多機能胴体デモンストレーター(MFFD)の前進
燃料排出量とエネルギー消費量の削減、および月に少なくとも60の割合で単通路の民間航空機を生産する能力は、2035年以降に空を飛ぶ次世代航空機のためのClean Sky 2Europeanパートナーシップの技術開発を推進しています。 。特に多機能胴体デモンストレーター(MFFD)プロジェクトでは、軽量の複合材料とより高速で環境に配慮した製造プロセスにより、これらの目標が実現されています。
エアバス(ハンブルク、ドイツ)が学界および航空業界のパートナーとともに主導するこのプロジェクトの主な成果物は、長さ8メートルの熱可塑性複合材、単通路の民間航空機胴体バレルデモンストレーターです。 2022. MFFDは、Clean Sky 2の大型旅客機(LPA)の革新的な航空機デモンストレータープラットフォーム(IADP)内で製造されている3つの実物大の胴体セクションの1つです。
2014年に開始された、MFFDプロジェクトの目標は次のとおりです。
- 月に60〜100機の航空機の生産率を有効にする
- 胴体の重量を1,000キログラム減らす
- 経常コストを20%削減します。
これらの目標を達成するために、数十の個別のプロジェクトと作業パッケージが完成し、2つの主要な構造が作成されています。上部胴体シェルと下部胴体シェルが溶接されて最終的なデモンストレーターを形成します。実際、溶接による無塵接合(留め具や穴なし)は、プログラムの主要なコンポーネントの1つです。両方の半分は、Toray Advanced Composites(Morgan Hill、CA、U.S。)のToray Cetex TC1225低融点ポリアリールエーテルケトン(PAEK)炭素繊維熱可塑性プリプレグから製造されています。 Dr.-Ingによると。ドイツ航空宇宙センター(DLR、ドイツ、アウグスブルク)の接合および組立技術の責任者であるLars Larsenは、両方の半分が異なる製造技術の使用をテストします。
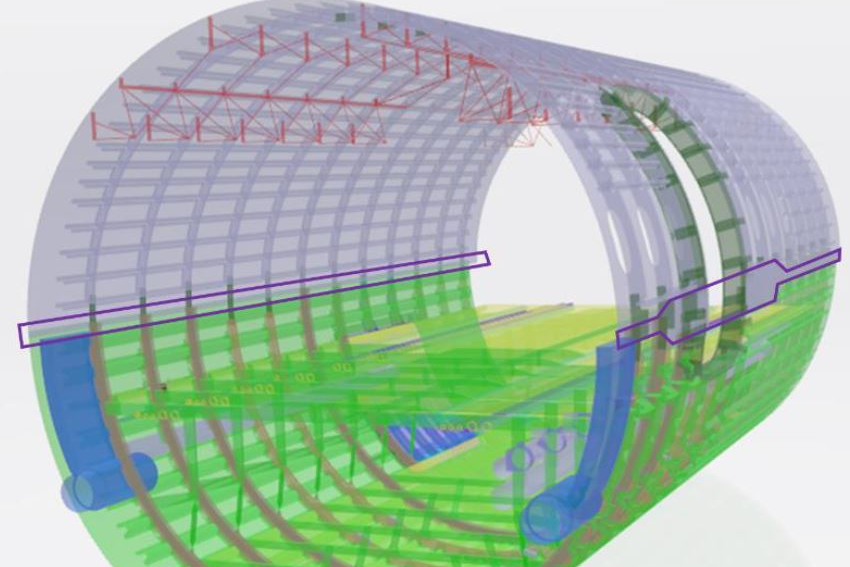
MFFDの下部胴体セクションは、プロジェクトSTUNNING(SmarT mUlti-fuNctionNalおよび統合熱可塑性プラスチック胴体)によって製造されています。このプロジェクト自体には、その下に多くのプロジェクトがあります(MECATESTERSなど、誘導溶接に焦点を当てています)。下部セクションは、溶接されたストリンガーとフレームを備えた下部胴体シェル、キャビンと貨物の床構造、および関連する内部要素とシステム要素で構成されます。
STUNNINGは、GKN Fokker(Papendrecht、Netherlands)と、主要パートナーであるDiehl Aviation(Laupheim、Germany)、Netherlands Aerospace Center(NLR; Amsterdam、Netherlands)、およびDelft University of Technology(TU Delft; Delft、Netherlands)が主導しています。このプロジェクトは、自動化された組み立てプロセス、熱可塑性プラスチックの製造と溶接の技術、統合された設計と製造の開発、および高度な電気システムアーキテクチャをさらに成熟させることを目的としています。
