アルミニウム押出成形プロセス:詳細な内訳
アルミニウム押出成形は、近年、製品の革新と製造においてますます人気が高まっています。 Technavioは、世界のアルミニウム押出成形需要は2019年から2023年の間に約4%の成長率になると報告しました。
たぶん、あなたはこの製造手順について聞いたことがあり、それが何であるか、そしてそれがどのように機能するかについて興味があります。この記事では、押し出しアルミニウムについて知っておく必要のあるすべての詳細について詳しく説明します。
何 私 s アルミニウム押し出し ?
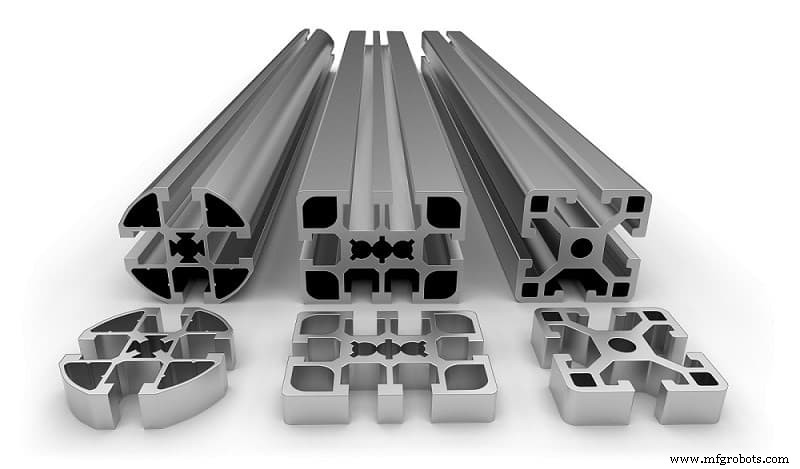
アルミニウム押出成形は、アルミニウム合金材料を所定の断面形状を有するダイに押し込む技術です。かなりのラムがダイを介してアルミニウムを押し出し、ダイの開口部から出ます。それはダイの正確な形で現れ、これが起こると振れテーブルに沿って運び出されます。
このプロセスは、基本的なレベルで理解するための非常に簡単な手法です。使用される力は、歯磨き粉のチューブを手で圧縮するときに使用される力に匹敵します。歯磨き粉は、絞るとチューブの開口部の形で出てきます。練り歯磨きチューブの開口部は、主に押し出しダイと同じ目的を果たします。
アルミニウム押し出しの履歴
この製造プロセスは、100年以上前に始まりました。押し出し手順は、1797年にJosephBramahによって鉛パイプを製造するために最初に開発されました。この手順は当初「噴出」と呼ばれ、トーマス・バーが1820年に最初の油圧プレスの製造を終了するまで手動プロセスでした。アレクサンダーディックは1894年に熱間押出プロセスを作成し、現在では現在使用されています。熱間押出技術のおかげで、メーカーは現在、押出プロセスで非鉄合金を使用しています。 1904年、最初のアルミニウム押出プレスが建設された後、自動車および建設業界でアルミニウムの用途が急増しました。
世界大戦中、アルミニウムの押し出しの需要が大幅に増加しました。それは、軍事用途や飛行機の建設に使用されました。押し出しアルミニウムの必要性はさらに拡大し始めました。それは今や私たちの日常生活の一部です。あなたが運転する車からあなたの家庭用品まで、それらはすべてこの効果的な製造プロセスの製品です。
直接 および 間接 アルミニウム押し出しプロセス
アルミニウム押出成形に使用されるプロセスには、直接と間接の2つの主要な種類があります。直接的なプロセスでは、ダイヘッドを静止状態に保ち、移動するラムに金属を押し込みます。一方、ビレットは間接押出プロセスでは静止したままです。次に、ダイアセンブリがそのビレットに逆らって移動し、金属をダイに押し込む圧力を発生させます。両方のプロセスの詳細を次に示します。
直接 アルミニウム押し出しプロセス
