射出成形で製造するための設計が必要な理由
すべての製造プロセスにおいて、すべての段階が確実に確実に実行され、適切に実行されることが不可欠です。材料の選択から実際の製造に至るまで、コストと品質のバランスを見つけることが不可欠です。射出成形プロセスでは、製造/製造可能性(DfMとも呼ばれます)の射出成形設計は、上記のすべてを確実に順守するプロセスです。
製造用の射出成形設計は、基本的に部品設計の改善と強化に関係しています。それはあなたの部品が生産に経済的に適合し、生産が容易であり、その機能的義務を果たすことを保証します。ただし、DfMは射出成形の設計だけを扱っているわけではありません。また、適切な材料の選択、射出成形金型の設計、製品のリードタイム、品質、使用に伴う危険性の評価などについても説明します。
この記事では、製造に設計を使用することの重要性と利点、および製造にプラスチック部品を設計する際に考慮すべき要素について説明します。このページには、製造用の射出成形設計を評価するための簡単で信頼性の高い方法もあります。
射出成形におけるDfMの重要性
クライアントとして、あなたは間違いなく生産コストを可能な限り最小限に抑えたいと思っています。したがって、製造プロセスの射出成形設計は不要なステップと見なされる場合があります。ただし、これはその後の問題につながるだけであり、必要以上にメンテナンスと修理のコストが高くなる可能性があります。
プラスチック部品のDfMプロセスが射出成形の生産に不可欠である他のいくつかの理由は次のとおりです。
1。製造の実現可能性の保証
すべてのプラスチックの設計および製造プロセスの開始時に、設計された部品が製造に適している可能性は比較的不明です。製造チェックの設計がないと、多くの製造プロセスは、生産が可能かどうかを判断する前に、実際の生産段階に到達する必要があります。
ただし、製造工程の射出成形設計により、製造工程の実現可能性を最初から判断することができます。メーカーは、部品が金型に詰まったり、3Dプリントが崩壊したりするなど、製造上の問題が発生したかどうかを確認できます。これにより、時間と資本を節約し、製品を手頃な価格で生産のタイムスケールを短縮できます。
2。部品の故障の防止
プラスチックの設計および製造プロセス中に発生する可能性のある最悪の事態は、完成した部品が意図した機能を実行できないことです。これは、部品の物理的な欠陥またはその他の機械的機能障害が原因である可能性があります。
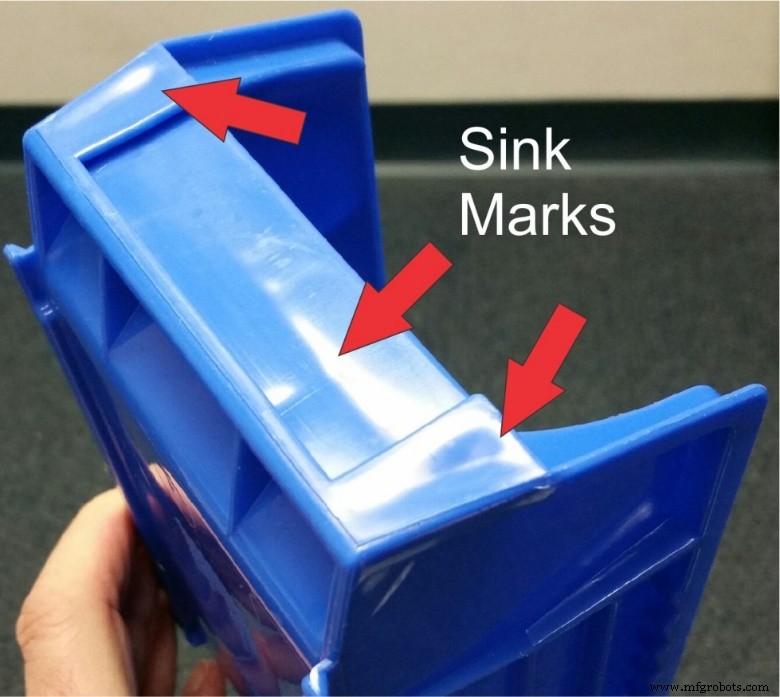
