CMMSの助けを借りて総合的生産的メンテナンスを実装する
事故が発生せず、予期しない機械の故障がゼロのメンテナンスチームを誇りに思う人はいないでしょうか?
これは不合理に思えますが、総合的設備管理を実装することを決定した組織の最終的な目標です。 。
メンテナンスに対するこのプロアクティブなアプローチは、完全に実装するのに何年もかかる可能性があるため、何が先にあり、どのツールがこの移行をスムーズにすることができるかを十分に認識していることを確認する必要があります。それらのツールの1つは、コンピューター化された保守管理システム(CMMS)です。これは、その標準機能の多くがTPMの要件とうまく調和しているためです。
一般的なTPM方法論、および最新のCMMSを使用して組織に実装する方法について詳しく知りたい場合は、適切な場所に来ています。
CMMSとは何かがまだわからない場合は、CMMSシステムとは何かとその仕組みガイドをご覧ください。
総合的設備管理(TPM)とは何ですか?
Total Productive Maintenanceは、組織の機器を最適な作業条件に保ち、機器の可用性を高め、コアプロセスの故障や遅延を回避することに重点を置いたプロアクティブな資産メンテナンスシステムです。
他のメンテナンス戦略とは異なり、TPMでは、機械のオペレーターは、操作する機器のメンテナンスプロセスに関与します。 TPMはいくつかの業界に適用できますが、主に機器のメンテナンスに対する根本的でユニークなアプローチのために、製造業で最も一般的に使用されています。
TPMを製造プロセスに特に関連させる1つの要因は、設備総合効率です。 。それは生産的である計画された生産時間のパーセンテージを決定しようとします。これは、非効率的なシステムの40%から完全な生産の100%までの範囲のスコアで、「完全な生産」への進行を追跡することを目的としています。
TPMの目的は何ですか?
TPMの背後にある概念は、次のような特定の目的を達成することを目的としています。
- 機器の手入れに対する責任を共有する、メンテナンスに対するプロアクティブで「オールハンズオンデッキ」のアプローチ。
- 企業内のすべてのレベルのスタッフがメンテナンスプロセスに関与しており、稼働時間の増加につながります。
- 機器の欠陥やダウンタイムをゼロにする。
- 事故レベルをゼロにし、より安全な作業環境を構築します。
- 製造プロセスでの無駄を省きます。
- 最終製品の品質を向上させます。
TPMの利点は何ですか?
生産チームと保守チームの従来の区別を曖昧にすることで、TPMを採用している企業は次のメリットを享受できます。
- オペレーターは、マシンを保守して「所有権」の感覚を与えることができます。
- メンテナンス技術者の注意を待たずに、マイナーなメンテナンスの問題に気づき、より早く修正します。
- 故障や停止が少なくなるため、生産性が全体的に向上します。
- 製品の品質とその後の顧客満足度の向上。
- 製造コストの削減。
- 作業プロセスでの事故の数を減らしました。
総合的設備管理の構造
TPMは、 5S手法で構成されています それはベースと 8本の柱として機能します 、それぞれが、上記で説明したTPMの目標を達成するために実装および使用する必要がある1つのタイプのアクティビティを示しています。
5S –「S」の背後にある意味
総合的生産管理の実装は、基盤となる強力な基盤(読み取り作業環境)を作成することから始まります。その基盤は、5S手法を採用することで実現されます。
5Sの目標は、機器を使用するための手順を定義することにより、作業環境がクリーンで適切に整理されていることを確認することです。
5Sの各「S」は次の略です:
- 並べ替え –有用なアイテムを特定し、不要なアイテムを排除します。障害物を取り除き、不要なアイテムによる妨害のリスクを減らすことで、作業が簡単になります。
- 順番に並べる –新しいスペースと残りのアイテムを整理します。ツール、機器、およびその他のリソースは、必要に応じて適切に配置され、近接しています。
- シャイン –職場を清掃および検査します。作業エリアはより安全で、作業がより快適になり、設備はよりよく保存されます。
- 標準化 –上記の手順の標準を文書化します。一貫性を確立し、それを日常業務の一部にします。
- サステイン –標準を定期的に適用します。定期的な監査、トレーニング、および規律を実行し、改善のためのフィードバックや提案を受け入れます。
総合的設備管理の柱
TPMには、機器の可用性を向上させるための予防的かつ予防的な手順に焦点を当てた8つの柱があります。
第1の柱–自律保守(AM)
