単結晶銅の切断ベースの単一原子層除去メカニズム:エッジ半径効果
要約
機械的切削の最終的な目的は、最小の切りくずの厚さを単一の原子層に減らすことです。この研究では、単結晶銅の切削ベースの単一原子層除去メカニズムを一連の分子動力学分析によって調査します。研究結果によると、切削深さが原子スケールまで減少すると、丸みを帯びたエッジツールを使用した機械的切削により、最小チップ厚が単一原子層まで減少する可能性があります。切削ベースの単一原子層除去中の材料除去挙動は、せん断応力駆動転位運動による切りくず形成、処理された表面の弾性変形、原子サイジング効果、および最先端の半径効果を含む4つの特性を示します。この理解に基づいて、ナノカッティングや従来のカッティングとは大きく異なる、カッティングベースの単一原子層除去プロセスにおける材料除去挙動を研究するための新しいカッティングモデルが提案されています。結果は、原子および原子に近いスケールの製造技術の研究開発に理論的なサポートを提供します。
はじめに
最も重要なサブトラクティブ加工方法の1つとして、機械的切削が適用され、高い表面仕上げ品質の部品が製造されています[1、2]。基本的なナノカッティング理論を確立し、充実させるために、ナノスケールで下層材料の除去メカニズムを明らかにするために、多数の理論的および実験的研究が実施されてきました[3,4,5,6]。研究成果は、学界や産業界でのナノメートル切削の応用に大きく貢献し、複雑な形状とナノメートルの表面仕上げ品質を必要とする高性能部品の製造を可能にします[7、8]。しかし、原子および原子に近いスケール(ACS)での切断における材料除去のメカニズムに関する報告はまだなく、次世代の製造技術である原子および原子に近いスケールの製造の開発の進展を深刻に制限しています( ACSM)、つまり製造III [9]。さらに、原子スケールデバイスの進歩的な開発は、ACSMを達成するためのさまざまな機械加工プロセスの需要も強調しました[10]。
従来のマクロスケール切削では、切削深さは刃先半径よりも大幅に大きく、材料の除去は材料のせん断による切りくず生成によって実現されます[11、12、13]。マイクロ/ナノカッティングでは、切削深さが工具刃先半径に匹敵するかそれよりも小さいため、押し出しの切りくず形成が徐々に支配的になり、切削深さがナノスケールまで減少します。これは、刃先半径の影響に大きく影響されます[14、15、16 、17、18、19]。 ACS切削では、切削深さがさらに原子スケールに近く、さらには刃先半径よりもはるかに小さい原子スケールにまで減少するため、刃先半径の影響は必然的に材料除去挙動に影響を及ぼします。
さらに、従来の切削やマイクロ/ナノ切削とは異なり、ACS切削では、切削深さは刃先半径よりも大幅に小さいだけでなく、ワークピース原子の半径よりも同等またはさらに低くなります。実際の材料除去挙動は、ワークピースの原子半径に対する切削深さのさまざまな比率で変化します。これは、1つの新しいサイジング効果、つまり原子サイジング効果として認識されます[20]。したがって、ACS切断では、最先端の半径効果と原子サイジング効果の両方を考慮する必要があります。ただし、ACS切断技術の研究におけるこの非常に重要な問題についての報告はありません。
これらの理由から、本研究では、分子動力学(MD)モデリングを使用して、切削ベースの単一原子層除去メカニズムに対する原子サイジング効果とエッジ半径効果を調査します。
このペーパーは、次のセクションで構成されています。セクション2では、モデリングとプロトコル、適切な潜在的機能など、使用される方法論を紹介します。セクション3では、分析結果と関連する議論を示します。セクション4では、最先端の効果と原子のサイジング効果の結合の影響下で、詳細な切断ベースの単一原子層除去メカニズムについて説明します。調査結果はセクション5で締めくくられています。
方法論
シミュレーションモデルとプロトコル
切削深さが原子スケールまたは原子スケールに近づくにつれて、実際に材料除去プロセスを経験的に観察することは実際に困難です。この研究では、一連のMDシミュレーションを実行して、切削ベースの単一原子層除去メカニズムを分析し、ワークピースの原子サイジング効果と最先端の半径効果に重点を置いています。
