ハイブリッド金属-熱可塑性複合構造の自動接合
産業規模のハイブリッド参加を可能にする
FlexHyJoinは、プロジェクトのユースケースであるフィアットパンダのように、金属製のボディインホワイトに組み立てるための溶接金属ブラケットを備えた熱可塑性複合屋根補強材を製造するための大量生産プロセスを示しています。 シティカー。ソース| IVW
ハイブリッド金属複合構造は、自動車および航空宇宙用途で引き続き関心があり、「適切な材料を適切な場所に配置する」ことにより、軽量化とパフォーマンスの向上を実現します。熱可塑性複合材料(TPC)は、溶接や熱成形などの迅速な処理が可能なため、このようなマルチマテリアル構造に魅力的です。ただし、これまで、複合材料を金属に接合することは、主に機械的ファスナーに依存していました。これには、耐荷重性繊維に損傷を与えるドリル穴が必要です。接着剤による接着も使用されていますが、多くの熱可塑性プラスチックはこの方法で接着するのが困難です。また、接着剤は材料と重量を追加します。たとえば、BMW i3 は、炭素繊維強化プラスチック(CFRP)シャーシとプラスチックボディパネルを使用し、16 kgの接着剤を使用しており、複合材料の軽量化の可能性を部分的に打ち消しています。
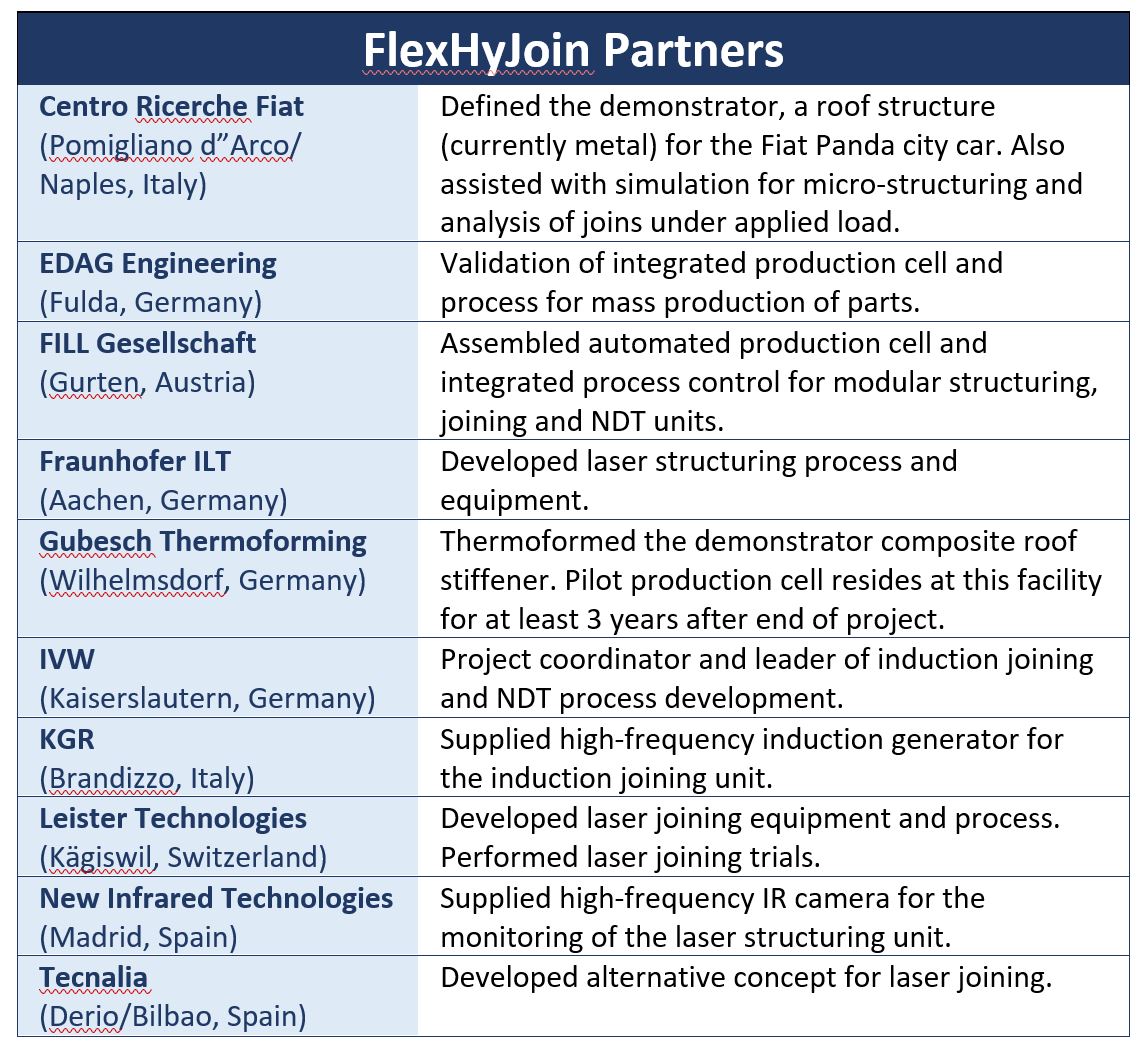
FlexHyJoinは、2015年10月から2018年12月に実施された、欧州連合のHorizon 2020研究およびイノベーションプログラムによって資金提供されたプロジェクトであり、TPCと金属部品の結合の課題に対処することを目的としています。ラインラントプファルツ州の非営利研究機関であるInstitutfürVerbundwerkstoffe(IVW)とドイツのカイザースラウテルン工科大学がコーディネートしたFlexHyJoinは、ヨーロッパ全土から10のパートナーを集めて、TPC自動車屋根を可能にする自動プロセスを開発しました。金属製のボディインホワイト(BIW)に組み立てられる構造。戦略は、金属ブラケットをレーザーで前処理し、誘導とレーザー接合を介してこれらを屋根補強材に取り付けることにより、接着剤や留め具なしで、重量に中立で高強度の接合を作成することでした。これは、統合されたプロセス制御とインライン非破壊検査(NDT)を備えた単一の自動化された生産セルで達成されました。
140秒でハイブリッドデモンストレーター
プロジェクトパートナーのCentroRicerche Fiat(ポミリアーノダルコ/ナポリ、イタリア)は、デモンストレーター部分(フィアットパンダの屋根補強材)の仕様を提供しました。 現在鋼で製造されているシティカー。 FlexHyJoinの場合、部品は、Bond-Laminates(Brilon、ドイツ)。このTPC屋根補強材をパンダに結合するために の鋼製BIW、厚さ0.7 mmのDC04鋼製のサイドブラケット(左右)のセットを両端にレーザー接合しました。同じ材料で作られたセンターブラケットは、誘導接合を使用して取り付けられました。 FlexHyJoinは、両方の接合方法が産業用ハイブリッド構造の製造に使用できることを示しました。
