機械加工 ものづくり 穴あけ技術 101
穴加工で最も一般的なツールとして、ドリル ビットは機械製造で広く使用されています。特に、冷却装置、発電設備の管板、蒸気発生器およびその他の部品の処理では、その用途は特に広範囲で重要です。
機能 O f D リリング
ドリルビットは通常2つの主切れ刃を持ち、加工時にはドリルビットが回転しながら切削を行います。ドリルのすくい角は中心軸から外刃に向かってどんどん大きくなっています。ドリルの切削速度は外円に近いほど速く、中心に向かって徐々に切削速度が遅くなり、ドリルの回転中心の切削速度はゼロになります。ドリルのチゼルエッジは回転中心軸の近くにあり、チゼルエッジの二次すくい角が大きく、チップスペースがなく、切削速度が遅いため、軸方向の抵抗が大きくなります。チゼル エッジを DIN1414 で A タイプまたは C タイプに研磨し、中心軸に近い刃先を正のすくい角にすると、切削抵抗が減少し、切削性能が大幅に向上します。
工作物の形状、材質、構造、機能に応じて、ドリルビットは高速度鋼ドリルビット(ツイストドリル、グループドリル、フラットドリル)、超硬ソリッドドリル、交換可能な浅穴ドリルなど、多くのタイプに分類できます、深穴ドリル、ネスティングドリル、互換ビットドリルなど
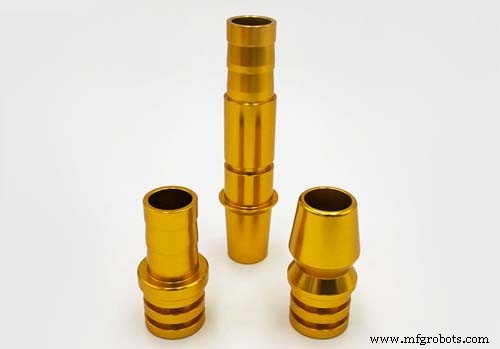
切りくず処理と切りくず除去
ドリルの切削は狭い穴で行われ、切りくずはドリルの溝から排出される必要があります。そのため、切りくずの形状がドリルの切削性能に大きな影響を与えます。一般的なチップ形状には、フレーク チップ、管状チップ、ニードル チップ、円錐スパイラル チップ、バンド チップ、ファン チップ、パウダー チップなどがあります。
チップ形状が不適切な場合、次のような問題が発生します。
①細かい切りくずは刃先の溝をふさぎ、穴あけ精度に影響を与え、ドリルビットの寿命を縮め、ドリルビットを壊すことさえあります(粉状の切りくず、扇形の切りくずなど);
② 長い切りくずがドリルビットに巻き付き、作業を妨げたり、ドリルビットが折れたり、切削液が穴に入るのを妨げたりします (スパイラルチップ、リボンチップなど)。
不適切なチップ形状の問題を解決する方法:
① 送り量アップ、間欠送り、チゼルエッジ研磨、チップブレーカ設置などの方法を単独または組み合わせて使用することで、切りくず処理、切りくず排出効果を向上させ、切りくずによるトラブルを解消します。
②専門のチップブレーカドリルで穴を開けることができます。たとえば、ドリル ビットの溝に設計されたチップ ブレーカーを追加すると、切りくずがより簡単に掃除できる切りくずに分解されます。ゴミは溝に沿ってスムーズに取り除かれ、溝に詰まることはありません。したがって、新しいチップブレーカー ドリルは、従来のドリルよりもはるかに滑らかな切削効果を発揮します。
同時に、短い破砕鉄チップにより、クーラントがドリル先端に流れやすくなり、加工プロセス中の放熱効果と切削性能がさらに向上します。また、新たに追加されたチップブレーカがドリルビットの溝全体を貫通するため、研削を繰り返しても形状と機能を維持できます。上記の機能改善に加えて、この設計によりドリル本体の剛性が強化され、1 回の研削前に掘削される穴の数が大幅に増加することに言及する価値があります。
掘削精度
穴の精度は、主に開口サイズ、位置精度、同軸度、真円度、表面粗さ、穴のバリなどの要因で構成されます。
ドリル加工中に加工される穴の精度に影響を与える要因:
① 工具ホルダー、切削速度、送り速度、切削液など、ドリルのクランプ精度と切削条件。
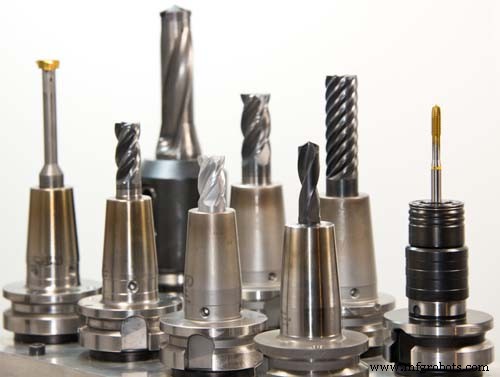
② ドリルビットの長さ、刃の形状、ドリルコアの形状など、ドリルビットのサイズと形状。
③オリフィス側面の形状、オリフィスの形状、厚み、クランプ状態などワークの形状
リーミング
リーマ加工は、加工時のドリル刃の振れにより発生します。ツールホルダーの振れは、穴径や穴の位置決め精度に大きく影響しますので、ツールホルダーの摩耗が激しい場合は、早めに新しいツールホルダーに交換する必要があります。小径穴加工の場合、振れの測定・調整が難しいため、刃と柄の同軸度が良く、粗シャンクの小刃ドリルを使用するのがベストです。リグラインドドリルを使用した場合、穴精度が低下する原因の多くは、背面形状の非対称性によるものです。刃の高低差をコントロールすることで、穴の切り込みや拡大を効果的に抑制できます。
穴の真円度
ドリルビットの振動により、ドリル穴が多角形になりやすく、穴壁にライフルのような線が現れます。一般的な多角形の穴は、ほとんどが三角形または五角形です。三角形の穴の理由は、穴あけ時にドリルに 2 つの回転中心があるためです。それらは、600回ごとに600回の交換の頻度で振動します。振動の主な理由は、アンバランスな切削抵抗です。ドリルが1回転すると、加工穴の真円度がイマイチになり、切削2回転目で抵抗力がアンバランスになり、最後の振動を再び繰り返すが、振動の位相がある程度ずれて、ホールウォールのライフルライン。ある程度の穴あけ深さになると、ドリルビットの刃先面と穴壁との摩擦が大きくなり、振動が減衰し、ライフルラインがなくなり、真円度が良くなります。このタイプのオリフィスは、縦断面で見ると漏斗状です。同じ理由で、切断時に 5 角形や 7 角形の穴が開くこともあります。この現象を解消するためには、チャックの振動、刃先の高低差、刃先の非対称や刃先形状などを制御することに加え、ドリルの剛性を上げ、 1回転あたりの送り、逃げ角、および研削を改善する必要があります。刃先などの対策
傾斜面や曲面へのドリル穴あけ
ドリルビットの切削面や穴あけ面が傾いたり、曲がったり、段差があると位置決め精度が悪くなります。このとき、ドリル ビットは放射状の片面切削工具を使用しているため、工具の寿命が短くなります。
測位精度を向上させるために、次の対策を講じることができます:
<オール>バリ処理
穴あけの際、特に強靭な材料や薄板の加工では、穴の入口と出口にバリが発生します。その理由は、ドリルビットが穴をあけようとしているときに、加工材料の塑性変形が発生するためです。このとき、外縁近くのドリルビットの刃先で削るべき三角形の部分は、軸方向の切削力の影響を受けて外側に変形し、ビットの外縁で曲がる作用を受けます。面取りや刃先の加工により、さらにカールしてカールやバリを形成します。
穴あけ加工条件
総合ドリル製品カタログには、加工材料別にまとめた「切削基本パラメータ一覧表」があります。ユーザーは、提供されている切削パラメータを参照して、ドリル加工の切削条件を選択できます。切削条件の選択が適切かどうかは、加工精度、加工能率、ドリル寿命などを総合的に試切削で判断する必要があります。
1.ドリルビットの寿命と加工効率
