アプリケーションスポットライト:医療用インプラントの3D印刷
[画像クレジット:カナダ保健省]
より適切で、より長持ちし、より高性能な骨インプラントを作成することは、整形外科医と外科医の両方にとって継続的な探求です。 3D印刷は、この分野の進歩に大きく貢献しています。
このテクノロジーにより、インプラントメーカーは、機能が強化され、特定の患者のニーズに合わせてパーソナライズされたインプラントを作成できます。さらに、3D印刷は、ポイントオブケアで作成できるパーソナライズされたインプラントへの扉を開きます。
今週は、医療用インプラントへの3D印刷の使用と、このテクノロジーの利点と現在のアプリケーションを見て、3D印刷アプリケーションスポットライトシリーズを継続します。
このシリーズで取り上げられている他のアプリケーションを見てみましょう:
熱交換器用の3D印刷
ベアリングの3Dプリント
自転車製造用の3Dプリント
デジタル歯科およびクリアアライナー製造のための3D印刷
3Dプリントロケットと宇宙船製造の未来
靴製造のための3Dプリント
電子部品の3Dプリント
鉄道業界における3Dプリント
3Dプリントアイウェア
最終部品生産のための3D印刷
ブラケットの3Dプリント
タービン部品の3Dプリント
3Dプリントで高性能の油圧コンポーネントを実現する方法
3Dプリントが原子力産業のイノベーションをどのようにサポートするか
2019年の医療用3D印刷市場
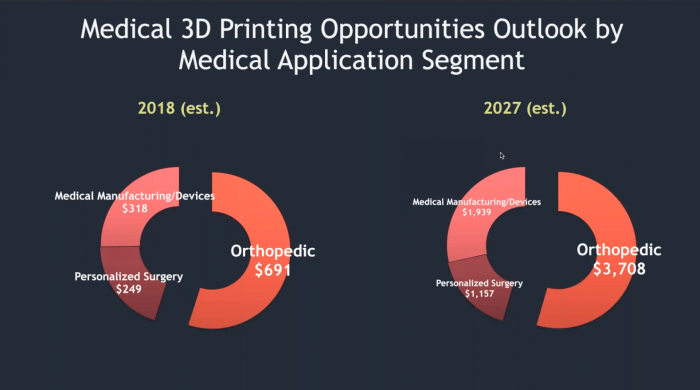
整形外科用インプラント(失われた関節や骨を置き換えるために外科的に使用される医療機器)は、3Dプリントが医療業界に提供する1つの機会にすぎません。
整形外科3D印刷市場は2018年に6億9100万ドルと評価され、SmarTechAnalysisによって2027年までに37億ドルの市場に成長すると予測されています。
ただし、インプラントの製造はかなりですが3D印刷の新しいアプリケーション— 2007年頃に最初に使用されました—過去10年間で急速な成長を遂げました。
2010年、Arcamの電子ビーム溶解(EBM)金属3D印刷技術の早期採用者が3Dプリントされたインプラントに対する最初のFDA承認。 7年後、世界中で300台を超える3Dプリンターが整形外科製品を製造していました。
今日、この技術は、股関節と膝関節の置換術、頭蓋再建インプラント、脊椎インプラントの作成に使用されています。 2019年の時点で、60万を超えるインプラントが3D印刷の助けを借りて生産されると推定されています。 2027年までに、この数は400万を超えるように設定されています。
このように大きな成長の機会があるため、すべての主要な医療機器メーカーが3D印刷技術をますます採用しているのは当然のことです。
世界最大の医療技術企業の1つであるStrykerは、最近、3DプリントされたTritanium TL Curved Posterior LumbarCageを含む独自の3Dプリントされたインプラントを発売しました。この中空体の脊椎インプラントは、2018年3月にFDAの承認を受けました。
Strykerの他に、Johnson&Johnsonの子会社であるDePuySynthesやMedtronicなどの他の著名な整形外科用デバイスメーカーが3D印刷に多額の投資を行っています。後者は、脊椎外科用インプラントのより複雑な設計と統合された表面技術を可能にすることを目的として、2018年5月に3D印刷プラットフォームであるTiONICテクノロジーを立ち上げました。
確立された医療機器メーカーに加えて、医療の新興企業も過去10年間に出現し、3Dプリントされた整形外科用インプラントへの独自のアプローチを開発しています。
その中には、Osseus Fusion Systems、Nexxt Spine、4WEB Medical、SI-BONEなどの企業があります。これらの企業の製品のいくつかは、すでにFDAの承認を受けており、患者の治療に成功しています。
明らかに、過去10年間、3Dプリントされたインプラントには上向きの軌道がありました。しかし、このテクノロジーが医療用インプラントに非常に役立つ理由は何ですか?