図1は、単結晶銅ワークピースとダイヤモンド切削工具で構成されるダイヤモンド銅切削モデルの原子配置のスナップショットを示しています。シミュレーションは単結晶銅の(111)面で行われます。 x でのワークピースの寸法 -[1 -1 0]、 y -[1 1 -2]、および z -[1 1 1]方向は、それぞれ27、10、および5nmです。 MDシミュレーションでは、ワークピースの原子は、図1に示すように、それぞれ境界層原子、サーモスタット層原子、ニュートン層原子に分割されます。ワークピースの下部にある2つの層、つまり境界層は固定されたままです。 MDシミュレーションを介して、ワークピースの切断による位置移動の可能性を排除します。境界層に隣接する3つの原子層は、サーモスタット層の原子です。恒温層の温度は、速度再スケーリング法によって298Kに保たれています。残りのワーク原子はニュートン層に属します。現在のシミュレーションでは、切削工具のすくい角と逃げ角は0°と12°です。詳細なモデルパラメータを表1にまとめます。ACS切削は低速の切削速度で行うことが好ましいため、切削速度と計算時間の影響を考慮した上で、[-1 10]方向に沿って25m / sの切削速度を使用します。コスト。
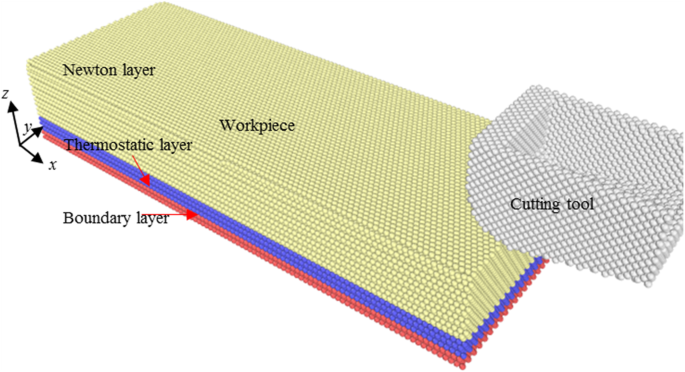
ダイヤモンドカッティングモデルのシミュレーションモデル
潜在的な機能
銅とダイヤモンドの切断システムには、主に銅とダイヤモンドの2種類の原子が含まれます。 MDシミュレーションでは、シミュレーション結果の計算精度を確保するために、原子間相互作用を正確に記述する必要があります。したがって、潜在的な機能の合理的な選択は非常に重要です。この研究では、銅原子間の原子間相互作用を説明するために、頻繁に使用される埋め込み原子法(EAM)ポテンシャル関数が採用されています[21]。モース関数は、主に r。に応じて、銅原子とダイヤモンド原子(Cu-C)間の相互作用を計算するために適用されます。
$$ E ={D} _0 \ left [{e} ^ {-2 \ alpha \ left(r- {r} _0 \ right)}-2 {e} ^ {\ alpha \ left(r- {r} _0 \ right)} \ right] $$(1)ここで E および D 0 ポテンシャルエネルギーと凝集エネルギーのペアαを参照してください。 定数 r を表します 0 は平衡距離であり、 r 2つの原子間の距離です。 Cu-C相互作用の場合、 D 0 は0.087ev、 r 0 は0.205nm [22]であり、α は51.40nm -1 。 切削工具(C-C)の炭素原子間の相互作用については、銅原子よりもダイヤモンド原子間の結合強度が大幅に強いことは無視できます。切削工具は、分析中は剛性があると見なされます。
切削深さの定義
切削深さ( a )は、ワーク表面の最上点と切削工具の最下点の間の距離として定義されます。ワークピースの原子のサイズは通常、原子半径( r )で表されます。 w )。 図2に示すように、最上部の最初の原子層をワークピースの表面から除去することを目標とする場合、理論的には、使用される最大切削深さは次のように取得できます。
$$ {a} _ {\ mathrm {max}} ={r} _w + 0.5 \ ast {d} _ {layer} $$(2)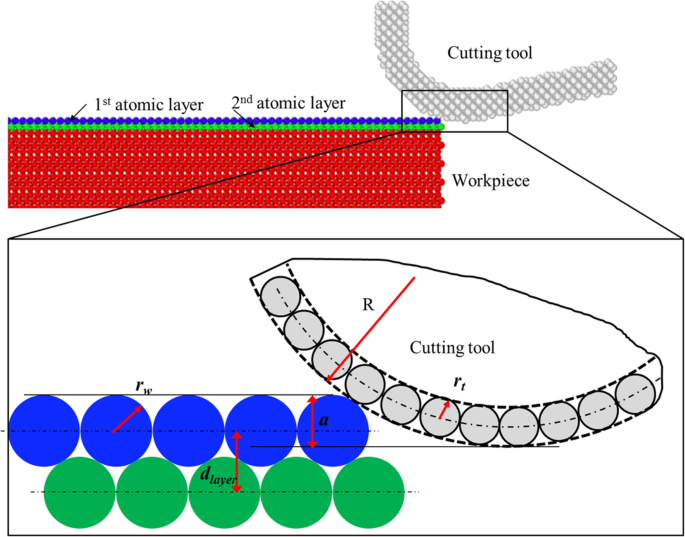
単一原子層除去における切削深さ定義の概略図
ここで、 d レイヤー ワークピース表面の最上部に隣接する原子層間の間隔を表します。この研究では、すべての分析は単結晶銅ワークピースの(111)表面に基づいています。したがって、 r w 式で。 (2)は、銅原子の半径、つまり1.28Åを指します。 d レイヤー 2.087Åです。 a の場合 a より大きい max 、切削工具の最下点が2番目の原子層と直接接触し、材料の変形や除去さえも引き起こす可能性があります。したがって、本研究では、使用する切削深さは a よりも浅い。 max (2.32Å)。
調査結果に基づいて、基本的な切断ベースの単一原子層除去メカニズムは、 a の比率のさまざまな組み合わせで大幅に変更されます。 R へ および a r へ w 。
結果と考察
MDの結果によると、原子サイジング効果と最先端の半径効果の両方が、切断ベースの単一原子層除去プロセスに大きな影響を与えています。次のセクションでは、アトミックサイジング効果とツールエッジ半径効果を明確に説明するために、切削深さの比率( a )ワークピースの原子半径( r w )、 a / r w 、および切削深さ( a )からエッジ半径( R )、 a / R 、 採用されている。解析結果は、切りくず生成、表面生成、表面下変形、原子変位挙動の観点から体系的に研究されています。調査結果は、切削ベースの単一原子層除去メカニズムの典型的な特性に関する詳細な洞察を提供します。
チップフォーメーション
分析結果は、ワークピースの原子サイジング効果[20]により、切削深さの比率( a )の2つの臨界値があることを示しています。 )ワークピースの原子半径( r w )、つまり、臨界値1(C 1 )および臨界値2(C 2 )、チップ形成挙動をさまざまなケースに分割しました。
