Hitachi Powdered Metals はロボティック オートメーションを採用し、逼迫した労働市場で生産量を 400% 増加させました
粉末冶金 (PM)、または焼結は、さまざまな複雑さの機械部品を効率的に作成するために、既製の金型で元素粉末または合金粉末のカスタム ブレンドを圧縮するプロセスです。成形が完了すると、制御された雰囲気の炉で形状が加熱され、粒子が結合され、パーツが硬化します。
グリーン圧縮とも呼ばれるこのプロセスでは、通常、最終部品の初期原材料の 97% 以上を使用するニアネット コンポーネントが生成されます。カスタム粉末合金混合物は、非常に要求の厳しい用途に必要な強度と公差の仕様を満たす、複雑で複雑な部品を製造する能力を提供します。
インディアナ州グリーンズバーグにある Hitachi Powdered Metal (USA) Inc. の工場は、世界に 9 つある日立の施設の 1 つです。同社は、米国の大手自動車サプライヤー向けのバルブ トレインおよびトランスミッション コンポーネントの製造を専門としており、オートバイおよび造園機器メーカーの間で存在感を増しています。
最初の動機
Hitachi Powdered Metals (HPM) は、2005 年にグリーンズバーグ工場で産業用ロボットへの段階的な投資を開始しました。これは、労働市場の逼迫の出現と、非常に壊れやすい製品を生産する機会に駆り立てられたものです。
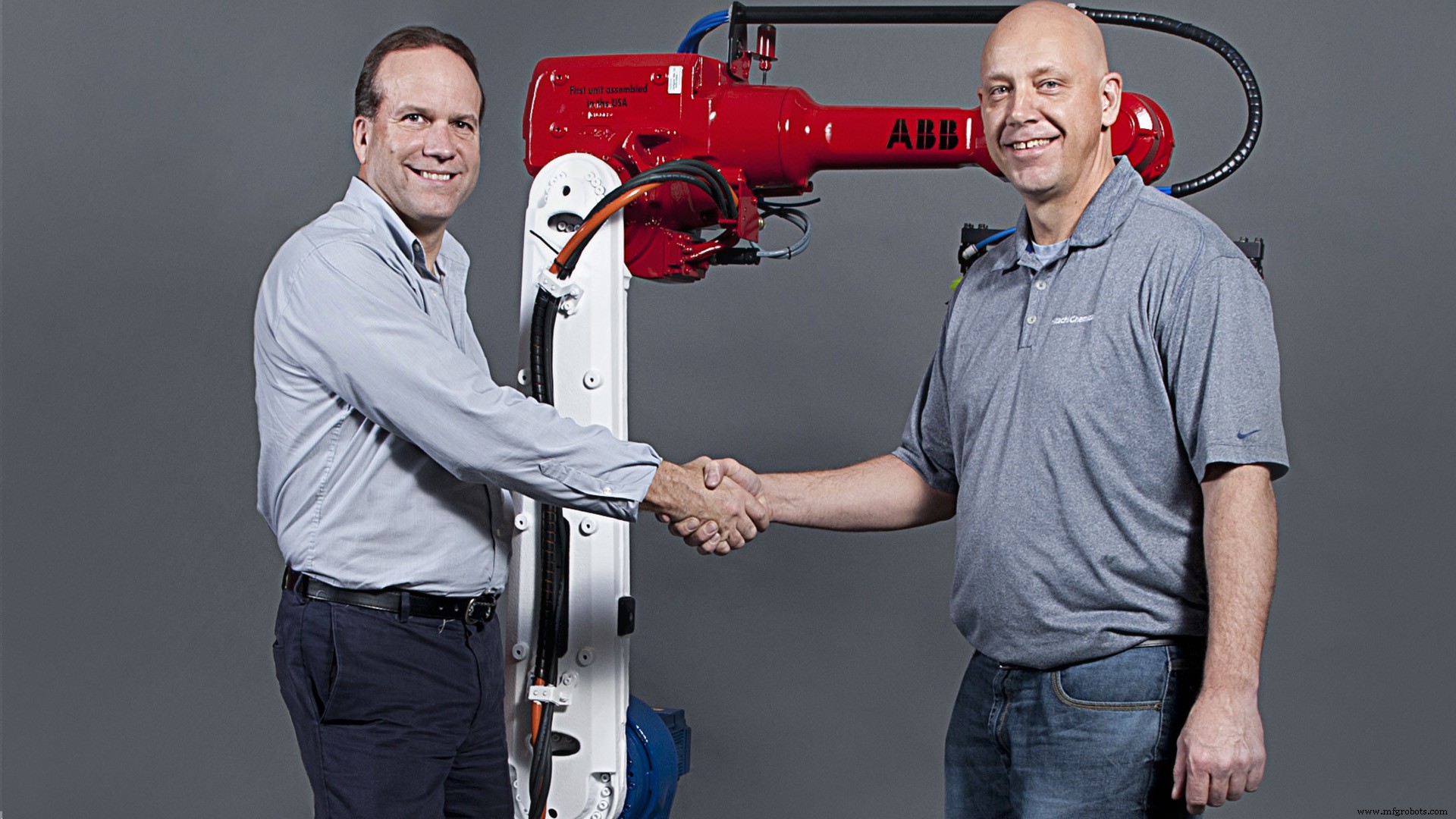
「私たちは、手動で扱うことができない小さくて壊れやすい歯を持つ顧客のために部品を作成する必要があったため、ロボットから始めました。その時点で、すべての圧縮プレスは手作業で処理されていました。」 HPM グリーンズバーグ工場。 「人件費の削減も要因でしたが、最初の設置の直後に、主要な自動車 OEM が町に製造施設を開設しました。従業員の雇用と維持が非常に困難になったため、人件費の問題は労働力の問題に移行しました。」
