オーバーモールドされたハイブリッド部品は、新しい複合材料市場を開きます
複雑さと強さ。 航空機の収納ビン用のBブラケットのようなコンポーネントは、非常に複雑であり、高強度の要件の両方を示します。これは、ハイブリッドオーバーモールディング技術が特に適している組み合わせです。ソース、すべての画像| TxV Aero Composites
多くの場合、航空宇宙市場では、OEMは、コンポーネントの軽量化による燃料節約、摩耗の減少による寿命の延長、またはその他の運用上の削減により、投資が利益をもたらすことを知って、複合コンポーネントに対してより多くの費用を支払う用意があります。とメンテナンスコスト。この「製品ライフサイクル」ビューにより、多くの市場とアプリケーションが複合材料に開かれました。さらに珍しいのは、取得コスト自体が金属バージョンよりも低い複合コンポーネントです。しかし、これは変化しています。いくつかの新しい自動複合材料製造プロセスは、複合材料を支持して規模を縮小し始めており、その中には、TxV Aero Composites(Bristol、R.I.、U.S。)によって開発されたハイブリッドオーバーモールディングプロセスがあります。
Tri-Mack Plastics Manufacturing(Bristol、R.I.、U.S。)とVictrex(Thornton Cleveleys、UK)の合弁会社であるTxVは、ハイブリッドオーバーモールディング技術を商業生産の段階にまで発展させました。同社はSFSintec Aircraft Components(Althengstett、Germany)と提携して、以前は航空宇宙グレードのアルミニウムで作られた航空機用収納ビンブラケットを再設計し、商業生産しています。独自のサクセスストーリーであるこのブラケットは、ハイブリッドオーバーモールディングとVICTREX AE 250一方向炭素繊維/ポリアリールエーテルケトン(PAEK)テープの可能性を示しており、多くの航空宇宙アプリケーションで貴重な重量とコスト削減を実現します。材料が差し引かれるのではなく、追加される複合プロセス。
減算から加算まで
