自動プリフォーミング、パート7:Gesellschaftを埋める
これは、プリフォームに関する7部構成のシリーズの最終回です。このシリーズの詳細については、以下のリンクをクリックしてください。
出典:記入Gesellschaft
自動化のケースヒストリー
フィルの最初の機械は、フィッシャーのスキー板の製造を自動化するために開発されました。今日、元の年間生産量の80%を生産するには、労働者の25%が必要です。スキーはハイブリッドデザインであり、ガラスや炭素繊維の複合材の層、木製の芯、スチールのエッジ、複数の種類のプラスチックで構成されていることにも注意してください。
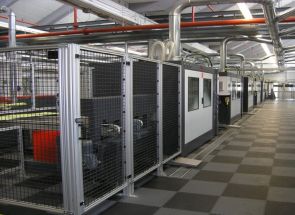
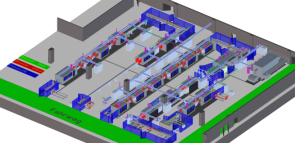
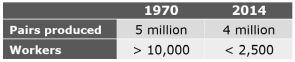
塗りつぶしが提供されました複合スキーを製造するための複数世代の自動装置。
出典:Gesellschaft 2017CAMXプレゼンテーションに記入してください。
BMW
BMWがi3、i8、および新しい7シリーズモデルを開発したとき(これらはすべて炭素繊維強化プラスチック(CFRP)複合材を使用)、Fillはさまざまな自動化ソリューションを提供しました。
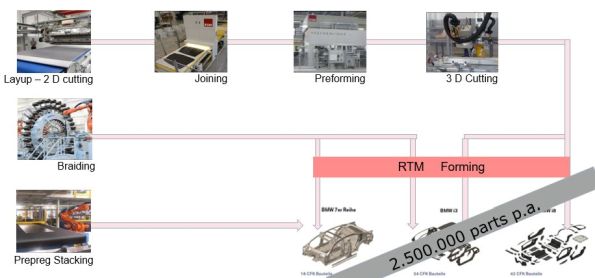
出典:記入Gesellschaft 2017CAMXプレゼンテーション
複合モノコック
フィルはまた、フォルクスワーゲンVWXL1とポルシェ918スパイダーの2つの異なる車種のCFRPモノコックを生産できるMubeaCarboTechの独自の生産ラインを開発しました。この自動化されたラインには、マルチピース作動成形ツール、ハイプレス樹脂トランスファー成形(HP-RTM)プレス、後硬化および機械加工機能が含まれていました。
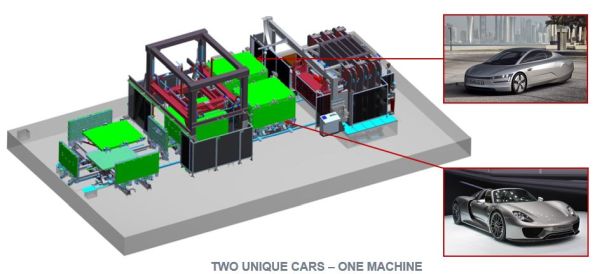
入力してMubeaCarboTechの複合モノコック生産ライン。
出典:Gesellschaft 2017CAMXプレゼンテーションに記入
レイアップの自動化
自動レイアップのために、Fillは、幅3 mまでの乾いた布地(BMWでの大量生産用)など、さまざまな材料用のシステムを開発しました。風力タービンブレード用のSpeedLayer800自動桁キャップ敷設システムは、報告されている速度1.5 m / sおよび精度±1.5mmで幅800mmまでの一方向炭素繊維プリプレグを適用します。 600 kgのプリプレグロールを処理でき、プロセス検証と品質保証機能を統合します。
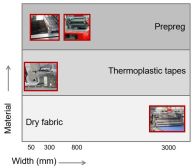
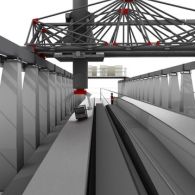
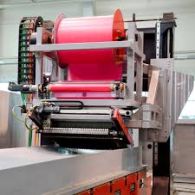
フィルが開発されました幅800mmまでのUDカーボンプリプレグを使用したウィンドブレードスパーキャップ用のSpeedLayer800(右)を含む一連の自動レイアップシステム(左)。
出典:Gesellschaft 2017CAMXプレゼンテーションに記入