- a。
a / r の比率 w 臨界値1よりも小さい(C 1 。
図3は、約1.1Åの切削深さでのさまざまな工具エッジ半径でのMDシミュレーションの結果を示しています。ここでは、切削深さの比率( a )ワークピースの原子半径( r w )は0.781です。
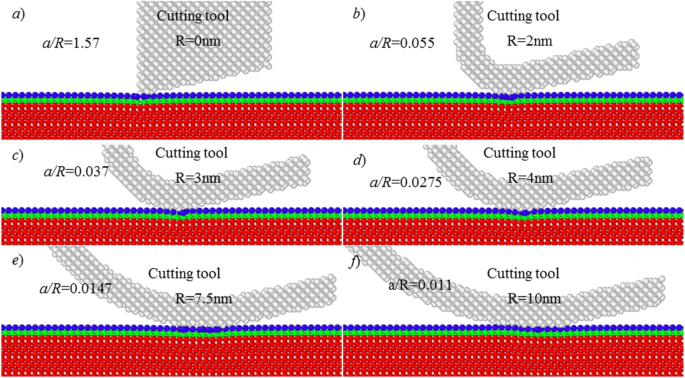
1.1Åの切削深さでのシミュレーション結果
最先端の半径が大きくなっているにもかかわらず、処理された各Cu(111)表面に弾性変形が発生しています。切削工程での切りくずの形成や材料の除去はありません。この研究では、Cu(111)表面で材料を除去できるようにするには、切削深さを約1.1Åより大きくする必要があることが示されています。
- b。
a / r の比率 w C1よりも大きいが、臨界値2(C 2 )よりも小さい 。
切削深さが約1.1Åより大きい場合、つまり a / r の比率 w が0.781より大きい場合、ワークピースの表面で材料の除去が発生します。図4に示すように、材料の一部がワークピースの表面から除去されますが、最上部の第1層内のより多くの原子が新しい処理された表面に残り、表面欠陥を形成します。さらに、エッジ半径が7.5 nmに増加すると、 a / R の比率が増加します。 0.019です。このような場合、図4eに示すように、第1原子層の原子の一部が第2層、さらには第3原子層に押し込まれます。これは、切削工具の押し出し作用によるものと考えられます。また、連続的な材料除去は得られませんでしたが、工具エッジ半径効果が材料除去プロセスに影響を及ぼし始めていることも示しています。
- c。
a / r の比率 w C 2 より大きい 。
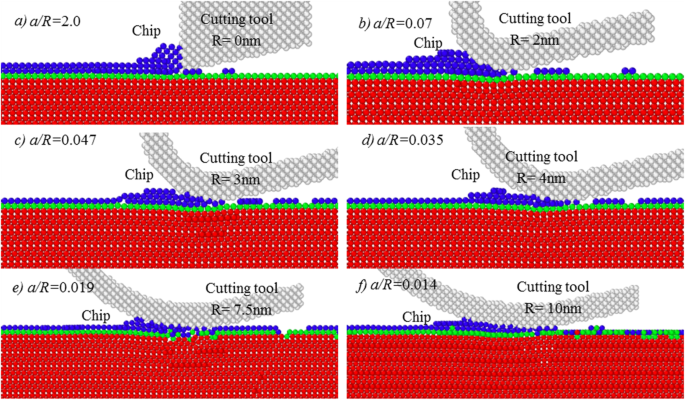
1.4Åの切削深さでのシミュレーション結果
図5は、約2Åの切削深さでの切りくず生成を示しています。ここで、 a / r の比率 w =2Å/1.28Å=1.563。図3と比較して、切削深さを2Åに増やすと、ターゲット原子層内の原子は、チップ形成によって連続的かつ安定して除去できました。これは、切削深さが単結晶銅の最小切りくず厚さよりも大きく、最小切りくず厚さが約2Åの切削深さの単一原子層まで下がることができることを示しています。切断後、最初の原子層内の材料はワークピースの表面から完全に除去されました。
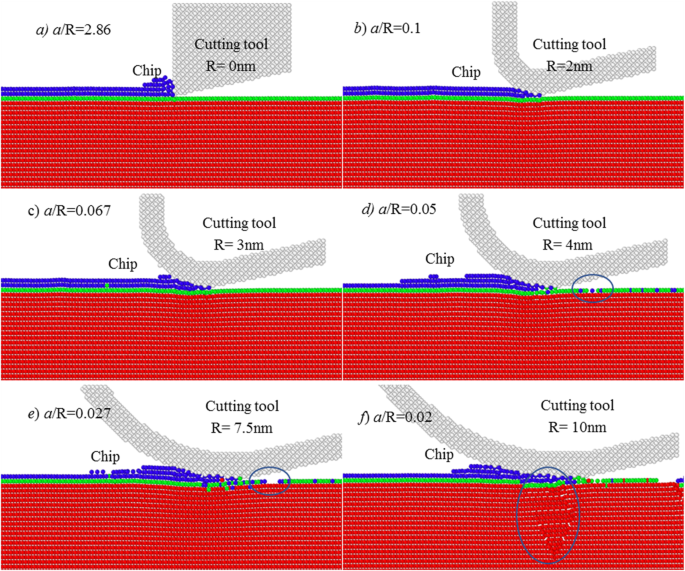
切削深さ=2ÅでのACS切削のシミュレーション結果
ただし、図5でも、 a / R の比率が増加していることがわかります。 、最初の原子層の原子は、明らかに異なる除去プロセス、特に処理された表面での切削による変形を受けます。切削深さ2Åで、鋭利な切削工具を使用した場合、つまり a / R の比率 は5.70であり、処理された表面でわずかな変形のみが発生します。最先端の半径が3nmに増加すると、 a / R の比率 は0.134であり、弾性変形の振幅は明らかに増加しました。
図5dに示すように、ツールのエッジ半径を4 nmに増やすと、ターゲットの第1原子層内の多くの原子が第2原子層に押し込まれ、新しい処理済み表面が形成されます。ツールエッジ半径が約7.5nmの場合、第1層の原子の一部が第3原子層にまで拡散します。ツールのエッジ半径が約10nmに達すると、明らかな弾性および塑性変形が発生します。これは、次のセクション3.3でも確認できます。
したがって、切断ベースの単一原子層の除去は、 a / r の比率だけでなく依存します。 w 、だけでなく、 a / R の比率 。機械的切断による単一原子層の除去、つまり原子スケールでの材料除去を実現するには、マイクロ/ナノ切断や従来のマクロスケール切断とは大きく異なり、原子サイジング効果と最先端の半径効果の両方を考慮する必要があります。
表面生成
切削ベースの原子層除去の目的の1つは、理想的な結晶構造を備えた欠陥のない処理済み表面を取得することです。最近、ACS切断における表面生成に対するワークピースの原子サイジングの影響が研究されています[20]。本研究では、ACS切削における表面生成に対する最先端の半径の影響を明確に示すために、新しい処理された表面の表面トポグラフィーと表面組成を次のように研究します。
表面の地形
図6は、さまざまなエッジ半径で処理されたCu(111)表面の表面トポグラフィを示しています。ここでは、2Åの切削深さを採用しています。図6a、bに示すように、工具刃先半径が3 nmより小さい場合、理想的な結晶構造を持つCu(111)表面を得ることができます。ワーク表面左側の不良は、工具の切削出口での変形によるものです。定常段階での切断中、加工面に表面欠陥は発生しません。
