CAD/CAM プログラムにより、部品のオン/オフをより迅速かつ効率的に
ツールパスの改善、ジョブのセットアップ時間の短縮、デジタル ツール ライブラリとの統合、マシン シミュレーション、検証、分析ツールの改善に焦点を当てたソフトウェアの進歩
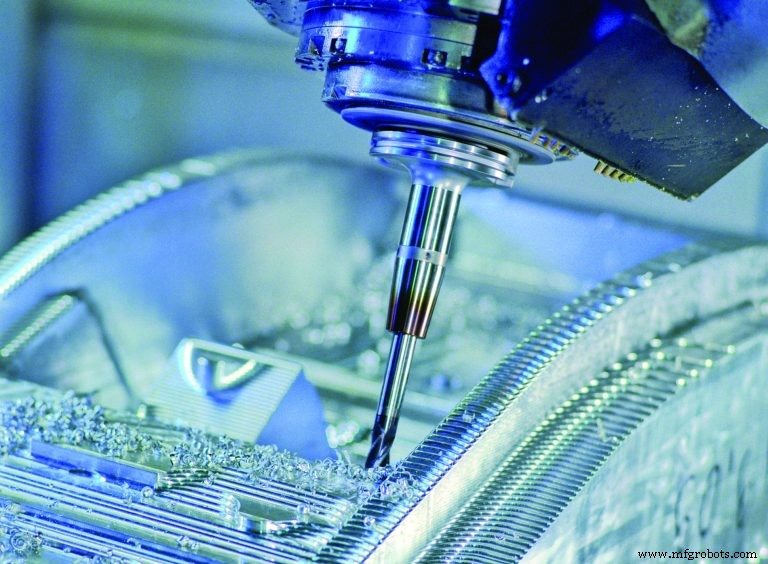
ほぼすべての CAD/CAM ベンダーに、何に重点を置いているかを尋ねてみると、5 年前も今も同じで、5 年後も同じだという答えが返ってきます。できるだけ早くマシンから取り出してください。これら 2 つの主な領域における現在の状況は次のとおりです。
近年、効率を高め、ジョブのセットアップ時間を短縮するために、CAD/CAM ソフトウェアにさまざまな変更が加えられています。しかし、「特効薬はありません」と、NX CAM、Siemens PLM Software (テキサス州プラノ) の製品開発担当ディレクターである Vyncent Paradise 氏は述べています。彼は自動化が最も重要な支援であると述べ、事前定義されたテンプレートの使用に加えて、CAD ファイル内の製品および製造情報 (PMI) の使用の増加を含めました.
「公差や仕上げ要件など、下流の CAM で使用できる CAD モデリング プロセスに、より多くの情報を常に追加しようとしています」と Paradise 氏は説明します。 「スマート デジタル モデルを読み取ることができれば、それを使用して、必要な公差に基づいて機械加工方法を自動的に選択できます。」
Open Mind Technologies USA (マサチューセッツ州ニーダム) のマネージング ディレクターである Alan Levine 氏は、ショップのベスト プラクティスを保存するマクロを使用して CAM プログラミングを自動化することの価値を繰り返しました。 「たとえば、さまざまなペッキング ステップとフィードを使用して、特定の方法で深い穴をあけたいとします。これらのプロセスをマクロとして簡単に保存できるようにしたため、プログラマーはこれらの手順を継続的に実行する必要がありません」と彼は言いました。 Open Mind のソフトウェアは、ユーザーがマクロを分類するのにも役立ち、マクロを簡単に見つけて適用できるようにします。また、プログラミング アシスタント モジュールは、ショップごとに異なる特定のセットアップ タスクを自動化しますが、ゼロ点をどこに設定するかなど、通常は特定のショップ内で標準化されています。
Open Mind の hyperMILL ソフトウェアの hyperCAD-S モジュールは、点、曲線、面、ソリッド、またはポリゴン メッシュを簡単に選択できるようにすることで、NC プログラマーの CAD 指向のタスクを高速化します。 Levine 氏によると、要素はすばやく追加、削除、変更、表示、または非表示にすることができ、すべての機能は NC プログラマーのタスクに合わせて調整されています。さらに、モジュールにはフィクスチャの配置が含まれており、ユーザーが作成しているパーツのどの側にも一致するように調整する機能を提供します。たとえば、クランプジョーなどの要素を直線的または放射状に最適な位置に移動できます。
