自律保守:それが何であり、なぜ重要なのか
自律メンテナンス マイナーなメンテナンスタスクを実行するようにオペレーターをトレーニングすることにより、効率を向上させます。以下では、自律保守の実装、維持などについて説明します。
自律保守とは?
自律保守は、機械のオペレーターが継続的に機器を監視し、調整を行い、機械のマイナーな保守タスクを実行する保守戦略として定義されます。これは、メンテナンスと定期的な維持管理を実行する専任のメンテナンス技術者を割り当てるのではなく、行われます。
自律保守は、総合的生産的保守戦略の最初の柱です。自律保守の訓練を受けたオペレーターは、清掃、注油、検査などの日常業務について完全な知識を持っていることを意味します。オペレーターは、機器とその周辺地域の所有権を取得する必要があります。これは、機械を「新品同様」のクリーンな水準に保ち、そこに維持し、オペレーターが定期検査を実施するための適切な技術スキルを習得し、自律検査スケジュールを標準化することから始まります。
自律保守は、2つの主要な原則に従います。
- 適切な操作によって機器の劣化を防ぐため、および;
- 復元と適切な管理を通じて、機器を「新品同様」の状態に保ち、維持します。
これの多くは、マシンのアップグレードが必要な場合、または簡単な修正でマシンをすばやく再実行できる場合を知っているオペレーターに依存しています。自律保守では、オペレーターは、機械のコンポーネントを理解し、改善を行い、起こりうる品質問題を特定し、その原因を特定することにより、異常を検出するなどのスキルを習得する必要があります。
総合的生産的メンテナンスの最終的な目標は、組織の全体的な設備効率を高めることであるため、これが自律的なメンテナンスから始まるのには理由があります。これにより、熟練したメンテナンススタッフは、単純でありふれたメンテナンスタスクについて心配する必要がなくなり、専門的なメンテナンスプロジェクトに集中できます。これにより、次のような複数の利点がもたらされます。
- 機器に関するオペレーターの知識を増やす
- 機器を「新品同様」の状態に保ち、清潔で潤滑されていることを確認します
- 障害になる前に新たな問題に気付く能力
機械のオペレーターがこれらの定期的な保守点検や作業に取り組むことができるようにすることで、故障や機器の劣化を減らし、OEEをさらに最大化できます。
自律メンテナンスの実装方法
自律保全の実施は、各プラントの運転状況によって若干異なる場合がありますが、通常は7つのステップに分かれています。
- オペレーターの知識を増やします。 オペレーターは、マシンを最大容量まで実行するマスターである可能性がありますが、自律保守を効果的に行うには、マシンの内外を知る必要があります。これには、メンテナンス技術者による、マシンのコンポーネントの動作とその目的に関する技術的な詳細に関するトレーニング、および問題解決スキルに関するトレーニングが含まれます。つまり、オペレーターは4つの機器関連スキルを持っている必要があります。
- 異常の検出
- 異常の修正と復元
- 最適な機器条件の設定
- これらの最適な機器条件を維持する
これらのスキルが教室で確認されると、オペレーターは自分のマシンで基本的なメンテナンスタスクを実行でき、メンテナンス技術者はすべてがカバーされていることを確認します。
- 最初の機械の洗浄と検査。 このステップでは、機器を「新品同様」の状態に戻すことを目的として、機器を「ベースライン」状態に戻します。生産、保守、エンジニアリング、およびオペレーターのメンバーを含め、すべての手がこのタスクのためにデッキにいます。設備の徹底的なオーバーホールと清掃だけでなく、周辺地域の清掃も行っています。目標は、劣化の兆候を特定して排除することにより、各機器を完全に完全なパフォーマンスに復元することです。チームは次のようなものを探して修正する必要があります。
- リーク
- ボルトが緩んでいる
- 適切な潤滑
- 亀裂–明らかなものと明らかでないものの両方
- 液体汚染率
- 水と油からの物質の除去
- ほこりや汚れの除去
- 油やほこりの堆積による電気製造の導電性制限
- ほこりの蓄積による停止の排除