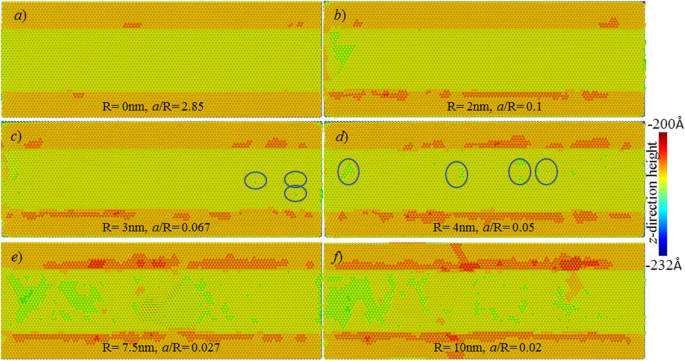
表面形状に対する工具刃先半径の影響。原子は、z方向の高さに基づいて色付けされます
ただし、工具刃先半径が大きくなると、加工面に徐々に多くの欠陥が発生します。エッジ半径4nmでは、処理された表面に多くのピット状の欠陥が形成されます。図6dを参照してください。また、工具刃先径が5nm以上の場合、表面欠陥が多数発生し、表面品質が著しく低下します。このような場合、ワークピースの表面から複数の原子層が除去されています。したがって、2Åの切削深さで、工具エッジ半径が3 nm未満の場合、Cu(111)表面で単一原子層の除去を達成できると判断できます。刃先半径効果により、切削深さの比率( a )からエッジ半径( R )は、切断ベースの単一原子層の除去によって欠陥のない処理済み表面を実現するために、1つのしきい値よりも大きくする必要があります。ここで、 a / R の比率の臨界値 は[0.05、0.067]です。
表面構成
図7は、さまざまな工具エッジ半径と2Åの切削深さでの加工面の構成を示しています。ここで、緑と青の原子は第1層と第2層の原子であり、赤の原子は第2原子層の下の原子です。図7aに示すように、鋭利な切削工具を使用する場合、 a / R の比率 は2.85で、処理された表面は最初の層の原子のみで構成されます。この結果は、対象の第1原子層がワークピースから完全に除去されたことを示しています。さらに、これは、材料の除去が層ごとの形で行われることを意味します。この場合、除去される材料は、ワークピース表面の対象となる最初の原子層からのみ発生します。
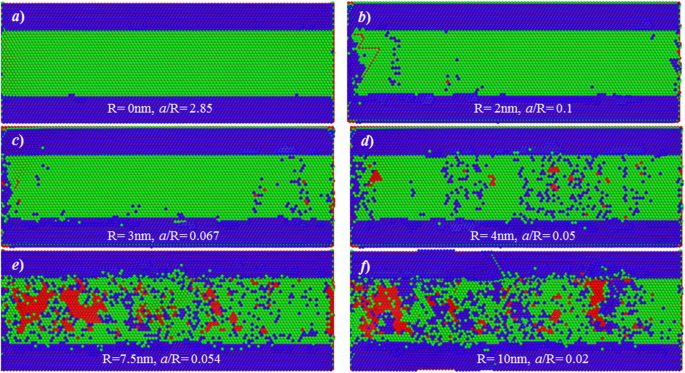
処理された表面の表面組成。原子は原子層の数に基づいて色分けされます
ただし、図7b、cに示すように、工具のエッジ半径が2nmと3nmの場合、処理された表面は2つの原子層(青と緑)で合成されます。これは、単一原子層の除去が達成されたものの、表面生成プロセスには最低2つの原子層が含まれることを示しています。さらに、工具刃先半径が4 nmより大きい場合、処理された表面に第1原子層の原子が多数存在し、第1層の多くの原子がプレスされて新しい表面が生成されたことを示します。
したがって、刃先半径の増加に伴い、表面生成が大幅に変更されました。関連する2種類の表面生成メカニズムを以下に要約します。
- 1。
レイヤーごと :ターゲットの最初の原子層が完全に削除され、新しい処理済みサーフェスが生成されます。切断プロセスでは、最初の層内の原子のみが削除されます。
- 2。
多層除去 :単一の原子層の除去は実現できますが、ターゲットの原子層内の原子は2つの典型的な変位動作を起こします。原子の一部は、せん断応力によって駆動される転位運動によってチップに形成され、他の原子は、切削工具の作用の下で、処理された表面に押し出されます。材料除去プロセスには、最低2つの原子層が含まれます。
地下変形メカニズム
ナノカッティングでは、カッティングプロセス中に処理された表面に弾性および塑性変形があります。切削工具がワークピースの表面を通過した後、弾性部分が跳ね返りますが、塑性変形した部分は持続的な変形につながります[1、2]。切削深さが原子スケールまで減少するにつれて、単一原子層の除去に向けた切削では、処理された表面で発生する弾性変形のみが存在すると仮定されます。それを検証するために、切削中および切削後のワークピースの表面下の変形状態を分析します。図8は、さまざまな工具エッジ半径でのワークピースの表面下の欠陥構造を示しています。ここでは、原子は中心対称性パラメーター(CSP)に基づいて色分けされており、CSPが3未満の原子は省略されています。これは、完全なFCC構造を持つ原子を表しています。
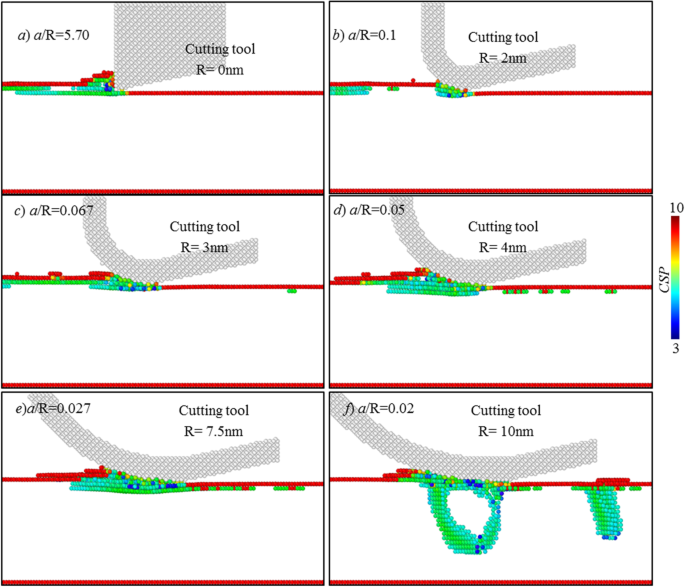
処理された表面の表面組成。原子は、CSPに基づいて色分けされています
刃先半径が4nm未満の場合、加工面に表面下欠陥は発生しません。切削時に加工面に弾性変形のみがあります。
図8に示すように、刃先半径が4 nm以上の場合、初期化された表面下欠陥があります。さらに、最先端の半径が大きくなると、表面下の欠陥の数が大幅に増加します。図9eに示すように、エッジ半径が約10 nmに達すると、1つの転位ループが形成され、切断後に消えることはありませんでした。加工面に塑性変形が発生していることを明確に示しています。
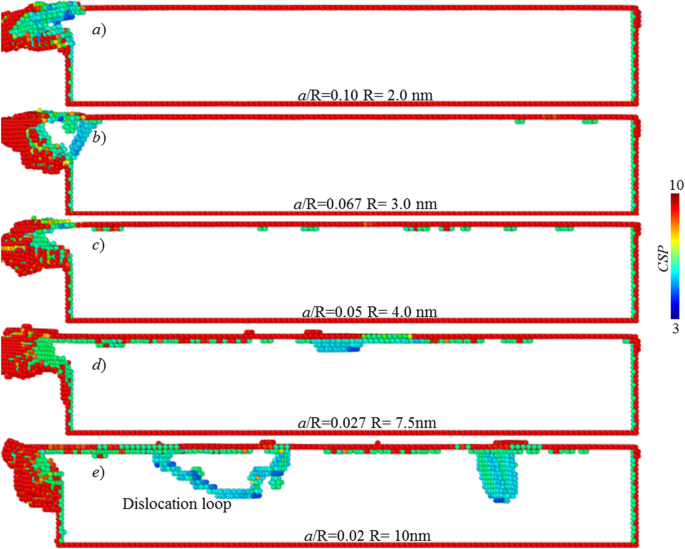
さまざまな工具エッジ半径での表面下欠陥。原子は、CSPに基づいて色分けされています
