新技術がロボット溶接の成長を促進
溶接作業を自動化する適切な時期ですか?経験豊富な溶接工をどのくらい維持できるか心配ですか?スループットを向上させる必要がありますが、利用可能な労働力ではどうすればよいかわかりませんか?より丈夫な素材に挑戦?さまざまな技術的進歩により、溶接作業を自動化することでこれらの問題を比較的簡単に解決でき、驚くほど迅速な投資回収が可能です。
3 倍高速
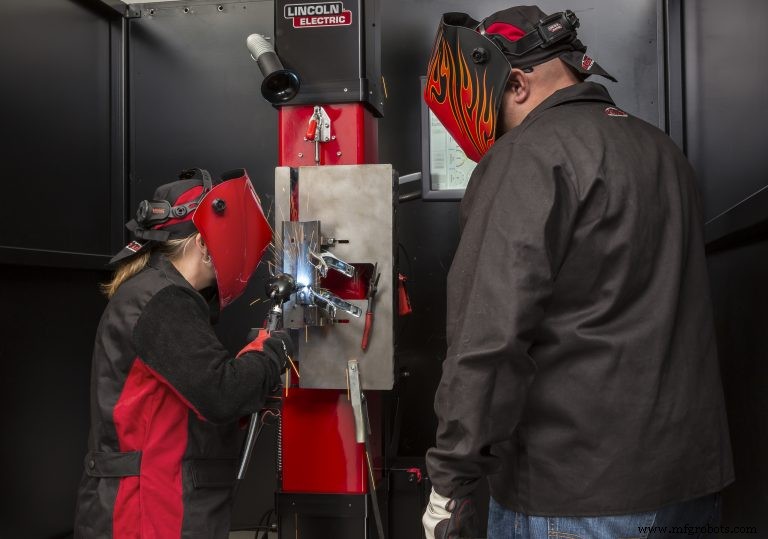
自動溶接には、いわゆる「固定」自動化と「柔軟」(またはロボット)溶接の 2 つの大きなカテゴリがあります。固定自動化は多くの場合、アプリケーションに固有であり、部品の形状と溶接が非常に単純な場合に最適です。たとえば、パイプの溶接には一般的に最適なソリューションです。しかし、ほとんどの産業用途や複雑なものには、ロボット溶接が理想的であり、この記事の焦点です.
Lincoln Electric Co. (Cleveland) のインサイド セールス マネージャーである Jason Lange 氏は次のように説明しています。第二に、溶接機の酷使を減らすことです。一日中部品を動かし、さまざまな備品の下を這うことは、人間に負担がかかります。ロボットは人間工学に役立ちます。」
溶接工を見つけるのが難しくなっているため、溶接工にとって簡単にすることは二重に重要です。 「そのギャップを埋めるために、溶接プログラムに投資している技術系の学校が全国にたくさんあります」と Lange 氏は続けました。 「しかし、ある日、退職者の数が次期補充者を上回り、空白が生じています。ロボット溶接は、その隙間を埋めるのに役立ちます。」
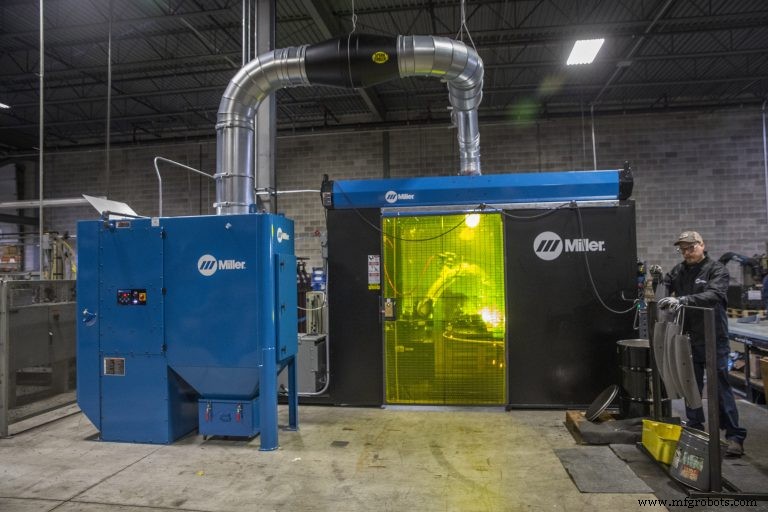
同時に、「ロボット システムの投資回収率は、一般的に想像以上に優れています」と、Miller Electric Mfg. Co. (アップルトン、ウィスコンシン州) のレーザー グループのビジネス開発マネージャーである Erik Miller 氏は説明しています。 「1 台のロボット システムで、3 人の溶接機と同じ数の部品を製造できます。シフトごとに 2 つの給与を節約でき、事前に設計されたセルの平均コストは 100,000 ドルから 120,000 ドルです。約1年で元が取れます。通常、プロセスを自動化して 1 年以内に回収できる場合は、すぐに実行できます。 2 年であれば、真剣に検討する必要があります。」
そのため、ロボットによる自動化は、スループットの向上に大きく役立ちます。しかし、この記事のためにインタビューした情報筋は、それは熟練労働者の代わりにはならないと強調しました。ランゲが言ったように、「そのロボットを動かすには、やはり優秀な溶接担当者が必要です。」
材料の変更も自動化の理由
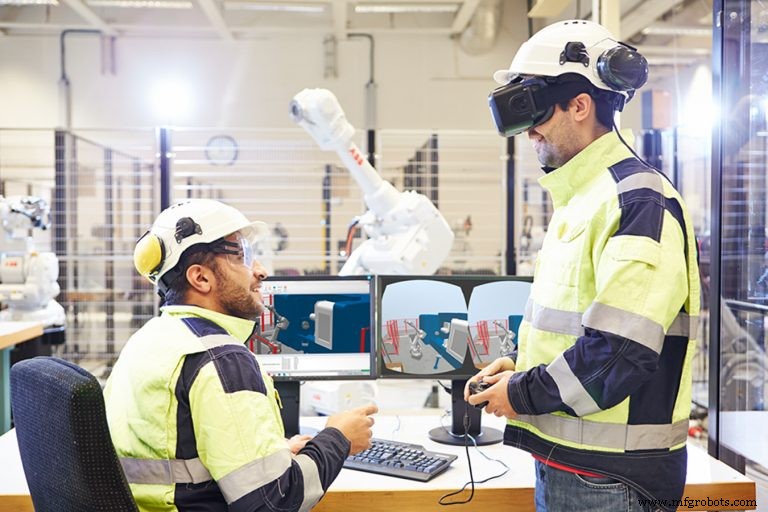
