少量の航空構造物の自動複合材料製造のための設計
民間航空機用の複合航空構造物の製造は50年以上にわたり、ボーイング787およびエアバスA350用に2000年代初頭に開発された、小さな部品から非常に大きな一次構造(胴体、翼、尾翼、エンジン)へと着実に進歩しました。この進化の大部分は、オートクレーブで硬化した炭素繊維/エポキシプリプレグの使用に依存していました。最初は手作業で敷設し、最終的には自動繊維配置(AFP)、自動テープ敷設(ATL)、およびその他の機械ベースのプロセスを介して敷設しました。
これらの材料およびプロセス(M&P)テクノロジーは、パンデミック前の月間ビルドレートが10〜15であったワイドボディの787およびA350に適していました。ただし、ボーイングとエアバスは将来を見据えており、月間60〜100の建造率が見込まれる単通路航空機の一次構造に複合材料を適用することを検討しているため、設計とM&Pは高率の脱オートクレーブ成形を優先します。 -オートクレーブ(OOA)、高度に自動化されたプロセス。これらのプロセスには、とりわけ、樹脂トランスファー成形(RTM)、圧縮成形、および液体樹脂注入が含まれます。
ただし、高率の製造が商用航空宇宙セクターを支配する場合でも、低率の複合航空構造の製造 リージョナル航空機やビジネスジェットプログラムを含む航空機は、存続するだけでなく、高レートのプログラムで展開されるのと同じコスト、設計、およびM&Pの革新のいくつかから利益を得ることができます。
European Clean Sky 2プログラムがOPTICOMSを立ち上げたのは、このすべてを念頭に置いていました— Opti mized Com posite S 小型航空機用の構造。 OPTICOMSは、航空宇宙製造業者であるIsrael Aerospace Industries(IAI、Lod、Israel)が主導するコンソーシアムであり、革新的な自動化技術、材料、ソフトウェア、工具、機械を提供するパートナーと協力しています。 OPTICOMSの目的は、自動製造、統合構造、OOA硬化、大規模な構造ボンディング、革新的な製造および組み立てツール、ボンドラインの構造ヘルスモニタリング、仮想テストを特徴とする低率生産ウィングボックスの設計を評価することです。
