プロセスプランニングとは|プロセス計画のステップ、タイプ、利点
この記事では、プロセス計画とはについて学習します。 ? 要件とは何ですか このプロセスの場合、プロセス計画の手順は何ですか 、タイプ 、利点 、短所 およびシーケンス 含まれている活動の。 定義から始めましょう 。
プロセス計画とは何ですか?
プロセス計画 は、部品または製品の製造に必要な製造操作の詳細なリストを作成するために使用される手順です。これは、製品設計と製品製造の間のリンクです。
プロセス計画は、効率的な一連の操作を確立し、適切な機器とツールを選択し、製品が仕様に規定されているすべての要件を満たすように操作を指定します。同時に、プロセスは最小のコストと最大の生産性で実行されます。
基本的に、プロセスプランを生成する方法は2つあります。彼らです :
1。 手動プロセス計画および2。 コンピュータ支援プロセス計画
プロセス計画の要件
適度に優れたプロセス計画は、次の要件を満たす必要があります。
1。 サービス機能を明確かつ包括的に定義する、製造されるジョブの簡単な説明。
2。 サービス機能を規定する仕様と規格。
3。 完全な仕様のジョブの作業図面。
4。 ブランクの描画。
5。 ある期間に製造される部品の数量に関するデータ。各ユニットに必要なスペアパーツ。
6。 期間中に製造される部品の総数。
7。 工作機械の仕様や容量データ、その他の利用可能な機器、店舗内の機器の配置や積載に関するデータを含む機器データ。
8。 生産エンジニアリングと製造が組織化され、達成される条件、つまり、新規または既存のプラント、プラントで利用可能な機器、新しい機器を入手する可能性など。
9。 プラントの場所。
10。 工場に人員を配置するための人的資源の利用可能性。
11。 作業開始日と納品日。
基本的な要件を理解した後、次のことは異なるプロセス計画のステップ 。
プロセス計画手順
プロセス計画の目的は、部品の製造に必要な最適なプロセスを決定して説明することです。これらの目的を達成するために、次のプロセス計画手順に従うことができます:
1。 部品のサービス機能に精通すること。
2。 サービス機能を定義する製造仕様およびさまざまな標準(精度、出力、効率など)を調査し、批判的に分析すること。
3。 製品の年間生産量に精通すること。
4。 作業中の図面を調査して批判的に分析し、部品を製造することがすべての点で実行可能かどうかを確認し、図面の誤りを明らかにして修正します。
5。 完全な識別と必要な数量を使用して、製造する部品と購入する部品を決定します。
6。 外部から購入する適切な品質と量の原材料のリストを作成し、その形状、サイズ、および特殊な特性を示します。
7。 ブランクを取得するための最も経済的なプロセスを選択し、原価計算の目的で生産される数量を決定します。
