複合材料プロセスの最適化と制御のための超音波センサーのカスタマイズ
このブログは、CosiMo(「持続可能なモビリティのための複合材料」)プロジェクトに関する私のレポートのフォローアップです。このプロジェクトは、複合バッテリーボックスカバーの「スマート製造」を実証するために、Faurecia Clean Mobility(フランス、ナンテール)によって2018年に開始されました。長さ1,100ミリメートル、幅530ミリメートルのチャレンジパーツは、不織布ガラス繊維と一方向炭素繊維強化材、金属とフォームのインサート、さまざまな半径と厚さを2.5〜10ミリメートルまで含む複雑な形状を特徴としていました。部品は熱可塑性樹脂トランスファー成形(T-RTM)を使用して成形され、カプロラクタムモノマーが注入され、加熱プレスサイクル中にその場で重合されてポリアミド6(PA6)複合材料が形成されました。プロジェクトの主な目標は、閉ループのセンサーベースのプロセス制御を使用して完全に自動化されたプロセスを調査することでした。
このブログでは、CosiMoチャレンジパートで使用される74個のセンサーのネットワーク、特にアウグスブルク大学(UNA、アウグスブルク、ドイツ)によって開発された超音波センサーと、すべてのセンサーからのデータを使用してプロセスのデジタルモデル(デジタルツイン)。
CosiMoの成功と、センサーベースおよびAIベースの製造開発のための開発センターの必要性に基づいて、UNAは、CosiMoプロジェクトパートナーであるドイツ航空宇宙センター(DLR)の軽量生産技術センター( ZLP、アウグスブルク)およびFraunhofer Institute for Foundry、Composites and Processing Technology(Fraunhofer IGCV)。 「私たちは共同で運営する新しい5,000平方メートルの施設を設置しています」とUNAの教授でアウグスブルクAIプロダクションネットワークのディレクターであるMarkusSause博士は言います。 「自動化された生産セルがあり、その多くは複合技術に焦点を当てているため、AIで何ができるかを実証できます。」
CosiMoセンサーネットワーク
CosiMoプロジェクトでは、T-RTMバッテリーボックスカバーを成形するために、Christian Karl Siebenwurst GmbH&Co。KG(ドイツ、ディートフルト)が提供するスチールRTMツールに74個のセンサーが統合されました。樹脂注入、浸透(フローフロントモニタリング)、およびその場での重合中にプロセスパラメータを監視するために使用されるこのネットワークには、次のものが含まれます。
- 1つの真空センサー
- Kistler(スイス、ヴィンタートゥール)による4つの圧力/温度センサー
- キスラーによる4つの温度センサー
- Netzsch(Selb、ドイツ)による8つの誘電分析(DEA)/温度センサー
- アウグスブルク大学によって開発された57個の超音波センサー。
CosiMoに関する最初のレポートでは、このセンサーネットワークが標準的な生産ではなく研究開発にどのように役立つかについて説明しました。