IAIの航空グループのR&Dディレクターであり、OPTICOMSのマネージャーであるArnold Nathanは、次のように述べています。大量生産がある場合。」OPTICOMSは、しないときに自動化を正当化できるかどうかを確認するために設定されました。 大量生産しています。複合材料の製造自動化は、少量生産に対して競争力があり、費用対効果が高いでしょうか?」
翼のデザイン
OPTICOMSは、イタリアのビジネス航空機メーカーであるピアジオエアロスペース(ジェノヴァ)がP180 Avanti 用の全複合代替翼の開発を求めるCleanSky2リクエストから生まれました。 9人乗りビジネスツインターボプロップ。ウィングボックスの長さは6.8メートル、根元の幅は0.71メートル、先端の幅は0.28メートルです。ネイサン氏によると、ピアジオは、オールメタルのレガシーウィングボックスの代替品を評価することに熱心でした。同じ寸法でありながら、軽量化(20%)を提供する代替品です。さらに、従来の複合ウィングボックスの製造と比較して、コストを20〜30%削減する必要があります。 IAIとそのパートナーは契約を獲得し、2016年にピアジオとの協力を開始しました。
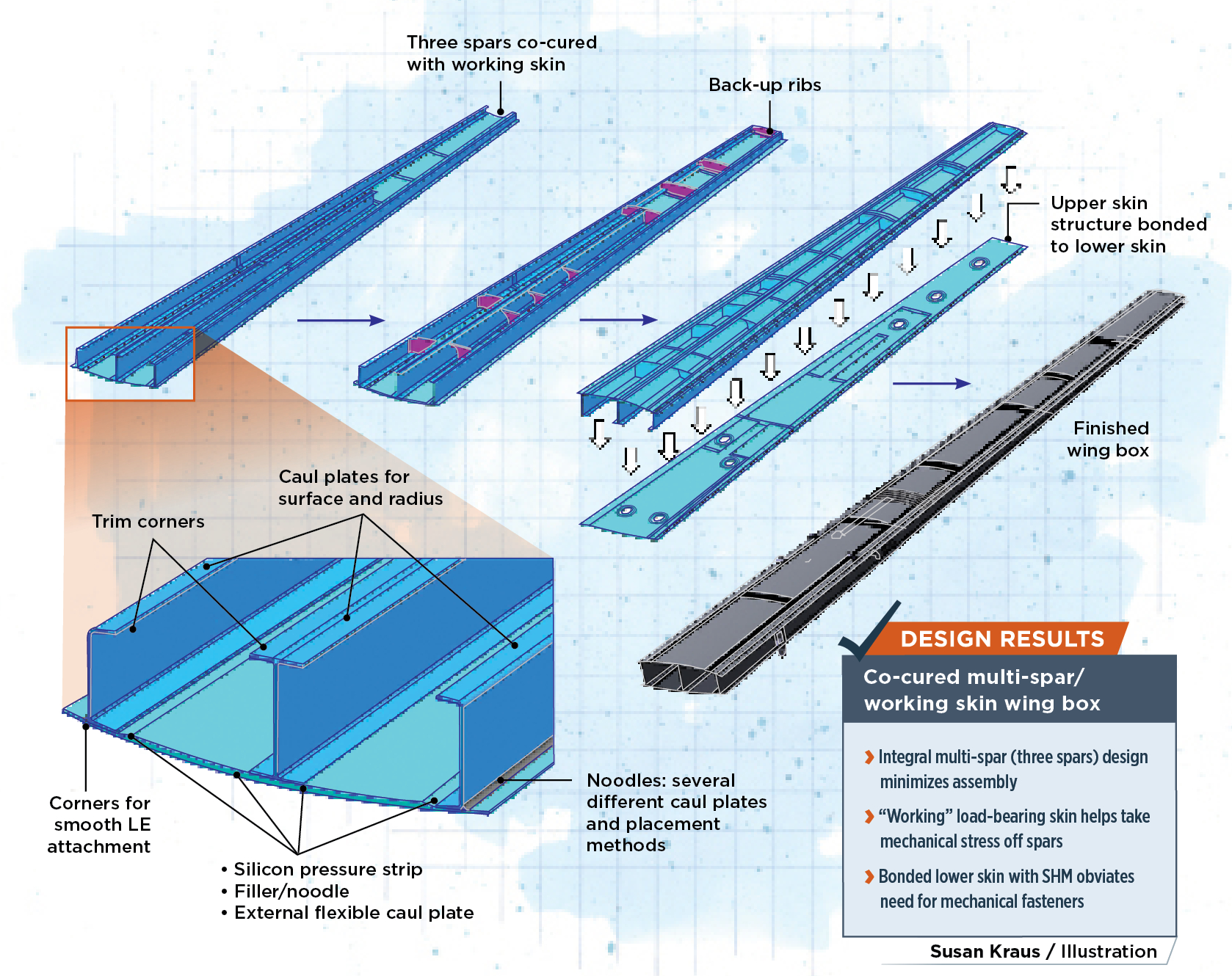
OPTICOMSは、少量の全複合ウィングボックスの自動製造に最適な翼の設計、材料の組み合わせ、およびOOA製造プロセスを評価および決定するために、一連の非常に詳細で入念に実施された貿易調査を実行するように設計されたマルチパートプログラムです。
IAIとOPTICOMSは、3つのパートナーが提供する3つの製造プロセスの使用に焦点を当てて評価することを早い段階で決定しました。Techni-ModulEngineering(TME、クード、フランス); Coriolis Composites(Queven、France)が提供する、ドライおよびプレプレグトトウの自動ファイバー配置(AFP)。 Danobat(Elgoibar、スペイン)が提供する自動乾物配置(ADMP)テクノロジー。これらのテクノロジーとパートナーの選択は、IAIの多変量貿易研究全体を導くために重要です。
