Total Productive Maintenance Plan(TPM)を実装する方法
Total Productive Maintenance(TPMとも呼ばれます)の成功した持続可能な実装は、良心的なプラントマネージャーまたは生産リーダーにとって重要な関心事であるはずです。 TPMにより、ダウンタイムが短縮され、停止や故障が少なくなり、製造プロセス中に製品が品質欠陥を被る可能性が低くなります。
なぜTPMはそのような効果的なツールなのですか?つまり、自分の機器の検査と保守に積極的な役割を果たす権限を与えられたオペレーターは、常に生産と機器の信頼性の向上に貢献するからです。
長年にわたる研究により、TPMプログラムの実装と全体的な製造パフォーマンスとの間に正の相関関係があることが確認されています。いくつかの調査結果は、企業が総合的生産的保守計画を実行することにより、失われた生産を約20%削減できることを示しています。それでも、1つの重要な質問が発生します。企業が効果的にTPMを実装するにはどうすればよいかということです。 ?次の情報は、その質問に対処します。
メンテナンスコストの節約に関心がありますか?
ここから、より役立つリソースや研究論文にアクセスできます。
総合的設備管理とは
レビューとして、TPMプログラムには、イニシアチブの最終的な成功を決定する上で大きな役割を果たす少なくとも8つのコアコンセプトが含まれます。これらの8つの概念は次のとおりです。
-
自律保守
TPMのこの基本的な要素は、機械オペレーターなどの保守担当者が自分で定期的な保守管理を実行できるようにするためのトレーニングと権限付与に重点を置いています。 -
焦点を絞った改善
TPMのこの柱は、プロアクティブなメンテナンス手法を指します。つまり、現在のプロセスを全体的な方法で調査し、それを改善する方法を特定します。 -
計画的なメンテナンス
計画されたメンテナンスプログラムは、過去のダウンタイムデータと予測分析を活用して、予想される故障率または予想されるアイドル時間に関する主要なメンテナンスタスクをスケジュールします。 -
品質の維持
品質保守プロセスは、実行されている実際の保守タスクが、エラー検出、欠陥防止、および品質保証の全体的な目的を効率的に達成するように設計されています。 -
初期の機器管理
実務経験のあるオペレーターからのフィードバックを活用して、初期の機器管理により、新しい機器の設計により、機械の寿命、アクセス可能性、および生産性が最適化されます。 -
トレーニング
すべてのTPMプログラムには、オペレーターとマネージャー向けのトレーニングと教育の要素を含める必要があります。 -
安全と健康
すべてのTPMプロセスでは、オペレーターや他の従業員の安全な作業環境を促進するために、安全衛生要因を考慮に入れる必要があります。 -
TPM指向の管理
純粋に機械的な考慮事項とは別に、適切に設計されたTPMプログラムは、注文処理やスケジュール管理などの管理機能も考慮に入れ、生産現場をサポートするためにそれらを改善する方法を探します。
TPMの実装方法
TPMプログラムは特定の企業のニーズや状況に合わせて調整する必要がありますが、 7 以下に示すように、TPMを実装するための基本的な手順:
1。 TPM実装の計画を発表する
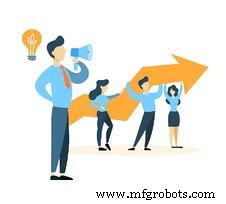
2。パイロットTPMプログラムの領域を特定する
改善が最も簡単な機器、または問題があることが証明されており、収益性を迅速に改善するために修正が必要な生産エリアに焦点を当てることができます。 TPMプロセスのこの初期段階では、SMARTである目標を特定します。具体的、測定可能、達成可能、現実的、および時限です。3。対象となる機器を最高の動作状態に復元することに重点を置きます