ABB ロボティクス (ミシガン州オーバーンヒルズ) の溶接および切断ビジネス ラインのディレクターであるアーウィン ディマランタ氏によると、過去 10 年間の被削材の変化により、溶接の改善が促進されました。その多くは、レーザー溶接など、手動で適用することは不可能です。 . 「鉱山用車両から自動車まで、あらゆるメーカーがさまざまな材料を使用して、コストと重量を削減し、さまざまなパワートレイン ソリューションに対応しています。 「自動車メーカーは、より強く、より軽く、より耐食性を高めながら、高い成形性と溶接性を備えた冶金特性を備えた、より高強度および超高強度の鋼に切り替えてきました。これにより、金属構造の設計、形成、組み立ての方法が劇的に変化しています。」メーカーは従来のプレス金型を使用してパーツの特徴をカットしていた可能性がありますが、現在はホット スタンプ プロセスと自動化されたレーザー技術を使用してパーツを形成およびカットしています。
「別の例は、より多くの用途のためにアルミニウムに切り替えることです」と DiMalanta 氏は述べています。 「クルマによっては、ボディの90%がアルミになっているかもしれません。導電率が高いため、アルミニウムをスポット溶接するにはより多くの電流が必要であり、電流は熱と同義です。それでも、ゲージ材料を薄くするつもりです。一部の車両では、材料の厚さは約 1 mm です。では、逆方向に進んでいるこれらのトレンドにどのように対処しますか?」
その答えは、アーク溶接の電子制御と機械制御の両方の技術の向上と、レーザー溶接の使用の増加です。アーク溶接について、DiMalanta 氏は次のように述べています。溶接プールへの材料の堆積は、カスタマイズされた波形で慎重に制御されます。」 Miller 氏は、このような特殊な波形が「部品への入熱を制御することで、歪みを減らし、溶接部の外観を改善することができる」と付け加えました。
彼はまた、Panasonic の Active Wire と呼ばれる機械的な方法を指摘しました。 「これは双方向のワイヤー送りで、ワイヤーが前方に送り出されてショートし、水たまりから逆戻りして、このミシンのような動作を 120 ヘルツで繰り返します。これにより、入熱量が減少し、スパッタも大幅に減少します。また、すべての溶接でのアーク ストライクの一貫性も向上します。アルミ溶接や薄板金属の溶接に非常に人気があります。」
コンポーネントが軽くなればなるほど、強度を維持しながら複雑な構造を可能にするために、より高度な材料が必要になると DiMalanta 氏は述べています。 「ロボットとその高度なソフトウェア システムは、これらの材料を処理するプロセスをロボットのパスに接続するのに役立ちます。」
有力なオプションであるレーザー溶接
多種多様な材料 (異種材料を含む) を超高速で溶接できるレーザーは、おそらくここ数十年で最も大きな溶接技術です。また、Trumpf Inc. (イリノイ州ホフマン エステート) のレーザー溶接の上級先端技術エンジニアである Masoud Harooni 氏は、次のように述べています。
「レーザー溶接システムは制御が簡単です」と Harooni 氏は続けます。 「1 つのパワーと 1 つの速度を選択します。調整したら、部品全体を少しスパッタで処理します。アーク溶接ではアークを維持する必要があり、溶接パラメータはトーチとワークピース間の距離の変化に敏感です。 [ワークピース] のさまざまな部分でより多くの電流が必要になったり、電流が少なくなったりするため、プロセスの安定性が低下します。最新のアーク溶接システムのフィードバック ループは非常に優れていますが、これらのシステムが実際に完全に調整されることはありません。レーザー溶接部品は、多くの場合研削が必要なアーク溶接部品よりも後処理がはるかに少なくて済みます。また、アーク溶接システムでは、スパッタの処理やノズルのクリーニングが必要になるという問題もあります。」