3Dプリントされたインプラントの利点
設計の柔軟性
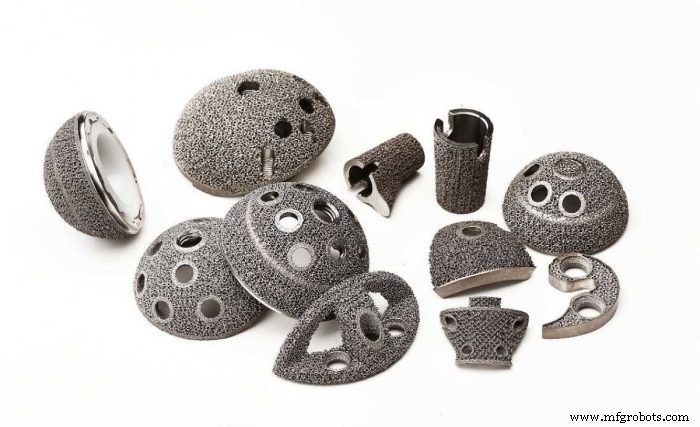
3D印刷を使用すると、従来のテクノロジーでは実現が困難な複雑なデザインを作成できます。インプラントメーカーは、この利点を利用して、小柱構造などの複雑な設計機能を備えたインプラントを製造できます。
海綿骨は、人体に見られる2種類の骨組織の1つです。スポンジ状の多孔質構造であるため、インプラントで模倣するのは困難です。従来、インプラントメーカーは特殊なコーティングを使用してインプラントに小柱構造を作成していました。ただし、これにはインプラントの層間剥離や破損のリスクが伴います。
一方、3D印刷では、小柱構造のインプラントを直接製造できるため、コーティングプロセスをバイパスできます。さらに重要なことに、3D印刷されたインプラントに統合された小柱状の多孔質構造は、層間剥離のリスクを低減したより強力なインプラントを作成します。
このような設計の柔軟性は、選択的レーザー溶融や電子などの金属3D印刷技術によって提供されます。ビーム溶解。これらの技術は、チタンのような生体適合性粉末の薄層に、レーザー(SLM)や電子ビーム(EBM)のような強力なエネルギー源を適用します。
このプロセスを何百もの層で繰り返すことにより、従来のインプラントよりもはるかに効率的に人間の骨の構造に適応する複雑なインプラントを作成することができます。
多孔質3Dプリントインプラントのもう1つの重要な利点は、オッセオインテグレーションの改善です。
オッセオインテグレーションは、インプラントが体の恒久的な部分になることを可能にするプロセスです。多孔性の小柱構造により、骨が細孔内で成長し、インプラントと既存の骨との間の結合がさらに強化されます。
応力遮蔽の低減
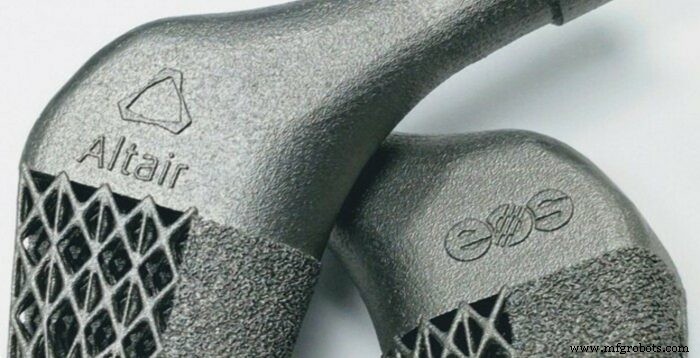
さらに、医療機器メーカーは、患者の骨のこわばりと密度を模倣するインプラントを設計できます。オッセオインテグレーションの改善に加えて、3D印刷されたインプラントは、応力遮蔽を低減し、物理的機能をさらに強化することができます。
応力遮蔽とは、金属製のインプラントが患者の骨から典型的な応力を取り除く現象を指します。その結果、骨密度が低下し、骨が弱くなります。応力遮蔽は、骨折や脱臼を引き起こす可能性があります。このため、患者の骨組織にできるだけ近いインプラントを設計することは、応力遮蔽を減らし、これらの望ましくない影響を排除するための鍵となります。
この最近の例では、IT企業のAltairが、3D印刷とトポロジー最適化ソフトウェアを組み合わせて、改良された股関節ステムインプラントを作成しました。
サイズ、重量、インプラントが負担すると予想される負荷などのパラメーターを入力することにより、トポロジー最適化ソフトウェアを使用して、股関節インプラントの新しい設計を作成しました。最適化された設計により、一般的なインプラントよりも効率的な方法で応力とひずみが分散されます。
さらに、トポロジー最適化ソフトウェアは、インプラントを軽量化するために、材料を格子構造に置き換えることができる場所を決定するのに役立ちました。