低コストの柔軟な統合複合プロセス(LOWFLIP)プロジェクトは、3年間(2013年10月から2016年10月)のEU資金によるイニシアチブであり、Fillと他の9つのパートナーが含まれ、脱オートクレーブ(OOA)硬化輸送のプリプレグレイアップを自動化することを目的としています。構造。 3人のデモ参加者で構成されていました:
- トラックトレーラー用の2.5×2.9mの前壁
- 長さ1.2mの自動車用クロスビーム
- 1.0×1.2mの補強された航空機のテールコーンパネル
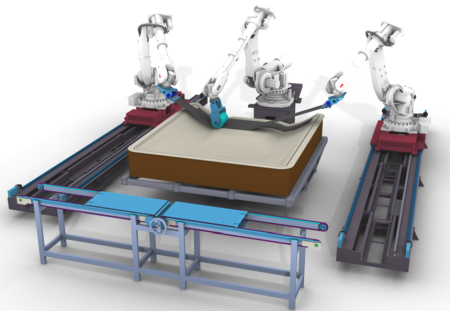
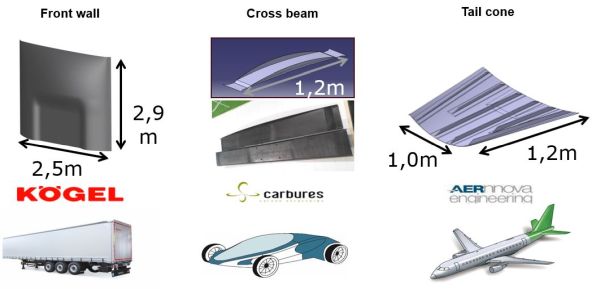
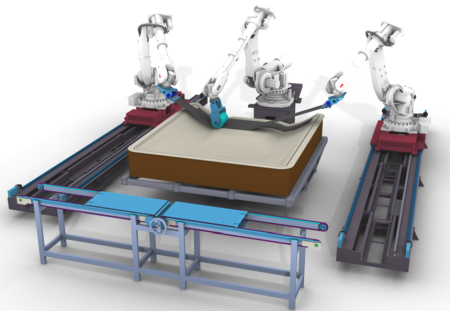
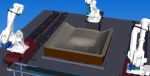
アニメーション
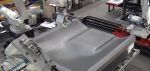
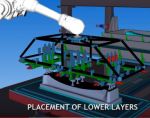
Fillは、LOWFLIPの9つのパートナーと協力して、オートクレーブなしで大型の複合輸送構造を製造するための自動レイアップセルを開発しました。
出典:Gesellschaft 2017CAMXプレゼンテーションに記入
「金型を120°Cまで加熱するために電気抵抗加熱を使用しました」と、Fillの複合材料およびプラスチックコンピテンスセンターの責任者であるWilhelmRupertsberger氏は振り返ります。 「自動レイアップ中、材料は常に張力がかかっていました」と彼は付け加えます。「そして、金型に直接しわのないドレープを実現しました。人間のプロセスを構築しましたが、再現性を向上させるためにロボットを使用したプロセスです。」
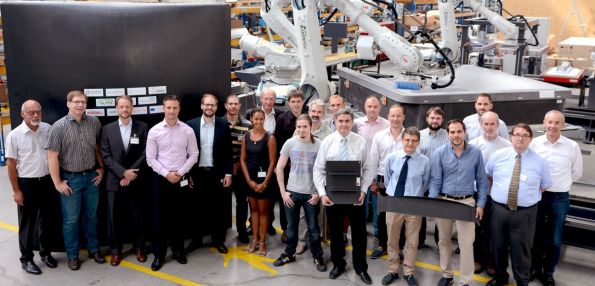
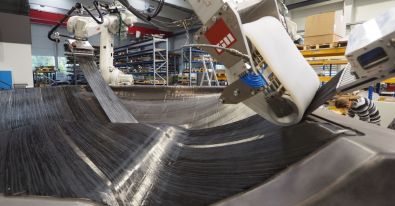
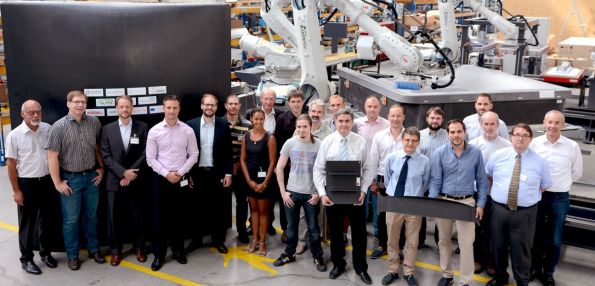
左側のトラックトレーラーの壁と、上のLOWFLIPチームの写真にある車のクロスビームと航空機のテールコーンパネルのデモンストレーターを見ることができます。 。
出典:Gesellschaft 2017CAMXプレゼンテーションに記入
マルチレイヤーシステムへのマルチレイアップ
フィルのマルチレイアップシステムは、熱可塑性テープを使用して、後壁や下部バンパー補強材などの自動車のボディインホワイト(BIW)部品を製造するために開発されました。これらの部品にはオーバーモールドされたリブやその他の機能が含まれることが想定されていたため、プリフォームのレイアップサイクルは、後続の射出成形サイクルと一致する必要があります。
私のJEC2017のショー後のブログ投稿には、マルチレイアップシステムのビデオが含まれていました。マルチレイアップシステムは、複数のロールからテープを送り、レイヤーごとに必要なすべてのテープを、一度に1つずつではなく、同時に配置しました。このようにして、レイヤーあたり10〜15秒のサイクルタイムを達成しました。
