コンポジット4.0:デジタルトランスフォーメーション、アダプティブプロダクション、新しいパラダイム
Composites 4.0は、インダストリー4.0の世界にある小さな銀河の1つです。これは、商品やサービスの設計、生産、提供、運用、保守、廃止の方法におけるデジタルトランスフォーメーションです。複合材料製造の目標は、自動化、センサーとデータ、5G通信、ソフトウェア、およびその他の継続的に進化するデジタルテクノロジーを使用して、製品とプロセスをより効率的、インテリジェント、適応性のあるものにすることです。
複合材料メーカーは、スペクトルに沿ってこのデジタルトランスフォーメーションを進めています。最初のステップには、インライン検査と最適化されたプロセスが含まれ、部品の品質と歩留まりを向上させながら、無駄とコストを削減します。より高度なソリューションは、アジャイルであるだけでなく、応答し、予測するインテリジェントで自律的な生産に向けて機能します。 変化する市場と顧客の需要。
「コンポジット4.0は終わりではなく、ツールです」と、アーヘン工科大学(ドイツ、アーヘン)のAZLアーヘン統合軽量生産センターのマネージングディレクターであるマイケルエモンツ博士は説明します。自動車のフロアパンのコストを50〜64%削減できる可能性があります。
「物事をデジタル化することと、ビジネスの背後にあるプロセスを実際に変更し、新しい機会とビジネスモデルを開くデジタルトランスフォーメーションとの間には違いがあります」と、複合部品プロデューサーDynexa(ドイツ、ラウデンバッハ)のマネージングディレクターであるChristianKoppenbergは主張します。>>
「コンポジット4.0はロボットを使用しているだけではありません」と、人工知能[AI]を搭載した作業セルを開発したドイツ航空宇宙センター(DLR)の軽量生産技術センター(ZLP、アウグスブルク)の責任者であるマイケルクプケ博士は主張します。協働ロボットは、再プログラミングや再訓練を行うことなく、複合後部圧力バルクヘッドの製造から胴体パネルに切り替えることができます。 「これは、ビジネスケースがないため、ロボットに教える必要がないことを保証するテクノロジーです。 Composites 4.0は、効率の向上とコストの削減だけではありません。どの企業が生き残り、どの企業が生き残れないかを決定するのは、企業が生産について考え、アプローチする方法の変化です。」