同様に、Autodesk (カリフォルニア州サンラファエル) の PowerMill および FeatureCAM の製品マーケティング マネージャーである Mark Gadsden 氏は、FeatureCAM を使用するオペレーターは、機械を段階的にプログラムする必要がないことを指摘しました。代わりに、「回転」、「ボア」、「ボルト」などの日常的な用語を使用してプログラムします。そのような用語からニーズと要件を認識するのに十分なインテリジェンスを備えており、ラインごとに指示する必要なく、適切な速度とトルク強度を自動的に採用します。」
Gadsden 氏はまた、FeatureCAM の Directed Automated Feature Recognition (DAFR) 機能についても指摘しました。これは、「単一のワークフローで穴、ボス、側面、およびポケットを自動的に認識し、より高速なプログラミングを可能にします。標準の AFR は、アクティブな Z 軸でモデルをスライスし、モデルを下降するときに完全な機能を生成しますが、DAFR では、認識が始まる前であっても、ユーザーが必要な機能を選択できます。プログラミング時間を最小限に抑え、サイクル時間の短縮に役立ちます。慣習を破って、DAFR は旋削プロジェクトにも使用できます。これにより、ユーザーはインデックス角度を選択できます。これにより、必要な Z 軸の移動回数が減り、切断速度が向上します。」
3D Systems (サウスカロライナ州ロックヒル) のプロダクト マネージャーである Daniel Remenak 氏は、フライス加工を超えたプログラミング支援についても語っています。部品のすべての側面にアクセスするためのスピンドル、および同期と自動部品転送操作を支援することで、単一セットアップの完全自動加工を可能にします。同様に、GibbsCAM のトゥームストーン管理システムは、トゥームストーン治具の 1 つまたは複数のジョブの自動パーツ レイアウトを提供し、次のトゥームストーンがマシンの外でセットアップされている間、マシンをフルタイムで使用できるようにします。」
Mastercam ソフトウェアの開発者である CNC Software (Tolland, CT) のシニア マーケット アナリストである Ben Mund 氏は、ほとんどのショップがさまざまな顧客からさまざまな形式のパーツ ファイルを受け取っていることを指摘しました。 「そのため、私たちの焦点の大部分は、機械工が部品を準備してより速く機械に取り込めるように設計された CAD ツールを作成することにありました。穴埋め、固定具の作成、サーフェスやソリッドの修復などは、破損したり不完全になったりすることがよくあります。」 Mund 氏は、機械工は部品のモデリング時に設計者が考慮していなかった可能性がある状況に対処することが多いと付け加えました。これは、機械工に特化した CAD 機能を提供するもう 1 つの原動力です。
シミュレートまたは無視
3 次元マシニング シミュレーションは、プログラミングの大きな助けとなり、改善され続けています。ロボットによるローディングや引き戸のロゴなど、工作機械全体のシミュレーションを行います。機械加工の観点からは必要ないかもしれませんが、Mund が観察したように:
「オペレーターは、金属の塊に工具を通すつもりです。精度に対する彼らの信頼を高めるためにできることは何でも良い.これは、検証全体に自信を持たせるための優れた方法です。」彼は、複雑なマルチタスク マシンの場合、すべての詳細をシミュレートすることが重要になると付け加えました。そうしないと、プログラマーが衝突を予測して回避することが困難になるからです。
