モバイルサセプタを使用して熱可塑性誘導溶接を革新する
Institut de Soudure Group(IS Groupe、Villepinte、France)—文字通りフランスの「溶接研究所」—は、金属の溶接で100年以上の経験があり、現在、熱可塑性複合材料の溶接のリーダーとしての地位を確立しています。 CW で報告されているように の2018年の特集「溶接熱可塑性複合材料」、ISGroupeとその複合材料ブランド複合材料の完全性 エアバスTier1サプライヤーSTELIAAerospace(フランス、トゥールーズ)との「ArchesTP」デモンストレーションプロジェクトで、炭素繊維(CF)/ポリエーテルケトンケトン(PEKK)一方向(UD)テープストリンガーと胴体スキンを接合するために使用される「動的誘導溶接」プロセスを開発しました。 、2017年パリ航空ショーで発表されました。
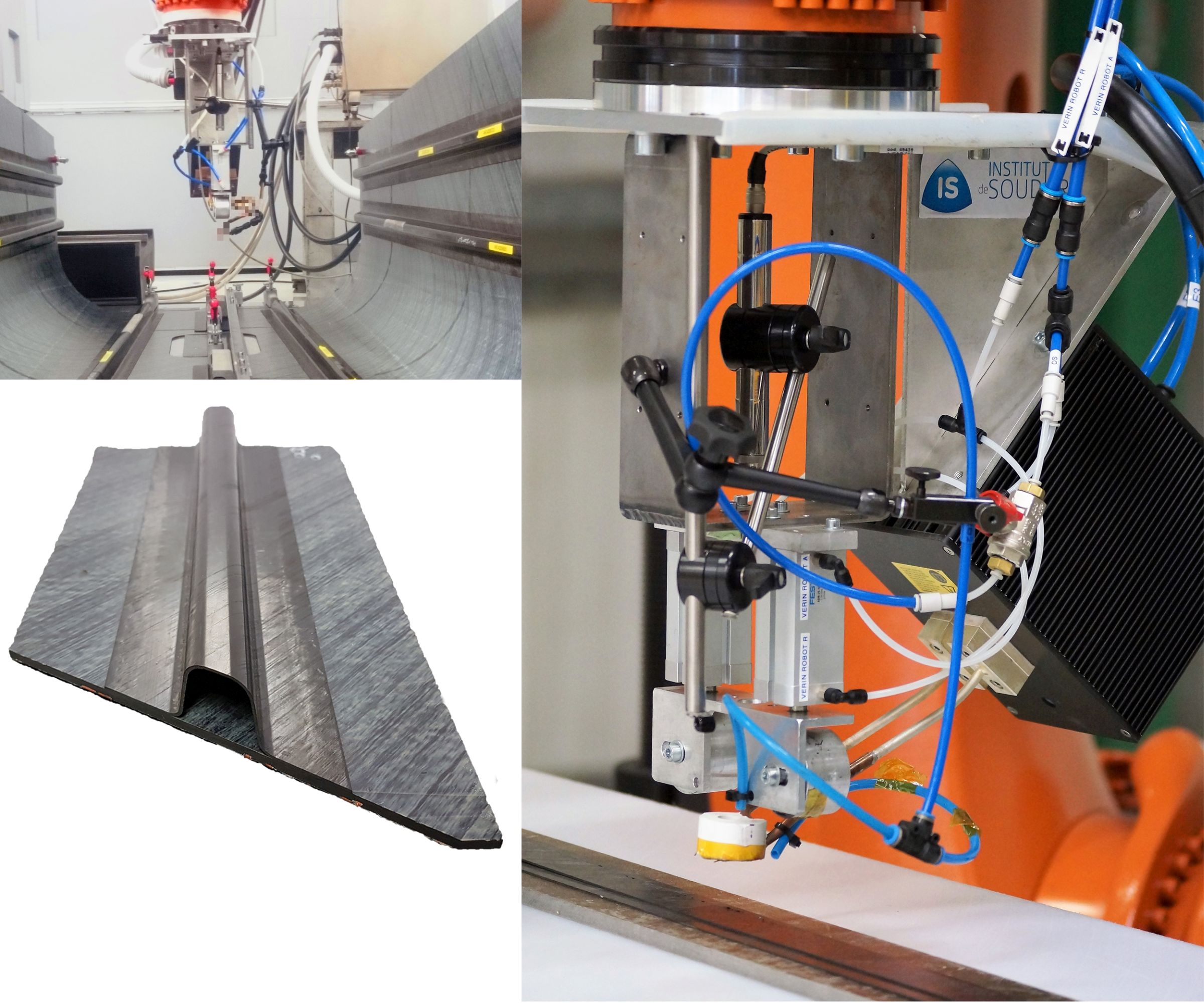
「これは、航空構造部品の誘導溶接による開発の始まりでした」と、ISGroupeの航空および複合材料ディレクターであるJérômeRaynalは説明します。 「私たちが開発した動的誘導溶接プロセスは成功しましたが、界面にサセプタがないため、結合ストリンガーの半径での性能とパネルの全体的な加熱に関していくつかの制限がありました。」