「産業用シリアル生産の場合、これほど多くのセンサーを設置する人は誰もいません。それは私たちが期待することではありません」と、DLRZLPのCosiMo製造プロジェクトリーダーであるJanFaber氏は述べています。 「しかし、この調査調査では、この大規模なセンサーのネットワークは非常に正確でした プロセスを完全に可視化するのに役立ちました および重要な動作 。それに応じて、プロセスにおけるローカルの効果を確認できました。 パーツの厚さや、フォームコアなどの統合された材料のバリエーションに対応します。」
では、このネットワークはどのように設計されたのでしょうか。 「コストが最も低いため、ほとんどが超音波センサーでした」とFaber氏は説明します。 「私たちは、互いに定義された距離でグリッドでそれらを使用しました。いくつかの位置で、超音波センサーを取り出し、キスラー温度/圧力またはNetzsch DEA /温度センサーを入れました。そして、これらの特定のセンサー(DEAとキスラーの両方)については、樹脂が入ったスプルーの近くに1つ、次に遠くに1つを配置しようとしました。したがって、金型の温度をしばらく確認した後、樹脂が到着する場所を監視することができました。」
なぜ異なるタイプのセンサーを使用するのですか? 「1つの研究課題は、信号を比較し、さまざまなセンサーがどのように機能するかを確認することでした」とFaber氏は言います。さまざまなタイプのセンサーがさまざまな測定原理に基づいているため、これは重要です。たとえば、DEAセンサーは、樹脂のACインピーダンスを測定します。このインピーダンスは、さまざまな割合に分割され、ポリマーでさまざまな効果を示します。一方、キスラーは、シリコンベースのホイートストンブリッジ(動的電気抵抗の測定に使用される回路の一種)に依存するピエゾ抵抗センサーを使用します。このセンサーは、成形キャビティの壁に取り付けられた検出端を形成する膜に接続されています。膜は圧力下で伸び、シリコンホイートストンブリッジの電気抵抗が変化し、電気信号が出力されます。 「また、圧力と温度の両方を測定するキスラーの新しい4001aセンサーを使用しました」とFaber氏は述べています。 「ツールで選択したローカルポイントに両方の値を設定すると非常に便利でした。」
UNA超音波センサー
CosiMoパーツネットワークで使用されるセンサーの大部分は、UNAによって開発された超音波センサーでした。 Sauseは、これらが低コスト(<10ユーロ)であるだけでなく、幅広い情報を提供できるという理由で好まれたと述べています。
超音波センサーは、完成した複合部品を検査するために何十年も使用されてきましたが、射出成形でも長い歴史があります。超音波センサーは、高周波音波を媒体に送り、その反射(パルスエコー)および/または透過を測定します。 CosiMoプロジェクトでは、公称周波数は2,000キロヘルツでした。金型に取り付けられた57個の超音波センサー(キャビティ表面から20ミリメートルの距離)のうち、10個は伝送モードで動作し、残りはパルスエコーモードで動作しました。超音波センサーは、波の速度と振幅の減少(減衰)を測定します。どちらもポリマーの特性に敏感です。さらに、波の速度は圧力と温度の関数として計算できますが、超音波データは調査対象のポリマーに合わせて調整する必要があります。
