二光子重合によるギャップサイズが100nm未満の高分解能周期構造のナノファブリケーション
要約
この論文では、2光子重合(2PP)によってサブ100nmスケールでギャップサイズを持つ高解像度の周期構造を実現するためのアプローチが提示されます。フィーチャサイズと表面品質に対するレーザー強度の影響を調査します。構造形成に対する異なる感光性材料の影響を比較します。ボクセルの楕円幾何学的特性に基づいて、著者は、ガラス基板に対するレーザーの焦点位置を制御することにより、100nm未満の特徴サイズを備えた高解像度構造を実現するというアイデアを提示します。この調査は、ボクセルの主軸に沿った平面と垂直な平面でそれぞれ製造された構造を対象としています。著者らはまた、周期距離が200 nm、ギャップサイズが65nmの提案された周期構造の製造を管理するための有用なアプローチを提供しています。
はじめに
近年のナノテクノロジーの継続的な進歩に伴い、デバイスのダウンスケーリングに対する需要は急速に高まっています。回折限界未満の特徴サイズを持つ小型化された構造は、プラズモニクス[1]、マイクロおよびナノオプティクス[2]、ナノフォトニクス[3、4]、生物医学[5、6]などのさまざまな分野に適用できます。さらに、サブ波長寸法の構造は、マイクロスケールおよびナノスケールでの特性評価のパフォーマンスを促進することもできます[7、8]。たとえば、チップ[9]とナノアンテナ[10]は、近接場での光の閉じ込めを強化することで高解像度構造の特性評価性能を向上させるために使用でき、グレーティング[11]は近接場からの光学情報を変換できます。フィールドからファーフィールドへ。
高解像度構造の実現に関しては、2光子重合(2PP)が、高解像度と3D製造を実現する能力のために広く利用されています[12]。二光子重合は、二光子吸収(2PA)に基づく製造方法であり、理論的には回折限界未満の分解能を達成できる非線形プロセスです。高い開始効率で光開始剤を追加する[13]、非活性化ビームの空間位相を形成する[14]、サブ10 fs [15]および520nmフェムト秒レーザーパルスを使用する[16]、組み合わせなど、さまざまな2PPベースの方法ハイブリッド光学系[17]と開発されたサブ回折光ビームリソグラフィー[18]を使用して、サブ100nmスケールのフィーチャサイズを実現しました。ただし、これらのサイズは、ほとんどの場合、中断された回線または単一の回線で実現されます。隣接するフィーチャ間の中心間距離が非常に近くなると、ギャップ領域でのラジカル拡散交換効果により、周期構造の回折限界を超えるフィーチャサイズとギャップサイズを実験的に実現することは依然として困難です[19]。それにもかかわらず、ナノスケールのギャップ距離で周期構造を実現する目的で、いくつかの戦略が実証されました。フォトレジストにクエンチャー分子を添加することにより、周期距離400nmのフォトニック結晶を実現しました[20]。このアプローチでは、フォトニック結晶の隣接する線の間のギャップサイズは約300nmです。さらに、周期距離が175 nm、ギャップサイズが75 nmのグレーティングラインが、STEDリソグラフィー技術によって実現されました[19]。最近、煆焼によるサンプルの単純な熱後処理プロセスが、約85nmまでのフィーチャサイズを実現できることが発表されました[21]。上記のアプローチは、回折限界未満のギャップサイズを有する周期構造の実現を可能にした。ただし、2PPと比較すると、コストが高く、操作と手順が複雑であるため、非常に特殊です。