アダプティブプリフォーミング、RTM
「iComposite4.0プロジェクトのアイデアは、乾燥した長いガラス繊維(25〜30ミリメートル)をスプレーし、自動繊維配置によって一方向(UD)炭素繊維のグリッドで補強することにより、費用対効果の高いロービングとトウからプリフォームを作成することでした。 (AFP)」とEmontsは説明します。 「選択されたデモンストレーター、リアアンダービークルフロアパンは、以前はより高価なテキスタイルで作られていましたが、これも60%以上の廃棄物を生み出しました。」
Composites 4.0の変換では、繊維の噴霧、繊維の堆積、およびそれに続く樹脂トランスファー成形(RTM)プロセスを統合して、相互に反応させ、ステップ間で測定された部品品質に基づいて適合させる必要がありました(図1)。 「スプレーされたプリフォームの表面トポロジーを特徴づけるために、光学レーザーセンサーとカメラモジュールを備えたApodius GmbH [アーヘン、ドイツ]のマシンビジョンシステムを使用しました」とEmonts氏は言います。 「Apodiusは、各方向の繊維の割合を分析するためにソフトウェアを適応させました。 iComposite 4.0ラインは、これをデジタルデザインと比較し、機械的要件を満たしているかどうかを判断しました。はいの場合、補強のために標準のUDグリッドを適用しました。いいえの場合、追加のUDファイバーレイヤーを配置する場所を決定しました。」
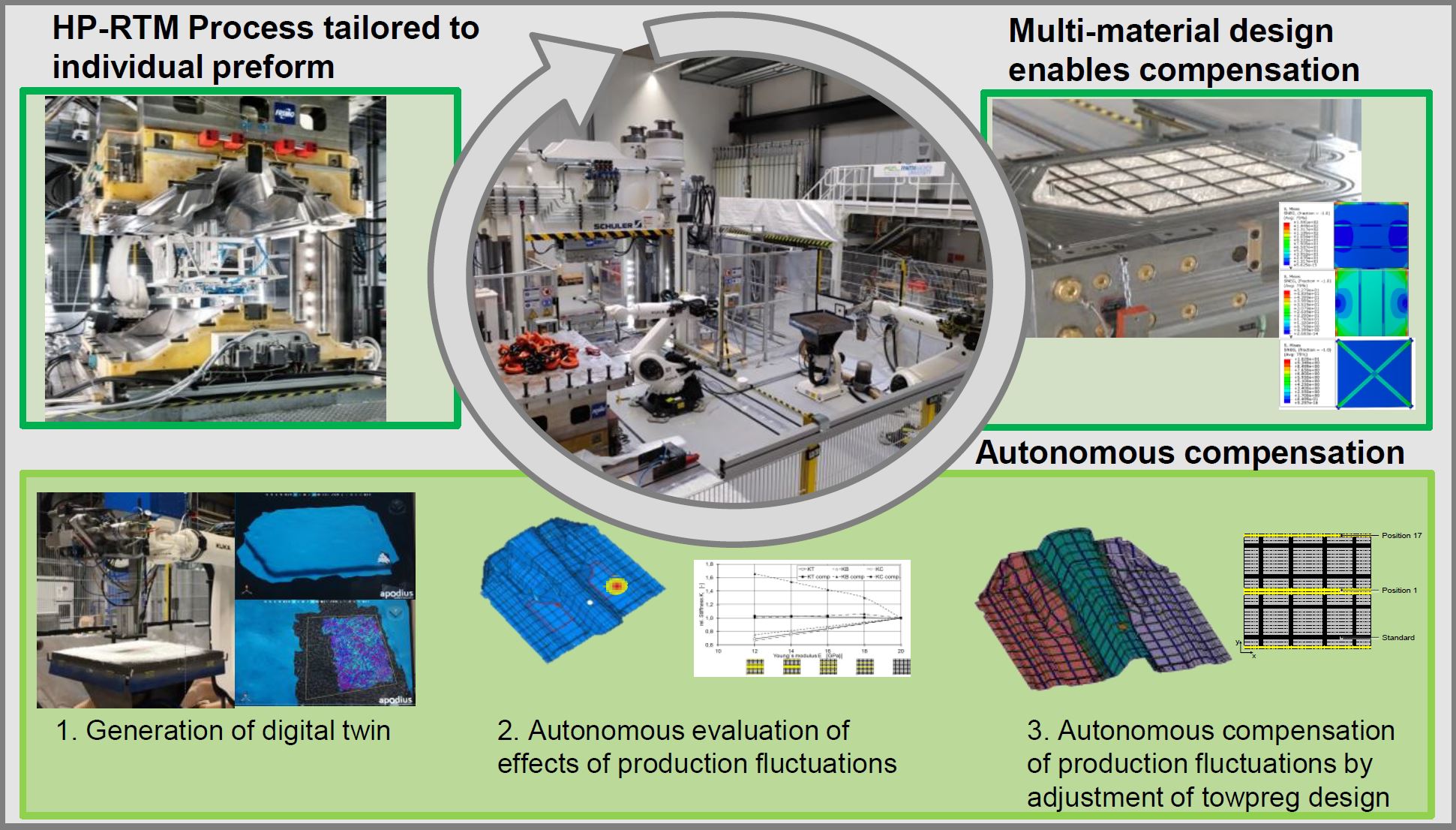
ただし、これらの追加のUDレイヤーにより、パーツの厚さと形状が公差を超える可能性があります。 「したがって、予備成形ラインを適応型RTMプロセスと組み合わせ、必要に応じて、プレスの特定の部品にかかる圧力を上げることで部品の厚さを調整しました」と彼は説明します。これも、ラインオペレーターからの介入を置き換えることを目的として自動化されましたが、測定データと標準のFEAソフトウェアを使用した部品性能のシミュレーションが必要でした。