おそらくもっと重要なことは、レーザー溶接は、アーク溶接では亀裂や気孔が生じやすいアルミニウムやマグネシウムなどの材料でも、熱による損傷なしでより深い溶接を実現できることです。 Harooni 氏は、これは、レーザーが 1 平方センチメートルあたり 108 ワットの出力密度に達することができるためだと説明しました。これにより、ワークピースの金属が気化することによって作成された深い中空領域であるキーホールが生成されます。レーザー ビームが部品に沿って移動すると、この小さな鍵穴が溶融プールに囲まれ、背後の材料が固化します。
「部品に極端な熱を加えることなく、強力で深い溶接が得られます」と彼は言いました。 「アーク溶接には出力密度がないため、より深い溶接を達成する唯一の方法は入熱を増やすことです。入熱量が少なく歪みが少ない溶接部品の機械的特性は、入熱量が多い部品よりもはるかに優れています。」
Miller 氏は次のように述べています。板金メーカーは、レーザー溶接にも目を向けるべきです。真の利点は、中規模から少量の生産では困難な抵抗スポット溶接を置き換えることにあります。部品の上面と底面の両方にアクセスする必要があるため、固定が難しい場合がありますが、レーザー溶接では上面のみにアクセスする必要があるため、自動化が容易です。単純な固定光学系とともに、レーザー溶接用のペイロードの低いロボットを使用することもできます。」
2 つの電極を備えた大型ツールを運ぶ強力なアームを備えた大型ペイロード ロボットと比較して、メーカーはより安全な 8 kg ロボットを使用し、それにプロセス ヘッドを取り付け、抵抗スポット溶接を比較的簡単に自動化できるようになりました。
「レーザー溶接が有益な板金の他の分野は、箱の製造です」と彼は言いました。 「外観を美しくする必要があり、その後の金属仕上げをほとんどまたはまったく必要としない外側コーナー溶接は、私たちが多くの関心を集めている分野です。」
Miller 氏によると、レーザーは、アクセスが制限されている部品に対して優れたソリューションを提供します。レーザーは、溶接を行うために視線のみを必要としますが、アーク溶接アプリケーションでは、ロボットが部品内および部品の周りでかさばるトーチを動かさなければならず、これは非常に困難な場合があります。 「レーザー溶接では、ワークピースから 500 mm 離れていることがよくあります。光線銃を撃つようなものです。また、レーザーは加工速度がはるかに速く、部品への全体的な熱入力が少ないため、歪みが減少します。自己溶接に最適なツールです。」
Harooni 氏によると、レーザー溶接の欠点は、「コンポーネント間に実質的に隙間がないことを確認するか、レーザー溶接とワイヤー補助を組み合わせたフュージョン ラインを使用する必要があることです。隙間をカバーできます。しかし、レーザー溶接は非常に高速であるため、治具に追加投資する価値があります。たとえば、ロボット アーク溶接で 1 日に 50 個の部品を製造している場合、ロボット レーザー溶接では、同じ部品を 1 日に 300 個、500 個、さらには数千個製造できます。」
溶接自動化について