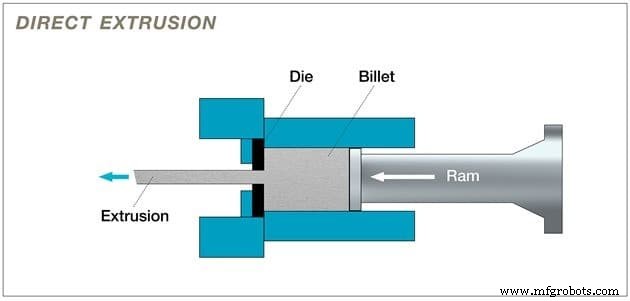
直接押し出しは、アルミニウムを押し出す最も一般的な方法です。アルミニウム押出機は、ビレット(加熱されたアルミニウム)を加熱された壁の容器に入れます。次に、移動するラムが金属をダイに押し込みます。このステップでは、非常に大きな圧力が発生します。
機械工はまた、ビレットとラムの間に材料のブロックを配置することもよくあります。この手順により、ラムと加熱されたビレットが接触するのを防ぎます。アルミニウムビレットとラムは同じ前方方向に移動するため、この方法は前方押し出しプロセスとも呼ばれます。
間接 アルミニウム押し出しプロセス
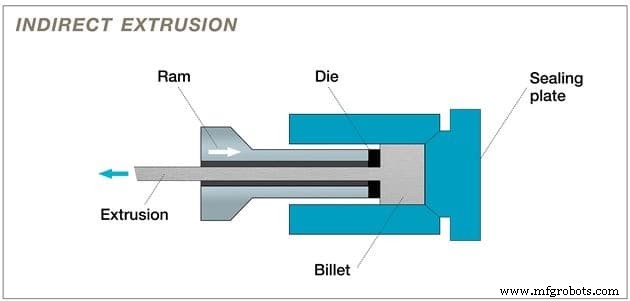
逆押し出しとしてよく知られている間接押し出しは、直接プロセスとは異なります。ここでは、ビレットとコンテナが同時に移動する間、ダイは静止したままです。メーカーは、このプロセスを実行する際に「ステム」を使用します。このステムは、コンテナの長さより長くなければならず、ラムを所定の位置に保持します。したがって、アルミニウムビレットは固定ダイに押し込まれます。
直接法とは異なり、この方法では摩擦が少なくなり、熱制御が向上します。間接押し出しの製品品質は通常、より一貫しています。これは、加えられた力が比較的安定していることが原因である可能性があります。温度の一貫性により、機械的特性と粒子構造も向上します。
ステップ- B y-ステップガイド アルミニウム押し出し 手順 期間
ステップ1 : 準備 E 押し出し D すなわち
最初に行うことは、丸型のダイを加工することです。一方、あなたはすでに利用可能なものをすることができます。押し出しプロセスの前に、ダイを約450〜500 0 に予熱します。 C.これにより、金属の流れが均一になり、ダイの寿命が最大になります。予熱プロセスの後、ダイを押出プレスにロードできます。
ステップ2 : アルミビレットを予熱
次のステップは、アルミニウム合金の厚い円筒形のブロックであるビレットを、細長い丸太の材料から切り出すことです。次にオーブンで約400-500 0 に予熱します C.このプロセスにより、ビレットは操作を実行するのに十分な可鍛性になります。また、溶融しないようにします。
ステップ3 : 転送 B 違法 E 押し出し P レス
ビレットを予熱した後、機械的にプレスに移します。ただし、プレスにロードする前に、必ず潤滑剤を追加する必要があります。さらに、離型剤を押出ラムに塗布します。このプロセスにより、ラムとビレットが互いに付着するのを防ぎます。
ステップ4 : プッシュ B 違法 M アテリアルから 押し出しプレス コンテナ
