特注のプロセスにより、毎分複合ブレーキペダルが製造されます
Tier 1 Boge Rubber&Plastics Group(ドイツ、ダンメ)は、世界で最も軽く、最も安価で、最強の全複合ブレーキペダルであり、商業生産で最初のものであると述べています。 1月のFODで詳しく説明されているように(「熱可塑性複合構造がセーフティクリティカルなブレーキペダルの金属に取って代わる」を参照)、サプライヤーは現在、ドイツの自動車メーカーが製造する4つの車両プラットフォーム用に年間25万のブレーキペダルを製造しており、システムは最大1つを製造できます。年間100万ペダル。ペダルは構造的であり、既存の鋼やアルミニウムと同じ厳しい性能要件を満たす必要があり、設計には3種類のガラス強化熱可塑性複合材料が採用されているため、これは重要です。
3つの材料が繊維効率を向上させます
ペダルを軽く、薄く、費用対効果が高く、困難なOEM仕様に対応できるようにするために、Bogeはシェル構造として連続ガラス繊維有機シートを使用して、3,000ニュートンもの高さの部品の主な負荷を支えます。有機シートブランクは、サイズに合わせて事前にカットされて提供され、2層または3層は、サプライヤーLanxess Deutschland GmbH(ケルン、ドイツ)によって完全に統合されています。 オルガノシートブランクの主な荷重経路を補強するために、Bogeは、有限要素シミュレーション結果に基づいて、一方向(UD)ガラス繊維テープ(米国テキサス州アーヴィングのCelanese Corp.から提供)のストリップを方向とレイアップに追加します。これを行うために、Bogeは、OEMの顧客が指定した温度と湿度の条件下で各材料について測定された応力/ひずみ曲線に基づいて、同社がサプライヤと共同で開発したソフトウェアと材料カードを使用します。機能的な形状を追加するために、Bogeは(複数のサプライヤーからの)オーバーモールドされたチョップドグラスファイバーコンパウンドを使用して、構造的なリブと取り付け機能を提供します。
すべての材料は、自動車産業で広く使用されている丈夫なポリマーである、着色済みの黒色ポリアミド6(PA6)のマトリックスを備えています。 OEM仕様でそのようなことが要求された場合、Bogeには、オーバーモールディングコンパウンドでより高温で吸湿性の低いPA6 / 6マトリックスを使用するオプションもあります。これは、両方のポリマーが互いに結合するのに十分類似しているためです。 3つの異なる形態のガラス補強材を備えた3つの異なるタイプの複合材料を使用することにより、Bogeは、過剰なエンジニアリングを回避しながら、パフォーマンス要件を満たすために必要な場所に繊維を正確に配置できます。このハイブリッド複合アプローチの継続的な効果は、材料の使用量、公称肉厚、サイクルタイム、および全体的な部品コストを削減することです。
