加工プロセス ルートの開発方法
試作加工のメーカーとして最先端のCNC設備を有し、より複雑な構造のワークピースの加工を得意としています。ワークピースを機械に取り付ける前に、エンジニアは通常、機械加工プロセス ルートをシミュレートします。参照される原則は次のとおりです。
機械加工プロセス ルート参照の原則
1.1次加工基準面
できるだけ早く後続のプロセスのベンチマークを提供するために、位置決め基準面としてプロセス内の部品を最初に処理する必要があります。
2.処理段階の分割
高い加工品質が要求される表面は、加工段階に分けられます。一般に、粗加工、半仕上げ、仕上げの 3 つの段階に分けることができます。主な目的は、処理の品質を保証することです。機器の合理的な使用に役立ちます。それは熱処理プロセスの整理に便利を提供します;原材料などの欠陥のタイムリーな検出を容易にします。
3.穴の後の最初の面
ハウジング部品、ブラケット、コネクティングロッドなどは、穴加工より先に平面加工を行ってください。これを平らな面に配置して穴を加工し、平らな面と穴の位置精度を確保し、平らな面での穴の処理を便利にすることができます。
4.仕上げ工程は最後に配置する
研削、ホーニング、精研削、転造加工、その他の仕上げ工程などの主表面の仕上げ工程は、機械加工工程経路の最終段階に配置する必要があります。加工後のワークの表面粗さがRa0.8以下の場合、わずかな衝突で表面が傷つくことがあります。工程間の移動やワークピース間の取り付けによる表面の損傷を避けるため、通常、仕上げプロセス後に手や他の部品でワークピースに直接接触することは許可されていません。
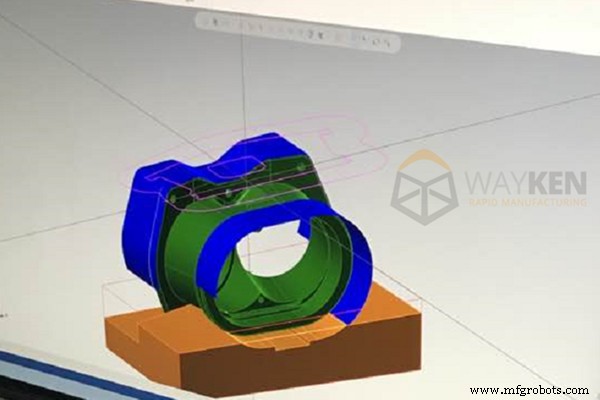
機械加工プロセス配置の一般的な状況を紹介した後、特定の状況に遭遇したときの次の原則を紹介します。
加工工程ルートを開発する際の考慮事項
1.荒取りと仕上げを別々に
荒加工のワークピースは、切削工具の切削量が非常に大きいため、ワークピースは大きな切削力とクランプ力を受け、ワークピースの表面は多くの熱を発生させ、より重要な加工硬化の表面を引き起こします現象が発生すると、ワークピースの大きな内部応力が発生します。荒加工と仕上げ加工を連続して行うと、完成品の内部応力が再分配され、ワークピースの寸法精度が限界を超えてしまいます。高精度が要求される一部の部品では、部品の内部応力を除去するために、通常、粗加工後、仕上げ前に低温アニーリングまたはエージング プロセスが配置されます。
2.適切な機器の選択
荒削りは主にワークピースの加工代を切り落とすことであり、加工精度の要件はそれほど高くないため、荒削りはパワーが高く、精度が高すぎない工作機械で行う必要があります。仕上げ加工には工作機械の高い精度が要求されます。粗加工と微細加工を加工精度の異なる工作機械に配置することで、設備の能力をフルに発揮させるだけでなく、精密工作機械の寿命を延ばすことができます。
3. 熱処理工程はよくアレンジされています
熱処理プロセスの場所の配置は、次のように参照できます。(1) 機械加工前のアニーリング、正規化、焼き戻しは、金属の切削性能を向上させることができます。
(2)荒加工後の時効処理、焼き戻しは、ワークピースの内部応力を仕上げ前に除去できます。
(3) 機械加工後の浸炭、焼入れ、焼き戻しは、部品の機械的特性を向上させることができます。熱処理後のワークの変形が非常に大きい場合は、次に別の最終加工プロセスを配置する必要があります。
まとめ
部品の機械加工プロセスを開発する場合、部品の生産の種類が異なるため、工作機械と機器、クランプとゲージ、ブランク、および作業者の技術的要件を追加するために使用される方法が大きく異なります。
CNCマシン