本論文では、2PPを用いた回折限界以下の特徴サイズとギャップサイズの両方を備えた周期的デバイス(図1)の実現に関する実験的調査を行った。ピラーが周期的に配置された格子線で構成される高解像度の周期構造は、マイクロとナノ構造。構造の空間分解能は、主に感光性材料、光学系、および処理パラメータによって決定されることが知られています[15]。具体的には、研究者は、レーザービームの偏光の向きが構造の寸法に影響を与える可能性があることを報告しています[24]。レーザーがその走査方向に平行に直線偏光されるとき、最小の特徴寸法を実現することができます。したがって、実験で使用したレーザーは、より小さなフィーチャサイズを取得するために、レーザースキャン方向に平行な直線偏光を備えています。この構成に基づいて、フィーチャサイズに対するレーザー強度の影響が最初に調査されます。次に、構造形成に対する異なる感光性材料の影響を比較します。レーザーがガラス基板上に構造を直接書き込む場合、ボクセルの他の部分はガラス基板の内側にあるため、ボクセルの一部のみがフォトレジストを重合します。ボクセルの楕円幾何学の恩恵を受けて、ガラス基板に対するレーザーの焦点位置を制御することにより、フィーチャサイズとギャップサイズを縮小するというアイデアが特別に提示されます。相対的なレーザー焦点位置に応じた格子線(ボクセルの主軸に垂直な平面で製造される)およびピラー(ボクセルの主軸に沿った平面で製造される)の特徴サイズがそれぞれ調査される。その結果、最小幅78nmのグレーティングラインと直径110nmのピラーが実現されています。さらに、20×20 μの面積サイズの提案された構造 m、周期距離200 nm、ギャップサイズ65 nmは、格子線とピラーを別々に製造することによって示されます。
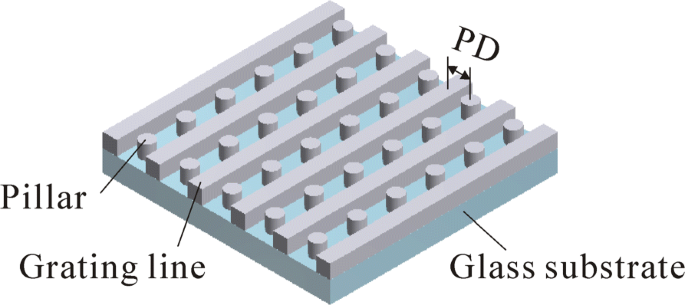
提案された周期構造の概略図。隣接するフィーチャ間の周期的な距離は、 PD で表されます。
メソッド
製造方法
この論文で提示された構造は、二光子重合を使用して製造された。実験装置の概略図を図2に示します。この2PP製造システムは、市販されており[25、26]、すべての軸を同時に調整し、ステッピングやスティッチングなしで全移動範囲にわたって速度に到達できます。最大50mm / sの速度で。 513 nmで出力が2倍になり、パルス幅が60 fs、繰り返し周波数が76MHzの直線偏光フェムト秒レーザーが使用されます。レーザー出力は、半波長板と偏光ビームスプリッターキューブによって制御されます。移動距離15cmの高精度エアベアリング並進ステージも採用。オンラインモニタリング用にCCDカメラが搭載されています。重合によって引き起こされるフォトレジストの屈折率の変化により、CCDカメラで重合プロセスを監視できます。サンプルは、ガラス基板上の感光性材料の液滴で構成されており、裏面にフォトレジストが付いた平行移動ステージに固定されています。レーザービームは、開口数(NA)が1.4の高い100倍の油浸顕微鏡対物レンズによってフォトレジストに集束されます。