8。 現在の生産コミットメント、納期、生産量、品質基準を考慮して、部品を製造するための最も経済的なプロセスを決定する。
9。 特定のプロセスの各部分で実行される操作の最適なシーケンスを決定すること。
10。 必要な精度で操作を実行する工作機械を選択します。
11。 より高い生産率を実現するために必要となる可能性のある、ジグ、フィクスチャ、ダイ、ゲージなどの他のアクセサリや機器を選択するため。
12。 機器と作業場をレイアウトするには、機械の負荷を計算し、その過程で必要な修正を行います。
13。 プロセスを修正して、プロセスが実際の生産で実現されたときに発見されたすべての間違いや欠点を修正します。
14。 検査の段階を決定するために、製造のさまざまな段階に必要な検査手順と限界ゲージを正確かつ高速に検査します。
15。 各操作のセットアップ時間と標準時間を決定し、支払い率を修正します。
16。 仕事を成功させるための労働の種類を決定するため。
17。 製品の推定コストを決定して、それが販売市場で完了するかどうかを確認します。
プロセス計画は、技術変更プロセスを考慮して処理を簡素化するための動的なものであり、計画担当者は製造における製造手順を分析する必要があることに注意してください。
さらに説明が必要なプロセス計画の前述のステップのいくつかを、以下でより詳細に説明します。
製造仕様: 製造仕様書が記載されている主な文書は詳細図です。図面は以下を指定します:
1。 適切な幾何学的形状からの許容偏差を伴う寸法と加工精度。
2。 許容偏差のあるさまざまな表面の調整の精度。
3。 熱処理の対象となる場所および必要な熱処理の種類。 4.表面品質。
5。 必要に応じて、指定された表面仕上げを得るために必要な加工方法。
6。 このコーティングの種類と厚さの保護コーティングの場所。 7.完成品の寸法を測定する場所を探します。 8.必要に応じて、X線、水圧試験などの特別な検査手順。
最後に、仕様は機械加工プロセスおよび検査と可能な限り調整する必要があります。必要に応じて、計画を成功させるためにわずかな変更または変更を加えることができます。
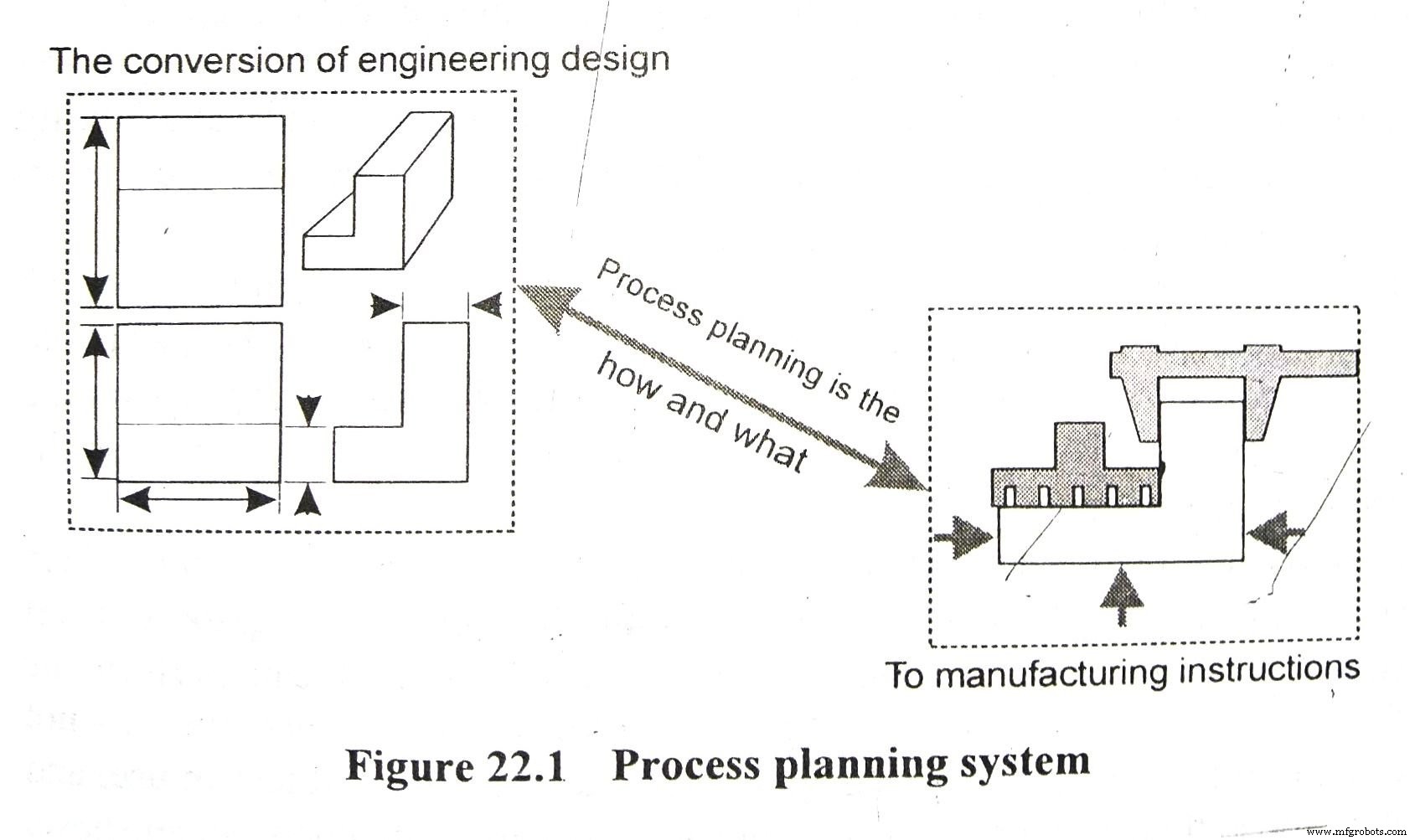
空白の決定: プロセス計画は、実際にはブランクの選択から始まります。ブランクサイズと完成品の仕様は相互に関連しており、機械加工と仕上げ操作の一般的な概要を決定します。
ブランクの精度は、その製造方法に依存し、完成した機械部品の仕様によって、機械加工プロセスの一般的な概要と、荒加工、半仕上げ、および仕上げ操作への細分化が決まります。