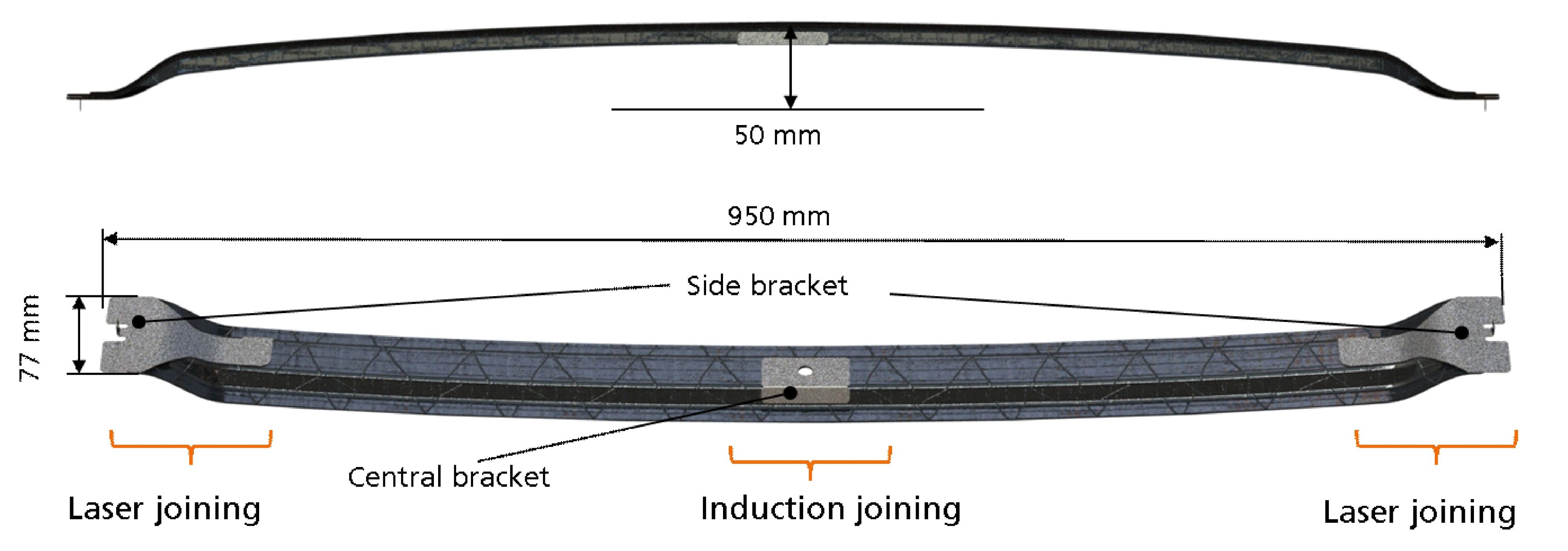
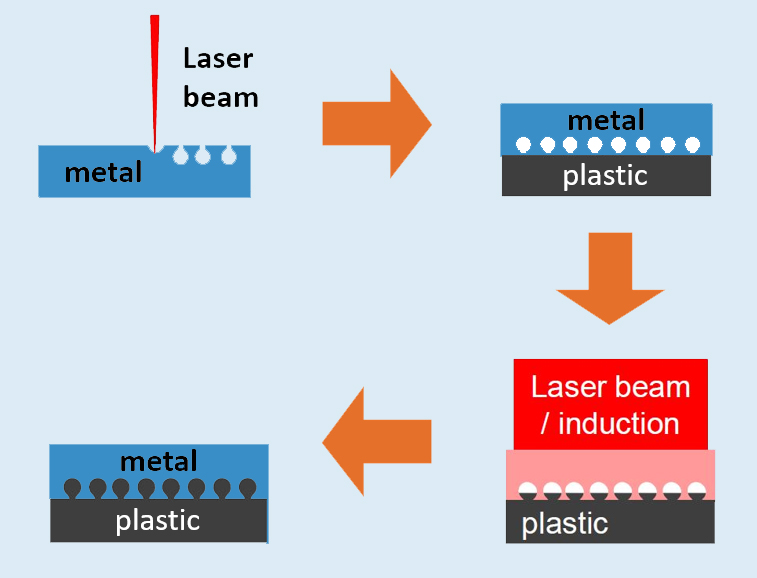
図。 1ハイブリッド結合の表面構造化
FlexHyJoinは、刻印されたGF / PA6屋根補強材( top )への鋼製ブラケットのレーザーおよび誘導接合を示しています。 )。これらのハイブリッドジョイントは、金属ブラケットの表面処理に依存してアンダーカットを作成します。アンダーカットは、接合プロセスのステップで溶融プラスチックで満たされます(下部 )。
ソース| IVW
PA6マトリックスをスチールブラケットに溶かすだけでは、構造要件を満たすのに十分な強度の結合は生成されません。したがって、接合前にレーザー表面処理が必要でした。 「ブラケットの表面は、アンダーカットを作成するためにレーザーで構造化されました」と、自動生産セルの組み立てと統合を担当したFill Gesellschaft(オーストリア、グルテン)のプロジェクトマネージャーであるJohannesVoithofer氏は説明します。 「処理されたブラケットは複合部品に配置されます。次に、接合中に熱と圧力が加えられ、複合材料からのPA6マトリックスがレーザー誘起アンダーカットに流れ込みます[図1を参照]。構造化プロセスは、さらに別のパートナーであるFraunhofer Institute for Laser Technology(ILT、アーヘン、ドイツ)によって開発され、材料の接着と機械的ロックを組み合わせた金属複合接合を実現しました。
次に、結合された部品はNDTステーションに転送され、そこでサーモグラフィのタイプを使用して欠陥がないかスキャンされます。 「ハロゲンスポットライトは、複合材料表面の変調加熱に使用されます」と、IVWのリサーチアソシエイトであり、FlexHyJoinNDTおよびプロセス制御の開発を主導するVitalijPopow氏は説明します。 「これにより、複合構造内で振動する温度場が発生します。時間の経過に伴う表面の熱応答を分析し、接合部の欠陥を特定します。」完全に自動化されたテストは、製造された各コンポーネントの生産セル内で完了します。プロセスの検証は、約400のジョイントで実行されました。
FlexHyJoin自動生産セルは、現在構成されているように、レーザー構造化、結合、およびNDTを、それぞれ81秒、98〜108秒、および100秒のサイクル時間で並行して実行します。これには、ステーション間の部品のロボット転送の時間が含まれません。 Voithoferによると、完成したハイブリッド部品あたりのサイクル時間は約140秒です。
図。 2産業規模のハイブリッド結合を可能にする
