ツールホルダーは、機械加工の生産性への重要なリンクを提供します
精密工作機械と高度な切削工具を組み合わせることで、卓越した金属切削生産性を実現します。ただし、その生産性を完全に達成するには、切削工具と機械のスピンドル(工具ホルダー)の間のリンクが重要です。工具メーカーはさまざまな工具ホルダースタイルを提供しており、それぞれが特定の機械加工アプリケーションで最適なパフォーマンスを発揮するように設計されています。したがって、機械加工工場は、特定の操作と製造する部品に基づいてツールホルダーを選択する必要があります。それでも、ショップは最先端の機械技術と切削工具の材料を習得しようと努めていますが、特定の生産ニーズに最適な工具ホルダーを選択、適用、維持することをほとんど重要視していないことがよくあります。
すべてのホルダーが同じように作成されるわけではありません
考えられるすべてのアプリケーションに適したツール保持方法はありません。高速仕上げ作業を実行するように設計されたツールホルダーは、通常、たとえば生の鋳物の深い荒加工で効果を発揮するために必要な剛性と強度を欠きます。逆に、荒加工用のホルダーは、通常、仕上げ作業で高速でスムーズに動作できるバランス品質を欠いています。さらに、荒削りホルダーの堅牢な設計とかさばりにより、細かい部品や深い部品の特徴へのアクセスが制限される可能性があります。頑丈なワークピースの材料には、強度と剛性が強化されたツールホルダーが必要です。振動を減衰させ、クーラントを供給するツールホルダーの能力も重要な選択基準です。
不適切なツールホルダーを使用すると、工作機械のスピンドルの過度の摩耗、ツールの寿命の短縮、ツールの破損の増加に加えて、寸法エラーや部品の廃棄が発生する可能性があります。重要でない仕事では、価値のあるツールホルダーが満足のいく結果を生み出すかもしれません。しかし、再現性のある精度が必須である操作、特に高価なワークピースを廃棄すると部品の利益率が低下する場合、アプリケーションに重点を置いた最高品質のツールホルダーへの投資により、このような予期しない損失に対する低コストの保険が提供されます。
一部の店長にとって、さまざまなアプリケーションで使用されるツールホルダーの長いバージョンは、有効なコスト削減戦略です。ただし、常に可能な限り短いホルダーを適用すると、剛性が最大になり、表面劣化振動が最小になり、工具寿命が維持されます。
ツールホルダーは、総生産コストの2パーセント未満を占めます。そのコストを半分に削減しても、ごくわずかな節約になりますが、スクラップされたワークピースや壊れたツールは、測定可能な経済的効果をもたらします。プレミアムツールとホルダーは、金属切削の生産率を高めて、ツールへの投資を即座に回収することができます。特に、機械加工プロセスの安定性が最優先される航空宇宙部品製造などの業界では、多くのメーカーが、欠陥部品の製造を回避し、トラブルシューティング作業や生産停止に時間を浪費することを避けるために、何よりもプレミアムツールの取得に重点を置いています。航空宇宙メーカーは通常、生産のためにそれらを認定する前に、新しいホルダーの概念を検証するために長い時間を要します。
ワークピースの要因がホルダーの選択に影響を与える
ツールホルダーの選択に影響を与える要因には、各ジョブでのワークピース材料の被削性、および特定の輪郭や特徴に到達するために必要なツールホルダーの寸法を決定する可能性のある最終部品の構成が含まれます。ただし、ツールホルダーは、オペレーターのエラーの可能性を最小限に抑えるために、できるだけシンプルで使いやすいものにする必要があります。
どの工具保持技術が適用されているかに関係なく、工作機械の剛性、スピンドルパワー、および厳しい公差を生成する能力によって、実行可能な操作が決まります。たとえば、摩耗した機械でミクロンスケールの公差を作成しようとすると、時間の無駄になります。
工作機械の基本要素が重要な役割を果たします。リニアガイドウェイを備えた高速マシンは、高速アプリケーション用に設計されたツールホルダーを最大限に活用し、ボックスウェイを備えたマシンは、重加工をサポートします。マルチタスクマシンは、旋削とフライス盤/穴あけの両方の操作を実行できるツールホルダーの機能を十分に活用します。
