信頼性工学101:定義、目標、技術
購入した製品の品質をどのように評価しますか?
工場での従来の品質管理は、事前定義されたチェックとテストの実行で構成されます。製品が設定された要件を満たしている場合、準備完了と見なされます。 。ただし、保証期間が終了する前に2回以上再生プロセスを実行する必要がある場合は、高品質の製品を購入したとは決して言えません。
信頼性と信頼性エンジニアリング 品質方程式に時間の次元を追加することにより、製品の品質を定量化するのに役立ちます。言い換えれば、製品が購入時に意図した機能を実行できるかどうかを知りたいだけではありません。代わりに、製品が通常の状態で大きな誤動作なしにできるだけ長く動作することを確認したいと思います。
信頼性エンジニアリングは、組織がより信頼性の高い製品を製造するのに役立つだけでなく、MTBF(平均故障間隔)と資産の寿命を延ばすためにそれらを保守する方法について保守チームに通知します。
詳細については、この記事の続きで、以下について説明します。
- 信頼性の概念
- 信頼性工学のコア原則
- 信頼性評価の基本
- 信頼性エンジニアが機器の信頼性を向上させる方法
信頼性とは何ですか?
信頼性とは、通常の動作条件を想定して、特定の期間にわたって特定のパフォーマンス基準を満たすコンポーネントまたはシステムの能力を表すために使用される用語です。
別の見方をすれば、同じ条件下で動作する2つのシステムがある場合、大きな問題が少なく、より長く動作するシステムの方が信頼性が高くなります。
誰も将来を予測できず、製品が正確にX時間使用しても故障しないことを保証できないため、信頼性の計算 には、確率の形で表される不確実性が伴います 。特に、信頼性計算を使用して、x時間または数日間の使用後にシステムが適切に動作する可能性を見積もることができます。当然、どのシステムの信頼性も最初は高く、時間の経過とともに低下します。
信頼性は、耐久性、品質、および可用性と混同されることがよくあります。概念は似ていますが、同じ意味で使用しないでください。それぞれについて簡単に説明します。
信頼性と耐久性
耐久性とは、設計寿命全体にわたって通常の操作の課題に直面したときに、過度のメンテナンスや修理を必要とせずに、物理的な製品が機能し続ける能力として定義できます(Tim Cooperから定義が盗まれました)。
信頼性と耐久性の主な違いは、耐久性は主に、製品が故障しても製品がどれだけ長く続くことができるかに関係しているということです。 、信頼性はそれらの故障の総数と頻度を減らそうとしている間。
さらに、耐久性コンポーネントは物理的なアイテムの特性を表すために使用されますが、信頼性は仮想システムにも使用できます。
製品とその適用分野に応じて、耐久性は使用時間、動作サイクル数、または存在年数で表すことができます。
信頼性と品質
品質は定義するのが難しい概念です。それを説明する一般的な方法の1つは、製品の品質に影響を与える要因を調べることです。これは、品質の8つの次元の概念につながります。
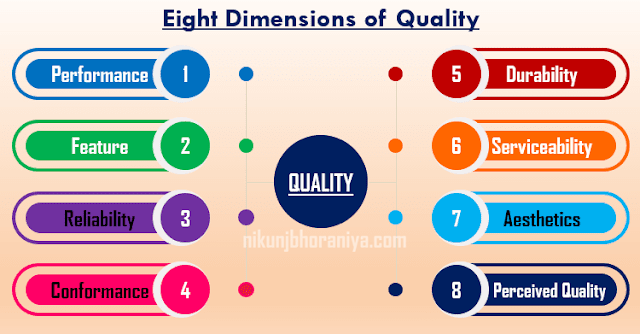
これは、信頼性(およびよく見ると耐久性)を品質の1つの側面と見なすことができるため、実際には信頼性と品質を区別する簡単な方法です。
信頼性をスタンドアロンの概念と見なす場合、それらの関係を確認する別の方法は、信頼性の高いシステムとは、長期にわたって品質を維持するシステムであるということです。 。
信頼性と可用性
可用性は、システムが設計されたとおりに実行できる(完全に機能している)時間の割合を示します。
この概念は、クラウドインフラストラクチャの可用性を説明するためにITで非常に頻繁に使用されます。可用性が最も高いシステムは99.99%の範囲です(つまり、サービス/システムは年間のうち約52分間しか利用できません;多くの場合、定期メンテナンスを実行するためだけです。
可用性は、信頼性と保守性の影響を受けます。信頼性の高いシステムでは、障害が少なくなり、可用性が向上します。同様に、定期メンテナンスの実行が速ければ速いほど、ダウンタイムが少なくなり、可用性が向上します。
信頼性工学とは何ですか?