サセプタは、溶接ヘッドの誘導コイルによって加熱される、溶接された熱可塑性複合接合部の2つの被着体の間に配置される材料です。サセプタは、抵抗加熱の場合は導電性、ヒステリシス加熱の場合は磁気であり、溶接界面でマトリックスを溶融し、同時に一緒にプレスされて、非常に高い強度の融着接合を形成します。 2000年1月の論文「複合材料の誘導接合中の均一加熱のための抵抗性サセプタの設計」で説明されているように、ブルースフィンク、シュリダールヤラガッダ、ジョンW.スクリーンまたはメッシュ、ポリマーが含浸されている場合があります。
IS Groupeは、遭遇した最初の問題は、さらに開発することで解決できると信じていました。 「私たちは内部反射の新しいラウンドを始めました」とレイナルは言います。これには、開発パートナーシップに進んだ熱可塑性(TP)材料サプライヤーのアルケマ(フランス、コロンブ)との話し合いが含まれていました。 「私たちは今、溶接のための革新的なソリューション(ISW)と呼ばれるアルケマとの新しい技術を開発して共同特許を取得しました」とRaynalは付け加えます。
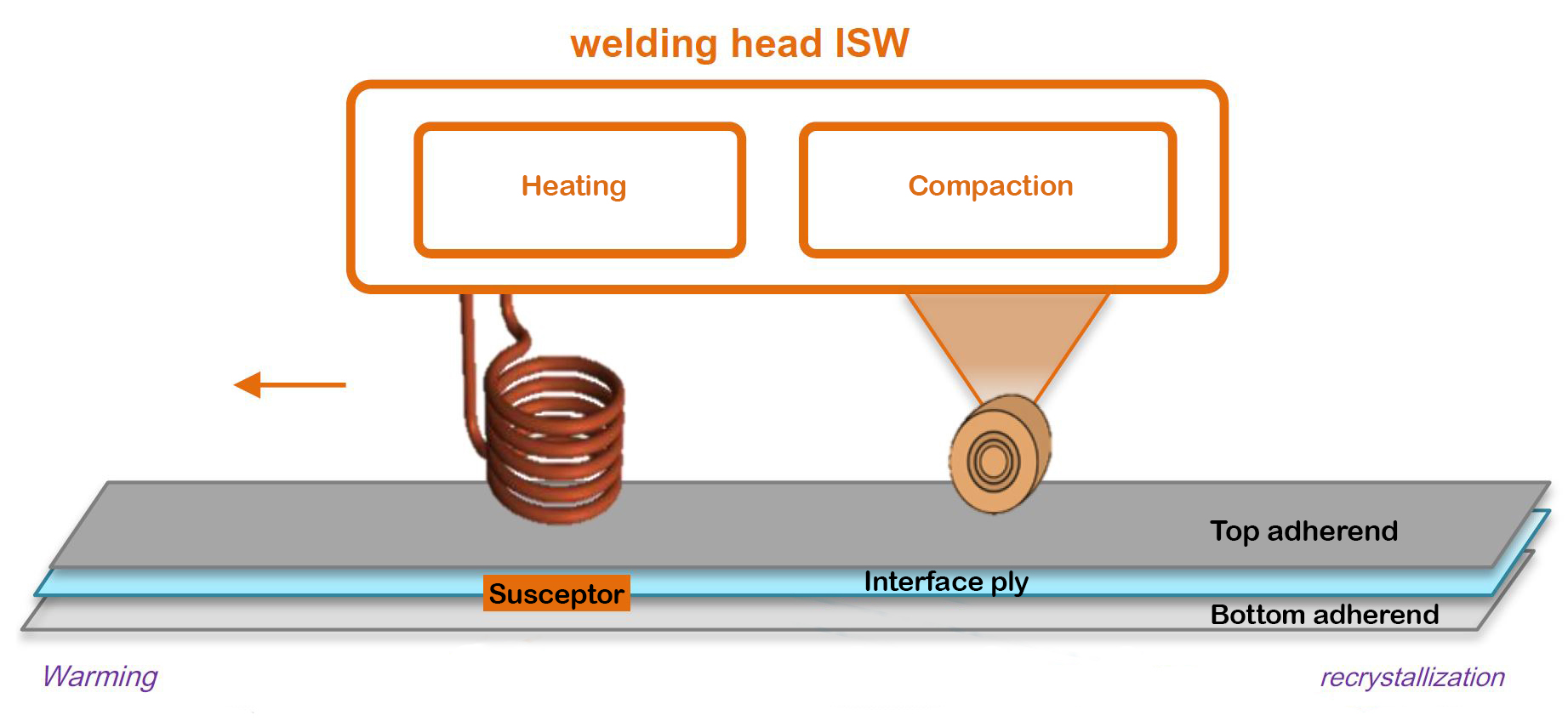
ISWの基本
「ISWの基本は、サセプタを使用して溶接インターフェースを加熱することですが、これは溶接ヘッドにリンクされたモバイルサセプタです」とRaynal氏は説明します。 「サセプタを使用すると、溶接部の加熱ゾーンを完全に特定できますが、サセプタを備えた溶接ヘッドが移動しているため、溶接構造の特性を妨げるものが界面に残っていません。」誘導溶接の初期の反復では、金属メッシュサセプタが溶接部に残っていましたが、これは望ましくないと見なされていました。一般的な航空宇宙ラミネートの炭素繊維は導電性であるため、最近の技術ではサセプタを排除することができました。これにより、サセプタとしての炭素繊維材料の使用も可能になりました。