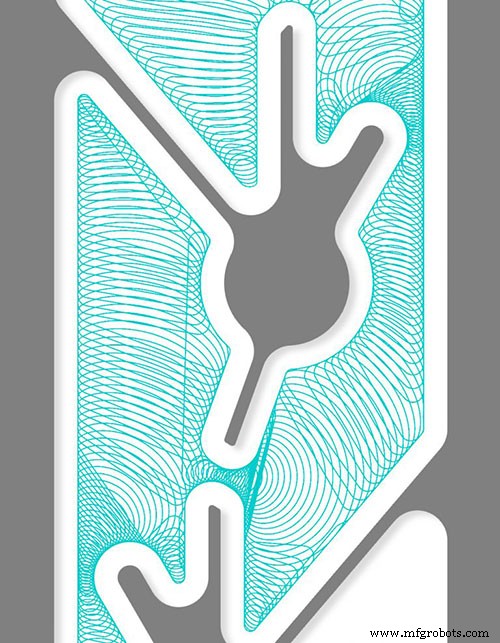
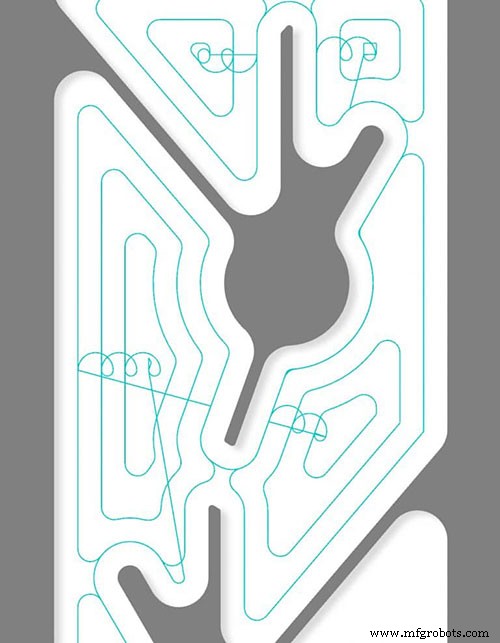
Remenak 氏は、CAM ベンダーがシミュレートする対象の範囲を拡大していることに同意しました。「プログラマーは、補間旋削、スレッド ワーリング、ポリゴン旋削、ブローチ加工、さらには付加的な金属堆積プロセスなど、新しいタイプの機械加工の正確なシミュレーションを求めているためです。」
シーメンス パラダイスは、「プログラマーが利用できるようにしたツールパスよりも、CAM システムの方が長い間、ツールパスについて多くのことを知っていました。しかし、ここ数年で、より多くのツールパス情報を表示するようになりました。」例としては、ツールの角度、残っている材料の厚さ、問題があるかどうかを示すこと、プログラマーをそのポイントに連れて行くことが含まれます。
「それはすべて非常に明白に聞こえますが、それは非常に新しいものです」と彼は指摘しました. 「これらのことは、何が起こっているのかを理解しようとしている、または優れた結果を得ようとしているプログラマーにとって非常に重要です。」また、自動衝突検出は CAM パッケージの一般的な属性でしたが、プログラマーがどこで、なぜその理由を見つけるのが常に簡単になるとは限りませんでした。パラダイスはそれが変化していると言いました。 「私たちは、より良い機械加工オペレーションを作成するのに役立つ、何が起こっているかについてより正確な情報をユーザーに提供しています。」
CNC ソフトウェアの Mund 氏は、モーションの色分けが役立つと付け加えました。 「速度と送り、動作の種類、使用されているツールの種類が一目でわかります。」彼は、最新の CAM は、検証用の幅広いツールパス分析ツールとプログラムが生成するものの両方を提供するというパラダイスの見解に同意し、さらに、プログラマーが「動きの 1 つの部分を調べて、それを動かしている数字を確認できるようにする」分析ツールを提供します。人々がそれを必要とすることはあまり一般的ではありませんが、そうするときはそれを持っていることが重要です。」
逆に、物事をそのまま表示しない方がよい場合もあります。 Mund 氏によると、CAD から CAM への移行は、加工を容易にするために、パーツ コーナーの R などのフィーチャを一時的に抑制する機能を機械工に与えることで支援できるとのことです。
Paradise 氏によると、CAD モデルの詳細を減らしながら、その領域のフィーチャを機械加工するよう CAM プログラムに指示することが役立つ場合もあります。 「モデリングの時間を節約できます。ファイルサイズを節約します。そして、CAM を自動化します。すべて同じプロセスで。」この最後の例は、Autodesk と同様に、Siemens PLM が NX を備えた完全な CAD/CAM パッケージを提供していることを思い出させてくれます。
最後に、Paradise は、すべての CAM シミュレーションが同じように正確でシームレスであるとは限らないと主張しました。 「工作機械に送られる最終的な G コードを使用して、NX CAM 内でシミュレーションを実行します。後処理はシステムに組み込まれています。そのため、パスをプログラミングするとすぐにシステムが G コードを生成し、その G コードを使用してシミュレーションを実行します。」