「私たちが開発した超音波センサーは、実際には市販されているものとそれほど変わりません」とSause氏は言います。 「これは、弾性運動を電気信号に変換するのに非常に敏感な圧電材料に基づいています。しかし、一般的なセンサーが150°Cまでの温度で動作できる場合、200°Cを超える熱可塑性成形品の高温に合わせる必要がありました。これは、センサーの電子機器にとっては少し難しいことでした。」
「センサーを金型に適切に統合するための機械システムも考案する必要がありました」と彼は説明します。センサーが満たさなければならない要件の大規模なポートフォリオがありました。そのため、ほとんどゼロから設計する必要がありました。また、システム全体の適切な音響設計も行いました。」
重合とフローフロントモニタリング
「音響は金型内の材料の弾性特性に焦点を合わせています」とSause氏は続けます。 「基本的に、液体の剛性は、重合が完了したときと同じではありません。その移行を効果的に監視しています。金型から各センサー位置のポリマー材料までの界面での波の反射の音響強度を調べ、時間の経過とともに硬化を継続的に追跡します。」
この測定の仕組みは、Sause andFaberらによって説明されています。 al。、SAMPE Europe 2021カンファレンスペーパー、「カプロラクタムを使用したT-RTM製造におけるinsitu重合のセンサーベースのプロセスモニタリング」。プリフォーム含浸前後の音響信号エコーの振幅の比率は、金型と部品の界面での屈折率Rに依存します。これは、重合が進むにつれて一定値に近づきます。理想的には、重合が完了に近づくと、Rの変化はゼロになります。
音響伝達信号から、超音波が含浸されたプリフォームを通過するための移動時間を抽出することも可能である。これは、重合度に関連するプリフォームを通過する音速として役立ちます。 SAMPE Europe 2021の論文の時点で完了した実験では、センサーの位置でプリフォームを完全に濡らしてから重合が完了するまでの時間は240秒でした。
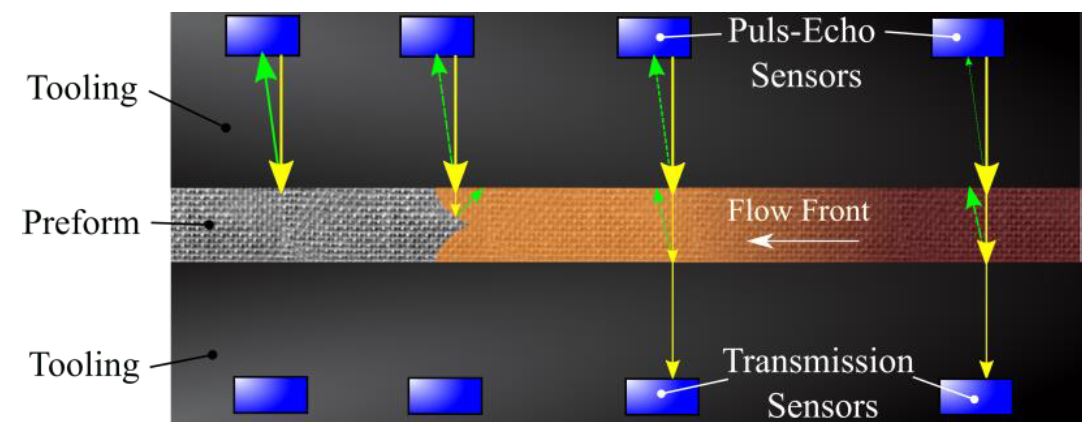
「注入中の流れを監視することもできます。これは、ポリマーのフローフロントがセンサーを通過するときに音響信号情報が変化するためです」とSause氏は説明します。また、SAMPE Europe 2021の論文で確認されたように、注入開始後15秒で、選択したセンサーのカプロラクタムフローフロントが到着すると、音響信号は初期の正規化値1から0.85〜0.9の間に急激に低下しました。
プロセスのデジタルツインの開発
Sause氏によると、超音波センサーの開発は、実際にはUNAがCosiMoプロジェクトで行ったことのごく一部であり、「最も魅力的な部分でさえありません」。本当の成果は、部品製造中の閉ループ制御を可能にするプロセスのデジタルモデルのデータ分析と開発にあったと彼は述べています。