ISWソリューションのもう1つの部分は、溶接界面で純粋なTPマトリックスまたは低繊維体積の層を使用して、樹脂の流れを増強することです。このインターフェースプライの溶融温度と粘度は調整可能であり、たとえば炭素繊維とアルミニウムまたは鋼の間のガルバニック腐食を防ぐために導電性または絶縁を提供するように機能化することもできます。
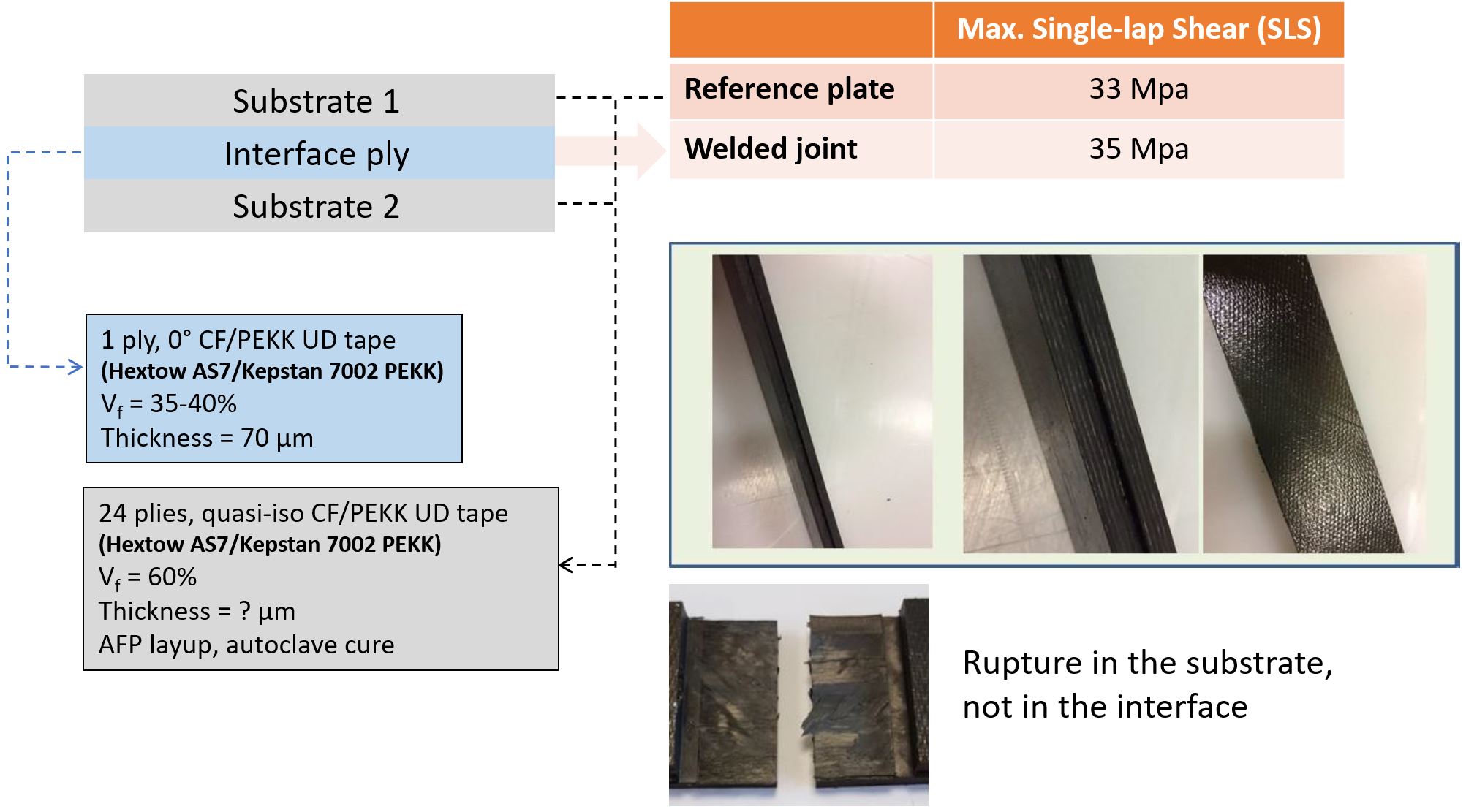
ISWの結果
「最終的には80〜90%の結合係数になります」とRaynal氏は言います。接合係数は溶接の強度に対応し、金属、プラスチック、複合材料で使用されます。 「ISWを使用して溶接された2つの事前圧密プレートのシングルラップせん断試験で、溶接されていないオートクレーブ圧密参照プレートの特性の80〜90%を達成しました。」これらの試験では、Hextow AS7カーボンファイバー(Hexcel、コネチカット州スタンフォード、米国)とArkema Kepstan 7002PEKKで作られたUDテープを使用しました。
Raynalによると、ISWは、PE、PA、PEKK、PEEKのほか、炭素、ガラス、またはアラミド繊維で強化された熱可塑性複合材料など、あらゆる種類のマトリックスの溶接に使用できます。 「また、航空構造物の生産の鍵となる落雷防止(LSP)用の銅メッシュを備えたコンポーネントを溶接することは問題がないことを示しました」と彼は付け加えます。 ISWは、溶接ヘッドを6軸ロボットアームに取り付けて完全に自動化するように設計されています。