工作機械の選択 : 次のプロセス計画ステップは、部品の機械加工の方法またはプロセスの選択によって主に決定される工作機械の選択です。言い換えれば、機械加工プロセスを支配する原則は、工作機械の選択の基礎となるはずです。あらゆるタイプの機械加工用の工作機械を選択するための明確なルールを策定することは困難ですが、特定の操作用の工作機械を選択する際には、次の要素を考慮する必要があります。
1。 ワークピースのサイズ、形状、材質。
2。 精度と表面仕上げが必要です。
3。 工作機械に必要な生産能力と生産能力。
4。 操作を実行するのに十分かどうかを知るための工作機械の力。
5。 経済的かどうかを知るための操作のパフォーマンス。 6.工作機械の操作のしやすさと便利さ。
可用性チャート : 可用性チャートは、クラス(つまり、分類されたリスト)に従って配置された工作機械のリストです。たとえば、エンジン旋盤、タレット旋盤、オートマチックなどで、識別とモデル番号、場所、一般的な状態、使用可能な工具、切削速度が示されます。ただし、新しい工作機械の場合、切削速度と送りは、付属のカタログから取得されます。この可用性チャートは、既存のプラントで新製品の工作機械を選択する際に必要です。
マシン負荷チャート どのマシンがアイドル状態のままで、どのマシンがロードされているかを示します。したがって、プロセスプランナーは、機械加工操作を実行するために使用できる特定の工作機械を選択します。プロセスプランナーは、生産プランナーほど機械負荷チャートに関心がありません。
機能チャート : 能力チャートは、工作機械が作業を行う能力を示すチャートとして定義することができます。能力チャートは、工作機械がその機能を十分に実行できる定格容量の量を示します。工作機械は、他の機械と同様に、使用中の傷みにより購入時と同じ状態にならず、長期的には精度が低下します。マシンの現在の状態を示す機能チャートは、プロセスプランナーが適切なマシンを選択するためのガイドです。
操作シーケンスの計画
最適な操作シーケンスを決定することは、計画プロセスおよび生産用に設計された製品の実現における重要なステップの1つです。製品のコストと品質の両方が、操作シーケンスに密接に関連しています。実行される操作のシーケンスが異なると、操作時間、作業区への輸送時間が異なり、位置決め面とクランプ面が異なるため、工具が異なります。
製品用に新しいプラントが設置された場合、プロセスプランナーは目的に最も適した操作の順序を決定する際の自由度が大幅に高まります。既存プラントの場合、新製品の運転順序は、利用可能な設備と設備の積載状態に基づいて決定されます。後者の場合、プロセスプランナーに次の情報を提供する必要があります:
- 使用可能なマシンのリスト。
- 利用可能な汎用ツールのリスト。
- 機器の能力。
- 機械負荷チャート。
- 標準データ。
ただし、いずれの場合も、最適な操作シーケンスの計画で従わなければならない特定の基本原則があります。 。これらは:
1。 まず、データムサーフェスを慎重に選択する必要があります。 データムの選択 その後のすべての機械加工操作と検査に影響します。機械加工されていない面は、最初の機械加工操作の場合にのみ、最初の設定基準面として選択する必要があります。以降の操作では、機械加工されたサーフェスのみがセットアップデータとして機能します。
2。 機械加工によってワークの剛性がそれほど低下しない表面は、シーケンスの早い段階で機械加工する必要があります。
3。 内部操作は外部操作に先立って実行されます。これは、常に遵守する必要のある規則ではありません。主な理由 内部操作の実行 初期の段階では、マテリアルハンドリングやその後のプロセスで内面が損傷する可能性が低いため、内面はワークを保持するためのより良い手段を提供し、内径と外径の間の同心性を確保するのに役立ちます。
4。 シーケンスの操作は、金属の最大層を除去するから開始する必要があります。 。重いカットで厚い層を取り除くと、軽いカットよりもはるかに簡単に原材料(通常は鋳物や鍛造品)の内部欠陥が明らかになります。また、ワークピースは内部応力から解放され、その後の操作での反りの危険性を排除します。
ヘビーカットに関連する可能性のある大きな切削力とクランプ力は、同じワークピースの別の部分の仕上げ面の精度に影響を与え、荒加工を目的とした機械を必要とします。さらに、粗いまたは粗い仕上げを含む重いカットは、通常、細かい仕上げよりも安価な作業員でより速くなります。
5。 上記のように欠陥が明らかになったためにリジェクトの数が増えることが予想される操作は、マシンシーケンスの開始にできるだけ近いところで実行する必要があります。二次プロセスへの投資を最小限に抑えながら、欠陥のある材料に対してできるだけ早く作業が行われていることを確認することは常に有利です。
6。 仕上げ作業は、作業シーケンスの最後に実行して、仕上げ面に損傷を与えたり、部品の他の面を基準にして寸法や調整を変更したりする危険性を減らす必要があります。
7。荒削りと仕上げの操作 荒加工での重い負荷によって仕上げを目的とした機械の精度が妨げられないように、別々の機械で行う必要があります。
8。 検査段階 導入する必要があります(a) 荒削り後、(b) 他の店舗や部門で行われる作業の前に、(c) 面倒で重要な操作の前(たとえば、データムサーフェスを準備する前)とその後、および(d) ラス加工後。
9。 機械加工操作のシーケンスは、熱処理操作と調整する必要があります これらは機械部品の製造において非常に重要です。熱処理後の作業場の変形は、機械加工による部品の幾何学的形状の必要な修正のために、その後の操作のための機械加工許容量の増加を必要とします。