FlexHyJoinパイロット生産セルは、表面構造化、結合、およびNDT用の3つのモジュラーステーションを備えています。セルのシングルハンドリングロボットは、コンポーネントをローディングドロワーからこれらの各ステーションに転送し、完成したハイブリッドパーツを隣接するドロワーに配置します。ソース| IVWと塗りつぶし
レーザー構造化
レーザー構造化プロセスにより、金属ブラケットの接合面にアンダーカット形状のラインが生成されます。 FlexHyJoinの場合、アンダーカットの幅は75マイクロメートル、奥行きは215マイクロメートルでした。これらの測定値、およびラインの数とラインの全体的なパターンはすべて調整でき、理想的には、部品とサイクルタイムの要件を満たすように調整されます。
「接合面の微細構造の位置と数は、コンポーネントの負荷に合わせて調整できます」と、IVWのリサーチアソシエイトであり、FlexHyJoin誘導接合ユニットの開発チームのリーダーであるStefanWeidmannは説明します。 「微細構造間の距離は、接合面の高負荷領域では短縮でき、低負荷領域では増加できるため、効率的な微細構造化プロセスが可能になります。」
構造化は、IPG Photonics(Burbach、Germany)が提供する高出力のシングルモードファイバーレーザーを使用して金属ブラケットの表面をアブレーションすることによって実現されます。このYLR-1000-WCレーザーは、1,070ナノメートルの発光波長で1,000ワットの最大出力を備えています。 「集束性が高く、スポットサイズを約40マイクロメートルに維持できるため、マイクロストラクチャリングプロセスにシングルモードファイバーレーザーを使用しました」と、FraunhoferILTのポリマー加工のチームリーダーであるChristophEngelmann氏は説明します。
レーザーは、ABB1200ロボットアームに取り付けられた光学ヘッド内に含まれています。 「光学ヘッドの内部には、240ミリメートル×240ミリメートルの作業フィールドでビームを偏向させるための2つのガルバノミラーがあります」とエンゲルマン氏は説明します。 「さらに、z-height(z-shifter)を追跡するための可動レンズが1つあります。ロボットを使用してスキャンヘッドを金属部品の上に配置した後、ビームはミラーによって偏向され、微細構造の各単一ラインのz位置はzシフターによって調整されます。したがって、処理中にヘッドが動くことはありません。このようにして、2.5Dパーツを処理し、個別のラインごとに同じz位置を維持しながら、ライン間で調整することができます。」
「安全上の理由から、構造化ユニットと結合ユニットの両方が密閉されています」と、パイロット生産セルの黒いキャビネットに注目して、Voithoferは説明します(図2)。したがって、自動化されたゲート/ドアは、レーザー操作中は下げられたままであり、完成した部品の取り外しと新しい部品の挿入のために開きます。
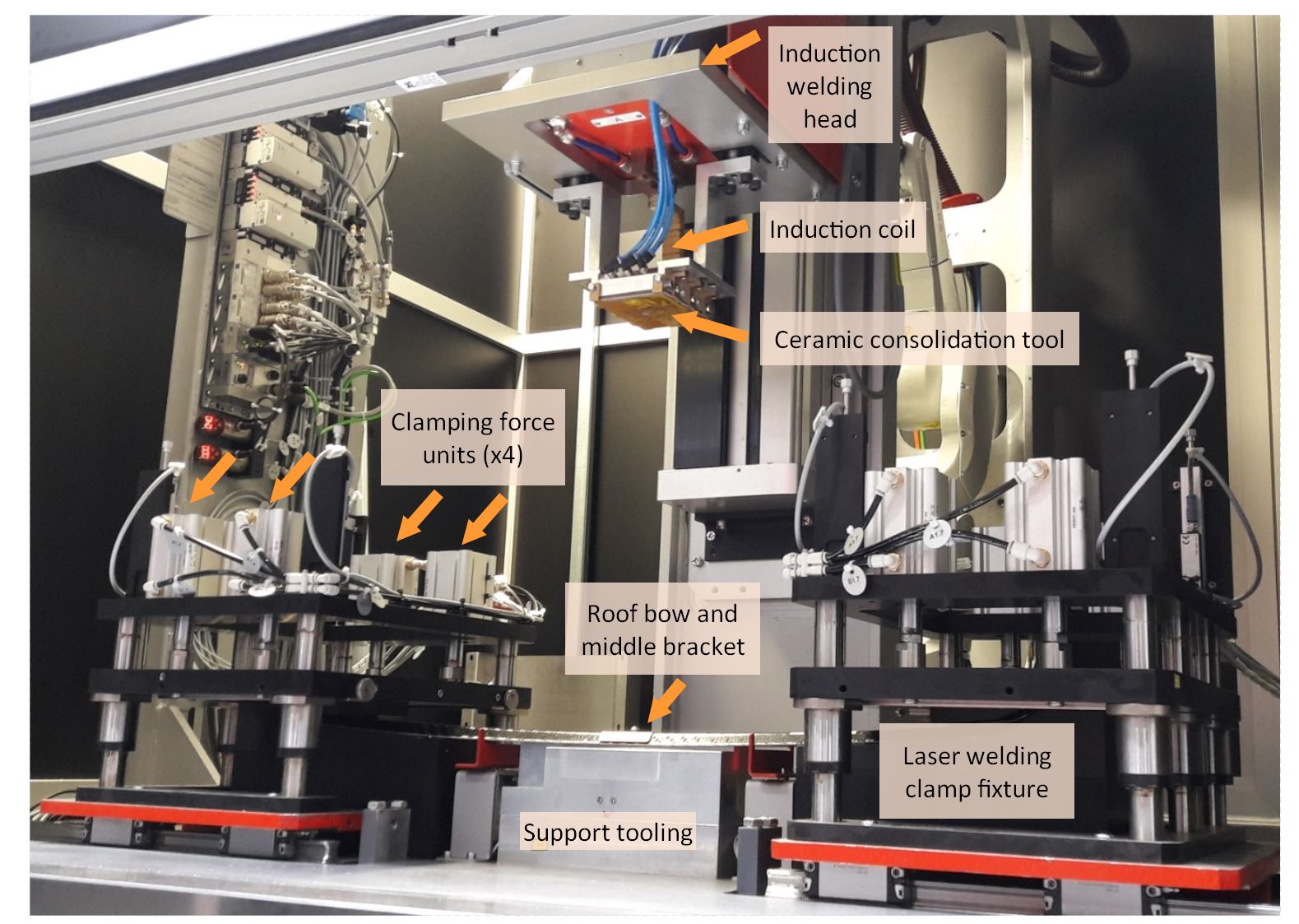
図。 3誘導およびレーザー結合セル