Paradise 氏によると、ほとんどの CAD/CAM パッケージは、加工シミュレーションにサードパーティ製品を使用しています。 「ポストプロセッサーから G コードをエクスポートし、別のシステムにインポートする必要があります。また、そのシステムで機械モデル、ワーク保持具、切削工具も複製する必要があります。次に、そこで G コード駆動のシミュレーションを実行します。また、設計の変更や問題が発生した場合は、CAM システムに戻って変更を加え、サイクルをやり直す必要があります。そのすべてを NX CAM 内でオンザフライで実行できる点で、私たちは他に類を見ません。」
パーツオフ
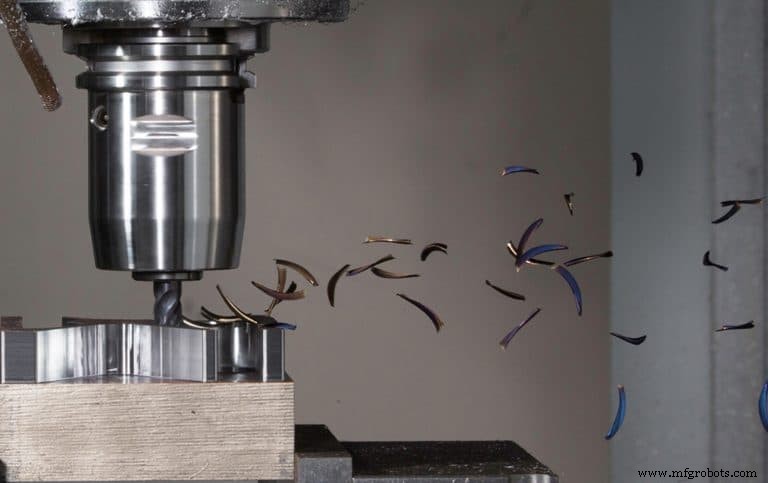
カッターの直前の材料の体積分析に基づいて最適な送り速度を自動的にプログラムする機能は、おそらく、サイクル タイムの短縮を推進する中で最もホットなトピックです。すべての CAM プロバイダーは、操作と軸構成のさまざまな名前とバリエーションで機能を提供しています。 Mund 氏が説明したように、ソフトウェアが「切りくずの負荷が一定に保たれるようにツールのエンゲージメントを絶えず変更している」ため、Mastercam ではダイナミック モーションと呼ばれています。
簡単な例としては、直線部分で速く進み、コーナーで減速するというものがあります。一方、切削をプログラムする古い方法では、ツールがコーナーで耐えられる送り速度を設定し、全周で同じ速度を適用します。
目標は、物理的に可能な限りワークピースとの関わりを維持することでもあり、部品のセクションを切断してから別の小さなセクションを切断するためにループを回す従来の荒加工およびトロコイド加工の両方とこの技術を区別します。上から見ると、Dynamic Motion のツールパスは比較すると無秩序に見えることがありますが、チップのサイズと形状は一貫しています。切断と再結合は工具の摩耗に寄与するため、カッターにとっても良いことです。
Mund 氏は、もう 1 つの理想は、工具の切削面をできるだけ多く使用して、軸方向に深い切削を行うことであると付け加えました。直感に反するように思えますが、一連の深いラジアル カットをステップ ダウンするよりも、浅いラジアル エンゲージメントでより深いアキシャル カットを行う方がはるかに高速です。」
Mund 氏は、ほとんどの CAD/CAM パッケージに同様の技術があることを認め、「ここ数年で複雑な荒加工と 2D 仕上げの両方の標準的な方法になりました。普遍的に有益なツールパス タイプの作成に近づいています。旧型の機械と高級でないツーリングを使用しているショップでは、加工時間が 50 ~ 60% 短縮されています。」
Open Mind のアプローチは、Celeritive Technologies Inc. (カリフォルニア州ムーアパーク) から基本的な VoluMill キットのライセンスを取得し、複数の深さを取得するためのスライス、セクショニング、衝突チェックなどの独自の方法を追加することでした。カスタマイズを考慮して、彼らは製品に明確な名前を付けました:Maxx Machining 荒加工.