設計結果
- 一体型マルチスパー(3つのスパー)設計により、組み立てが最小限に抑えられます
- 「機能する」耐荷重スキンは、スパーから機械的ストレスを取り除くのに役立ちます
- SHMで接着された下部スキンにより、機械的な留め具が不要になります
この貿易調査の最初のステップは、設計評価でした。この取り組みは、高度な技術の構造設計エンジニアであるAdamSawdayがIAIで主導しました。 Sawdayは、彼とIAIが翼の設計にクリーンシートアプローチを採用し、さまざまなアーキテクチャにわたって18を超える概念を研究したと述べています。デザインはすぐに2つのカテゴリのいずれかに分類されました。 1つ目は、ウィングボックススキンが耐荷重構造になる「作業」スキンを採用しています。 2つ目は、スパーキャップがロードされた非動作スキンを採用しています。これらのカテゴリには、リブ、ストリンガー、2つのスパーを使用した従来のコンセプト、またはリブやストリンガーを使用しないマルチスパーと呼ばれる3つのスパーを使用したデザインが含まれます。いくつかの概念では、半ば機能するスキンを生成するサンドイッチパネル構造の使用も検討されました。
「私たちのモットーは、製造の労力を減らし、組み立ての労力を減らすことでした」とSawday氏は言います。 「そして、より統合されたより効率的な構造を開発できれば、より安価で軽量な構造が得られると信じています。」
Sawdayは、プログラムのコストと重量の目標を達成する能力を評価するために、一連のメトリックに対して設計が測定されたと述べています。これらの指標には、材料費、設計の複雑さ、コンポーネントの製造コスト、組み立てコスト、非破壊検査(NDT)コスト、工具およびジギングコスト、重量、強度、技術準備レベル(TRL)、生態学的考慮事項、リスクプロファイル、堅牢性、および信頼性。これらのうち、最も重視される基準は、重量、製造および組み立てのコスト、設計の複雑さ、TRL、およびリスクプロファイルでした。