2PP製造システムの概略図
資料
構造製造におけるさまざまなフォトレジストの性能は、独自の化学組成と物理的特性により多様化する可能性があります。この作業では、ゾルゲル有機無機Zrハイブリッド材料[27]およびE-shell 300(Envisiontec)と呼ばれるフォトレジストがそれぞれ構造化に適用されます。 Zrハイブリッド材料は、2PP製造での低収縮性と高安定性でよく知られている、高粘度のジルコニウムベースのゾルゲル有機無機ハイブリッドポリマーです。このフォトレジストの調製手順およびその他の光学特性は、参考文献[27]に記載されています。 E-shell 300は、粘度339.8 MPa・sのジメタクリレートベースの液体フォトレジストです。補聴器や医療機器の3D印刷や製造、および高解像度、強度、剛性、耐薬品性を備えた構造物に使用できます。
結果と考察
処理パラメータは、構造のフィーチャサイズを決定する上で重要な役割を果たします。その中で、レーザー強度は、構造形成に効果的に影響を与えることができ、正確かつ便利に制御できる1つのパラメーターです。このパラメータは、参考文献[28]
に記載されている式を使用して取得できます。 $$ {I =\ frac {2 P T M ^ {2}} {\ pi w_ {0} ^ {2} f \ tau}} $$(1)ここで P 平均レーザー出力を表します[4、28]、 T 目的/システムの透過係数( T =15 % [4])、 M 2 M によるビーム品質 2 =1.1、 f 繰り返し率、τ パルス幅、および w 0 \(w_ {0} =0.61 \ frac {\ lambda} {NA} \)( w のスポット半径 0 ≈223.5nm)。この式で、\(\ frac {P} {f} \)と\(\ frac {P} {f \ tau} \)は、それぞれパルスあたりのエネルギーとパルスあたりの平均電力を示します。強度単位kW / μ m 2 TW / cm 2 の代わりに使用されます (1 TW / cm 2 =10 kW / μ m 2 )スポット領域に実際にどれだけの電力が集中しているかを簡単に表示するために、マイクロスケールの範囲もあります(\(\ pi w_ {0} ^ {2} \ approx 0.16 \)μ> m 2 )。ここでは、単一線の寸法に対するレーザー強度の影響について調査しました。 Zrハイブリッド材料とEシェル300の両方が研究に適用されました。レーザー強度 I に対する両方の材料で作られた線の幅と高さ 図3a(Zrハイブリッド材料)と図3b(Eシェル300)にそれぞれ示されています。 7 μの速度 製造にはm / sを使用しました。レーザー強度 I 0.67〜0.78 kW / μの範囲にあります m 2 (対応するレーザー出力範囲1.44〜1.69 mW)Zrハイブリッド材料および0.78〜1.02 kW / μの場合 m 2 E-shell 300の場合(レーザー出力範囲1.69〜2.20 mW)。レーザー強度の増加に伴い、フィーチャサイズ(直径と高さの両方)が大きくなることがわかります。 