コンポジットを多用する傑作:2020コルベット、パート1
パート2については、「コンポジットを多用する傑作:2020コルベット、パート2」をお読みください。
待望の第8世代シボレーコルベット 2019年7月18日の公式発表以来称賛を集めているゼネラルモーターズ社(GM、デトロイト、ミシガン州、米国)の(C8)は、今年初めに商業生産を開始しました。新しいコルベットスティングレイ コンバーチブルとクーペは、その美しさと、GMが60,000米ドル未満から始まる高性能のストリートリーガルミッドエンジンロケット船を製造したという事実だけでなく、同等のパフォーマンスのミッドエンジンの3分の1の価格で注目に値します。車—しかし、それらはまた、ここと来月のパート2で説明する、新しくて真に革新的な複合コンテンツの印象的な配列を備えています。
新しいエンジン構成はすべてを変える
GMエンジニアリングは、ミッドエンジン車に取り組んでいることを認識して予備設計を開始しました。これは最初の生産コルベット その構成をスポーツするために8世代で。 「パフォーマンスのためにフロントエンジンアーキテクチャを可能な限り進化させたので、ミッドエンジンデザインに移行することは、すでに優れた車を改良し、セグメントリーダーになるための次の論理的なステップでした」とGMのエグゼクティブチーフエンジニアであるTadgeJuechterは説明します。 -グローバルコルベット 。 Z51パフォーマンスパッケージを搭載した2020 コルベットスティングレイ 2.9秒で0-60mph(0-97 kmh)を加速し、194 mph(312 kmh)の最高速度に達することができます。エンジンを車両の後方に押し出すと、車両の重心、乗員の相対位置、トランスミッションの位置、アンダーボディパネルとトランクストレージの設計など、多くの影響がありました。ミッドエンジンの設計はまた、車の新しい領域により高い作動温度と騒音をもたらしました。