この徹底的なクリーニングを実行しながらプロトコルを文書化することをお勧めします。これにより、問題を簡単に追跡でき、オペレーターは簡単な手順を含むアクセスできるものを手に入れることができます。
- 汚染の原因を取り除き、アクセスを改善します。 最初のクリーニングが完了し、すべての機器が復元されたので、再び不良状態にならないようにします。これは、考えられるすべての汚染源を排除し、清掃とメンテナンスのアクセシビリティを向上させることで実現できます。
このステップでは、安全性も考慮されます。稼働中のマシンを維持することは危険であるため、より良いアクセスポイントを通じて安全性と可視性を向上させることが最も重要です。これを行うための一般的な方法は、不透明なカバーを透明なカバーに交換して、実行中のパーツをすばやく簡単に視覚化することです。汚染の原因を取り除くには、次の方法があります。
- 洗浄基準の確立と遵守。
- 汚れを避ける。 高品質のシーリングと機械カバーは開始するのに適した場所ですが、一部の汚染は、空気圧または乾式スクリーニングのいずれかによって、ポンプや除塵などに投資することによってのみ封じ込められる場合があります。
- 清潔さを促進します。 検査およびメンテナンス中は、常に清潔さを繰り返してください。
- 秩序の促進。 ツールがその場所にあり、そこにとどまるようにすることで、効率が向上します。
- 潤滑と検査の基準を作成します。 このステップは、各機器とそのオペレーターに基づいて必要に応じて調整できます。清掃、検査、および注油に関するオペレーターの基準を確立することは、ファイルにある現在の文書から始めて、これらの手順を達成するための改善された方法で終わる必要があります。規格は、どのコンポーネントを洗浄および潤滑する必要があるか、それらをどのように洗浄および潤滑する必要があるか、および他のすべての保守責任を割り当てる必要があることを示す必要があります。基準は、マシンが非クリティカルと見なされるかクリティカルと見なされるかによって異なります。
- 重要でない機械の場合、オペレーターは、確立された基準に従うように経験豊富な保守エンジニアによって訓練されます。その後、オペレーターは独自のルーチンを確立できます。
- 重要なマシンの場合、標準を開発するために、メンテナンス方法に専念するメンテナンスエンジニアのチームを作成できます。
完成したら、すべての標準を文書化し、オペレーターがすぐに利用できるようにする必要があります。
- 検査と監視。 従うべき一連の標準が用意されたので、オペレーターは基本的なメンテナンスルーチンを変更して、タスクを合理化および改善できます。オペレーターの保守タスクは追跡され、保守部門自身のスケジュールと比較され(通常はコンピューター化された保守管理システムを介して)、タスクの重複が問題にならないようにします。オペレーターは、潤滑レベルの確認、漏れの特定、ボルトの締め付け、亀裂や摩耗などの差し迫った機械的問題の検索、張力測定やセンサー調整などの機械的調整の実行など、見過ごされがちな基本的なメンテナンスタスクを実行します。
- 視覚的なメンテナンスを標準化します。 自律保守を標準化し、機器を「視覚的」にすることは、各機械の完全性を維持するための重要なステップです。機器をどのように視覚化しますか?例としては、パイプを通る流体の流れを特定する、不透明なカバーを可能な場合は透明なカバーに置き換える、バルブとレバーの開閉方向にラベルを付ける、ゲージとサイトグラスに危険な緑色の「安全」または「通常」の動作値をマークするなどがあります。赤のレベル。要するに、マシン上のものをできるだけ明白にします。
- 継続的な改善。 定期的に時間をかけて標準化されたプロセスを分析し、改善の余地がある場所を確認することは、効率的に運用していることを確認するために重要です。メンテナンスエンジニアが将来のマシンを設計するときに使用できるデータを提供し、それらへのアクセスとメンテナンスをさらに容易にするためには、障害の適切な記録を保持することが不可欠です。
継続的な改善は、チームリーダーや保守技術者がオペレーターの作業を定期的に監査することからも生じる可能性があります。これにより、改善点を指摘できるだけでなく、オペレーターが良い仕事をしたことを祝福する機会が得られます。