「私たちがやろうとしているのは、金型で実際に起こっていることについての情報を提供することです」と彼は付け加えます。 「私たちは、多かれ少なかれ温度と圧力にプロセスを適応させるためのルートを確立しましたが、現在行っているのは、各センサー位置でアクティブなパルスを実行することによって音響信号情報を活用することです。これにより、フローフロントの形状、プリフォームの各部分に到達するまでの時間、各センサー位置での重合度など、さまざまなことを判断できます。」
「理想的には、閉ループ制御を有効にし、プロセス中に調整するための設定を確立できます」とSause氏は言います。 「これらには、射出圧力、金型圧力、温度などのパラメータが含まれます。この情報を使用して、資料を最適化することもできます。」
デジタルツインの開発は、多段階かつ複数のパートナーによる取り組みでした。それは、DLRZLPに割り当てられた作業パッケージの1つから始まりました。 「2Dプレートに基づくシミュレーションを設定しました。ESIGroup(フランス、ランジス)のPAM-RTMシミュレーションソフトウェアを使用して、充填と重合をシミュレートしたいと考えました」とFaber氏は言います。 「プロジェクトパートナーのITA(Institute for Textile Technology、RWTH Aachen、Germany)とSGL Carbon(Wiesbaden、Germany)からプリフォームの透過性データを取得し、アウグスブルク大学から熱可塑性ポリマー反応の反応モデルも取得しました。次に、すべてをシミュレーションに統合し、実際に実際のセンサーデータにどれだけ近づけることができるかを確認しようとしました。」
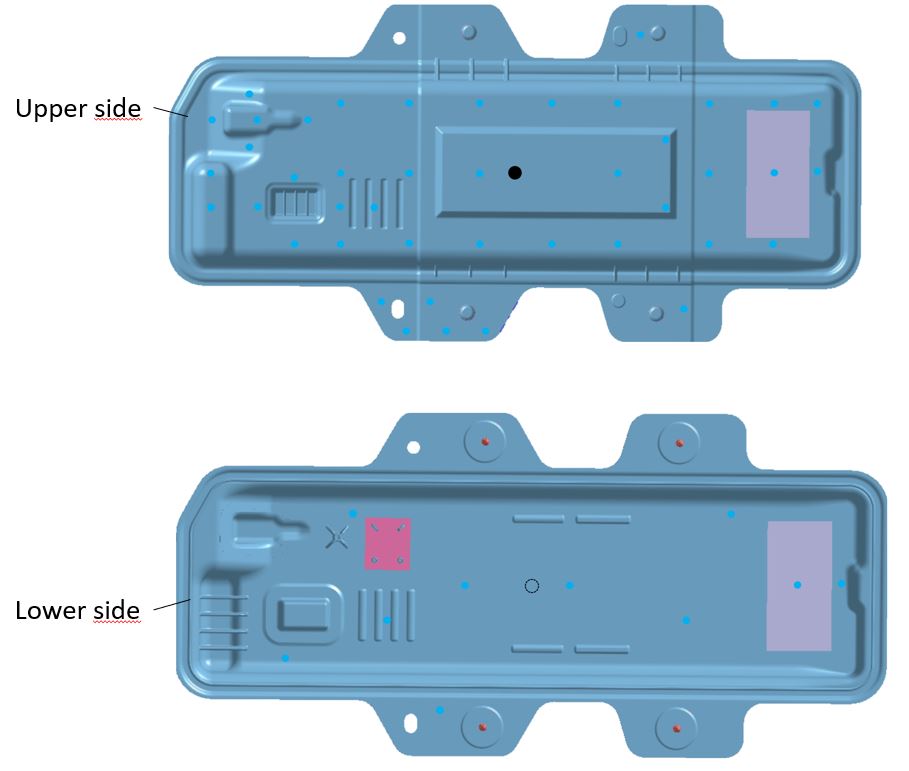
CosiMoプロジェクトのデモンストレーター部分の上部と下部の金型の水色の点は、プロセス全体の特定のポイントでデータを提供しました。次に、これをデジタルツインシミュレーションで使用して、センサーの位置を補間し、パーツ全体のプロセスをモデル化しました。写真提供者:CosiMoプロジェクト、DLR ZLPオーグスバーグ、オーグスバーグ大学
「2Dプレートモデルに基づいて、充填に関しては実際には非常に近いことがわかりました」とFaber氏は続けます。 「しかし、重合中には、シミュレーションでは説明できない温度の影響がありました。たとえば、この重合反応は発熱性であり、実際のデータでは温度センサーでわずかな増加が見られますが、シミュレーションでの増加ははるかに大きかった。ですから、これは私たちがいくつかの作業を続けてきた分野です。」
チームがシミュレーションから発見したかったことの1つは、重合が完了するのに必要な時間でした。 「私たちが本当に望んでいたのは、金型で必要な最小限の時間でした」とFaber氏は述べています。この情報はシミュレーションモデルから導き出され、すべてのシミュレーションと同様に、複数のタイプのセンサーとAIアルゴリズムに依存していました。たとえば、Netzschは、誘電分析に使用される誘電センサーを提供しましたが、プロセスのデジタルツインの一部にも役立ちました。 「彼らは、注入内のメカニズムを調査し、重合を終了するタイミングと重合状態を予測するために、予測AIモデルを設定しました」とFaber氏は述べています。