Zrハイブリッド材料の場合(図3a)、レーザー強度は約0.67 kW / μです。 m 2 、ボクセルの横方向の寸法は約115 nmに縮小できます。これは、回折限界(回折限界\(\ frac {\ lambda} {2NA} =185 \)nm)を下回っています。アスペクト比(高さ対幅)が2.5〜4の範囲にあることも計算できます。 E-shell 300(図3b)の場合、レーザー強度が0.78 kW / μのときに178nmの線幅が実現されました。 m 2 。このフィーチャーの寸法は、回折限界(185 nm)を下回っています。上記の調査に基づいて、フィーチャサイズは適用されるレーザー強度によって効果的に影響を受けると結論付けることができます。レーザー強度を下げることで、より小さなフィーチャサイズを実現できます。
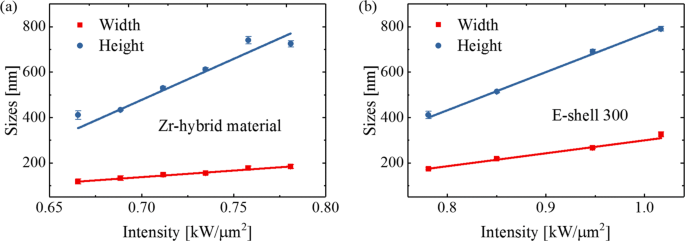
線の寸法とレーザー強度の関係 I 。構造化に使用される速度は7 μです。 MS。赤と青の線は、それぞれボクセルの幅と高さの線形フィットの結果です。 a Zrハイブリッド素材で作られた一本の線の幅と高さ。 b E-shell300で作られた1本の線の幅と高さ
2PPによる構造形成に対するさまざまな材料の影響
材料が構造形成に与える影響を調査するために、「材料」のセクションで紹介した材料を使用して、さまざまな周期的な格子線を作成しました。書き込み速度7 μ m / sが適用されました。図4aとbは、それぞれZrハイブリッド材料とEシェル300で作られた周期的距離( PD )の周期的格子線のSEM画像です。 、1 μの図1)に示されています m。製造に適用されたレーザー強度は1.25kW / μでした m 2 (レーザー出力2.7 mWに対応)Zrハイブリッド材料および1.02 kW / μの場合 m 2 (レーザー出力2.2mWに相当)E-shell300の場合。両方の材料で作られた格子線が滑らかであることがわかります。図4cおよびdは、Zrハイブリッド材料と P を備えたEシェル300で作られた周期的格子線のSEM画像を示しています。 D =400 nm、それぞれ。周期的な距離が短くなると、製造に使用されるレーザー強度も低下し、高解像度を実現すると同時に、隣接するフィーチャ間のスペース内での過剰重合を回避します。この調査では、0.69 kW / μのレーザー強度 m 2 両方の材料での製造に適用されました。 PD を減らして 、Zrハイブリッド材料で作られた格子線は粒子が粗く(図4c)、Eシェル300で作られた格子線は粗さが少なくなっています(図4d)。 Zrハイブリッド材料で作られた格子線の粒状性は、不安定な重合に起因する可能性があります。これは、材料の重合しきい値にレーザー出力が近接しているために発生します。この比較により、E-shell300がナノスケールの周期的距離を持つ構造の製造に適していることがわかります。さらに、SEMで観察されたすべての構造には、厚さ20nmの金の層が堆積しています。
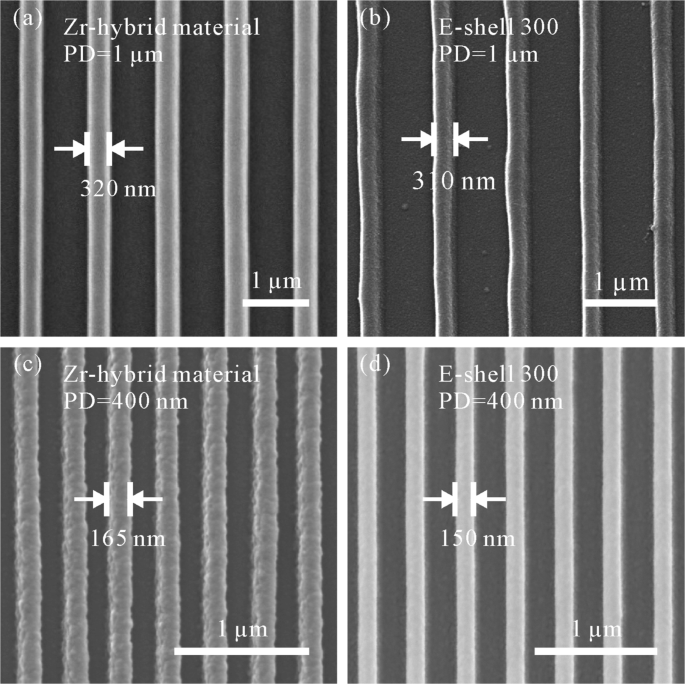