CNCマシンで金属部品を製造する機械工や機械工場は、そのプロセスが金属ブランクから不要な材料を切り取って部品を製造し、金属スクラップチップを作成するという明らかな理由から、「チップメーカー」と呼ばれています。これらのチップは、廃棄されるか、リサイクル業者に送られるか、社内で再処理されるかにかかわらず、金属加工のコストのかかる側面を表しています。 SFS intecのオーバーヘッド収納ビンブラケットの場合、アルミニウムの60〜70%は、機械加工に必要ないくつかのフライス盤ステップでスクラップになります。
この高いスクラップ率により、ブラケットのネットシェイプまたはニアネットシェイプの複合バージョンの原材料コストは、金属材料のコストよりも低くなる可能性があります。 「チップのおかげで、より安価な(ポンドあたりの)アルミニウムと競争することができます。バイ対フライの比率が8:1の場合、購入したアルミニウムのほとんどがスクラップになります」とTxVのシニアアカウントマネージャーであるJonathanSourkes氏は述べています。 「もう1つの要因は、各コンポーネントのフライス盤に費やす時間です。 [複合]部品は数時間ではなく数分で作成できます。」
原材料のコストを超えて、ブラケットのようなコンポーネントの複合バージョン(複雑な形状を特徴とし、高い耐荷重性能を必要とする)は、歴史的に利用可能な製造オプションを使用して経済的に実現可能ではありませんでした。一方では、コンポーネントが射出成形のような高速でロータッチのプロセスで低コストのチョップドファイバー補強材で作成された場合、コンポーネントは十分な耐荷重性能を達成できません。一方、低速で高接触のプロセスを介して、より高い耐荷重性の連続繊維強化で製造された場合、通常は手動でレイアップする必要があり、製造が遅すぎるか、製造コストがかかり、最終製品が高すぎる。
