RTMフラッペロン、外骨格などの3D印刷CFRP金型
写真提供者:TUミュンヘンカーボンコンポジット(LCC)およびQPointコンポジットの議長
カーボンコンポジットの議長(LehrstuhlfürCarbonCompositesまたはLCC)は、SGLカーボン(ドイツ、ヴィースバーデン)からの資金提供を受けて、ミュンヘン工科大学(TUM、ドイツ、ミュンヘン)の機械工学科に2009年に設立されました。その使命は、シミュレーションとテストのプロジェクトを含む、炭素繊維強化ポリマー(CFRP)の材料、プロセス、およびアプリケーションの研究開発を行うことです。ドイツの大学システムの「椅子」は、教授と彼のチームで構成される最小の単位です。 LCCチームは、Prof。Dr.-Ingによって率いられています。クラウス・ドレクスラーは現在、30人のフルタイムの研究者を雇用しています。 SGLの資金提供は2016年に終了しましたが、LCCは、多機能胴体デモンストレーター(MFFD)の下半分の金型の構築を含む複合材料のR&Dでリーダーシップを発揮し続けています。下のサイドバーを参照してください。現在、3D印刷/添加剤も含まれています。製造。
このブログは、CEAD(オランダ、デルフト)が、LCCがロボットアームを使用した3D印刷用の押出機ベースのAMフレックスボットシステムの1つを購入したことを私に知らせたときに始まりました。しかし、LCCの研究者であるPatrick Consulとのその後のインタビューでは、Clean Sky 2内で、熱硬化性複合航空機の胴体を製造するための熱可塑性複合RTM金型と、ツールを製造するためのEMOTIONを3D印刷する、COMBO3Dを含むプロジェクトの宝庫が明らかになりました。 Clean Sky 2の熱可塑性複合材料多機能胴体デモンストレーター(MFFD)の下半分と、(オートクレーブからの)直接の現場圧密によって同じ胴体がどのように製造されるかを示すための二次部分ツールを成形するため。 TUMがどのようにしてこの時点に到達し、どこに向かっているのかについての議論全体が興味深いものであることがわかりました。
MMFD下半分型
私の2020年2月のブログ「多機能胴体デモンストレーターのLMPAEK溶接の証明」を参照してください。このサイドバーは、GKN Fokker(オランダ、ホーヘフェーン)のMFFDのプログラムマネージャーであるBasVeldmanによる2020年2月の論文「多機能胴体デモンストレーターの開発」から抜粋したものです。