テストしたところ、最適化されたインプラントは50.7%の応力遮蔽の低減を提供しました。同時に、その耐久限度は約1,000万サイクルに増加しました。これは、股関節インプラントがロサンゼルスからニューヨークへのジョギングとその逆のジョギングに耐えることができることを意味します—2回。
3Dプリントによる患者固有のインプラント
より複雑なケースでは、既製のインプラントでは、必要な柔軟性を提供できないことがよくあります。 3D印刷はそのような場合に役立ち、インプラントを含む医療機器をカスタマイズおよびパーソナライズする機能を提供します。
患者固有のインプラントを製造するために、メーカーは、コンピューター断層撮影(CT)や磁気共鳴画像(MRI)スキャンなどの患者スキャンから取得したデータを使用します。次に、患者のデータがCADにインポートされ、製造の準備が整い、3D印刷され、完成します。
カスタムの3D印刷されたインプラントを使用すると、手術時間が短縮され、インプラントの適合性が向上する可能性があります。
現在、3D印刷を使用して、機能性と同様に美的要件が重要なカスタム頭蓋および顎インプラントを作成できます。
たとえば、10歳の中国人の少年は、2018年に3Dプリントされた顎のインプラントを受け取りました。彼の顎には、重大な顔の奇形を引き起こさずに取り除くことができなかった腫瘍がありました。
外科チームは、従来の顔の再建はそのような若い患者にとって危険すぎると結論付けました。より良い解決策を探して、彼らは男の子の顎のデジタルモデルを使用して完全に適合したカスタムチタンインプラントを設計する3D印刷に目を向けました。
外科医によると、顎インプラントはそれ以来簡単にフィットしました患者の解剖学的構造に基づいていました。処置の3か月後、顎がうまく整列し、大量の組織が成長した状態で、移植が成功したことが証明されました。
3Dプリントされたインプラントの3つの例
3Dプリントされた股関節インプラントにより、極端な登山が可能になります
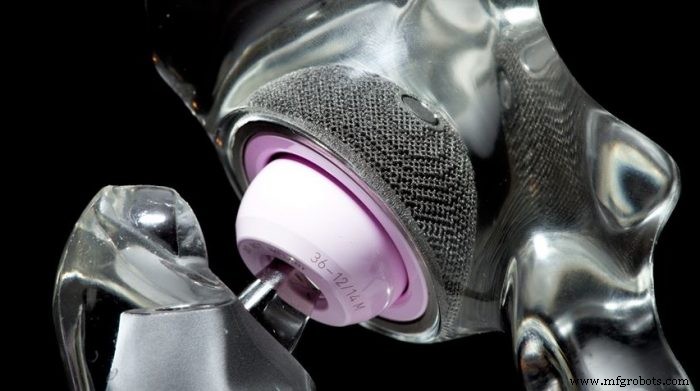
ロマーノベネットと彼の妻、ニベスメロイは、長年にわたって世界で最も危険な山々を登頂してきました。 2017年、登山チームは、世界で最も高い14の山すべてに登った最初のカップルになりました。しかし、この偉業を達成することは、3Dプリントの助けがなければ不可能であることが証明されたでしょう。
ベネットは両側性無血管性壊死に苦しんでおり、これは本質的に骨の崩壊につながります。
最初に診断されたとき、ベネットと彼の妻は、14の山すべての世界サーキットを完成することを恥ずかしがる3つのサミットでした。彼らの旅を続けるために、登山家は彼がすぐに回復することを可能にする安定したインプラントを必要としていました。
このため、Benetの外科医は3Dプリントされたインプラントを使用することにしました。
Delta Trabecular Titanium(TT)カップのブランド名で知られるインプラントは、イタリアの医療機器会社であるLima Corporateによって、ArcamのEBM3Dプリンターを使用して製造されました。
リマの小柱チタン技術と3D印刷を組み合わせることで、天然の骨の多孔質構造を模倣したインプラントを作成することができました。