使用中の加工戦略は、ツールホルダーの選択にも役立ちます。たとえば、ショップは、より軽い切削深さを伴う高速切削(HSC)操作、または適切な出力で速度能力が制限されたマシンで高い金属除去率を生成することに焦点を当てた高性能切削(HPC)状況で、生産性を最大化するツールを選択できます。 。
繰り返し可能な低い振れは、一定の工具係合を保証し、それによって振動を低減し、工具寿命を最大化するのに役立ちます。バランスは非常に重要であり、高品質のツールホルダーはG2,5-25000 RPM品質(1 g.mm)で微妙にバランスが取れている必要があります。機械加工店は、独自の調査を実施し、工具サプライヤーと相談して、生産ニーズを費用効果の高い方法で満たす1つまたは複数の工具保持システムを決定できます。
各ホルダーにはニッチがあります
単純なウェルドン、コレット、熱収縮、機械式、油圧式のいずれのタイプでも、ツールホルダーは特定の操作要件に適合させる必要があります。たとえば、ウェルドンシャンクツール用のシンプルなエンドミルホルダーは、剛性が高く、使いやすく、高トルクを伝達でき、強力な引き抜き防止作用を備えた安全で強力なクランプを提供します。それらは重い荒削りによく適していますが、正確な同心性を欠いています。一般に、これらは本質的に不均衡であり、高い回転速度を使用するアプリケーションには生産的に適用されません。
コレットチャックと交換可能なコレットは、ラウンドツール保持技術の最も一般的な形式です。費用効果の高いERスタイルは、さまざまなサイズで利用でき、信頼性の高い軽いフライス盤および穴あけ作業に十分なグリップを提供します。高精度のERコレットホルダーは、振れが少なく(工具先端で5μm未満)、高速操作でバランスをとることができる対称設計を備えており、頑丈な加工には強化バージョンが用意されています。 ERホルダーは、迅速な切り替えを容易にし、さまざまな工具径に対応できます。
熱収縮フィットホルダーは、強力なクランプ力、3xDで3μmの同心性、および優れたバランス品質を提供します。小さくてシンプルなノーズ構成により、タイトなパーツの機能に簡単にアクセスできます。
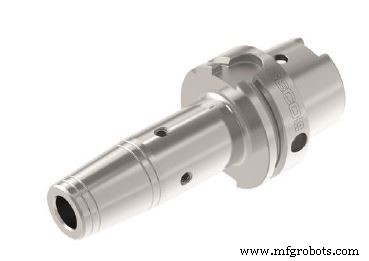
強化バージョンは中程度から重度のフライス盤を実行できますが、グリップ力はツールシャンクとホルダーのID公差によって異なります。焼きばめツールは特別な加熱ユニットを購入する必要があり、加熱/冷却プロセスは単にコレットを切り替えるよりも多くのセットアップ時間を消費します。
メカニカルミリングチャックは、複数列のニードルベアリングを介して強力なグリップ力と高いラジアル剛性を提供します。この設計により、大量のフライス盤と迅速な工具交換が可能になりますが、振れはコレットシステムよりも大きくなる可能性があります。メカニカルチャックは通常、他のツールホルダースタイルよりもサイズが大きいため、一部のパーツ機能へのツールアクセスが制限される場合があります。
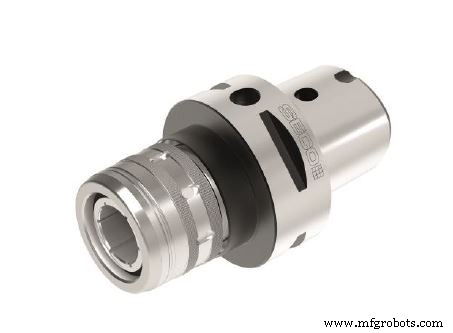
油圧を使用してクランプ力を発生させる油圧チャックは、機械式チャックよりも内部要素が少なく、その結果、比較的スリムなプロファイルになっています。油圧チャックは振れが少なく、高いスピンドル速度でのリーマ加工、穴あけ加工、軽フライス盤加工に効果的ですが、大きなラジアル荷重に敏感です。
ホルダーが切削工具を固定する方法と同様に、工作機械のスピンドルに取り付ける方法も重要です。ツールホルダーのスピンドルまたはテーパーエンドは、トルク伝達能力を決定し、ツールのセンタリング精度を確立します。従来のBT、DIN、およびCATツールテーパーは、小型のマシンでは効果的ですが、高速機能が制限される場合があります。ホルダーのテーパーと面の両方に接触するバージョンは、特に長いオーバーハングの状況で、剛性と精度を向上させます。より大きなトルクを確実に伝達するには、より大きなテーパーサイズが必要です。たとえば、HSK-E32ホルダーは、重い加工状況でHSK-A125Aを置き換えることはできません。
