ミニチュアエンドミルで加工しながら結果を最適化する方法
機械加工業界では、一般に、マイクロマシニングとミニチュアエンドミルを直径1/8インチ未満のエンドミルと見なしています。これは、多くの場合、許容誤差をより狭いウィンドウに保持する必要があるポイントです。工具の直径は工具の強度に直接関係するため、ミニチュアエンドミルは大型のエンドミルよりもかなり弱いため、マイクロマシニングでは強度の不足を考慮する必要があります。これらのツールを繰り返しのアプリケーションで使用している場合は、このプロセスの最適化が重要です。
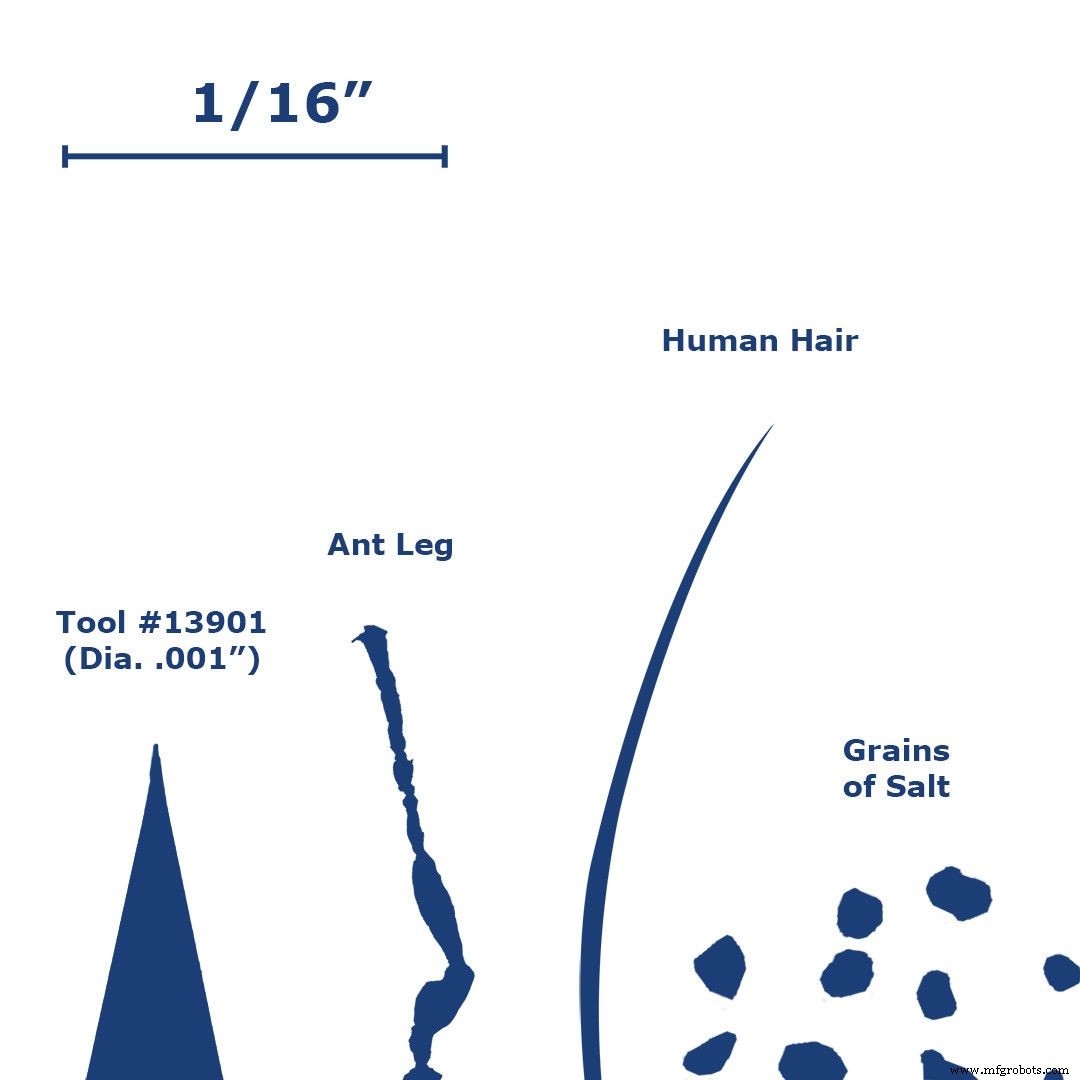
非常に少量でも工具の噛み合いと切削抵抗に大きな影響を与える可能性があるため、操作中の振れは小型工具にはるかに大きな影響を及ぼします。振れにより、フルートの不均一な噛み合いにより切削抵抗が増加し、一部のフルートは従来の工具よりも早く摩耗し、小型工具では破損します。断続的な衝撃により工具が欠けたり、小型工具の場合は破損したりする可能性があるため、工具の振動も工具の寿命に影響を与えます。操作を開始する前に、セットアップの振れを確認することが非常に重要です。以下の例は、直径.500インチの工具と直径.031インチの工具の.001インチの振れの違いを示しています。
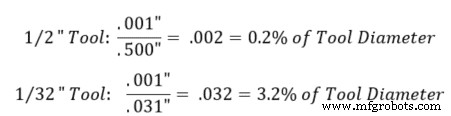
ミニチュア工具の場合、切りくずの厚さとエッジ半径(エッジプレップ)の比率ははるかに小さくなります。この現象は「サイズ効果」と呼ばれることもあり、切削抵抗の予測に誤差が生じることがよくあります。チップの厚さ対エッジの半径の比率が小さい場合、カッターは材料を剪断するのではなく、多かれ少なかれ材料を耕します。この耕起効果は、基本的に、薄いチップを切断するときにエッジ半径によって作成される負のすくい角によるものです。
この厚さが特定の値よりも小さい場合(この値は使用するツールによって異なります)、材料はツールの下に押し込まれます。ツールが通過し、切りくずが形成されなくなると、耕された材料の一部が弾性的に回復します。この弾性回復により、工具とワークピース間の接触面積が増加するため、切削抵抗と摩擦が大きくなります。これらの2つの要因により、最終的には工具の摩耗と表面粗さが大きくなります。
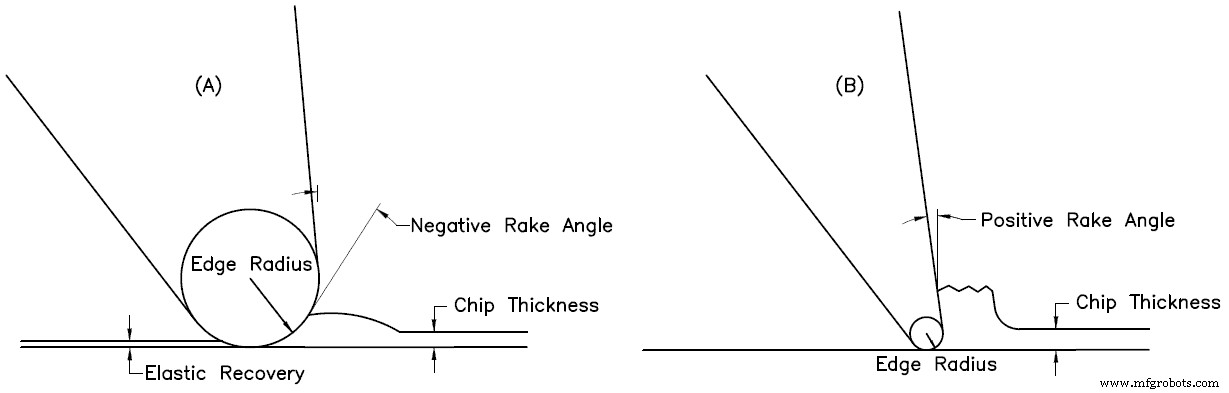