信頼性エンジニアリングとは、費用効果の高い方法でより信頼性の高い製品を作成するための、最良のエンジニアリング手法と手法を体系的に適用することを指します。 。信頼性工学の方法論は、設計と製造から運用と保守まで、製品ライフサイクル全体に適用できます。
とはいえ、信頼性工学の主な価値は、起こりうる信頼性の問題を早期に発見することにあります。設計段階などの製品ライフサイクルの早い段階で信頼性の問題を見つけた場合、将来のコストを大幅に最小限に抑えることができます(つまり、すでに市場に出た後の大幅な製品再設計の必要性を排除することによって)。このアイデアは、以下のグラフに示されています。
信頼性工学の目標は次のとおりです。
- エンジニアリングの知識と技術を使用して、特定の障害モードを防止し、障害の可能性と頻度を減らします。
- 障害を防止するための努力にもかかわらず、発生する障害の原因を特定して修正するため。
- 原因が修正されていない場合に発生する障害に対処する方法を決定するため。
- 新しい設計の信頼性の可能性を推定し、信頼性データを分析するための方法を適用する。
リストをさらに詳しく見ると、さまざまな信頼性手法の適用の自然な進歩に沿った方法で目標が順序付けられていることがわかります。簡単な設計変更で一部の障害を防ぐことができれば、特定されたすべての障害に冗長性を追加しようとしても意味がありません。つまり、上記のリストは、順番に実行する必要のある手順を表しています。 信頼性の実践が費用効果的に適用されることを確実にするため。
信頼性評価の基本
信頼性評価の最終目標は、定性的および定量的な証拠の堅牢なセットを用意することです。 当社のコンポーネント/システムの使用には、許容できないレベルのリスクが伴うことはありません。 。これは信頼性工学の不可欠な部分です。
この文脈では、リスクは失敗の確率の組み合わせとして定義できます。 (障害が発生する可能性がどの程度あるか)および障害の重大度 (障害のフォールアウトは何ですか。安全上のリスク、潜在的な二次的損傷、スペアパーツと人件費のコスト、生産損失などが含まれる可能性があります。)
故障メカニズムと故障モードを理解する
原因と失敗の間に線を引くことは必ずしも容易ではありません。そうでない場合は、信頼性エンジニアや障害分析はほとんど必要ありません。
障害モードと障害メカニズムを十分に理解してそれらに効率的に対処するには、複雑なシステムをコンポーネントに「分解」する必要があります。このようにして、それらを個々のレベルで分析するだけでなく、それらが互いにどのように相互作用するかに基づいて分析することができます。
上記のすべてに加えて、システムがユーザーや環境と対話する方法は、誤用や劣悪な作業条件の両方が製品の信頼性を低下させる可能性があるため、考慮する必要があるもののリストに追加するもう1つの要素です。
信頼性工学で使用される一般的なタスクと手法
システムの複雑さと私たちが見ているシステムのタイプに応じて、信頼性工学の取り組みの一環として適用できるさまざまな手法とタスクがあります。
- 根本原因分析(RCA)
- 信頼性中心のメンテナンス(RCM)
- FMEAおよびFMECA
- FMEAの設計とFMEAのプロセス
- 失敗の物理(PoF)
- 自己診断装置
- 信頼性ブロック分析
- フィールドデータ分析
- フォールトツリー分析
- 単一障害点(SPOF)の排除
- ヒューマンエラー分析
- 運用上の危険分析
- メンテナンス履歴を調べて障害率を分析し、障害データを収集します
- システム/コンポーネントがストレス下でどのように機能するかを測定するあらゆる種類のデータ収集テスト
- …
これらすべての対策を講じることで、システムの弱点を見つけ、これらの弱点が誤動作を引き起こす可能性がどの程度あるかを確認できます。認識されたリスクが十分に高い場合、是正措置を通じてそれらに対処する必要があります。一般的なソリューションは、設計変更の形で提供されます (例:冗長性の追加)、検出制御、メンテナンスガイドライン、ユーザートレーニング 。
信頼性の定量化
この記事の冒頭で述べたように、信頼性は多くの場合、運が左右するゲーム(確率)です。リスクを定義するためにパーセンテージと統計データを扱っているので、チーム全体が同じページにいて、達成しようとしているリスクの許容レベルについて合意することが非常に重要です。
これが、問題を説明し、解決策を提案するときに正確な言葉を使用することが非常に重要である理由です。さらに、不完全な統計データやその他の不確実性のために、信頼性の専門家の中には、失敗の可能性よりも解決策に焦点を当てることを推奨する人もいます。
部品/システムの障害については、信頼性エンジニアは「いつ」を予測するのではなく、「なぜ、どのように」に集中する必要があります。障害が発生する可能性のある「理由」を理解することは、障害が発生する可能性のある「時期」を定量化するよりも(たとえば、MTBFを決定することによって)、使用する設計とプロセスの改善につながる可能性がはるかに高くなります。 )。これを行うには、最初に、部品/システムに関連する信頼性の危険性を分類して順序付けし(可能な場合は何らかの形式の定性的および定量的ロジックに基づいて)、より効率的な評価と最終的な改善を可能にする必要があります。
O’Connor、Patrick D. T.(2002)、 実用的な信頼性工学
信頼性エンジニアはどのようにして施設の機器の信頼性を向上させることができますか?