溶接自動化への取り組みは、これまでになく簡単になりました。まず、主力企業はオフライン セットアップ ソフトウェアを提供しており、PC 上で次の作業を非常にリアルにプログラムし、そのプログラムをロボットに転送して溶接を開始します。 ABB はバーチャル リアリティ技術を使用して、ユーザーがロボット溶接装置と「共同作業」できるようにしています。
「いわば文字通りロボットの首をつかんで、ひもにつないだ犬のようにロボットを向けることができます」と DiMalanta 氏は説明します。 「これは、ティーチ ペンダントを使用するよりもはるかに直感的です。」
第二に、これらのシステムは、ある部品から次の部品への位置の変化に自動的に適応し、溶接品質を監視するメカニズムを備えている可能性があります。
Miller Electric の製品スペシャリストである David Schaefer は次のように説明しています。 1 つは単純なタッチ センシングで、もう 1 つはスルー ザ アーク シーム トラッキングです。タッチ センシングを使用すると、ロボットが下降し、アーク溶接ワイヤを使用して部品をプローブできます。プログラムされた場所と実際の場所の間の差分をチェックして、基本的にそれ自体を再プログラムします。
「スルー ザ アーク シーム トラッキングでは、材料が十分に厚い場合はフィレット溶接やラップ溶接のようにジョイントを横切るときに、アンペア数の変化を検出し、ジョイント内にあるときと外れたときを判断します。そして、溶接中にその溶接をたどります」とシェーファー氏は続けました。 「ワイヤ タイプ センシングの代わりにレーザー光学を使用するオプションもありますが、基本的な考え方は同じです。」
Lincoln Electric の Lange 氏は次のように述べています。パーツの物理的な位置に基づいて、プログラムをオフセットし、ジョイントをオフセットできます。最近のカメラは、数年前のカメラほどグレアの影響を受けていません。彼らはより多くの色を認識し、パーツの定義を読み取って、パーツから影と反射を区別することができます。」 Harooni 氏は、「今日の光学系により、破壊試験を行うことなく溶接の品質をリアルタイムでチェックすることもできます」と付け加えました。
第 3 に、すべてのロボットがなんらかの形式の衝突検出を提供します。 Miller Electric の Miller 氏は、これがロボット アーム自体の最も重要な改善点であると述べています。 「以前は、顧客は既知のトーチの X-Y-Z 位置に基づいてプログラムを作成していました。ロボットがシフトの半分を溶接していて、オペレーターがクランプを開いたままにしているとしましょう。ロボットがクランプにぶつかり、トーチが曲がる可能性があります。トーチの端が曲がり、その位置が変わったため、プログラム内のすべての溶接がずれてしまいます。現在、ロボットが物体に衝突すると、たとえ高速であっても、結果として生じる電流スパイクが障害物として読み取られます。これにより、ロボットはすぐにフレックス サーボ モードになり、各軸に指定された特定の距離だけブレーキの適用が遅れます。ロボットは事実上「ぐったり」します。これにより、ロボットは運動量を消散させ、ツールへの損傷を最小限に抑えることができます。これは、トーチを曲げることなく高速衝突できることを意味します。」