接合セルでは、誘導接合を使用して中央のブラケットを取り付け、レーザー接合を使用して複合ルーフボウの両端のサイドブラケットを接合します。ソース| IVWと塗りつぶし
誘導とレーザー接合
構造化セルに隣接するのは結合セルで、これは2つの異なる操作で構成されます。中央ブラケットの誘導結合と左右のサイドブラケットのレーザー結合です。 「センターブラケットのように中程度の複雑さを持つ大きな部品の場合、誘導接合がより適切な接合方法です」とWeidmannは言います。 「インダクターを備えたセラミック圧密ツールは、接合領域に圧力を加え、電磁界を透過するため、加熱のために金属ブラケットに効率的にエネルギーを入力できます。これはフラットな形状には便利ですが、サイドブラケットの形状などの複雑な形状にはさらに困難です。したがって、これらにはレーザー接合を使用する方が効果的でした。」 Weidmann氏は、「誘導接合は大きな部品と中程度の複雑さの部品に最適ですが、レーザー接合は高度な複雑さの部品に適しています」と付け加えています。
複合屋根補強材に開けられた穴は、熱成形された補強材の曲率に一致するように形作られた、サポートツールの上にそれを合わせます。センターブラケットのレーザーカット穴がルーフスティフナーに配置され、サイドブラケットはルーフスティフナーの端に一致する形状で位置合わせされます。
「中央のブラケットは不連続を使用して結合されました 誘導結合。 「これは本質的に準静的なプレス接合です」とWeidmannは言います。「これは単に静的なプロセスであり、1つの場所で面接合を実現しますが、複合材料の厚さがわずかに変化するため、z方向に動きがあります。 (誘導)接合中に加えられる圧密圧力に。」
誘導接合ユニットには、誘導コイルに交流電界を供給するためのKGR(Brandizzo、イタリア)高周波発生器が含まれています。ヘッドは電気モーターとスピンドルを介して移動し(図3)、セラミック圧密ツールが金属製ブラケットを押し下げます。圧密ツールの誘導コイルにより金属が加熱され、複合マトリックスが溶けて接合部が形成されます。 「圧力は暖房と冷房全体に適用されます」とWeidmann氏は述べています。
サイドブラケットのレーザー接合は、誘導接合と同時に開始されます。サポートツールの両側にある2つのクランプ装置は、サイドブラケットに4,000ニュートンのクランプ力を加えることができます。 「複合部品と金属部品の間のギャップを最小限に抑えるには、クランプが必要です」とVoithofer氏は説明します。 「これにより、関節のボイドが防止されます。」クランプ力が加えられると、レーザーヘッドが所定の位置に移動します。 Leister Technologies(Kägiswil、スイス)が提供するLineBeamダイオードレーザーを搭載しています。 LeisterのJohannesEckstaedtは、このレーザーの最大出力は980ナノメートルの発光波長で600ワットであると説明しています。ビームは光学レンズによって27ミリメートル×1ミリメートルの線に形成され、金属ブラケットに集束されます。レーザーヘッドはロボットアームに取り付けられており、成形されたブラケットの表面に沿って移動できます。 「ブラケットの各領域に異なる速度を設定して、均一な接合温度を実現し、熱応力を低減して最良の接合結果を実現します」とEckstaedt氏は述べています。
