計画的なダウンタイムを管理するための途方もなくシンプルなガイド|スケジュールされたダウンタイム
予防保守は、多くの利点をもたらすと同時に、実装が信じられないほど難しくも費用もかからないため、最も一般的な保守戦略です。
そうは言っても、予防保守には欠点があります。
最もよく言われる反対意見の1つは、それを実装すると、過度のメンテナンスを行うことになるということです。言い換えれば、技術者は、(まだ)そのレベルの注意を必要としない可能性のある不要な検査や資産に時間を浪費することになります。
もう少し深く掘り下げると、これがより重大な問題につながることがわかります。アセットに対して予防作業を行う場合、多くの場合、そのアセットを最初にシャットダウンする必要があります。翻訳では、計画的なダウンタイムをスケジュールする必要があります。
生産のピーク時や、まだ実行する必要のないメンテナンス作業のために資産をシャットダウンすることは誰も望んでいないため、これらの課題を考慮し、スケジュールされたダウンタイムを最小限に抑えるメンテナンススケジュールを作成する方法を見てみましょう。
計画されているダウンタイム|予定されているダウンタイム?
簡単に言えば、計画的なダウンタイムとは、資産をシャットダウンする必要がある、スケジュールされたメンテナンスとアップグレードのために予約する期間です。
プロアクティブなメンテナンスは本番環境にとって重要な重要な資産に対して行われることが多いため、修理/検査/アップグレードが完了するまで通常の本番環境の運用を一時停止する以外に解決策はありません。
組織は、夜間シフト中(またはマシンが使用されていないとき)にメンテナンスをスケジュールすることにより、これらの問題を回避しようとしています。ただし、メンテナンス部門が夜間シフトを実行していない場合、または24時間年中無休の生産サイクルがある場合、計画されたダウンタイムをスケジュールする適切な時間を見つけることは、非常に複雑で、非常に高速になる可能性があります。
クイックノート:この記事の残りの部分では、「計画的ダウンタイム」と「計画的ダウンタイム」という用語は、実際には同じものを指すため、同じ意味で使用します。
計画的および計画外のダウンタイム
計画的ダウンタイムと計画外ダウンタイムの違い 自明です。ダウンタイムを計画する時期はあなたが決定し、休憩をとる時期はMACHINESが決定します。そして、それがあなたのスケジュールに合っているかどうかをわざわざ尋ねることはありません。
冗談はさておき、計画外のダウンタイムにつながる予期しない機器の故障は、非常にコストがかかる可能性があります 、これが、多くの企業が事後対応型から予防型保守に切り替えている主な理由の1つです。 。
計画的メンテナンスと計画外メンテナンスにどれだけの時間を費やすかを知ることは不可欠であるため、Limbleが追跡している多くのことの1つです。
Limbleを使用して、計画されたメンテナンスタスクに費やした時間と、予期しない問題に対応するために費やした時間を追跡する方法の例を次に示します。
生産速度と生産量への影響を最小限に抑えて適切なメンテナンスを実施できるように、計画的なダウンタイムをスケジュールする方法を見てみましょう。
計画的なダウンタイムを管理する方法
#1)制作を理解する
年間を通じて、あなたはおそらく日々の生産で衰退と流れを持っているでしょう。実行している各マシンを把握し、さまざまな季節が生産サイクルにどのように影響するか、ひいてはマシンの日常的な使用にどのように影響するかを識別します。
生産のピーク時には、収益に最も影響を与えない最適な時間を見つけるように計画します。準備する時間を見つけることは、時間外を意味するかもしれません。 24時間年中無休のショップを経営している場合、それは1日の中で最も遅い時間を意味する可能性があります。
重要なのは、生産がいつ減速し、いつ計画どおりに加速するかを知ることです。
#2)CMMSで過度のメンテナンスを減らす
メンテナンス計画を成功させるための主な方法の1つは、さまざまなソースにわたる大量の情報を整理、管理、追跡できることです。
最新のCMMS そのすべてのデータを追跡して理解するのに大いに役立ちます。
リアクティブメンテナンスを73.2%削減
ケーススタディ
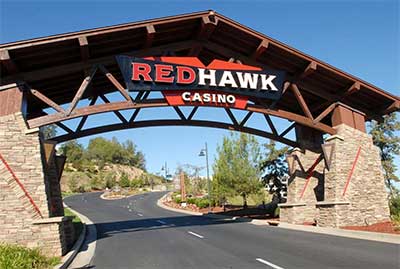
CMMSで行うことのほんの一部を次に示します。
- マシンのパフォーマンスと資産の履歴を記録する
- すべてのタスクの進行状況を追跡する(作業指示書を読む)
- すべての在庫とスペアパーツの使用状況を追跡する
- 技術者のパフォーマンスを追跡する
- 完全な予防保守スケジュールをスケジュールして監視する
このすべてのデータを自由に使用できるようにすることで、過度のメンテナンスを減らすことができます。 :
- それを処理できる資産の保守作業の頻度を減らす
- 診断とチームのコミュニケーションをスピードアップすることで、ダウンタイムイベントの長さを短縮します
- 必要なときにすべてのスペアパーツを利用できるようにする
- 一般的によく組織された保守部門を持っている
CMMSの詳細については、CMMSシステムとは何かとその仕組みガイドをご覧ください。
#3)メンテナンス計画の焦点を絞ります
メンテナンススケジュールをどこから開始するかを知るための優れた方法は、すべての資産を一覧表示し、それらにランクを割り当てることです。当たり前のように思えるかもしれませんが、工場で最も優先度の高いマシンを知っていると、北になります。