「現在、部品の機械的特性のシミュレーションはオフラインで実行されています」とEmonts氏は言います。 「プロセスと部品のバリエーションのデータベースを生成し、各バリエーションに対応するアルゴリズムを作成し、FEAを介してこれらを検証しました。したがって、ラインによって測定された変動に基づいて、アルゴリズムは適切な緩和を実行するようにラインに指示しました。ラインを現場で適応させるための次のステップは、機械学習を追加することです。」一方、AZLは、ハイブリッド熱可塑性複合材料の自己最適化生産や、テープベースのテーラードブランクの強化を統合した射出成形部品など、多数のComposite4.0プロジェクトを推進しています。
ゼロディフェクトCFRPウィングスキン
ZAeroプロジェクト(「複合部品のゼロ欠陥製造」を参照)は、2016年に開始されたもう1つの重要なComposites 4.0プロジェクトです。これは、ウィングスキンなどの大型炭素繊維強化プラスチック(CFRP)構造の生産性を向上させることを目的としています。欠陥は、プリプレグAFPまたはDanobat(スペイン、エルゴイバル)の自動乾燥材料配置(ADMP、「乾燥布の実行可能性の証明、大きな航空構造物への注入」を参照)を使用した自動インライン検査を使用することで軽減されます。樹脂注入またはプリプレグ硬化中のプロセス監視は、硬化状態を予測し、サイクルタイムを短縮します。収集されたプロセスおよび欠陥データは、部品の性能を予測するためにFEAで使用されました。次に、これは、特定された欠陥に対処する方法についての意思決定支援ツールに入力されました。 CFRPウィングスキンのパーツフローシミュレーションが開発され、このツールに入力すると、リワーク戦略の最適化に役立ちました(図2)。今日、そのような部品の多くは製造中に再加工されますが、NDIの後でのみです。早期の再加工とプロセス制御の改善は、実際にZAeroプロジェクトの目標であり、生産率を15%向上させ、15〜20%削減することを目標にしています。製造コストと廃棄物の50%削減。
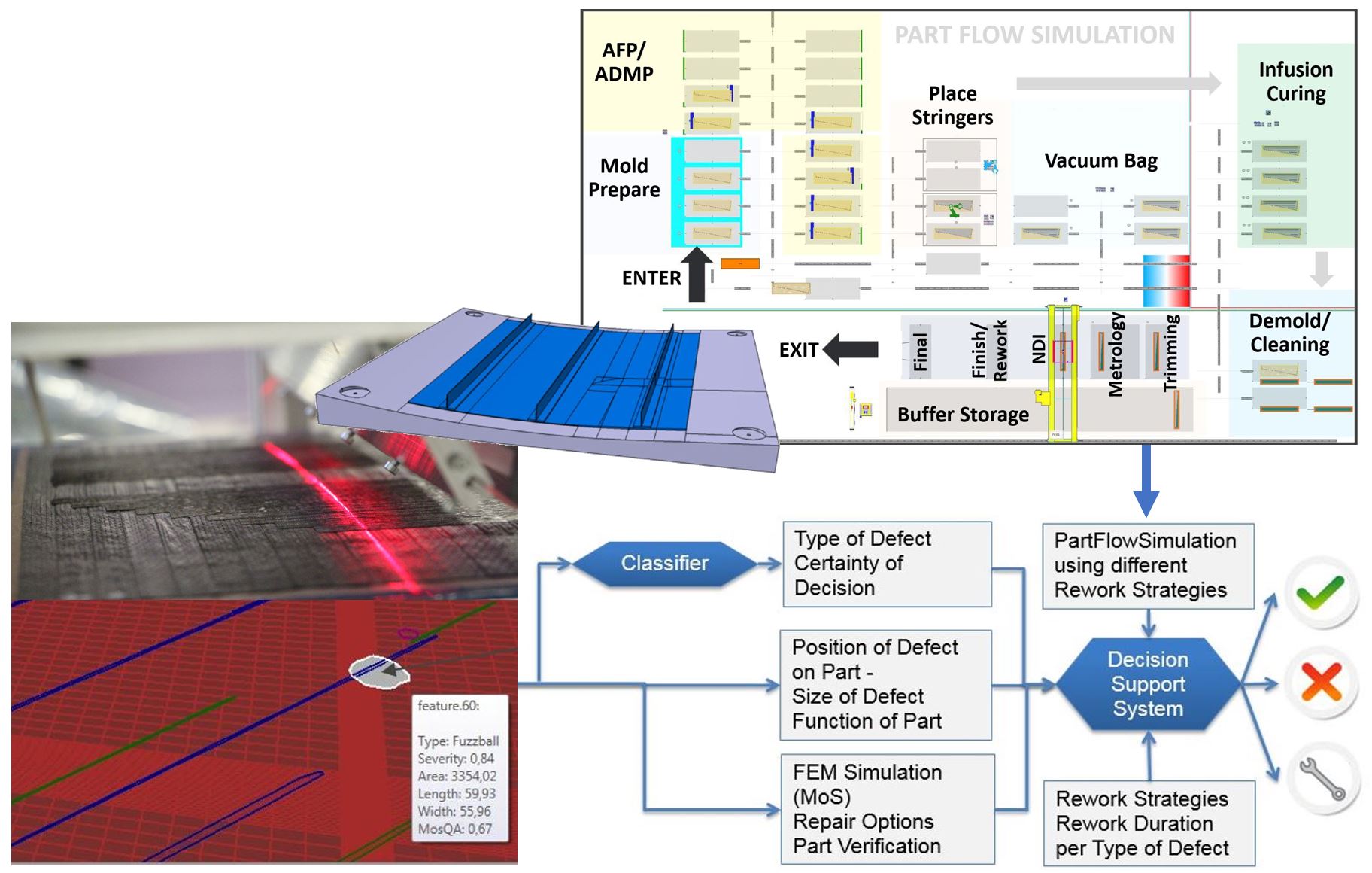
2019年9月の最終レビューまでに、プロジェクトリーダーのProfactor(Steyr、オーストリア)によって開発されたprepreg AFPセンサーは、自動インライン検査を実現しただけでなく、その場で部品を修正するためにも使用できました。 