MFFDの下半分のシェルは、溶接されたストリンガー、クリップ、およびフレームで補強された熱可塑性スキンで構成されています。デモンストレーションされる製造プロセスは、次の3つの主要なステップで構成されます。
- デモンストレーターの大きな皮膚用のプリプレグテープは、NLRの既存のレーザーAFPマシンによって平らな傾斜したテーブルに置かれます。
- レイアップは、吸盤を使用してロボットでメスの圧密型に運ばれ、加熱せずにドレープされます。
- 真空バッグに入れた後、皮膚はオートクレーブに固められます。
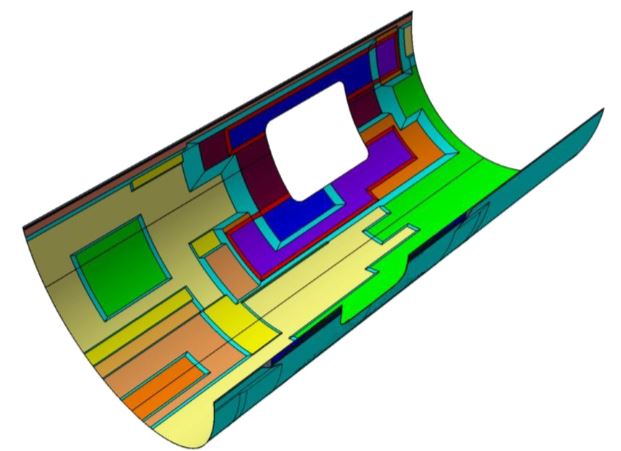
メスの圧密金型を使用すると、オスのツールよりもはるかに単純な(平らな)表面が得られ、皮膚の外面品質に対する空気力学的制約が直接制御されます。
MFFDプロジェクトでは、オートクレーブ外も必要です。 調査対象のプロセス—大型の多機能胴体デモンストレーターと並行して開始—後続の小型のデモンストレーターで。特に、その場での熱可塑性複合材料 オートクレーブのステップを完全に排除し、製造を単一ステップの手順に減らすことができるため、レイアップ中に統合が達成される製造が検討されます。
オートクレーブ圧密、またはEMOTION(https://cordis.europa.eu/project/id/864474)の内外での熱可塑性胴体用の強化金型は、MFFD下部シェル工具を製造するためのClean Sky2プロジェクトです。 「それは単純に聞こえます」と、プロジェクトのコーディネーターであるTUミュンヘンのPatrick Consulは言います。「しかし、400°Cに加熱する必要があるため、実際には非常に困難です。これは、Invar36が有意なCTE [熱膨張係数]を持たない温度範囲をはるかに上回っています。」インバーは、高温硬化サイクル中の膨張が小さいため、複合成形ツールに一般的に使用されます。ただし、InvarのCTEは温度とともに増加します。 「課題は、硬化中の8メートル×4メートルのカビと胴体の外板の加熱と冷却中の熱膨張を制御することです」と領事は述べています。
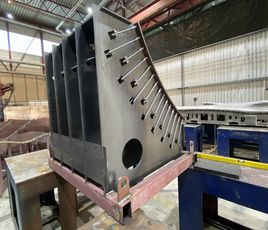
積層造形の進歩