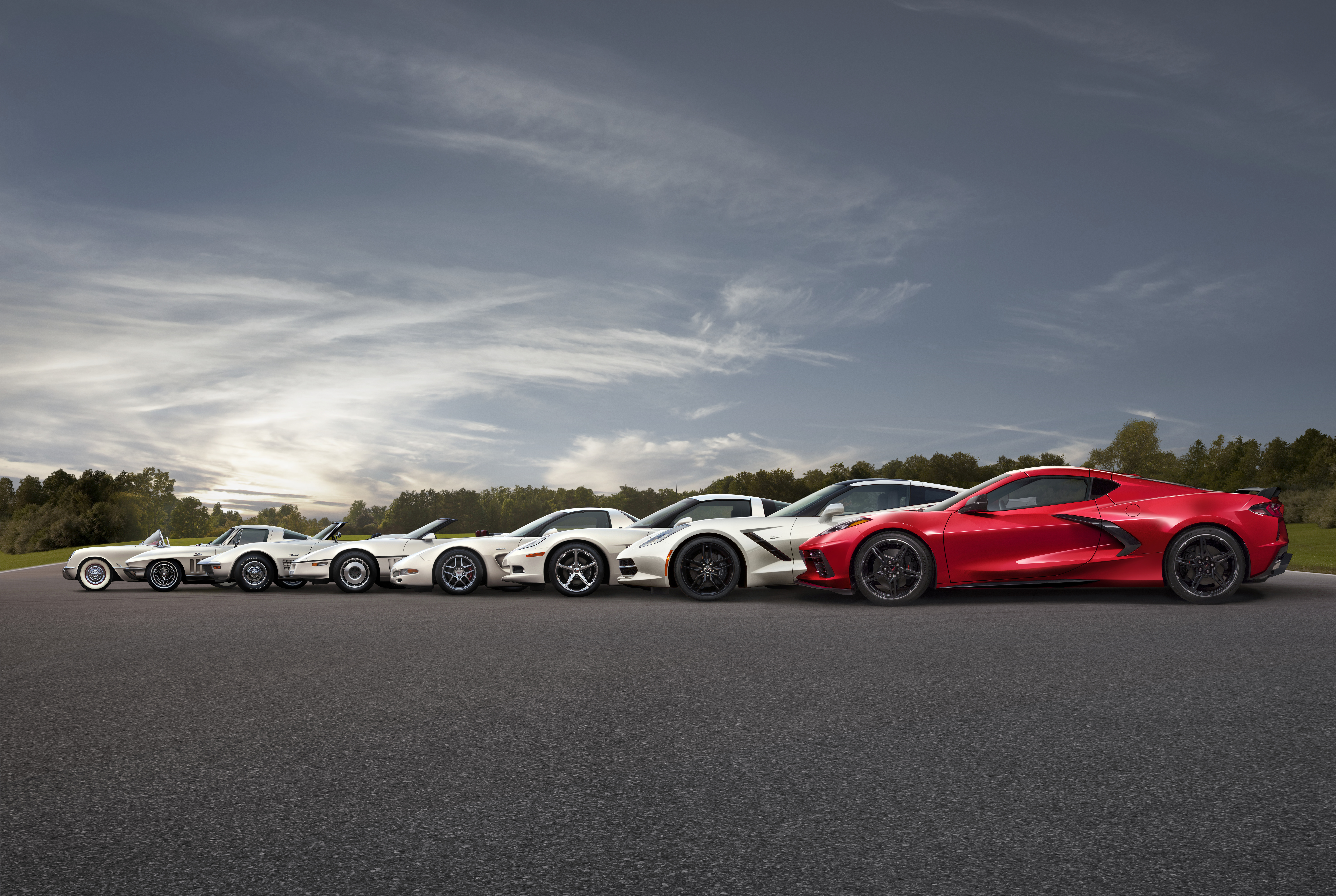
「ミッドエンジンのため、私たちは別のことをしなければなりませんでした」と、エド・モス、コルベットは説明します。 体構造工学グループマネージャー。 「最初から、体の構造をどのようにレイアウトするかについて多くの議論がありました。ある時点で、各システムを設計および構築するための最良の方法について話し合ったとき、すべてがテーブルにありました。たとえば、ホイールハウスの金属と複合について議論しました。 C7の複合ホイールハウスを維持した場合、ミッドエンジン車の前輪に直接隣接するヒンジピラー[Aピラー]に接着する必要があり、パッケージスペースはほとんど残りません。そこに金属を持って行きました。金属と複合のボディパネルについても簡単に説明しました。ただし、メタリックでC8のスタイリングラインを作成することは経済的に不可能でした。」
「私たちが直面した本当の課題は、空気誘導をどのように処理するかでした」と、クリス・バセラ、コルベットは回想します。 ボディストラクチャーのリードエンジニアは、自然吸気の495馬力の6.2リッターV8エンジンに冷却空気を注ぎ込み、470フィートポンド(637ニュートンメートル)のトルクを発生させる別の方法の必要性を説明します。 「私たちは、空気が本当に曲がりくねった道を進むように強制するあらゆる種類の設計を試み、私たちが望まない渦と流れを作り出しました。車は制限なく自由に呼吸する必要があるため、空気の流れに最適な経路を開発するには、パワートレインチームとの多くの反復作業が必要でした。また、エアボックスへのアクセスが必要であり、後部トランクスペースを回避する必要がありました。