ホルダーテーパースタイルの選択は、多くの場合、地域の好みによって決定されます。 HSKは、5軸機の人気が高まった1990年代半ばにドイツで登場しました。 CATテーパーは主に米国で使用されていますが、アジアではBTシャンクが人気があり、テーパー/フェースコンタクトバージョンでよく使用されます。
HSKは5軸加工で非常に一般的です。 PSC(多角形クランプシステム:Capto)およびKM接続は、主にマルチタスクマシンで使用され、現在はISO規格になっています。 KMとCaptoはどちらもモジュラーシステムであり、エクステンションまたはレデューサーを積み重ねることにより、さまざまな長さの特定のツールを組み立てることができます。マルチタスクマシンの使用が増えるにつれ、1つのフィクスチャで部品を回転、フライス加工、またはドリル加工できるツールホルダースタイルの人気が高まっています。
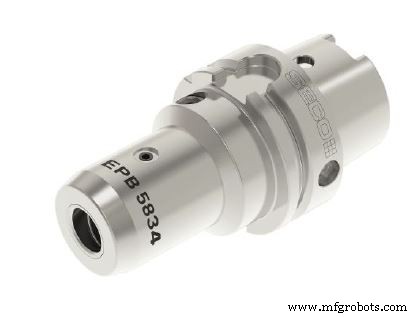
独自のホルダーとコレットを革新的な方法で使用して印象的な結果を達成する独自のツール保持システムがありますが、ショップはそれらの利点を計算する必要があります。これらのシステムは通常、コストが高く、単一のサプライヤからのツールの選択肢が限られています。
コストおよびその他の考慮事項
油圧式または機械式のホルダーの基本的なコストは、コレットまたは焼きばめのホルダーに比べて高くなりますが、焼きばめ加熱システムの費用や工具の交換に必要な時間など、他の要因も関係します。コレットチャックホルダーシステムでコレットを切り替えるだけで異なる直径に対応するのと比較して、各ツールの直径に合う焼きばめホルダーも必要です。
機械のオペレーターとツールのメンテナンス担当者も、ツールホルダーのアプリケーションを成功させる上で重要な役割を果たします。工作機械やその他の製造装置と同様に、工具所有者は、その利点を最大限に活用し、それらを最大限に活用するために、正しい使用法とメンテナンスを必要とします。たとえば、オペレーターはツールシャンクをホルダーに完全な長さまで挿入する必要があります。これは、不適切な着座は、振動を破壊したり、ツールを排出したりする精度につながるためです。次のツールアセンブリの仕様が重要です。オペレーターは、チャックを締めるときに延長ハンドルを使用して過度のトルクを加えないでください。これにより、コレットがねじれ、ツールの位置がずれることになります。
ツールのメンテナンスも重要ですが、無視されることがよくあります。オペレーターは、使用前に必ずホルダーを清掃し、工作機械のスピンドルも検査する必要があります。ホルダーは、ツールのテーパーを保護するためのキャップを付けて、清潔で乾燥した状態で保管する必要があります。油圧チャックの液圧は定期的にチェックする必要があります。
結論
機械工場は、機械加工システムにおける工具ホルダーの重要性を認識し、適切な工具ホルダーを特定の工作機械、機械加工戦略、およびワークショップに適切に適合させることで、生産性を高め、コストを削減する方法を学ぶ必要があります。同時に、ツールホルダーメーカーは、より包括的なホルダーの選択肢を提供しています(サイドバーを参照) 個々の運用上のニーズを満たすように設計されています。
将来の改善は、ホルダーハードウェア自体を超えています。ソフトウェアとRFIDタグを使用したツール管理は、データベースの製造の要素であり、より一般的になりつつあります。ツールホルダー技術の進歩には、ホルダーにかかる力をリアルタイムで監視できるセンサー付きホルダーが含まれます。収集されたデータにより、オペレーターが、または機械制御ユニットと連携した人工知能(AI)を介して自動的に、機械加工パラメーターの工程内調整が可能になります。これらおよびその他の新技術は、工具所有者が機械加工作業で提供する生産的な貢献をさらに強化します。
産業技術