信頼性エンジニアが施設のメンテナンスプロセスを改善および最適化するのに役立ついくつかの方法があり、最終的には機器の信頼性が向上します。それらのいくつかについて以下で説明します。
スペアパーツの設計と開発を支援する
日常の使用に伴う傷みは区別されません。効率的な運用を継続するには、ほとんどの資産に定期的にスペアパーツを取り付ける必要があります。
適切なリソースを持っている企業は、スペアパーツの在庫を絶えず補充するのではなく、CNCマシンまたは3D印刷を使用して独自のパーツを作成することを選択する場合があります。さらに、彼らはもはや販売されていないスペアパーツを備えた古いマシンを持っているか、カスタムパーツを必要とする厄介な故障に対処する必要があるかもしれません。
これらのシナリオでは、信頼性エンジニアは保守チームと緊密に連携して、オンサイト資産の信頼性を向上させる高品質の交換部品を設計、テスト、および製造できます。
根本原因分析の実行
信頼性エンジニアが非常に得意とするべきことの1つは、障害の原因を特定して理解することです。そのため、根本原因分析(RCA)の実行を任せることができます。 。彼らは、OEMマニュアル、メンテナンスプラクティス、機器メンテナンスログ、およびその他のドキュメントを調べて、特定のマシンが故障している理由を見つけることができます。 および排除および/または軽減する方法を提案する 見つかった各障害の原因。
潜在的な原因に対処する1つの方法は、RCMプラクティスを適用することです。
メンテナンスアクションが適切な障害モードに対処していることを確認する
これは前のポイントの拡張です。最後のポイントは、自分が行っていないこと(どの障害モードに対処していないか)を見つけることに集中していたため、ここでは、間違っている可能性のあることに焦点を当てましょう 。
ほとんどの企業は、資産の定期的なメンテナンスを行っていて、その資産がまだ故障している状況に陥っています。それには多くの理由が考えられますが、その1つは、保守技術者が適切な障害モードに対処していないなど、何か間違ったことをしていることです。これは、RCA分析を参照することが非常に役立つ場合がある場所です。
同様に、信頼性エンジニアは、さまざまな保守作業がどのように実行され、どのように改善できるかを時々確認できます。彼らは、保守チームが時代遅れの慣行を使用しているかどうか、および付加価値を付けて適切な問題に対処する予防保守タスクを実行しているかどうかを確認できます。これらはすべて、優れたCMMSシステムで簡単にアクセスできる必要があります。
CMMSの詳細については、ガイド「CMMSとは何ですか。どのように機能するか」をご覧ください。
最後になりましたが、信頼性エンジニアは、状態ベースのメンテナンスや予知保全などの高度なメンテナンス戦略を実装するための適切な状態監視センサーと機器の選択を支援することもできます。
最終的な考え
真剣な信頼性工学の取り組みは、真剣な結果をもたらします。適切な知識があれば、会社の規模に関係なく、信頼性の手法を実装できます。
今後も、関係者全員に役立つ信頼性への投資を継続していきたいと考えています。制作会社はより高品質の製品を生産することで恩恵を受け、保守チームはそれらを保守するのに苦労することが少なくなり、ユーザーは製品の寿命全体にわたってパフォーマンスの問題が少なくなります。それはお互いに有利な状況です。
あなたは信頼性エンジニアですか、それともメンテナンスの専門家ですか。重要なポイントを見逃したと思いますか?以下のコメントであなたの考えを共有してください。
機器のメンテナンスと修理