ホットドレープフォーミング
2021年3月の記事「AdvancingOOAinfused wing box」のこのオンラインサイドバーは、 CW をまとめることを目的としています。 何年にもわたってホットドレープが1つの場所に形成され、うまくいけば、有用なリソースを提供することについて書いています。以下は、2010年から2020年までの複数の記事からの抜粋であり、ホットドレープ成形が複合材料の製造を自動化するのにどのように役立つかを示すのに役立つ写真が付いています。
2010、GKN Aerospace、A400Mスパー
差出人:「複合翼桁は巨大なターボプロップエンジンを搭載しています」
GKNAerospaceのテクニカルディレクター兼最高技術責任者であるPhilGraingerは、初期のA400Mスパーで行われたように、このような大部分を手動で構築するのは遅く、通常は0.75kg / hr(1.5 lb / hr)のレイダウン率であると説明しています。ただし、連続生産中は、自動テープ層(ATL)を使用して部品が平らに配置され、その後ホットドレープが形成されます 帝王切開の形に。この時点で、25 kg / hr(50 lb / hr)のレイアップ率が達成可能になります。グレインジャーは、これらは実際の部分で、シフト全体で達成可能な平均レートであることを強調しています。
プロセスを自動化するために、GKN Aerospaceは、MTorres(スペイン、ナバラ)によって製造された20m / 63フィートのベッドを備えた大型ATLに投資しました。 ATLは、Cytec Engineered Materials Ltd.(現在は英国レクサムのソルベイ)が提供する977-2炭素繊維/強化エポキシユニテープを使用して、一方向プリプレグから開発された形状で複雑なプリフォームを配置できます。帝王切開を形成するために、プリフォームはテープ層からホットドレープフォーマーに移動されます 機器メーカーのAeroformLtd。(Poole、Dorset、UK)から提供されました。真空引きを容易にするために、レイアップは、DuPont Electronic Technologies(Circleville、Ohio)が提供するKaptonポリイミドフィルムで作られた2つのダイアフラムの間に挟まれます。