もう1つの問題は、乗員がエンジンの後ろに座っているのではなく、エンジンの真正面にいるため、客室内の熱とエンジンの騒音でした。また、C7以降、ヨーロッパやその他の地域で法律が変更されたため、客室の空気の質を特に意識していました。そのため、VOC [揮発性有機化合物]の削減に真剣に取り組みました。」
「組み立てる方法を考えても 車は挑戦でした」とモスは付け加えます。 「フロントエンジンの設計により、長いフードと大きなエンジンコンパートメントがあり、フロントバンパービームがすでに溶接されている場合でも、コンパートメント内から車を組み立てるのに十分なスペースがオペレーターに提供されます。ミッドエンジンのコルベット 、フロントクリップが非常に短いため、車両が組み立てられている間、車のフロントを開いたままにしてから、フロントバンパーをボルトで固定します。」
「サプライヤーがボウリンググリーン[GMのケンタッキーを拠点とするコルベット]で部品とチームを生産できるようにしながら、適切な形状を得るのは非常にバランスの取れた行動でした。 組立工場]はそれらを組み立てることができます」とBaselaは続けます。 「結局、C7のボディからC8へのキャリーオーバーコンポジットは1つしかありませんでした。」これは、2016年のコルベット用に開発されたタフなクラスA、1.2比重(SG)シート成形コンパウンド(SMC)でした。 新しい車両のさまざまな外装クロージャーに使用されています。
車両アーキテクチャ
4世代(C5-C8)の場合、コルベット フレームという3層のマルチマテリアルボディ構造が特徴です。 、通常はアルミニウムまたは鋼の混合物—今回は炭素繊維強化複合材(CFRP)部品を使用。 体の構造 、設計と製造の柔軟性を活用するために主に結合された複合材料。プラスボルトオン見切り (ボディパネル)、 Covette’s 以降合成されています 1953年6月デビュー。