パイロットエリアが特定されたら、現在の生産性のベースライン基準を記録します。 TPMの実装の計画を整理して定義します 。 5S手法(並べ替え、設定、輝き、標準化、維持)を使用します。最初に自律保守プログラムの実行に焦点を合わせ、必要に応じて機器オペレーターにトレーニングを提供します。車の所有者が基本的な定期メンテナンスを実行することで修理コストを大幅に節約できるのと同様に、企業も、オペレーターが基本的なメンテナンス手順に定期的に参加できるようにすることで、機械の寿命を延ばし、機械的な問題を早期に特定できます。4。設備総合効率(OEE)の測定を開始します
ただし、OEEを追跡することにした場合は、計画外の停止時間を文書化することが不可欠であり、発生するたびに理由が示されます。オペレーターが停止原因がわからない場合は、「原因不明」または「未割り当て停止時間」のカテゴリーを指定してください。時間の経過とともに、これは最初に特定するのに役立ちます 大きな損失の原因は、ステップ#5につながります。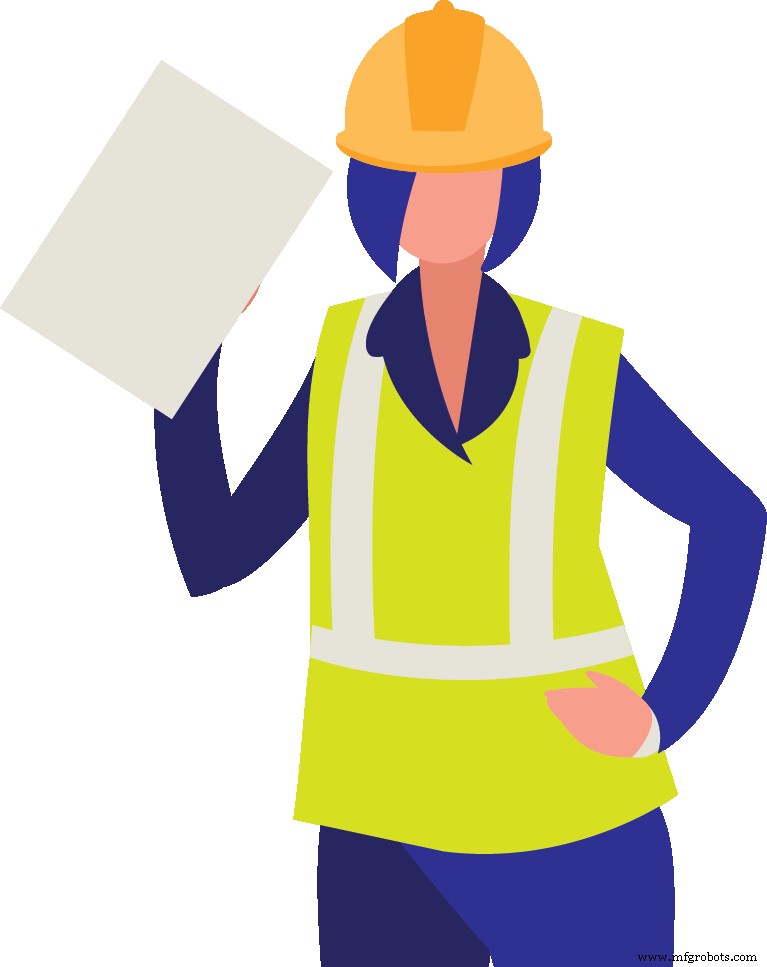
5。主な損失の原因に対処する
このステップでは、ダウンタイムの主な原因の1つを調査するために、約4〜6人の従業員からなる部門の枠を超えたチームを指定する必要があります。 。このチームは、損失の原因を排除するための計画を作成し、このイニシアチブを実行するための計画された停止時間をスケジュールします。たとえば、大きな損失が頻繁なフィラージャムによるものである場合、このチームは現在のオペレータープロセスと修理オプションを調べ、ジャムを停止する計画を作成し、計画を実行する時間をスケジュールします。指定されたアクションが完了すると、今後OEEを測定し、必要に応じてプロセスを再開します。
6。プロアクティブなメンテナンスを実装する
このステップでは、故障や停止時間の防止に重点を置きます。 機器の故障を引き起こす可能性のある主要な「問題点」を特定する 、定期的な予防保守のスケジュールを作成します。最後に、プログラムの有効性を継続的に監視できるようにするフィードバックプロセスを開始します。このフィードバックシステムには、メンテナンスログ、月次または隔月の監査、サーモグラフィおよび/または振動分析からのデータ編集が含まれる可能性があります。
7。必要に応じて特定のTPMの概念を実装する
たとえば、生産現場用の新しい機械を設計および/または設置する場合は、初期の機器管理を活用する必要があります。おそらく、新しい機器の設計は、アクセシビリティの向上、より簡単な洗浄または注油手順、または安全機能の追加を含むように最適化する必要があります。一方、調達の問題や作業指示の処理の遅延がある場合は、これらの管理上のボトルネックにできるだけ早く対処する必要があります。TPMを活用して保守管理を改善する
総合的生産的メンテナンスは、ダウンタイムによる生産損失を削減するための重要な要素です。効果的なTPMプログラムにより、従業員は重要な機械の維持管理に積極的な対策を講じることができます。これにより、生産設備の機能寿命を延ばすことができます。 TPMの実装は、品質の欠陥と最適ではない実行時間を削減するのにも役立ちます。
企業資産管理プラットフォームや関連プログラムなど、企業のTPM実装を支援するツールは数多く市場に出回っています。最終的な分析では、総合的設備管理計画は適切な設計と実行のためにいくらかの努力を必要としますが、そうすることの見返りは投資する価値があります!
機器のメンテナンスと修理