TPMの最初の柱は、自律保守です。これには、基本的なメンテナンス活動の責任をメンテナンス担当者から機械オペレーターにシフトすることが含まれます。 。このようなタスクには、検査、清掃、注油などのアクションが含まれます。ただし、機械のオペレーターが能力を超えた問題に遭遇した場合、必要なのはメンテナンスチームの注意を引くための作業指示書を作成することだけです。
自律保守が達成しようとしていること
Autonomous Maintenanceは、機械のオペレーターに機器の毎日の維持管理を任せることで、保守技術者がそれほど重要でない活動に専念することを防ぎます。したがって、これらの技術者は、より要求の厳しい技術的修理に集中することができます。
適切に実装されたAM手順により、障害の検出が速くなり、機器のダウンタイムが減り、従業員の参加が向上します。 。
CMMSが自律保守にどのように役立つか
AMをコンピューター化された保守管理システム( CMMS )で使用する場合 )、組織は次のようないくつかの分野で重要な結果を見ることができます。
アクティビティログ: 一つには、マネージャーはおそらく、機械のオペレーターにTPMタスクを実行させるという課題に関係している可能性があります。通常、オペレーターはむしろマシンで作業し、それで完了します。ただし、CMMSを使用すると、プロセスを効果的に監視し、誰が何をしたか、何をしていないかを確認するのが簡単になります。
オペレーターが最小限のトレーニングで毎日のTPMタスクを把握してログに記録できるようにし、日常のワークフローにほとんどまたはまったく影響を与えないようにすることで、オペレーターはそれを使用する意欲が高まり、TPMへの移行がはるかに簡単になります。
作業指示管理: CMMSでこのモジュールを使用すると、オペレーターは作業指示をすばやく作成して、自分で処理できないマシンの障害を報告できます。
第2の柱–メンテナンスの改善(MI)
メンテナンスの改善により、リアクティブメンテナンスに大きく依存している組織は、計画されたメンテナンスへの移行を開始できます 。
この移行は段階的に行われますが、計画されたメンテナンスプログラムに配置される資産を決定することから始まります。企業は、少数の機器から始めて、時間の経過とともに他の機器を追加することを決定する場合があります。その後、彼らの焦点は資産の復元/改善と、各機器の定期的なメンテナンスタスクのリストの作成に移ります。
達成を目指すもの
マシンの信頼性を向上させる予防的かつ計画的なメンテナンス計画を作成します。
現在、メンテナンスが計画されているため、企業は、メンテナンスコストの削減(より適切にメンテナンスされた資産による)、重要な部品コストの削減(実際の部品の使用による)、および人件費の削減(残業時間の短縮による)のメリットを享受し始めます。
>CMMSがメンテナンスの改善にどのように役立つか
機器データの使用: CMMSの最も重要な利点の1つは、修復履歴をキャプチャできることです。この機能は現時点では貴重であり、機器の履歴を参照することで、保守技術者は、復元または改善を正確に行う前に、各資産を診断するのに適した立場にあります。
プロアクティブなメンテナンス戦略を実装する: とりわけ、プロアクティブなメンテナンスには綿密な計画が必要であり、過去にリアクティブなメンテナンスに大きく依存していた組織にとっては、すべてが当惑するように見える可能性があります。幸いなことに、CMMSは、プロアクティブなメンテナンス計画のすべてのステップを非常に簡単に整理およびスケジュールできるため、ここで再び輝いています。
第3の柱–焦点を絞った改善(FI)
製造プロセスで一般的に遭遇する6つの重大な損失があり、FocusedImprovementはそれらを特定して排除しようとしています。そうすることで、組織は運用の品質、速度、効率を向上させ、OEEを向上させることができます。
達成を目指すもの
FIは、機器の運用を定期的かつ持続可能な方法で改善するシステムを構築するために集まった、企業内に多才なチームを作成するための環境を構築します。事実上、製造プロセス内での損失を最小限に抑えることが保証されます。
CMMSが焦点を絞った改善にどのように役立つか
データ分析: CMMSで利用可能な履歴データトレイルを使用せずに、どの資産で最もダウンタイムが発生しているかを正確に把握するのは面倒です(またはほとんど不可能です)。 CMMSを使用することで、プロセスの問題をより正確に特定し、将来の損失を排除するための新しい戦略を迅速に展開できます。
第4の柱–教育およびトレーニング(ET)
TPMは、検査と軽微な予防保守タスクを実行するために不可欠な能力を持つすべての作業者に重点を置いているため、保守に対する独自のアプローチです。したがって、TPMを確実に成功させるために必要なトレーニングに全員が参加する必要があります。
