンポジットと機体が含まれます。コックピットやその他の翼のコンポーネントを含む開発。
FTB#2を準備するためのすべてのプロジェクトは、実際、エアバスのより広範な長期戦略の一部です。目標は、より軽量で効率的な将来のターボプロップ機体を開発することです。製造プロセスは、より安価でエネルギーの使用量が少なく、液体や補助材料を製造しますが、スクラップの発生も少なく、リサイクル性も向上します。
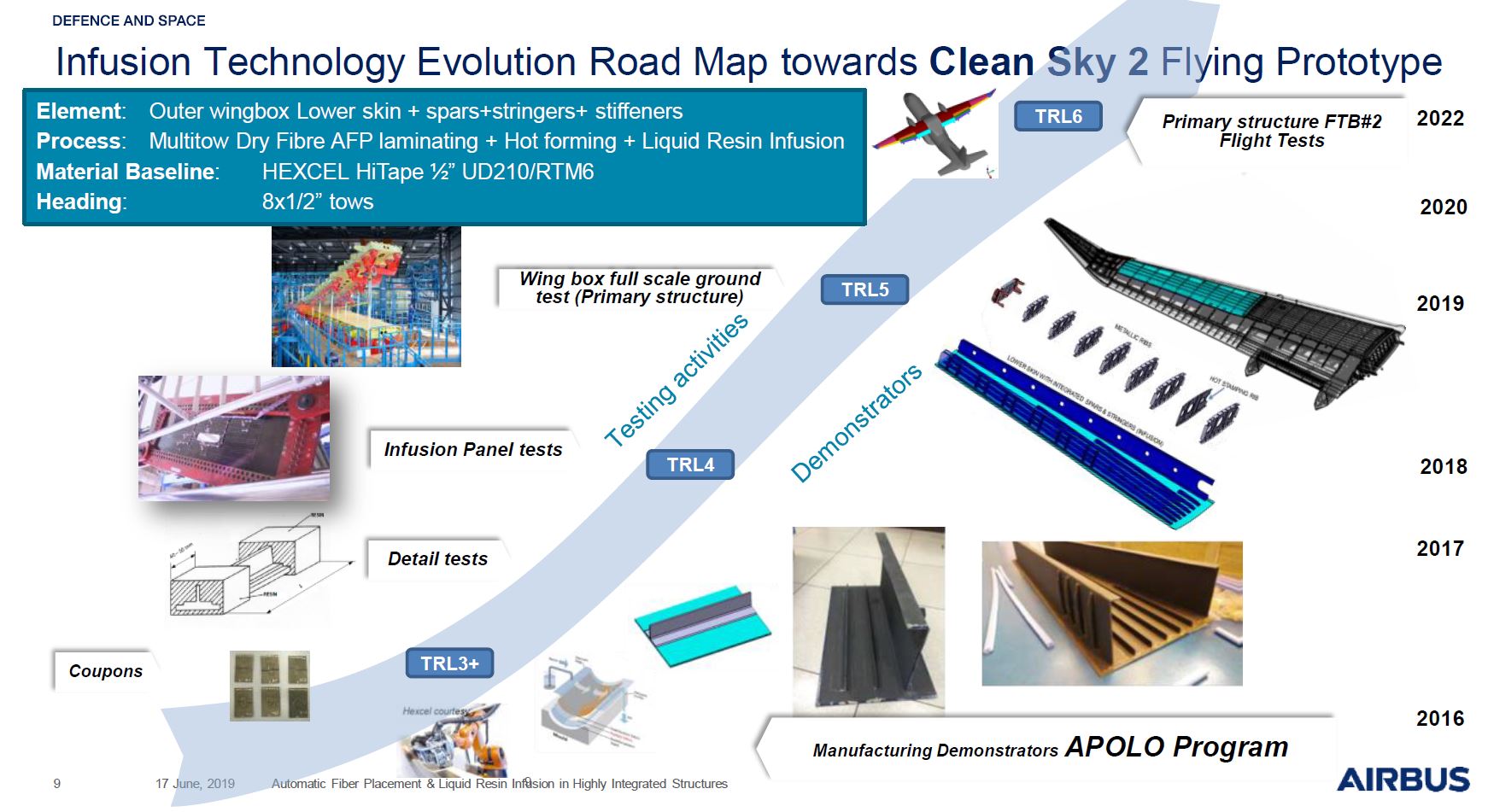
「私たち[AirbusDS]は、クーポンから外翼の本格的な構造テストまで、機体構造テストピラミッド全体を段階的に実行しています」と、2020年9月のA.E.JiménezGahete氏は説明します。 MaterialesCompuestos 「エアバスディフェンスアンドスペースの高度に統合されたウィングボックスセクションは、乾式繊維の配置と液体樹脂の注入によって製造されました。」というタイトルの記事。材料特性試験、設計詳細試験マトリックス、および設計許容値のサブコンポーネント試験はすべて完了し、良好な結果が得られています。 MTorresは、テストクーポンや部品の製造、ウィングボックスの製造プロセスと設計の詳細を検証するためのデモンストレーターなど、このテストを支援しました。飛行のためのFTB#2資格を取得するために、最終的な外翼の実物大の静的および機能テストのみが残っている、とGaheteは言います。
「ワンショット注入は、関節を減らし、体重を減らし、頑健性を高めます」とディアスは言います。 「MTorresが開発した新しいドライテープは、処理(AFP、ホットドレープの形成と注入)と部品の構造特性の両方で優れた結果を生み出しました。」彼は、歴史的に、樹脂を注入した複合材料がオートクレーブで硬化したプリプレグと同じ構造性能と公差に一致する可能性があるとは考えられていなかったと述べています。
「ソフトな[非金属]工具を使用したシングルショットプロセスで同じ公差を実現することが、私たちの最大の課題でした」と彼は認めています。 「しかし、この技術が機能し、将来の航空機に必要な大きな一次構造を生み出すことができることを証明しました。次のステップは、本番システムのデジタルテクノロジーと移植性を進化させ続けることです。」
樹脂