重要なマシンをリストしたら、日常のメンテナンスに含める必要がないほど二次的な可能性のあるマイナーアセットをリストします。
たとえば、個々のマシンは、使用する際の負担が少なくなります。オイルや潤滑剤は必要ないかもしれません。他のデバイスは他のデバイスよりも関与が少なく、可動部品がはるかに少ない可能性があります。
いずれにせよ、特定のマシンは全体的なメンテナンスが少なくて済みます。また、どのマシンがこのカテゴリに該当するかを明確にする必要があります。結局のところ、多くの場合、すべてのマシンを予防保守計画に入れる価値はありません。
上記のすべてに加えて、各メンテナンスタスクがどのくらい続くべきかを理解する およびマシンの使用が最も少ない場合 効果的な予防保守計画を作成するには非常に重要です。 計画されたダウンタイムを最も適切なタイミングでスケジュールできるようにします。
#4)明確に定義されたSOPを持っている
標準的な操作手順を明確に定義している 頻繁に繰り返す必要のあるすべての操作は、メンテナンス操作を合理化するための優れた方法です。
計画的なダウンタイムは合理的に定期的にスケジュールする必要があるため、明確なガイドラインがあると、技術者は作業をより迅速に実行できます。つまり、資産が作業に戻るまでの時間が短縮されます。
速度と品質に注意してください 実行されたメンテナンス作業のうち、同様に重要 。スケジュールされたダウンタイムを最小限に抑えることは良いことですが、不十分なメンテナンス作業はほぼ確実に計画外のダウンタイムの増加につながります。
そして、計画外のシャットダウンや停止の1日よりも、さらに2時間の予定されたダウンタイムの方がはるかに許容できることに同意できると思います。
#5)ボトルネックを理解する
配達が頻繁に遅れると、必要なスペアパーツの在庫を維持するのが難しくなりますか?一部の上級保守技術者は退職したか会社を辞めたので、経験とトレーニングが不足している若いチームと一緒に働いていますか?多くの注意が必要で、予期せず故障したい古い資産を使用していますか?
予防保守のために計画されたダウンタイムを最小限に抑えるという観点から、スペアパーツ 、経験の浅い/熟練していない技術者 、および老朽化した資産 スケジュールする必要がある最も一般的な3つのボトルネックです。
良いニュースは、これらのボトルネックは、少しの回避策と先見性で回避できることです。
スペアパーツがすぐに届かない場合は、早めに注文するか、可能であれば新しいプロバイダーに切り替えることを検討してください。
経験の浅い技術者がいることがわかっている場合は、次のことができます。
- 経験豊富な同僚とペアを組む
- 先ほど話したSOPが明確に定義されている
- 必要なトレーニングを提供する
- より厳格な採用プロセスがあります
そして最後に、老朽化した資産を説明する方法を見つける必要があります。ほとんどの場合、これは、これらの資産が非常に面倒であり、多くの予定外のダウンタイムの原因となる可能性があるため、これらの資産に特別な注意を払う必要があることを意味します。それを行うことができるいくつかの方法は次のとおりです:
- 資産履歴を注意深く追跡して、一般的な故障パターンを推定し、計画されたダウンタイム中にそれらに対処できるようにします
- アセットの機能中に実行できる追加の検査をスケジュールする
- センサーをインストールして状態ベースの監視を実行
#6)効果的なコラボレーションにより、スケジュールされたダウンタイムの期間を短縮します
保守担当者とやり取りする部門は同じページにあり、定期的な調整と修理を調整する必要があります。計画されたすべてのシャットダウンのメンテナンスチームがどこにいるのかを全員が理解している限り、機械のオペレーター、清掃スタッフ、およびその他の作業者は、必要な作業のみに集中してダウンタイムを最小限に抑えるように環境の準備を開始できます。
逆のことが起こり、部門間のコミュニケーションが不十分な場合、発生する可能性のあるさまざまなミスや事故を想像するのは難しくなく、資産がスタンバイに費やす時間を長くします。
計画されたシャットダウンが生産の遅延を引き起こした理由として、不十分な組織とコミュニケーションを許可しないでください。
計画的なダウンタイムをいつスケジュールしますか?
施設のメンテナンスマネージャーとして、施設で計画されたダウンタイムをスケジュールする適切な時間を見つけることができるのはあなただけであることは明らかです。
そうは言っても、役立つヒントがいくつかあります。
- 営業時間後に計画されたメンテナンス作業をスケジュールする
- 主要な休日の直前
- 予想される悪天候の前
- 2年に1回、停電をシミュレートし、すべての重要な機器を一度にテストします
詳細な説明については、計画的なメンテナンスをいつスケジュールするかについて説明しているゲスト投稿を確認してください。 。
すべては事前の計画です
ご覧のとおり、十分な計画と編成があれば、計画されたメンテナンス中のダウンタイムを大幅に最小限に抑えることができます。
生産のピークシーズンであろうと、1年で最も遅いシーズンであろうと、組織化され、正確なメンテナンススケジュールを設定することで、生産が最高レベルで実行され、マシンがピークの動作状態にあることが保証されます。
Limbleが計画されたダウンタイムに費やす時間を最小限に抑えるのにどのように役立つかを完全に調査することに興味がある場合は、以下にコメントを残すか、メッセージを送信してください 。
機器のメンテナンスと修理