総合的設備管理を採用するための「方法」だけでなく「理由」も知っている従業員に重点を置く必要があります。成功するには、従業員のサポートとプロセス全体への取り組みが不可欠です。
たとえば、自律保守の柱を考えてみましょう。 XYZ社の保守技術者は各機器の動作に精通していますが、必要な知識を機械のオペレーターに伝えようとしないとどうなるか想像してみてください。または、プロセスを見たり理解したりしないため、無計画でつまらない方法でそうします。このような場合、実装中に深刻な問題が発生するだけでなく、不適切なトレーニングによってオペレーターが機械関連の怪我を負うリスクがあります。
達成を目指すもの
適切なトレーニングを行うことで、維持している資産に出資しているように感じるマルチスキルの従業員のチームが作成されます。彼らは、割り当てられた修理を効果的かつ独立して実行する権限を与えられています。時間の経過とともに、組織は、ダウンタイムを最小限に抑えることができる「専門家」でいっぱいのシステムのメリットを享受できるようになります。
CMMSが教育とトレーニングにどのように役立つか
スキルの適切な移転: CMMSを使用すると、TPMプログラムに配置されたすべての機器について、詳細な(写真付きの)段階的なメンテナンス手順を作成することにより、オペレーターが機械を効果的かつ安全に処理できるようになります。
第5の柱–品質管理(QM)
品質維持の背後にある概念は単純です。優れた製品品質(歩留まり)を維持するために機器を完璧な状態に保つことです。
新しい機器はすべて特定の間隔でチェックされ、動作条件が確立され、一貫した出力品質が保証され、欠陥が事前に防止されます。これは、時折の手動検査、状態監視センサーの使用、または両方の方法の組み合わせによって行うことができます。
達成を目指すもの
QMは、欠陥のない製造と資源の無駄の排除を実現することを目指しています。これは、製造プロセスで生産される商品に直接影響を与える資産の潜在的な不適合を特定して修正することによって行われます。その結果、生産効率が向上し、完成品に対する顧客の喜びが高まります。
CMMSが品質維持にどのように役立つか
予知保全: 計画的なメンテナンスは、定期的な手動検査による品質の維持に役立ちますが、人為的ミスの余地がまだあるため、それだけでは不十分な場合があります。
代わりに、組織は、リアルタイムの状態監視センサーを使用して、製品の品質に直接影響を与える可能性のある潜在的な問題を検出することで、事態をさらに進めることができます。どちらの方法を採用する場合でも、CMMSは、センサーからのデータであろうと人間の入力からのデータであろうと、データを適切にキャプチャして分析します。
第6の柱–初期設備管理(EEM)
この柱は、設計と製造という根本的な問題に対処することにより、機械操作における一般的な問題を回避することに焦点を当てています。
初期の機器メンテナンスでは、割り当てられた担当者が特定の機器に関連する一般的な問題に関する詳細を収集します。次に、その情報を製造元または社内のエンジニアリング部門に転送して検討します。これにより、以前のものを改善するために再設計された新しいマシンまたはコンポーネントが作成されます。
リアクティブメンテナンスを73.2%削減
ケーススタディ
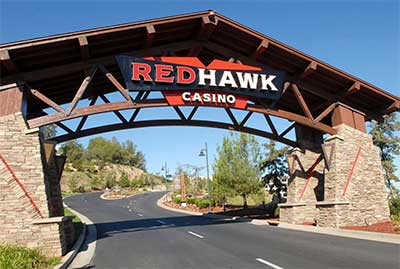
達成を目指すもの
EEMは、直接のユーザーからフィードバックが寄せられるため、将来の機器の問題を排除するための最良の方法の1つです。新しい設計はより適切に構成されており、起動と停止の問題が少なくなるため、製造プロセスに迅速に導入できます。
CMMSが機器の早期メンテナンスにどのように役立つか
レポート: ここでも、CMMSのレポート機能は非常に重要です。技術者は、問題が発生している場所と、問題の原因となっているコンポーネントを具体的に特定できます。その後、数回クリックするだけでソフトウェアから情報を取得し、関係者に送信して修正するだけの簡単な作業になります。
第7の柱–安全、健康、環境(SHE)
SHEの柱は、内部とその周辺の両方で安全な作業環境を作成することを目指しています。安全性の必要性は繰り返し発生するものであり、他のすべてのTPMの柱を実行している間は最前線にとどまる必要があります。
組織は、頻繁な検査、個人用保護具(PPE)の提供などの活動を通じて、従業員と資産を安全に保つことができます。
達成を目指すもの
SHEは、安全で健康的で事故のない職場を目指しています。
CMMSが安全、健康、環境にどのように役立つか
安全と健康は大きな問題です。自己満足の企業は、多額の罰金と厳しい罰則の対象となる可能性があります。このような組織が存在することを回避するために、TPMのSHE段階でCMMSを使用して達成できるものは次のとおりです。