この階層化されたハイブリッド構造は、特にこのパフォーマンスクラスの車に対して、大量生産で手頃な軽量化を提供するだけでなく、少ない工具投資で複数の車両バリエーションを生産することもできます。実際、現在のC8の場合、GMは、ベースモデルのクーペとコンバーチブルの両方で、わずか20個のツールを使用してすべてのクラスA複合ボディパネル(接着されたインナーとアウター)を製造することができました。
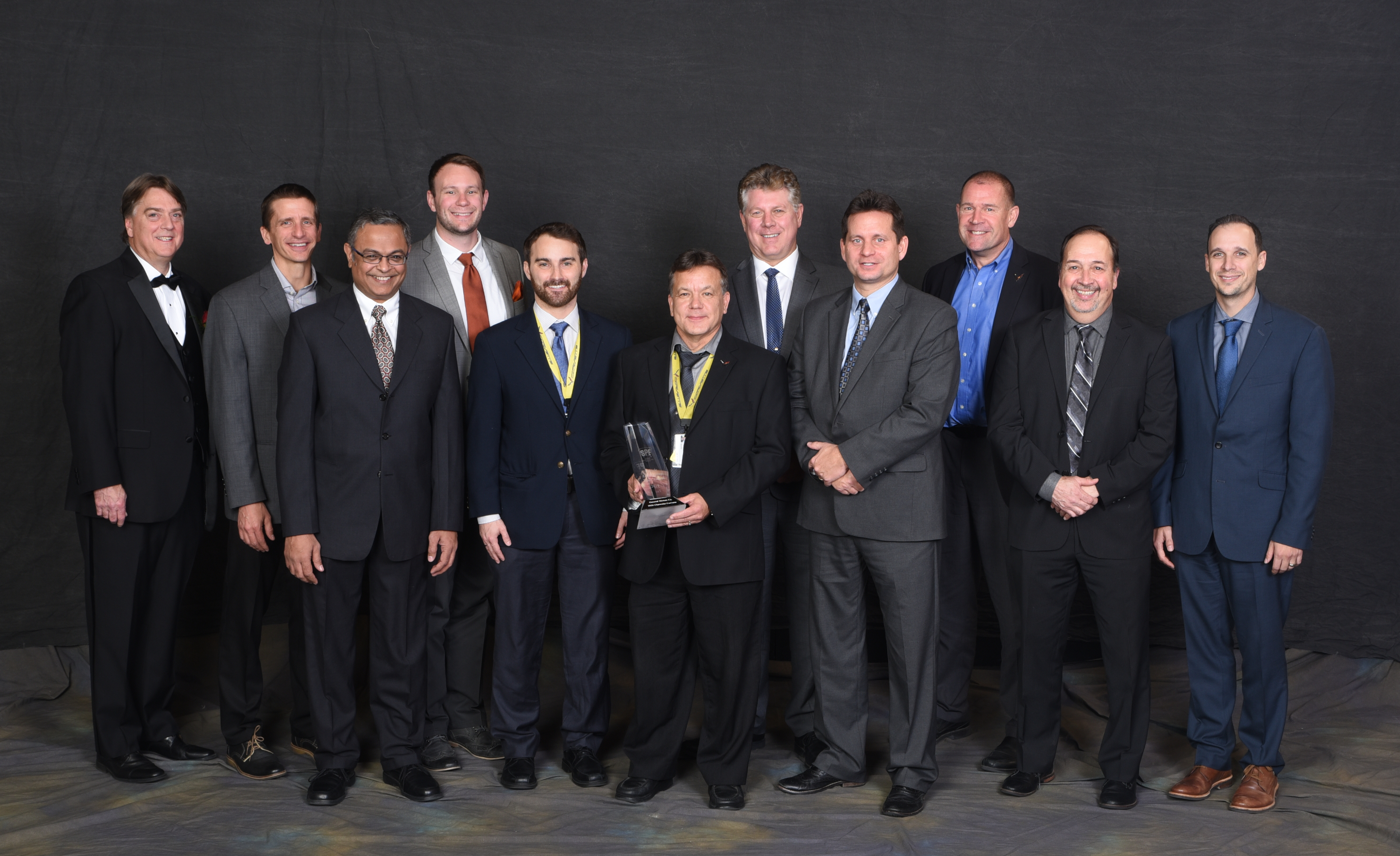
さらに、コルベット それらが実際にコンバーチブルであるか、固定または取り外し可能なルーフパネルを備えたクーペであるかに関係なく、常にオープンルーフアーキテクチャで設計されてきました。オープンルーフの車両は一般に固定ルーフの車両よりも剛性が低いため、各コルベットの重要な焦点 エンジニアリングは常に、サスペンションとステアリングを改善するために可能な限り堅い基盤を作成することです。歴史的に、トンネル (フロントエンジン車のハウジングトランスミッションとドライブシャフト)はコルベットを支配してきました ボディ構造と高いねじり剛性を実現するための重要なイネーブラーとなっています。新しいコルベットの場合 、GMはさらに高い剛性を実現しました。ルーフを取り外した状態で、C8ボディはベンチマークの高性能ミッドエンジン競合他社より53.78%剛性が高く、2番目の高性能ミッドエンジン競合他社より29.27%剛性が高く、C7より13.79%剛性が高くなっています。 2つの複合部品が車両の剛性に重要な貢献をしました。1つはフレーム構造に直接取り付けられ(リアバンパービーム)、もう1つはアンダーボディに取り付けられています(下部トンネルの閉鎖)。
フレーム構造