工具がワークピースの表面を通過した後、弾性変形した部分が跳ね返ります。したがって、表面下の欠陥の一部が消滅します。図9a–cに示すように、最終的に、工具のエッジ半径が2nmまたは3nmの場合、表面下の欠陥は存在しません。
塑性変形部分は持続的な変形につながります。図9に示すように、工具刃先半径が7.5 nmの場合、表面下の欠陥はほとんど残っていません。工具刃先半径が10nmの場合、最終的には転位ループと積層欠陥がワークピースの表面下に存在します。
上記の分析に基づいて、切断ベースの単一原子層の除去を可能にするには、塑性変形を回避する必要があり、処理された表面では弾性変形のみが許可されると推測できます。これは、切断ベースの単一原子層除去プロセスの特徴の1つと見なされています。
原子変位挙動
MD軌道ファイルによると、転位運動が切削ベースの単一原子層除去プロセスを支配してきました。図10は、さまざまな工具エッジ半径を使用したシミュレーション結果を示しています。エッジ半径2nmでは、切削工具の作用により、最初の原子層のみが切削方向に沿って滑ってチップになり、他の原子層は固定されたままになります。これは、1つのエッジ転位の1つの断面と見なすことができます。
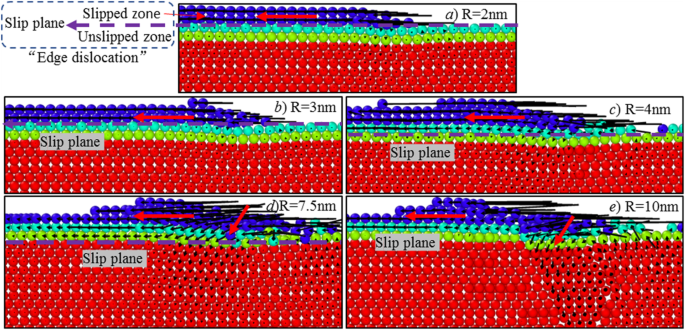
さまざまな最先端の半径での原子変位挙動
ツールのエッジ半径が大きくなると、最初の原子層内の材料の一部が処理された表面に押し込まれ、最初の層の下に原子層が滑り込みます。さらに、工具のエッジ半径が大きくなると、材料のスリッププロセスを受ける原子層の数が増える傾向があります。図10に示すように、工具刃先半径が4 nmの場合、第1原子層を除いて、第2原子層も切削方向に沿って材料の滑りを伝導します。工具刃先半径が7.5 nmの場合、切削工具が進むにつれて、最上部の3つワーク表面の原子層が切削方向に滑り込んでいます。さらに、工具刃先半径を10 nmに拡大すると、多数の材料がプレスされて新しい加工面が形成されます。ワークピースの表面に塑性変形(図10eを参照)が発生しています。これは図9でも確認できます。
図11は、切断方向に沿ったターゲット原子層のすべりプロセスを示しています。スリップゾーンの領域は、切削工具が前進するにつれて継続的に拡大されます。 17.5 nmの切断距離で、スリップゾーンは最大値に達しました。続いて、スリップゾーン内の材料は連続的にチップに成形されます。チップの量も増えます。
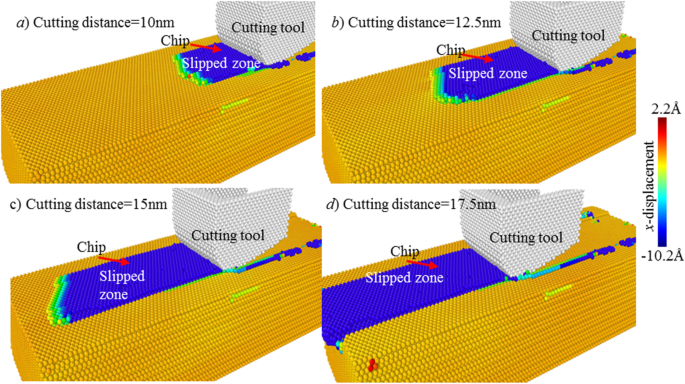
刃先半径2nmでのターゲット原子層のスリッププロセス。原子は、x方向の原子変位値に基づいて色分けされます
全体として、セクション3.3および3.4の分析によると、工具のエッジ半径が大きくなるにつれて、表面下の変形メカニズムと原子変位挙動の両方が大きく変化しました。表2に要約されているように、異なる工具エッジ半径では、異なる数の原子層が切削方向に沿ってスリップする傾向がありますが、処理された表面では異なる変形レジームが発生します。さらに、切削ベースの単一原子層の除去では、プロセスでは、切りくず生成はせん断応力駆動の転位運動によって支配され、従来の切削やナノ切削での切りくず形成とは大きく異なります。これは、切削ベースの単一原子層除去の1つの特徴と見なすこともできます。
<図> 図>切断力
エッジ半径効果の影響
図12は、2Åの切削深さでの平均切削抵抗に対する刃先半径の影響を示しています。ここで、切削抵抗の接線成分と法線成分、つまり F t および F n 、比較されます。示されているように、鋭利な切削工具の場合、 a / R の比率 は2.85で、 F t 16.4nNは明らかに F よりも小さい n 23.7nNの。工具刃先半径が大きくなると、両方の F t および F n 増加します。ただし、 F n F よりもはるかに大きな成長振幅を示しました t 。これは、工具の刃先半径が大きくなると、通常の切削抵抗がACS切削プロセスでの材料除去プロセスに大きな影響を与えることを明確に示しています。ただし、ツールエッジの半径が約3 nmより大きい場合、単一原子層の除去は達成できませんでした。したがって、より大きな通常の切断力は、切断ベースの単一原子層の除去を可能にするのに役立たず、より低い通常の切断力が好ましくは採用されるべきである。
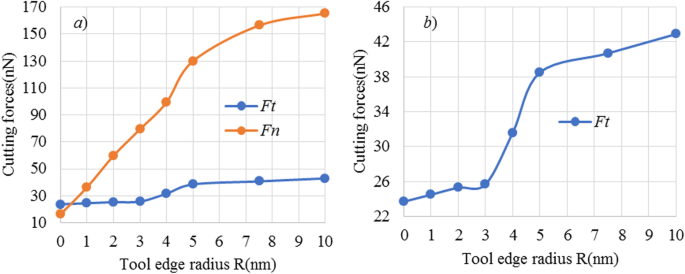
2Åの切削深さでの切削抵抗と刃先半径のプロット