この段階で、可鍛性ビレットはすでに押出プレスにあります。ここで、油圧ラムは約15,000トンの圧力をかけることができます。圧力により、可鍛性ビレットがコンテナに押し込まれます。次に、アルミニウム材料が膨張してコンテナの壁を埋めます。
ステップ5 : 押し出し材料をダイに押し付けます
アルミニウム材料が容器の壁を満たすと、押し出しダイに押し付けられます。この時点で、圧力が継続的に材料に加えられます。したがって、その唯一の方向はダイの開口部を通ります。それは完全に形成された形でダイの開口部から現れます。
ステップ6 : 押し出しをクエンチする
プーラーは、出てきた後、押し出しを所定の位置に保持します。プーラーは、プレスから出るときにそれを保護します。合金がテーブルに沿って移動すると、プロファイルはファンまたはウォーターバスによって均一に冷却されます。このプロセスは「クエンチング」です。
ステップ7 :せん断 テーブルの長さへの押し出し
押し出しがテーブルの全長に達したらすぐに、ホットソーを使用してせん断します。押出プロセスの各ステップでは、温度が不可欠です。プレスを離れた後、押出成形を急冷しましたが、まだ完全には冷却されていません。
ステップ8 :かっこいい 室温への押し出し
せん断プロセスが完了すると、押し出しは振れテーブルから冷却プレーンに転送されます。プロファイルは、室温に達するまでそこに留まります。室温に達すると、ストレッチが行われます。
ステップ9 : 移動 ストレッチャーへの押し出しと それらを伸ばす に 配置
この段階で形状にねじれがあることに気付くでしょう。これを修正する必要があります。この修正を行うには、ストレッチャーが必要です。各プロファイルの両端を機械的に保持し、完全に真っ直ぐになるまで引っ張ります。このプロセスにより、それらが仕様に組み込まれます。
ステップ10 :移動 フィニッシュソーへの押し出しと カット から長さ
押し出しが真っ直ぐで加工硬化されたので、それらをソーテーブルに移すことができます。この時点で、それらを特定の長さに、主に8〜21フィートに切断できます。鋸引きプロセスが終了したら、オーブンに移動して適切な温度(T5またはT6)に熟成させることができます。
ステップ11 :実行 セカンダリ O 操作 (H 食事療法 F アブレーション、および S 表面 F 終了)
押し出しプロセスが完了したら、プロファイルを熱で処理して特性を高めることができます。熱処理後の次のことは、寸法を修正する必要がある場合にそれらを製造することです。 表面仕上げを追加 また、外観と耐食性の向上にも役立ちます。
どのような形を作ることができるか アルミニウム押し出し ?
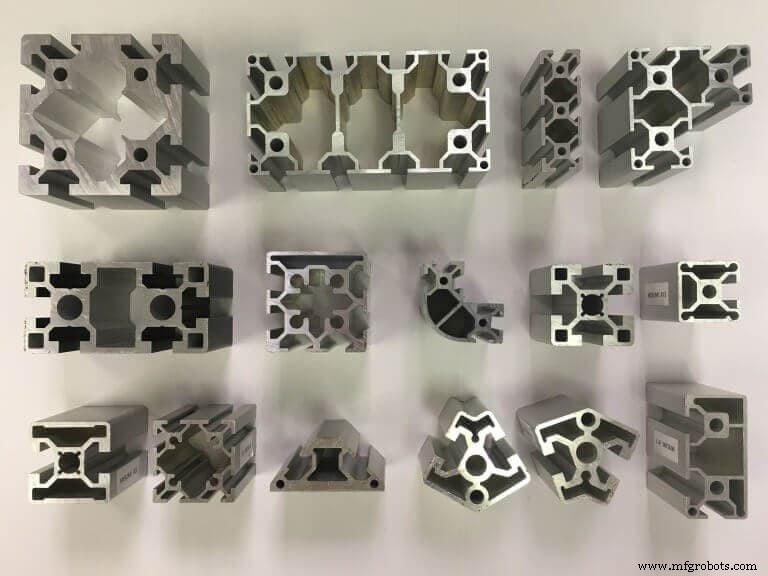
押し出し形状には主に4種類あり、次のとおりです。
1。しっかりしている。 これらの形状には、閉じた開口部やボイド(ビーム、アングル、ロッドなど)はありません。