フィルム間の隙間を空けてから、部品の上から赤外線加熱を行い、1時間かけて60°C / 140°Fまで温度を上げます。これにより、ルートエンドの最も厚いセクションの中央にある材料でさえ、同じ温度に均一に暖められます。次に、圧力を穏やかに加えてラミネートを形成し、スパーの内面を正確に表す軽量ツール上で2つのダイアフラムによって拘束されます。このC成形プロセスは、20分間で非常にゆっくりと達成されます。 (成形後、カプトンフィルムは廃棄されます。)
2014、FACC、A321フラップ
差出人:「FACCAG:Aerocompositespowerhouse」
プラント3では、さまざまなフラップ、フェアリング、および飛行制御面が製造されています。ここでも、自動テープ敷設(ATL)とホットドレープ形成による効率 悪用されます。後者は、コアと柔軟な成形パッドを使用して平らなATLプリフォームに熱と圧力を加え、3次元形状を生成します(図7を参照)。一例として、進行中の A321 フラップの製造。Fill(オーストリア、グルテン)がカスタム設計した最先端の自動ワークセルを使用しています。
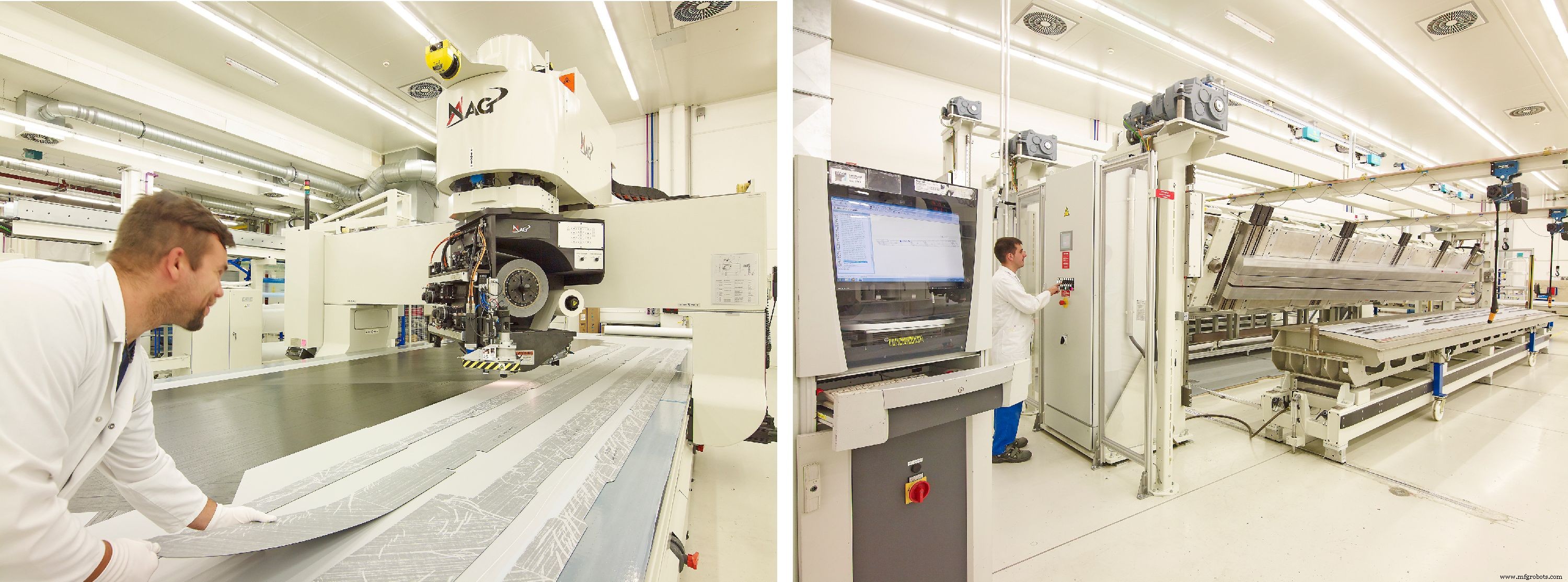
2018、塗りつぶし、自動プリフォーム
差出人:「自動プリフォーミング、パート7:Gesellschaftの充填」
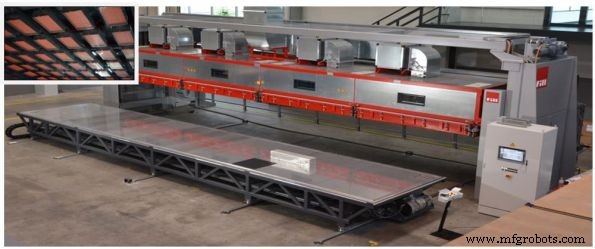
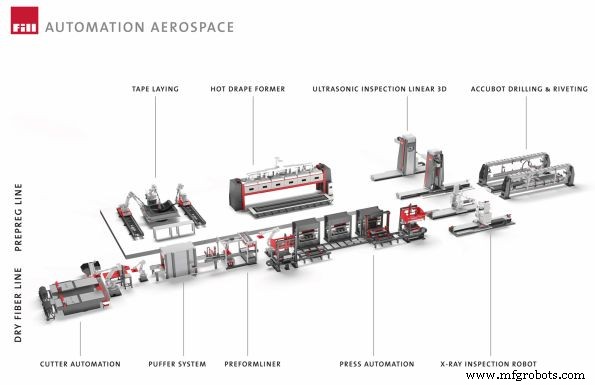
サラブラックと私がイスラエルでの高性能複合材料について書いた最近のツアー記事では、ほとんどの企業がホットドレープフォーミングを使用していることに気づきました。 。実際、Elbit Cycloneで、ツアーガイドのJonathan Hulatyは、ボーイング787アセンブリの梁と支柱について、「ホットドレープ成形なしでこのタイプの高速プリプレグ部品をどのように製造するかわかりません」と述べています。 ホットドレープフォーマー(HDF) また、FBMとイスラエルエアロスペースインダストリーズによって不可欠であると見なされています。
