ショップシェア ライトアウト 学んだ教訓
午後3時頃平日は毎日、カスタム ツール ショップの担当者がターニング センターのセットアップを開始し、夜間に消灯してジョブを実行します。
ヤング兄弟にとって、製造現場の自動化は、既存の CNC ターニング センターに棒材供給機を追加することから始まりました。
これは、ギレンとボブ・ヤングが 2008 年にテネシー州クックビルのカスタム ツールを購入した直後に起こりました (ジレンは社長、ボブは副社長です)。スタッフのいる日の時間は、以前の会社の管理方法と比較して、店舗文化の大幅な変化を表しています。つまり、手作業の自動化は考えられていなかったので、買収前は給与計算さえ手作業で行われていました。
現在、さまざまな自動化の例が実装されており、ショップはさまざまな方法でそれらから恩恵を受けています。たとえば、サブスピンドル、ライブ ツーリング、およびパーツ コレクターを備えた 2 つの新しいバー供給 Y 軸ターニング センターを、ショップで利用可能な 15.5 時間のうちの生産時間を可能な限り確保しながら、パーツの機械加工を完了することを目標に、夜通し稼働するようにセットアップできます。スタッフがいません。作業現場の従業員の多くは、機械への単純な積み降ろしから解放され、プロセスを改善する方法をよりよく検討し、提案できるようになりました。多くの場合、これらの有益な提案は、既存の手作業の自動化 (部品のバリ取りを機械加工サイクルに統合するなど) に関連しています。さらに、新しい検査技術により、夜間に機械加工された複数の部品の一部の測定ルーチンが自動化されました。
Custom Tool は最近、約 10 年前に確立した「生産ログ」計画戦略のためのデータ収集を自動化しました。オペレーションのバックボーンとなっている生産ログは、予想される 1 日の生産量と比較して、ショップの機械が 1 日にどれだけ効果的であったかを明らかにし、ショップがどれだけの「盗まれた時間」をポケットに入れているかを示します。 (これは、毎晩 15.5 時間無人の兄弟のニックネームです。) また、ショップが年間の自動機械加工時間の割合を 50% 以上に増やすことを目指しているため、夜間生産に適した仕事を特定するのにも役立ちます。総生産。ボブが言うように、無人の機械加工時間は、はるかに低いコストで 2 回目のスタッフシフトに相当します。
バーフィーダーの後
Bob Young がサイト運営を管理し、Gillen (AT&T Consulting の IoT ソリューションのチーフ アーキテクトとしても働いている) はジョージア州アトランタにいます (彼は時間が許す限り頻繁にショップを訪れます)。 2 人は、以前は工作機械の販売代理店で働いていた Bob が、定年を間近に控え、出口を探していた前の所有者から連絡を受けて、Custom Tool の購入を決定しました。
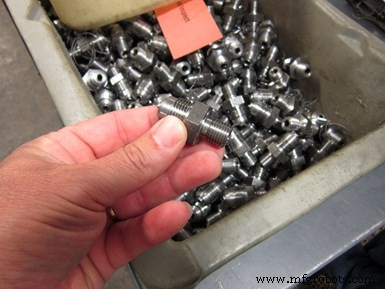
この燃料フィッティングは、ショップが夜間に無人で行った最初の仕事です。工具の摩耗を補うために 2 つのねじ切り操作に冗長工具を使用し、完全自動で加工できる部品の数を 2 倍にしました。また、この写真が撮影されて以来、このショップは特別なツールを使用してインサイクルバリ取りを実行し、二次的な手作業によるバリ取り作業をなくすようになりました。
兄弟たちは、会社の文化を変えることが不可欠であることをすぐに理解しました。 2 人は、可能な限り自動化を実装することを視野に入れて、継続的な改善の考え方を浸透させることに取り組み始めました。ある程度の自然減を考慮して、彼らは新しい人々を何人か雇いました。その多くは比較的若く経験の浅い人々で、高度なテクノロジーをより受け入れやすく、プロセスを合理化する方法を提案する傾向がありました.