この小柱構造のおかげで、3Dプリントされたインプラントは、過酷な活動中の機械的ストレスに耐えることができます。他の患者にTTカップを数回移植したベネットの外科医は、優れた安定性と強度を提供することに加えて、3Dプリントされたインプラントは従来のインプラントの寿命を超えて持続する可能性があると信じていました。
Benetが最初の3D印刷されていないインプラントを受け取ったとき、彼は再び登り始める前に何ヶ月も活動していませんでした。 3D印刷されたインプラントを使用すると、登山家は2か月半後に活動を再開することができました。
最終的に、3D印刷されたインプラントはその役割を果たしました。これにより、Benetは迅速に回復し、正常に完了することができました。最後の3つの高地のピークに到達するという彼の探求。
Osseus Fusion Systems:パーソナライズされた金属インプラントへの道中

2012年に設立されたOsseusFusion Systemsは、脊椎関連の怪我のための高度な医療製品の開発に重点を置いている米国を拠点とする会社です。
製品の品質と機能を向上させるために、OsseusはPL3XUSと呼ばれる独自の3D印刷技術を開発しました。
この技術は、粉末床融合3D印刷、特に選択的レーザー溶融(SLM)に基づいており、骨融合と生物学的固定(生きている骨を作るプロセス)に最適化された80%多孔質チタンインプラントを作成できます。インプラント表面に恒久的に付着します)。
2018年8月、Osseusは、付加的に製造された腰椎椎体間固定装置のファミリーであるAriesのFDA 510(k)認可を取得しました。 Ariesファミリーのインプラントは、外科医が腰痛を和らげ、脊椎の回復時間を短縮できるように設計されています。
今年の初め、OsseusのAries製品は、JosephSpineによって初めて実用化されました。脊椎および脊柱側弯症の手術センター。 PL3XUSテクノロジーにより、患者の骨と同様のアーキテクチャでインプラントを設計することが可能になり、骨の成長が促進されました。
今後数年間で、Osseusは、患者のCTスキャン、X線、およびMRIに基づいてパーソナライズされたデバイスを発売する予定です。
この次のステップで、同社は病院が優れた患者ケアを提供できるようにし、最終的には患者の手術結果をさらに改善します。
高性能熱可塑性プラスチックを使用した3D印刷インプラント
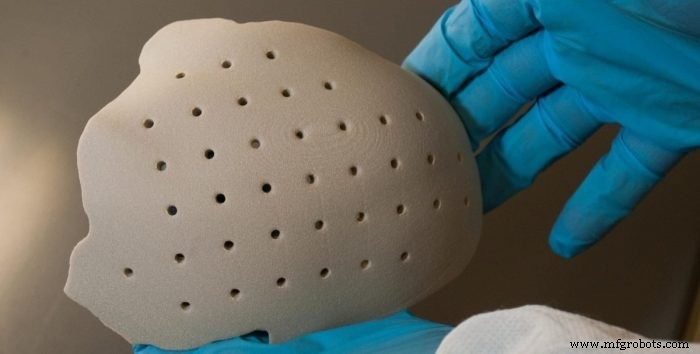
チタンやその他の生体適合性金属に加えて、3D印刷をPEEKやPEKKなどのポリマーと組み合わせてインプラントを製造することができます。これらの熱可塑性プラスチックは、その高い強度と生体適合性で知られており、低コストや放射線透過性など、金属インプラントに比べていくつかの利点もあります。
2013年、Oxford Performance Materials(OPM)は、患者固有の3DプリントされたPEKK頭蓋インプラントのFDA認可を取得した最初の企業になりました。 2017年までに、OPMは1400を超える頭蓋インプラントを出荷し、顎顔面インプラントと脊椎インプラントの2つのデバイスについてFDAの認可を受けました。