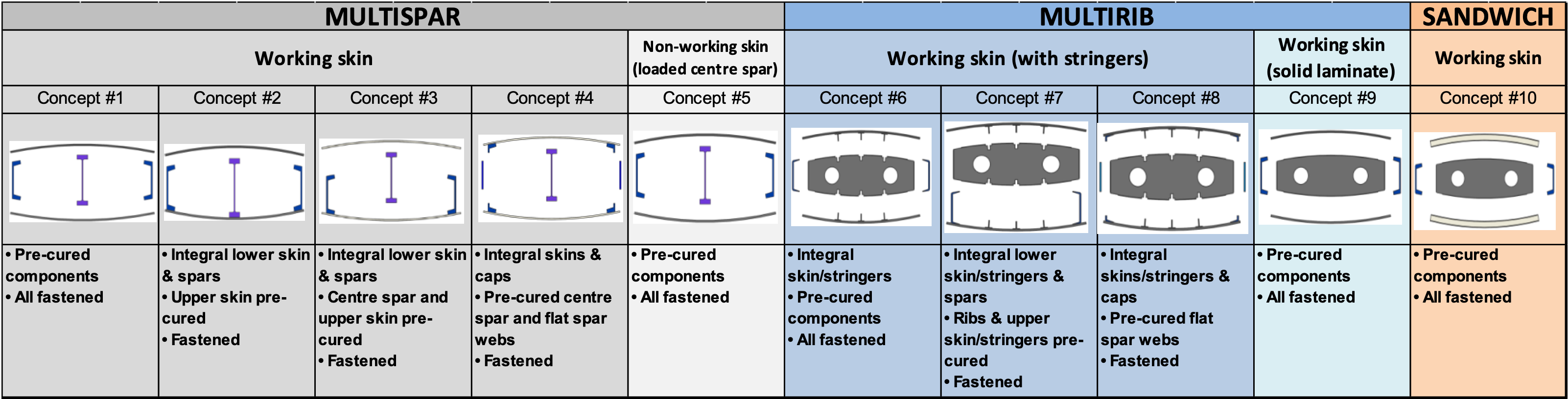
最終設計へのダウンセレクション
この評価のデータは、IAIが設計コンセプトを10人のファイナリストにダウンセレクションするのに役立ちました。 4つはマルチスパー/ワーキングスキン、1つはスパーがロードされたマルチスパー/非ワーキングスキン、4つはストリンガー付きのマルチリブ/ワーキングスキン、1つはストリンガーなしのマルチリブ/ワーキングスキン、1つはサンドイッチでしたストリンガーのない構造/作業スキン。各設計は、予備硬化、同時硬化、接着、または機械的固定のさまざまな組み合わせを提供しました。
最終的な設計に到達するには、最初の調査と同じ基準の多くを使用した別のラウンドの取引調査が必要でした。各デザインには、基準をどの程度満たしているかに基づいて、トレードバリューが与えられました。 「この大きなトレードオフテーブルがあり、各設計オプションには価値があり、これは最も強力なオプションを見つけるのに役立ちました」とSawday氏は言います。
Sawday氏は、最初から、貿易調査で一貫して良好に機能し、トップに立つ可能性が高いと思われる設計が1つありました。そして、それはしました。内部でマルチスパー/ワーキングスキン#2と呼ばれ、高度に統合され、同時硬化されたアッパースキンと3つのスパーを備えています。次に、これらはアクセスパネルのある下部スキンに接着されます。スパーの間に選択的に配置されているのは、曲げ荷重のほとんどに耐える皮膚をサポートするように設計された一連の「バックアップ」リブです。
「私たちが開発した最も好ましい構造は、皮膚が耐荷重性になるマルチスパーを備えた構造でした」とSawday氏は言います。その結果、スパーはより単純で薄い構造になり、従来の複合翼の設計ほど重くなりません。これらのスパーを一定の断面積で非常に単純にすることができれば、多くの頭痛とスクラップを節約できると考えました。」