4 つ目は、すべての主要なプレーヤーが、パレット (または複数) に必要なものすべてを備えた、事前に設計されたロボット セルを提供していることです。 「作業セルは、すべての安全装置を備えた完全に設計されたユニットです」と Lange 氏は言います。 「フェンスやスチール製の壁、通常はセーフティ スキャナー、ライト、ロボットを動かすためのプッシュ ボタン、キー インターロック、およびターンテーブルや観覧車など、ロボットの前にあるある種のポジショニング デバイスが見られます。これらのデバイスは、オペレータが反対側に追加の部品をロードしている間、部品を作業ゾーンに運びます。または、ロボットが処理する固定テーブルのみを使用することもできます。また、溶接電源、トーチ、および必要に応じてビットをクリーニングするためのリーマーもいくつかあります。電気とガス源に接続するだけです。」また、既製のソリューションのいずれかが機能しない場合は、カスタマイズされたターンキー ソリューションを利用できます。
では、何を心配する必要がありますか?
Miller Electric の Schaefer 氏は次のように説明しています。 「レーザーと CNC 機器を使用して材料を曲げたり、ブレーキをかけたり、切断したりする場合、手作業で切断したりチョップ ソーを使用したりするよりも、ロボットによる溶接の方がはるかにうまくいくでしょう。部品を手作業で溶接する場合、溶接工はそれに応じて調整できますが、ロボットは調整できないため、これらのショップは今では問題なく使用できます。」 Miller 氏は、上流のプロセスが最初に正確でなければならないため、通常、溶接は施設で最後に自動化されるものであると付け加えました。 「パーツは正確にカットしてから、正確に曲げる必要があります。その後、それらを溶接できます」と彼は言いました.
Schaefer 氏が説明したように、パーツが再現可能であることを保証するだけでなく、ギャップを制限または排除する固定具が必要です。人間のオペレーターはギャップを見て、それに応じて反応することができます。通常、アンペア数を減らすためにワイヤの突き出しを増やし、熱と浸透を減らし、織り始めてギャップを埋めます。ロボットはこれをしません。燃え尽きてしまいます。」
逆に、一部の顧客は部品を保持するためのツールに数千ドルから数十万ドルを費やしていると、上流工程を改善することで価格を半減できる場合もあると Lange 氏は述べています。これにより、必要な再現性がダウンストリームで提供され、最終的に工具のコストが削減され、再加工とスクラップの量が減少します。
部品の品質と再現性の次に重要な関心事は、「関連する溶接プロセスを知り、理解すること」です。自分自身を溶接し、自動化されたデバイスを介して溶接します」と Lange 氏は述べています。
では、自動溶接を実行するために誰をトレーニングする必要がありますか?経験豊富な溶接工、または溶接 (数週間かかる) と溶接の自動化を学びたいと熱望している人のいずれかです。
Schaefer 氏は、「施設には適切な文化が必要です。仕事を持っている人は、自動化が施設に入ってくることに脅威を感じることがあります。会社の効率性を高め、成長させ、競争力を高め、最終的にはより多くの人を雇う方法について、従業員に率直に伝えたいと思います。」
最後に、バッチ サイズは自動化に十分な大きさでなければなりません。 Lange 氏は次のように述べています。パート 1 時間を変更している場合、ROI の効果はそれほど高くない可能性があります。」
自動制御システム