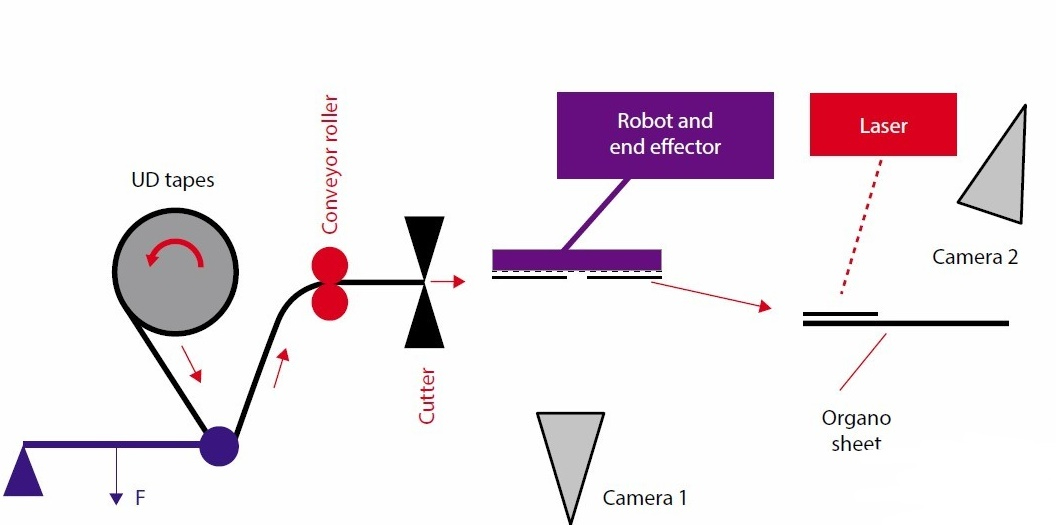
プロセスステップと機器基準
自動化/組立ライン開発者M.A.iとの提携GmbH&Co。KG(ドイツ、クローナハ)のBogeは、高速で効率的で、高品質の部品を手頃なコストで製造する3段階の製造プロセスを開発しました。プロセスと機器の設計において、チームにはいくつかの要件がありました。まず、部品コストを低く抑えるために、企業は総有効サイクル時間を約1分に保つ必要がありました。これを実現するには、材料が製造セル内をスムーズに移動するように自動化する必要があります。
第二に、オルガノシートブランクは事前に積み重ねられ、完全に統合され、サイズに合わせて事前にカットされて提供されますが(輪郭)、さまざまなペダルデザインの要件により、チームはさまざまな場所と方向にさまざまな長さのテープストリップをカット、方向付け、配置して補強する柔軟性が必要でした。有機シートシェルの主な荷重経路。繰り返しになりますが、コストを抑えるために、特注のテープ敷設プロセスは、高レベルの柔軟性と制御、および速度を提供するように設計されました。
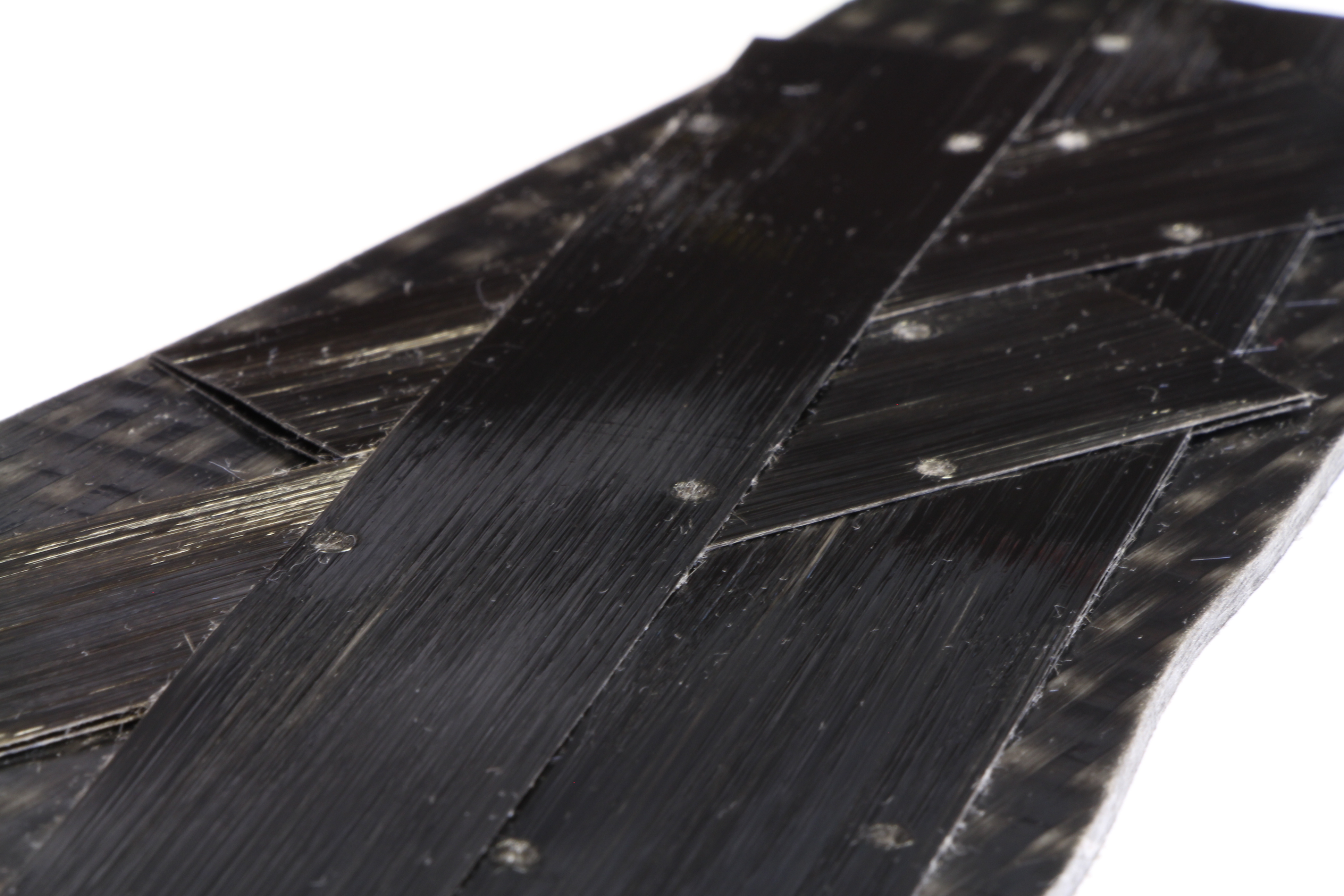
プロセスの開始時に、製造セルはプレカットの2つのスタックを保持します カセット内の有機シートブランクと一度に4クリールのUDテープ。まず、ロボットが有機シートの輪郭のあるブランクを拾い上げ、それを作業面に移動します。同時に、UDテープが送り出され、必要な長さにカットされます。次に、ストリップは、コンベヤーが前進するときにストリップを所定の位置に保持する真空ベルトに配置されます。次に、回転するピックアンドプレースユニット(エンドエフェクター)を備えたロボットが真空ベルトから一度に1つのストリップを引き抜き、カメラが各ストリップの品質、寸法、および位置をチェックします。 4つのピースがすべてピックアップされると、ロボットはワークスペースに移動し、画像ベースの位置補正によって決定された位置と位置で、オルガノシートブランクに一度に1つのストリップを配置し始めます。各ストリップは配置されているため、レーザーによって作成された複数のスポット溶接によってずれることはありません。その間、より多くのテープストリップが切断され、真空ベルトに配置され、特定のブレーキペダルの設計に必要なすべてのテープが積み重ねられ、有機シートの正しい位置に固定されるまで、このプロセスが繰り返されます。