工具のたわみは、従来の操作と比較して、切りくずの形成とマイクロマシニング操作の操作の精度にはるかに大きな影響を及ぼします。工具の側面に集中する切削抵抗により、送りと反対の方向に工具が曲がります。このたわみの大きさは、工具の剛性とスピンドルから伸びる距離に依存します。小径の工具は、操作中に所定の位置に保持する材料がはるかに少ないため、大径の工具に比べて本質的に剛性が低くなります。理論的には、ホルダーから突き出る長さを2倍にすると、たわみが8倍になります。エンドミルの直径を2倍にすると、たわみが16分の1になります。ミニチュア切削工具が最初のパスで破損した場合は、たわみ力が超硬の強度に打ち勝ったことが原因である可能性があります。ツールのたわみを最小限に抑える方法をいくつか紹介します。
工具径が小さくなると、ワークの均質性が疑わしい要因になります。これは、容器の表面、不溶性不純物、粒界、転位などの多くの要因により、材料が非常に小規模で均一な特性を持たない可能性があることを意味します。材料の微細構造の均一性が問題となるためには、切削システムを非常に小さくする必要があるため、この仮定は、カッターの直径が.020インチ未満の工具では一般的に保存されます。
マイクロマシニングは、従来のマシニングと比較して、バリや表面粗さが増加する可能性があります。フライス盤では、送りが増加するとバーリングが増加し、速度が増加するとバーリングが減少します。機械加工作業中に、一次せん断ゾーンに沿ったワークピース材料の圧縮とせん断によって切りくずが作成されます。このせん断帯は、下の図2で見ることができます。前に述べたように、チップの厚さとエッジの半径の比率は、ミニチュアアプリケーションでははるかに高くなります。したがって、塑性変形ゾーンと弾性変形ゾーンが切断中に作成され、一次せん断ゾーンに隣接して配置されます(図2a)。その結果、刃先がワークピースの境界に近づくと、弾性ゾーンもこの境界に到達します(図2b)。塑性変形は、刃先が進むにつれてこの領域に広がり、結合する弾性変形ゾーンにより、境界でより多くの塑性変形が形成されます(図2c)。塑性変形ゾーンが接続すると永久的なバリが形成され始め(図2d)、チップがスリップラインに沿って亀裂を入れると膨張します(図2e)。チップが最終的にワークピースの端から外れると、バリが残ります(図2f)。
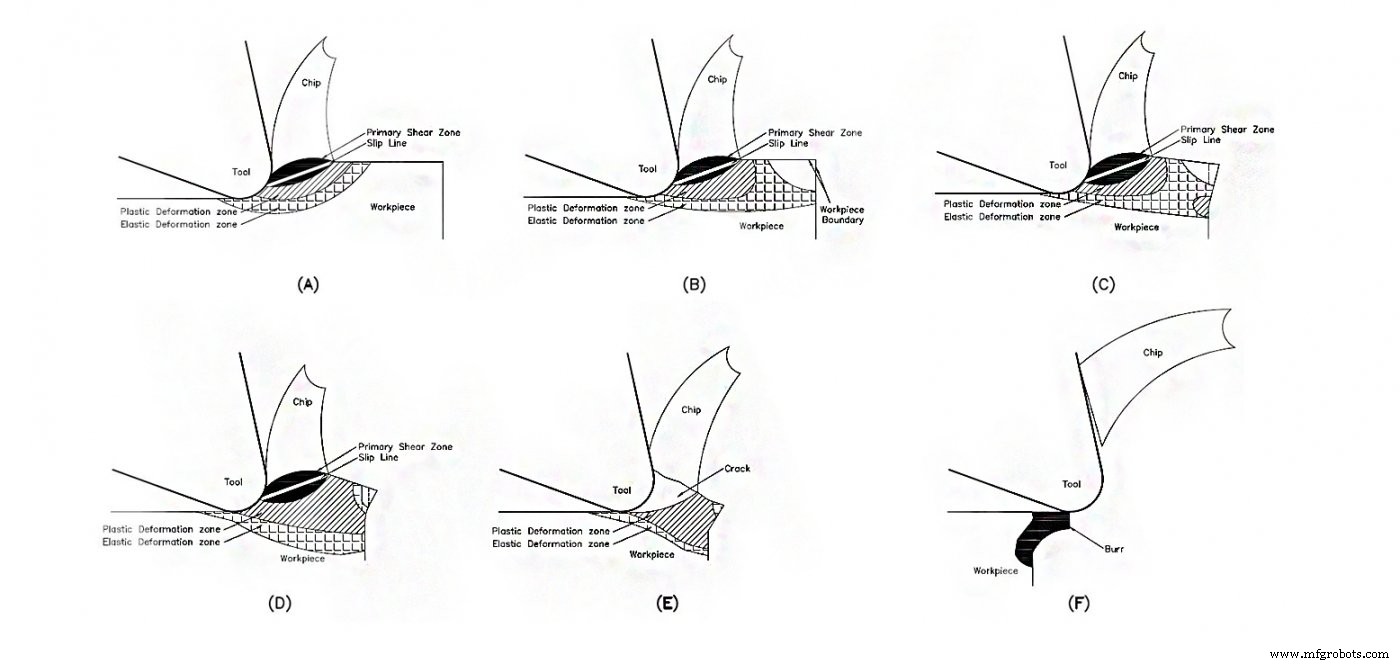
ミニチュア工具は壊れやすいため、工具経路は、突然の切削抵抗を回避し、複数の軸に沿って切削抵抗を分散できるようにプログラムする必要があります。これらの理由から、ミニチュアツールパス用のプログラムを作成する場合は、次の方法を検討する必要があります。