異なる材料で製造された格子線のSEM画像。製造速度は7 μです。 MS。 a 材料:Zr-ハイブリッド材料; P D =1 μ m;レーザー強度:1.25 kW / μ m 2 。 b 材質:Eシェル300; P D =1 μ m;レーザー強度:1.02 kW / μ m 2 。 c 材料:Zr-ハイブリッド材料; P D =400 nm;レーザー強度:0.69 kW / μ m 2 。 d 材質:Eシェル300; P D =400 nm;レーザー強度:0.69 kW / μ m 2
レーザー焦点位置に関する構造形成の調査
ガラス基板の表面にナノ構造を配置するには、2PPプロセス中にレーザービームを基板/フォトレジスト界面に集束させる必要があります。したがって、ボクセルの一部のみがフォトレジストの重合を開始することができます。ボクセルの他の部分は、構造物の接着を確実にするためにガラス基板にあります。ボクセルの形状は楕円形であるため、その断面サイズのバリエーションが主軸に沿って存在します。高解像度のマイクロおよびナノファブリケーションでは、基板とフォトレジストの界面でのボクセル断面サイズの変動が、構造形成とその特徴サイズに影響を与える上で非常に重要です。
図5は、 z に沿ったレーザー焦点調整の概略図です。 方向。フォトレジストと基板の間の界面の位置は、基準焦点位置 z として定義されます。 0 (図5a)。フォトレジスト液滴はガラス基板の下側にあるため、レーザーフォーカススポットは基準位置 z から下に移動します。 0 フォトレジストに。現在のレーザー焦点位置間の距離 z および基準位置 z 0 Δ z で表されます =∣ z − z 0 ∣。図5bおよびcで濃い緑色で示されている領域は、フォトレジスト内のレーザー焦点領域を表しており、重合しきい値を超える光強度での重合を可能にします。レーザーフォーカスをさまざまな z に配置することで、さまざまなフィーチャサイズを実現できます。 位置。フィーチャーサイズ w は、同じ z で製造されたフィーチャーの平均半値全幅(FWHM、図5c)によって特徴付けられます。 1つの配列内の位置。
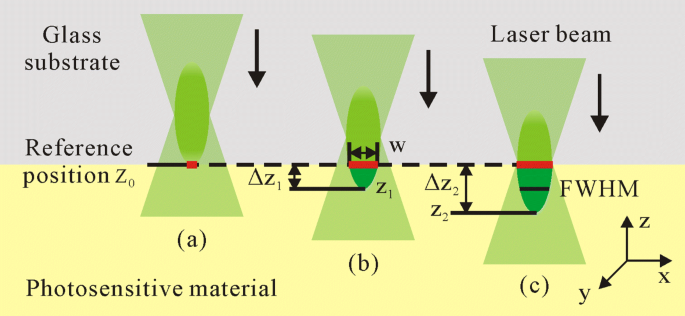
z に沿ったレーザー焦点位置の変化の図 方向
図6に示すように、異なるレーザー焦点位置で製造された周期的格子線が得られました。周期的距離( PD )格子線の間は1 μです m。この近くで PD 、レーザーがΔで集束されると、隣接するフィーチャがギャップ領域での余分な重合によって相互に接続し始めます。 z =500 nm(図6a)。格子線からのクラスターは、追加の重合から生じます。 2PPプロセス中に、光開始剤分子のレーザー誘起結合開裂によってフリーラジカルが生成されます。これらのラジカルは、隣接するフィーチャ間の小さなギャップに蓄積され、その結果、ラジカル濃度が増加します。この高いラジカル濃度は、重合閾値を超える可能性があり、したがって、望ましくない重合を引き起こす可能性がある。さらに、基板への重合構造の不安定な接着も生じる可能性があります。この場合、構造は開発プロセス中に簡単に洗い流されます。レーザービームの焦点が基板の内側にあるほど、重合するフォトレジストは少なくなります。図6bに示すように、この場合、幅78nmのグレーティングラインが実現されました。ただし、構造物の視認性が低いこともわかります。したがって、より高い解像度だけでなく、基板への構造のより良い接着のためにも、重合プロセス中に適切なレーザー焦点位置を設定することが非常に重要です。