コストを抑え、最初の試用期間中の露出を最小限に抑えるために、HPM は、近くのインディアナ州ノーブルズビルにある CIM Systems Inc. から中古の 1993 年型の ABB S3 ロボットを購入しました。製造開発エンジニアであり、以前の雇用主でのロボット関連の仕事から、米国で最も長く勤務している ABB ロボティクス バリュー プロバイダー (つまり、システム インテグレーター) である CIM に精通していました。
「CIM には、意図したとおりに機能しない場合に備えて、最初の露出を制限して、ロボットによる自動化への道を容易にすることができる中古のロボットがありました」と Adams 氏は述べています。 「彼らはまた、プログラミングと既存の運用へのシステムの統合に関して切望されていたサポートを提供してくれました。」
スクラップの削減、より良い労働配分
粉末状の金属パーツは、プレスから出た後、オーブンで固める前に軽く触れると簡単に崩れてしまいます。部品を処理するための電磁グリッパーを備えた新しく設置されたロボットにより、新製品の廃棄率は 11% から手作業では 0.5% になりました。
「部品を手動でプレス機から引き抜く際、ハンドリングにかなりのダメージがありました。部品は気付かないうちに変形している可能性がありますが、オーブンから 5 時間後に出るまではわかりません。適切にプログラムされ装備されたロボットは、パーツの取り扱いがはるかに穏やかです」と Adams 氏は述べています。
新しいシステムにより、HPM は手動の機械ハンドラーのいくつかをプラント内の平凡な位置に移動させ、反復作業のストレスを軽減し、より効率的な方法で労働力を再配置することができました。
生産量が 400% 増加
翌年、HPM はさらに 5 台の使用済み S3 ロボットを追加し、最初のシステムから学んだことを他の小型プレスの自動化に適用しました。 18 か月後、HPM は最初の新しいロボットに投資するのに十分なスクラップと人件費を節約しました。
話を 2019 年に進めましょう。現在、200 台を超えるロボットが設置されたグリーンズバーグ工場には、10 年前と同じ数の従業員がいますが、生産量は 4 倍になり、世界中のどの日立 PM 工場よりも少ない人員でより多くの部品を簡単に納入できます。 .