このタイプの新しい複合材料アプリケーションへのこれらの障害のために、複合材料業界は全体として、航空宇宙の顧客のニーズと仕様を満たすのに十分な耐荷重能力を備えた適切な高い生産率でそのようなコンポーネントを生産できる自動化プロセスの開発に多大なリソースを費やしてきました。 。このような複合部品の商業生産を視野に入れて、TxVは、特に航空宇宙産業全体でのポリケトンベースの複合アプリケーション向けの革新的な製造プロセスの商業的採用を加速するために2017年に誕生しました。
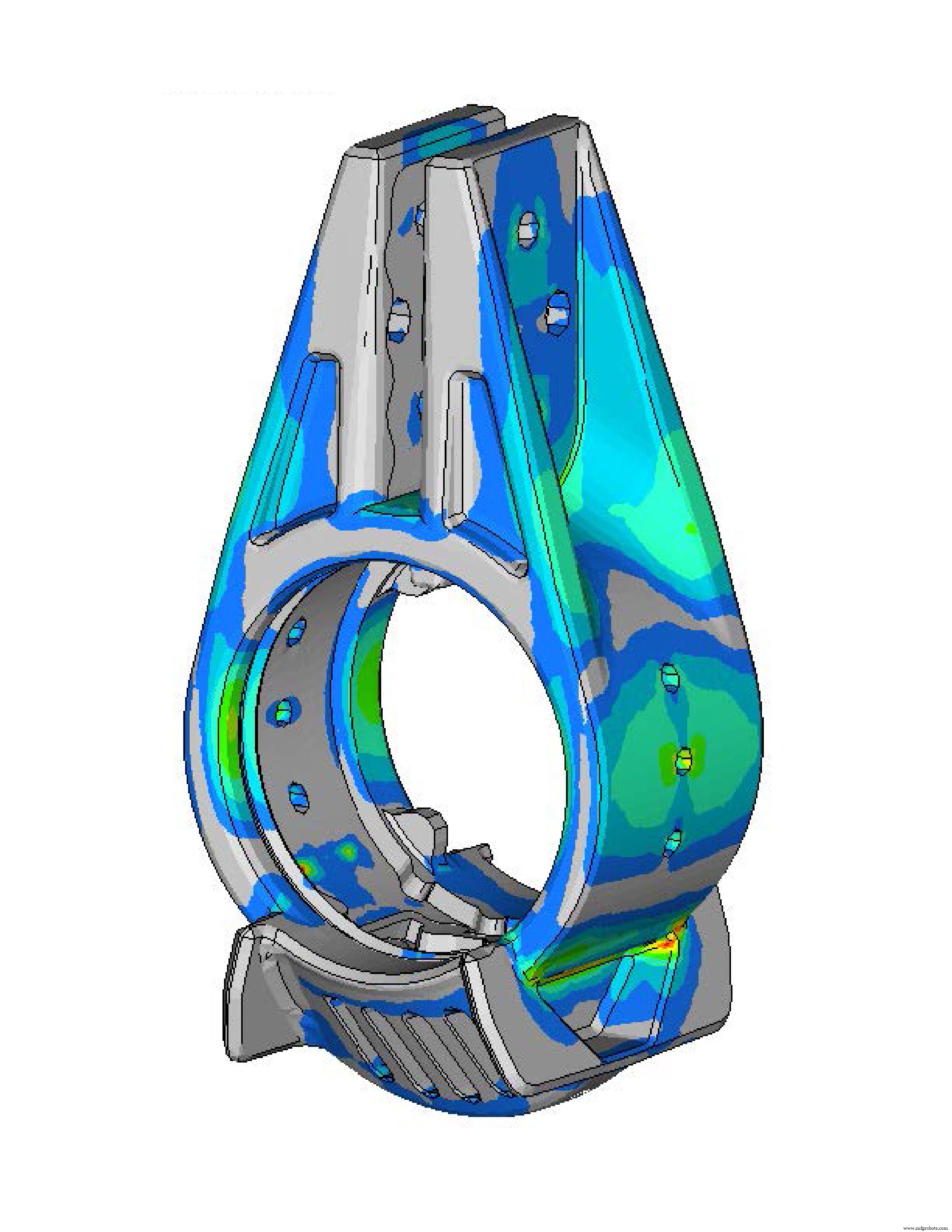
仮想プロトタイピング。 TxVは、ラミネートとオーバーモールドの関係を特徴づけるために開発された独自のデータを使用して、物理的なプロトタイプを製造およびテストすることなく、レイアップとプライの方向を繰り返しました。ここに示されているように、目に見える応力が提供された荷重ケースの範囲内になるまで、反復が続きます。
TxVのオーバーモールドハイブリッドソリューションには、複合コンポーネントの製造における最先端技術への2つの重要な進歩が組み込まれています。まず、連続繊維強化の強度または剛性を必要とするコンポーネントの部品の生産を自動化します。次に、射出成形の速度を利用して、コンポーネントの複雑な形状を完成させます。より具体的には、荷重を処理するために調整されたラミネートを生成し、次にオーバーモールドして機能化し、最終部品の形状を作成します。 SFS intec AircraftComponentsのイノベーション責任者であるSaschaCostabel氏によると、ハイブリッド技術は、「従来の機械加工が使用される場合に複数の加工ステップを必要とする高レベルの機械的応力と形状に耐える必要があるコンポーネントに適したオプションです。」
>SFSインテックとの提携は素晴らしい選択でした、とSourkesは言います。 「システムアタッチメントのグローバルリーダーとして、SFSは常に本当に興味深いことを行っています。彼らは非常に革新的であり、新しいテクノロジーに投資する用意があります」と彼は述べています。 SFS intecは、航空機の顧客とも強力な関係を築いており、航空宇宙産業が再設計されたコンポーネントを採用するための鍵となる認定プロセスを実行する機能を備えています。