円形の傾斜は、x、y、およびz平面に沿って切削力を均等に分散するため、軸方向に部品に移動するためのベストプラクティスです。特定の切削深さで半径方向にパーツに移動する必要がある場合は、アーチ型のツールパスを検討してください。これにより、一度にではなく、徐々に切削力がツールに負荷されます。
直線パスの場合と同じ速度と送りを円形パスに使用しないでください。これは、複合角速度と呼ばれる効果によるものです。切削工具の各歯は、スピンドルでアクティブなときに独自の角速度を持っています。円形のツールパスを使用すると、別の角速度成分がシステムに追加されるため、ツールパスの外側部分の歯は予想とは大幅に異なる速度で移動します。工具の送りは、それが内部または外部の循環操作であるかどうかに応じて調整する必要があります。フィードを調整する方法については、サークルでの実行に関するこの記事をご覧ください。
大きなスロットと同じようにミニチュアスロットに近づかないでください。ミニチュアスロットでは、ツールにできるだけ多くのフルートが必要です。これにより、より大きなコアを介してツールの剛性が向上します。これにより、たわみによる工具の破損の可能性が減少します。フルートの数が多いと切りくずが排出される余地が少なくなるため、軸方向の噛み合いを減らす必要があります。より大きな直径のツールを使用すると、ツールの直径の50%〜100%をステップダウンする場合があります。ただし、フルート数が多いミニチュアエンドミルを使用する場合は、直径のサイズとたわみのリスクに応じて、5%〜15%の間でステップダウンするだけです。軸方向の噛み合いの減少を補うために、送り速度を上げる必要があります。ボールノーズエンドミルを使用すると、これらの軽い切込みで切りくずが薄くなり、高送りミルのように機能し始めるため、送りをさらに高くすることができます。
より多くの工具が部品にかみ合うようになると、部品の角が追加の切削抵抗を生み出します。このため、角を加工するときに送りを遅くして、ツールにこれらの力を徐々に導入することが有益です。
マイクロマシニングアプリケーションでのクライムミリングと従来のミリング
これは、マイクロマシニングに関しては、答えるのがやや難しい質問です。パーツプリントで高品質の表面仕上げが必要な場合は、常にクライムミリングを使用する必要があります。このタイプの工具経路は、最終的に、より予測可能でより低い切削抵抗、したがってより高品質の表面仕上げにつながります。クライムフライス盤では、カッターはカットの開始時に最大の切りくずの厚さにかみ合い、ワークピースから押しのける傾向があります。セットアップに十分な剛性がない場合、これによりチャタリングの問題が発生する可能性があります。従来のフライス盤では、カッターが回転してカットに戻ると、カッター自体が材料に引き込まれ、切削抵抗が増加します。従来のフライス盤は、壁が長く薄い部品や繊細な操作に使用する必要があります。