フィルは、FACCで生産されているいくつかのユニットを含め、HDFシステムを何年にもわたって供給してきました。それらは基本的に真空成形システムであり、赤外線または他のタイプの発熱体と、硬化前にツール上のプリプレグレイアップを加熱および圧縮(デバルク)するための再利用可能なシリコーンゴム膜を備えています。 HDFは、以下に示す完全なエアロコンポジット生産ラインの重要な部分になります。
2018、FBM、787パーツ
差出人:「起業家精神にあふれた金属中心の企業の合併は、コンポジットを最初に主張します」
CW 最初にクリーンルームに導かれ、そこで労働者はさまざまな部品をレイアップします。今日、それぞれがコンピューター化されたレイアップアシストコンピュータースクリーンを備えた多くのステーションで、焦点はボーイング787の部品です。わかりやすいタッチスクリーンは、各プライのレイアップ角度とその状態を明確に示します。各ツールに配置されます。 Century Design(San Diego、CA、US)の「ギロチン」マシンは、中央に直径2mの回転テーブルとナイフの刃があり、カーボン/エポキシプリプレグから角度の付いたプライをすばやく切断できます。 787ドアサラウンド用のツールは、通常は幅よりも長く、長さ数センチメートルから長さ約2メートルまでの形状の鋼製マンドレルであり、数百のフレーム、ブラケット、およびクリップを製造するために使用されます。 Assyst-Bullmer Inc.(Wakefield、UK)の自動フラットベッドカッティングテーブルは、レイアップ技術者が1回の操作で最大50枚の積み重ねられた層を切断するために使用されます。
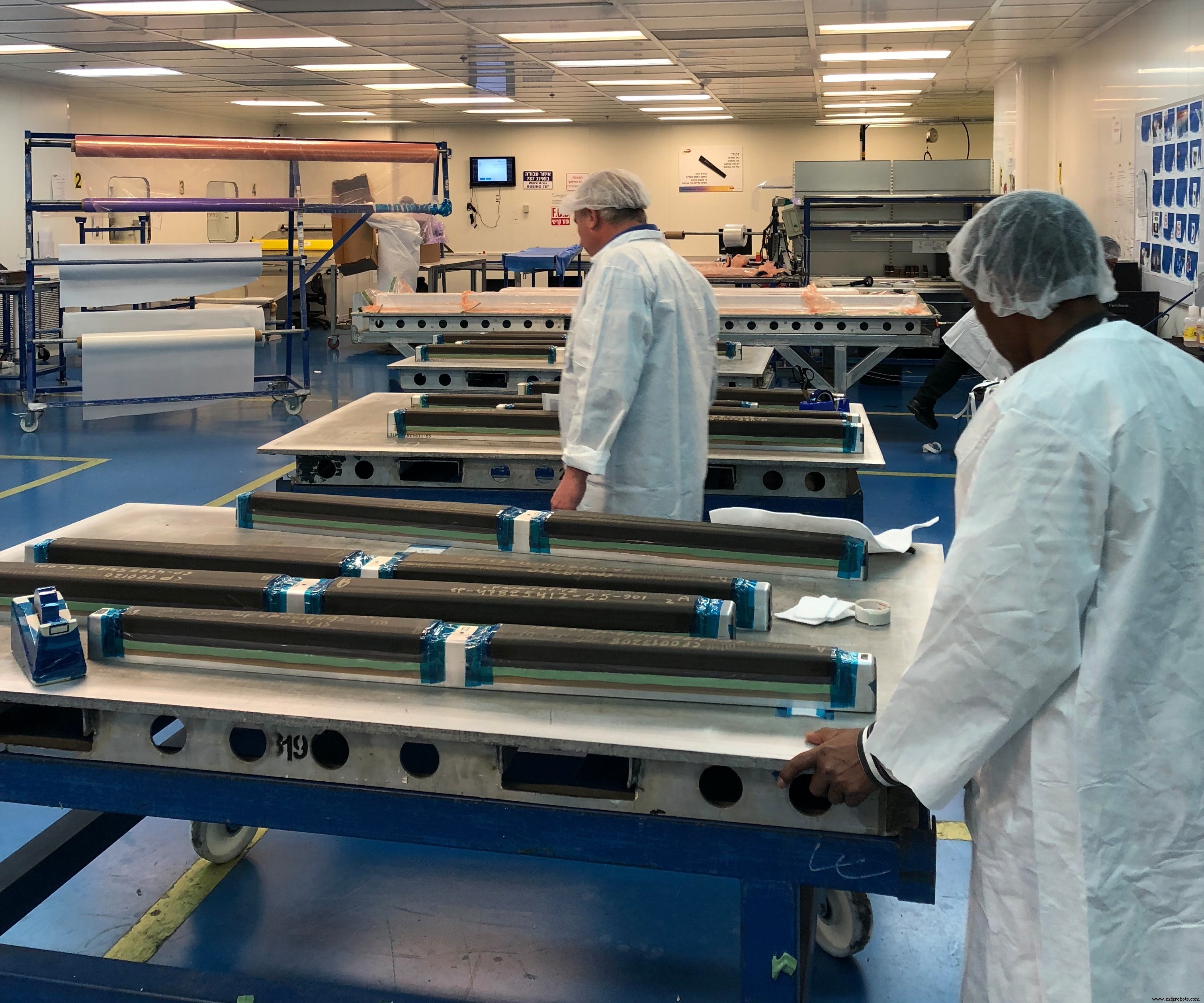
さまざまな小さなオートクレーブ部品用のFBMのクリーンルーム内での小さな部品の切断、キッティング、およびレイアップ。 Photクレジット: CW 、サラブラック。
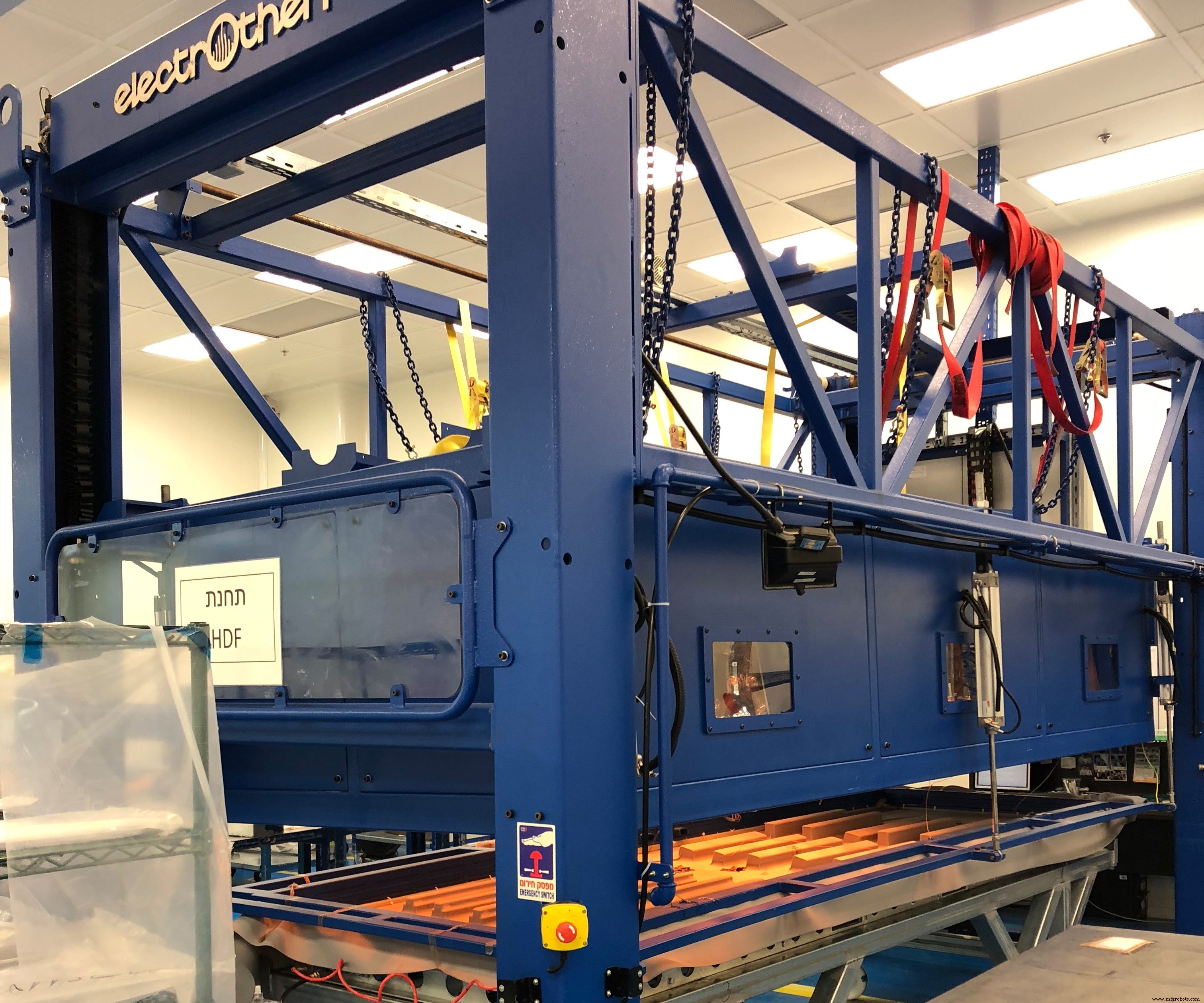