通常の切削力は、処理された表面に弾性および/または塑性変形を可能にする圧縮応力を提供するため、接線方向の切削力は、チップ形成にせん断応力を提供します。したがって、切削ベースの単一原子層除去における切りくず形成は、主に接線方向の切削力によって駆動されるべきであると推測することができます。図12bでも、 F t は3種類の変化を示し、さらに次のようなさまざまな表面トポグラフィー(図6を参照)につながります。
工具刃先半径が約3nmより小さい場合、つまり a / R の比率 は0.067、 F t ほぼ変化せず、エッジ半径が大きくなるにつれて、常に25nNより小さくなります。このような場合、ワークピースの表面から除去される原子層は1つだけです。
工具刃先半径が3nmと5nmの場合、 a / R の比率 F は、0.04と0.067です。 t 明らかに約38.5nNに増加します。その結果、複数の原子層がワークピースの表面から除去されますが、形成される表面欠陥はわずかです。
5 nmより大きいエッジ半径については、 F t また、徐々に一定値に収束します。この場合、複数の原子層が削除されます。ただし、ワーク表面と表面下に多数の表面欠陥が形成されます。
非常に低い接線方向の切削力により、2nmなどの妥当な刃先半径での切削ベースの単一原子層の除去が可能になると結論付けることができます。次に、接線方向の切削抵抗が大きいにもかかわらず、単一原子層の除去を実現できませんでした。
アトミックサイジング効果の影響
図13はさらに、2nmの刃先半径での切削抵抗と切削深さのプロットを示しています。刃先半径2nmでは、切削深さが増すにつれて、通常の切削抵抗と接線切削力の両方で3段階の変化が見られます。約1.1Åと1.6Åの切削深さで明らかな変化があります。対応する切削深さの比率( a )ワークピースの原子半径( r w )は0.055と0.080であり、これらは上記の a / r の2つの臨界値です。 w 、C 1 およびC 2、 セクション3.1に示されているように。
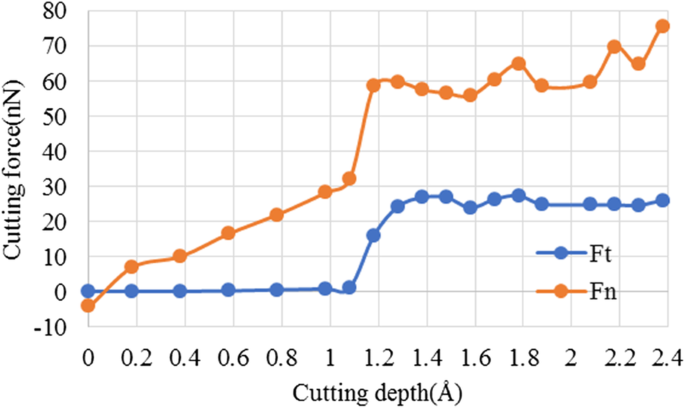
刃先半径2nmでの切削抵抗と切削深さのプロット
切削深さが1.1Å未満の場合、つまり a / r の比率 w 0.055未満、 F t F の間、は常に0nNです。 n は約32nNまで直線的に増加します。しかし、切削抵抗は、プラスチック材料の変形とワークピース表面の除去を可能にすることができませんでした。その結果、図3に示すように、ワークピースの表面には弾性変形しかありません。
切削深さが1.1Åより大きく1.6Åより小さい場合、 a / r の比率 w 0.055より大きく0.080未満です。この場合、 F t F が、0nNから約25Nnに大幅に増加しました。 n さらに約58nNに増加しました。切削抵抗は、ワークピース表面の材料除去を可能にするのに十分な大きさです。 1.4Åの切削深さでは、ワークピースの表面に切りくずの形成と材料の除去があります。しかし、図4に示すように、安定した連続的な材料除去は実現できず、加工面に多くの欠陥が形成されます。
切削深さが1.6Åより大きい場合、両方の F t および F n ワークピース表面の連続的な材料除去を可能にするのに十分な大きさです。その結果、ワーク表面上にチップが安定して形成され、図5bおよび図6bに示すように、ターゲット原子層がチップ形成によって連続的に除去され、新しい処理済み表面が形成されます。
全体として、最先端の半径効果と原子サイジング効果の両方が、切削ベースの単一原子層除去プロセスの切削力に影響を及ぼし、それによって材料除去と表面生成プロセスを変更します。
切断ベースの単一原子層除去メカニズムに関する議論
上記の分析によると、原子サイジング効果と最先端の半径効果の両方が、切断ベースの単一原子層除去メカニズムに大きな影響を及ぼします。表3に要約されているように、ワークピースの原子半径に対する切削深さの比率( a / r w )および刃先半径に対する切削深さの比率( a / R )、切削ベースの単一原子層除去プロセスでは、材料の変形と除去挙動の典型的なケースが5つ以上あります。このセクションでは、各ケースの基本的な材料の変形と除去のメカニズムを要約します。
<図> 図>従来の加工では、切削深さが刃先半径よりも大幅に大きいため、刃先半径の影響は無視できます。切削深さがナノスケールに減少すると、これはエッジ半径と同等かそれよりも低くなるため、エッジ半径の影響を無視することはできなくなります。ナノカッティングでは、材料除去プロセスは、最先端の半径に大きく影響される押し出し変形によって支配されます。刃先半径効果を除いて、切削深さがさらに原子スケールまで減少するため、新しいサイジング効果である原子サイジング効果[20]は、材料の除去に大きな影響を与えます。