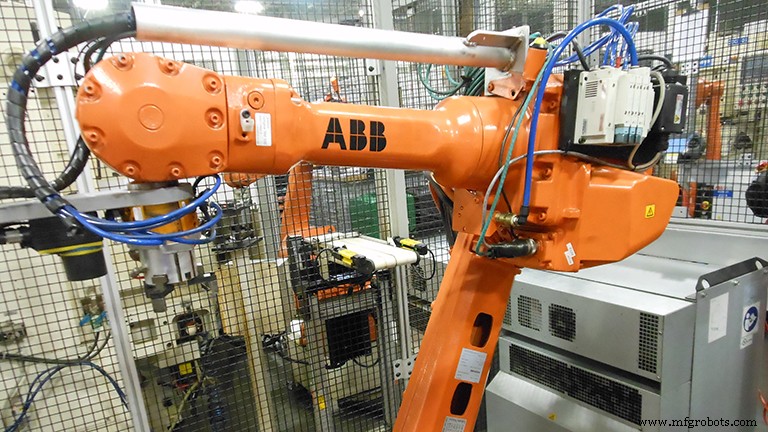
「最初のロボットが壊れやすい部分に設置されると、さらなるロボット オートマトンを実際に活用できることが非常に明白になりました」と Owens 氏は述べています。 「ロボットは私たちの当初の期待をはるかに超えており、私たちが直面し続けている労働力不足により、率直に言って、ロボットが存在しない可能性から私たちを救ってくれたと思います。」
最初のロボットの成功により、その後の設置のペースは安定しました。設置されたロボットが 100 台に達するまでに 10 年かかりました。その後、ビジネスと経済が改善し続けたため、最近設置された 200 th に達するまであと 4 年しかかかりませんでした。 ロボット。
機会が訪れたとき、HPM は中古の ABB ロボットを良好な状態で購入し続けましたが、フリートには新しいロボットがどんどん追加されました。実際、2015 年の #147 以降に追加されたロボットはすべて新しいものです。
HPM の設置ベースには、ABB の中小型 6 軸ロボット、Delta ロボット 1 台、最近追加された複数の SCARA モデルが含まれます。 350 人の従業員とともに、自動化への投資は十分に活用されており、週 5 ~ 6 日 3 シフトで稼働しています。
「当社の本社は日本にあります」と Adams 氏は言います。 「彼らは、ロボットのパフォーマンスと投資に対する迅速なリターンを見て、私たちのロボット計画を非常に支持してくれました。」
新品および中古のロボットの一部は、ABB ロボティクス (ミシガン州オーバーン ヒルズ) の ABB Foundry Prime です。IP67 等級のモデルで、接続部がしっかりと密閉されており、ロボットの内部構造を細かく鋭利な金属から保護しています。植物の大気中を浮遊する粉末。 HPM のフロアにある多くの標準的な IP65 等級のロボット モデルは堅牢で、ほこりの多い環境に耐えることができました。
継続的な拡大
HPM でのロボットの急増は、既存のアプリケーションを複製し、自動化を施設内の他の機能に拡張することによってサポートされました。
最も壊れやすい製品のコンパクト プレスの世話をする最初のロボットを設置した後、Adams と彼のチームは、他のプレスからのコンパクトの取り出しを順次自動化しました。このプロセスの一部は、各部品をはかりに載せてその完全性を検証することでした。検証が終わると、部品は炉に通じるコンベアに置かれました。
労働効率がさらに向上し、ロボットの巧みな操作により、壊れにくい部品の廃棄率が初期部品の 7% から同じ 0.5% になりました。
コンベアの最後で、部品は焼結トレイに置かれ、充填されると、硬化プロセスのために炉に入れられます。この炉への投入プロセスは、自動化される 2 番目の主要な機能になりました。
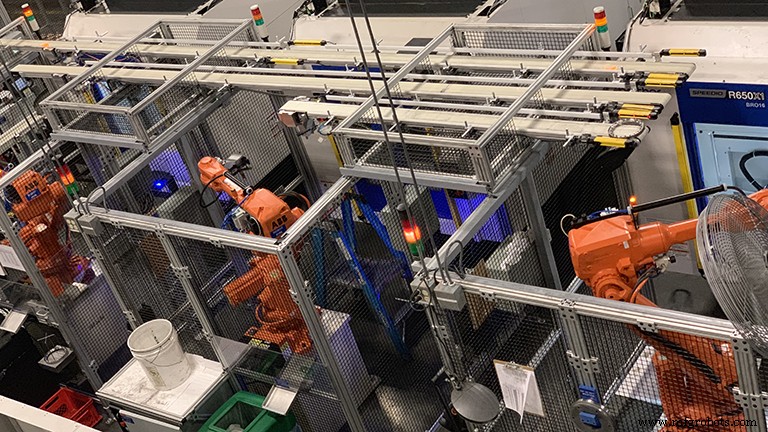