温度制御
上記のKirk / Yarlagadda / Gillespieの論文で説明されているように、磁場にさらされる金属メッシュサセプタの一般的な問題は、溶接される部品に不均一な温度分布が生じることです。 「サセプタを使用して溶接界面のみを溶融することでこれを制御しています」とRaynal氏は説明します。 「実際にサセプタのエッジを側面から測定するレーザー高温計で温度を感知します。したがって、界面の温度を正確に知ることができます。また、冷却を使用して温度を管理し、溶接全体で熱可塑性材料の十分な結晶化を確保します。」
STELIAストリンガースキン溶接試験
エアバスのTier1サプライヤーであるSTELIA(フランス、トゥールーズ)は、この誘導溶接開発の最初の顧客の1つです。 IS GroupeとArkemaは、STELIAに対して、落雷保護(LSP)用の銅メッシュを備えた14プライのスキンに7プライのCF / PEKKストリンガーを溶接するための特定の調査を実施しました。最終的な目標は、長さ30メートルの構造物を、直線部分と二重曲線部分で溶接することです。コンポーネントは、Tenax HST45カーボンファイバー(帝人、大阪、日本)とKepstan 7002PEKKを含む194gsmUDテープを使用して作成されました。 STELIAは、オートクレーブで固められた参照材料の85%を超える機械的性能を持ち、被着体の熱的または機械的特性の低下がない均質溶接を指定しました。また、被着体の厚さの変化に対して堅牢なプロセスを要求しました。溶接部品の化学的および特性試験はISGroupeによって実施されました。