一般に、レーザー接合では、透過接合または熱伝導接合のいずれかを使用できます。レーザー透過接合の場合、接合される複合材料は、レーザーの選択された波長に対して透明でなければなりません。次に、レーザーは複合材料を通過し、ブラケットの金属表面に当たり、それを加熱します。ただし、屋根補強材の有機シートラミネートはレーザー透過性ではなかったため、この方法はFlexHyJoinデモンストレーターでは使用されませんでした。代わりに、熱伝導接合の代替方法が使用されました。これは、レーザーを金属表面に直接適用するだけで、金属ベース材料を介して複合材料に熱を伝導し、220〜300ºCでPA6マトリックスを溶融し、接合部を作成します。 「スチールブラケットの高い熱伝導率により、レーザー熱は急速に広がり、サイドブラケットを効率的に結合します」とVoithofer氏は言います。
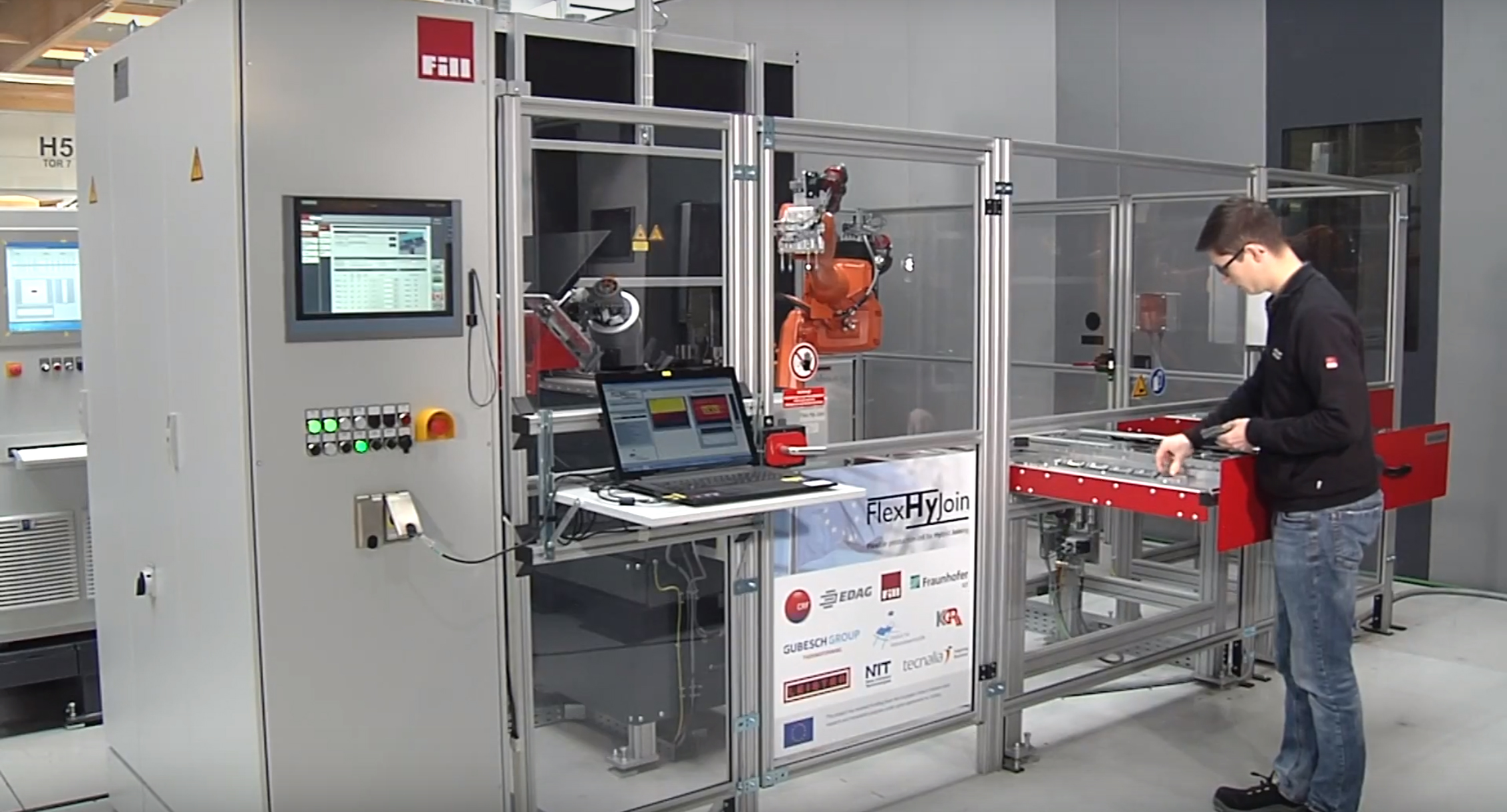
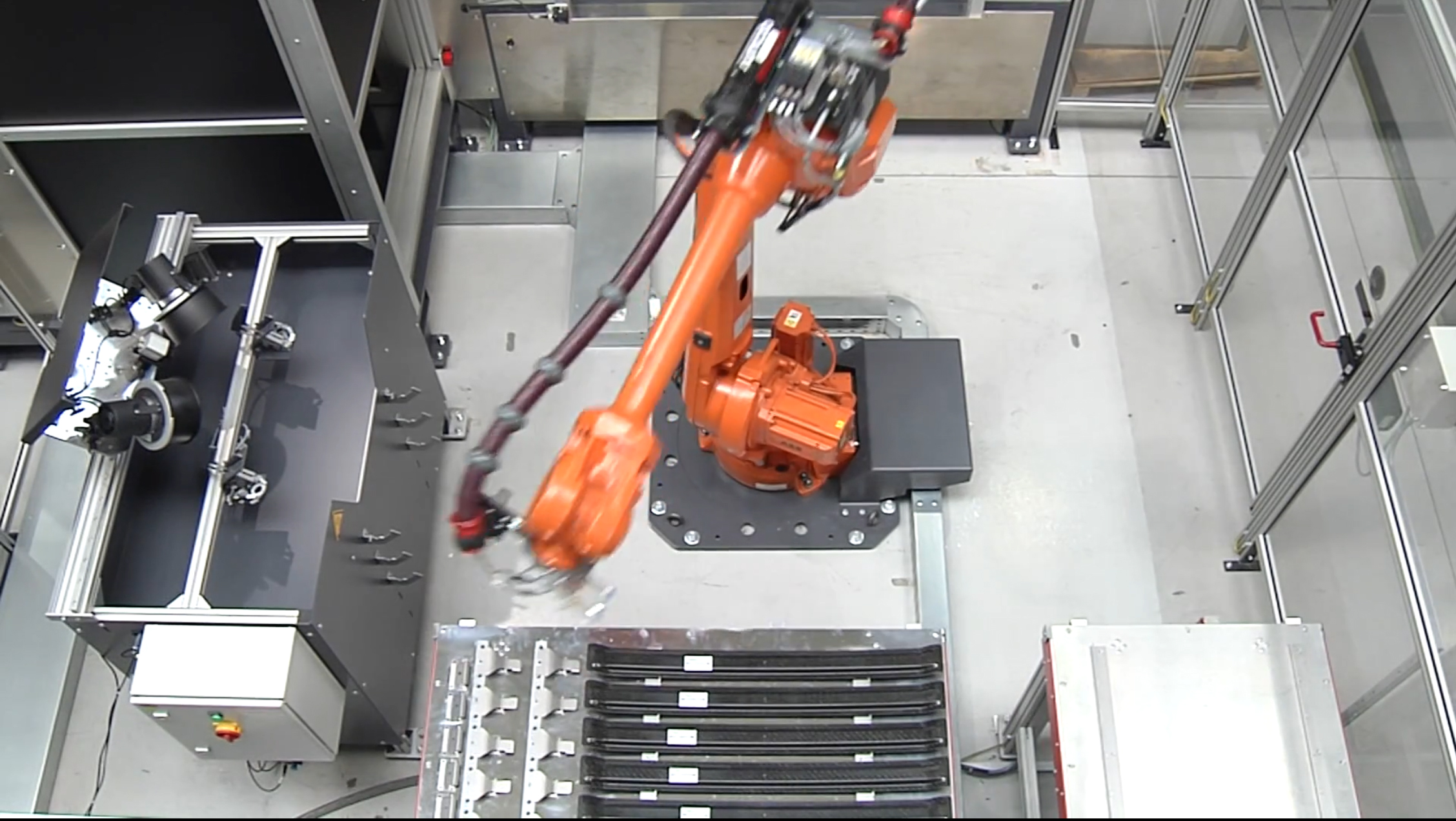
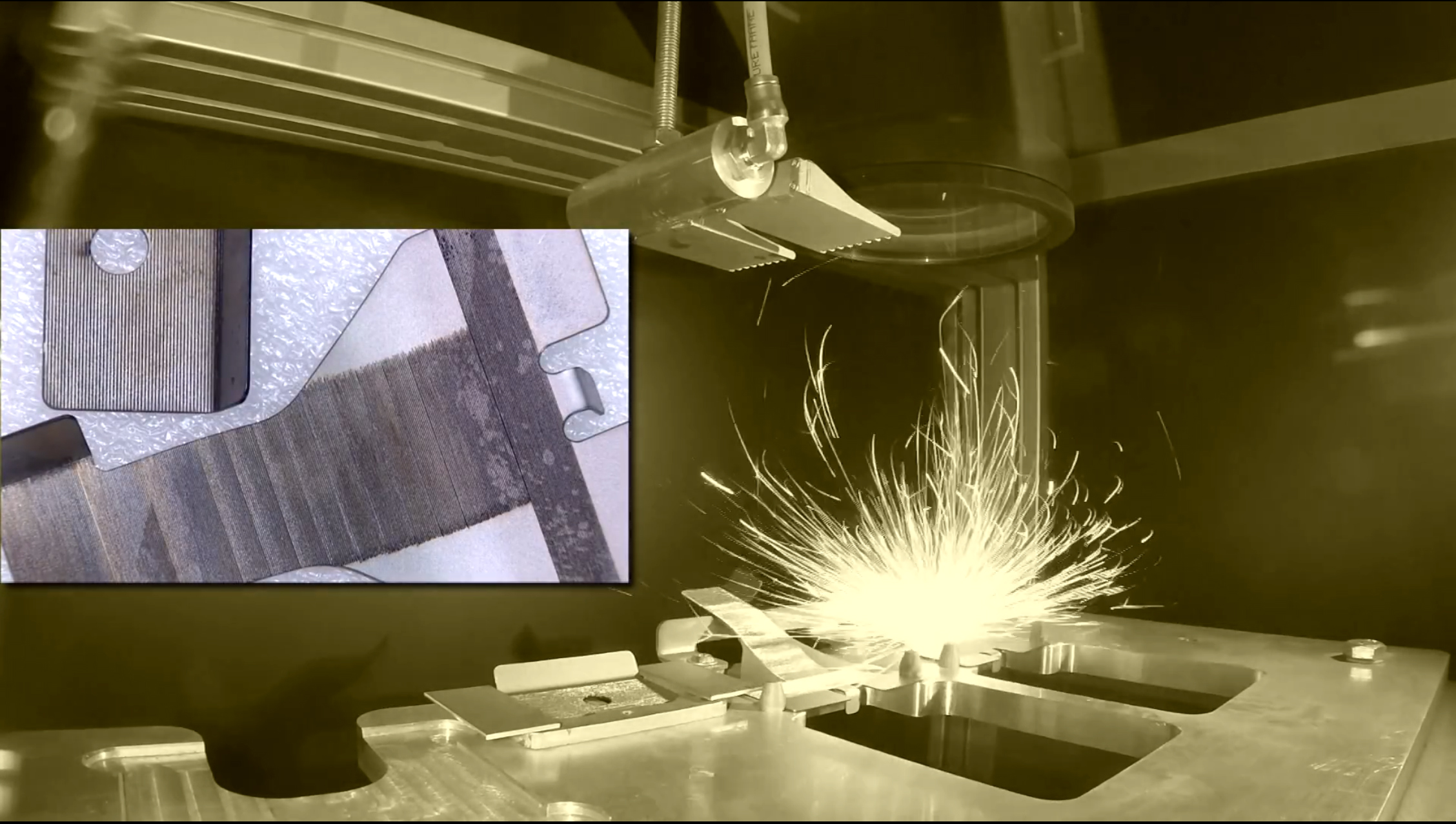
ステップ3。 構造化セルの内部では、高出力ファイバーレーザーがブラケットの表面にアンダーカットを作成し、複合屋根補強材で結合します。
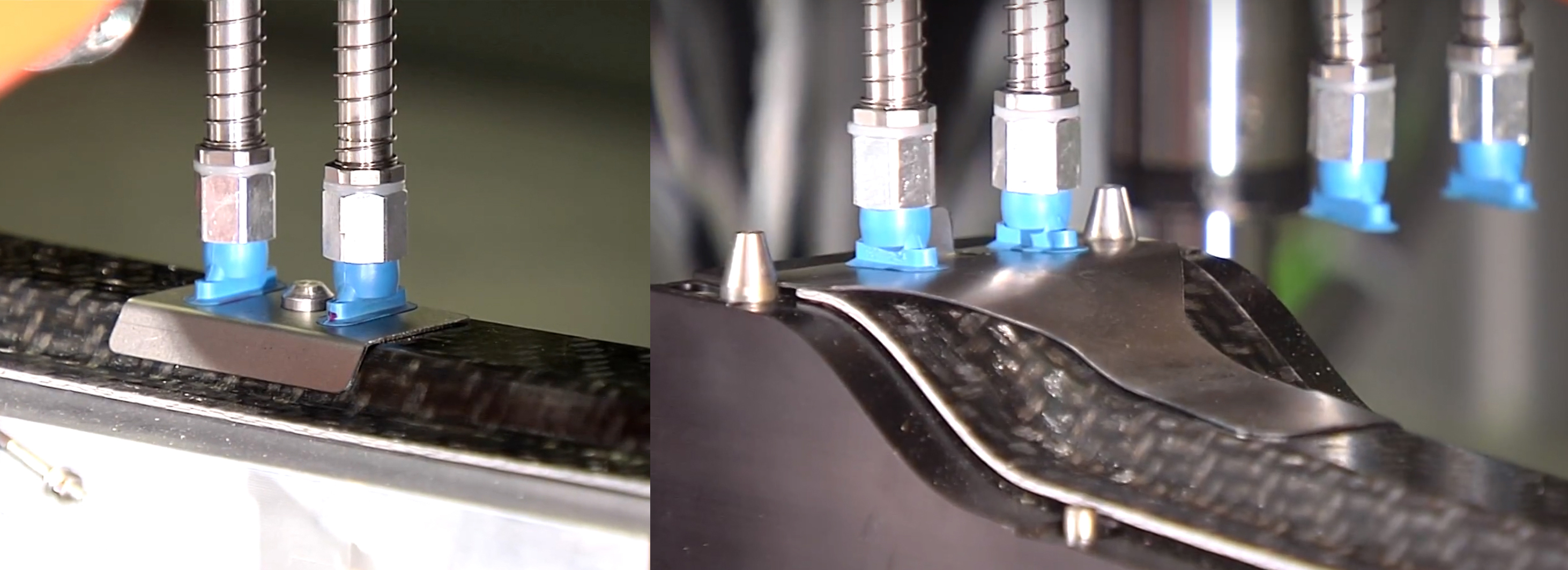
ステップ5。 ロボットは構造化セルに戻り、処理されたブラケットを持ち上げて、構造化された面を下にしてTPCルーフボウに配置します。
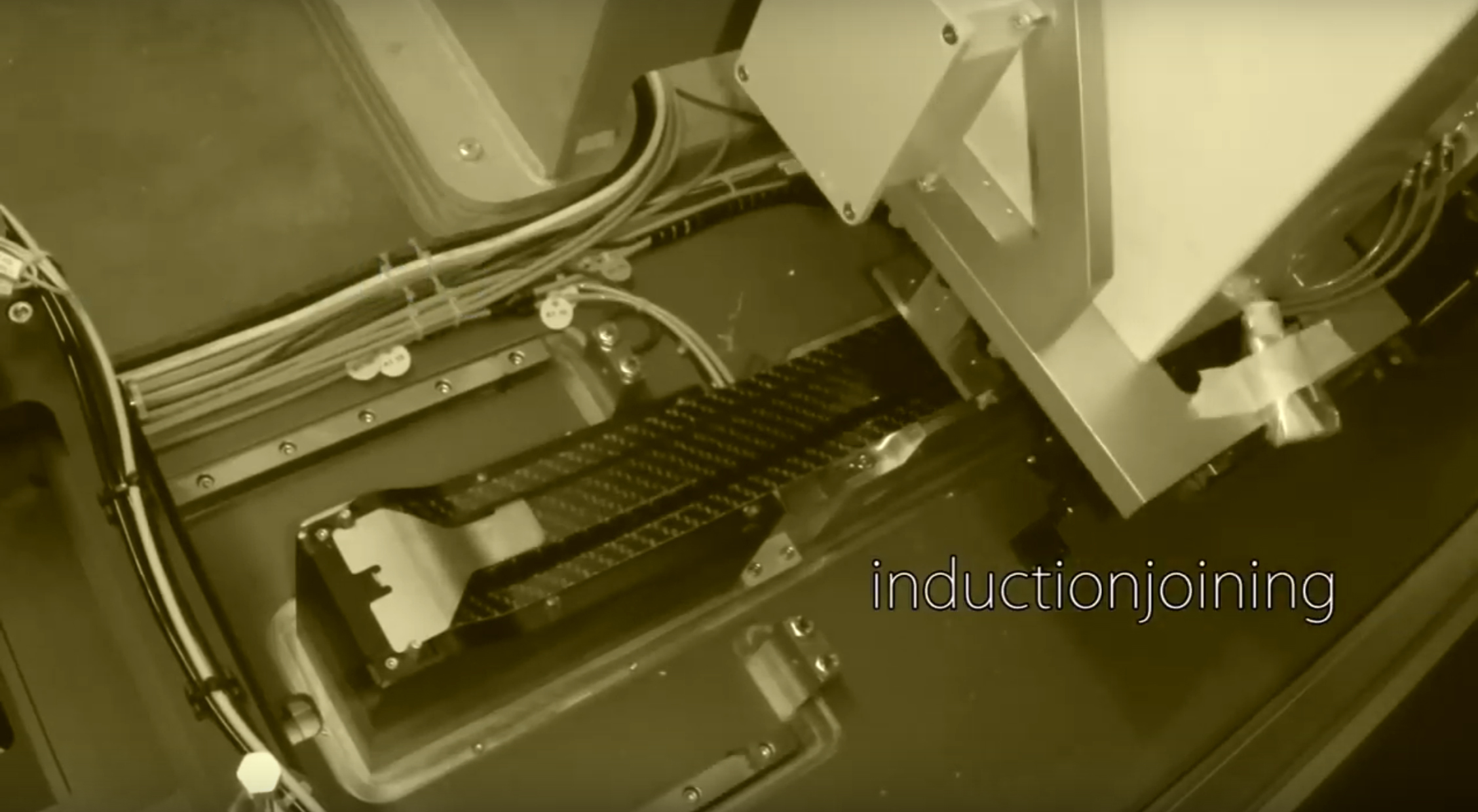
ステップ6。 次に、ロボットは3つのブラケットにクランプユニットを配置します。誘導結合ユニットがセンターブラケットに下がります。誘導コイルにより金属ブラケットが加熱され、下にある複合材のPA6マトリックスが溶けます。
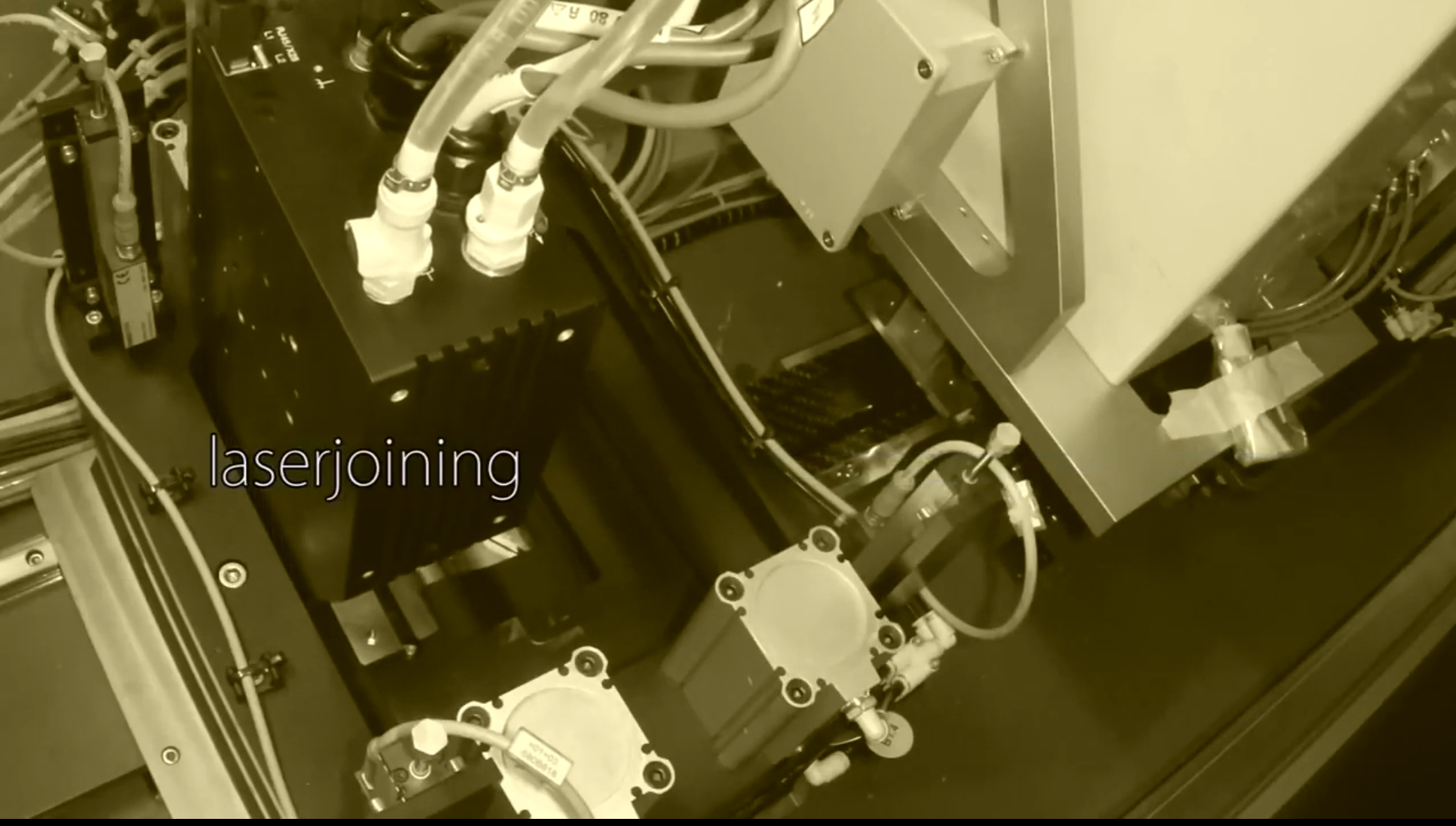
ステップ7。 誘導接合が完了すると、レーザー接合ユニットを下げて左側ブラケットと右側ブラケットを接合します。レーザーが金属を加熱し、下にあるPA6マトリックスをアンダーカットに溶かして、高強度の接合部を作成します。
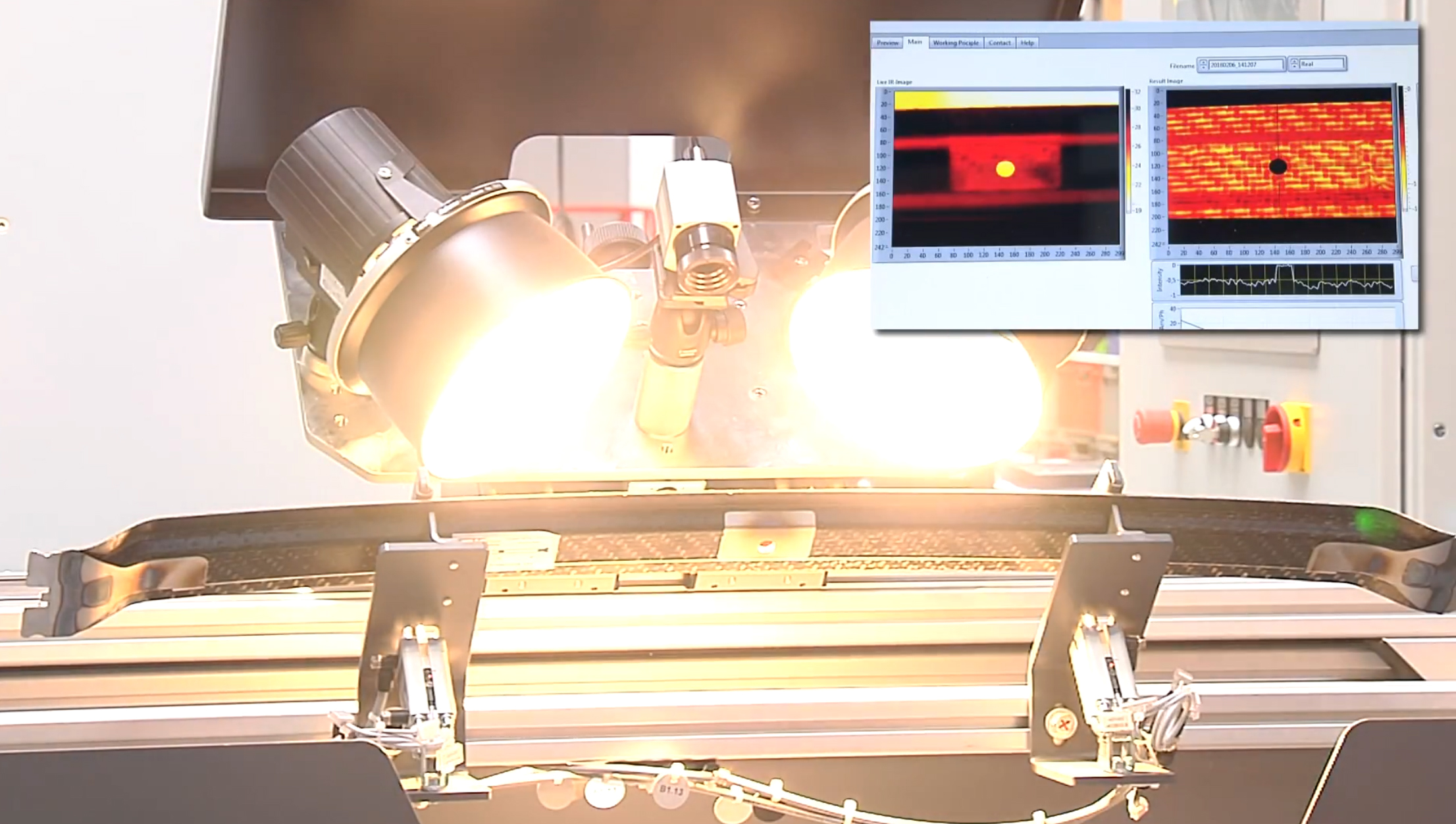
プロセス制御への参加