加工するワークの技術的要件を満たすことを前提として、ドリルが適切に使用されているかどうかは、ドリルの寿命と加工効率に応じて総合的に測定する必要があります。ドリルの耐用年数の評価指標は、切削距離を選択できます。加工能率の評価指標は送り速度を選択できます。ハイス鋼のドリルビットの場合、ドリルビットの寿命は回転数に大きく影響され、1回転あたりの送りにはあまり影響を受けません。したがって、1回転あたりの送りを大きくすることで、ドリルの寿命を延ばしながら加工能率を向上させることができます。ただし、1回転あたりの送りが大きすぎると、切りくずが厚くなり、切りくず処理が困難になることに注意してください。したがって、切りくず処理をスムーズに行うための 1 回転あたりの送りの範囲を、試し切りで決定する必要があります。超硬ドリルは刃先のすくい角マイナス方向の面取りが大きく、1回転あたりの送りの任意範囲がハイスドリルに比べて小さくなります。加工中に1回転あたりの送りがこの範囲を超えると、ドリルの使用は寿命を縮めます。超硬ドリルはハイスドリルに比べて耐熱性が高いため、回転数による寿命への影響はほとんどありません。したがって、超硬ドリルの寿命を確保しつつ、加工能率を向上させるには、回転数を上げる方法が有効です。
2.切削液の合理的な使用
ドリルの切断は、狭いスペースの穴で行われます。そのため、切削液の種類や噴射方法がドリルの寿命や穴の加工精度に大きく影響します。切削油剤は、水溶性と非水溶性の2つのカテゴリーに分けることができます。非水溶性切削油剤は、潤滑性、濡れ性、付着防止性に優れ、防錆効果もあります。水溶性切削油剤は、優れた冷却特性、非発煙性、不燃性を備えています。近年、環境保護への配慮から、水溶性切削油剤の使用が比較的多くなっています。ただし、水溶性切削液の希釈率が不適切だったり、切削液が劣化したりすると、工具の寿命が大幅に短くなりますので、使用には注意が必要です。水溶性切削油剤、不水溶性切削油剤を問わず、切削油剤は使用中に切削点に十分に到達する必要があります。同時に、切削液の流量、圧力、ノズルの数、および冷却方法 (内部冷却または外部冷却) を厳密に管理する必要があります。
ドリルの再研磨
ドリルビット再生判定
ドリル ビットを研ぎ直す基準は次のとおりです。
<オール>実際の使用では、特定の条件に応じて、上記の指標から正確で便利な判断基準を決定する必要があります。摩耗量を基準にすれば、経済性に優れた最適な再研磨時期を見つけることができます。主な研ぎ部位は後頭部とノミ刃なので、ドリルの磨耗量が多すぎると刃の磨耗時間が長くなり、研ぎ量が多くなり、研ぎ直し回数が少なくなります(全工具寿命 =再研磨後の工具寿命 × 再研磨可能な回数)、ドリル ビットの総寿命を短くします。加工穴の寸法精度を基準とする場合は、コラムゲージまたはリミットゲージを用いて穴の切れや広がり、凹凸等を確認し、管理値を超えた場合は速やかに再加工すること。研ぎます。切削抵抗を基準とする場合は、設定した制限値(主軸電流など)を超えるとすぐに自動停止するなどの方法が考えられます。処理量制限管理を採用する場合は、上記の判別内容を統合して基準を設定する必要があります。
ドリルの研ぎ方
ドリルを再研磨するときは、ドリルの寿命と加工精度を確保するために非常に重要な、ドリルを研磨するための特別な工作機械または万能工具研削盤を使用するのが最善です。元のドリル タイプが良好な加工状態にある場合は、元のドリル タイプとして再研磨できます。元のドリルタイプに欠陥がある場合は、使用目的に応じて適切にバック形状を改善し、チゼルエッジを研ぐことができます.
研ぐときは次の点に注意してください:
<オール>製造プロセス