これらの欠陥により、クライアントは部品の製造コストを2倍にする必要が生じる可能性があります。その結果、生産コストが増加します。生産プロセスは、クライアントにとって不採算になる可能性さえあります。
3。製造の複雑さの決定
部品の射出成形設計を行った後、機械工が製造を容易にするために使用しなければならないさまざまな複雑さはまったくわかっていません。ただし、製造用の射出成形設計を評価した後、エンジニアはアンダーカットやドラフト角度の使用など、さまざまな複雑さを判断できます。これにより、生産段階に向かう不確実性が少なくなります。
また、射出成形金型の設計は、この要因の恩恵を受けます。射出成形金型の設計段階から複雑さを理解することで、金型の構造と形状がより明確になります。また、これはプロトタイプの作成に役立ちます。
これらのオプションとは別に、製造用のプラスチック部品の設計で防止できるその他の問題には、次のものがあります。
- シンプルなデザインに高価な部品を使用する。
- 非常に複雑な部品や射出成形金型の設計などを簡素化する。
製造プロセスの射出成形設計は重要ですが、一部の製造業者は製品を製造するときにそれを省略しがちです。ほとんどの場合、このプロセスに必要な人員または必要なソフトウェアが不足していることが原因である可能性があります。これは、小規模な地元の契約製造業者の間で一般的です。
ただし、RapidDirectでは、製造用の射出成形設計を伴う高品質の射出成形サービスを提供しています。射出成形の専門家チームと最新のソフトウェアをすべて備えており、部品の製造に不規則性や改善がないか評価します。
射出成形プロセスのDFM中に考慮すべき要素
製造のための射出成形プロセスを最適化するために、設計者は次の段階に進むために設計をクリアする前に多くの要因を考慮します。これらの要因は、材料の選択や工具の考慮から機械加工方法自体に至るまで、生産の多くのセクションを考慮しています。このような要因の例は次のとおりです。
1。材料の選択
プラスチック材料の選択は、プラスチックの設計と製造において非常に重要な準備プロセスの1つです。パーツが意図した環境で機能できるかどうかを判断できます。メーカーが選択しようとすると、次のような多くのプロパティが考慮されます。
- 材料の収縮率
収縮とは、射出プロセス後に成形品が冷えるときの成形品の寸法の変化です。すべての材料は異なる収縮率を持っています。収縮率は、プラスチックのファミリー、メルトフローインデックス、および加工条件(射出圧力など)などの多くの要因に依存します。部品の収縮率は、その性能と形状に影響を与える可能性があります。
- アセンブリ