(注:Netzschは、材料特性評価、動的シミュレーション、センサーテクノロジーの能力を組み合わせて、AIおよびクラウドソリューションの新しい製品を確立しました。このタイプの統合ソリューションは、重合度のリアルタイム評価を提供するためにCosiMoで成功裏に実証されています。 sensXPERTというブランドで商品化されます。)
センサーとシミュレーションの完全なネットワークから、96%が達成された最大の重合であり、4.5分を要したことがわかりました。 「したがって、これは注入プロセスよりもはるかに高速ですが、たとえば熱硬化性樹脂を使用した高速注入よりもはるかに低速です。」
「センサーデータはデジタルツインモデルに適合します」とSause氏は言います。 「アイデアは、センサー情報によって数値的に安定化されたプロセスと同時にモデルを実行することでした。青い点は超音波センサーの粗いグリッドを提供し、次にそれらのポイント間を補間することができました。たとえば、センサーからの測定データに基づいて、時間の関数としてCosiMoパーツでフローフロントがどのように発達するかを示すビデオを提供することができました。」
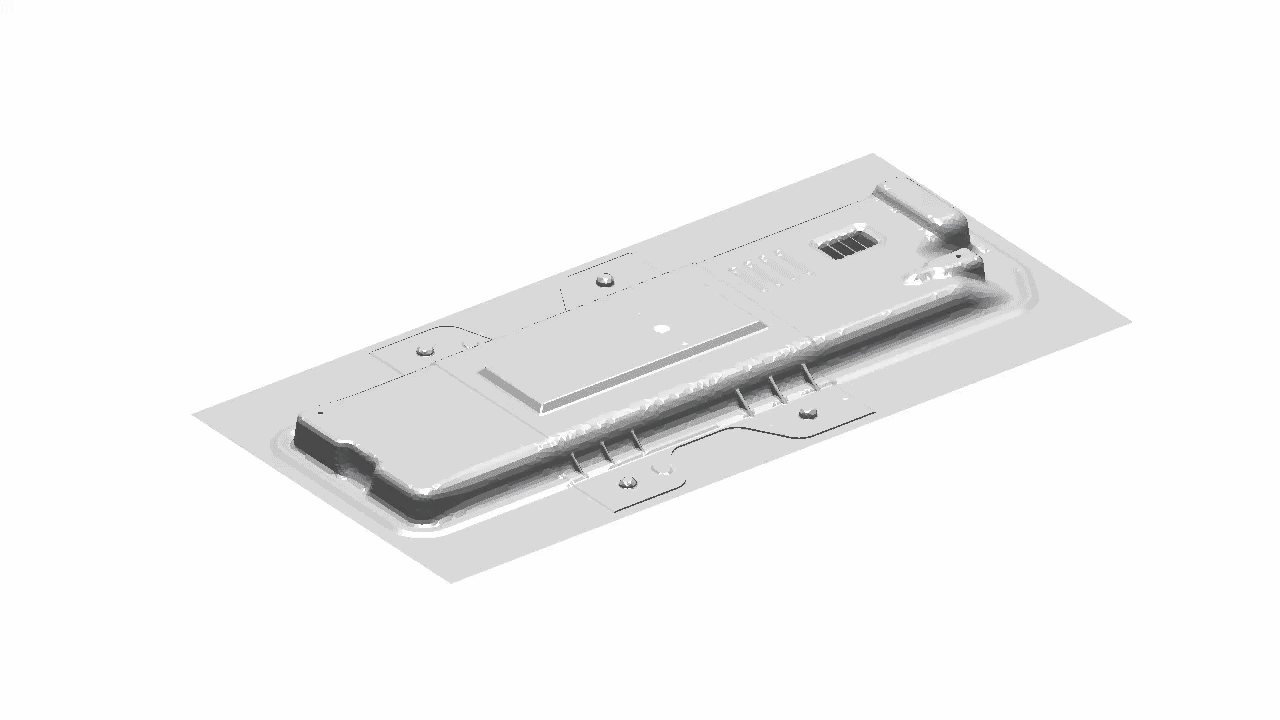
重合速度の予測はどのように検証されましたか? 「私たちはいくつかのアプローチを取りました」とSauseは言います。 「最初に、ここUNAの博士課程の学生は、カプロラクタムからPA6への材料システムの反応速度論のモデリングのフルセットを行っていました。そこで彼は、赤外線分光法をレオメトリックデータおよび誘電分析センサーからのデータと一緒に同時に研究して、そのシステムの硬化速度論の非常に正確な材料モデルを提供し、そのモデルを検証していました。そのため、同じモデルを使用してセンサーを相互検証しました。」
デジタルツインのアーキテクチャ
デジタルツインがどのように動作するかのアーキテクチャは、Stieberらによって説明されています。 al。 2020年のテクニカルペーパー「複合構造を製造するためのリアルタイムのプロセス監視と機械学習に向けて」:
これは、T-RTM機械、金型工具の現場センサー、デジタルツインの3つの部分で構成されています。この構造と特にデジタルツインは、次の目的O1〜O4を念頭に置いて開発されました。
- O1:工具の現場センサーを使用して、すべての複合部品の製造プロセスを監視します。
- O2:各製造プロセスをリアルタイムで視覚化して、プロセスに関する洞察をさらに深めます。
- O3:製造プロセスの結果を予測するために、シミュレーションデータと実際のデータでMLモデルをトレーニングします。
- O4:トレーニング済みのMLモデルを使用して、生産の拒否を減らします。
次に、センサーはデータをデジタルツインのエッジ分析に送ります。これを使用して、将来のフローフロントダイナミクスを予測し、各テキスタイルプリフォームの繊維量を決定し、ドライスポットを予測し、不良部品を減らすことができる異常を検出できます。
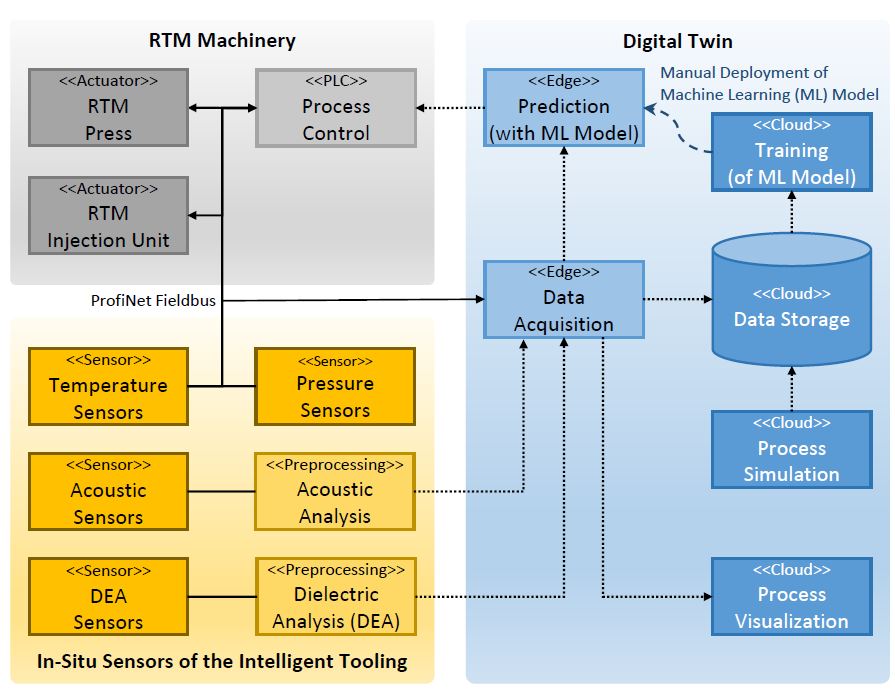
T-RTM機械は、2つの既製のコンポーネントで構成されています。Wickert(Landau in der Pfalz、ドイツ)440キロニュートンホットプレスとKrausMaffei(Munich、ドイツ)のT-RTM射出装置です。これらのマシンの両方とセンサーネットワーク全体は、製造プロセス全体の制御を担当するPLC(プログラムされたロジックコントローラー)に接続されています。