背の高い薄壁の部品をマイクロマシニングする場合は、これらの操作を考慮する必要があります。仕上げパスのために部品を十分にサポートできない場合があるためです。
ミニチュアエンドミルでマイクロマシニング操作を成功させるための役立つヒント
振れとたわみを最小限に抑えるようにしてください ミニチュアエンドミルでマイクロマシニングする場合は、可能な限り。これは、焼きばめまたは圧入ツールホルダーを使用することで実現できます。手術中の突き出しの量を最小限に抑えながら、コレットとのシャンクの接触の量を最大にします。印刷物を再確認し、可能な限り最大のエンドミルがあることを確認してください。ツールが大きいほどたわみが少ないためです。
- 適切な切り込みの深さを選択してください チップの厚さとエッジの半径の比率が小さすぎないようにします。これにより、耕起効果が発生します。
- 可能であれば、ワークピースの硬度をテストします 機械加工の前に、ベンダーが宣伝する材料の機械的特性を確認します。これにより、オペレーターは材料の品質を知ることができます。
- コーティングされたツールを使用する これらのタイプの金属を機械加工するときに発生する過剰な熱量のために、可能であれば鉄系材料で作業する場合。工具コーティングは、工具寿命を30%〜200%延長し、マイクロマシニングの鍵となる高速化を可能にします。
- サポート資料の使用を検討してください マイクロマシニングアプリケーション中のバリの発生を制御します。支持材料は、補助的な支持力を提供するだけでなく、ワークピースの元のエッジの剛性を高めるために、ワークピースの表面に堆積されます。動作中、支持材はバリになり、ワークピースではなく塑性変形します。
- フラッドクーラントを使用する 切削抵抗を下げ、表面仕上げを向上させます。
- ツールパスを精査する これは、いくつかの調整がミニチュアツールの寿命を延ばすのに大いに役立つ可能性があるために適用されます。
- ツールの形状を再確認 加工する材料に適していることを確認します。可能な場合は、可変ピッチおよび可変ヘリックスツールを使用します。これにより、ミニチュアツールが通常実行される非常に高いRPMで高調波が低減されます。
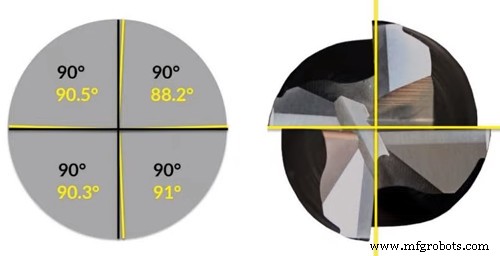
CNCマシン