「私たちはLCC内で積層造形に取り組んでいる8〜9人です」と領事は言います。彼はこの作業の歴史を、LCCが2012年にAFPT(ドイツのDörth)からレーザー支援熱可塑性複合テープ配置機を購入したことから始まります。その後、自動繊維配置(AFP)を可能にするCoriolis Composites(フランスのQuéven)機械を追加しました。 )熱可塑性プレプレグの。最初のフィラメントベースのデスクトッププリンターは2017年に購入されました。「2017年には、Clean Sky 2などの提案書作成など、新しいアプリケーションや研究プロジェクトの開発を支援するためにも参加しました。」彼は、Clean Sky 2プロジェクトは、公開されたCalls for Proposals(CFP)に応じてトピックマネージャーに提出された提案に基づいて授与されると説明しています。 LCCは、CFP08COMBO3DプロジェクトとCFP09EMOTIONプロジェクトの提案に成功しました。両方について以下で説明します。
「他にもいくつかのプロジェクトがあり、連続的な繊維強化を使用した3D印刷を検討しているプロジェクトもあります」と領事は言います。 「他の企業は、レーザー統合プリントヘッドを使用して、複合基板を予熱し、すでに統合されたCFRP部品に印刷したり、印刷層間の層間せん断強度(ILSS)を高めたりしています。別のプロジェクトでは、たとえば、特殊な複合部品の数が少ない工具アプリケーションを検討しています。」
「これらのプロジェクトは、印刷プロセス中および印刷プロセス後の添加剤製造部品の動作を予測するために、数値シミュレーションによって継続的にサポートされています」と彼は続けます。 「LCCは、3DプリントされたCFRPを使用して外骨格を製造することを目的としたロンドンのインペリアルカレッジとのプロジェクトにも関わっています。別のプロジェクトでは、剛性、強度、またはエネルギー吸収に関して3D印刷部品の特性を最適化するために、格子構造を研究しています。」
プリンターの進歩

「私たちは、Apium(Karlsruhe、Germany)のFDM(溶融堆積モデリング)に基づくシンプルな3Dプリンターを使用して、高い剛性を必要とする特殊なテストフィクスチャを印刷することから始めました」と領事は説明します。 「このプリンターは、長さ3メートル×幅1メートルで、印刷時間を短縮するために高素材出力を備えていました。連続繊維は使用できませんでしたが、PEEK、PEKK、およびチョップドカーボンファイバー強化PEEKを使用した印刷用に設計されています。加熱されたベッドだけでなく、プリントヘッドの周りに加熱されたプレートも使用され、プリントに均一な温度分布を生成し、熱応力を低減し、結晶化を確実にしました。」