一定のペースでロボットが設置され、トレイから部品を取り出してパレットに載せると同時に、各パレット レイヤーの間に仕切りを挿入しました。
「ロボットに慣れるにつれて、学んだことを取り入れて、施設内のアプリケーションを複製しました」と Adams 氏は言います。 「プログラミングがはるかに簡単になりました。ライン インストールの最終日には、既存のプログラムを微調整し、コピーして貼り付けるだけで、数時間で起動して実行できるようになりました。」
ABB のオフライン シミュレーションおよびプログラミング ソフトウェアである RobotStudio は、HPM によるロボット技術の採用の増加を促進する上で貴重なツールとなりました。生産でロボットを実行する実際のソフトウェアの正確なコピーである ABB VirtualController 上に構築された RobotStudio は、現場で使用されるものと同一のロボット プログラムと構成ファイルを使用して、現実的なシミュレーションを実行します。 Adams は、RobotStudio を使用して、最適なセル レイアウトを設計し、ロボットを特定の操作に統合する前にその性能を検証することができました。
「これまでに開発された中で最高のソフトウェアです」と Adams 氏は述べています。 「新しいアプリケーション用のシステムを作成することと、プラントの他のエリアに既にインストールされているシステムを複製することの両方で、時間とお金を節約できます。」
ビジョンの紹介
レプリケーションが比較的単純になるのは、特定のアプリケーションがインストールされ、プラント フロアに改良された後でのみです。多くの場合、新しいアプリケーションはより困難です。 18 か月後、6 台のプレス テンディング ロボットの統合に成功した HPM は、当時 (2006 年) 初期段階であったビジョン対応テクノロジを採用して、複雑なコイニングまたはプレス操作をロボットで自動化する自信を持っていました。
部品が炉から出た後、反りが生じることがよくあります。そのため、まっすぐまたは平らな状態に戻すためにプレス機に入れる必要があります。多くの部品にはキー溝や歯があり、すべての面を正確に並べて金型に配置する必要があります。ロボットが登場する前は、鋳造される部品はハード オートメーション システムによって処理されていました。このシステムでは、多くの異なる製品バリエーションがあり、頻繁で時間のかかる切り替えが必要でした。切り替えは非常に長かったため、それぞれ約 100 の部品を含む 250 の製品ロットのバックアップが一般的でした.
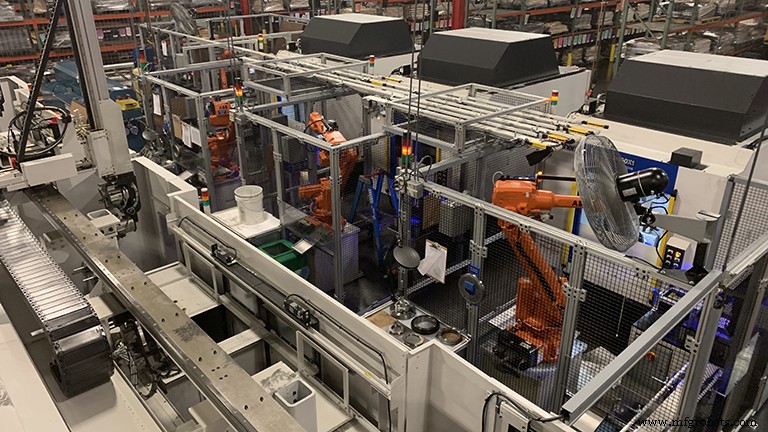
ビジョン対応ロボットにより、ダウンタイムはありません。ロボットは、多くの異なる部品のグループから部品を識別し、それを持ち上げて、半径方向に向け、再プレスに正確に配置することができます.