特に「Bブラケット」と呼ばれる航空機の収納ビンブラケットは、設計と製造が困難なコンポーネントを代表するものであるため、複合材料の再設計の最初の取り付けコンポーネントとして選択されました。共同エンジニアリング、部品の概念化と設計、およびAltair(Troy、Mich。、U.S。)有限要素解析(FEA)ツールによるパフォーマンスのモデリングに続いて、プロジェクトチームは最初の記事から繰り返し、モデルの検証、テスト、および証明を行いました。製造のための設計は、連続繊維強化要素の自動テープ敷設とチョップド繊維強化要素の高速射出成形の製造上の利点を活用する複合ブラケットの開発の中心でした。
Bブラケットの作成
ハイブリッドオーバーモールディングプロセスの重要な側面の1つは、同じクラスの異なるポリマーを使用することです。 PAEKはブラケットの連続繊維複合部分のマトリックス樹脂として機能し、ポリエーテルエーテルケトン(PEEK)はオーバーモールド領域で使用されます。 VICTREX PAEKおよびPEEKは、優れた耐疲労性、耐薬品性、耐食性を誇ります。優れた耐煙性、耐炎性、耐毒性。迅速な成形性;と溶接性。低融点PAEK(LM PAEK)であるVICTREX AE 250は、40℃の溶融温度を提供します PEEKよりも低い。 「溶融PEEKがLMPAEK複合材料の表面上を流れる場合、溶融温度が低いため、強い付着が可能になります」とSourkes氏は説明します。
Bブラケットの特定の原材料は、幅2インチのVICTREX AE 250一方向炭素繊維強化PAEKテープ(58%炭素繊維)です。短い炭素繊維を充填したVICTREXPEEK 150CA30(30%炭素繊維)。これらの材料は、ハイブリッドオーバーモールディング生産作業セルに供給され、次の多段階プロセスを通じてブラケットを作成します。
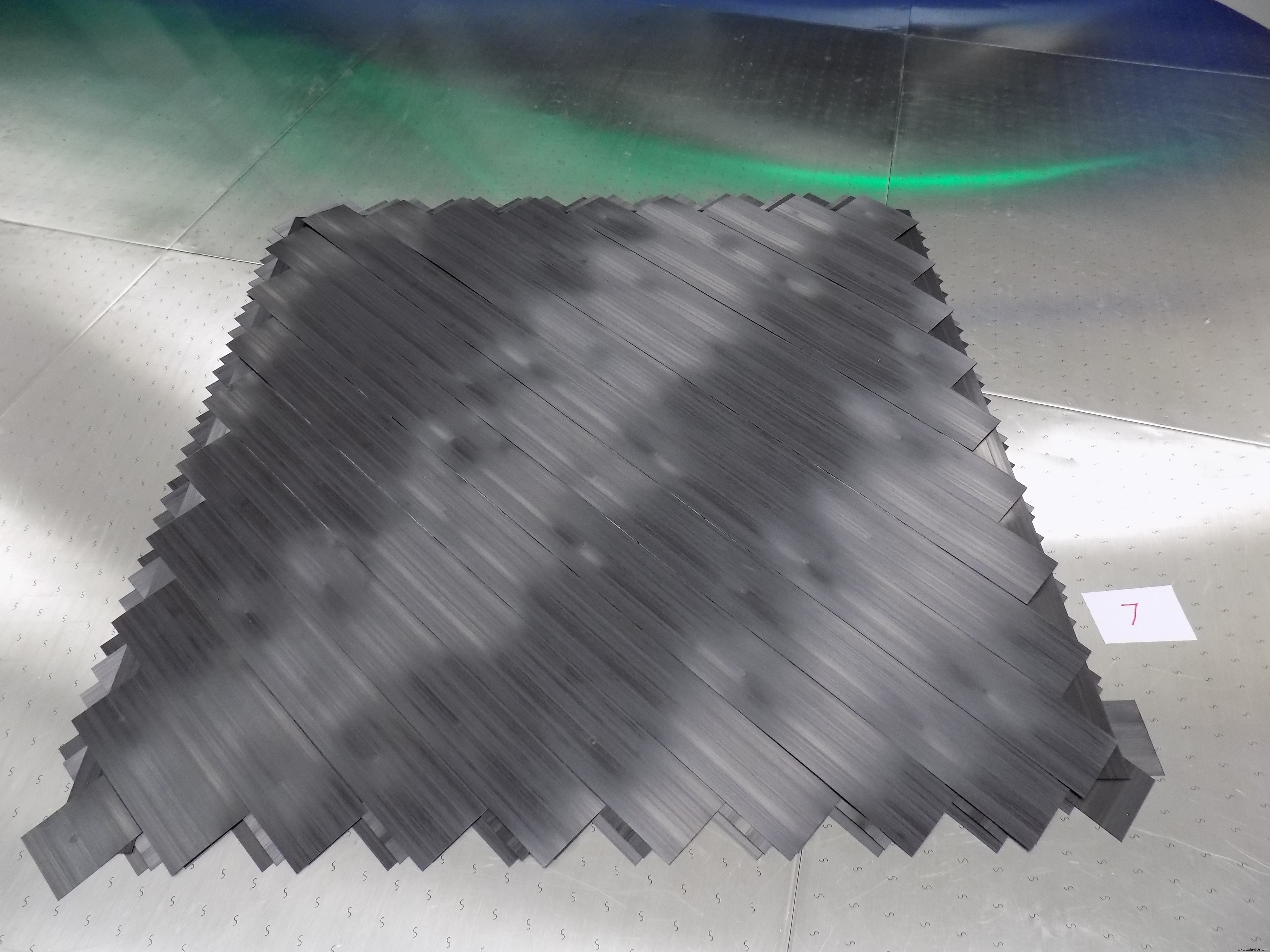
ステップ1。 Dieffenbacher Fiberforge 2000自動テープ敷設システムは、調整されたラミネートブランクを生成します。
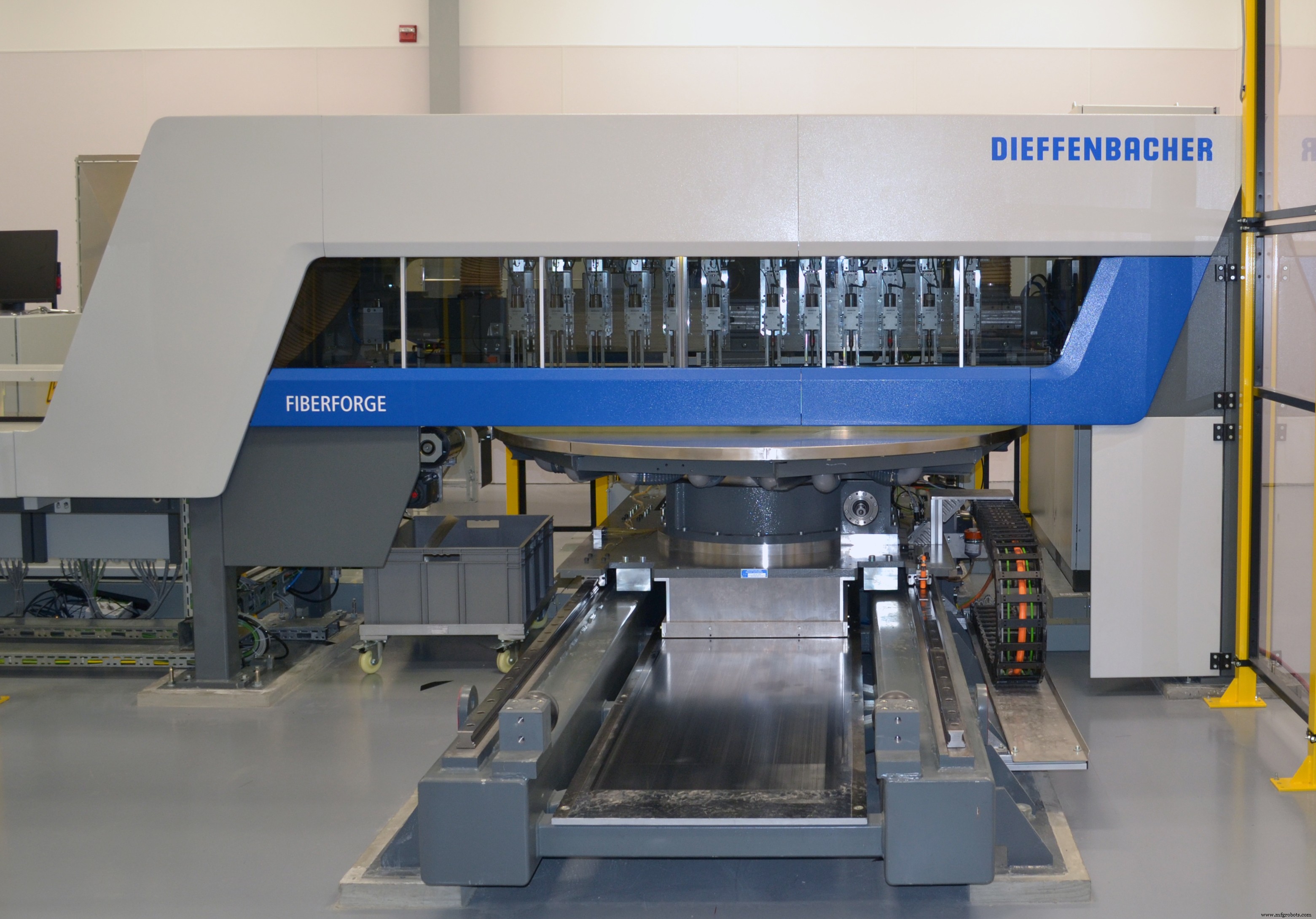