イスラエルの企業ElectrothermIndustryが提供するFBMのホットドレープ成形機は、中間の減量ステップを削除し、1回のショットで50もの一方向プライを成形し、硬化前にFBMのレイアッププロセスを加速したことで評価されています。写真提供者: CW 、サラブラック。
クリーンルームはホットドレープフォーマー(HDF)によって支配されています 。 ElectroTherm Industry(Migdal HaEmek、イスラエル)によって製造された静的機械(同社はカート上で可動バージョンも製造しています)は、赤外線加熱要素と複合材料を加熱および圧縮するためのシリコーンゴム膜を備えたカスタムメイドの真空成形システムです硬化前のツールのレイアップ。 HDF 中間の減量ステップなしで、50もの積み重ねられた層を形作ることができる、とPolikerは言います。プリプレグが加熱され、 HDF に統合された後 、袋詰めする前に、レイアップ全体にコールを配置します。炭素繊維複合材で作られたコールは、粗い表面仕上げを示します。 Polikerは独自の素材の詳細を明らかにしませんが、177°Cのオートクレーブ硬化温度に耐えることができると述べています。「マッチドダイツールをシミュレートします。」彼は、マンドレルツールは必要に応じて社内で再調整されると付け加えています。バギングと消耗品は、Airtech International(Huntington Beach、CA、US)から供給されます。
2018、Elbit Cyclone、787パーツ
差出人:「イスラエルと米国で複合材料の世界にサービスを提供する」
右側では、ボーイング787部品のクリーンルームの作業員が、小さなクリップや支柱から複雑なJビーム、Iビーム、Cビーム、マルチピースのノーズランディングギアドアまで、さまざまな部品のプリプレグを配置しています。プリプレグは、Assyst Bullmer(Wakefield、UK)自動ファブリックカッターとギロチンマシンを使用して切断され、任意の角度で厚いスタックを切断します。プリプレグ冷凍庫はクリーンルームに隣接しています。 Hulatyは、プリプレグのスタックがカットされ、キット化され、冷凍庫に戻されることがあると述べています。クリーンルーム全体に配置されたAlignedVision(Chelmsford、MA、US)レーザープロジェクションシステムは、手のレイアップを支援します。