「このセンサーは、ギャップ、オーバーラップ、FOD、ファズボール、ツイストトウなどの標準的な欠陥、および各トウのアーリーカットとレイトカットを検出できます」と、プロファクターのマシンビジョン責任者であるクリスチャンアイツィンガー博士は述べています。欠落しているトウは、追加のトウを省略された場所に正確に配置することで自動的に修正できます。ただし、ファズボールやねじれたトウを取り除くには、機械を停止する必要があります。 「DassaultSystèmes(パリ、フランス)を使用して構築されたCATIAの3Dエクスペリエンスにより、欠陥のサイズ、形状、およびタイプに基づいて、パーツのパフォーマンスへの影響を計算できます。プライ内のすべての欠陥の処理には数秒しかかかりません。次に、機械のオペレーターは、どの欠陥を残すことができ、何をやり直す必要があるかを決定します。」
注入プロセスの監視と制御については、Airbus(フランス、トゥールーズ)が子会社のInFactory Solutions(ドイツ、タウフキルヘン)と協力して、温度、硬化状態、樹脂フローフロントを測定する3つのセンサーを開発しました(「樹脂注入フローフロントを監視するセンサー」を参照)。 )「これらをCATIA 3D Experienceと統合し、データを確実に取得して各部品のデジタルスレッドに追加できることを示しました」とEitzinger氏は述べています。 (オンラインサイドバー「コンポジット4.0:デジタルスレッドとデジタルツイン」を参照してください。)
3部構成のデモンストレーターの最後は、3つのストリンガーを備えた上翼カバーのサブセクションでした(オンラインサイドバー「ZAeroプロジェクトの更新」を参照)。このパートでは、Profactorの意思決定支援ツールがパートナーFIDAMC(スペイン、マドリッド)で実演され、オーストリアのProfactorのサーバーで実行されているSiemens PLM(Plano、Texas、U.S。)Tecnomatix PlantSimulationソフトウェアに基づくパートフローシミュレーションに接続されました。欠陥データベースの構築に加えて、ZAeroは機械学習を使った実験を行いました。手動で設計された生成型コンピューターモデルとディープニューラルネットワークを組み合わせて欠陥を検出および分類し、実際のADMPモニタリングデータでさまざまな領域(ギャップ、オーバーラップ、トウ、ファズボール)を95%正確に分類します。 > 人工的に作成された欠陥データは、ディープネットワークトレーニングに使用されました(超音波試験システムがさまざまな意図的な欠陥に対してどのように較正されているかに類似しています)。