最初に、炭素繊維/ PAEKテープは、Dieffenbacher(Eppingen、ドイツ)のFiberforge2000テープ敷設システムを使用してテーラードブランクに敷設されます。 「このマシンは現在、世界で最も高速なテープ敷設システムの1つです」とSourkes氏は証言します。テープスプールをロードおよびリロードするロボットが装備されているため、中断することなく実行でき、手動のタッチ時間を最小限に抑えることができます。レイアップは、テープ間のギャップが最小限に抑えられるように設計されています。 Bブラケットテーラードブランクの各プライは、次のプライが配置される前に検査されます。このプロセスは、異物や破片(FOD)の可能性を最小限に抑えるために、環境管理された領域で実行されます。
テーラードブランクは、ラミネートのロードとアンロードに最小限の手動操作を必要とする自動化された特注セルに統合されます。セル内で、一致した加熱プラテンがパネルを圧密し、ボイドを排除します。次に、一致したコールドプラテンがパネルを冷却します。温度を維持した2セットのプラテンは、1セットのプラテンを備えたスタティックプレスよりもはるかに効率的です。 「その結果、サイクルタイムが数分対数時間で大幅に短縮されました」とSourkes氏は言います。
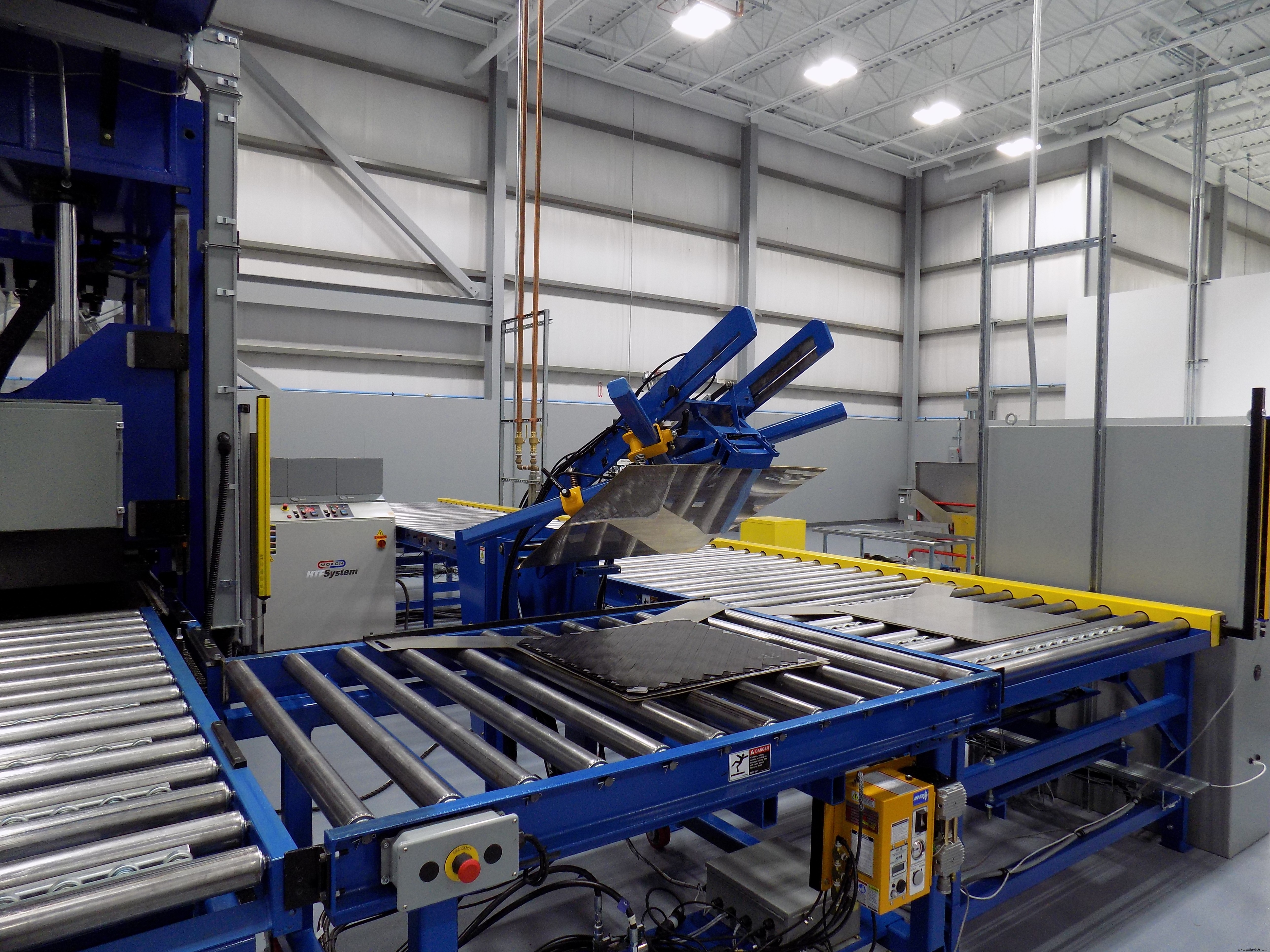
ステップ2。 テーラードブランクは、自動化された特注の統合セルに統合されます。このセルは、このステップを高速化するために温度(1つは高温、1つは低温)に保たれる2セットのプラテンを備えています。
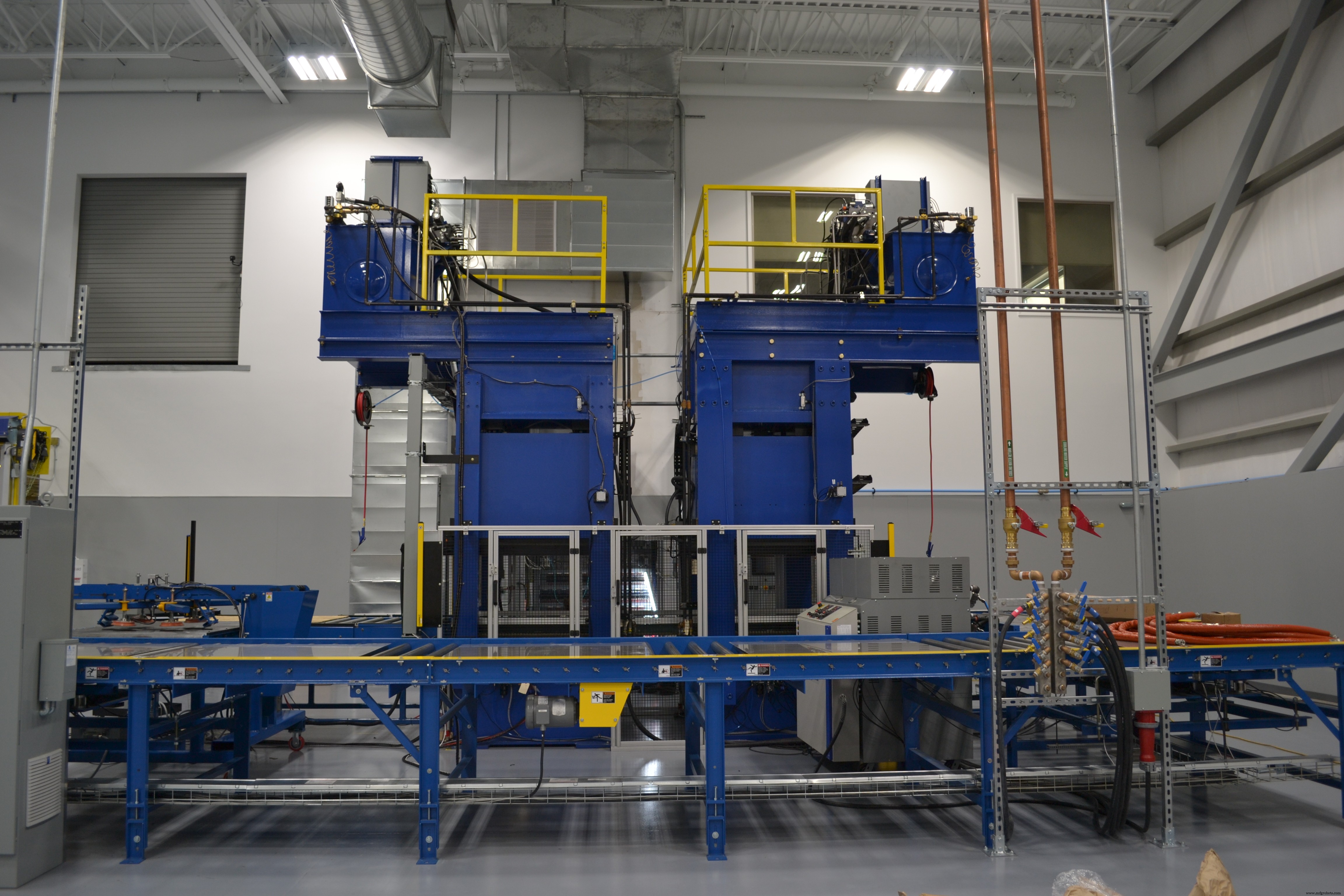
次に、統合されたラミネートプリフォームは、独自の作業セルでさらに処理され、ブラケットの主要な形状を形成します(ステップ3)。次に、Flow International(Kent、WA、U.S。)ウォータージェットカッターを使用して、形成されたブランクから最終的な炭素繊維/ PAEKインサートを切り取ります(ステップ4)
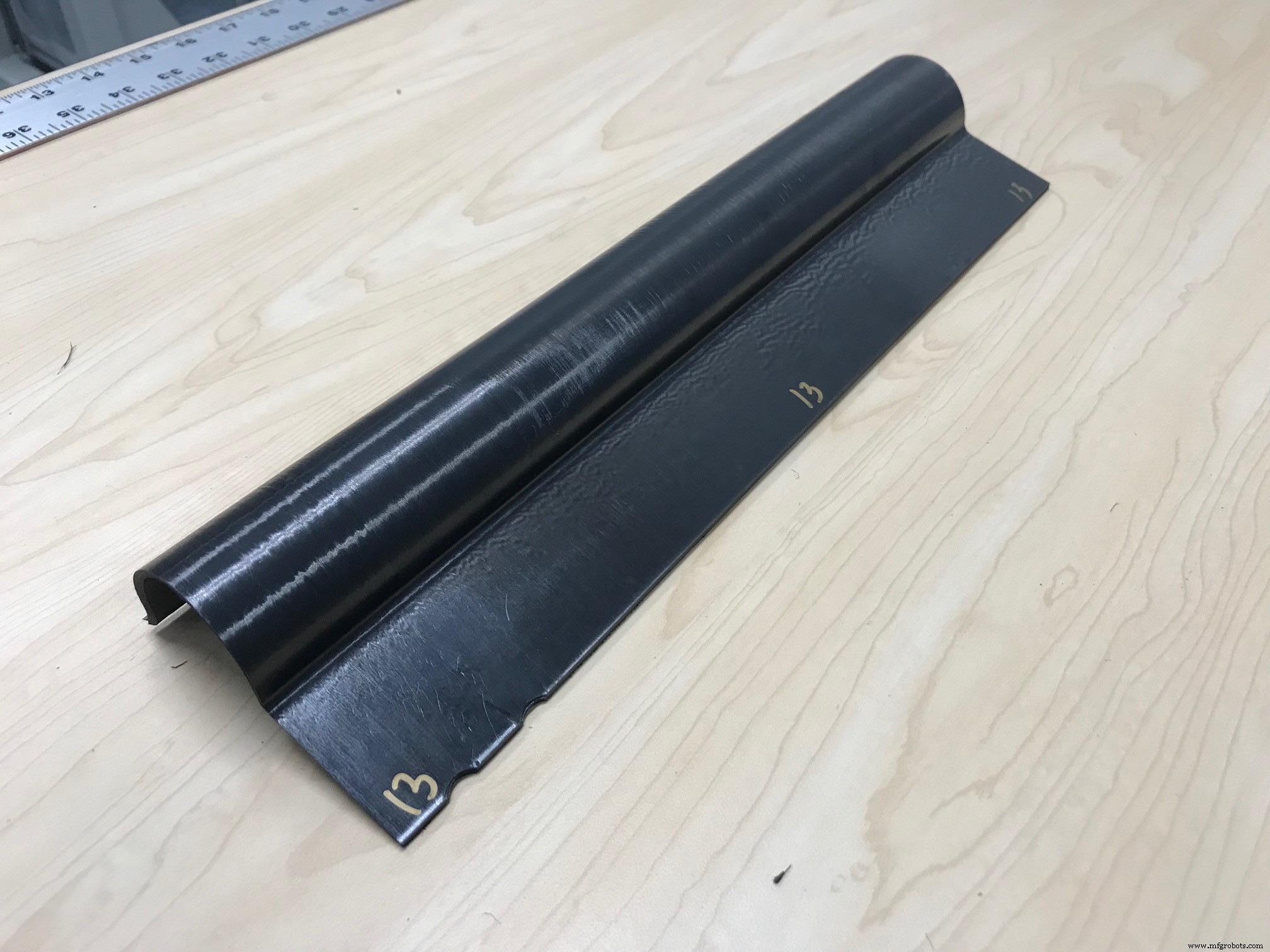