Sawdayによると、結合された一体型マルチスパー/ワーキングスキンの設計は、組み立てコストの削減、軽量化、自動化の容易さ、および全体的な部品点数の削減に特に期待できます。ただし、この設計を実現するために最適な材料と製造プロセスはどれかという疑問が残りました。
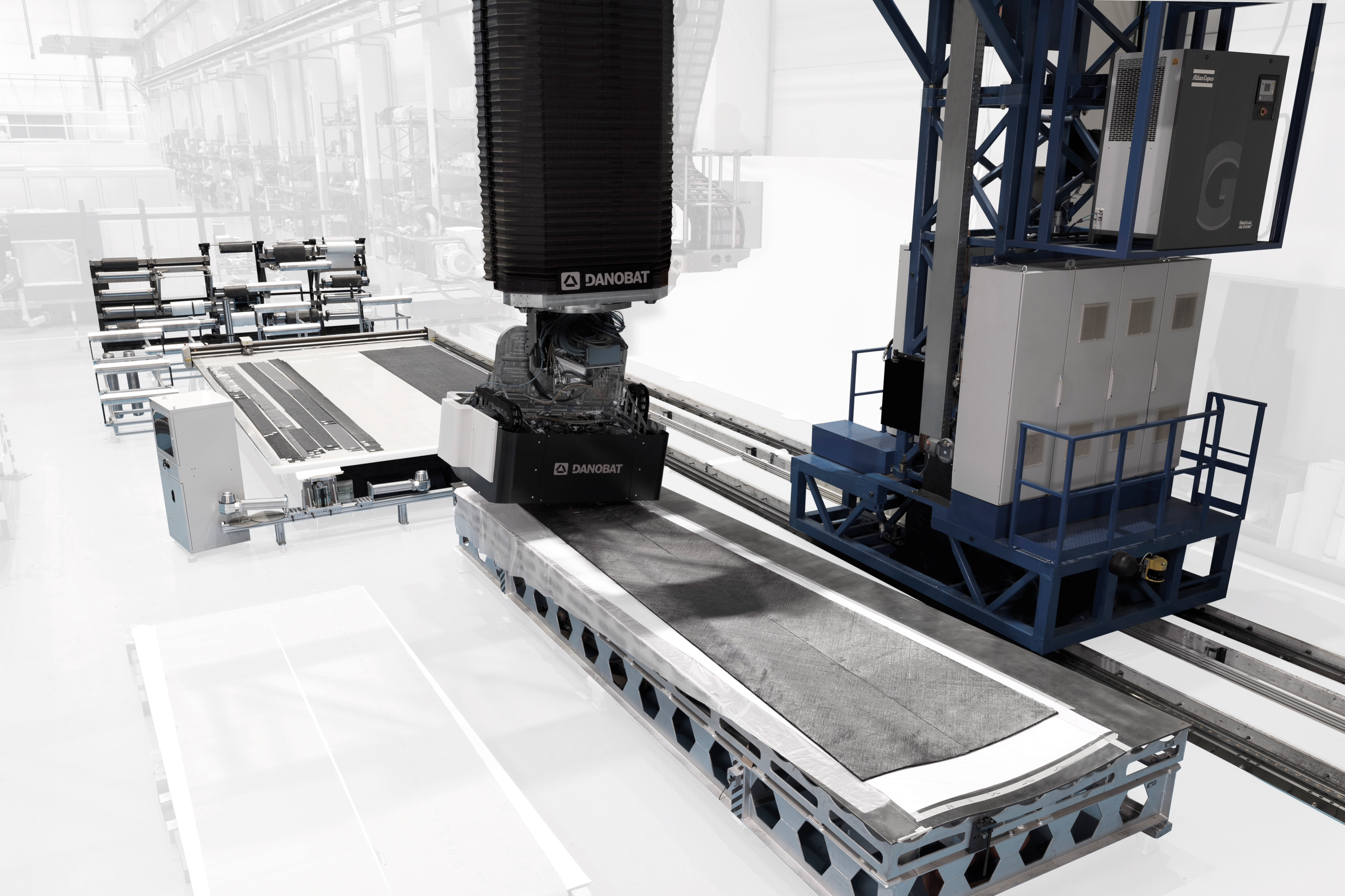
M&Pトレードスタディ
最初は材料貿易の研究でした。これらは、IAIで複合材料エンジニアのYanivYurovitchによって実行されました。彼は、OPTICOMSが、Piaggio、IAI、および技術パートナーからの推奨に基づいて、OOA炭素繊維プリプレグ、乾燥炭素繊維(テープおよびファブリック)、および樹脂の評価を開始したと述べています。その結果、35の認定された新しい資料のリストが作成されました。
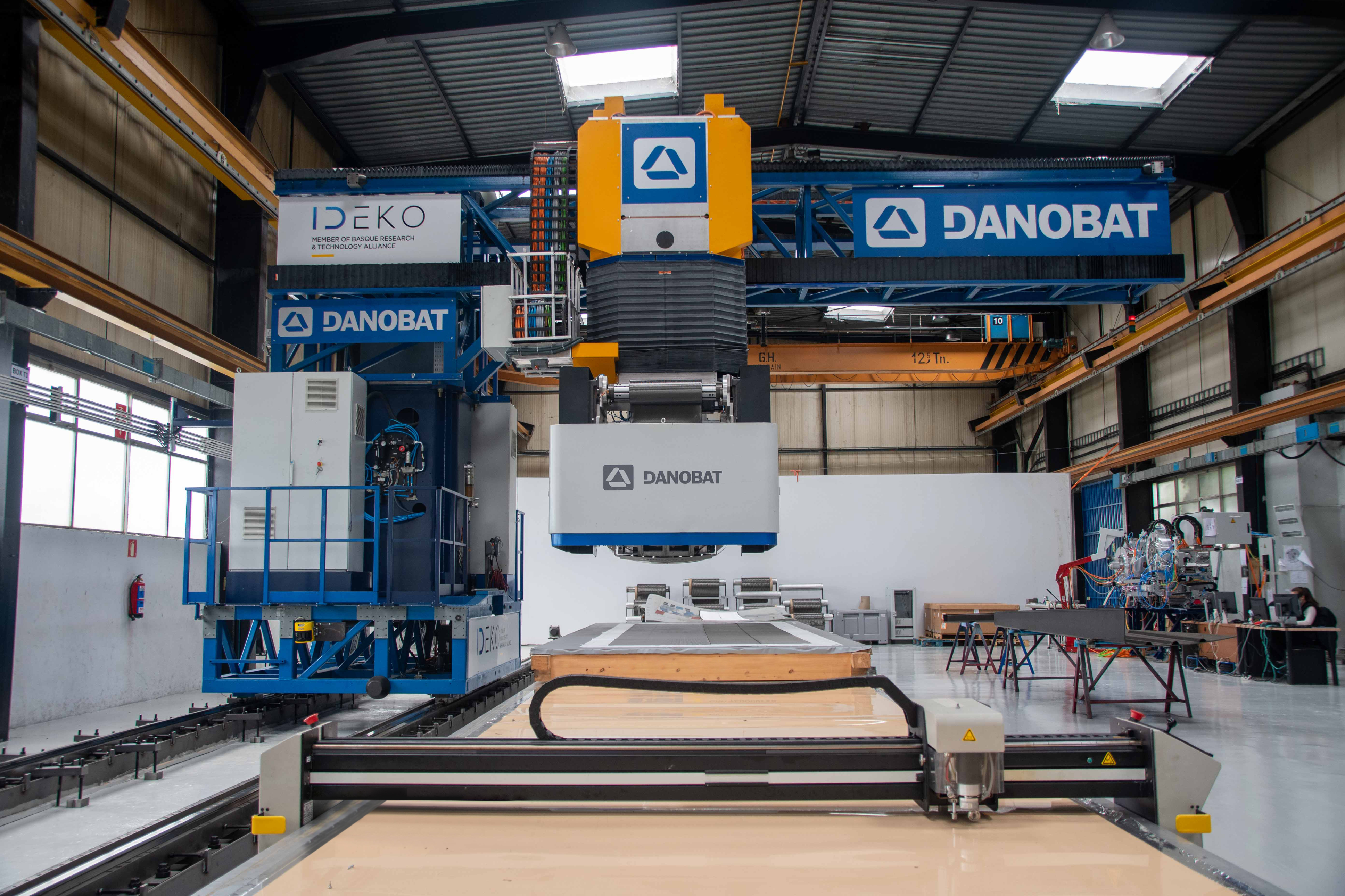
次に、この最初のグループの材料は、OPTICOMSプロジェクトの最も重要なパラメータであるコスト、ガラス転移温度(T g )に基づいてスクリーニングされました。 )、粘度(注入または注入用)および自動レイアップ技術への適合性。この評価により、材料リストが35から20のプリプレグ、乾燥繊維、および樹脂に減少しました。
これらの20の材料のそれぞれのサンプルが注文されました。その後、ユロビッチはクーポンを作成し、次のダウンセレクトの一部として機械的テストを実行しました。 「それは本当に大きな作業パッケージでした」とYurovitchは言います。 「これにより、より多くの決定を下し、最後の3つの材料を選択することができました。」これらの繊維/樹脂の組み合わせは次のとおりです。
- Toray Composites Materials America’s(Tacoma、WA、U.S。)2510炭素繊維/エポキシプリプレグ。
- Hexcel(米国コネチカット州スタンフォード)のHiTapeカーボンファイバーUDテープ、HexcelのHexFlowRTM6エポキシ樹脂で使用。