最初のバーフィード ターニング センターの無人加工の利点を見て、完全自動加工が現実のものになる時を思い描いた後、Custom Tool は 2012 年にさらに多額の投資を行い、Y 軸の Okuma LB3000 EX Spaceturn をライブで追加しました。一部の部品の完全な機械加工を可能にするツーリング、サブスピンドル、Edge Technologies バーフィーダー。ショップは 2016 年にそのような機械をもう 1 台追加し、2019 年 1 月に 3 台目を追加しました。
とはいえ、完全自動加工のメリットを享受するには時間がかかりました。ショップは、新しい機器に慣れ、夜通しの加工作業の可能性を検証する必要がありました。それから、店が夜通しうまく処理できることを完全に確信するまで、夕方に向けてますます長い時間にわたってジョブを実行し始めました。信頼性の高い無人プロセスを確立するためにいくつかの要素が考慮され、ショップはその過程で多くの教訓を学びました。これらのいくつかは以下に関連しています:
- クーラント システム。 予期せぬクーラント圧の低下やクーラント供給の中断により、工具が破損する可能性があります。夜間に稼働する機械は、1 シフトのみを稼働する機械よりも多くのメンテナンスが必要です。そのため、ブースター ポンプ フィルターは通常、1 つのシフトを実行する機械で数日おきにチェックされる場合、そのフィルターは毎日チェックする必要があります。さらに、Custom Tool の 2 番目の Y 軸ターニング センターには、クーラント システムの問題を検出した場合に機械を停止する信号を送信するコントローラーが備わっています。
- <強い>
Bob Young が上級編集者の Lori Beckman に説明しているように、完全自動機械加工プロセスを開発する際には切りくず管理を考慮することが重要です。このユニットは、ターニング センターが夜間に無人で稼働する場合に、長く糸のようなアルミニウム チップをより適切に処理できるようにするコンベヤーの歯を特徴としています。
チップコンベア。 すべてのチップコンベアが同じというわけではありません。 Custom Tool の最初の Y 軸ターニング センターには従来のユニットがありますが、2 番目のユニットには、コンベヤに歯が付いた Hennig ユニットが搭載されています。若い兄弟は、このコンベヤは、アルミニウムを機械加工するときに一般的に生成される長くて糸のような切りくずをより効果的に除去するため、他の機械よりもこの機械で一晩アルミニウムジョブを実行する可能性が高いと述べています.これにより、部品収集システムを妨げる可能性のあるチップの「鳥の巣」がなくなります。 - パーツ コレクション。 当初、チップ ホッパーはパーツ コレクターの役割も果たしていました。現在、各ターニング センターにはパーツ コレクターが統合されています。コレクターのサイズは、夜間の生産量に対応できる必要があります。生産能力が小さすぎると、夜間に生産できる大型部品の数が制限されます。さらに、収集されたパーツごとにクーラントが出てくるため、パーツ コレクターからクーラントを排出してマシンのサンプに戻す何らかの手段が必要です。
- バーフィーダー。 ジョブのパーツがかなり大きい場合、バーフィーダーの能力によって、一晩で加工できるパーツの数が制限される可能性があります。一方、サイクル タイムが非常に速い場合は、積み込まれた棒材をすべて消費する可能性があります。つまり、夜通しの部品生産が減少しないように、材料を補充するために誰かが店に来る必要があります。
- 冗長なツール。 示されている 2 種類のねじ山を備えた燃料フィッティング パーツは、カスタム ツールが冗長ツールを使用して一晩実行するように設定した最初のジョブでした。オペレーターが待機している状態でこのジョブを実行すると、そのオペレーターは、工具の摩耗によりオフセットの変更が必要になる時期を知ることができました。しかし、工場では、2 つのねじ切り工具のオフセット調整が必要な時点であったため、最初は 4 時間しかその作業を行うことができなかったことがわかりました。それを認識した工場では、工具の摩耗が問題になる直前に、特定の部品数で工具交換を要求する冗長なねじ切り工具の使用を開始しました。この工場では、ねじ切り工具インサートの潜在的な寿命をすべて引き出すことはできませんが、機械を無人で稼働できる追加の時間はこれを正当化します。
- 負荷の監視。 スピンドル負荷監視機能により、負荷がゼロになると、工具が破損したことを意味します。パーツ プログラムは、ジョブを実行し続けて後続のツールを壊す危険を冒すのではなく、マシンがその時点で停止するように記述されています。
- 測定能力。 何百もの部品を一晩で加工できるのは良いことですが、その無人生産により、一部のカスタム ツールの製造現場の従業員が毎日何を始めるべきかが変わりました。部品の分離、検査、機械の評価、および次のジョブのセットアップのために時間を確保する必要があります。実際、工場が最初に完全自動生産を導入したときは、部品の検査がボトルネックになりました。検査ルーチンを高速化するために、Custom Tool は Keyence IM シリーズの画像寸法測定システムを追加しました。このシステムは、デバイスにセットアップされた 1 つまたは複数の部品の多数の外部部品の特徴を自動的に測定および記録できます。