フィルはシステムをさらに変更し、マルチレイヤーに名前を変更しました。最大50mm(それぞれ0.01〜0.04 mmの厚さ)の幅で最大16本のテープを回転テーブルに送り、切断し、配置します。テープ敷設ベッドは、最大1.6×1.6mの部品を製造できます。テープは約500m 2 の速度で貼り付けられます / hr — 12〜15秒ごとに、完成したプリフォームごとに約1分のサイクルタイムでフルサイズのパーツレイヤーが適用されます。層は完全には統合されていませんが、熱結合によって結合されています。各スプールのテープがなくなると、マシンを停止することなく自動的に交換されます。
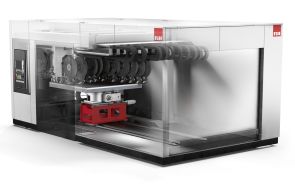
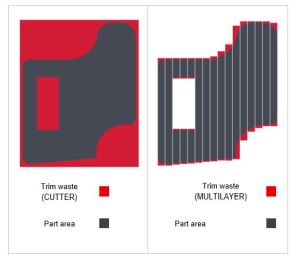
フィルのマルチレイヤー自動予備成形システムにより、必要な場所にのみテープを配置し、必要に応じてテープを方向付けて調整されたラミネートを実現しながら、トリミングの無駄を大幅に削減できます。
出典:Gesellschaft 2017CAMXプレゼンテーションに記入
完成したプリフォームは、プレスで統合されます。 「Multilayerを自動圧密プレスおよびEngel射出成形セルと統合しました。これらは連携して機能し、1分のサイクルタイムを実現します」とRupertsberger氏は述べています。フィルは、今年初めにスインバン工科大学(オーストラリア、メルボルン)から最初の多層システムの注文を受け、JEC World 2019(3月12〜14日、フランス、パリ)で初めて機器の実演を行います。
>RTMプレスとアダプティブインジェクション
フィルは、HP-RTMプレスを含む複数のRTMプレスをSGLコンポジットに供給しています。
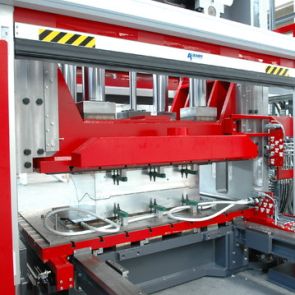
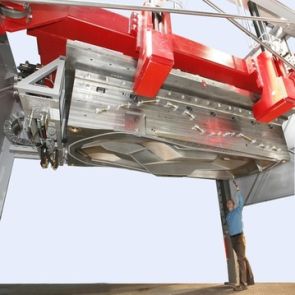
塗りつぶしが提供されましたHP-RTMプレスからSGLコンポジット(右)まで、コンポジット生産用の多種多様なプレス。
出典:記入 Gesellschaft
エアバスオペレーションズ(ドイツ、シュターデ)とアーヘン工科大学のプラスチック加工研究所(IKV)とともに、フィルは最初に航空複合構造用のRTM用の革新的な適応型射出装置を開発しました。 RTMで作成された部品が航空機で飛行する前に、時間とコストのかかる品質保証(QA)プロセスに合格する必要があります。このプロセスを短縮するために、RTM成形ツールにはセンサーが装備されており、生産中にQAをインラインで展開できます。 IKV、Airbus、Fillは、これらのセンサーを射出システムに統合し、すべての成形ツールを装備する必要をなくしました。一般的なRTMシステムでピストンインジェクションシステムが使用されるのと同じ方法で使い捨てカートリッジを使用するアダプティブインジェクションユニットには、次のデータをその場で測定および記録できるセンサーボックスが装備されています。
- 温度
- 圧力
- 樹脂粘度
- 樹脂システムの架橋密度
- ガラス転移温度(Tg)。