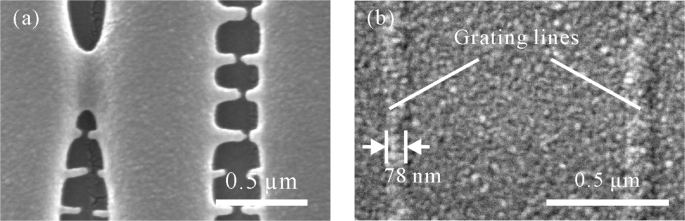
構造形成に対するレーザー焦点位置の影響。材質:Eシェル300。 a レーザーで製造された垂直格子線は、フォトレジストのより内側に焦点を合わせます。製造用のレーザー強度 I =0.71 kW / μ m 2 (レーザー出力1.55 mWに対応)、相対的なレーザー焦点距離Δ z =500nm。フィーチャー間の余分な重合が生成され、隣接するフィーチャーが接続されます。 b レーザーで製造された垂直格子線は、基板のより内側に焦点を合わせます。製造用のレーザー強度 I =0.65 kW / μ m 2 (レーザー出力1.4 mWに対応)、相対的なレーザー焦点位置Δ z =0 nm
特徴サイズに対するレーザー焦点位置の影響に関して、 x で製造される格子線に対するその影響の調査 − y 飛行機が実施されました。相対距離Δ z を増やすことによって 、異なるレーザー焦点位置の下で製造された格子線が得られた。格子線の測定幅 w l 相対的なレーザー焦点位置に応じて、図7aに示すドットとしてプロットされます。製造に使用されるレーザー強度は0.85kW / μです。 m 2 (レーザー出力1.84mWに対応)。赤い曲線は、主軸が z と一致する楕円フィットの結果を示しています。 軸。対応する楕円は、楕円の式\(\ left(\ frac {x} {a} \ right)^ {2} + \ left(\ frac {400-y)を使用して再構築されました(図7aの右下隅を参照)。 } {b} \ right)^ {2} =1 \)、ここで(400,0)は楕円の中心、 b =90は短半径、 a =5.65 b は準主軸、 x 相対距離Δ z を表します 主軸に沿って、 y フォーカスサイズの半分を表します L これは短軸に沿っています。結果は、線幅がボクセル楕円幾何学の主軸に沿って変化するレーザー焦点断面サイズに従うことを明らかにしています。相対位置Δ z の場合 =50 nm、フィーチャサイズが w のグレーティングライン l =130 nmが実現されました(図7b)。さらに、レーザー強度を下げることにより、 w の格子線 l =100 nmは、図7cに示されているのと同じレーザー焦点位置で得られました。
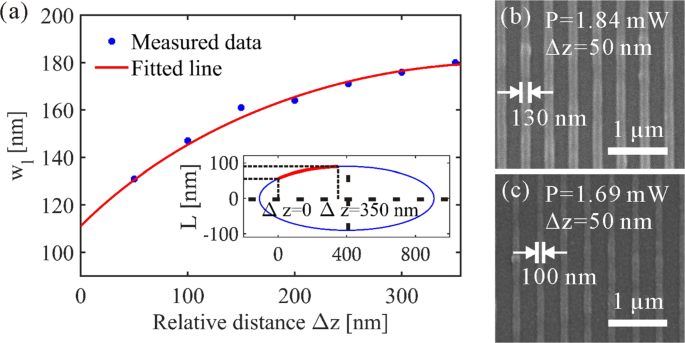
x で製造された格子線 − y 異なる相対レーザー焦点距離Δ z に関する平面 。素材:E-shell300。書き込み速度は7 μ m / sが適用されました。 a さまざまなΔ z に関して測定された線幅とフィット曲線 。右下の図は、フィットした線に対応する楕円を再構成したものです。 b I のレーザー強度で製造されたグレーティングライン =0.85 kW / μ m 2 (レーザー出力 P =1.84 mW)。相対的なレーザー焦点距離はΔ z =50nm。 c I のレーザー強度で製造されたグレーティングライン =0.78 kW / μ m 2 (レーザー出力 P =1.69 mW)。相対的なレーザー焦点距離はΔ z =50 nm