ステップ3。 独自の作業セルがブラケットの主要な形状を形成します。
テーラードブランクのサイズを決定する際に、Sourkesは、プロジェクトごとにトレードオフを検討する必要があると指摘しています。 「1つの正方形のブランクから3つまたは4つの長方形を圧縮できるように、ラミネートのサイズを設定できます。できるだけ大きなブランクを配置し、それをプリフォームにカットすることで、バイ対フライの比率を最大化します。しかし、プリフォームを切断することは、ウォータージェット切断操作により多くの時間を意味します。」 Bブラケットプロジェクトでは、各統合ラミネートが複数のプリフォームにカットされます
次は、エンゲル(シュヴェルベルク、オーストリア)の高温射出成形機で実行されるオーバーモールドステップです(ステップ5)。インサートは射出成形キャビティに配置され、溶融PEEKが充填されます。インサートは、溶融PEEKで満たされた射出成形キャビティに配置されます。これにより、VICTREX AE 250ラミネートの最上層が溶融し、強力な溶融接合コンポーネントが作成されます。
必要に応じて、コンポーネントは機械加工によってネット形状に仕上げられます。 「ニアネット部品を成形することが私たちの目標ですが、プロセスジオメトリをクリーンアップするために、事後に最小限のレベルの機械加工が必要になることがよくあります」とSourkes氏は認めています。機械加工は、ウォータージェットまたはCNC機械加工で実行できます。
画期的な結果
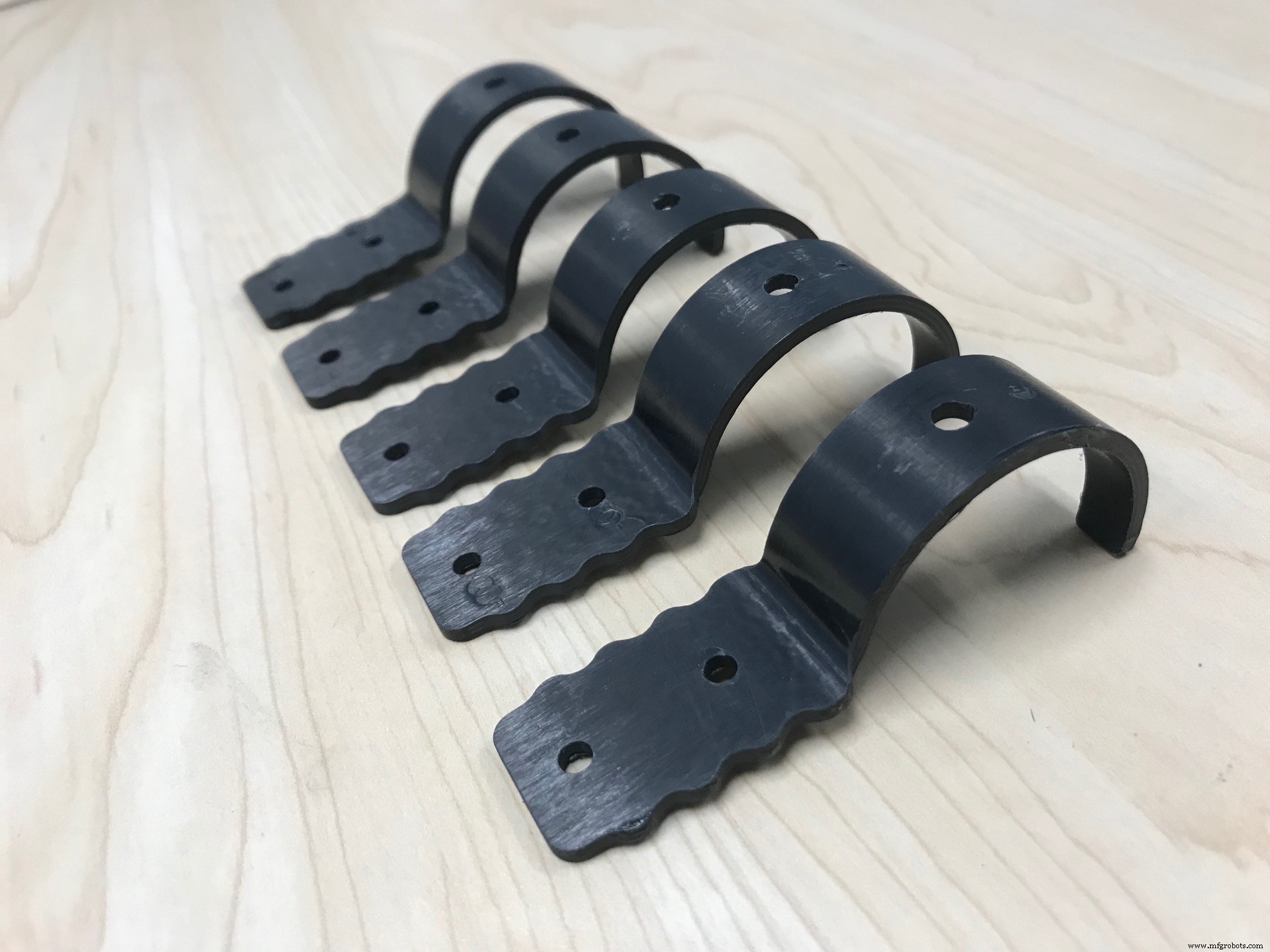
ステップ4。 Flow Internationalウォータージェットカッターは、形成されたブランクからカーボンファイバー/ PAEKインサートを切断します。これらのインサートのうち2つは、各ブラケットで使用されます。