安全計画: CMMSを使用すると、ユーザーは特定のプロジェクトやタスクの安全計画を立てると同時に、複数の機器や場所にまたがる危険を追跡できます。
検査の証明: 事故が発生していない場合でも、外部機関は定期検査の一環として安全検査記録を要求することができます。 CMMSは、コンプライアンスの証拠として検査の記録をすばやく生成できます。
一般的な安全記録: 最新のCMMSソフトウェアを使用すると、ユーザーはMSDS、SOP、機械的および電気的安全チェックリストなどのさまざまな安全関連の記録を保存および取得できます。
第8の柱–管理およびオフィスTPM(AO)
Total Productive Maintenanceのメリットは、プラントフロアに限定されません。この柱は、いくつかの管理機能における廃棄物の問題に対処します。このような機能の例には、調達、事務機器の管理、注文処理などがあります。
達成を目指すもの
管理機能の改善は、製造プロセスに直接影響を与える可能性があります。たとえば、タイムリーな注文処理により、生産の遅延をなくすことができます。
AO TPMは、通信の損失、オフィス機器の故障、記録管理の不備による時間の浪費、ロジスティクスの低さなど、オフィスでの損失にも対処しようとしています。
CMMSが管理およびオフィスTPMにどのように役立つか
特に文書化と調達に関して、プラント労働者と管理スタッフの間にはしばしば断絶があります。 CMMSは、簡単にアクセスできるストレージとして機能し、両方のプロセスを高速化します。
ドキュメント管理: CMMSユーザーは、他の当事者からの助けを待たずに、数秒で情報を保存および取得できます。
在庫管理: CMMSの在庫管理モジュールを使用すると、ユーザーは、オフィスまたは工場のどちらの場合でも、供給を管理し、再注文レベルを監視できます。
組織にTPMを実装する方法
Total Productive Maintenanceは、組織の運営方法を変革するシステムです。確かに、これは迅速な解決策ではなく、会社の業務の規模と複雑さによっては、完全に実装するのに数年かかる場合があります 。
他の製造ツールと同様に、体系的なフェーズで実装されます。以下は、 12ステップのアプローチの概要です。 TPMの実装に。組織は、その時点でのビジネスまたはリソースに合わせて実装プロセスを調整できます。そのため、1つのテスト機器またはパイロット機器で簡単に開始することを選択することも、他のユニットに徐々に拡張する前に、1つのユニット内のすべてのマシンでTPMを実装することを決定することもできます。
A。準備段階
ステップ#1-TPMの発表
適切な審議の後、トップマネジメントはTPMを導入するという決定とコミットメントを宣言します。情報は、部門の会議や電子メールなどを通じてスタッフに届きます。
ステップ2–教育プログラムを開始する
上級管理職から始めて、同社はオリエンテーションとトレーニングプログラムに着手し、トップレベルのマネージャーに何が期待できるかを完全に理解できるようにします。残りのスタッフはすぐにトレーニングを受ける必要があります。
ステップ3–組織のTPMチームを確立する
準備はTPMチームの編成に続きます。これらのグループは、その特定の会社に適した望ましい組織モデルを作成および促進する責任があります。
ステップ#4 –分析と目標設定
受けた総合的設備管理トレーニングと企業文化の分析に基づいて、委員会と上級管理職は次のように進みます。
- TPM方法論で対処できる問題領域を特定します。 CMMSからのデータは、この時点で緊急設備の問題を確認するのに役立ちます。
- 一般的なTPMの原則と目標を設定します。
- プロセスを標準化およびガイドするためのベンチマークをマップする基本的なTPMポリシーを作成します。
- その他の予測される目標をすべて挙げてください。
ステップ5–詳細なマスタープランを作成する
良い出発点は、総合的生産管理を実施するための3年間のマスタープランです。この計画では、とりわけ、TPMの8つの柱のそれぞれを導入するために、どのように、どの時点で行うかを文書化します。
この計画には、TPMの実装に必要なすべての詳細が含まれます。また、組織が運営する固有の問題や課題もカバーする必要があります。これを怠ると、マスタープランが実用的でなくなり、早い段階で深刻な後退を引き起こす可能性があります。
B。キックオフステージ
ステップ#6 –総合的設備管理プログラムを開始します
この段階で、組織は正式にTPMプログラムを開始します。このステップは、この新しいシステムに対する企業の取り組みを意味し、顧客、ベンダー、請負業者、関連会社、およびその他すべての利害関係者を含むすべての利害関係者に広く公開されます。