成形品の品質を確保しながら、このデータを使用して射出プロセスを管理および制御することもできます。このインダストリー4.0アダプティブインジェクションシステムは、エアロコンポジット用に開発されており、自動車などの他の業界にも拡張されています。
ホットドレープフォーミング
最近のツアー記事で、サラ・ブラックと私はイスラエルの高性能複合材料について書きましたが、ほとんどの企業がホットドレープ成形を使用していることに気づきました。実際、Elbit Cycloneで、ツアーガイドのJonathan Hulatyは、ボーイング787アセンブリの梁と支柱について、「ホットドレープ成形なしでこのタイプの高速プリプレグ部品をどのように製造するかわかりません」と述べています。ホットドレープフォーマー(HDF)も、FBMおよびIsrael AerospaceIndustriesによって不可欠であると見なされています。フィルは、FACCで生産されているいくつかのユニットを含め、HDFシステムを何年にもわたって供給してきました。それらは基本的に真空成形システムであり、赤外線または他のタイプの発熱体と、硬化前にツール上のプリプレグレイアップを加熱および圧縮(デバルク)するための再利用可能なシリコーンゴム膜を備えています。 HDFは、以下に示す完全なエアロコンポジット生産ラインの重要な部分になります。
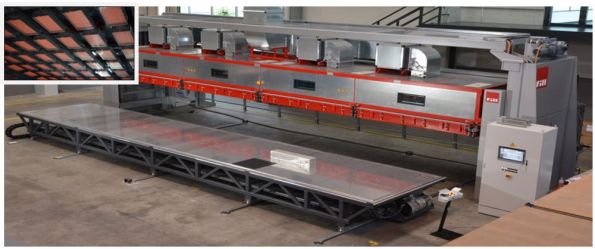
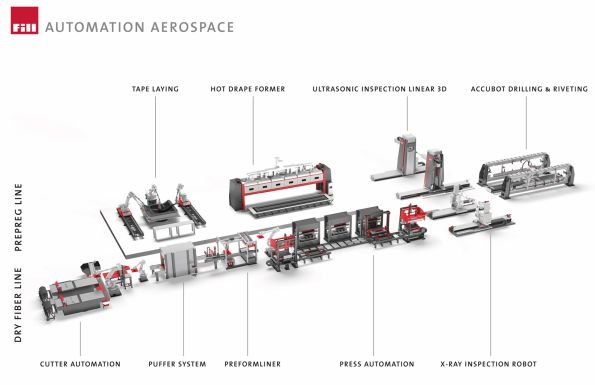
ホットドレープフォーミングは、プリプレグ複合航空構造の大量生産を可能にする重要な要素になり、完全なプロセスチェーンソリューションの一部としてFillによって自動化されています。出典: Gesellschaftを埋める
CFRP用のインダストリー4.0生産セル
2013年の終わりに、Fillは、Tierサプライヤーと共同で、エアバスA320着陸フラップシェルの補強に使用されるCFRPストリンガーを製造するための生産システムの開発を開始しました。このシステムをインストールすると、ステーションの数が減り、生産フローが改善され、使いやすさが向上しました。構成:
- 自動成形ツールの保管
- HDFステーション
- ラミネートがストリンガーに加工されるプレスターンリフティングステーション。
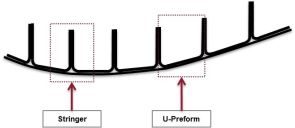
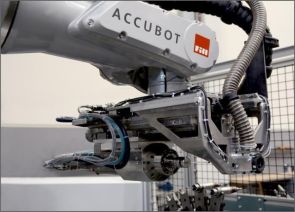
フィルが開発されましたプリプレグ(左)から作られた着陸装置フラップストリンガー用の3世代の自動生産セル(右)。
出典: Gesellschaftを埋める
同じタイプの部品を製造する第2世代のシステムは、2017年に稼働を開始しました。最初のシステムが個々のステーションの最適化に重点を置いていたのに対し、この後のシステムは、手動タスクを最小限に抑え、すべてのツールロジスティクスを統合することを目的としていました。 3つの主要な開発分野により、この第2世代システムは、高い再現性と大幅な生産性の向上を実現できます。
- 成形工具の手動検索と保管は、完全自動の工具返却に置き換えられ、ロジスティクスプロセス時間が短縮されます。これにより、必要なスペースも50%以上削減されました。