Levine 氏によると、この実装の最もユニークな側面は、5 軸加工に拡張されていることです。 「タイヤの金型や航空機エンジンのケーシングなどの成形部品がある場合は、5 軸の荒加工パスを使用して提示できます。従来の CAM をタイヤの金型のような曲面に使用すると、多くの Z カットが行われ、その面に多くの階段ができてしまいます。 5 軸で高性能の荒加工を適用すると、形状に変化し、仕上げパス用に一定量の材料が残ります。プロセス全体がよりスムーズに進み、中間のクリーンアップ カットを大幅に節約できます。」
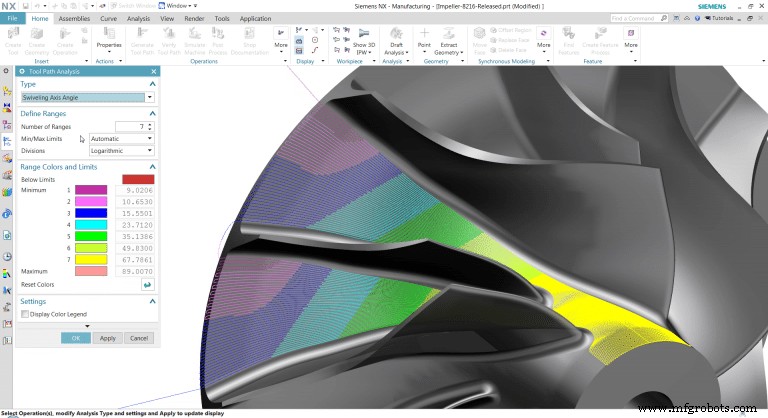
Mund 氏によると、Mastercam は最近、5 軸の荒加工と旋削加工に Dynamic Motion を追加し、Gadsden 氏は、PowerMill の新しい「自動ツール軸ティルト」は、すべてのモデル形状とツールパス タイプに対してスムーズで安全な 5 軸モーションを生成するのに役立つ単一のソリューションを提供すると述べています。 3 軸コードと同じくらい簡単に 5 軸プログラムを作成できます。」
GibbsCAM も VoluMill を使用しており、Remenak は、切削時間と工具寿命が大幅に改善されたと評価しています。 「最近の進歩により、これらの高効率フライス加工アルゴリズムで学んだ教訓が旋削に適用されました。その結果、GibbsCAM 12 で利用可能な VoluTurn などの新世代の旋削ツールパスが生まれました。これらの新しい旋削ツールパスは、材料除去率が高くなります。機械と工具のストレスを軽減し、切断品質とカッターの寿命を向上させます。」
非切削時間の切削
当然のことながら、最新の CAM は、リフトオフ高さとリフトオフ距離の両方を減らすことで、非切削時間を最小限に抑えます。 「リフトオフの高さは小さなことのように聞こえますが、大きな部分で大きな違いを生む可能性があります」とパラダイスは述べています。また、切断経路と非切断経路の両方の移動をスムーズにすることの重要性にも熱心に取り組んでいます。
「非切削動作に対処する簡単な方法は、マシンを停止してリフトオフし、次の加工領域の上のスポットにすばやく移動し、再び停止して下降し、エンゲージするように指示することです。数回の移動であれば問題ありませんが、時間をかけて機械加工する部品の場合、メカニックのまったく同じ位置で数千回のそのような移動が発生し、機械に損傷を与える可能性があります。それも遅いです。適切な曲線を計算し、両端で加速と減速を構築することが最善の方法です。たとえば、大規模な顧客は最近、非切削パスを滑らかにするだけで、数百台のマシンのサイクル タイムを 10% 節約しました。」
非切削時間を平滑化するために、高度な制御や高価な機械は必要ありません。経済的な機械でも生産性を向上させる簡単な方法です。また、機械の摩耗も減少するため、機械の寿命が延びます。
その他のエキサイティングな進歩
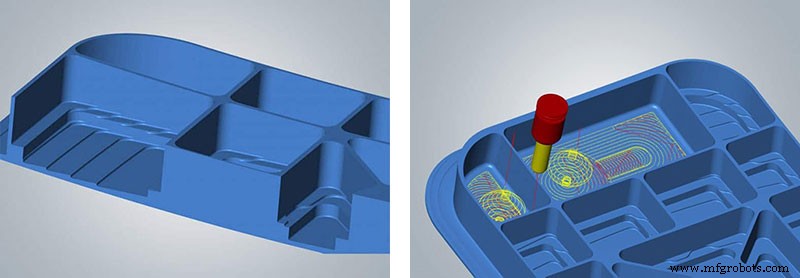
その他の改善点には、Open Mind の hyperMILL の新しい 3D 最適化荒削りサイクルが含まれます。これは、高送りカッター (高いステップオーバーで浅い切削を行う) を使用するアプリケーション向けに強化されています。ステップオーバー距離は、高送りカッター ジオメトリに対して測定されたスキャロップの高さから計算でき、大きなステップオーバーがある場合、特別なツールパスの動きによってコーナーから削り残しが除去されます。