機械工は、材料の選択時に、機械的固定、溶接、接着などの組み立てプロセスを処理するプラスチック材料の能力も考慮します。この要素は、検討中の部分がより大きな矛盾の一部である場合に必ず作用します。
- コスト
プラスチック材料の望ましい属性は重要ですが、コストを考慮することも重要です。これは、多くの機械工がプラスチックが持たなければならない他の属性と一緒に考慮しなければならない重要な要素です。ただし、設計者はプラスチックの購入コストだけを考慮しているわけではありません。また、プラスチックの仕上げ、機械加工、メンテナンスのコストなどの他の要素も考慮します。これにより、製造コストを可能な限り最小限に抑えることができます。
2。ドラフト
パーツのドラフトは、プラスチックパーツの垂直壁の狭さまたはテーパーの程度です。部品の角度は、機械工が製造用のプラスチック部品の設計で考慮する要素にとって重要です。その理由は、プラスチック部品のドラフトは、完成した部品を金型から簡単に排出するために不可欠であるためです。製造工程の射出成形設計では、設計者はドラフト角度が金型の方向にあるかどうかを評価します。これは、金型が開き始めたときに成形品を簡単に排出するためのクリアランスを確保するために重要です。
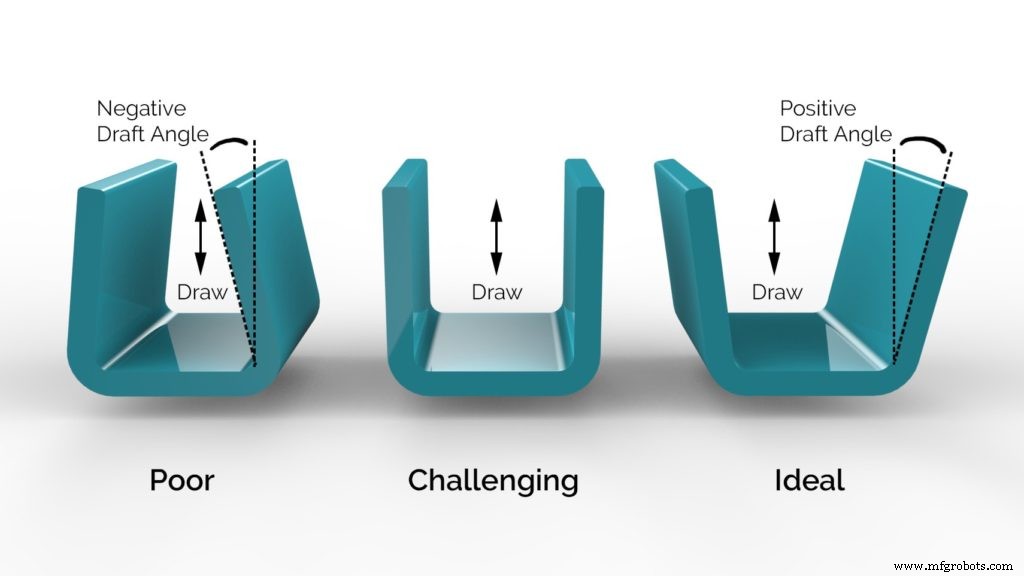
一般に、ドラフトの角度は、パーツの寸法に応じて1度から2度の間で変化します。また、分離するときは、すべてのパーツドラフトを金型の動きと平行な方向に設計することをお勧めします。これは、厚い壁の作成を回避するのに役立ちます。
3。壁の厚さの均一性
製造用の射出成形設計では、設計者は部品の壁の厚さの均一性を徹底的にチェックします。これは、部品の壁の厚さの一貫性が、完成した部品の多くの欠陥を防ぐのに役立つためです。これは、厚さが不一致であると、プラスチックが流れるときにプラスチックの流れが不均一になる可能性があるためです。
肉厚が不均一な部品の場合、通常、材料はより厚い領域に流れ込みます。これにより、薄い領域の充填が不十分になる可能性があります。ただし、このフローの順序は、パーツのゲートの位置によって異なります。また、厚みが不均一な場合、形状が変形する可能性があります。これは、厚い領域の冷却が遅くなる傾向があるためです。したがって、冷却が不均一になると、部品に物理的な欠陥が生じる可能性があります。
ただし、パーツのいずれかのセクションでさまざまな厚さが必要な場合、設計者は可能な限りスムーズに移行する必要があります。これにより、樹脂の流れの乱れが最小限に抑えられます。
4。ゲートの場所