- サブプロセスのさらなる自動化により、非生産的な時間が短縮されました。
- すべての記録とレポートのインダストリー4.0デジタル化。 Fillによって開発されたソフトウェアを使用すると、プロセスを常に視覚化し、プロセスチェーン全体で各コンポーネントの履歴を記録できます。センサーは、ボトルネックを回避し、並べ替えを改善するために、ツールと材料の可用性を検出します。
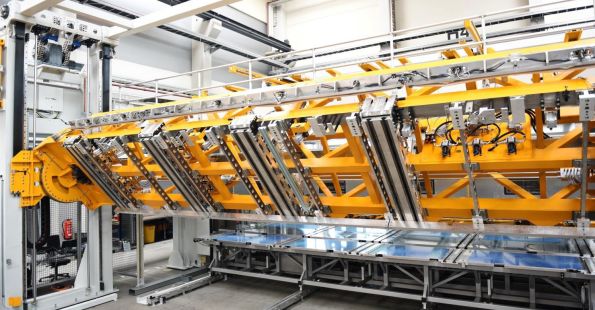
プレスターン-A320およびA350着陸装置フラップストリンガーの自動生産セルで使用されるリフティングステーション。
出典: Gesellschaftを埋める
フィルは現在、エアバスA350-900向けの着陸フラップシェルの第3世代生産システムに取り組んでいます。工具保管、膜形成(HDF)ステーション、プレスターンリフティングステーション、自動工具返却も含まれますが、オートクレーブ工具の輸送システムで強化され、以前の手動輸送トラックと電気トラクターが無人搬送車(AGV)に置き換えられました)。フィルはすでに将来のシステムに取り組んでおり、人と機械のコラボレーションをさらに改善する方法を検討しています。
アキュボット
複合材業界がマルチオペレーションワークセルの将来の必要性を言葉で表現し始める前でさえ、Fillはすでに最初のプロトタイプ、いわゆるAccubotを開発していました。アイデアは、空間補正と直接外部測定システムにレーザートラッカーを使用して正確なロボットを開発することでした。このロボットは、エンドエフェクターで機能を切り替えることができ、非破壊検査(NDT)セルだけでなく、機械加工セルにもなります。 Accubotアプリケーションには次のものが含まれます:
- 掘削
- リベット留め
- NDT –噴出器を備えた超音波
- NDT –X線
- NDT –コンピューター断層撮影
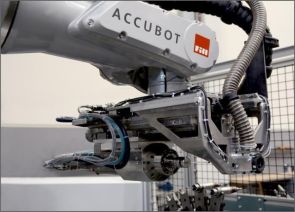
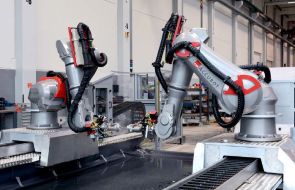
出典:Gesellschaftを埋めます。
FlexHyJoin
Fillは、EUが資金提供するプロジェクトFlexible Production Cell for Hybrid Joining(FlexHyJoin)のメンバーです。この3年間のプログラムは、レーザー接合と誘導接合技術を組み合わせることにより、自動車用途で金属ブラケット/継手を熱可塑性複合材料と接合するための完全に自動化されたパイロットプロセスを開発することを目的としています。フィルは、ソフトウェアやさまざまなテクノロジーの統合を含む自動セルを設計および構築しました。
フィルの研究開発は継続されています。複合部品の製造をより経済的にし、より多くの量に対応できるようにするには、革新的でインテリジェントな生産システムが必要であることを理解しています。また、お客様の規模と特定のニーズに応じて、これらのシステムの開発に取り組んでいます。
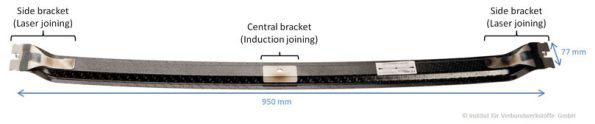
出典:FlexHyJoin。
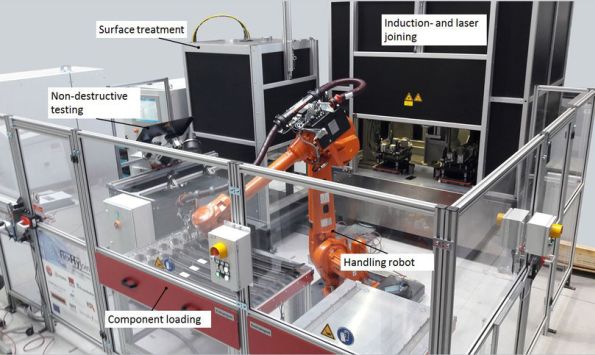
樹脂