Levine 氏は、秘密はカッターの底部の形状を正確にモデリングすることであると述べていますが、「他のソフトウェアは高送りカッターをコーナー R を持つブルノーズ カッターとして近似しています。高送りカッターの底部は、実際には有効半径が大きく、そのようにモデル化しています。」
利点の 1 つは、ソフトウェアがカッターのジオメトリに余裕がある場所を認識しているため、壁の近くで加工できることです。一方、平らな底部でカッターを近似するシミュレーションでは、接触がない場所が確認されます。 Levine 氏は、カッターをモデル化することで、隣接するカット間の距離をより適切に計算して、表面の品質を制御できるようになったと付け加えました。
高送りカッターに限らないもう 1 つの Open Mind の特徴は、「インテリジェントなカット分割」です。たとえば、ワークピースのセクションで 4.1 インチ (104 mm) の材料を除去する必要があり、プログラマーが 1.0 インチ (25.4 mm) のステップオーバーを指定した場合、最後のカットは非常に薄くなります (これよりもさらに薄くなる可能性があります)。例)。そのようなスライバーの機械加工は、非効率であるだけでなく、一部の材料では非常に有害である可能性があると Levine 氏は述べています。 「そのため、すべてのカットが同等の材料を使用するように、ステップの合計数に基づいて再計算して、規定のステップオーバーを無効にするこのオプションを提供しています。」
最後に、多くの企業が「サークル セグメント エンド ミル」やその他の新しいコニカル バレル ツール設計の使用を可能にしています。 (2018 年春号、ME Tooling &Workholding 号「New Tool Designs Power Faster-Tever-Ever Cutting」を参照してください)。 Levine 氏が説明したように、このようなツールは 1,500 mm もの有効半径を特徴としており、6 および 8 mm のステップオーバー距離を実現し、サイクル タイムを 90% 以上削減して優れた表面仕上げを実現します。 「丸みを帯びた内部コーナーなど、隣接する領域を仕上げるためにカッターを切り替える必要はなく、届きにくい領域を効率的かつ安全な方法で加工できます」と彼は言いました。
Gadsen 氏は、3 年前に顧客と提携して、バレル工具を使用して非常に複雑なブリスクの 5 軸加工を最適化し、フライス加工のサイクル時間を 200 時間から 35 時間に短縮できたと述べました。コストを 72% 削減します。」
もう 1 つの改善分野は 3D プリントです。 Autodesk の Gadsden 氏は、減算プロセスと加算プロセスを組み合わせたマシンの利用可能性が高まっていることを強調しました。 「これらのハイブリッド マシンは、部品の製造方法を変革するように見えますが、付加的なプロセスは単なる逆の除去的なプロセスではないため、CAM ソフトウェアにプログラミング上の課題をもたらします。これを念頭に置いて、Autodesk は PowerMill に特殊なツールを追加して、高速な付加製造プロセスをプログラム、制御、およびシミュレートしました。」
自動制御システム