ビジョンシステムは最新のロボット技術と連携する必要があったため、これがグリーンズバーグ施設に設置された最初の新しい ABB ロボットでした。稼働開始後すぐに、同じアプリケーション用にさらに 2 台の新しいロボットが購入されました。
「コイニング ステーション ロボットを設置する前は、リプレスのスタッフは毎日働いていました」と Adams 氏は言います。 「最初のビジョン ロボットが設置されてから 6 か月後、バックアップがなくなり、スタッフは週末を休みました!」
さらなるビジョン
HPM は、自動化される主要なプロセスの最後の工程、つまり特殊な熱処理のために送られた部品のデパレタイジングで、ビジョンを再び使用しました。パーツは、パレット上の階層化されたレイヤーにきちんと配置されて発送されますが、比較的バラバラになって戻ってきて、積み重ねることが困難です。統合ビジョンを備えた ABB ロボットは、部品を見つけてしっかりと掴むことができるため、安全にデパレタイズできます。
「これは、ABB ロボットのユニークな機能の 1 つです」と、さまざまなビジョン システムの統合を支援した CIM Systems のプレジデントである Dave Fox 氏は述べています。 「パーツはスキッド上で本当にバラバラで、均一な列ではなく、逆さまになっているものもあります。典型的な 6 軸ロボットには、あらゆる種類の特異点の問題があり、もはや動けない位置に置かれます。しかし、高度な特異点回避を使用する ABB ロボットは、部品を見つけてつかみ、ビートを逃さずに安全にコンベアに配置することができます。」
品質検査用スカラロボット
驚くことではありませんが、バルブガイドを検査するためのより効率的なシステムを最近検索した結果、ロボットに戻ってきました。この場合、ABB SCARA (Selective Compliance Assembly Robot Arm) モデルのグループで、通常は小さな部品の組み立てやマテリアルハンドリングに使用されます。
HPM プロトコルでは、すべてのバルブ ガイドを 100% 検査する必要があります。これは、テストする必要があるさまざまな部品 (30 の異なるサイズ バリエーションと各部品の 16 の検出ポイント) を考えると、かなりの作業です。一般的なハード自動化テスト システムではボリュームに十分に対応できないため、Adams はより優れたシステムを探し始めました。