「私たちの業界への影響は2つあります。デモンストレーターの組み立てに適用する自動化のレベルと、部品を生産する持続可能な方法の開発です」と、GKNFokkerのプログラムマネージャーであるDr.BasVeldmanは述べています。
2020年2月に発行されたVeldmanの論文によると、胴体下部のモジュール式アセンブリは、生産時間を短縮するという目標を達成するための鍵です。胴体のメインスキンを製造するために、炭素繊維/熱可塑性プリプレグで作られた大きなプリフォームが、超音波またはレーザー加熱自動テープ敷設(ATL)マシンによって敷設されますが、その場で統合されません。詳細は、自動ファイバー配置(AFP)マシンによって作成されます。次に、ロボットがプリフォームをメスの圧密型に入れ、袋詰めした後、皮膚をオートクレーブに圧密します。 Veldmanによると、オートクレーブ外プロセスも調査されています。ストリンガーとフレームはスキンに溶接されます。
「当初、計画ではすべての部品を今年製造する予定でした」とベルドマン氏は言いますが、コロナウイルス関連の遅延のため、「現在は来年にも移行しています。しかし、航空機の座席やその他のコンポーネントを取り付けるために使用されるクリップ、ストラット、ブラケットなどの小さなプレス成形部品の多くを含め、現在完成している部品はかなりあります。持続可能な製造を強調し、Veldmanは、一部のクリップは、ECO-CLIPと呼ばれるClean Sky 2プロジェクトを通じて、デモンストレーターの他の部品から再利用された端材から製造されていると付け加えています。
2020年初頭から、長さ8メートルの上部シェルを製造するコンソーシアムには、エアバス、プレミアムエアロテック(ドイツ、アウグスブルク)が含まれます。これは、産業および構造設計のリーダーです。 DLR、スキンレイアップおよび溶接技術開発を担当。ストリンガーを製造しているAernnova(Vitoria-Gasteiz、スペイン)。
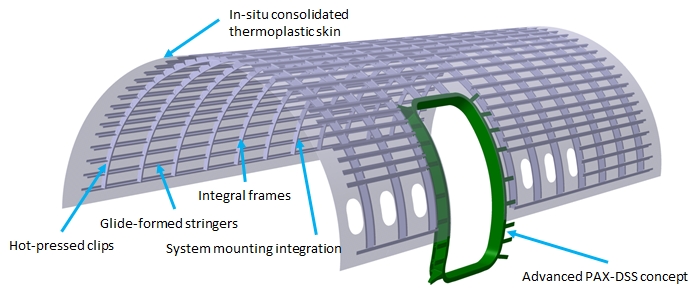
航空宇宙産業がより高価な熱可塑性材料に移行するためには、Larsen氏は「生産中にコストを節約できることを示さなければなりません」と述べています。上半分のコンソーシアムは、特に炭素繊維/ PAEKスキンレイアップの現場での圧密、およびストリンガー、フレーム、他のコンポーネント、安全性の向上とコストの削減。 DLRは、実物大のデモンストレーターが構築される前に、技術を検証するために最初に長さ1メートルのプレデモンストレーターテストシェルを構築し、2020年末までにプレデモンストレーターシェルのスキンを製造する予定です。ストリンガーは2021年初頭に予定されています。
両方の半分の実物大バージョンは、2021年末までに完成する予定です。完成すると、Fraunhofer Institute for Manufacturing Technology and Advanced Materials IFAM(Stade、ドイツ)の最終デモンストレーターに溶接されます。
>樹脂