両方の結合プロセスを制御するための基本的な方法は、温度と時間を測定することと、テストを通じて定義された最適化されたパラメーターのセットを測定することです。 「したがって、さまざまなパラメータを使用して結合テストサンプルを作成し、特別なテスト設定を使用して各パラメータセットの機械的テストを実行しました。サイドブラケットについては、せん断試験と剥離試験の組み合わせを開発し、センターブラケットについては、重ねせん断試験に匹敵する圧力負荷試験を使用しましたが、せん断荷重を得るために、引っ張る代わりに押すと、参加エリアで」とPopow氏は言います。これらの特別なテストのセットアップは、テスト結果の分析も行ったEDAG Engineering GmbH(EDAG、フルダ、ドイツ)と共同で設計されました。この手順に従って、結合プロセスに最適なパラメータセットが特定され、パイロット生産セルで使用されました。
「誘導結合プロセスは事前に調整されています」とWeidmann氏は言います。 「約30秒後に接合部温度に達することはわかっていますが、過熱を避けるために安全上の理由からその場で温度も測定しています。」表面の放射を遠隔測定する高温計を使用して、誘導接合領域の既知のホットスポットを測定しました。 「しかし、高レベルの照射光とその場での熱のために、レーザー接合の正確な測定を提供することはできません」と彼は説明します。ただし、接触センサーはレーザー接合領域の複合側で使用できますが、通常は金属でできており、誘導によって加熱されて測定が歪むため、誘導接合プロセスには適用できませんでした。
「すべてのジョイントの加熱領域も、プレスツールとクランプ固定具で覆われています」とWeidmann氏は述べています。 「このように、品質保証方法として、接合前後の圧力と熱による部品の厚み変化を検証しました。」この厚さの変化は、ルーフスティフナーのポジショニングツールに統合された距離センサーによって測定されます(図3にも示されています)。 「部品を一緒に押すと、距離センサーが移動します」と彼は説明します。 「熱と接合圧力を加えると、溶融マトリックスポリマーはレーザー構造の空洞に流れ込み、接合部が冷えるまで接合ゾーンからわずかに押し出されます。これは、距離センサーによって記録される厚さの変化につながります。」 WeidmannとIVWチームは、この距離を部品の品質と関連付けました。 「厚さの変化、つまり圧縮が0.1ミリメートルを超えると、接合部の品質が良好になります」とWeidmann氏は述べています。
インラインNDT
IVWは、品質保証のための別の方法であるインラインサーモグラフィテストを開発しました。 「品質保証のために、主な目的は結合エリアのプロパティを確認することでした」とPopow氏は説明します。 「しかし、これは非常に困難だったので、パーツが完成した後、接合部の複合側でサーモグラフィを実行しました。」
IVWは、ロックインサーモグラフィと呼ばれるアクティブサーモグラフィ技術を選択しました。これは、他のアクティブな方法(パルス位相サーモグラフィなど)よりも優れた信号対雑音比を提供し、より深い欠陥を検査できるためです。 「基本的な考え方は、複合材料に熱を加え、それが接合領域に伝導して表面に戻ることです」とPopow氏は言います。 「ロックインサーモグラフィでは、コンポーネントは複数の にわたって定義された周波数で励起されます。 期間。次に、この応答を経時的に分析します。複合表面と接合領域の間に、ボイドまたは欠陥のために均一でない領域がある場合、それは熱応答に表示されます。」