「また、しばらくの間Markforged(ケンブリッジ、マサチューセッツ、米国)プリンターを持っていて、その後Anisoprint [Esch-sur-Alzette、ルクセンブルグ]を手に入れました」と領事は言います。 Markforgedプリンターは連続ファイバーでFDMを有効にしましたが、LCCチームはそれを維持しないことを選択しました。 「私たちが抱えていた問題は、システムが非常に閉鎖されていたことでした」と領事は説明します。 「Markforgedのスライサーソフトウェアは、私たちができることを大幅に制限していたため、研究に使用するのは難しすぎました。連続繊維材料の層を印刷し、次に短い繊維強化熱可塑性フィラメントの層をその上に印刷することしかできませんでした。コードを生成するスライサーは、私たちからのGコードを受け入れません。そのため、各レイヤーに連続繊維を使用して、希望どおりに印刷するようにマシンに指示する方法はありませんでした。」
これについて尋ねられたとき、Markforgedは、そのシステムが研究に使用されることを意図したものではなく、部品の製造に広く使用できるようにシンプルで堅牢に設計されており、ルールベースのファイバーパスを利用し、スライサーを構成するための労力と時間を節約できると説明しています。その Eigerソフトウェアを使用すると、ユーザーはレイヤーを個別に構成できます。Markforgedはフィードバックを歓迎し、顧客のユーザーエクスペリエンスの向上を優先します。
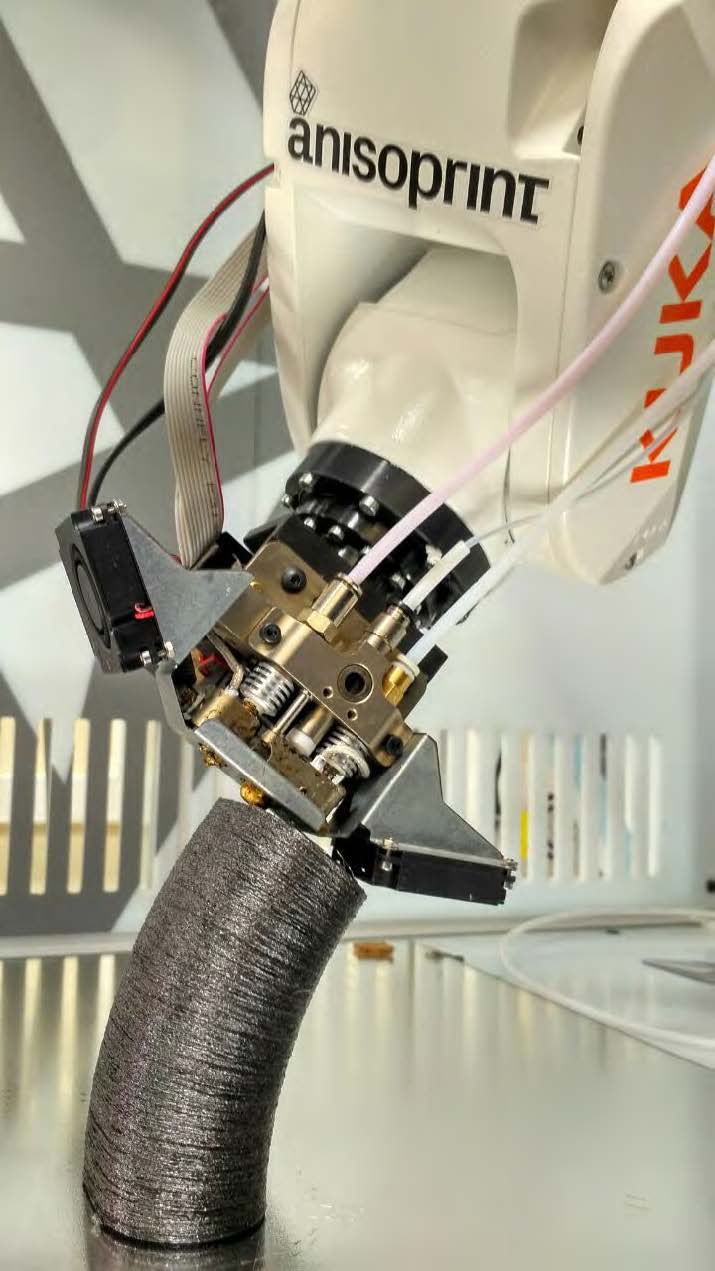
「完全にオープンなGコードスライサーを使用するAnisoprintにより、プロセスへのアクセスが向上しました」と領事は言います。 「2Dレイヤーだけでなく、面外の3Dカーブでも、連続炭素繊維を印刷することができます。小型のKukaロボット用のAnisoprintプリントヘッドがあり、1メートル×1メートルの部品を製造できます。これは、ほとんどのデスクトップよりも大きいですが、ロボットシステムとしては小さいです。」
しかし、Anisoprintのデュアルマトリックスについてはどうでしょうか 熱硬化性-熱可塑性(TS-TP)材料? Anisoprintに関する2019年のブログで説明されているように、「…最初に、連続的な繊維強化に熱硬化性樹脂を含浸させます。 ポリマーを使用し、印刷中にこれを溶融した熱可塑性フィラメントに押し出します。」領事は、TSフィラメントとTPの間の接着はかなり良いと答えています。 「最初の試行では、Markforgedプリンターと比較して、より多くのファイバーボリュームコンテンツを取得できましたが、これはGコードを変更できたためです。 AnisoprintプリントヘッドはTSフィラメントをTPに押し込み、それを配置します。そのプリンターを外骨格部品に使用することを計画しています。これは、より高強度の繊維を統合する簡単な方法です。」