- SAERTEX(ドイツ、ザーベック)が提供する炭素繊維非圧着布(NCF)で、ソルベイ複合材料(米国ジョージア州アルファレッタ)のPRISMEP2400強化エポキシと注入して組み合わせる。
このリストは明らかに乾燥繊維の使用を支持しており、それは製造プロセスとして注入を支持しています。ネイサンは、これは、少量の環境でプリプレグの貯蔵寿命を管理するという課題によって部分的に推進されていると言います。 「少量生産について話しているときは、多くのプリプレグを持ち歩き、貯蔵寿命の管理について心配する必要はありません」と彼は言います。 「乾いた繊維にはその問題はありません。」
これらの3つの材料は、OPTICOMS用に選択された1つ以上の製造プロセスともペアになっています。東レプリプレグはピックアンドプレースおよびAFPと一致し、HexcelのHiTape / RTM6はAFPおよびピックアンドプレースと一致し、SAERTEX NCFピックアンドプレースまたはADMPと一致します。
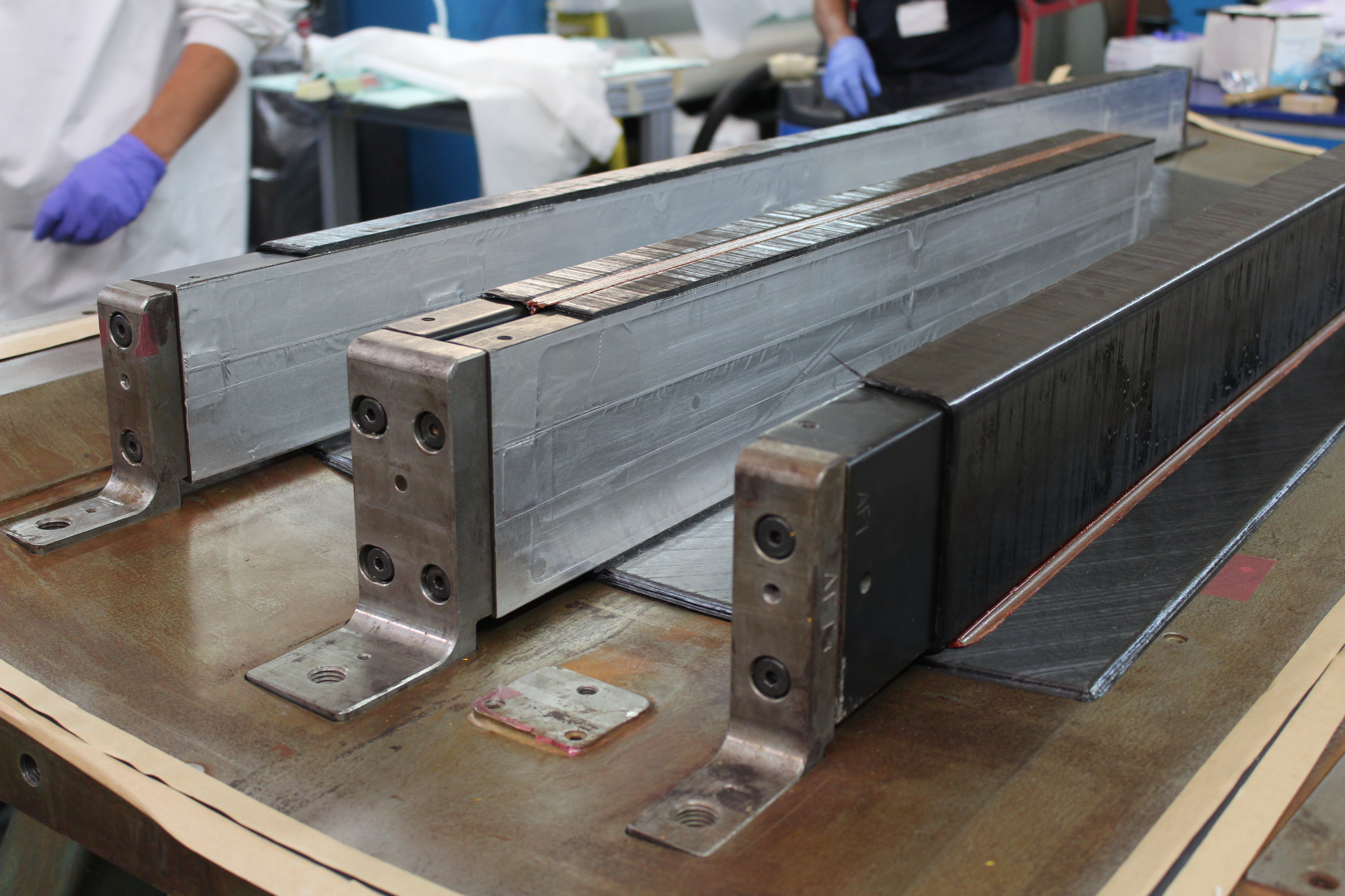
自動化された製造プロセス(どのタイプの部品に最も適しているか)に関する取引は、IAIとOPTICOMSによって現在も実行されています。しかし、予備的な結果は、確かに特定の方向に技術を向けているとネイサンは言います。たとえば、もともと風力タービンブレードの製造で幅の広い布地をすばやく配置するために開発されたDanobatのADMPテクノロジーは、OPTICOMSでも同様に効率的であることが証明されています。この技術はOPTICOMSの間に成熟し、その堅牢性と信頼性は向上しましたが、それでもAFPと比較して成熟度の低い航空宇宙レイアップ技術です。
逆に、豊富な航空宇宙経験を持つコリオリシステムを備えたAFPは、成熟した正確な技術ですが、ADMPに比べてレイアップ時間が長く、異常をチェックするために比較的頻繁な検査が必要です。コリオリは、この課題に対処するためのレイアップのインラインリアルタイム検査の開発により、OPTICOMSプロジェクト全体で目覚ましい進歩を遂げました、とネイサンは言います。