SFSインテックブラケットの製造において、TxVハイブリッドオーバーモールディングプロセスは、3分のサイクルタイムと1.06:1のバイツーフライ比を達成します。 「材料の効率的な使用と迅速な製造プロセスにより、付加価値のある熱可塑性複合部品を製造でき、既存の金属設計よりもシステムのコストを削減できます」とSourkes氏は強調します。 「効果的に、私たちは低コストの原材料を高いバイツーフライ比とかなりの処理時間で高度に設計された材料ソリューションに置き換えています。」その結果、同様の交換、つまり既存のコンポーネントと同じ幾何学的および操作上の仕様に従う交換部品で、30〜40%の範囲の軽量化と20〜30%の範囲のコスト削減が実現します。 「部品システムを完全に再設計する機会が与えられれば、特に重量の節約は60%にもなる可能性があります」と彼は述べています。
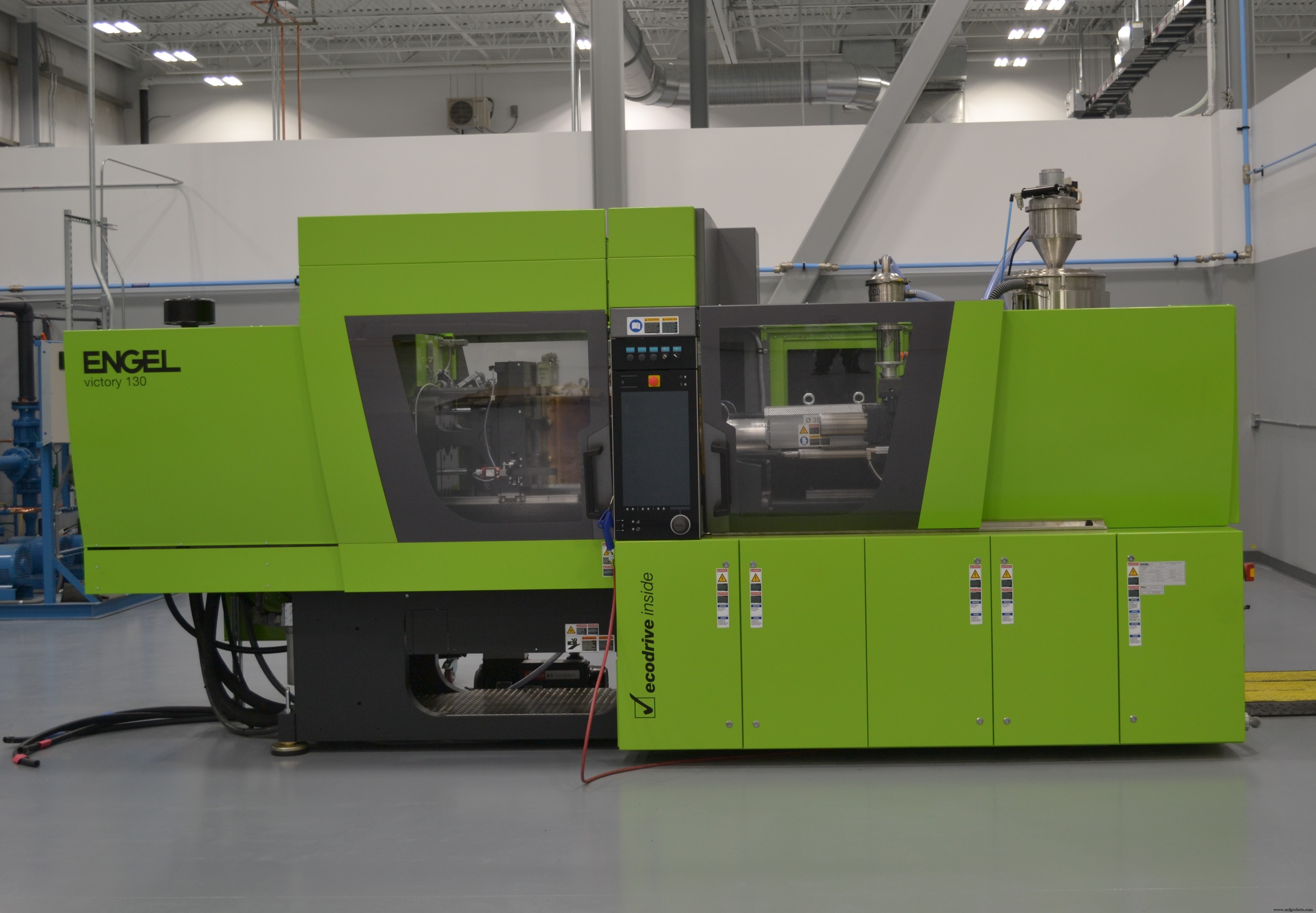
ステップ5。 PEEKハイブリッドオーバーモールド用に最適化されたエンゲル射出成形機は、インサートをオーバーモールドすることで複合部品を完成させます。
カーボンファイバー/ PAEK / PEEKブラケットも部品点数を統合しました。TxVとSFSは、機能化と他の機能の追加に使用されるのと同じ操作で、スプレッダーノーズを部品の下部に射出オーバーモールドすることに合意しました。以前は、スプレッダーノーズはPEEKで作られ、2つのリベットで固定されていました。したがって、統合により、部品点数が削減され、組み立てステップが不要になります。
TxVを立ち上げた2社の専門知識は、間違いなくハイブリッドオーバーモールディングの成功を可能にしました。 Sourkesは、PAEK材料および処理技術を開発した後、Victrexは最初に既存のビジネスパートナーとの機会を模索したと説明しています。 「しかし、射出成形の専門知識を持つ企業には、連続繊維強化複合材料を扱う専門知識がありませんでした。逆もまた同様です。」 VictrexとTri-Mackは、2017年にTxVを設立し、高度に自動化され、高速連続生産用に設計された、ベンチャー専用のポリケトン複合センターオブエクセレンスを構築する前に、数年間提携しました。