C8のフレームは主にアルミニウム合金で、GMの1キログラムあたりの厳しい目標を達成するために1つのCFRPパーツが開発されています。対照的に、C7フレームはオールアルミニウムで、C6はほとんどがスチールでした。
電気泳動ラストコートプロセス(GMではELPOと呼ばれます)を介してボディインホワイト(BIW)と一緒に移動する、フレームに直接取り付けられた唯一の複合部品は、独自のCFRPリアバンパービームです。この部分はフレームを補強するのに役立ち、リアインパクトのパフォーマンスに貢献します。その湾曲した形状は、Thomas GmbH + Co. Technik + Innovation KG(TTI、ブレーマーフェルデ、ドイツ)によって開発されたラジアスプルトルージョンと呼ばれる新しいプロセスのおかげで可能になります。エンジンベイの熱に。自動車業界初の湾曲した引抜成形部品(CW 2020年5月号のこの部品の全機能を参照)として、中空の2チャンバービームは、Shape Corp.(Grand Haven、Mich。、US)によって開発された機器で製造されました。 TTIによって構築されました。ビームの重量はわずか1.3キログラムで、25キロニュートンの引き抜き力が可能な接着/ボルトで固定された牽引フックアイを備えています。
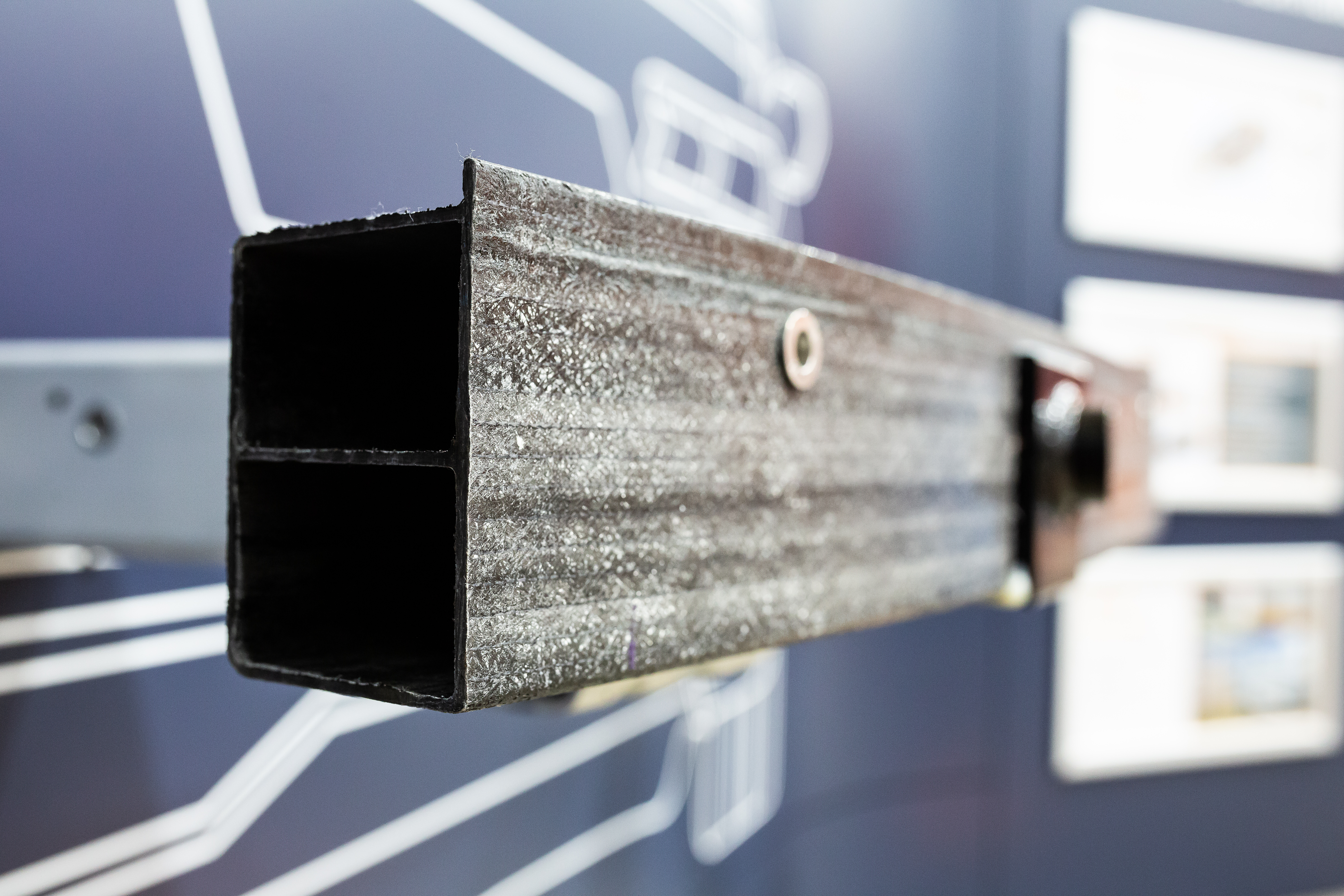
体の構造:パートA
事実上すべてのC8のボディ構造コンポーネントは複合であり、フレームがELPOを受けた後、フレームに接着および/またはボルトで固定されます。このレベルの注目すべき複合部品には、構造的なアンダーボディクロージャーとフロア(この号で取り上げます)、フロントとリアのトランク、インダクションダクト、リアサラウンドとバルクヘッド(ボディパネルとトリムとともにカバーします)が含まれます。 、来月。