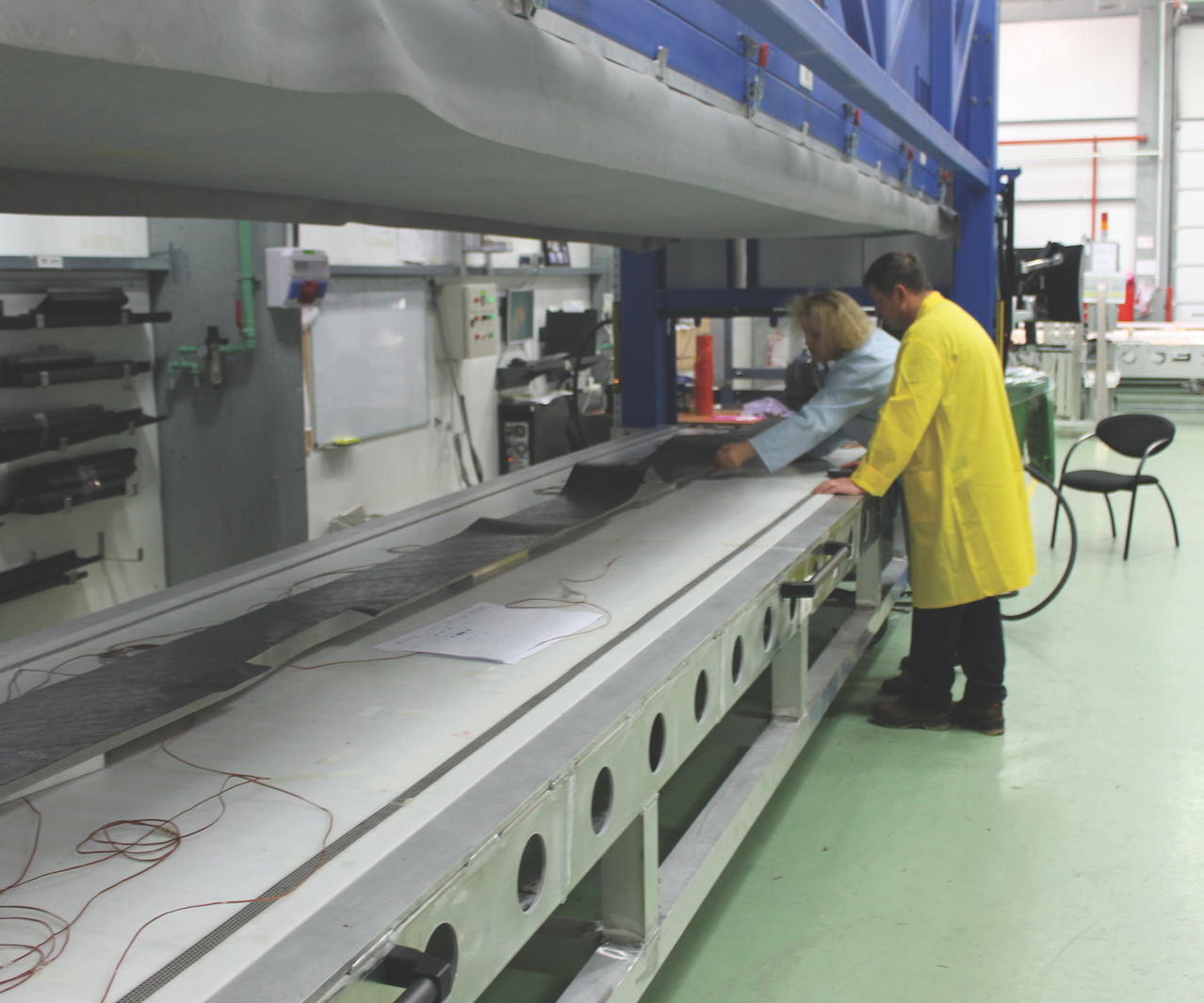
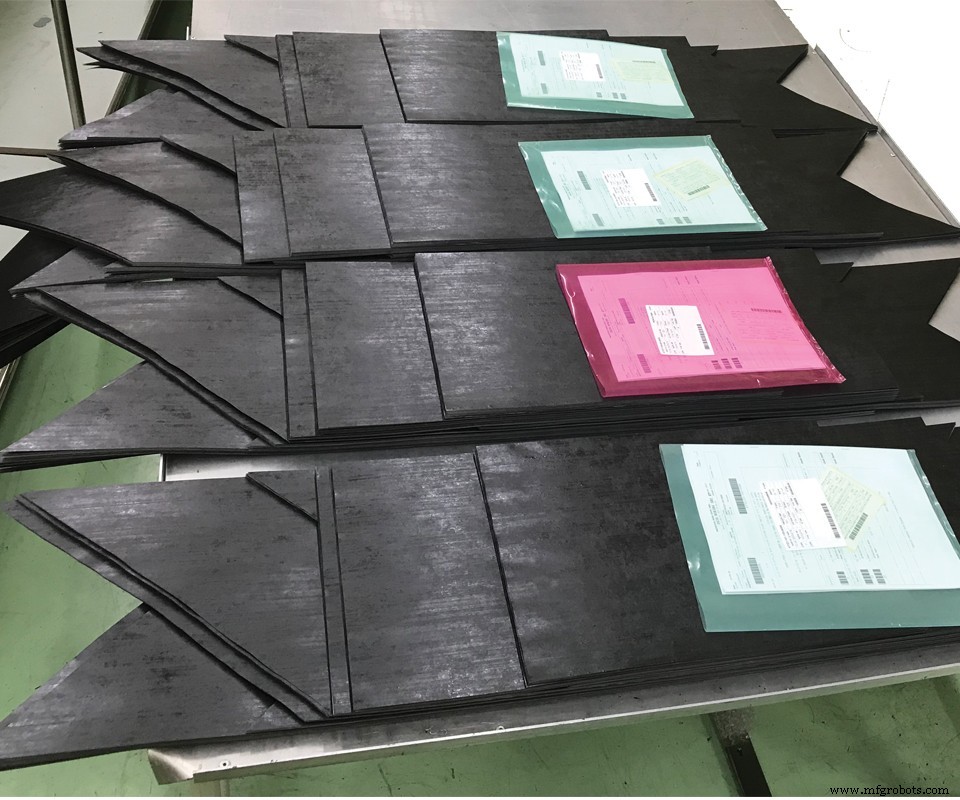
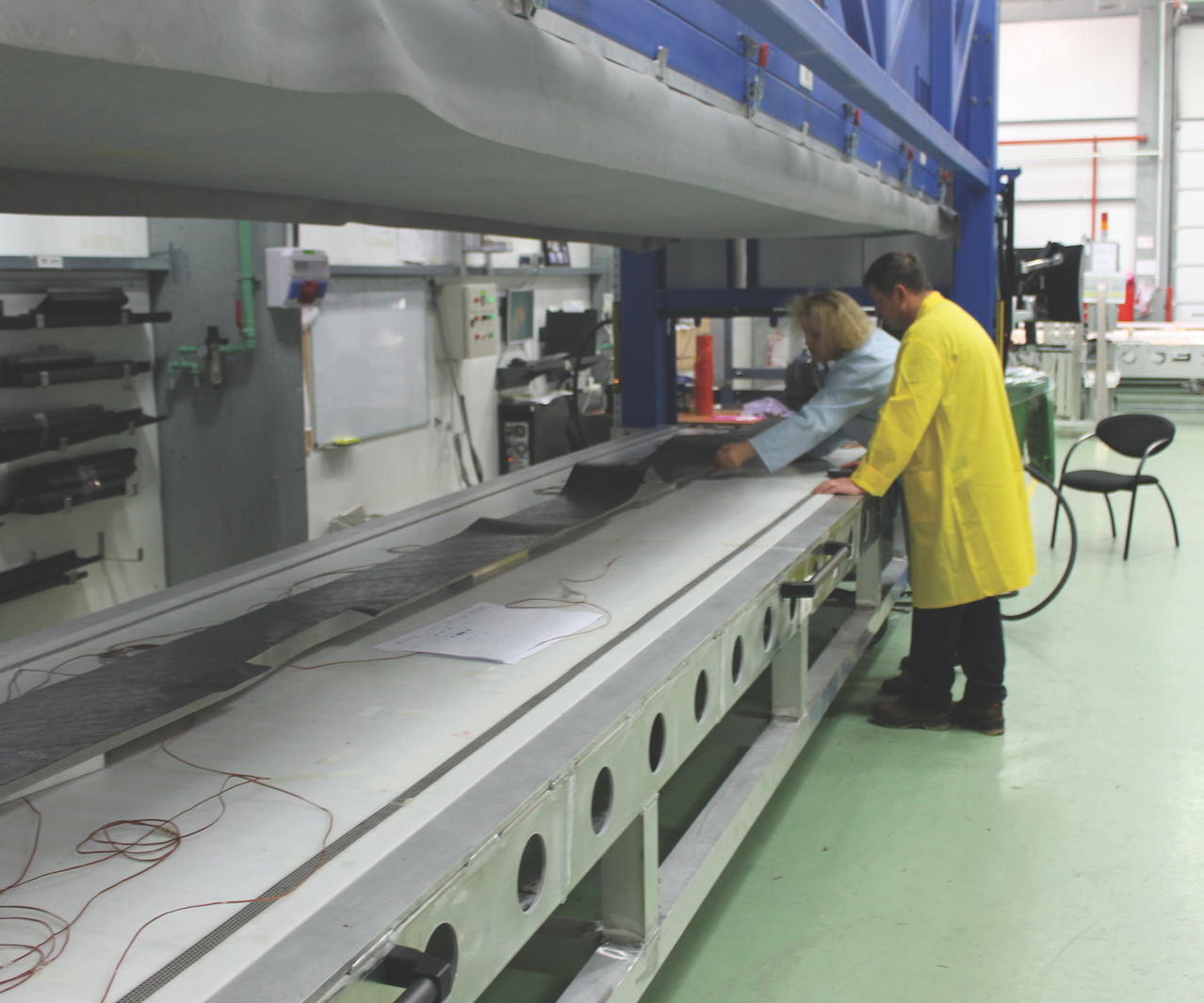
炭素繊維強化プラスチック(CFRP)の床梁部品は、男性の金属マンドレルに配置されています。 Hulatyは、合理化されたプロセスについて詳しく説明しています。「最初にプリプレグスタックを配置してから、マンドレルに適用します。これにより、ツールに少しずつ適用する場合に比べて、時間を大幅に節約できます。その後、レイアップは独自の設計のCFRPコールで覆われ、部品の100%の再現性を確保するのに役立ちます。」
ホットドレープフォーミング 機械はクリーンルームの後壁に沿って配置され、サイクルごとに多くの部品の減量を可能にします。 「ホットドレープを形成せずに、このタイプの高速プリプレグ部品をどのように製造するかはわかりません」と、梁や支柱などの部品に関してHulaty氏は言います。それでも、彼はこのステップがボトルネックではなく、オートクレーブでもないことを認めています。 「硬化後の最後の機械加工がボトルネックです」と彼は続け、長い床の梁部品の場合、単純なスタックを積み上げて硬化後に機械加工する方が速いと説明します。 「一度に硬化する部品をたくさん積み重ねることができるので、オートクレーブは問題ではありません」と彼は付け加えます。 「したがって、実際には、硬化サイクルごとに良好な生産率が得られます。」
2018、IAI、航空構造
差出人:「イスラエルの航空防衛の要は、より大きな世界的支援の準備ができている」
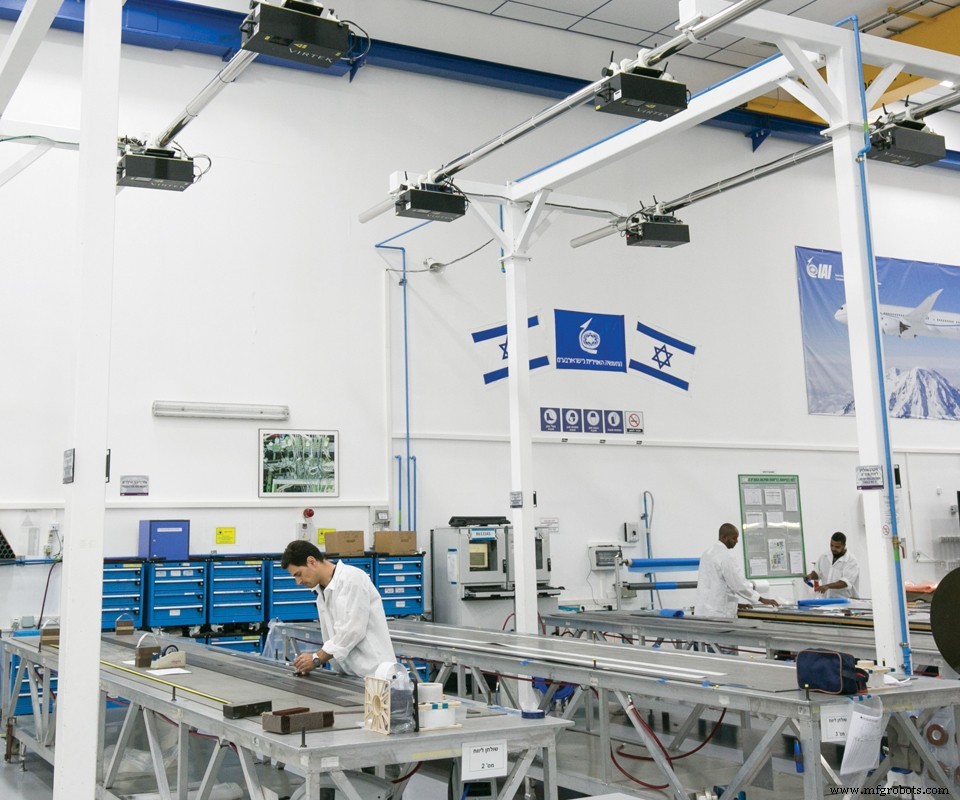
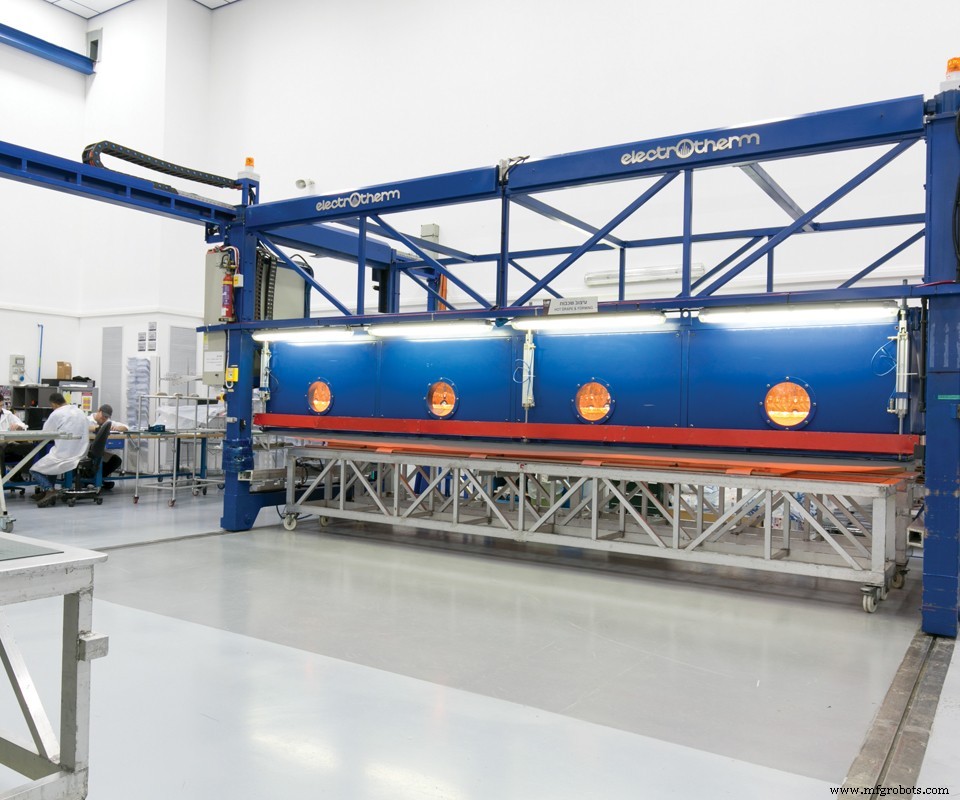
IAIは、ホットドレープ成形機を使用して、厚いプリプレグレイアップをまとめて減量し、従来の中間減量ステップの必要性を排除します。写真提供者:Israel Aerospace Industries