C。実行段階
企業は、トータルプロダクティブメンテナンスの8つの柱を、適切な順序で導入し始めることができます。
ステップ#7 –メンテナンスの改善を実装する
ここでの目標は、さまざまな機器を最高の動作状態に復元し、計画されたメンテナンススケジュールを確立してから、オペレーターに引き渡すことです。これには、新旧両方のアセットが含まれます。
メンテナンスチームは次のことを行う必要があります:
- 機器をクリーンアップして準備します。
- CMMSを使用して障害履歴を分析し、すべての資産を診断して改善します。
- わかりやすい予防/予知保全計画を立てます。
ステップ#8 –自律メンテナンスの実装
保守技術者から機械オペレーターへのトレーニングまたは責任の移転が行われる前に、ワークフローを中断することなくオペレーターが効果的に処理できるルーチンタスクを正確に決定することが最初に重要です。また、メンテナンスチームは定期的に機器をチェックする必要があり、資産を完全にオペレーターの裁量に任せる必要はありません。
それが決まったら、オペレーターのトレーニングを開始できます。オペレーターは次のことを教えられ、彼らができることを確認するために徹底的にテストされるべきです:
- 必要な検査を特定して実行します。
- 潤滑ポイントにアクセスして、機械を安全かつ正しく潤滑します。
- 異常を検出して報告し、必要な情報をCMMSに入力します。
オペレーターが自律保守で使用できる簡単な保守チェックリストを作成することをお勧めします。機器の上または近くに配置された視覚補助、図、およびグラフは、視覚的なリマインダーとして機能し、エラーを減らすのに役立ちます。たとえば、これは研磨ホイール装置グラインダーの簡単な色付きの図です。 わかりやすいチェックリストが付いています。他のマシンにも適応できます。
ステップ#9 –安全、健康、環境の柱を実装する
安全の重要性は言うまでもありません。 SHEはTPMのすべての柱に関連しており、経営陣は事故をゼロにすることを奨励し、可能であれば報いることができる環境を構築する必要があります。
ステップ#10 –品質メンテナンスを実装する
SHEの柱と同様に、品質の維持は組織のすべての領域に適用され、総合的生産的維持の実施に適用されます。品質が重要でないと見なされた場合、TPMを実装しようとしてもほとんど意味がありません。
この段階では、すべての関係者が製造プロセスの品質欠陥を減らすことを目的とした定められた基準を採用する必要があるため、品質の維持に積極的に取り組むことが重要です。そもそも欠陥を生まない条件を作り、それらの条件を改善するために継続的に取り組むよう努めてください。
これを達成するためのいくつかの方法は、頻繁な監査、資産の手動検査、および状態監視センサーの使用によるものです。
ステップ#11 –オフィスTPMを実装する
ビジネスの管理部門のプロセスを調査することで、損失の原因を簡単に検出できます。次のステップは、これらの非効率性と無駄の領域を阻止するための詳細な計画を作成することです。オフィスで最も損失が発生する一般的な領域には、エネルギー使用量と紙の無駄が含まれます。
すべてのオフィス機器をキャプチャして、追跡とメンテナンスのために特定のスタッフに割り当てる必要があります。
D。設立段階
ステップ#12 –継続的改善
この段階で総合的設備管理の実施は完了していますが、常に改善の余地があります。組織は、総合的なパフォーマンスの向上を目指しながら、すべての部門の定期的な監査を実施する必要があります。
結論
TPMは、製造工場、建物のメンテナンス、フリートのメンテナンス、建設、またはサービス業界のいずれでも機能する、実証済みのシステムです。
それは多くの利点をもたらしますが、完全に実装するには何年もかかる可能性があるため、Total ProductiveMaintenanceには徹底的な戦略と多くの取り組みが必要です。中途半端なアプローチではうまくいきません。
幸いなことに、それをうまく実装した組織は、それぞれのニッチのリーダーになることがよくあります。
保守部門で変更を加える前に、コア保守の操作と手順が適切に設定、定義、および追跡されていることを確認する必要があります。それについてサポートが必要な場合は、チャットしましょう お手伝いできるかどうか確認してください。
2コメント
-
Rakesh Bagle 2020年5月11日、午後10時23分
TPMとTPM8ピラーについてよく説明されています
返信 -
Naveen Kumar 2020年5月21日、午後9時37分
良い記事です。
返信
メンテナンスエンジニアに必ず読んでください。
機器のメンテナンスと修理