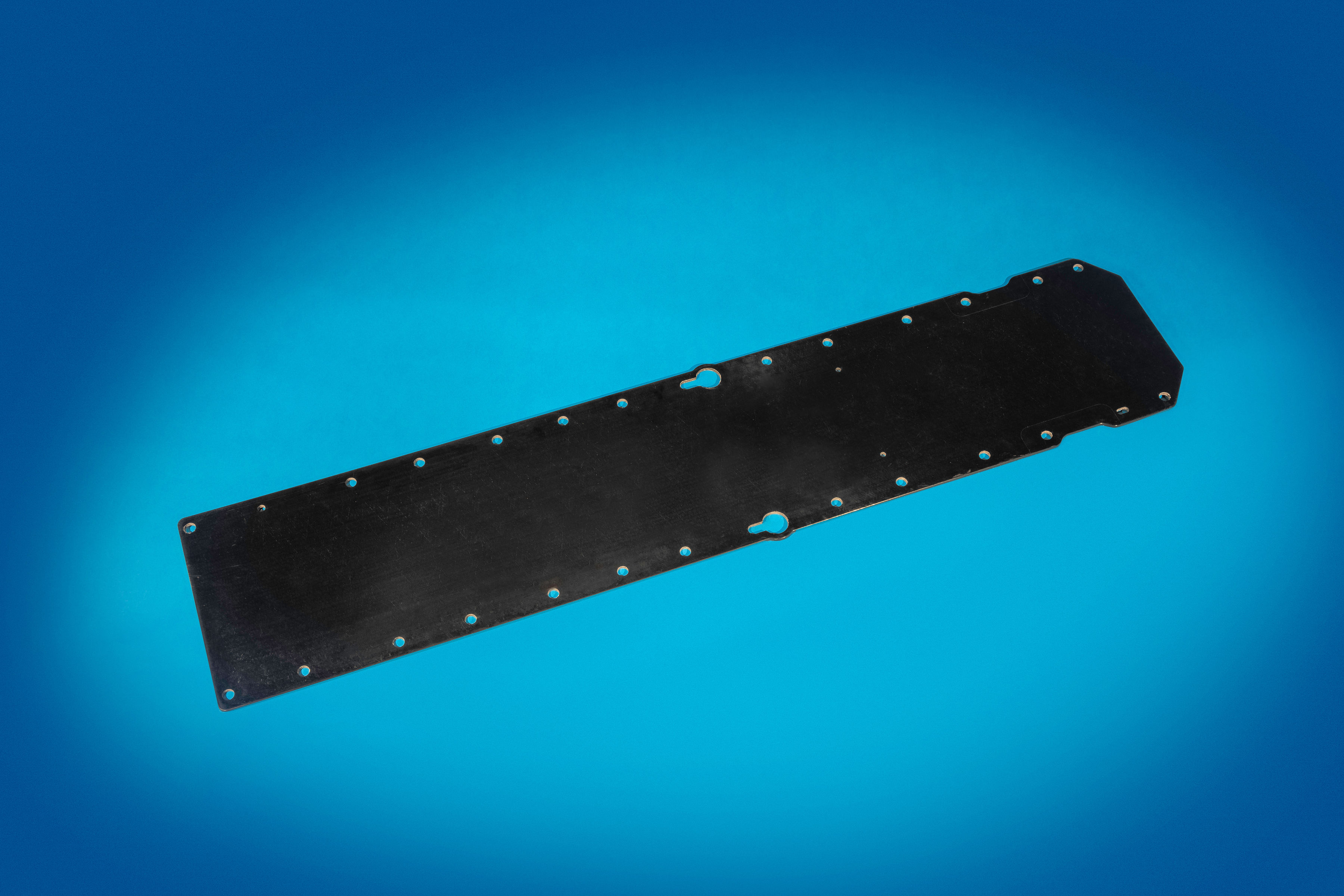
アクセスドアとして機能するC8の取り外し可能な下部トンネル構造の見切りは、車両のねじり剛性の10%以上に寄与し、衝突時の主要な荷重経路として機能します。このハイブリッド複合パネルは、3層のガラス繊維プリフォームで構成されています。これらは、38%の繊維体積分率(FVF)の連続/織物および細断/ランダム繊維で構成され、表面仕上げを改善するために各スタックの上面および下面層にベールが追加されています。ガラスプリフォームは、東レ(東京、日本)T700 12K標準弾性炭素繊維を21%FVFのNCF二軸布とビニルエステル(VE)マトリックスの形で使用して作成された2層のプリフォームでインターリーブされています。見切りは、Molded Fiber Glass Co.(MFG、Ashtabula、Ohio、U.S。)が、液体圧縮成形(LCM)の一種である独自のPRiME(製造の卓越性を保証する事前配置補強)プロセスを使用して製造しています。
エンジンクレードルの一部である後輪近くの単一のアルミニウム閉店を除いて、残りのアンダーボディパネルは圧縮成形されたSMCまたは射出成形された熱可塑性プラスチックのいずれかで構成されています。他の利点の中でも、これらのパネルは、車体下部の乱流と抗力を低減し、燃料効率を改善し、車両のエンジンとドライブラインに湿気、ほこり、石を寄せ付けません。さらに、それらは複数の外部および内部インターフェースの寸法基盤を提供します。
低密度ですが構造的 SMCパネルは、MFGによって開発された新しい配合(この場合、40%FVFチョップドグラスファイバー/不飽和ポリエステル(UP)樹脂)を備えています。各パネルの密度が1.0未満(平均SG =0.97)であり、水に浮く可能性があるため、この材料は「フロート」SMCと呼ばれます。 MFGは、車のすべての構造SMCおよびLCM部品を製造しました。