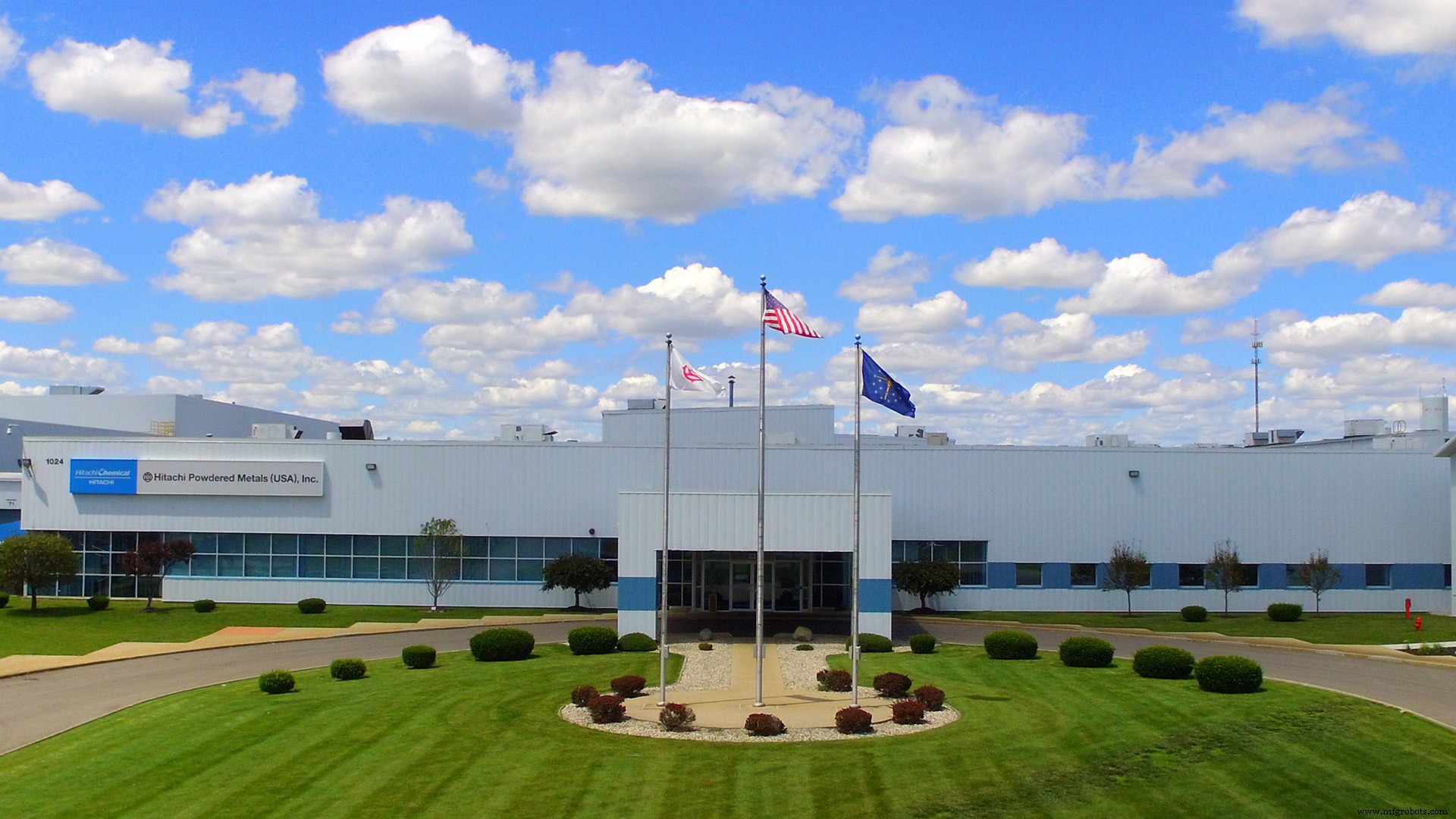
可動部品が多すぎて複雑なエンジニアリングが必要なさまざまなオプションを検討した後、Fox は、ABB が 2016 年にポートフォリオに追加した SCARA ロボットを中心にシステムを設計することを提案しました。設置面積が小さく、限られたスペースに収まる邪魔にならない取り付け方法です。
比較的単純なシステムは、3 台のスカラ ロボットがホッパー コンベアから個々のバルブ ガイドを選び、16 の検出ポイントにアクセスするために必要なさまざまな角度でビジョン カメラと静止した「コンパレータ」にそれらを提示するように設計されました。通過した部品は 1 つのコンベヤーに置かれ、通過しなかった部品はリジェクト ビンに置かれました。
異なる部品のバリエーションを同じように簡単に巧みに処理できる柔軟性により、このシステムは 2 秒ごとに部品を検査することができ、これは以前の方法よりも 30% 高速です。動きが短い距離に限定され、部品が非常に軽いため、6 軸ロボットは、滑らかでリーチが限られている SCARA ほど効果的に機能しません。
「SCARA は、ABB ポートフォリオへの素晴らしい追加です。そのソリューションがなければ、日立は部品検査のために別の技術を追求しなければならなかったでしょう」と Fox 氏は述べています。 「最初に頭に浮かんだ選択肢ではありませんでしたが、ロボット用の別のアプリケーションを見つけることができてよかったです。」
CIM システムは常に存在
HPM に設置された最初のロボットから現在まで、フォアグラウンドまたはバックグラウンドのいずれかでシーンに存在している不変の 1 つが CIM Systems です。必要なときにいつでも利用できる CIM は、新しいロボットと中古のロボットで HPM をセットアップし、プログラミングとトラブルシューティングを支援し、おそらく最も重要なこととして、HPM スタッフに多くのことを自分で行うように教えました.