図14に示すように、切削ベースの単一原子層除去プロセスでは、切削に関与する2つの部分、つまり、ナノメートルの刃先と最も低い切削工具原子( B )があります。 )。このような2つの部分を結合して、単一原子層の除去を可能にすることができます。 「ナノツール」と見なされる刃先のサイズは、刃先半径( R )で表されます。 )。刃先は、切削工具の最も外側の原子の包絡線です。最下位の原子については、「アトミックツール」として、ワークピースの原子半径( r )で表されます。 w )。切削ベースの単一原子層の除去は、ワークピース材料に対するナノツールとアトミックツールの連成作用の結果です。
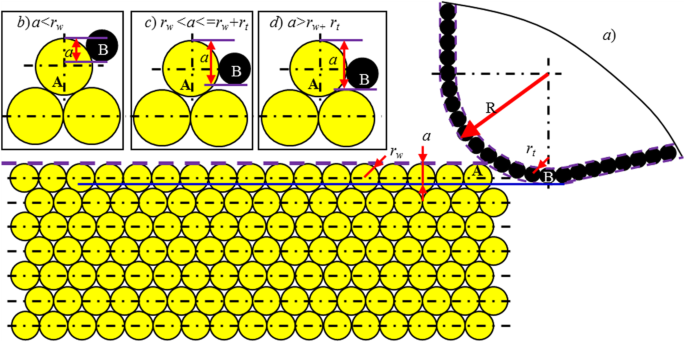
切削ベースの単一原子層除去の概略図
まず、切削深さの比率に応じて( a )ワークピースの原子半径( r w )、つまり a / r 、ACS切断プロセスには3種類の材料変形挙動があります。
- 1。
a / r の比率 w 臨界値1(C 1 。
図15に示すように、切りくずは発生しませんが、ワーク表面に弾性変形が発生します。切削工程では、ワークが切削工具の最下点を通過した後、弾性変形した部分が完全に回復します。その結果、最上面で材料の変形や除去は発生しませんでした。このような場合、ツールエッジ効果は無視できます。この比率は、材料特性の影響を受ける可能性があります(ケース1)。
- 2。
a / r の比率 w C より大きい 1 、ただし臨界値2よりも小さい(C 2 。
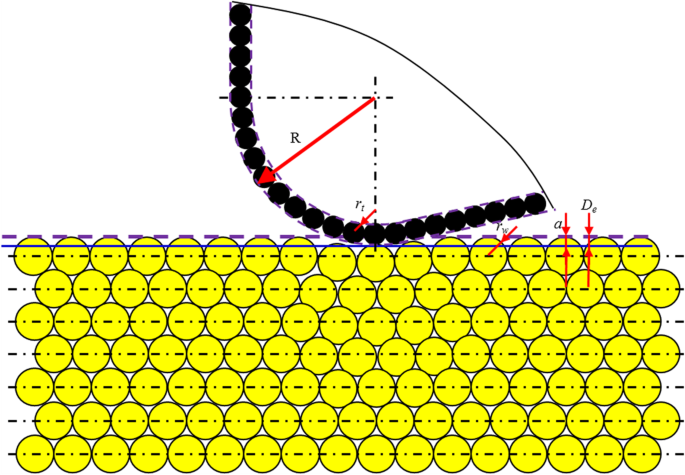
a / r w の比率での切断ベースの単一原子層除去の概略図 C1よりも小さい
原子半径に対する切削深さの比率として( a / r w )C 1 より大きくなるように増加します ただし、臨界値2(C 2 )、ワーク表面に材料の除去がありますが、それは不連続です。このような場合、対象となる原子層内の材料の一部のみがせん断応力による転位運動によってチップに形成され、他の材料はワークピースの表面に残ります。切削工具がワーク表面を通過すると、加工面の表面品質が著しく低下します(ケース2)(図16)。
- 3。
a / r の比率 w 臨界値2(C 2 。
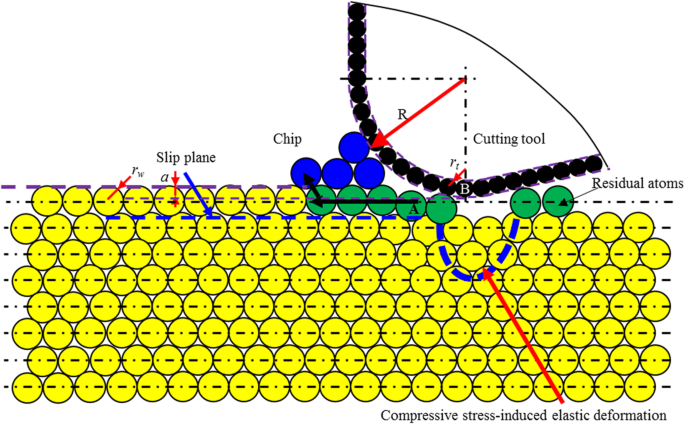
a / r w での切断ベースの単一原子層除去の概略図 C 1 より大きい C 2 よりも小さい
切削深さと原子半径の比率( a / r w )臨界値よりも大きくなるように増加すると、切削プロセス中に切りくず形成による連続的な材料除去があります。このような場合、エッジ半径の影響は無視できなくなります。 ACS切断プロセスの場合、最大切断深さはサブナノメートルオーダーです。このような非常に低い切削深さでは、公称すくい角に関係なく、有効すくい角は常に大きく負になります。負のすくい面は、転位運動による切りくず生成を可能にするために必要なせん断応力と、処理された表面の弾性および/または塑性変形を可能にする圧縮力を生成する可能性があります。
切削深さの比率に応じて( a )工具刃先半径( R )、さまざまな種類の弾性および/または塑性変形プロセスがワークピースの表面で発生します。 a / R には2つのしきい値があります つまり、しきい値1( T 1 )およびしきい値2( T 2 )、さまざまな材料除去プロセスにつながります。
- a。
a / R の比率 しきい値よりも大きい( T 1 。
図17に示すように、1つの原子すべり面があります。この平面より下のワークピースの材料は弾性変形します。このすべり面の上の材料は、転位運動により塑性変形します。材料の一部は、せん断応力による転位運動によってチップに形成され、他の材料は転位すべりを受けます。ワークが切削工具の最下点を通過すると、弾性変形した部分が完全に回復します(ケース3)。
- b。
a / R の比率 しきい値1より低い( T 1 )、ただししきい値2よりも大きい( T 2 。
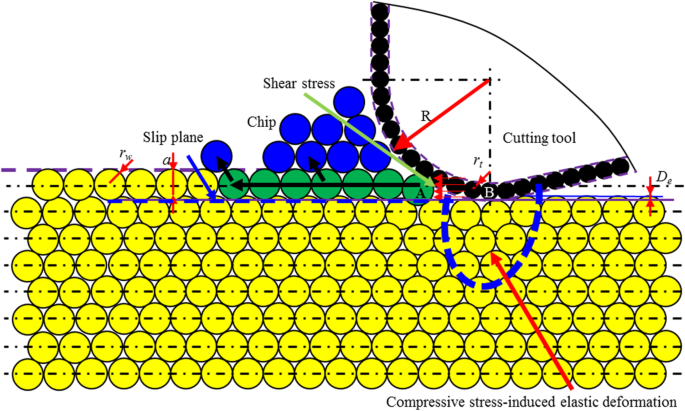
a / r w での切断ベースの単一原子層除去の概略図 C 2 より大きい およびa / RがT 1 より大きい
図18に示すように、刃先の作用により、少なくとも2つの原子層が転位すべりを起こし、加工面に弾性変形が発生します。刃先はせん断応力を発生させる力を与え、転位運動による切りくず生成を可能にします。加工面に弾性変形を誘発する圧縮応力。このような場合、目的の原子層内の材料の一部は転位運動によってチップに形成され、他の材料は他の原子層に押し出されて新しい処理された表面を形成します。また、ワークピース表面の他の原子層の滑りを促進し、負の転位上昇を引き起こします。被削材が切削工具の最下点を通過すると、弾性部分が跳ね返ります(ケース4)。
- c。