IS GroupeとArkemaは、STELIAの要件を満たすことができ、オートクレーブで固められた参照ラミネートと比較して、シングルラップせん断(SLS)および層間せん断強度(ILSS)のパフォーマンスの85%以上を達成しました。コンポーネントラミネートまたはLSPメッシュに開梱や劣化はありませんでした。彼らが足りなかった唯一の領域はスピードです。 STELIAは1メートル/分以上の溶接速度を要求しました。 「現在、私たちは毎分0.3メートル(10インチ)です」とレイナルは認めます。「しかし、私たちはその目標速度に向けて努力を続けています。」溶接できる基板の厚さに制限はありますか? 「航空宇宙構造物に典型的な厚さを溶接でき、5ミリメートルの厚さのコンポーネントを5ミリメートルの基板に溶接できます。」
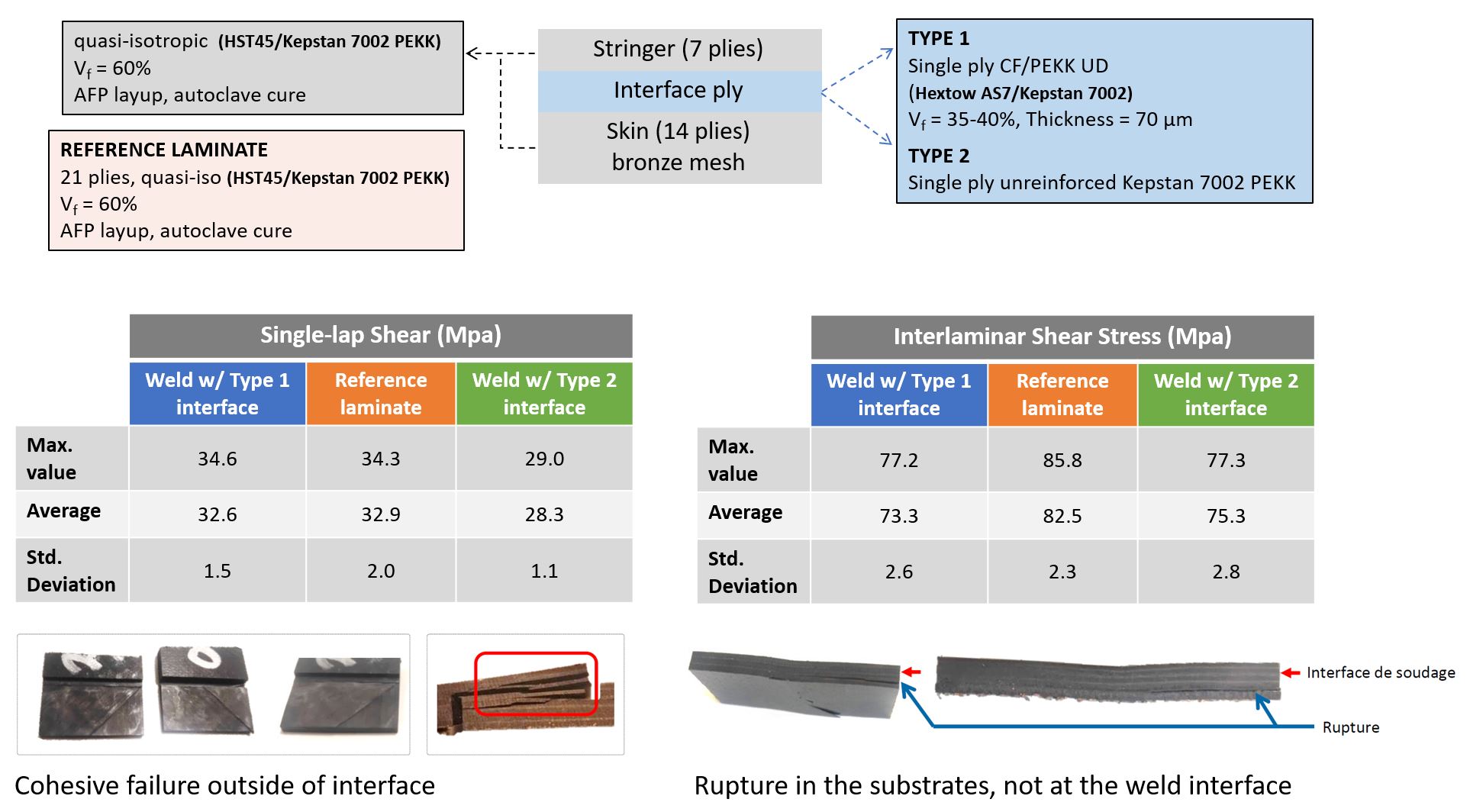
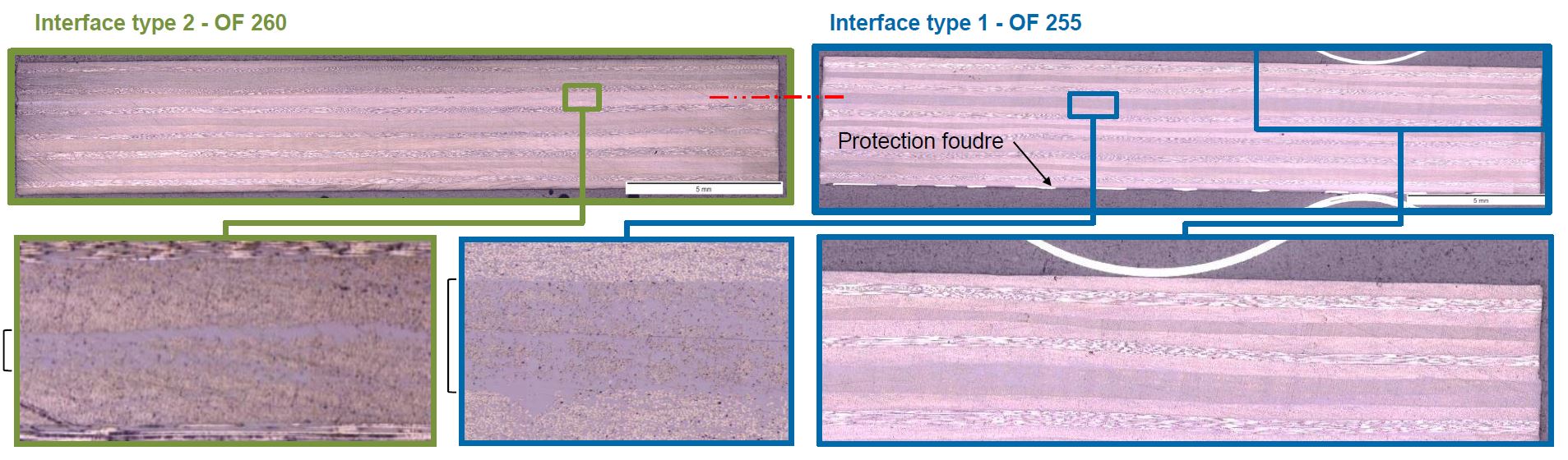
アルケマのパートナーシップ、機会、課題
なぜアルケマで働くのですか? 「テクノロジーと素材の間には関係があるからです」とレイナルは説明します。 「たとえば、界面の材料とその体積分率は違いを生みます。私たちはプロセスのスペシャリストですが、材料のパートナーと緊密に協力する必要がありました。この共同開発は、溶接技術を完全に最適化するために必要でした。」