押し出しペレットプリンター
次の進歩は、最初に短繊維強化TP、次に連続繊維TPを備えた大規模プリンターへの移行でした。 「私たちは最初にロボットに取り付けられた押出機を開発し、その後すぐにCEADマシンへの関心が高まりました。来年は、これらのシステムの両方に継続的なファイバーを統合することを望んでいます。」
しかし、ロボットアームに押出機がすでに搭載されているのに、なぜCEADマシンが必要だったのでしょうか。 「最初の押出機はDyzePulsarペレット押出機のベータ版で、PAEKで最大約2kg / hr、約1kg / hrを出力しますが、20%を超える炭素繊維の負荷に苦労しています」と領事は言います。 「ただし、印刷中にロボットが頻繁に加速および減速するため、平均出力は低くなります。 COMBO3Dの場合、最初の小規模な金型の半分はすでに少なくとも36キログラムを必要としていたため、半分を印刷するのに約48時間かかりました。また、材料の供給ラインの詰まりや部品の反りなどのエラーがいつでも発生する可能性があるため、常に誰かと一緒にいる必要がありました。」
COMBO3Dの最終デモンストレーターは、最初の小規模部品の約10倍の大きさであるため、この最初の押出機システムを使用して印刷することは不可能でした、と領事は言います。 「また、ビクトレックスが提供してくれた材料のいくつかは粘度が高く、この最初の押出機はそれらのポリマーを押し出すのに十分なトルクを提供できませんでした。 CEADプリンターでは、最大出力は約12.5 kg / hrであり、数時間の試行の後、約5〜6 kg / hrの安定した平均出力が得られました。これにより、小規模な金型の半分を8時間以内に印刷でき、繊維含有量を増やして反りを減らし、プロセス全体の制御を容易にすることができました。」
「したがって、パルサーはすでにペレットの使用を許可し、高い材料出力を達成し、ロボットの自由度を利用することを可能にしました」と彼は続けます。 。パルサーは、フィラメントベースのプリンターとCEADの間のギャップを、出力だけでなく、ノズルサイズと、結果として得られるプリントの詳細においても埋めます。」
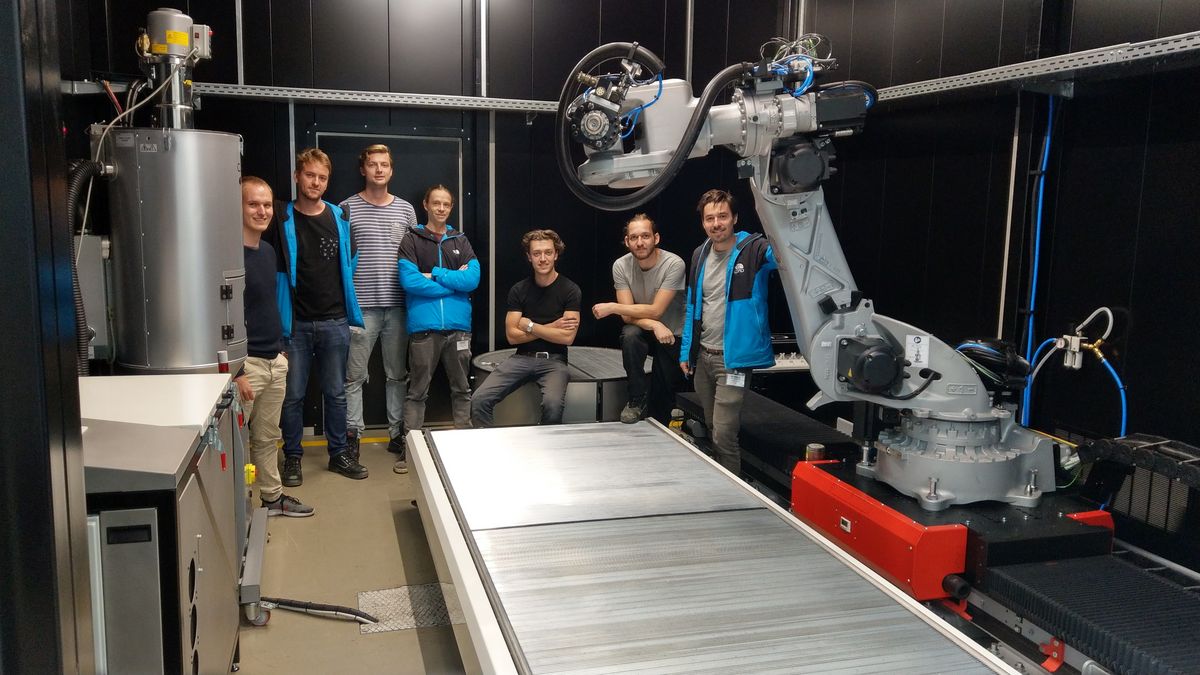