最後に、カッティングテーブルからモールドへのカッティングファブリックの転送を自動化するように設計されたTMEのピックアンドプレーステクノロジーは、マルチスパー/作業のバックアップリブなどのより小さな個別のパーツに最も効果的であるように見えます。スキンデザイン。
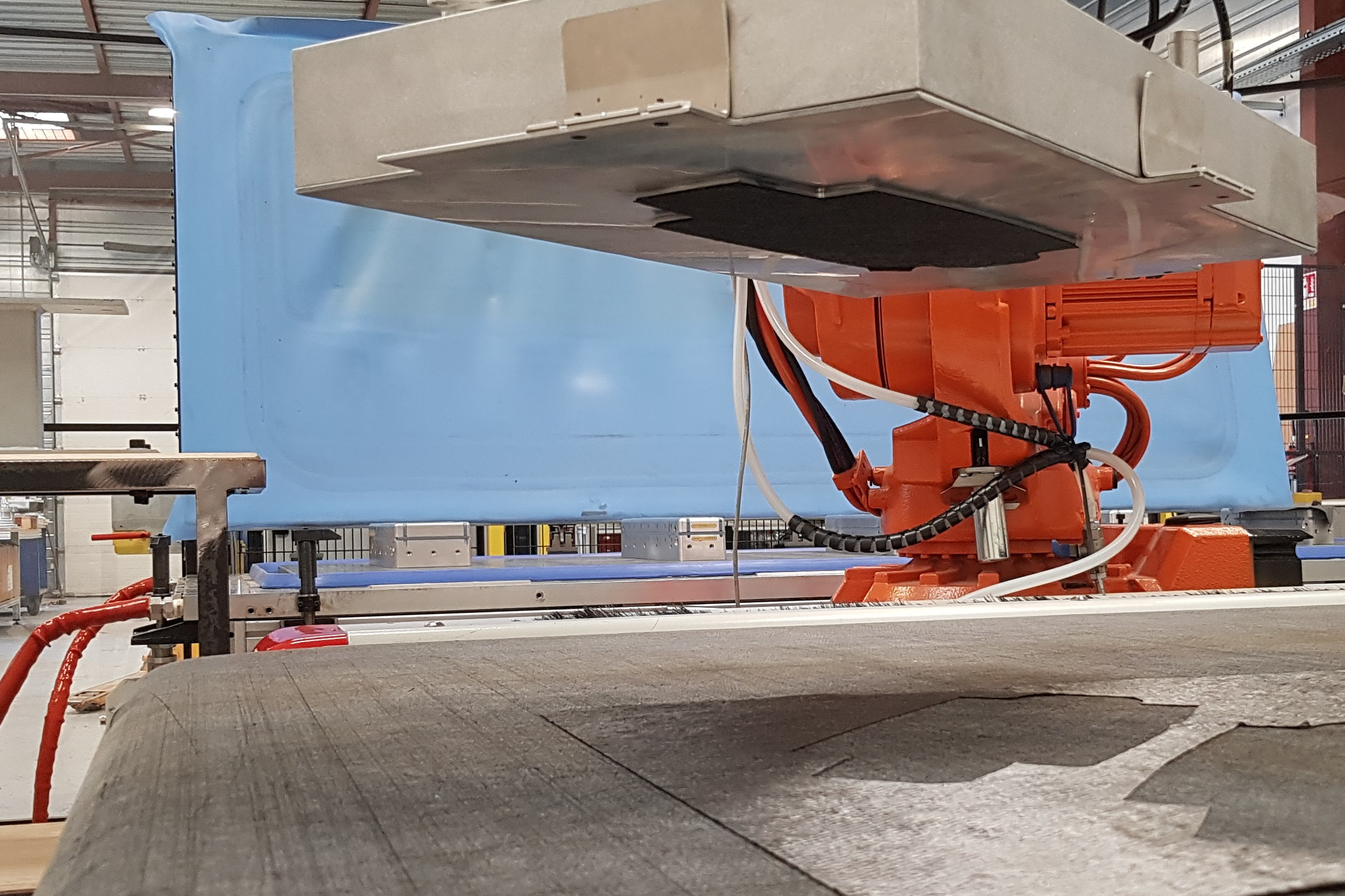
次のステップ
OPTICOMSは、プログラムによって定められた自動化、コスト、および軽量化の目標を達成するために順調に進んでいますが、製造プロセスと組み立てソリューションを評価するために行われる作業はまだ数か月あります。
「これはOPTICOMSの重要なポイントです」と彼は説明します。 「私たちはデザインの強力なダウンセレクションを持っていました。素材を厳選しました。プロセスのダウンセレクションがありました。これにはすべて時間と労力がかかります。これは、プロジェクトのユニークな側面の1つです。」
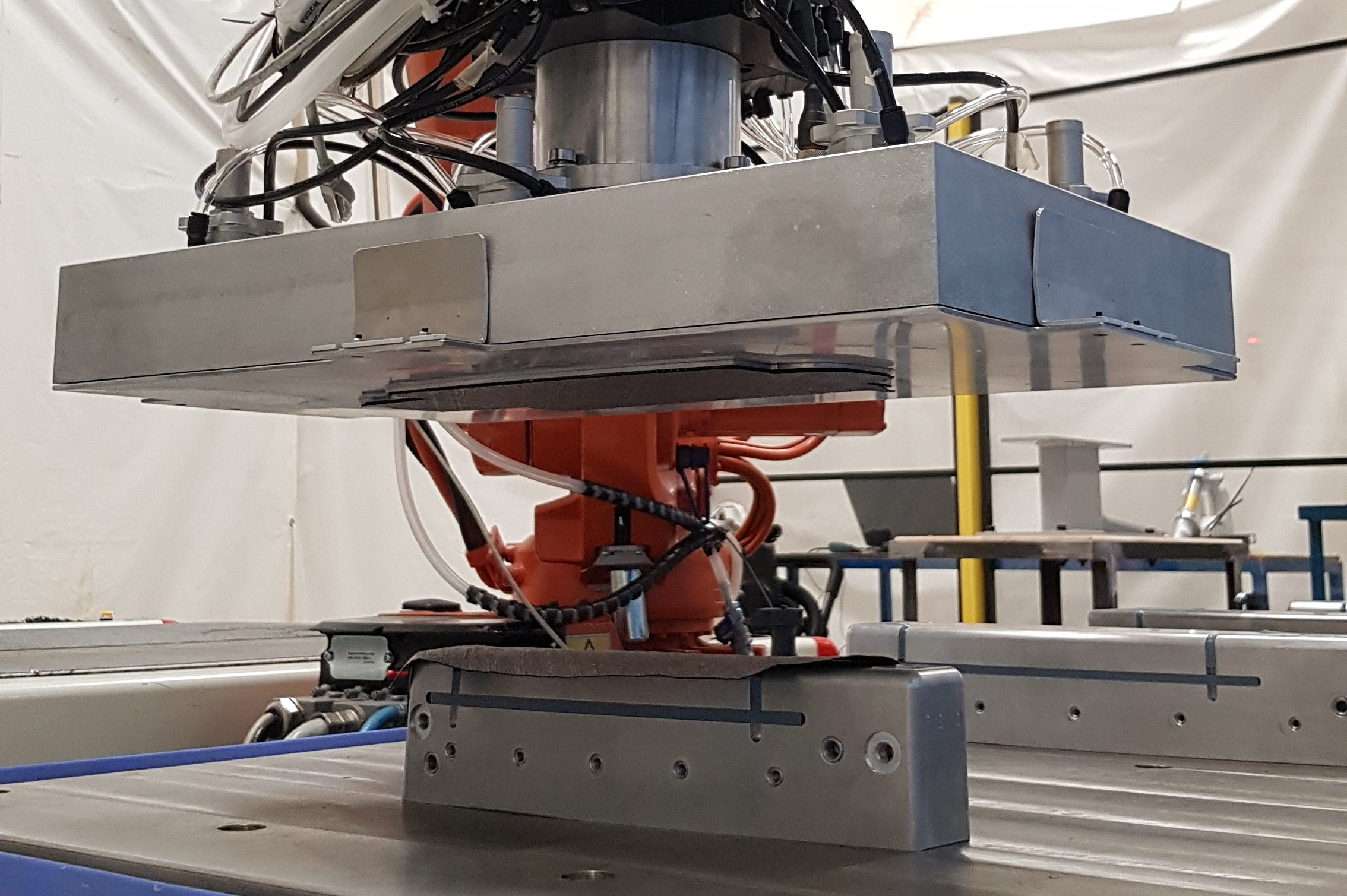
OPTICOMSは、プロジェクトの目標をサポート、保証、強化するためのテクノロジーとハードウェアの3つの提案募集(CFP)を開始しました。成功した提案は、OPTICOMSの「母」コアパートナーに関連付けられ、補足されるClean Sky 2プロジェクトになりました。これらはすべて、共通の目標に向けて協力しています。
この開発の最初の取り組みはFITCoWです。これは、作業用スキンと3つのスパーを同時硬化するための新しい一体型炭素繊維ツーリングシステムの開発を目的としています。 FITCoWの目標リストは野心的です。製造部品のコストを50%削減し、工具コストを30%削減し(金属代替品と比較して)、オートクレーブおよびOOA代替品と比較して製造時間を20%削減し、Invar工具と比較してCTEミスマッチを40%削減します。 、より優れた寸法制御機能により、加熱および冷却時間が20%短縮され、検査時間が40%短縮されます。