IS GroupeとArkemaはISWテクノロジーの共同所有者であり、すでに5つのフランスおよび国際特許出願を含む強固な特許ポートフォリオによってこのテクノロジーを保護してきました。 ISWは、あらゆる熱可塑性複合マトリックスで使用できます。ISGroupeは、ラテコエールを含むヨーロッパと米国の企業とのプログラムを通じて、この技術を実証しています。 (フランス、トゥールーズ)、および Collins Aerospace Aerostructures (米国カリフォルニア州チュラビスタ)
アルケマの場合、焦点はPEKKにあり、将来の航空機用のCF /熱可塑性テープを開発するためのHexcelとの2018年の戦略的提携に注目し、顧客に低コストとより速い生産速度を提供することに焦点を当てています。このパートナーシップの一環として、フランスに共同研究開発ラボが設立されています。
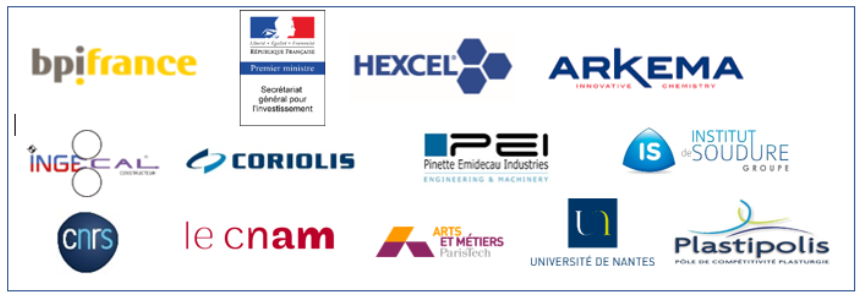
1,350万ユーロ、48か月の適応可能な構造を実行するための高度に自動化された統合複合材料 (HAICoPAS)プロジェクトは、アルケマとヘクセルの戦略的提携の継続です。この全フランスのコラボレーションには、IS Groupeのほか、カスタムマシンデザイナーのIngecal(Chassieu)、Coriolis Composites(Quéven)、Pinette Emidecau Industries(Chalon Sur Saone)、大学研究所のコンソーシアムが含まれます。 HAICoPASは、複合部品製造用の材料の設計と製造を最適化し、高速で競争力のあるコストを実現します。また、複合材料の配置/レイアップのためのより生産的な技術と、オンライン品質管理を使用した溶接によって最終部品を組み立てるための新しいシステムを開発することも目的としています。