このテーラードファイバーブランクを製造するシステムは、100%数値制御されており、操作のあらゆる側面が完全にプログラム可能であり、最大限の柔軟性が得られます。各ステップで、システムのオンライン品質管理(QC)システムに接続されているカメラまたはその他のセンサーが、テープストリップと有機シートシェルのすべてのエッジと位置を検出し、これらの材料の幾何学的データを既知のパラメーターと比較して、各材料が必要な場所に配置します。
生産速度を高速に保つために、テーラードファイバーブランクは次に赤外線オーブンに移動して、有機シートにテープをドレープ/プリフォーム/統合する直前に両方の材料を加熱します。テープおよび有機シート樹脂システムの特別な酸化防止剤パッケージは、熱による損傷を防ぎます。次に、ホットブランクをドレープ/プリフォーミングキャビティにすばやく移動し、高圧を使用してブランクをUチャネル形状に成形し、高品質の表面を確保します。 QCシステムは、時間、温度、圧力を介して、圧密と予備成形の品質を再度監視します。
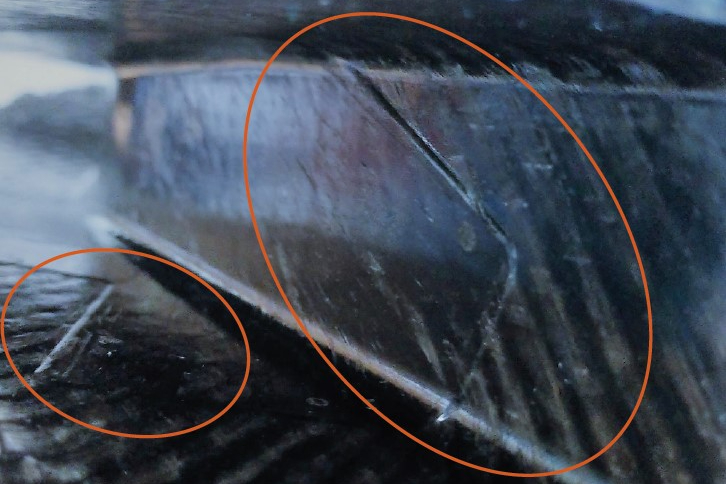
最後に、まだ暖かくドレープされたパフォームが射出成形金型にシャトルされ、そこでショートグラス/ PAコンパウンドでオーバーモールドされて、下側の複雑なリブ構造などの追加のジオメトリが作成されます。離型後、迅速な自動トリムと目視検査が行われます。塗装やその他の表面仕上げは必要ありません。最終的なペダルサイズは約350x 90 x60ミリメートルです。製造セルを離れる前に、固有のQRコードが各ペダルに添付され、品質システム内のそのペダルの製造および材料データにリンクされます。組み立て後、ブラケット内のペダルの機能テストと最終的なロボット検査が実行されます。ユニットが合格すると、完成したブレーキペダルアセンブリに別のQRコードが付加され、OEMに出荷する前に各ペダルと追加コンポーネントの完全なトレーサビリティを提供します。
ブレーキペダルは安全性が重要な部品であり、要求の厳しいOEMパフォーマンスと品質要件を満たす必要があるため、Bogeとそのパートナーは、インダストリー4.0準拠のQCシステムに複数のフェイルセーフメカニズムを組み込み、仕様が各ステップで満たされていることを迅速かつ正確に確認しています。プロセス。 QCデータが保存され、各ペダルはQRコードの形式で一意の識別番号を受け取り、その部品の製造に関連する材料、シフト、およびプロセス条件の100%のトレーサビリティを保証します。
Bogeが製造している全複合ブレーキペダルは、金属製のペダルの約半分の重量です。また、運転中の触覚を改善します 消費者にとっては、寿命の終わりに100%リサイクル可能であり、既存の鋼の強度要件を満たすか、それを上回ります。
樹脂