CEAD AM Flexbot技術データ:
- AM Flexbotの技術データ:
- 最大12.5kg / hrのペレットベースの押し出し印刷(非強化および短繊維強化)
- 450°Cまでの材料の処理
- ビルドボリューム3000x 1200 x1700ミリメートル
- 回転台またはフラットテーブル(加熱可能)上にプレートを構築します
- フライス盤による再加工。
COMBO3D
このCleanSky 2プロジェクトの目的は、金型を3D印刷して、大型旅客機用のデモンストレーター複合フラッペロン(1.5 x 3メートル)を作成することです。これは、ワークパッケージA-3.1:高速および低速用の学際的な翼の一部です。アディティブマニュファクチャリングを使用する目的は、工具製造のリードタイムを短縮することです。プロジェクトは2019年1月に開始され、2021年3月に終了します。パートナーには、Alpex Technologies(Mils bei Hall、オーストリア)、軽量金属スペシャリストLeichtmetallkompetenzzentrum Ranshofen(Ranshofen、オーストリア)、および高性能熱可塑性プラスチックのサプライヤーであるVictrex(Thornton Cleveleys、英国)が含まれます。ポリアリールエーテルケトン(PAEK)。
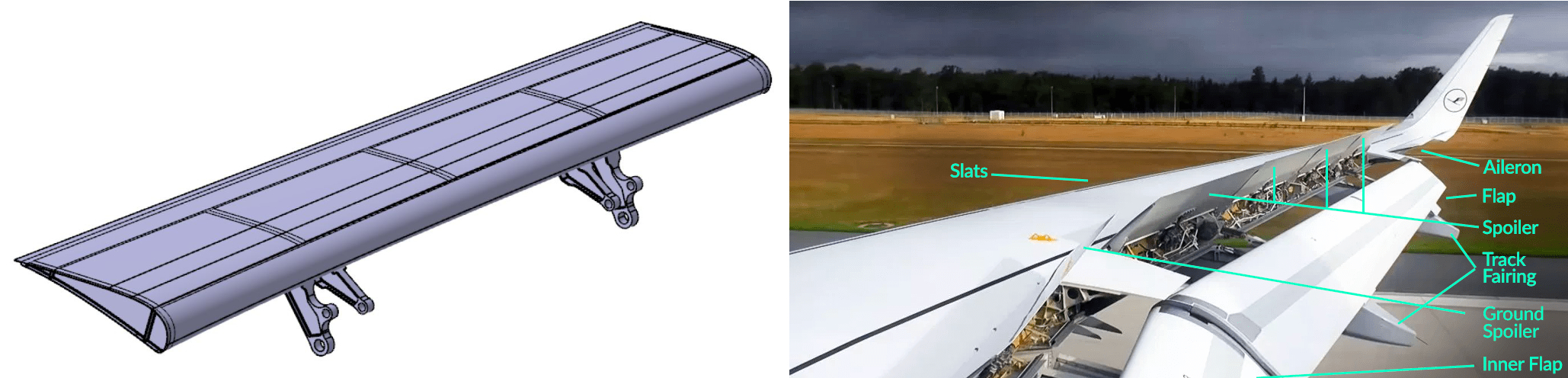
プロジェクトのもう1つの重要な部分は、この炭素繊維/エポキシフラッペロンがオートクレーブ硬化プリプレグの代わりに樹脂トランスファー成形(RTM)で製造できることを実証することです。 RTM部品はオートクレーブ部品と同じ180°Cで硬化します。熱安定性を確保するために、ツールは、305°Cの溶融温度を持つ短い炭素繊維強化PAEKで印刷されます。
硬化サイクルを短縮するために、3Dプリントされた金型はアクティブな温度制御を統合します。 「オートクレーブに比べて、金型をより速く加熱および冷却できなければなりません」と領事は述べています。 「金型表面から3ミリメートル下にある電気加熱要素のメッシュを使用し、金型表面から6ミリメートル下にある加熱されたオイルまたは空気用の印刷チャネルも統合します。このようにして、金型表面を非常に迅速に加熱できますが、チャネルを使用してツールボリューム全体を加熱することもできます。オートクレーブよりも50%速い加熱および冷却速度を目指しており、少なくとも30%速い速度を達成できると確信しています。」