a / R の比率 しきい値2( T 2 。
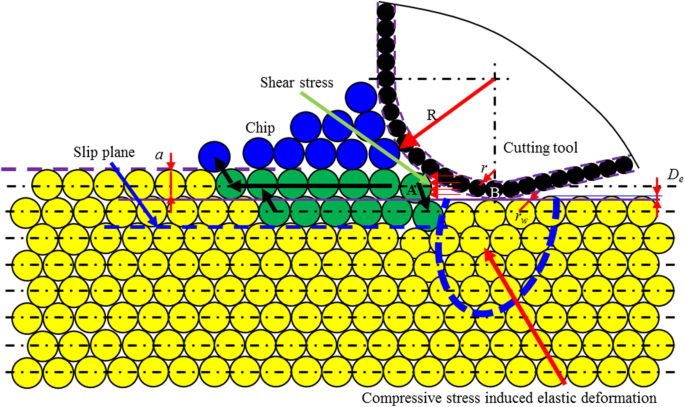
a / r w での切断ベースの単一原子層除去の概略図 C 2 より大きい 、a / RがT 2 より大きい 、T 1 よりも小さい
a / R の比率として T より低くなるまで減少します 2 、切りくずの発生がないか、切りくずの発生量が非常に少ないが、図19に示すように、加工面に弾塑性変形が発生します。被削材が刃先の最下点を通過すると、弾性変形部が跳ね返ります。 。塑性変形部分(Δ )持続的な変形につながります。このような比率は、材料特性、工具形状、およびプロセス条件に関連しています(ケース5)。
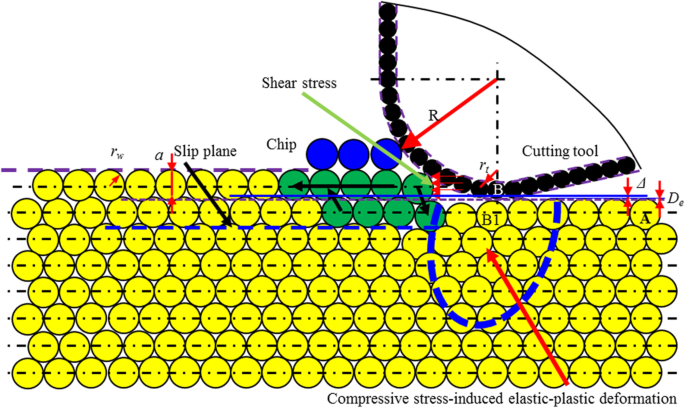
C 2 より大きいa / rでの切断ベースの単一原子層除去の概略図 およびa / RがT 2 よりも低い
結論
本研究では、原子サイジング効果と最先端半径効果の両方を分析して、単結晶銅を単原子層除去に向けて切断する際のチップ形成、表面生成、表面下変形、および原子変位挙動への影響を調査します。次の結論を導き出すことができます。
- 1。
転位運動による切りくず形成、加工面で発生する弾性変形、原子サイジング効果、最先端の半径効果。
- 2。
原子サイジング効果と最先端の半径効果の両方が、単結晶銅の単原子層除去に向けた切断プロセス中の材料の変形と除去に大きな影響を及ぼします。切削深さとワークピースの原子半径の特定の比率( a / r w )および刃先半径までの切削深さ( a / R )、切断ベースの単一原子層の除去は、Cu(111)表面で達成できます。
- 3。
切りくずの形成は、 a / r の比率の影響を受けます w および a / R 。 a / r の比率の場合にのみ、切りくずが形成されます。 w 1つの臨界値(C1)および a / R の比率よりも大きい 1つのしきい値(T1)よりも小さい。さらに、切りくず生成は主にせん断応力による転位運動に依存し、ナノカッティングでの押し出しが支配的な切りくず形成や、従来の機械加工でのせん断が支配的な切りくず形成とは大きく異なります。
- 4。
単一原子層の除去は、層ごとの除去と多層除去によって実現できます。前者は、対象となる原子層をワークピースの表面から完全に取り除くことができることを示しています。後者は、最初の原子層が部分的に除去され、残りの材料が他の原子層に押し込まれ、新しい処理された表面を形成することを意味します。
- 5。
ナノカッティングの弾塑性変形とは異なり、ACSカッティングプロセス中に処理された表面で発生する弾性変形のみがあります。これはACS切断の特徴の1つと見なすことができます。
- 6。
原子サイジング効果と最先端半径効果の複合効果に応じて、切削ベースの単一原子層除去中に材料の変形と除去プロセスの5つのケースが存在します。つまり、ワークピース材料は除去されません(ケース1)、ワークピース材料が非連続的に除去され(ケース2)、材料の一部がチップに形成され、他の材料が転位運動によって材料の滑りを起こし(ケース3)、対象の原子層内の材料の一部がチップに形成され、他の材料が他の材料に押し出されます原子層が新しい処理された表面を形成し(ケース4)、弾性変形部分が跳ね返り、プラスチック変形部分が持続的な変形につながります(ケース5)。
データと資料の可用性
著者は、資料、データ、および関連するプロトコルが読者に利用可能であり、分析に使用されるすべてのデータがこの記事に含まれていることを宣言します。
略語
- ACS:
-
原子および原子に近いスケール
- ACSM:
-
原子および原子に近いスケールの製造
- MD:
-
分子動力学
ナノマテリアル
- マイクロLEDおよびVCSEL用の高度な原子層堆積技術
- AgZnO /ポリオキソメタレートナノコンポジットの基本的なマゼンタ効果の相乗的な光触媒吸着除去
- 原子層堆積と水熱成長によって製造された抗菌性ポリアミド6-ZnO階層型ナノファイバー
- プラズマ化学原子層堆積によって調製されたCo3O4被覆TiO2粉末の光触媒特性
- 超循環原子層堆積によるZnO膜のフェルミ準位調整
- 分子動力学法によるアブレシブナノメートル切削プロセスに及ぼす衝撃方向の影響の研究
- c面GaN上に堆積した原子層AlNの界面および電気的性質への厚さ依存性
- 二酸化炭素を使用したSiO2の低温プラズマ強化原子層堆積
- 原子層堆積によって製造されたAl2O3パッシベーション膜を備えたシリコンナノワイヤヘテロ接合太陽電池
- 静電容量が強化されたスーパーキャパシタ電極用の原子層堆積によって製造されたTiO2ナノメンブレン
- シングルマイターカットとダブルマイターソーの比較