HPM がロボットを新しいアプリケーションに統合したとき、ビジョンやその他の方法で、CIM はセットアップとプログラミングを行い、RobotStudio の使用を含め、専門知識を共有することを常に意識していました。 HPM のロボット取得スケジュールが一時的に停滞している間、CIM はプログラムの更新、古いモデルの入手困難なスペア パーツの検索、さまざまなヴィンテージのロボットの操作に関するアドバイスの提供に利用できました。
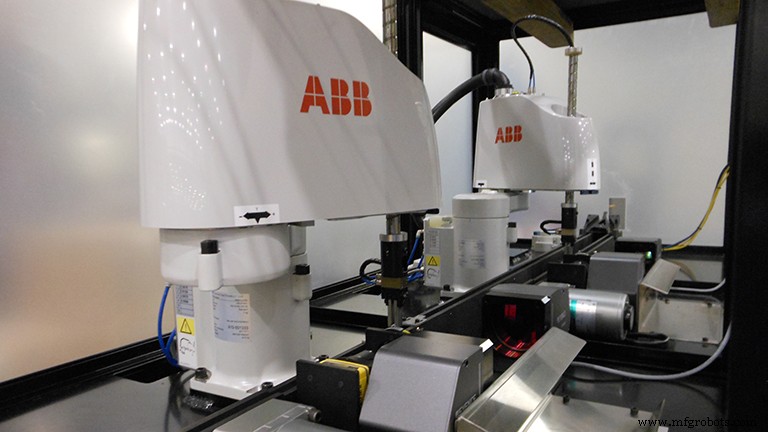
「さまざまなプロセスのそれぞれに当たると、CIM に最初の統合とプログラミングを任せました。工場全体でプロセスの複製を開始すると、自分たちで多くのことを行うことができるようになりました」と Adams 氏は述べています。 「ABB との緊密な関係により、デイブ・フォックスは常に新しい技術がいつ登場するか、そしてどのロボットが当社のさまざまな用途に最適であるかを知っています。 CIM Systems から得たサポートと ABB のサービスは、理想的な組み合わせでした。」
このような長期にわたる関係により、2017 年にオーバーン ヒルズにある ABB の米国製造施設で最初のロボットがラインオフしたとき、HPM の CIM によって委託されたのは当然のことです。他に類を見ない IRB 2400 ロボットは、工場で赤、白、青にカスタム塗装されており、HPM の施設で目立って配置され、検査とパレタイジング作業を行っています。
「HPM 用に最初のアメリカ製ロボットを調達できたことに興奮しています」と Fox 氏は述べています。 「インディアナ工場には、HPM の多くのグローバル施設の中で最も柔軟なオートマトンがあるため、これは特に重要です。」
他の HPM 施設のサポート
日本の HPM の経営陣は、グリーンズバーグ チームがロボットによって達成した生産性の大幅な向上に注目し、2017 年に Adams と Owens を「グローバル ロボティクス」イニシアチブのリーダーに任命し、世界中の他の日立粉末冶金工場がロボットの使用を拡大するのをサポートしました。 .