IAIの複合事業は、ビジネスジェットや商用航空機、無人航空機(UAV)、軍用機の部品製造と組み立てに及びます。製造される部品には、垂直尾翼と水平尾翼、舵、翼構造、エンジンナセル、フロアビーム、ドアサラウンド、構造バルクヘッド、リブと補強材、操縦翼面、フェアリング、レードームが含まれます。その製造能力の中には、プリプレグハンドレイアップと自動テープレイアップ(ATL)、ホットドレープフォーミングがあります。 、樹脂注入や樹脂トランスファー成形(RTM)などの液体成形プロセスに加えて、複雑な接着と組み立てを含むオートクレーブおよび脱オートクレーブ硬化(OOA)。同社はまた、独自のツールを設計および構築し、すべての主要な航空宇宙および複合材料の品質認証を保持し、包括的な非破壊検査および検査を通じて品質保証を提供しています。
- IAIの生産能力は非常に高く、10個のオートクレーブがあり、そのうち7個はAero-assembliesDivに属しています。サイズの範囲は、長さ4.5m、直径2mから、長さ14m、直径4.7mの最大のものまであります。
- プリプレグレイアップは、ホットドレープフォーミングを使用して硬化する前に減量されます Electrotherm Industry(Migdal HaEmek、イスラエル)の機械(6.9 x 2.7 x 3.1m)。
2020、Strata、A350-900船内フラップ
差出人:「StrataはA350-900用に100隻の船内フラップを納入します」
航空機の翼の総揚力能力を高めるように設計されたIBF [船内フラップ]は、離着陸時の翼の表面を増やし、飛行中の安定性を向上させるために、翼の後縁に取り付けられています。 Strataは、ホットドレープフォーミング(HDF)を使用して、IBF製造プロセスを完全に自動化することを計画していると述べています。 今年初めに第1部認定(FPQ)とFAIの設計および品質検証を取得した、コンピューター制御のロボット自動テープレイアップ(ATL)マシン。