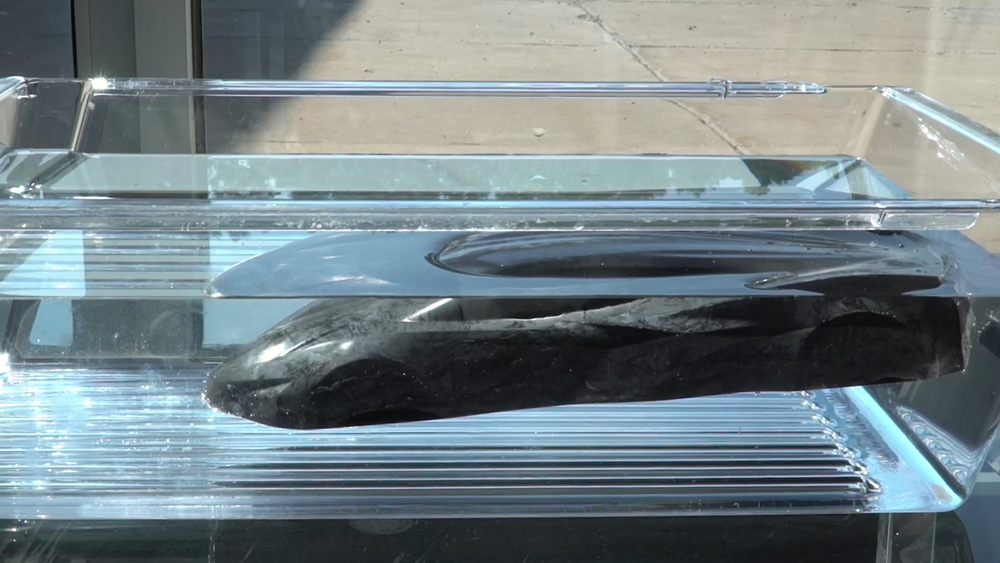
車両はまた、ねじれ曲げとサイドポール衝撃保護(それが結合されているロッカーパネルとトンネルに係合する)用に最適化されたハイブリッドフロアを備えています。フロアパネルは、PRiMEプロセスで製造された道路に面した1.5-SGコンポジット(60 wt-%の連続ガラス繊維/ VE)のシートに接着されたキャビンに面したプレス加工されたアルミニウムを備えています。 Ashland Global Holdings Inc.(Wilmington、Del。、U.S。)のPliogrip 9100ポリウレタン構造用接着剤で両方の層を熱接着する前に、MFGは材料を洗浄して準備します。
C8フレームに直接接着されたすべての複合部品は、最初にレーザーアブレーションを受けます。これは、GM、MFG、Adapt Laser Systems LLC(米国ミズーリ州カンザスシティ)が、2016年のコルベット向けに開発したプロセスです。 複合材業界の金型洗浄方法を採用しています。レーザーアブレーションは、手作業による研磨に取って代わり、労力、時間、コストを削減し、ほこりを取り除き、再現性を向上させます。レーザー経路、迎え角、エネルギーレベルは、各部品の材料と形状に合わせてカスタマイズできます。製造の柔軟性を最大化するために、床を含むアンダーボディ全体が、接着とネジを介してフレームとそれ自体に接続されています。
CWの8月号では、新しいコルベットの複合材料の革新について引き続き取り上げます。 、ボディ構造レベルで追加のコンポーネントを使用して再開し、外部クロージャー(ボディパネル)で仕上げ、さらに追加のトリムとアップグレードを行います。パート2を参照してください。
樹脂