2。中空。 それらには、1つまたは複数の開口部またはボイド(つまり、長方形または正方形のチューブ)があります。
3。セミホロー。 それらには、部分的に囲まれたボイドがあります(つまり、ギャップが狭い「C」チャネル)。
4。カスタムアルミニウム押し出し形状。 これらの種類の形状には、多くの場合、複数の押し出しがあります。また、さまざまなカラープロファイルを持つ形状を連動させることもできます。これらの形状は、多くの場合、設計者の仕様に準拠しています。
カスタム形状のカスタム押出成形部品を製造したいとお考えですか? RapidDirectにソーシングプロセスを任せてください。利用可能なアルミニウム押し出しプロセスは、最高のものです。高度な機械と専門のエンジニアリングチームを組み合わせて、一流のカスタム製造サービスを提供します。
また、最終製品にいくつかの表面仕上げオプションを提供することもできます。選択に関係なく、確実にお届けします。また、製造段階ごとに継続的なテストを行い、最高のものだけを入手できるようにしています。今すぐデザインファイルをアップロードして、すぐに見積もりを入手してください。
影響を与える要因 アルミニウム押し出し
アルミニウム押し出しは効果的な製造プロセスですが、いくつかの要因がプロセスから得られる最終的な結果に影響を与えます。プロジェクトを確実に成功させるには、これらの要素を念頭に置くのが最善です。
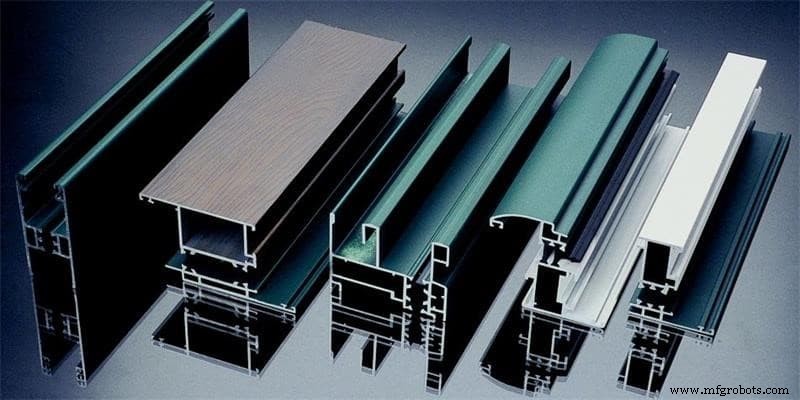
押し出し S おそらく
形状によって、部品を押し出すのがどれだけ簡単で高価になるかが決まります。押し出しによってさまざまな形状が生成される場合がありますが、いくつかの制限があります。たとえば、単純な立体形状は、半中空形状よりもはるかに簡単かつ迅速に押し出すことができます。また、より安価になります。一般に、形状が複雑になるほど、押し出すのが難しく、コストがかかります。
押し出し S 速度
原則として、押出速度は容器内の金属圧力および温度と直接相関します。したがって、速度、圧力、および温度は、安定したプロセスを維持し、一定の押し出しセグメントを生成するために適切に関連付ける必要があります。
ビレット T 温度
最適なビレット温度は、許容可能な公差と表面状態を提供する温度です。同時に、可能な限り最短のサイクルタイムを保証します。プロセスで可能な限り低い温度でビレットを押し出すことが常に理想的です。
温度が高すぎると、金属の流れがより流動的になります。これにより、金属がくびれた領域に入るのに抵抗します。その結果、形状の寸法が望ましい公差を下回る可能性があります。同様に、過度の温度は鋭い角や薄いエッジで金属を引き裂く可能性があります。
押し出し R 比率