対象となるアプリケーションには、航空機の一次構造、自動車産業向けの構造部品、石油およびガス産業向けのパイプラインが含まれます。熱可塑性材料によって提供されるリサイクル可能性と持続可能性の利点もこれらの市場にとって重要であり、HAICoPASで実証および定量化されます。
「ISWで提供できるメリットの1つは、電力を50%以上削減することです。 2017年からの動的誘導溶接プロセスと比較して必要です」とRaynal氏は指摘します。 「従来の誘導では、表面を加熱するために高出力が必要です。しかし、界面にサセプタがあると、加熱する表面がはるかに小さくなり、必要なエネルギーがはるかに少なくなります。」彼は、これがストリンガーの半径での圧縮解除を回避するのにも役立つと述べています。 「加熱しすぎると、半径内の材料を柔らかくして、ここの繊維を動かすことができます。したがって、半径を加熱せずに、溶接された基板の接触ゾーンのみを完全に加熱する必要があります。 ISWでは、これは問題ではありません。」
ただし、まだ熱の問題があります。 「フラットな形状の場合、熱制御は簡単ですが、形状が複雑になると、より困難になります」とRaynal氏は言います。 「2020年の主な目的は、開発を継続し、代表的な規模でストリンガーを皮膚に溶接することです。私たちの焦点は、この技術を新しい航空機開発プログラムに導入することでもあります。」
詳細については、JEC World 2020、ホール5、ブースN89でのCompositeIntegrityを参照してください。
樹脂