プロセスの一環として、同社は HDFマシンがカーボンファイバーコンポーネントをプリフォームすると述べています。 航空機部品の場合、高品質の複合部品のより迅速な製造を可能にし、その赤外線放射加熱システムは炭素繊維を迅速かつ均一に柔らかくして正確な部品を提供し、ストレスのしわがないと言われています。さらに、Strataの2台のATLマシンは、一方向のプリプレグ材料をフラットベッドに配置してから、さらに処理するために金型に移します。 Strataによると、2.5メートル×10メートルの作業範囲により、大規模な複合レイアップの自動処理が可能になり、別の超音波切断機が不要になり、処理時間が短縮されます。
2020、Techni-Modul、ウィングリブおよびストリンガー
差出人:「将来の航空構造物の生産のための圧縮RTM」
「私たちにとって、OPTICOMSは自動化にも関わっていました」とChevallet氏は言います。 Techni-Modul Engineeringは、OPTICOMSプロジェクト用のC-RTM噴射システムだけでなく、ピックアンドプレースロボットとホットドレープフォーミング(HDF)も提供しました。 機械、すべて完全に自動化された生産セルに統合されています。 …「ロボットによるピックアンドプレースを使用して、従来の手動によるプライの積み重ねを自動化しました」とChevallet氏は言います。 「ロボットは自動カッターからプライを取り出し、加熱されたプリフォームツールに転送します。 これは圧縮テーブルに置かれます[ステップ1と6]。」ピールプライ(ステップ6の青いフィルム)、ブリーザー(ステップ6の白い素材)、ヒンジ付きの再利用可能な真空膜(ステップ2と6の左側の水色)を適用し、真空と加熱を行って事前に成形し、空気を取り除きます。テキスタイルスタック(ホットドレープフォーミング、HDF )薄い熱可塑性ベールを溶かして、圧縮されたプリフォームを作成します。
OPTICOMSウィングリブとストリンガー
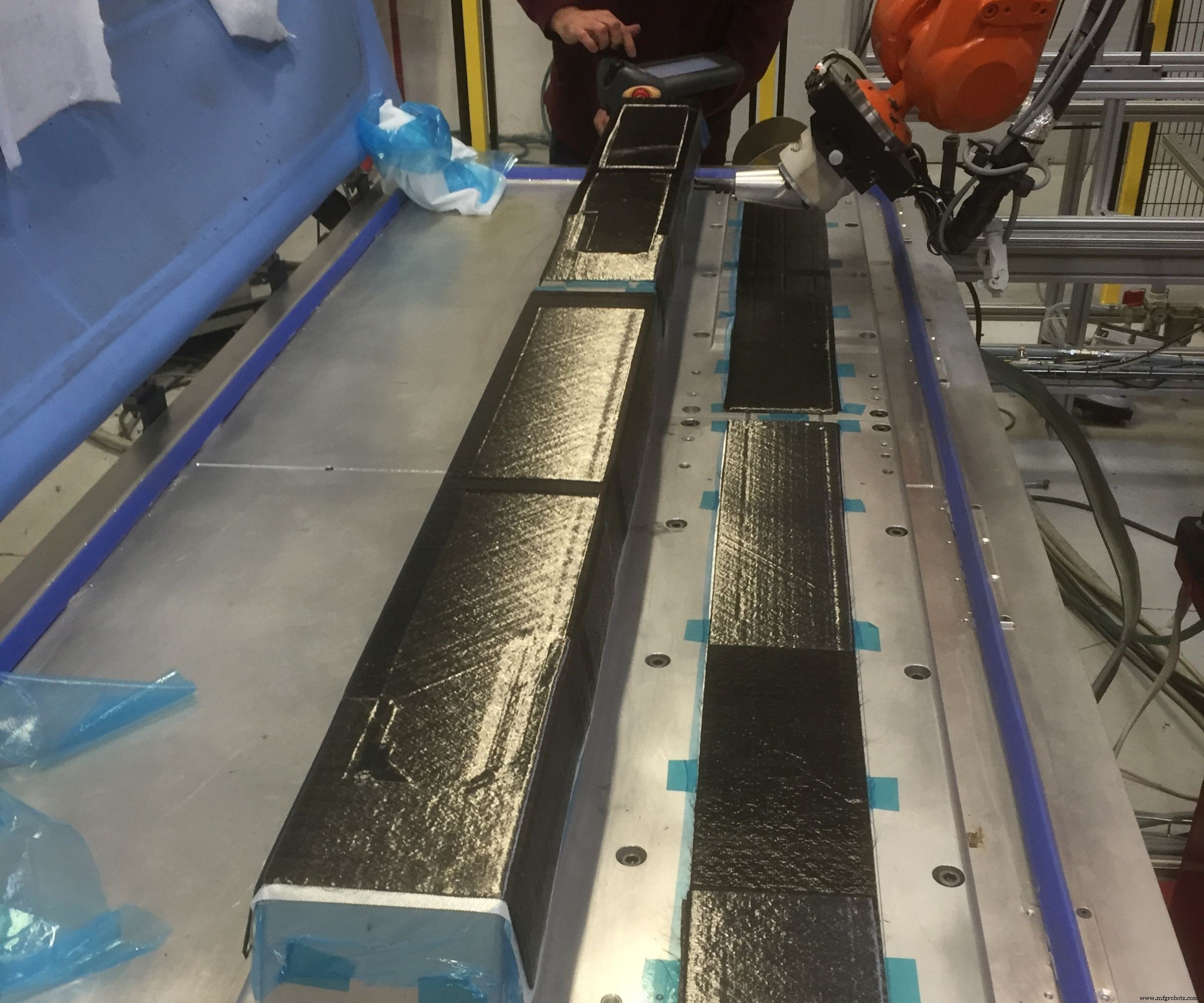
ステップ2.予備成形ツールは、レイアップ中に5〜8プライごとに加熱されたデバルクを完了するために使用されるヒンジ付きの再利用可能な真空膜(左側の青)を備えた圧縮テーブルに配置されます。写真クレジットすべての画像:Tecni-ModulEngineering。
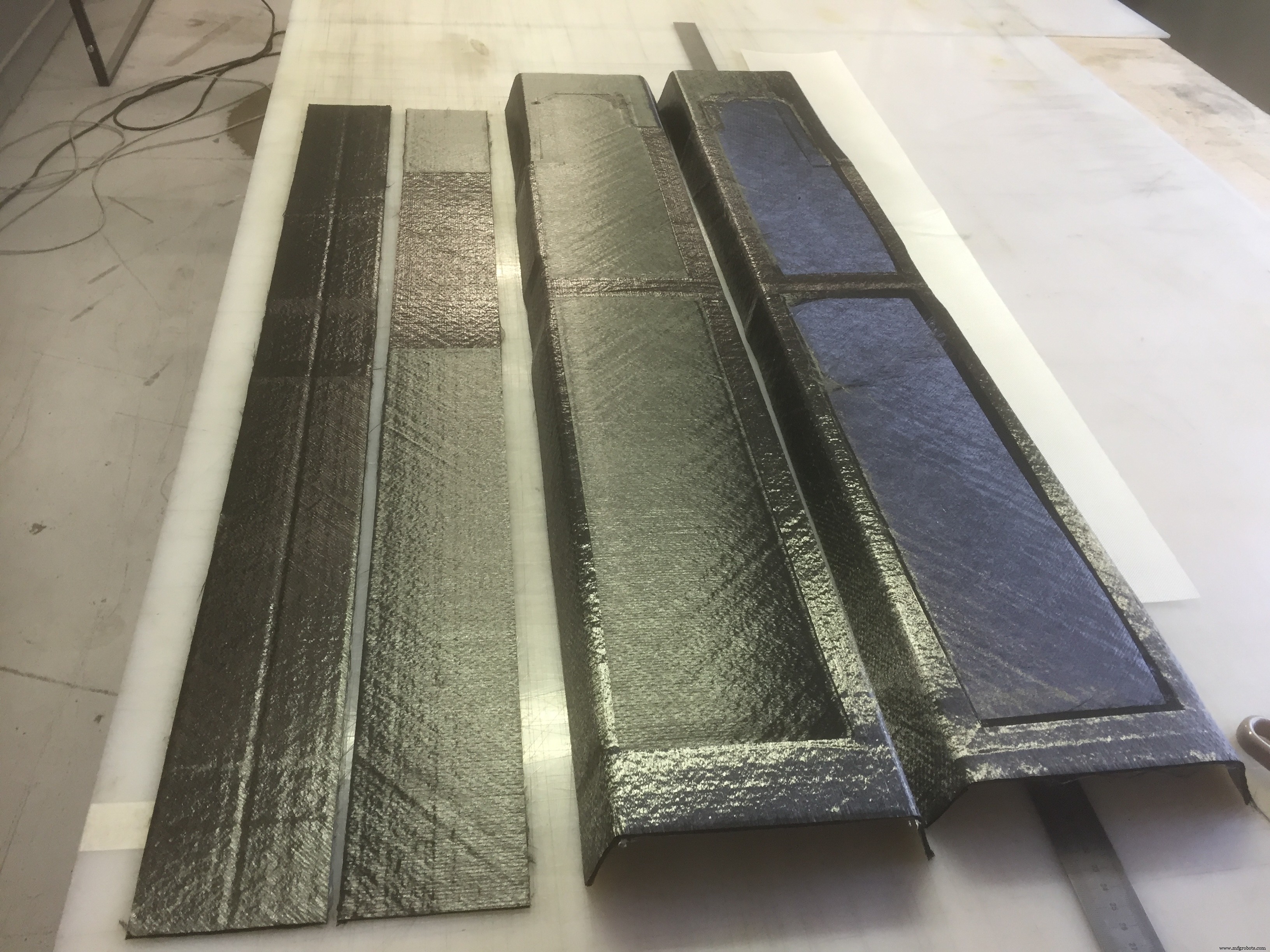