センサーは、生データをフローフロントまたは樹脂の硬化に関するより高いレベルの情報に変換するためにリアルタイムの前処理を必要とするため、前処理されたデータは、iba AGのibaPDAデータ取得ユニットを使用してエッジで直接記録されます( Fürth、ドイツ)。したがって、センサーデータは記録され、プロセスデータにリンクされた一貫したタイムスタンプとマージされ、部品情報は目標O1およびO2ごとのセンサーデータとマージされます。
製造プロセスを自動的に最適化するために、保存されたデータは、目的O3に対処するための機械学習(ML)モデルのトレーニングに使用されます。これらのモデルは、たとえば、センサーネットワークから樹脂のフローフロントを再構築し、フローフロントの進行を予測し、理想的には、プロセスインスタンス中または後続の実行のいずれかで結果を最適化するためにプロセスパラメーターを適応させる役割を果たします。 。信頼できるモデルをトレーニングするには、通常、実際のデータでは不十分であるため、デジタルツインチームは、PAM-RTMシミュレーション実行を使用して測定データを補強しました。シミュレートされたデータを使用して事前トレーニングした後、デジタルツインは実際のデータで微調整されました。この戦略は転移学習として知られており、コンピュータービジョンおよび自然言語処理アプリケーションでうまく採用されています。 MLで可能な高度な分析により、予測機能とプロセスの視覚化、および閉ループ制御が向上します。
工業用複合材料製造用のセンサー統合
では、複合部品メーカーは、この技術をどのように適用して、自社の製造プロセスで閉ループ制御を開発するのでしょうか。 Sauseは、いくつかのタイプのセンサーを使用して、流れと硬化/重合の監視を相互検証し、補足情報を提供することが理にかなっていると述べています。次に、各場所に配置されるタイプを含め、センサーの配置を定義する必要があります。 「たとえば、どこにでも圧力センサーや温度センサーは必要ありませんが、樹脂の入口や複雑な形状のポイントなど、重要なデータポイントが必要な場所だけに必要です。」
センサーはいくつですか? 「CosiMoの場合、74個のセンサーを使用しましたが、0.5メートルの部品の場合、使用するセンサーは少なくなります。ジオメトリと重要なポイントによっては、おそらく35〜40個になります」とSause氏は言います。 「それは製造プロセスにも依存します。たとえば、航空宇宙には何十年にもわたって使用され、確立されたプロセスがあります。これらの場合、あまり多くのセンサーを必要としない可能性があり、最初に多くの開発作業を行わなくてもセンサーを統合できる可能性があります。しかし、他のプロセスはより未知であり、事前により多くの作業が必要になります。 CosiMoの場合、PA6へのin-situ重合でT-RTMを使用することを検討していましたが、これは、たとえばエポキシを使用したRTMほど文書化されていませんでした。」
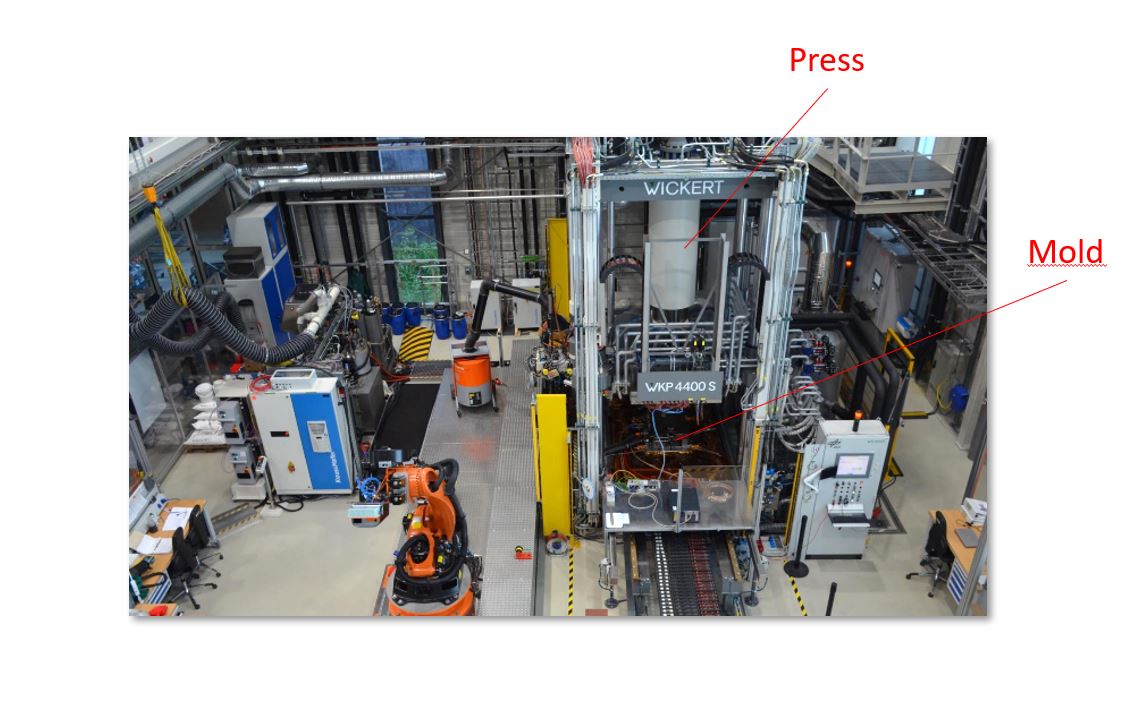