ピラーの特徴サイズに対するレーザー焦点位置の影響も調査された。ピラーは、ボクセルの主軸( x )の平面内にある基板平面に直交して焦点を移動することによって実現されます。 − z または y − z 飛行機)。レーザービームを z に沿って移動させることにより、単一の柱を作成しました。 距離が1 μの方向 m。図8aは、さまざまなレーザー強度と相対距離Δ z で製造されたピラーのSEM画像です。 。隣接する柱の中心間の距離は、 x に沿って400nmです。 方向と y に沿った500nm 方向。レーザー強度は、左から右に約0.23 kW / μのステップで増加しました。 m 2 (レーザー出力0.5mWに対応)。レーザー焦点位置間の相対距離 z および基準位置 z 0 垂直方向に沿って下から上に増加しました。図8bは、測定されたピラーの直径 w を示しています。 p レーザー強度と相対距離Δ z 。柱の直径 w p そのFWHMを測定することによって得られます。レーザー強度は0.74〜0.96 kW / μの範囲です。 m 2 。 w p 両方のΔ z の減少とともに減少します とレーザー強度。 Δ z の場合 =150 nm、直径 w の柱 p 比較的広いレーザー強度範囲(0.74〜0.81 kW / μ)で約110nmが達成されました m 2 )。また、図8c–dに示すように、ピラーのアレイを作成すると、ピラーサイズのウィンドウが比較的安定します。これは、 I > =0.74 kW / μ m 2 および相対距離Δ z =300nm。ピラーのアスペクト比は約2です。これは、ピラーの再現性が非常に優れていることを示しています。
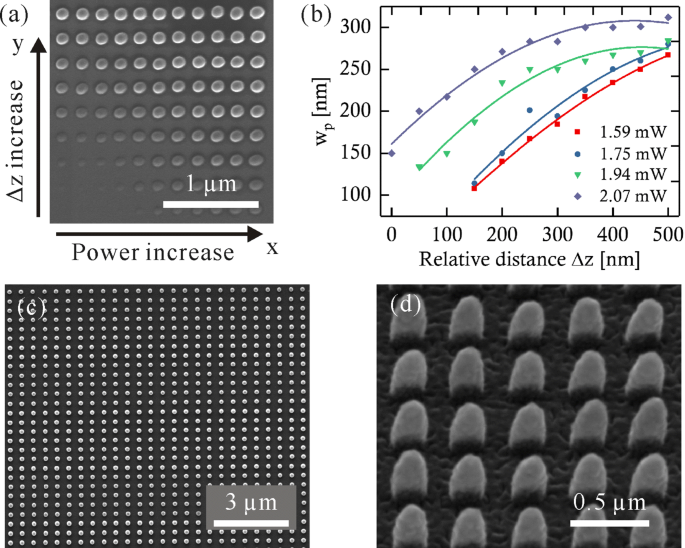
異なるレーザー強度とレーザー焦点相対距離Δ z で製造されたピラーアレイ 。材質:Eシェル300。 a 異なるレーザー強度と相対的なレーザー焦点位置で製造されたピラーのSEM画像。 b 測定された柱の直径 w p レーザー強度に関して I 相対距離Δ z 。レーザー強度はそれぞれ0.74kW / μです。 m 2 、0.81 kW / μ m 2 、0.90 kW / μ m 2 、および0.96 kW / μ m 2 レーザー出力1.59mW、1.75 mW、1.94 mW、および2.07mWに対応します。 c ピラーアレイの上面図。 d 45 ∘ で見たピラーアレイのSEM画像
回折限界未満の特徴サイズとギャップサイズを持つ周期構造の製造
周期的な格子線( x で製造)の特徴サイズに関するそれぞれの調査に基づく − y 平面)と柱、格子線と柱で構成される提案された高解像度の周期構造が製造されました。サイズは20×20 μです。 格子線の中心とピラーの間の周期的な距離が200nmのm。本研究では、グレーティングラインとピラーを別々に作製することにより、周期距離200nmの高解像度構造を実現する戦略を提案します。この場合、周期距離 PD 隣接するグレーティングラインと隣接するピラーの間は400nmです。重合プロセス中、格子線とピラーが別々に製造される場合、フィーチャ間に大きなギャップ領域が存在します。