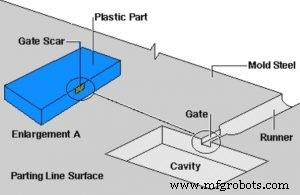
ゲートは、成形品とランナーシステムの間の通過領域です。それらは、金型への樹脂の流入に不可欠です。これらは、ランナーから部品のさまざまな領域への樹脂の流れを方向付けるガイドとして機能します。製造プロセスの射出成形設計では、設計者はゲートを検査して、樹脂の流れを妨げるのを防ぐのに十分な大きさであることを確認します。ただし、大きすぎてはならないため、機械工はランナーをパーツから簡単に分離できます。
5。肋骨の使用
メーカーが部品に厚い壁を使用する理由の1つは、部品の強度を高めるためです。ただし、これは、部品の変形、ボイド、およびその他の欠陥につながる可能性があるため、あまりお勧めできません。ただし、リブを使用すると、壁の厚さを増やさずにパーツの強度を増すことができます。
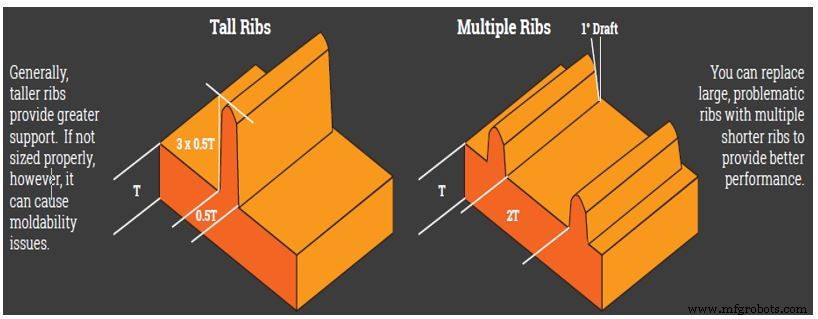
リブの厚さは、相対的なパーツの厚さの50〜70パーセントの範囲である必要があります。このように、パーツにはストレッチマークがなくなります。
6。エッジとコーナーに半径を追加する
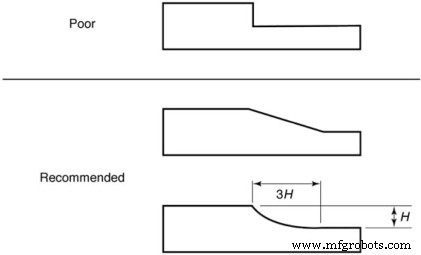
エッジとコーナーの半径は、射出成形金型の設計で設計者が考慮するもう1つの要素です。鋭いエッジとコーナーを使用すると、そのような接合部に応力が蓄積する可能性があります。ただし、十分な半径を追加することで、設計者は応力の集中を排除します。また、樹脂材料の流動性も向上します。これを行うと、部品の強度と製造の容易さも向上します。
7。アンダーカット
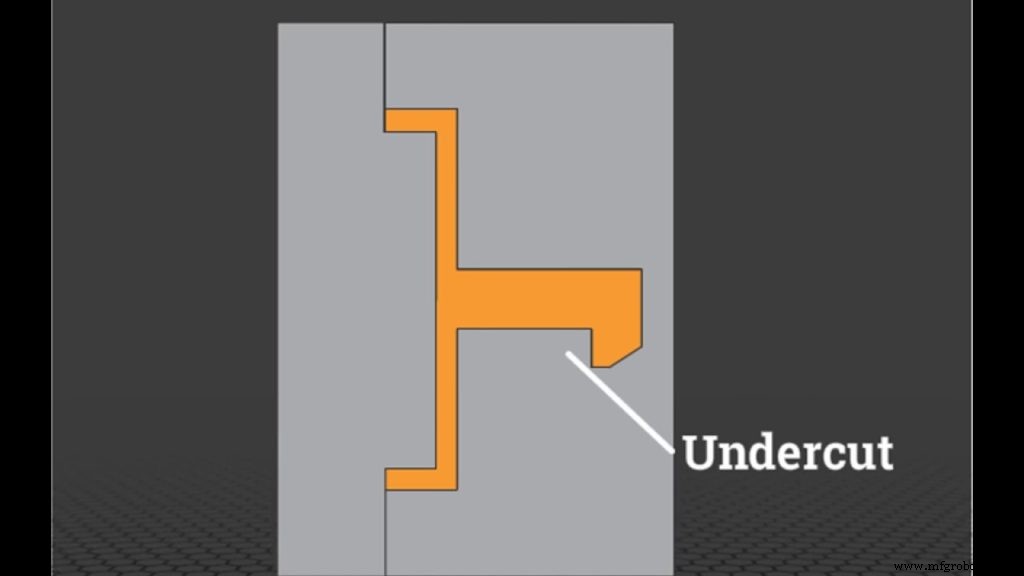
アンダーカットは、さまざまなプラスチック部品の射出成形金型設計に含まれるキャビティまたは突起です。設計者は通常、より大きな構造に組み立てることを目的とした部品にそれらを含めます。ただし、これらのキャビティまたは突起は、金型からの部品の排出を妨げる傾向があります。また、それらを追加すると、射出成形金型の設計と製造のコストと複雑さが増します。したがって、避けられないと思われるパーツでは、パーツのフィーチャーを描画された線に対して垂直方向に配置することをお勧めします。
RapidDirectがプラスチック部品DFMを処理できるようにする理由
単純でも複雑でも、すべての部品で製造プロセスに射出成形設計を使用する必要があります。製造機能用のプラスチック部品設計を使用すると、部品製造の段階を最適化する方法をいつでも見つけることができます。ただし、DfM調査は、どの業界にも割り当てる仕事ではありません。最良の結果を確実にするために、経験豊富な射出成形業者のチームにこれを処理させるのが最善です。