CosiMoプロジェクトの製造装置は、Wickert440kNプレスとKraussMaffei射出成形機で構成されていました。このシリーズの写真クレジット:CosiMoプロジェクト、DLR ZLPオーグスバーグ、オーグスバーグ大学
デジタルモデルの構築にはどのくらいの時間がかかりますか?そして、それは閉ループ制御を達成するために常に必要ですか? 「繰り返しになりますが、それはあなたのプロセスとあなたが到達したいレベルに依存します」とSauseは言います。 「まず、センサー情報を統合することで、処理のブラックボックス内で何が起こっているのか、どのパラメーターを使用するのかを視覚化できます。
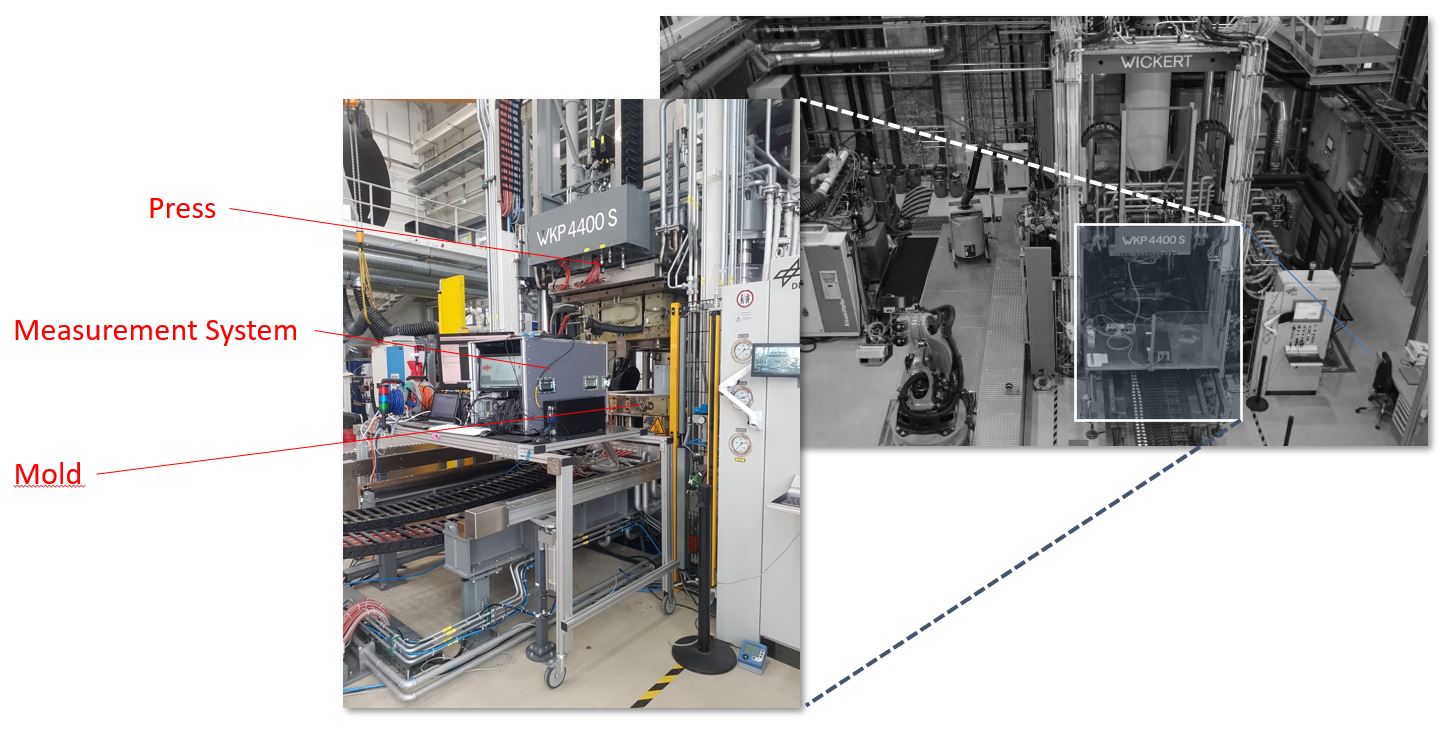
CosiMoで開発された閉ループ制御システムは、インモールドセンサーとiba AGによるデータ取得システム(ここに示す測定システム)も統合しました。
その最初の目標に到達したら、閉ループプロセス制御を実現するためにさらにいくつかのステップがあります。おそらく、中途半端なのは視覚化であり、プロセスを適応させてパーツの拒否を防ぐために、自分で停止ボタンを押すことができます。それも始まりです。そして、デジタルツインを開発することはできますが、トレーニングデータが必要です。したがって、何らかの方法でそれを提供する必要があります。つまり、入力データとして使用するいくつかのパーツを作成できます。ただし、低品質の部品も製造する必要があります。したがって、機械学習アプローチのトレーニングに投資する意欲の問題です。」
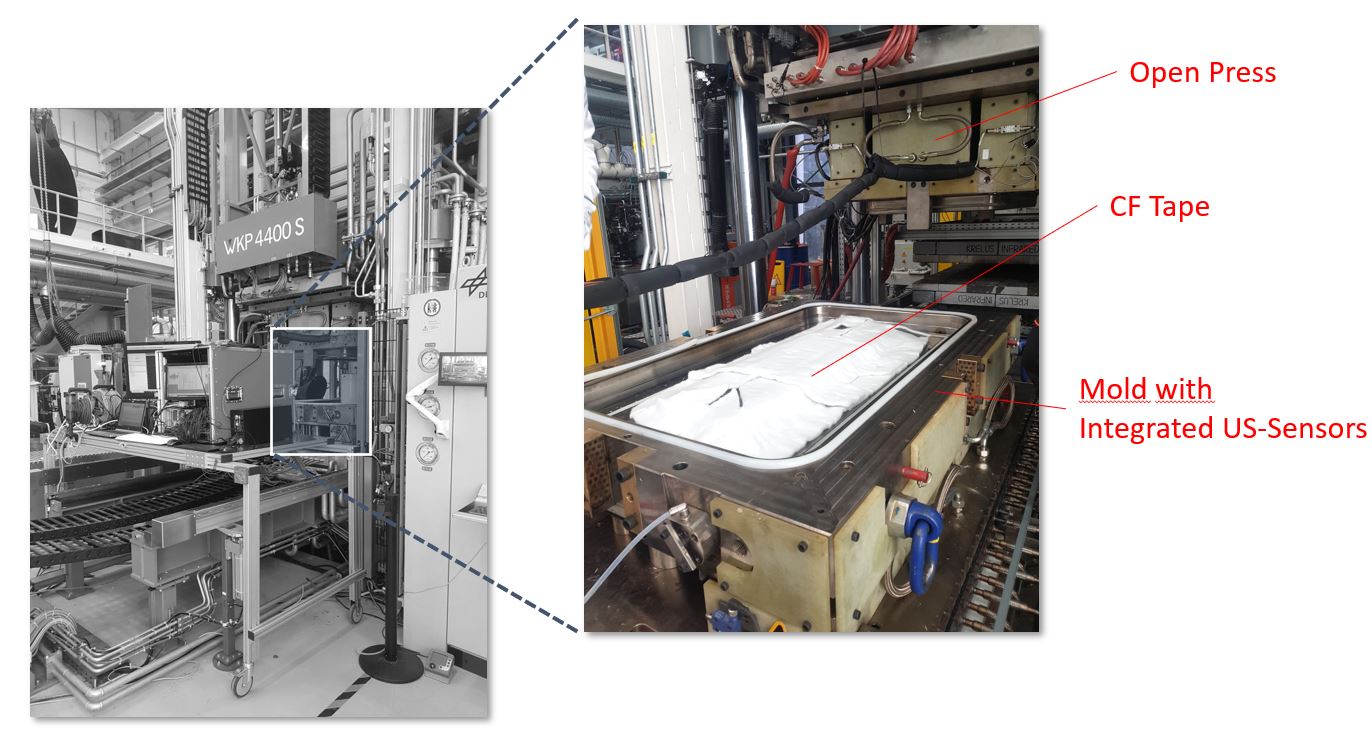
トレーニングが完了すると、デジタルツインはプロセスパラメータを最適化し、閉ループプロセス制御を提供できます。
ただし、Sauseは、CosiMoで採用されている転移学習アプローチは、「状況を完全に変えることのない同様の形状や材料システム、およびその他のバリエーションにある程度転移可能であることを認めています。したがって、この方法でデータベースを構築し、すでに取得したデータを使用して効率の傾向を特定することができます。その後、それを他の質問に使用できます。」
したがって、開始する方法は次のように思われます。センサーを使用し、センサーに合わせてデジタルモデルを構築して、プロセスを理解できるようにしますか? 「もちろんです」とSauseは言います。 「そして、今日の生産で使用されている機械のほとんどはまだ非常に愚かです。多くのマシンには、何が起こっているかについてフィードバックを提供するためのデータベースを提供できるセンサーがありません。そうです、センサーシステムの統合が最初のステップになります。ただし、体系的を実行する必要があります データを取得し、データストレージアーキテクチャを提供して、データを使用して何かを実行できるようにします。 。実際、センサーが統合されている企業はたくさんありますが、データに対しては何もしていません。」
AIプロダクションネットワーク
