単純な原理–Y軸分離の背後にある秘密
ターニングセンターに回転工具を追加すると、1台のマシンで複数のセットアップを組み合わせて、より合理化された生産的な加工プロセスを実現できます。これを達成するために、1990年代にターンミルマシンが導入されました。最初のアイデアは、タレットの1つまたは複数の工具位置でフライス、ドリル、またはねじ切りタップを駆動して、極補間の制限やその他の関連するプログラミングの問題を解消できるようにすることでした。
リーチを改善するために、回転ツールをスピンドル面全体に移動するための一連の方法が追加されました。これは、リボルバーの側面またはその面にツールを取り付けるか、傾斜したベッドにY軸ウェイを取り付けるか、独立したミリングヘッドを使用することによって実現されました。工作機械メーカーとメーカーの両方が、フライス盤と旋盤の両方の操作を統合することの利点をすぐに認識しました。
今日、Y軸オプションは、ほとんどのマルチタスクマシンでは標準機能になり、多くの新しいターニングセンターではオプションになっています。
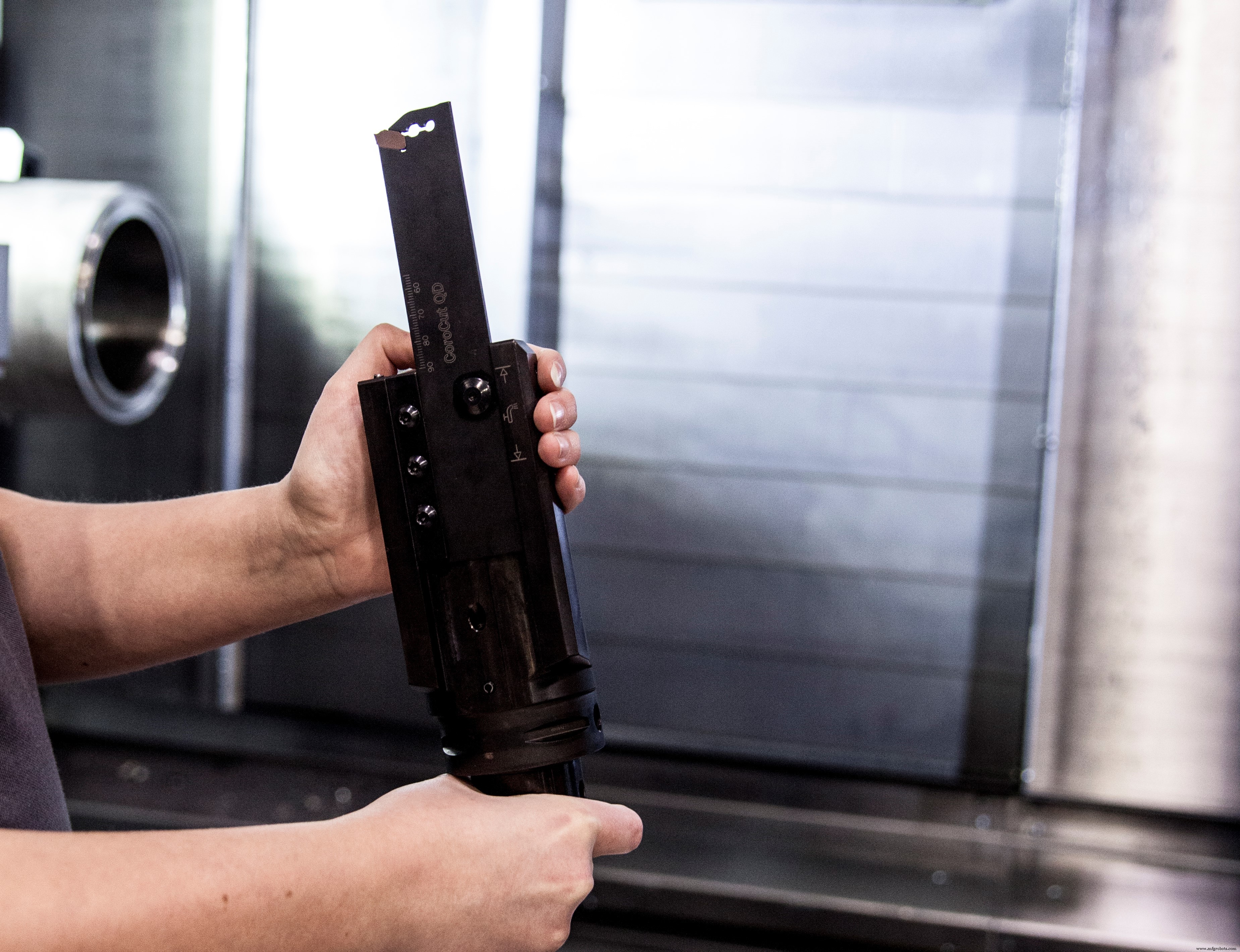
工具の破損により、コストのかかる機械のダウンタイムや部品の廃棄につながる可能性があるため、製造業者がセキュリティを妥協しない機械加工プロセスの段階です。これらのタイプのツールに対する高い要求を満たすために、システムCoroCut®QDは2013年にサンドビックコロマントによって開発されました。この高性能システムをさらに改善する方法を検討しながら、ツール開発者はY-を使用してこれらの最新のマシンを検討し始めました。軸容量。これにより、ツールの設計だけでなく、まったく新しい方法であるY軸パーティングを含む革新がもたらされました。
CoroCut®QDを使用したY軸の分割のデモンストレーションについては、この短いビデオをご覧ください。
Y軸パーティングの原則
Y軸の分離の背後にある原理は信じられないほど単純です。従来のパーティングオフツールは工作機械のX軸に位置合わせされていましたが、Y軸ツールはY軸に位置合わせするために反時計回りに90°回転しただけです。従来の工具構成では、比較的長くて細いパーティングブレードとホルダーが90°の角度で回転するワークピースに供給されます。最大の切削抵抗は切削速度によって生成され、残りは送り動作によって生成されます。
その結果、合力ベクトルが約30°の角度でツールに斜めに向けられます。つまり、ブレードの非常に弱い部分を横切るようになります。ツールの破損を防ぐために、これはブレードの張り出しを減らし、ブレードの高さを上げることで補われます。これにより、ツールの使いやすさが損なわれることがあります。
チップシートを90°回転させてY軸を利用することにより、工具は基本的に前端でワークピースに侵入できます。これにより、得られる切削力ベクトルがブレードの縦軸とほぼ一致します。 Sandvik Coromant R&Dチームが実施したFEM解析により、新しいソリューションが重大な応力を排除し、従来のブレード設計と比較してブレードの剛性を6倍以上向上させることが確認されました。
簡単に言うと、Y軸平面でのパーティングに切り替えると、切削抵抗の有益な方向が得られ、不安定性や振動が少なくなります。これは、安定性を失ったり、ツールを壊したりすることなく、非常に安全で生産的な分離プロセスのために送り速度を上げることができることを意味します。そのように簡単です。
ここからY軸分離の5つの理由を示すサンドビックの便利なインフォグラフィックのPDFをダウンロードしてください 。
産業技術