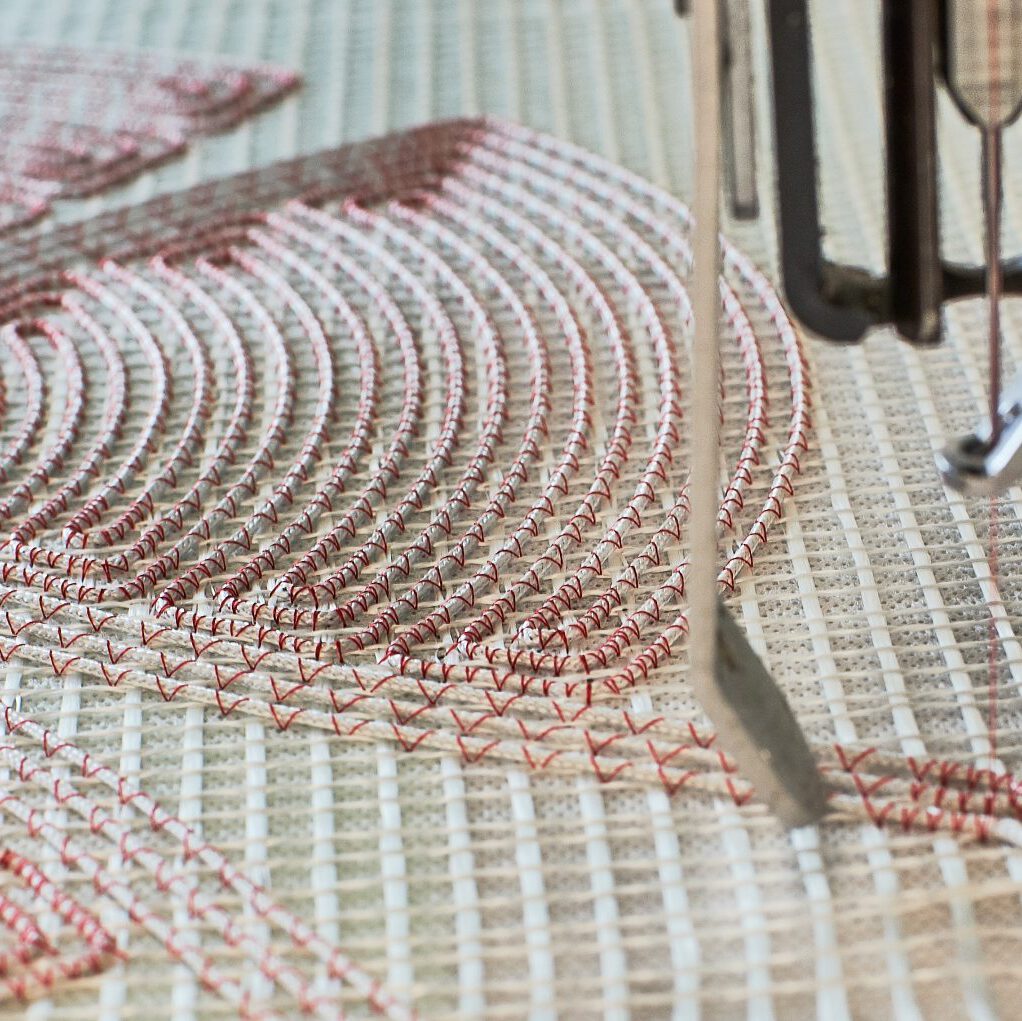
3Dプリントに統合される発熱体は何ですか? 「ヘリコプターのローターブレード用のCFRPモールドでさまざまなヒーターゾーンを実現するために、ヒーター要素としてガラス繊維テキスタイル上のカーボンロービングのテーラードファイバープレイスメント(TFP)を使用しました」と領事は説明します。 「これは、QPoint Composite(ドレスデン、ドイツ)との共同作業を完了したClean Sky1プロジェクト用でした。 COMBO3Dモールドでも同様のコンセプトで作業します。」
印刷されたツールの開発全体は、シミュレーションによってサポートされています。ツールの設計は、熱シミュレーションで加熱および冷却システムを実装することによって最適化されます。製造プロセスもシミュレートされ、印刷中の温度分布に関する知識を生成し、それを経路計画と相関させることにより、印刷プロセスをサポートします。
CEADマシンのインストールとプロジェクトの進捗状況
「CEADシステムは非常に迅速に納品されました。注文から設置までわずか6か月でした」と領事は言います。 「この時点で、材料テストを完了し、プレートツーリングを設計し、小さな部品の印刷を開始しました。 CEAD AM Flexbotでプロセスを正常に実行するには長い時間がかかるのではないかと心配していましたが、最初の試行ではうまく機能しました。」
プレートツーリング? 「これは小さな型で、すでに冷却チャネルとヒーター要素を統合して、クーポンテスト用のCFRPプレートを製造しています」と彼は説明します。 「このテストは、3DプリントされたCFRP RTM金型の品質が、サーブがオートクレーブプロセスで製造している現在のCFRPに匹敵することを確認するためのものでした。」
残念ながら、プロジェクトはCOVID-19によって中断されました。「しかし、今ではすべてが順調に進んでおり、追いついてきています」と領事は言います。そして、3Dプリントされた金型にPAEKを使用するのはどうですか? 「現在の唯一の問題は、PAEKのTg [ガラス転移温度]が130〜140°Cであるということです。これは、デモンストレーション部分の180°Cの硬化よりも低いです」と領事は述べています。 「したがって、クリープが発生したり、表面が損傷したりする前に、硬化温度で何サイクル完了することができるかを確認する必要があります。」
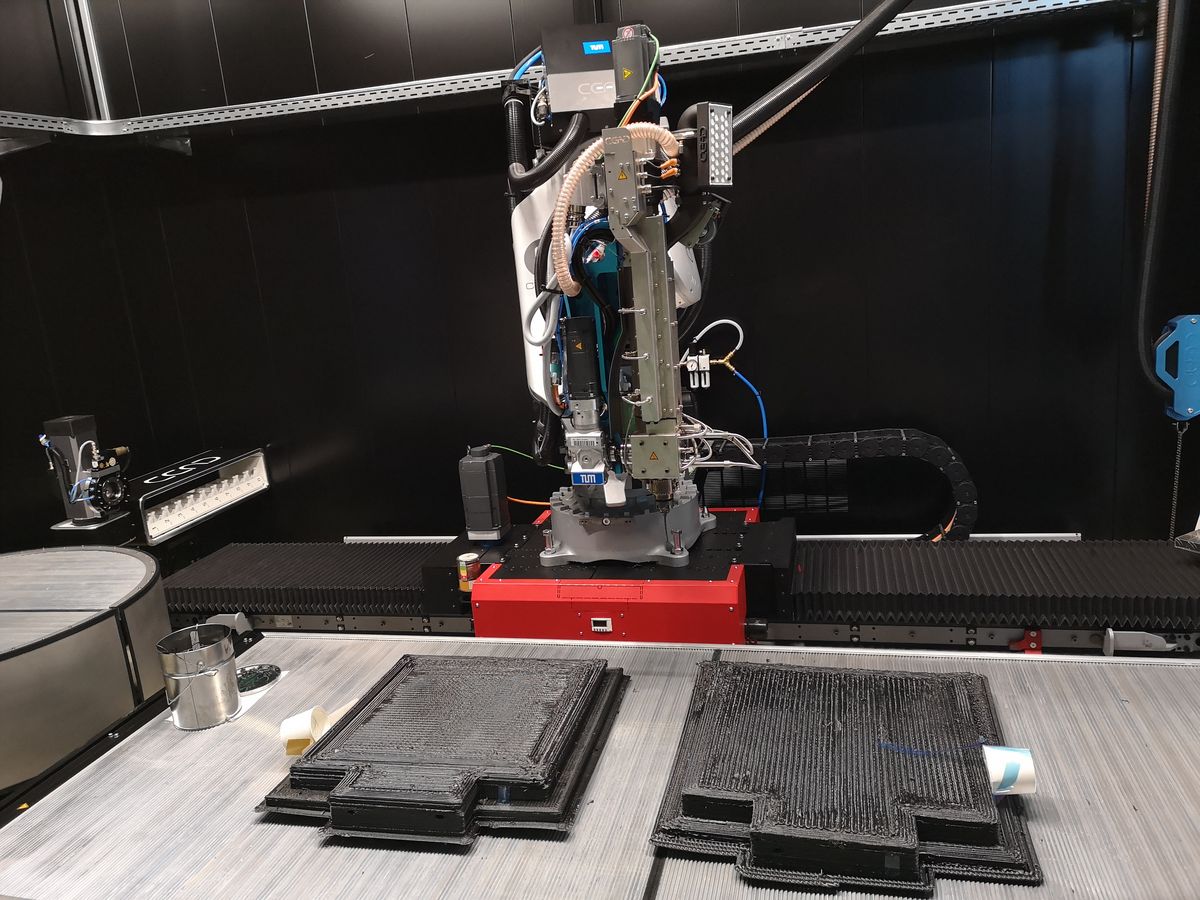
他のプロジェクトのCEADマシン?