熱応答は画像としてキャプチャされます。これらの画像を構成するドットはピクセルであり、画像要素の略です。各ピクセルは測定点でもあります。したがって、検査領域全体にわたる各ピクセルの温度信号が分析されます。 「その結果、各ピクセルの振幅と位相の情報が得られ、ソフトウェアはこれを画像に再構築して、視覚的に検査することができます」と彼は付け加えます。しかし、それはまた、テストされた126の部品の測定の大規模なセットを提供しました。 「これらのNDTの結果を、EDAGによって実行された機械的テストの結果と相関させました」とPopow氏は言います。彼のチームは、ブラケットを取り外した後、結合領域もテストしました。つまり、破壊的なテストです。 「このようにして、3セットのテスト結果を相関させ、サーモグラフィ結果の視覚的分析から低強度と高強度の結合領域を特定できるようになりました」と彼は言います。
大量生産用の統合セル
FlexHyJoinの最大の成果の1つは、それぞれが異なるプロジェクトパートナーによって開発されたすべてのテクノロジーユニットを、自動化された最適化された生産ラインに統合することです。フィルの機器を統合しているVoithoferは、次のように説明しています。さまざまなプロセスユニットをすべて制御するために、マスターPLCを考案する必要がありました。」これには、Fillから提供されたレーザーエンクロージャーとセルのハンドリングロボットが含まれていました。 「また、これらのプロセスステップは時間が異なるため、すべてを連携させることも非常に困難でした」と彼は付け加えます。
Voithoferは、各プロセスユニットとロボットのアーキテクチャを開発することから始め、これらを最適なフローに配置する方法を検討しました。 「私たちのコンセプトは、構造化、結合、NDTの3つのステーションを3つの別々のハウジングにモジュール式に保つことでした」と彼は言います。 「このようにして、単一のユニットを抽出し、見本市やその他のデモンストレーションプロジェクトで使用して、返却することができました。したがって、ワークセルはモジュール式でありながら統合されています。」
シリアルコンポジット生産のためのこのタイプのシステム統合におけるFillの数十年の経験は、PopowがFlexHyJoinの最大の偉業と見なしているもの、つまりラボスケールから産業スケールへの移行を達成するのに役立ちました。 「私たちは、金属に接合された複合材料の大量生産に適したこのようなプロセスを実現した最初のコンソーシアムです」と彼は言います。 「このプロセスは、スタビライザーリンク、バンパー、ドアなどの多くの自動車部品に使用できます」とVoithofer氏は述べています。 「軽量BIWの金属部品に接続する多くの複合部品があります。」
複数の業界への適応