TxVプロセスと結果を従来の製造アプローチと比較するように求められたSourkesは、Bブラケットは標準的な複合材料製造アプローチに適合しないと述べています。 「これは、複合ビレットからブラケットを機械加工しないと非常に困難です。これはコストがかかりすぎます」と彼は言います。
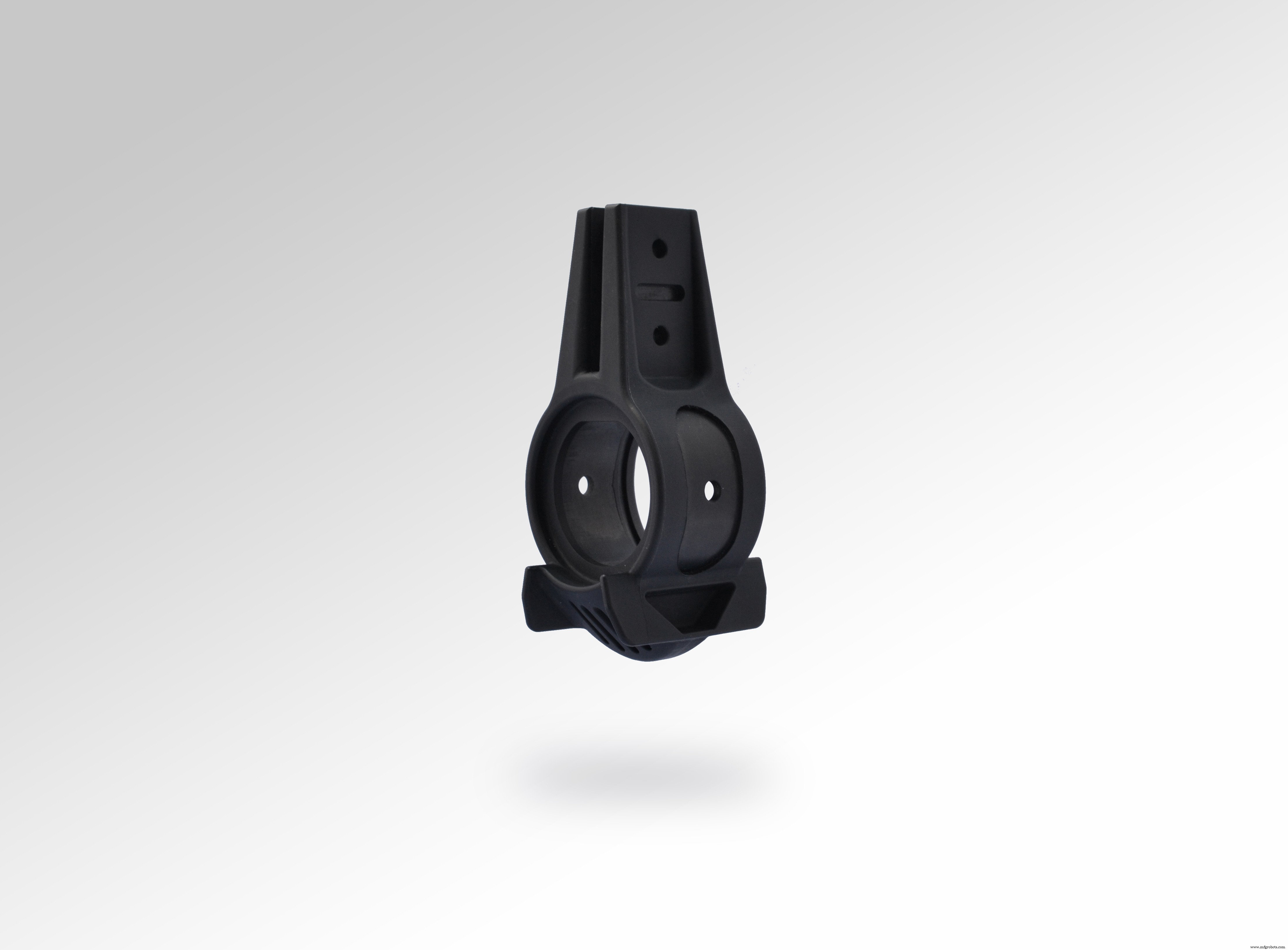
ステップ6。 最終的なBブラケットは、3分のサイクルタイム、1.06:1のバイツーフライ比、および30〜40%の軽量化で製造されます。
資格を取得してから飛行
SFS intecの認定を実行する機能を利用して、両社は「ポイント設計」による認定を進めました。これは、この特定の部品形状のみが飛行承認を取得することを意味します。部品が製造され、認定文書に記載されているテストの対象となりました。 「部品がオーバーヘッドビンブラケットであるとすると、操作上の負荷はかなり簡単に達成されます」とSourkes氏は述べています。 「しかし、性能要件はそれらの典型的な負荷を超えており、いくつかの極端な離陸および着陸操作をカバーする必要があります。」 CW として プレスに行くと、資格パッケージが提出され、仕様管理者からの最終承認を待っています。 TxVとSFSインテックは、この部品が2020年の初めに飛行することを期待しています。
Bブラケットが認定されると、TxVは生産量に合わせて拡張されます。同社は既存のハイブリッドオーバーモールディングラインを使用してこれらのブラケットを製造していますが、Sourkesは、テクノロジーを使用して部品を製造することと、テクノロジー自体の採用に関心のある業界メーカーをサポートすることの両方について、同社には2つの使命があることを強調しています。言い換えれば、複合材料メーカーは、自社の施設でこの製造技術を採用する可能性があります。
SFS intec製品のような複合ブラケットは、これらの種類のコンポーネントのかなり大きな市場を引き継ぐ可能性があります。民間航空機は何千ものブラケットとシステムアタッチメントを使用しており、航空機全体に多大なコストと重量の影響を与えています。 「熱可塑性複合部品は、航空機の製造においてますます大きな役割を果たすと確信しています」とコスタベル氏は予想しています。
ファイバ