「私たちは、CEADマシンとポリエーテルスルホン(PESU)を使用して、来年GKN Aerospace Deutschland(ミュンヘン)で始まる航空宇宙ツールのプロジェクトに応募しています」と領事は言います。 [注:ドイツのGKNは、A330とA350の複合翼フラップ、およびボンバルディアグローバルビジネスジェットファミリーのエルロンを製造しています。]「CEADは、連続炭素繊維の機械開発を担当するこの一部になります。また、CEADマシンを内部で使用して、RTMのプロトタイプ型を作成することも計画しています。これがなければ、下請けになります。作業を加速する上でメリットがあります。」
領事は、PESUのTgはPAEKよりも高いと述べています。 「また、半結晶性ではなくアモルファスであるため、耐クリープ性が問題になる可能性がありますが、印刷が容易になるはずです。私たちがやろうとしているのは、PEI(ポリエーテルイミド)を避けることです。過去に、エポキシ樹脂へのPEI結合の問題を検討しました。 RTM6 [RTMのエポキシ]はPEIを溶解し、2つの間の良好な接着を促進します。これは、パーツにくっつくのではなく、パーツを解放する必要がある3Dプリントされた金型にはまったく必要ありません。」
将来の産業用(および飛行用)3Dプリントコンポジット
LCCが積層造形で追求している他のプロジェクトのいくつかについて議論する際に、私は領事にCFRPを外骨格に戻した理由を尋ねます。 「外骨格は各着用者に適応させる必要があるため、パーツは特殊化されており、ボリュームは大きくありません」と彼は答えます。 「私たちのプロジェクトは、患者固有の下肢外骨格コンポーネントの製造を可能にし、24時間以内に患者固有の外骨格の製造を可能にすることを目的としています。これらの外骨格は、脳卒中患者の生物物理学的プロファイルと独自の医学的リハビリテーションのニーズに基づいて、脳卒中患者のリハビリテーションをサポートします。」 (CWの記事「C-FREX外骨格はCFRPに依存します…」を参照してください)
「人々は3D印刷であらゆる部分を印刷できるという概念を持っていますが、最初に3D印刷とコンポジットの経験が必要です。たとえば、層間の接着と異方性には、理解しなければならない問題がよくあります。 3D印刷された複合部品は、現在プラスチックと金属で作られているものと同じデザインにはなりません。」
彼は、高性能航空機部品の製造に3D印刷された複合材料を使用する場合、克服すべき問題がまだあると述べています。たとえば、これらの部品を積層造形用にどのように設計しますか。アディティブマニュファクチャリングが付加価値をもたらす部品をどのように特定しますか? 「航空宇宙ツールは、私たちのチームが現在検討しているアプリケーションの主な分野です」と領事は言います。 「金型の3Dプリントはぴったりです。これらの金型は、部品と同じ硬化条件のすべてに耐える必要がありますが、金型とフライング部品に関連するリスクは少なくなります。良い例は、翼のリブ補強材です。この場合、さまざまなパーツが多数ありますが、パーツあたりのサイクル数は多くありません。したがって、これはテクノロジーの経験を生み出すための良い方法です。飛ぶ構造部品を試すのは時期尚早です。私たちはこの長期的な目標を掲げますが、印刷ツールを使用すると、3D印刷プロセスを十分に安定させ、高性能な特性を実現し、シミュレーションでこれらの部品やプロセスを正確に予測する機能を開発できます。」
樹脂
- 3Dプリントとソフトウェアがデジタルトランスフォーメーションにとって重要である理由
- メンテナンスのトラブルシューティング:試行錯誤だけではありません
- 石油およびガス会社向けの3D印刷ソリューション
- DSMとNedcamが大型3Dプリント用の新しいアプリケーションを開発
- 低排出ガスキャリアに基づく自動車用およびその他用のアセタールカラーマスターバッチ
- IMLおよびスタックモールドの自動化
- 3DプリントPAEKパーツのVictrexとBondのパートナー
- 3Dプリント金型のヒント
- チタンをCNC加工するためのヒント:航空宇宙など
- 中小企業が3DプリントにアクセスしやすくするためのFormlabs
- コンポーネントおよびアセンブリ用 SIGRABOND® Chemical CFRP