2 年間のプログラムは中間点を過ぎており、他の国では人件費が低いにもかかわらず、関連会社は大幅な生産性の向上を認識し始めています。
Adams は、ABB のリモート監視機能を HPM にセットアップしました。これにより、ABB や彼のチームのメンバーは、ロボットがどのように動作しているかを確認し、ラップトップ、タブレット、またはスマートフォンを使用して、工場の外のどこからでもほとんどの問題をトラブルシューティングできます。 HPM は、より新しいロボットを使用して、ロボットのステータスとパフォーマンスに関するリアルタイム データを任意の場所から提供する、ABB の統合された業界横断的なデジタル サービスである ABB Ability Connected Services を活用したいと考えています。
将来の計画
HPM の継続的な使命には、ロボットによる自動化による運用の改善が含まれます。
「近い将来、年間 10% の成長が見込まれます。競争力を維持するためにできることは何でもしなければなりません」と Owens 氏は述べています。 「私たちは、電気自動車用にどのトランスミッション部品を製造できるかを検討しており、粉末金属が他の材料で作られた部品をより低コストで置き換えることができる可能性がある、重機などの非自動車セグメントに浸透することを目指しています。 .」
「私は確かに、ロボットの設置ペースが安定しているか、さらには増加していると予想しています」とオーエンズ氏は述べています。
Hitachi Powdered Metals (USA) Inc. の詳細については、www.hitachi-pm.us にアクセスするか、812-663-5058 に電話してください。 CIM Systems Inc. の詳細については、www.cimrobotics.com にアクセスするか、317-773-5600 に電話してください。 ABB Robotics の情報については、www.abb.com/robotics にアクセスするか、248-391-9000 に電話してください。
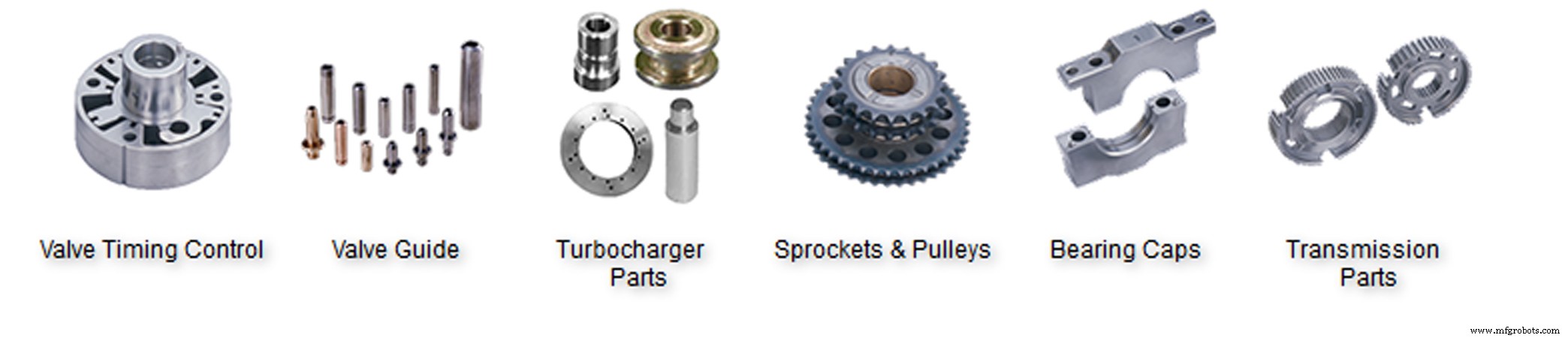
自動制御システム
- ロジスティクスと倉庫の自動化
- より多くの自動化=より多くの機能を備えたロボット
- NPE2018:ロボットと自動化が複雑さの増大に取り組む
- 自動化:ロボット用の準拠したバリ取りブレード
- ABBは、2022年にロボットの自動化を変える主要なトレンドを予測しています
- 新しいタイプのロボットの「頭脳」は、現代の工場を変革する可能性があります
- 日立がロボットシステムインテグレーターのJRオートメーションを14億ドルで買収
- 日立がJRオートメーションの買収を完了する
- ATIインダストリアルオートメーションがロボット用の新しいオービタルサンダーを発売
- BluePrismのデジタルワークフォースとその非常に安全な自動化から推進力を得るためのロボットプロセス自動化市場
- ロボットプロセス自動化市場は7億5000万ドルで成長