ただし、セルを連続生産する前に、いくつかの変更が必要です。 「レーザーの構造化と結合を別々のエンクロージャーに保持するのではなく、それらを1つにまとめます」とVoithofer氏は言います。 「これにより、これらのプロセス間でエンクロージャーのドアを開閉する必要がなくなり、サイクルタイムが短縮されます。」彼はまた、すべてのステーションをコンベヤーベルト上で直線的に接続しました。したがって、ラインは継続的に稼働し、部品がピックアップされて各ステーションのコンベヤーに戻されてから、セルを出てBIWに組み立てられるようになります。これにより、サイクルタイムがさらに短縮されます。また、何百もの部品を供給することができる拡張された引き出しは、補給を必要とせずにラインがシフト全体を通過することを可能にします。
このパイロット生産セルは自動車産業を対象としていましたが、Popowは、航空宇宙、スポーツ/消費財、および産業用途に簡単に適応できると述べています。 「これは実際には主要なガイドラインの1つでした」と、Weidmann氏は言います。「さまざまな形状や部品を結合できる必要があります。唯一の変更点は、誘導接合圧縮ツール、レーザー接合用のクランプ固定具、およびサポート工具です。セルの主要部分は同じままである必要があります。」彼はまた、IVWがチタンと鋼の織物炭素繊維/ポリフェニレンサルファイド(PPS)有機シート複合材料へのハイブリッド接合を実証し、現在、ポリエーテルエーテルケトン(PEEK)とポリエーテルケトンケトン(PEKK)の実証を開発していると述べています。 「これには、接合プロセスを高温に適合させ、最適なプロセスパラメータを再定義する必要があります」とWeidmann氏は言います。 「セルは、アルミニウムや銅、およびポリプロピレンやポリエチレンなどの他の熱可塑性複合マトリックスシステムを含むさまざまな材料に開放されています。」
「プロジェクトパートナーは協力してきており、開発をさらに進めることに興奮しています」と彼は述べています。 「この種の生産は非常に有望であると考えており、これまでの業界からの回答は、この約束を認識しているさまざまな企業があることを示しています。」
樹脂
- ソルベイが熱可塑性複合材料の容量を拡大
- Ti0.91O2 / CdSハイブリッド球構造の光学特性の合成と研究
- メタ表面/グラフェンハイブリッド構造の表面インピーダンス
- フラウンホーファーは、熱可塑性複合材料の研究開発のために自動化されたエンゲル製造セルを委託しています
- 樹脂選択の重要性
- DLR Institute of Structures and Designは、熱可塑性複合材の胴体構造の成熟度を高めます
- 使いやすいキットにより、複合構造の内野修理が可能になります
- 革新的な堆積技術を使用した複合アイソグリッド構造の開発
- コンソーシアムは、炭素繊維熱可塑性複合構造のソリューションを対象としています
- 建築用クラッディングコンポジットが発表
- コンポジット+メタル:中空プロファイルハイブリッドテクノロジー