10。 マテリアルハンドリングは、原材料、仕掛品、完成品、梱包材、およびスクラップの処分に適用されるため、生産活動の必需品です。したがって、操作シーケンスとマテリアルハンドリング 密接に関連しています。これは、可能なコスト削減のための有利な領域であり、製造コストの大きな部分を占めます。したがって、現代の傾向は、実行可能な場合はいつでも処理システムを機械化することです。
11。 店舗内および処理中の材料の待機は、それらに関連するさまざまなコストパラメータが関係するため、可能な限り回避する必要があります。したがって、可能な限り、最小限のコストで使用場所に隣接して配置されます。 。
操作シーケンスは厳密ではありません。それは製品ごとに、そして同じ製品でも異なります。常に改善の余地があり、より良い方法を開発し、生産性を高め、コストを削減するために継続的に見直す必要があります。
プロセス計画シート
プロセスプランニングシートは、部品の製造に必要なさまざまな操作に関連するすべての情報が表形式でリストされている詳細レコードです。これは分析シートとも呼ばれます 、説明シート 、操作シート またはプロセス設計シート 。プロセスシートの例を表22.1に示します。
プロセスシートに示されている操作とその要素の説明は、実行する内容とその理由に関する非常に簡潔で包括的な情報を提供する必要があります。データは、仕事がどのように、何で行われるか、そして可能であれば、それに必要な時間の支出を明確に示す必要があります。
このようなシートの形状は、製造条件によって異なる場合があります。プロセスシートの特性は、主に生産規模と製造される製品の重要度に依存します。さらに、さまざまな種類のシートが、すでに稼働している製造コンセプトや新しいプラントを設計する組織で使用されています。
ただし、ほとんどの場合、次の情報がプロセスシートに記載されています:
1。 可能であれば、名前、図面、サービス機能を含むワークピースに関する情報。
2。 素材、ブランクとして使用した場合のストックのサイズ、キャラクターなどを含むブランクに関する情報
3。 操作の説明と数、およびそれらの要素の数。
4。 機械付属品、工具、補助装置などの製造装置に関する情報。
5。 説明、サイズ、コード番号などのジグ、フィクスチャ、ツールに関するデータ。
6。 設定時間、処理時間、加工時間などの標準時間の要素。
7。 各操作に対するワーカーのジョブレーティング。
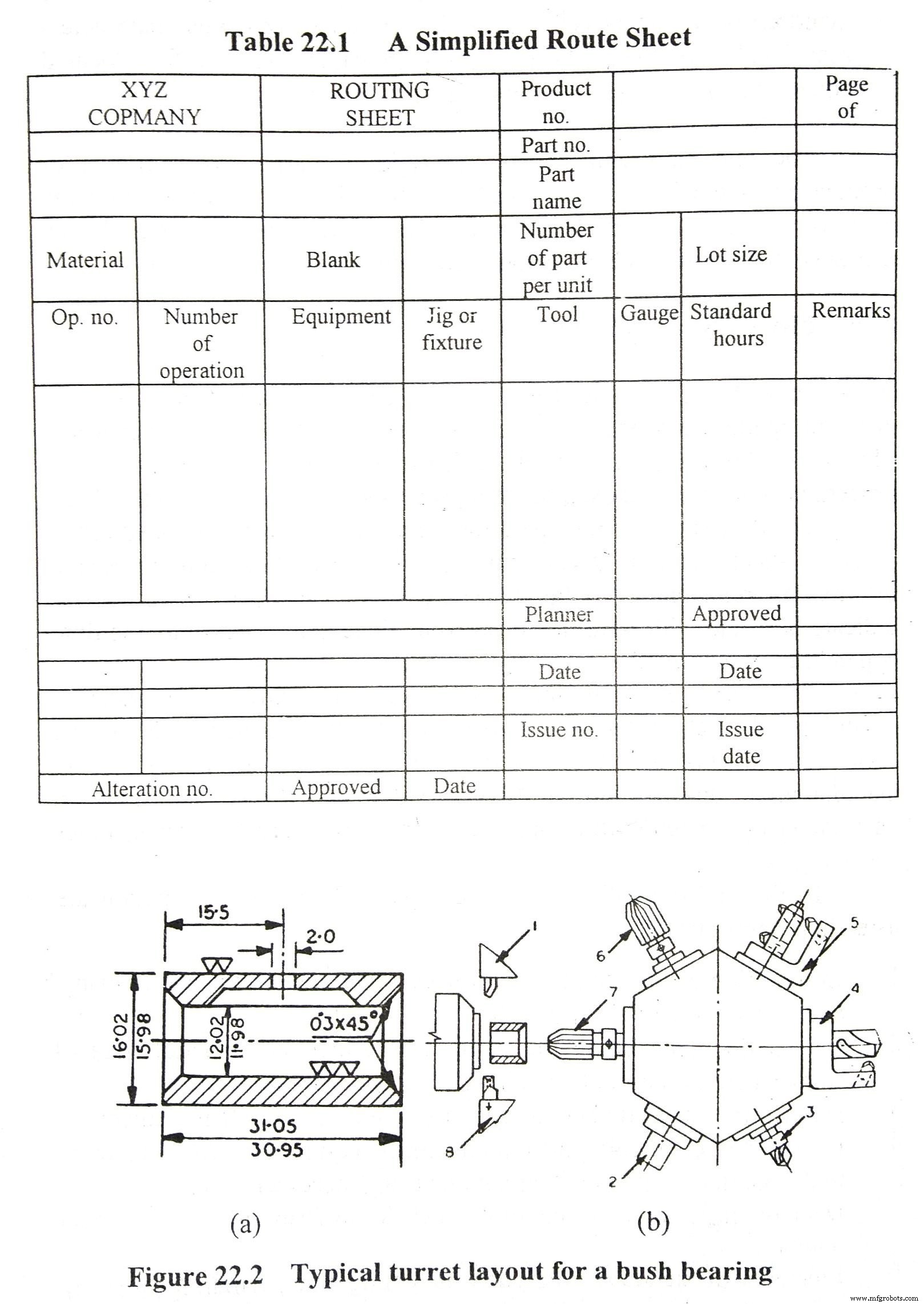
機械加工作業の製造工程を計画する際には、図1に示すように、さまざまな作業の作業スケッチが頻繁に描かれます。 22.2。希望する公差を与えるように機械加工される表面。
操作シーケンスの例
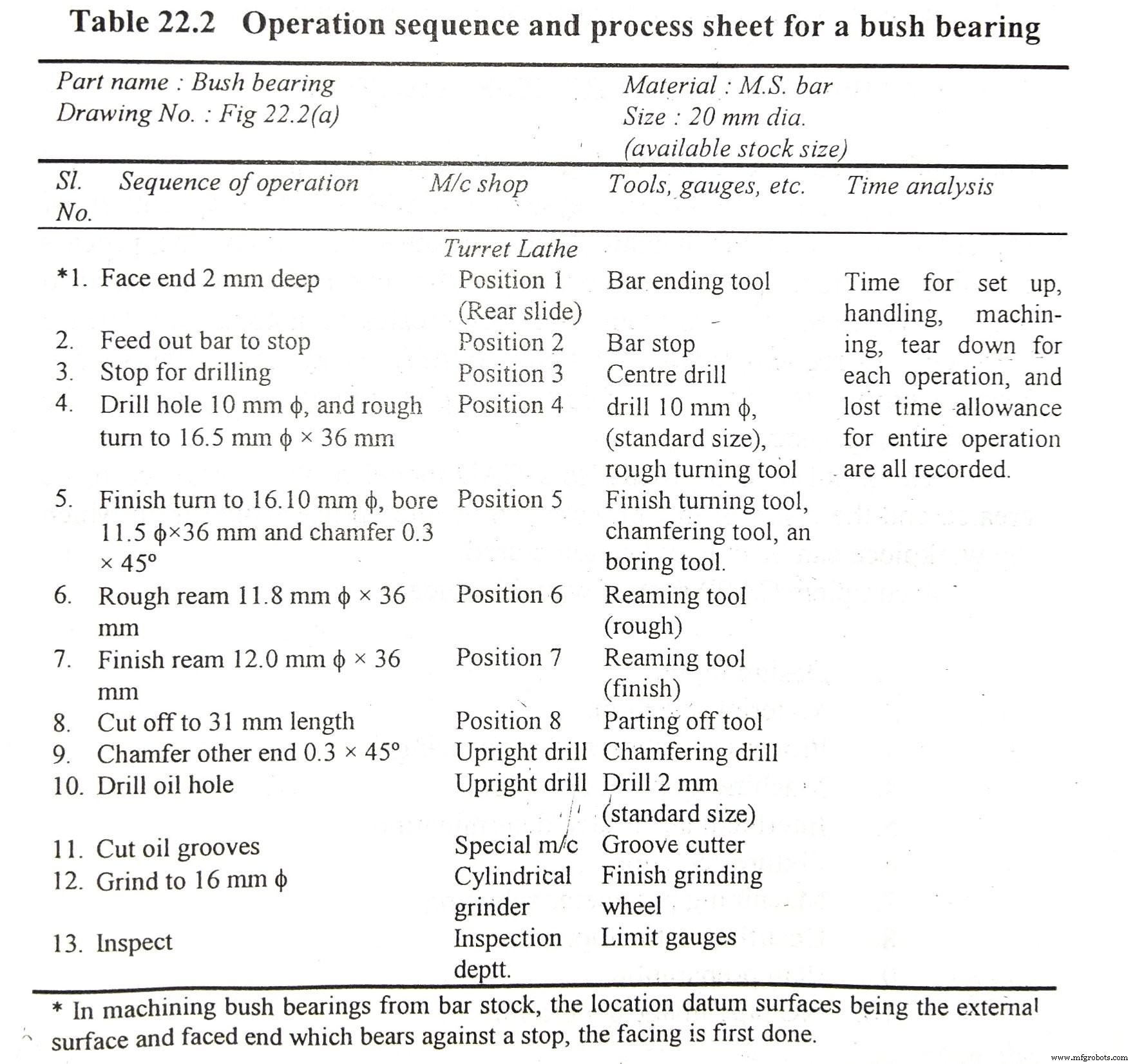
手動プロセス計画のデメリット
手動プロセス計画(MPP)には多くの欠点があります。それらは:
- MPPは主に主観的です。
- プロセス計画の品質は、計画担当者のスキルと経験に直接関係しています。
- プロセス変更の組み込みは非常に困難です。
- 技術的な変更またはバッチサイズの変更には、プロセス計画の変更が必要です。 MPPの応答は遅いです。
- プロセス計画が一貫していて最適化されているかどうかを確認することは困難です。最適化されていない場合は、過剰な工具と材料の要件が指定されます。
- 会社の大量のドキュメントから類似部品のプロセスプランを手動で検索するのは面倒です。
コンピューター支援プロセス計画
コンピューター支援プロセス計画 (CAPP)は、統合されたCAD/CAMシステムへの最も重要なリンクになっています。 CAPPは、人間のプロセスプランナーがプロセスプランニング機能を実行するのを支援するコンピューターのアプリケーションです。 CAPPはまた、一貫したプロセス計画を作成するために必要な時間と労力を削減するのではなく、コンピューター支援設計間の自動化されたインターフェースを作成するだけです。 (CAD)およびコンピューター支援製造 (CAM)製造システム内での完全な統合を実現します。
このプロセスの入力は、作成されるワークピースのCADモデルであり、このプロセスの結果は、ワークピースを作成/製造できる詳細なプロセス計画です。
完全なCAPPシステムには次のものが含まれます。
1。 設計入力。
2。 材料の選択。
3。 プロセスの選択と順序付け。
4。 機械と工具の選択。
5。 中間表面決定。
6。 フィクスチャの選択、
7。 加工パラメータの選択。
8。 コスト/時間の見積もり。
9。 計画の準備。
10。 NCテープ画像の生成。
自動化されたプロセス計画への2つの基本的なアプローチは次のとおりです。
1。 バリアント、および2。 ジェネレーティブ
1 。バリアントメソッド
バリアントメソッド: バリアントプロセスプランニングは、コンポーネント(パーツ)間の類似性を調査し、データベースを検索して、コンポーネントが属するパーツファミリの標準プロセスプランを取得します。計画は、新しいパーツに適した計画を作成するために取得および変更されます。
バリアントアプローチでは、プロセスプランは2つの運用段階で生成されます。彼らです :
1。 準備段階と2。 生産段階。
準備ステージマーク>
準備段階 既存のコンポーネントはコード化され、分類され、パーツファミリにグループ化されます。分類とコーディングは、パーツ間の類似性を識別するための比較的簡単な方法を提供します。その後、同様のパーツをクラスター化することにより、パーツファミリーを形成できます。