同社は、インプラントの開発と製造のためにOPM独自のOsteoFab®プラットフォームを強化する選択的レーザー焼結技術を使用しています。一例では、このプラットフォームにより、患者固有の頭蓋インプラントをわずか3営業日でOPMから設計、製造、テスト、および出荷することができました。外科医は1週間足らずで、インプラントの形状を変更するための切断や穴あけの変更を行うことなく、手術を成功させることができました。
医療用インプラントの3Dプリント:インパクトを与える
生体適合性、耐荷重能力、および耐久性は、整形外科用インプラントの基本的な要件です。 3D印刷は、インプラントの機能性と適合性を向上させながら、これらの要件を完全に満たします。
これは主に、患者の体が適応するのに役立つ多孔質構造のような複雑な形状を作成するテクノロジーの能力に起因する可能性がありますより速く、より少ない合併症でインプラント。
今後、インプラントの3Dプリントは進化し続けます。進行中の研究で特にエキサイティングな分野の1つは、3Dプリントされたインプラントとセンサーの組み合わせです。センサーを利用したインプラントを開発することで、医療提供者は患者の転帰を大幅に改善できる可能性があります。
内蔵センサーは、インプラント周囲の温度、インプラントにかかる動きやひずみなどのデータを収集できます。これにより、外科医は潜在的な問題に早期に対応し、個々の患者のニーズに合わせて治療を調整することができます。
英国の金属3Dプリンターメーカーであるレニショーとウェスタン大学は、大学のキャンパスに外科用ソリューションのアディティブデザイン(ADEISS)センターをすでに設置しています。センターでは、学者と臨床医が一堂に会し、上記のような新しい3Dプリント医療機器の開発に取り組んでいます。
明らかに、3D印刷技術は、整形外科分野で強力な足場を築いています。
ただし、ポイントオブケアで製造されたカスタム作成のインプラントの可能性を真に解き放つには、テクノロジーが成熟する必要があります。
確かに、現在3Dプリントでカスタム作成されているインプラントはごくわずかです。このテクノロジーには大きな可能性がありますが、標準化と規制に関する質問にも対処する必要があります。
とはいえ、カスタム医療用インプラントを作成することは、テクノロジーが最大の影響を与え、より多くの人々が個別化医療から利益を得ることができる場所です。この方向性は、今後数年間で大きな牽引力となると信じています。
次の記事では、3Dプリントがロケット製造をどのように強化できるかを見ていきます。しばらくお待ちください!
3Dプリント
- 医療用マイクロタンタル粉末
- アプリケーションスポットライト:デジタル歯科およびクリアアライナー製造のための3D印刷
- アプリケーションスポットライト:自転車製造のための3D印刷
- アプリケーションスポットライト:ベアリングの3D印刷
- アプリケーションスポットライト:熱交換器用の3D印刷
- アプリケーションスポットライト:鉄道業界での3D印刷
- アプリケーションスポットライト:3Dプリントの恩恵を受けることができる5つの電子部品
- アプリケーションスポットライト:履物の3Dプリント
- アプリケーションスポットライト:3Dプリントロケットと宇宙船製造の未来
- アプリケーションスポットライト:3Dプリントアイウェア
- 3D プリント用の 10 の最強素材