ステップ3.ストリンガープリフォーミングサイクルごとに、1つのCビームプリフォーム(2つはIビームウェブを構成)と1つのフラットフランジプリフォームが生成されます。各Iビームストリンガーに必要な2つのセットをここに示します。
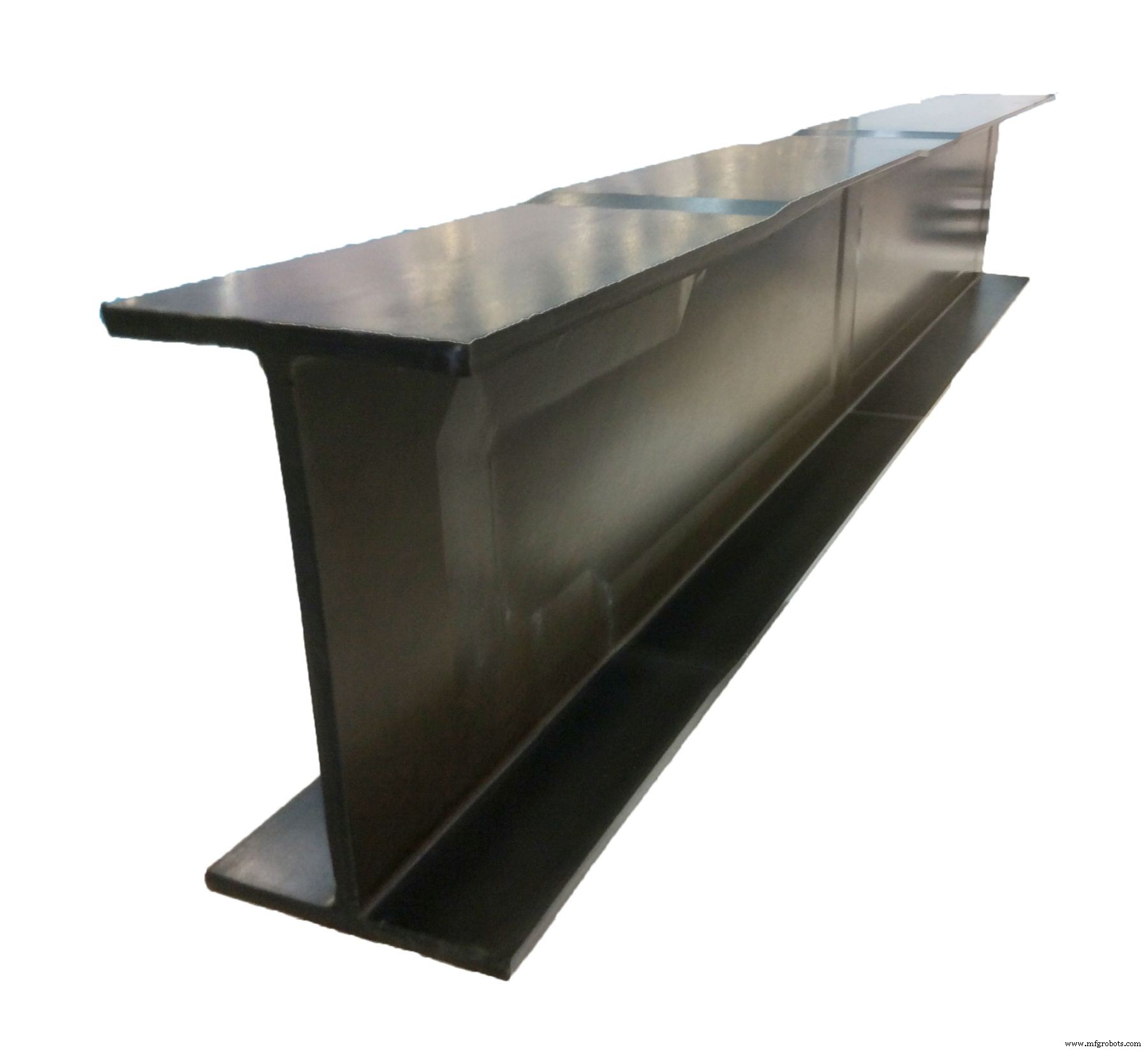
ステップ5.Clean Sky 2OPTICOMSプロジェクト用にHDFプリフォームとRTMを使用して作成されたIビームストリンガー。
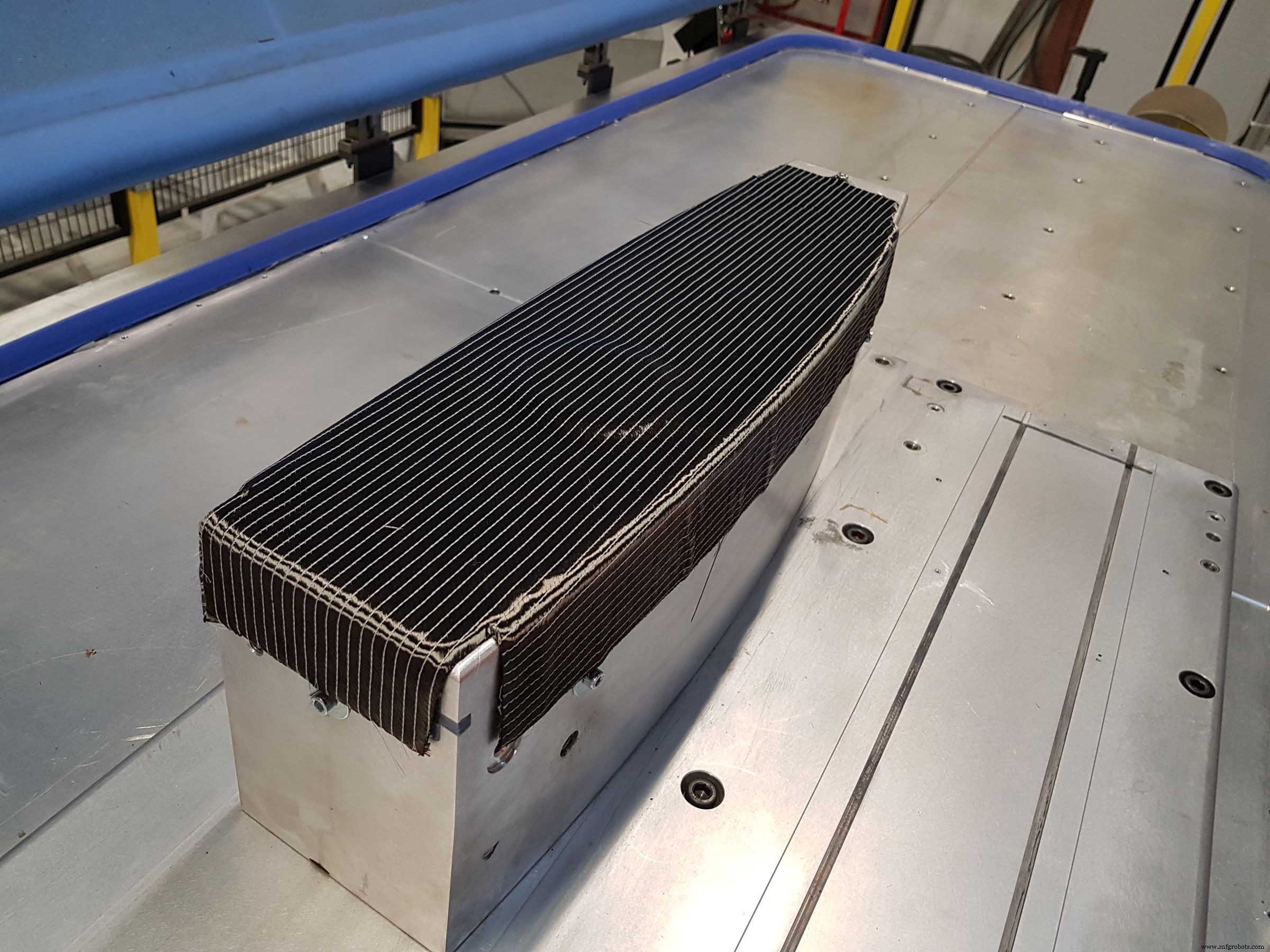
ステップ6.ロボットは、加熱されたプリフォームツールにカットプライを配置します。 5〜8層ごとに、プリフォームを圧縮するために加熱されたデバルクが完了します。
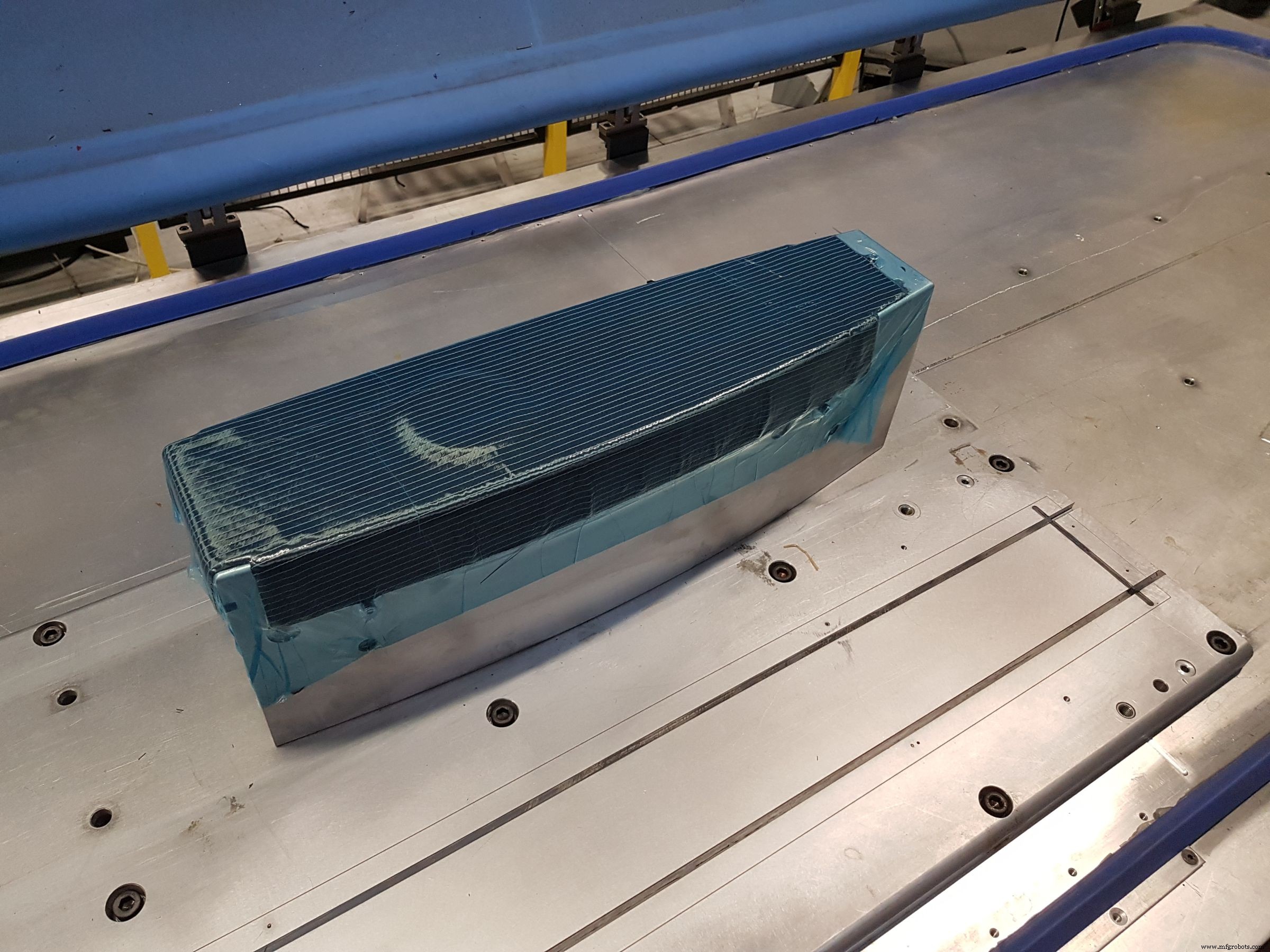
減量する前に、青いリリースフィルムが適用されます。
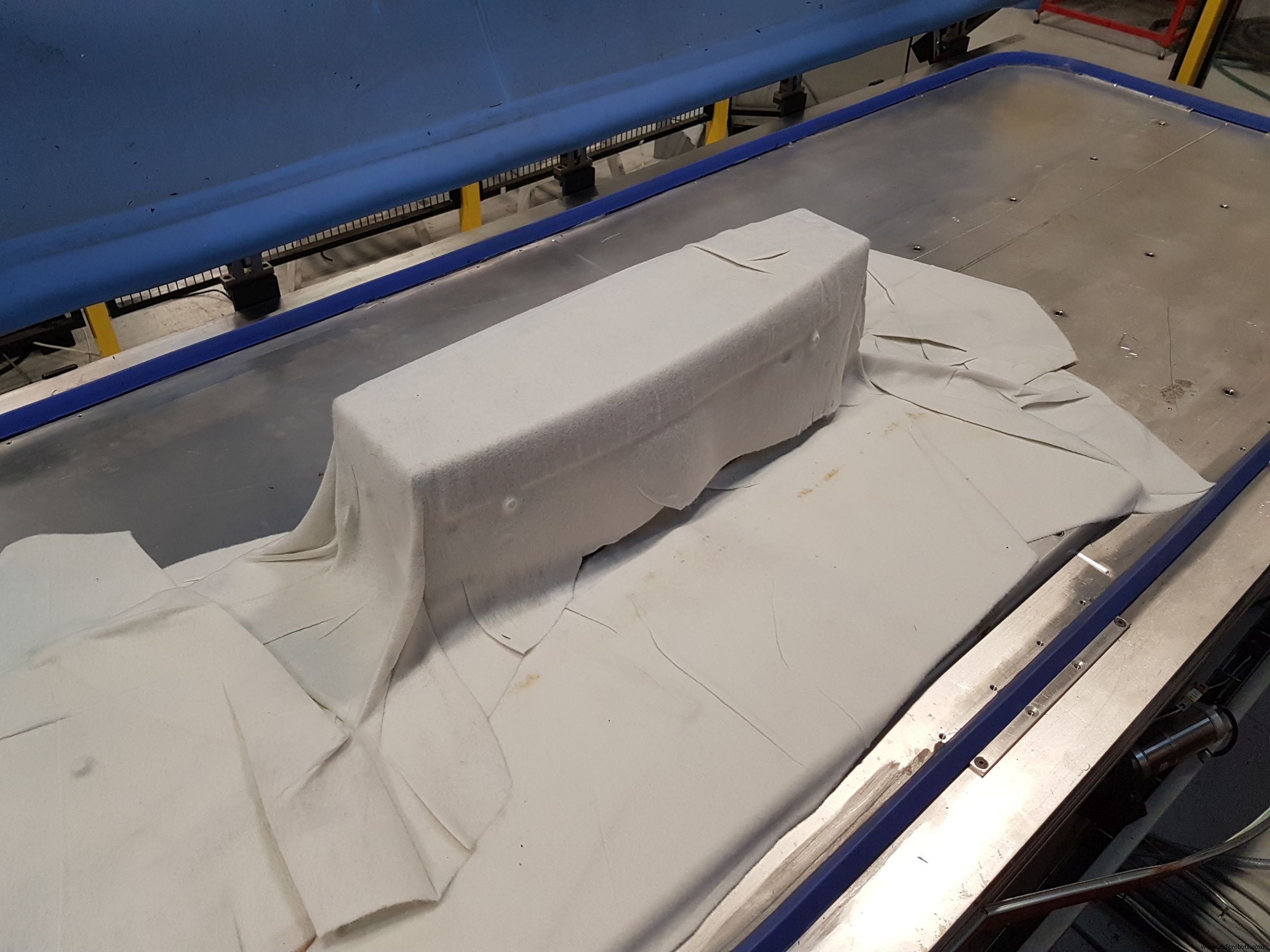
ブリーザーは、プリフォーム全体の空気を抽出するために使用されます。
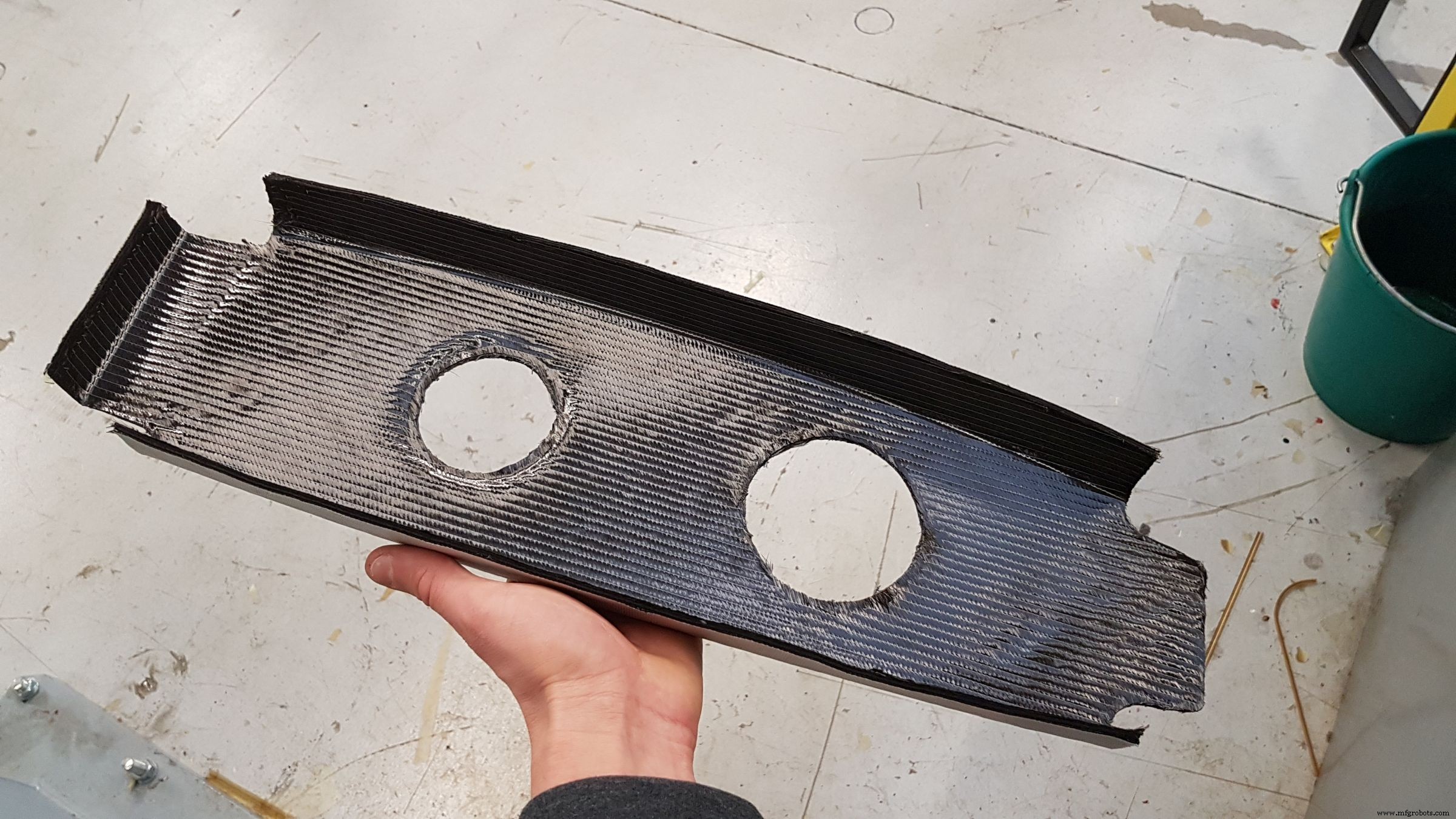
最終的なデバルク後、プリフォームはツール上で冷却され、カットアウトがトリミングされます。
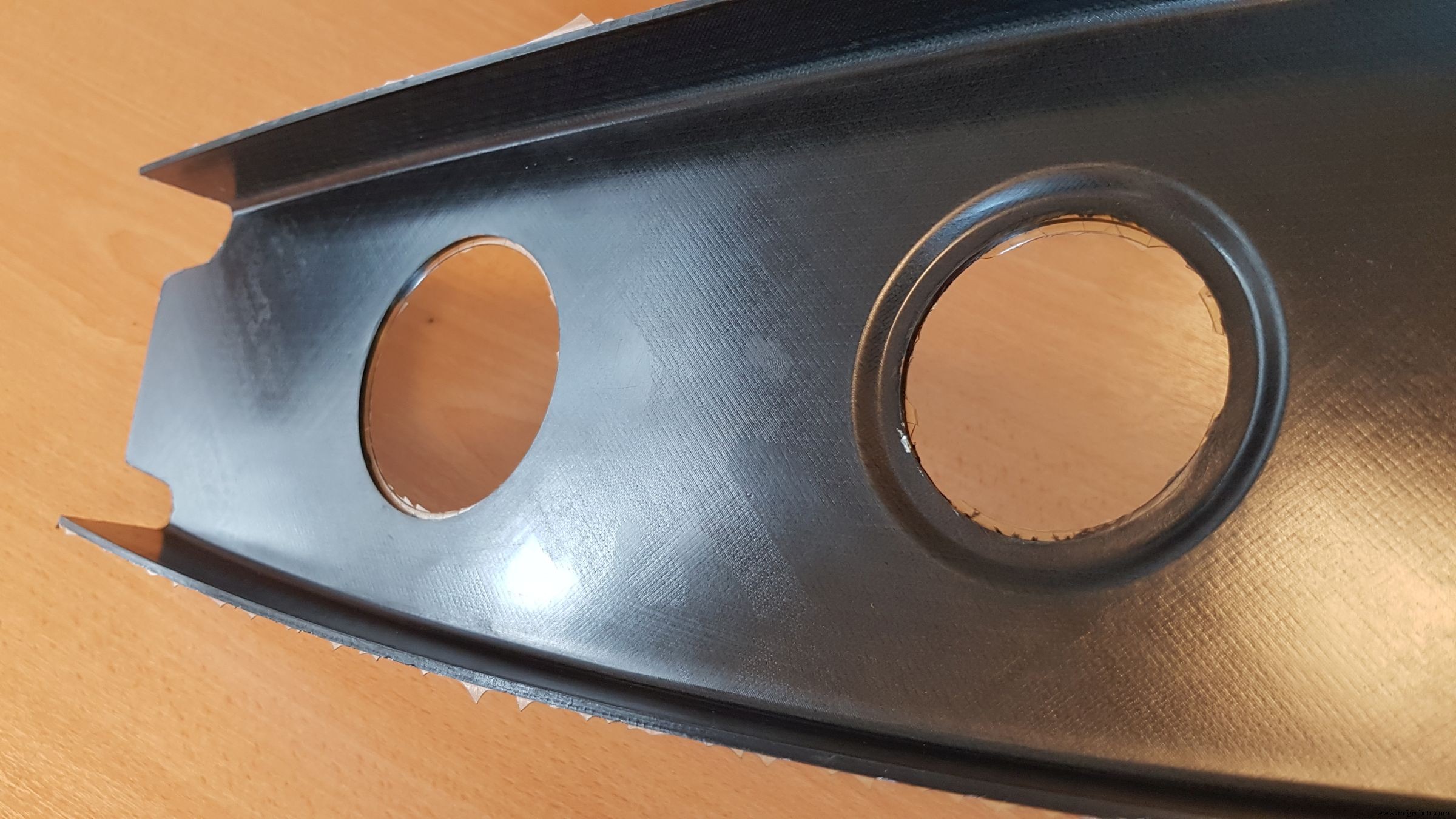
ステップ10.リブプリフォームはRTMとエポキシ樹脂を使用して成形されます。
前へ次へ「一度に圧縮できる層の数は、部品の材料と形状によって異なります」とChevallet氏は説明します。 「ウィングスキンのように曲率の低い部品の場合、50プライごとに圧縮できる可能性があります。ただし、OPTICOMSリブの角度は90度で、テスト用のIビームストリンガーはT字型であるため、予備成形中にプライにシワが形成されないように注意する必要があります。」彼は、このような複雑な形状では5〜8プライごとに圧縮が必要になる場合がありますが、それでも大量の工業化されたプロセスの一部である可能性があると付け加えています。スタックプライ、2分間のHDF圧縮 、再度開いて積み重ね、続いて圧縮サイクルを繰り返し、RTM金型に移す前にツールのプリフォームを最後に冷却します。
ファイバ