さまざまな成文化スキームが確立されています。 MICLASS、DCLASS、OPITZ、CODEは、分類スキームの一部です。パートファミリーが形成された後、各ファミリーには標準プランが割り当てられます。標準計画は、部品を製造するための一般的な一連のプロセスを表す一連の機械加工プロセスで構成されます。
プロダクションステージマーク>
本番段階 着信コンポーネントは、その幾何学的特徴または処理要件に基づいてコード化されます。準備段階で使用されたのと同じ成文化スキームがここでも利用されます。結果のコードは、パーツがパーツファミリに割り当てられる基礎として使用されます。
コーディングシステムが効率的に利用されている場合、そのパーツはそのファミリに属する他のパーツと同様である必要があります。新しい部品のプロセス計画は、データベースから取得した(新しい部品が属する部品ファミリの)標準計画を変更することで取得できます。
2 。生成方法
生成方法: Generative Computer Aided Process Planning(GCAPP)は、新しいコンポーネント(パーツ)のプロセスプランを作成するために、製造情報を統合します。決定ロジックと最適化方法はシステム自体にエンコードされているため、プロセス計画における人間の相互作用は最小限に抑えられるか、まったくありません。
生成システムは、設計図またはCADファイルから完全なプロセスプランを作成します。
GCAPPシステムの3つの領域は次のとおりです:
1。 CADファイルによるコンポーネント定義。部品の機能と仕様が含まれています。
2。 プロセスプランナーの知識の識別、取得、および表現。これは、プロセスの選択、順序付けなどについてプロセスプランナーが下した決定の理由を考慮に入れています。
3。 プランナーのロジックの互換性
GCAPPでは、設計仕様がシステムに入力されます。決定ロジックは、部品のストック材料と機械加工機能を認識します。さらに、最適なフィクスチャのタイプと場所とともに、最適な操作シーケンスを決定します。
ジェネレーティブコンピュータ支援プロセス計画のデメリット
GCAPPシステムでは、次の欠点が見られます。
1。 現在までの限定使用。必要な情報(公差など)は通常、CADモデルでは利用できません。
2。 供給されるさまざまな種類の部品すべてを処理できるようにするには、システムに多くの知識を追加する必要があります。
3。 アルゴリズムが非常に複雑で計算に多大な労力がかかるため、一部のシステムは特定のタイプのジオメトリの計画の作成に特化しています。いくつかのシステムは、部品の製造可能性をチェックし、必要に応じて設計の変更を提案するところまで行きます。
これまで、プロセス計画のステップ、定義、タイプ、アクティビティのシーケンス、さまざまなタイプのプロセス計画の長所と短所について学習しました。この記事をお友達と共有し、以下のコメントでフィードバックをお寄せください。
産業技術