任意の形状の押し出し比は、押し出し中に発生する機械的仕事の量を示す良い指標です。セクションの押し出し率が低い場合、金属の質量が最も多い形状の部分の機械的作業は最小限に抑えられます。一方、押出比が高い場合は、より大きな圧力が必要になります。圧力によって金属が小さな開口部に押し込まれ、極端な機械的作業が必要になります。
を押します O 操作
収益性の高いプレス操作を考えると、1フィートあたりの重量がアルミニウム押出成形に関連します。ご想像のとおり、軽いセクションを押し出すには、通常、小さなプレスが必要です。ただし、より大容量のプレスを要求する可能性のある他のいくつかの要因があります。大きくて薄い壁の中空の形が典型的な例です。
フィートあたりの重量が軽いにもかかわらず、それを押し出すのに必要なプレストン数はもっと多いかもしれません。この係数は、押し出し率と同様の効果があります。係数が大きいほど、パーツの押し出しが困難になります。その結果、これはプレス生産に影響を及ぼします。
舌 R 比率
タング比は、コンポーネントの押し出し性能を決定する上でも重要です。押し出しの舌の比率は、最も小さい開口部をボイドに2乗することで決定できます。次に、形状の全面積を計算し、開口部の2乗をこの面積で割ります。舌の比率が高いほど、パーツを押し出すのが難しくなります。
何ですか アプリケーション アルミニウム押し出し s ?
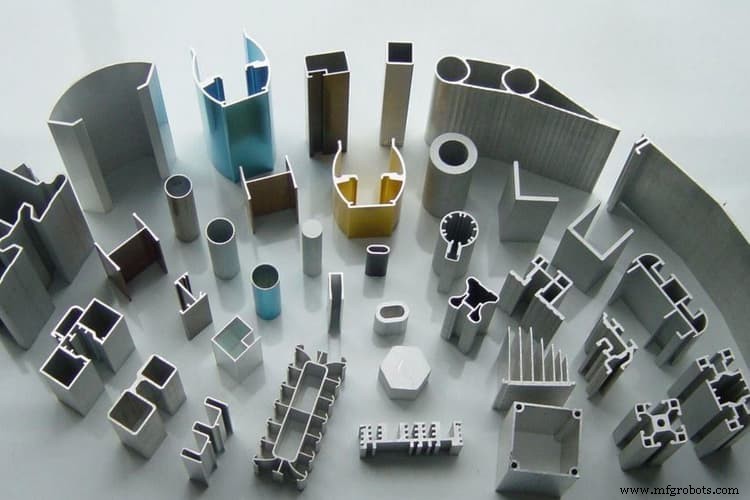
材料特性により、押出アルミニウムはいくつかの産業にとって効果的な製造プロセスになっています。材料の強度対重量比および引張強度により、エンジンブロック、パネル、トランスミッションハウジング、ルーフレール、車両のシャーシ、およびその他の構成部品の押し出しに最適です。
押し出しアルミニウムは、自動車のラジエーター、コンデンサーチューブ、エアコン、原子炉、および電子機器の冷却装置用の部品も製造しています。押し出しアルミニウムチューブは非磁性であるため、ワイヤーや同軸ケーブルを収納できます。アルミニウム材料の耐食性と防錆性は、屋外用途にも役立ちます。さらに、アルミニウムの押し出しは反射率が高くなります。したがって、これらは製品を光、赤外線、および電波から保護するのに役立ちます。
アルミニウム押し出し :重要な製造プロセス
アルミニウム押し出しプロセスは、カスタム断面プロファイルの部品を製造するために不可欠です。このプロセスは非常に興味深いものであり、熱処理、製造、および仕様に合わせて仕上げることができるさまざまな形状の製品を入手できます。 RapidDirectは、望ましい結果を得るために最高のアルミニウム押出成形サービスを提供します。今すぐお問い合わせください。プロジェクトを実現させましょう。設計ファイルをデジタル見積もりプラットフォームにアップロードして、即時見積もりと透過的な注文プロセスを行うこともできます。
産業技術