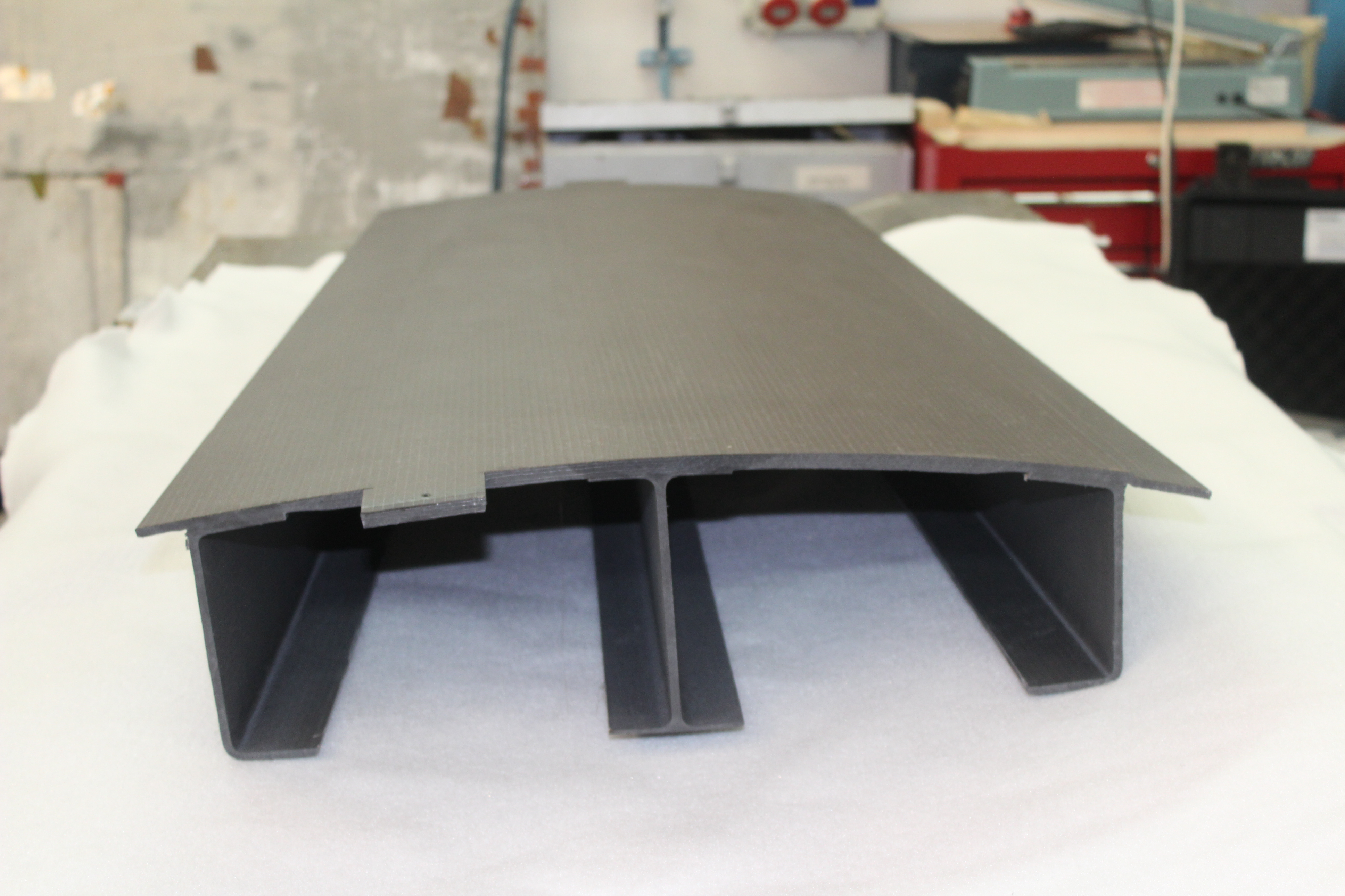
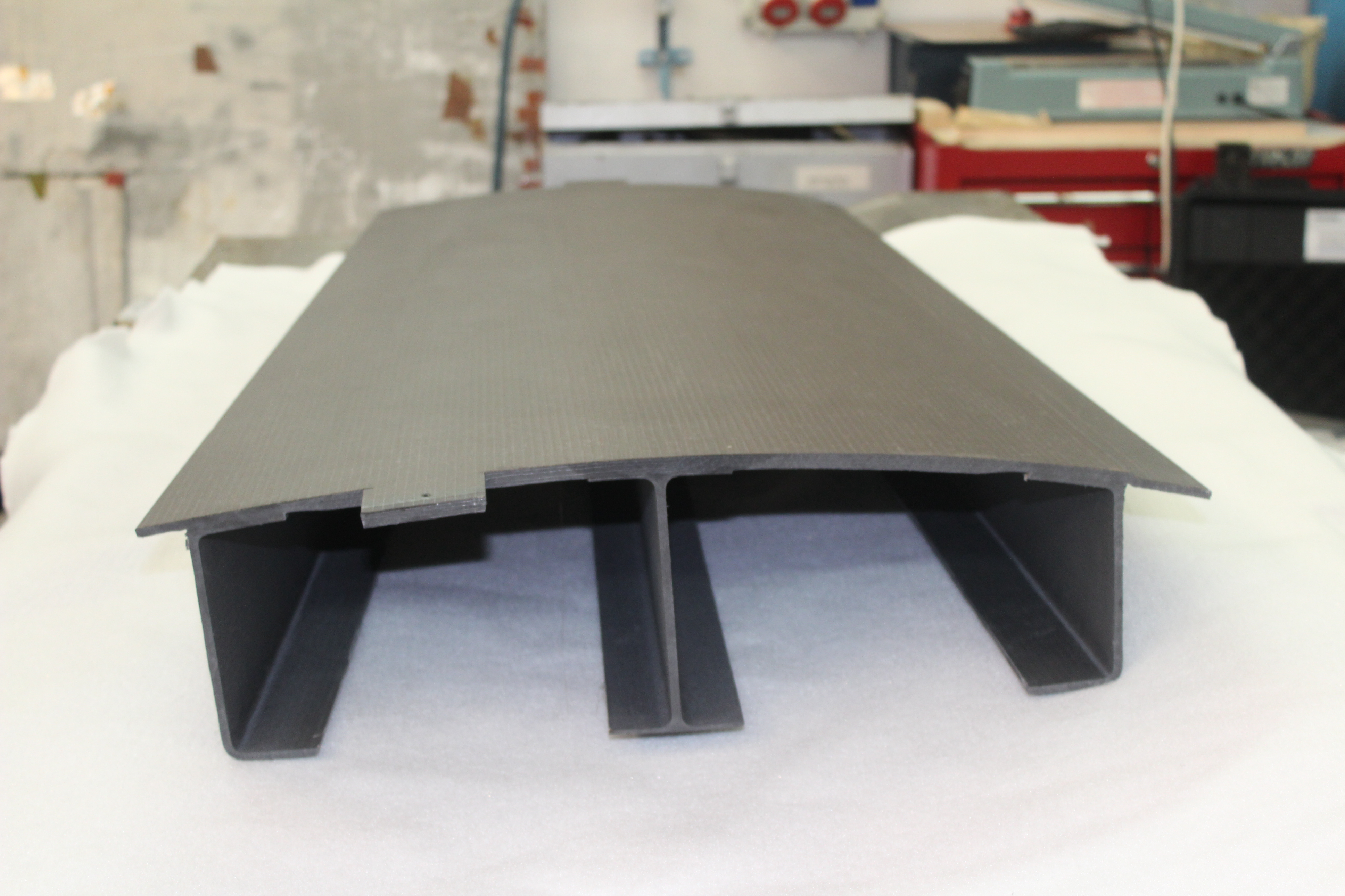
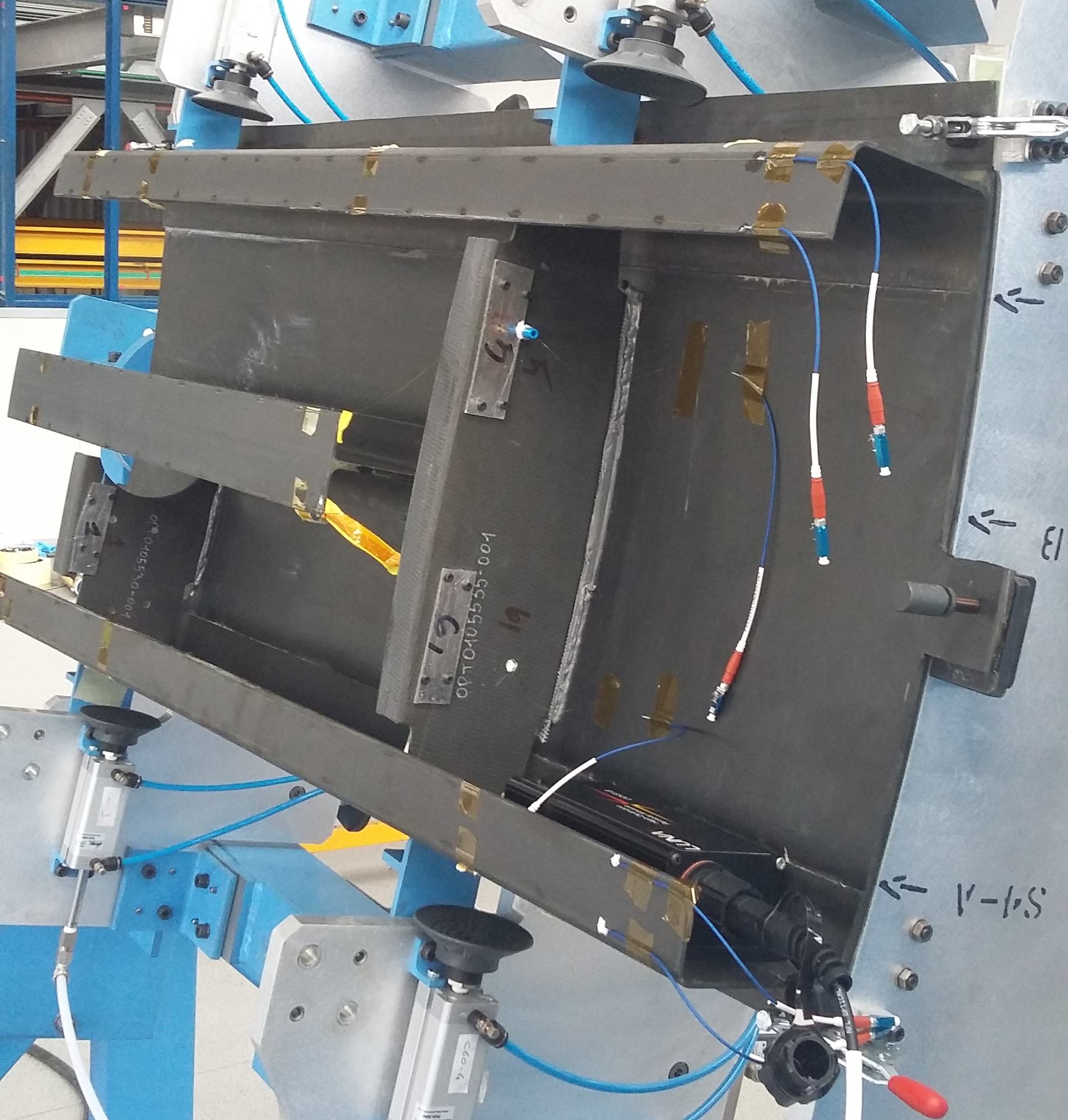
スパー/スキン構造を下のスキンに結合するために、2番目のCFPは、WIBONDと呼ばれる別のOPTICOMSプロジェクトをもたらし、接着剤を配置し、適切な圧力を加え、構造ヘルスのために結合ラインに光ファイバーセンサーを組み込む結合アセンブリツールを開発しました結合の監視; CW これと他のアセンブリ技術については、2022年に公開される別の記事で報告します。
3番目のCFPは、スパー/スキン構造の「スプリングイン」を引き起こす残留応力の重大な課題に対処するために開始されました。これらの変形は、ボンディングアセンブリプロセスに悪影響を与える可能性があります。 ELADINEプロジェクトは、OPTICOMSの取り組みに参加し、熱異方性、重合収縮、工具部品の相互作用、樹脂の流れ、圧縮、および構造全体の温度勾配をモデル化および予測するソフトウェアを開発しました。
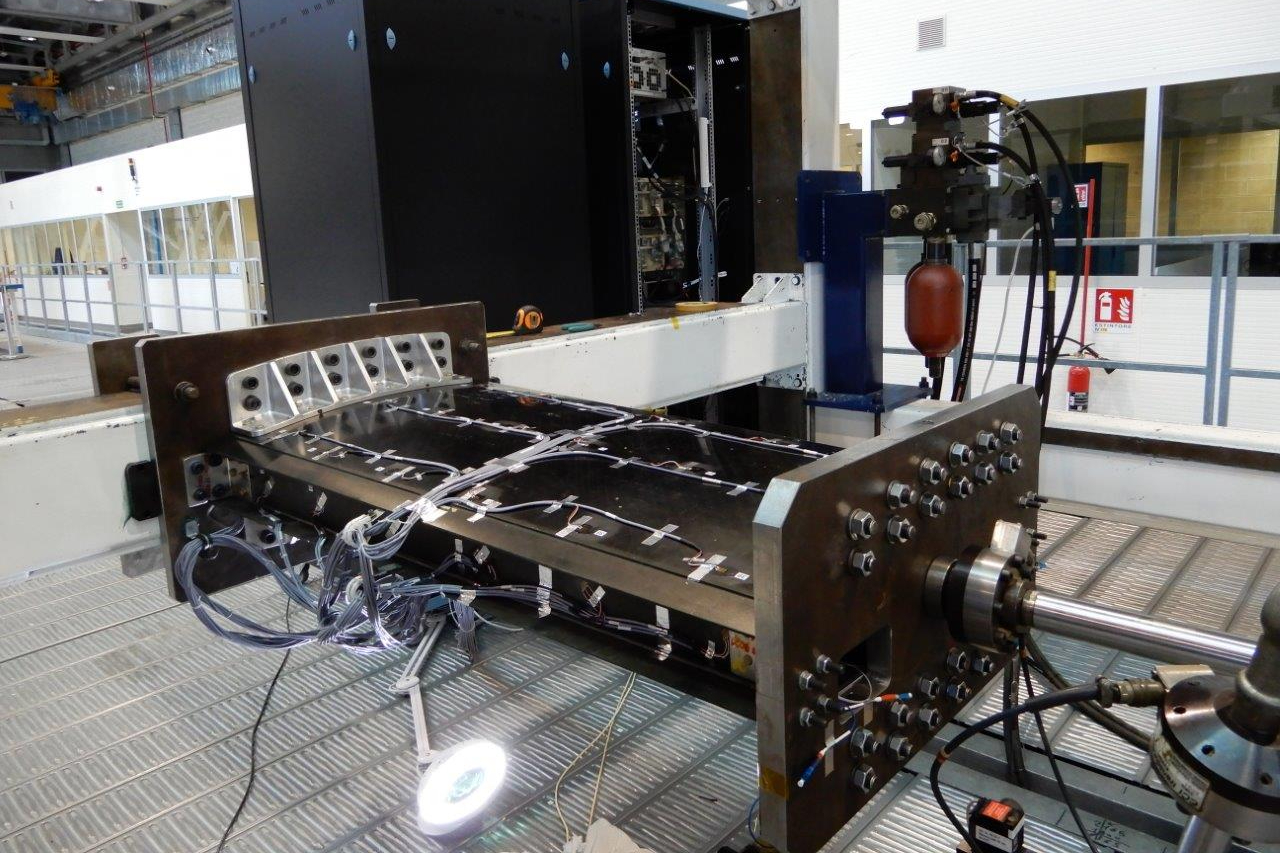
現在のIAIとOPTICOMSの主な焦点は、2022年第2四半期までに、静的および疲労試験のために完全な6.8メートルのデモンストレーターウィングをピアジオに提供することです。これに続いて、翼の全体的な性能と、プロジェクトの基準を満たすための設計、材料、およびプロセスの能力の分析が行われます。続いて、商品化に向けた次のステップの可能性について、ピアジオからの推奨事項があります。
ただし、IAIは、ピアジオを超えて、OPTICOMSウィングボックスが他の航空機にも適用されることを期待しています。 「このプロジェクトは特定の航空機に基づいていますが、設計をさまざまな厚さやサイズに拡張できるようにしようとしました」とSawday氏は言います。このテクノロジーは高度な適応性があり、またそうあるべきであるという事実を見失うことはありませんでした。」
樹脂