上記の質問に答える際に、Sauseは、センサー統合とデジタルツインサービスを提供できるスピンオフ企業だけでなく、UNA内のさまざまなグループに戻ってきました。そのために、アウグスブルクAIプロダクションネットワークは、2021年1月にUNA、DLR ZLP、およびFraunhoferIGCVによって立ち上げられました。 「コラボレーションフレームワークは、過去にDLRとフラウンホーファーで行ったプロジェクトから生まれました」とSause氏は言います。 「私たちはCosiMoからAIベースの生産開発の青写真を取り入れ、現在それを非常に大規模に拡張しています。たとえば、CosiMoでの作業の予算は1,000万ユーロでしたが、AI Production Networkの場合、初期資金として9,200万ユーロです。これにより、製造業でAIを活用するCosiMoのような多くの新しい研究プロジェクトを開始できるようになります。そして、私たちはコンポジットだけに取り組んでいるわけではありませんが、それらに重点を置いています。」
超音波センサーを使用してCNC機械加工を改善することは、2021年にすでに開始されたプロジェクトの1つです。添加剤の製造と、特別にリサイクルされた繊維強化材料の再利用。」
各組織が果たす役割については、各機関に予算が割り当てられているため、競争はないとSause氏は説明します。 「私たち全員がシェアを持っているため、これまでと同じように自由にコラボレーションできます。また、私たちはお互いをよく知っており、私たちの能力、長所、短所をよく知っています。できることとできないことを知っているので、一緒に仕事をするのは楽しいです。私たちは、私たちと協力したいと考えている多くの企業からアプローチを受けており、現在、私たちの能力の側面から理想的な一致を見つける方法について話し合っています。」
5,000平方メートルの生産施設に関しては、「私たちは皆一緒にそれを実行します」とSauseは言います。 「2023年の初めまでに開業し、機械の設置を開始する予定です。また、個々のセルをリンクする自動化された制作設定を提供します。それらの多くは、複合生産技術に焦点を当てています。また、このような制作環境でAIができることを、業界のパートナーに紹介してデモンストレーションするためにも行います。また、業界のパートナーが参加し、施設に機械を設置して、プロジェクトを一緒に実行し、サイトの新しいソリューションをリンクして統合する方法を確認できるようにしたいと考えています。」
樹脂
- 遮断と制御が難しいバルブ
- CBM用のセンサーとシステム
- スリーステートエレクトロクロミックデバイスのディップコーティングプロセスエンジニアリングと性能最適化
- OTOMcompositeは、レーザー支援テープの配置と巻き取りを使用して、Composites4.0を作成するためのソフトウェアを開発しています
- 複合材料用の再処理可能、修理可能、リサイクル可能なエポキシ樹脂
- 複合材料の硬化監視のためのACおよびDC誘電測定の組み合わせ
- TPACとTPRCは、熱可塑性複合材料のリサイクルプロセスを開発しています
- コントロールパネルハウジングの構成と配線に関するヒント
- 超音波加工とは何ですか?-作業とプロセス
- 制御用の接続:位置およびモーションセンサー用の通信インターフェース
- プロセス最適化のためにフィールドデータを収集する