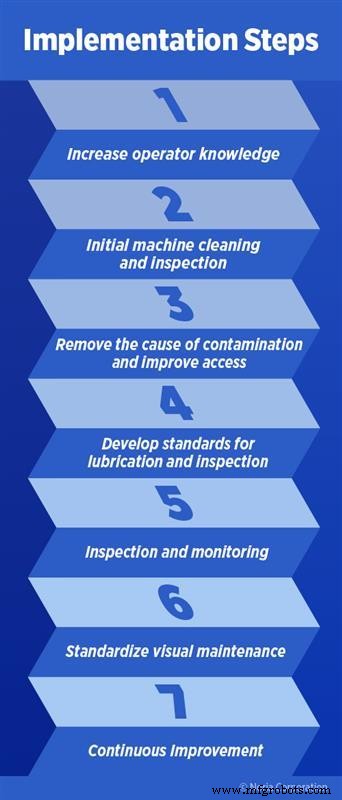
自律保守の維持
オペレーターが自律保守について適切にトレーニングされ、手順が標準化され、監査システムが導入されたら、このプロセスの維持に集中するときが来ました。自律的なメンテナンスプロセスを維持するために、日常業務に組み込むことができる簡単なツールがいくつかあります。
毎日のスタンドアップミーティング オペレーターとその直属のマネージャーが毎朝集まって、状況について話し合うのに最適な方法です。これらの会議は、サークルを回って、各自がうまく機能していることについて話し合い、遭遇した問題について言及できるようにすることで機能します。その他の議題項目には、学んだ教訓、人員の状況、管理の最新情報、およびその日の目標と行動が含まれます。毎日のスタンドアップミーティングは、オペレーターが対処している苦労を浮き彫りにしたり、組み込む必要のある上級管理職からの変更を導入したりする可能性があります。
シングルポイントレッスン チームメンバーが変更を実装するのを支援し、過去に発生した問題を覚えたり伝達したりして再発を防ぐのに苦労しているステップを見落とさないようにするのに最適です。ワンポイントレッスンは、通常、機器サブシステム、安全ポイント、および基本的な操作情報に焦点を当てています。ワンポイントレッスンの例は、レバーまたはガードに直接配置される貼り付けラベルを作成して、レバーまたはガードを安全位置に戻すことを忘れないように苦労しているオペレーターに思い出させることです。次の手順。
自律保守を維持するためのその他の手順は次のとおりです。
- 障害と故障のデータを追跡する: このデータは、自律保守手順の作成を開始するときに不可欠です。どの機器に最も注意を払う必要があるかをオペレーターに案内するだけでなく、このデータを長期にわたって追跡することで、改善を追跡できます。
- 指標を使用する: 確立された測定基準は、修理と性能に関する設備総合効率を監視および追跡するための鍵です。平均故障間隔や平均修理時間などのパターンを分析することで、将来の障害を予測し、さらには防止する方法を学ぶことができます。
- ドキュメントコンポーネントの摩耗: 他の手段を使用して、コンポーネントの摩耗を追跡します。オイル分析、振動分析、赤外線サーモグラフィーなどのメンテナンステクノロジーにより、機器の故障に関する追加の洞察を得ることができます。
- 作業指示書の作成を標準化する: 作業指示書ソフトウェアを使用すると、作業指示書の作成と保守データを自動化して追跡するのに役立ちます。コンピューター化された保守管理システム(CMMS)と統合されたソフトウェアを使用すると、プラント内の各機器の保守ログシートを作成できます。ここでは、障害、交換、およびコンポーネントの状態が変化したときのすべてのインスタンスを記録できます。
自律保守のメリット
ほとんどの組織は、重要な資産が失敗する理由を特定し、それらを修復するために、高度なスキルを持つ保守チームの採用、トレーニング、および開発に多額の投資を行っています。自律保守は、これらの技術者が検査、注油、微調整などのスキルの低いタスクを実行することから解放することを目的としています。とりわけ、自律保守が組織にもたらす3つの主要な利点があります。
最大のメリットは人件費の削減です。これには、移動時間に関連する非効率性の低減と可用性の待機が含まれます。常に機械の隣にいるオペレーターがいることで、このような問題は大幅に軽減されます。
自律保守のもう1つの利点は、高度なスキルを持つ保守要員の可用性が向上するため、より重要なニーズに対応できるようになることです。自律保守を採用することで、最も緊密なスタッフが配置された保守部門でさえ、日常の保守を犠牲にすることなく重大な問題に対処することができます。
最後に、自律保守は、「私たち/彼ら」の考え方を排除することにより、チームの結束力を向上させます。従来、オペレーターは「使用する」という考え方を持っていましたが、保守技術者は「保守して修正する」という考え方を持っています。自律的なメンテナンスは、これをよりまとまりのある「私たちが維持する」姿勢にシフトし、総合的生産的メンテナンスの柱に直接適合します。
機器のメンテナンスと修理