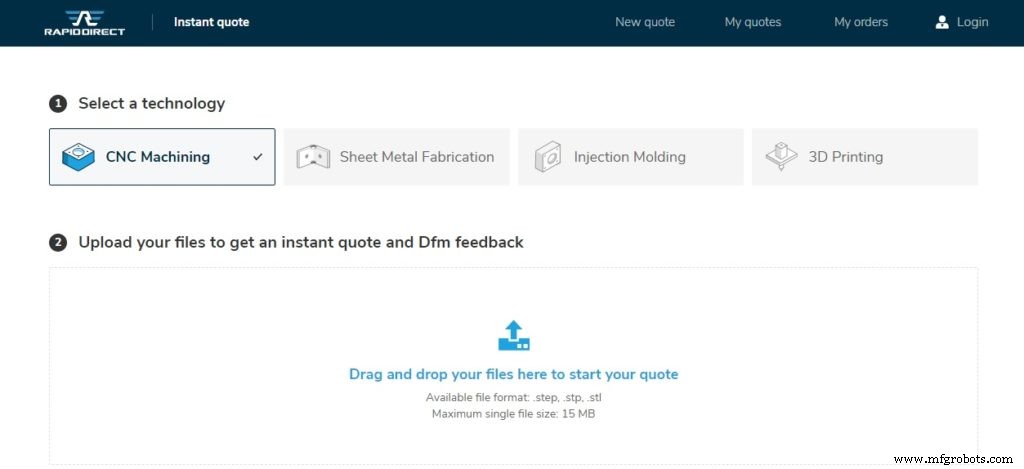
これが、RapidDirectで射出成形の仕事を外部委託する必要がある理由です。設計者、製造エンジニア、機械工、工具エンジニアの専任チームにより、製造可能性の提案に最適な設計を提供し、生産を費用効果が高く、可能な限り簡単にします。
製造のための射出成形設計を実行できますか?時間がありませんか?それとも、プロセスをどのように処理するかについてのアイデアさえありませんか? RapidDirectがお手伝いします。
プラスチック部品DFM分析の利点
製造分析のためのプラスチック部品設計の利点は、部品製造のさまざまな段階に影響を与えるため、非常に多くあります。メリットの例は次のとおりです。
1。リードタイムの短縮
製造用の射出成形設計により、射出成形業者のチームは、製造プロセスを改善するための最適な提案を考え出します。これにより、製造プロセスが非常に簡単かつ迅速になり、製品のリードタイムが向上します。
2。市場投入までの時間の短縮
最適化された生産プロセスからの迅速なリードタイムにより、製品所有者は短期間で製品を市場に投入できます。これにより、所有者の製品は、競争の激しい市場向けの製品で競合他社よりも優位に立つことができます。
3。生産コストの削減
クライアントとしての生産コストを削減し、それでも高品質の部品を生産する方法ほど楽しいものはありません。これはまさに、製造プロセスの射出成形設計が提供するものです。この評価プロセスにより、高品質の部品を製造しながらコストを削減する方法を見つけることができます。
4。より高品質の部品
その機能を果たせない部品は誰も望んでいません。プラスチック部品のDfMを使用すると、その環境で部品が最適に機能する可能性を確実に予測できます。
5。無駄を減らす
製造工程の射出成形設計を行わないと、時間と資源の浪費につながる可能性があります。これは、製造された部品が意図した機能を果たせず、製造プロセスを繰り返す必要が生じる可能性があるためです。製造用に設計されたプラスチック部品を使用すると、これらのシナリオを簡単に防ぐことができます。
結論
部品製造のプロセスは、製造プロセスの射出成形設計なしでは完了しません。これは、このDfMプロセスが製造プロセスの最適化に役立ち、それによって使用される材料と費やされる時間を節約できるためです。製造プロセスに最適な射出成形設計を入手するには、RapidDirectに今すぐお問い合わせください!
複合材料