プロダクション ロギングの自動化
Bob が 2011 年に実装した生産ログは、工場の 9 台の CNC マシンと 1 台のロボット溶接セルが毎日どの程度生産的であるかを、それぞれの毎日の計画作業と達成された実際の生産量を比較することで明らかにしています。また、店舗が利用可能な夜通しの時間をどれだけ効果的に利用しているかも明らかになります。
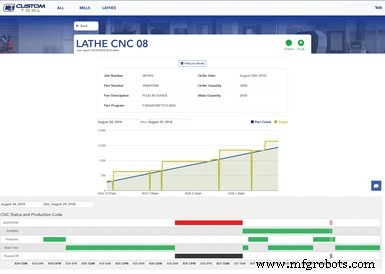
自動データ収集システムは、 20分ごとにマシン。また、ショップの ERP ソフトウェアからジョブ データを取得します。その後、レポートを作成して、生産ログ情報をよりグラフィカルに表示できます。写真提供:カスタム ツール
最近まで、このデータはすべて手動で収集されていました。従業員は、1 時間ごとに各マシンの部品生産番号を記録し、それらの値とマシン ステータス コードを生産ログ スプレッドシートに入力します。ショップは、コード 10 と 15 の値を最大化するよう努めています。これは、ショップの 1 日シフト中の生産時間と夜間の無人生産時間をそれぞれ表しています。これらの値を予想される毎日の生産量と比較すると、実際の機械の稼働率が明らかになるとボブは言います。セットアップ、再加工、材料、ツーリング、またはオペレーターの注意を待つ時間などのその他のコードは、実際の加工時間に加えて、ジョブを完了するのにかかる正確な時間を明らかにします。
各ジョブのステータスを追跡するために、共通の変数が設定されています。部品数は G コードで処理され、部品サイクルが完了するたびに 1 ずつ増加します。その他の変数には、オペレーターの入力が必要です。これらには、ラン ターゲット (部品数がその値に達するとマシンが一時停止します)、ジョブ番号 (これはジョブ トラベラーに記載されています)、および生産ログ コード (生産ステータスが変更されたときに表示されます) が含まれます。
生産ログは、自動運転に適したプロセスを特定するのに役立ちます。終夜稼働するように設定されたマシンが 15.5 時間の利用可能時間に近づいていない場合、このジョブは夜間の稼働にはあまり適していない可能性があります。または、あるマシンが一晩中稼働し、別のマシンが半夜稼働する場合、おそらく、半夜しか稼働していなかったジョブを別のマシンにプッシュし、稼働時間の長い他のマシンの作業に置き換えて、より高い使用率を達成することが理にかなっています。生産ログは、機械が目標生産値を下回った原因となったツールの破損やバーフィーダーの誤動作などの問題を記録するために使用されるため、一種の日記としても機能します。
ショップは、生産ログのデータを収集して入力するために、1 時間ごとにマシンを訪問する必要がなくなるというシナリオに向けて取り組み続けています。これは、Gillen が開発中の自動化されたデータ収集およびレポート システムのおかげです。このシステムは、Web ベースの産業用モノのインターネット (IIoT) プラットフォームを使用して、オープンソース MTConnect 通信プロトコルのエージェントを備えたマシンからデータを取得します。 Jobboss エンタープライズ リソース プランニング (ERP) ソフトウェア。プラットフォームは、IIoT モジュール、ソフトウェア、および接続サービスとソフトウェアを提供する Telit の Devicewise for Factory です。
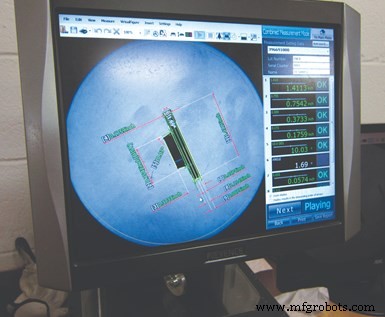
消灯加工とは、朝の現場スタッフの到着を待っている部品が多いことを意味します。カスタム ツールの場合、これが検査のボトルネックとなり、ショップは品質管理担当者の部品測定を高速化するために画像寸法測定装置を追加することになりました。
Gillen 氏によると、このシステムの利点は、さまざまなコントローラーと連携し、データ収集にカスタム プログラミングが必要ないことです。以前に機械から手動で収集されたすべてのデータ (部品数、機械コードなど) と ERP データ (ジョブ番号、ジョブの説明、注文日、注文数量、配達日など) を自動的に引き出して保存するように構成されています。それをクラウドに。 Web ダッシュボードからデータにアクセスできます。その後、レポートを作成して、以前は運用ログ スプレッドシートで利用できたものをよりグラフィカルに表示できます。
このシステムは、2018 年 6 月初旬から 20 分ごとにデータを収集しており、実行中のマシンのエントリを見逃すことはありませんでした。 Gillen 氏は、利用可能な優れた機械監視製品が数多くあると述べています。しかし、彼の技術的なバックグラウンドは、ショップが最も知りたいビジネス情報に対処する社内ソリューションを検討する機会を与えてくれました。彼はまた、このデータ収集機能は、切削時間を特定の種類の切削工具やインサートに結び付けるなど、さらに高度な分析にもつながる可能性があると感じています.
産業機器