この一時的に広がるギャップ領域は、ラジカルの蓄積を減らすことを可能にし、それはギャップ領域での望ましくない重合につながる可能性がある。レーザーの焦点位置も製造プロセス中に調整する必要があることに注意する必要があります。不適切なレーザー焦点位置で製造された構造を図9aおよびbに示します。レーザーの焦点がフォトレジストの内側にありすぎると、ラインとピラーが接続されていることがわかります。図9c–fは、適切に配置されたレーザー焦点を備えた構造のSEM画像です[23]。レーザーの焦点位置を適切に配置し、上記の製造戦略を利用することにより、回折限界未満の寸法(線幅110 nm、ピラー直径135 nm、ギャップサイズ65 nm)の構造を次のように実現しました。図9e。
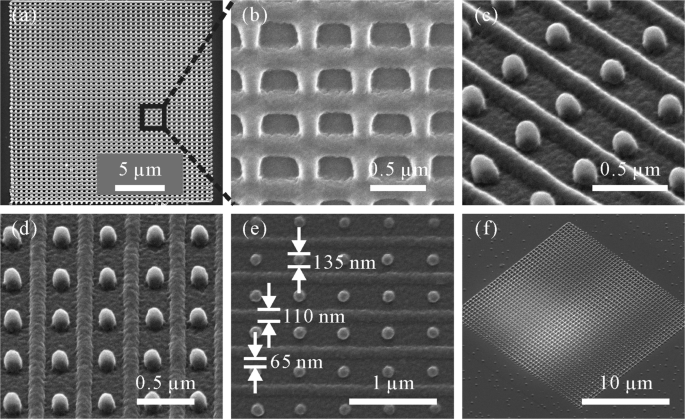
P を使用して2PPで作製した周期構造のSEM画像 D =200nm。材料:Eシェル300。格子線の製造に使用される強度: I =0.83 kW / μ m 2 ;柱:私 =0.6 kW / μ m 2 。グレーティングラインとピラーを製造するための相対的なレーザー焦点距離は300nmです。 a – b フォトレジスト内部にレーザーフォーカス位置を設定して作製した周期構造。 c – d 適切なレーザー焦点位置を持つ周期構造のSEM画像。 e 適切なレーザー焦点位置で製造された構造の上面図。 f アレイ全体のSEM画像
結論
結論として、構造形成に対するさまざまなフォトレジストと処理パラメータの影響を比較し、 z に沿ってレーザーの焦点位置を制御することにより、空間分解能を向上させ、隣接するフィーチャ間のギャップサイズを縮小する方法を示しました。 方向。 E-shell 300は、200nm未満の空間分解能を持つ構造の製造に適した材料であることが実験的に証明されました。また、ギャップサイズ65nm、フィーチャサイズ110nmの周期構造を実現することに成功しました。サイズはアッベの回折限界をはるかに下回っています。この高解像度構造の光学性能(光学画像の信号強調など)に関するさらなる調査は魅力的です。
略語
- 2PA:
-
二光子吸収
- 2PP:
-
二光子重合
- FWHM:
-
半値全幅
- IFTS:
-
干渉フーリエ変換スキャトロメトリ
- NA:
-
開口数
- PD:
-
定期的な距離
- SEM:
-
走査型電子顕微鏡
ナノマテリアル
- 金属を使用した3D印刷のサポート構造—より簡単なアプローチ
- DATA MODULは、タッチセンサーポートフォリオをさらに大きなサイズに拡張します
- 人工ニューロンによる教師なし学習
- カヴリ賞を受賞したAFMパイオニア
- 銅原子の心に合わせて
- 針を簡単に通す:最小ファイバーフィーチャーサイズ
- シフトの概念:自動車のアフターマーケットのギャップを3Dプリントされたパドルシフターで埋める
- エンジニアリングに対する認識の変化:自動化されたエンジニアリングでスキルのギャップを埋める
- サイズが小さく、コストが高い:シュリンクフレーションで何が起こっているのか?
- Gap Inc.は、ロボット工学、AIにより倉庫業務をスピードアップします
- 適切なサイズの掘削機で生産を最大化