「私たちは間違いなくある種の次の段階を追求します」とEitzingerは言います。一方、Profactorは、自動レイアップ中の繊維配向と欠陥用のモジュラーセンサーを商品化しています。 InFactory Solutionsは、AFPおよび樹脂注入センサーも提供しており、ファイバー配置パートナーのDanobatおよびMTorres(Torres de Elorz、スペイン、ナバラ)は、統合されたインライン検査を備えた機器を販売しています。
Dynexaのデジタルトランスフォーメーションの旅
Dynexaは、CFRPチューブとシャフトを専門とする複合部品メーカーです。 「私たちは常にすべてをデジタル化しようとしてきました」とマネージングディレクターのコッペンベルグは言います。 「私たちはすでに手動およびアナログプロセスを排除し、ほとんどすべてをERP [エンタープライズリソースプランニング]システムに統合しました。しかし、製造業でこれをどのように行うのでしょうか?ワーカープロトコルまたはプロシージャに入れるものはすべてコードであり、これがデジタルトランスフォーメーションの基礎であることを理解しました。しかし、それはどこに保存されていますか?ローカルサーバー、クラウド、またはマシン内? 5人に聞いて、何をすべきかについて7つの答えを得るでしょう。」 (オンラインサイドバー「コンポジット4.0:どこから始めればよいですか?」を参照してください)
幸いなことに、ドイツ政府は、中小企業(SME)に無料のインダストリー4.0コンサルティングを提供する大学向けのプログラムを設定しました。 Dynexaは、Darmstadt「Mittelstand(SME)4.0」コンピテンスセンターでの作業を開始しました。 「彼らはデジタルアーキテクチャについて心配するのではなく、測定する必要のあるものとその方法にもっと目を向けると言っていました」とコッペンベルグは回想します。 「私たちは、品質、時間、コストの問題があることを知っていた、重要な手動測定を伴うプロセスを1つ選びました。」
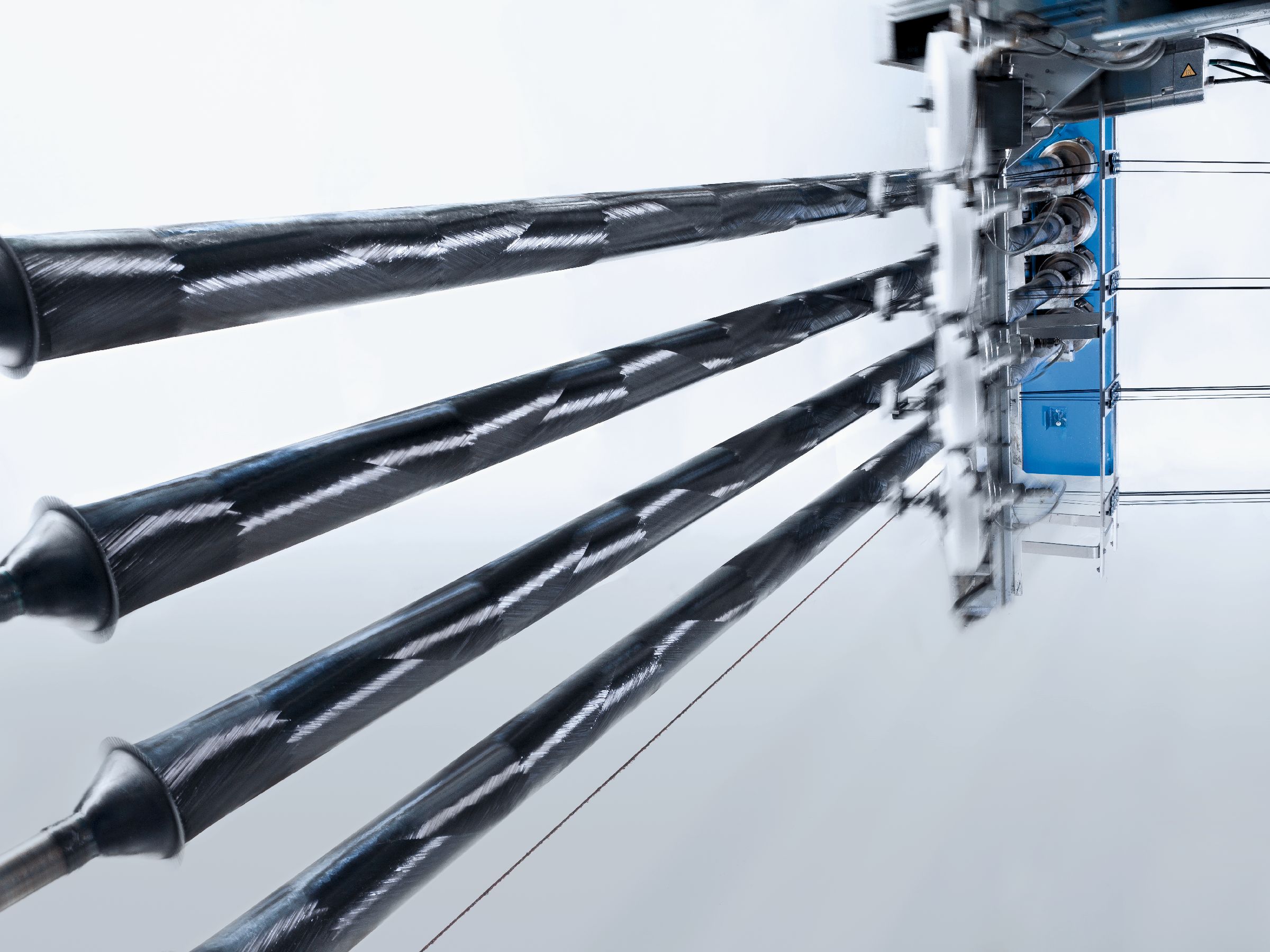
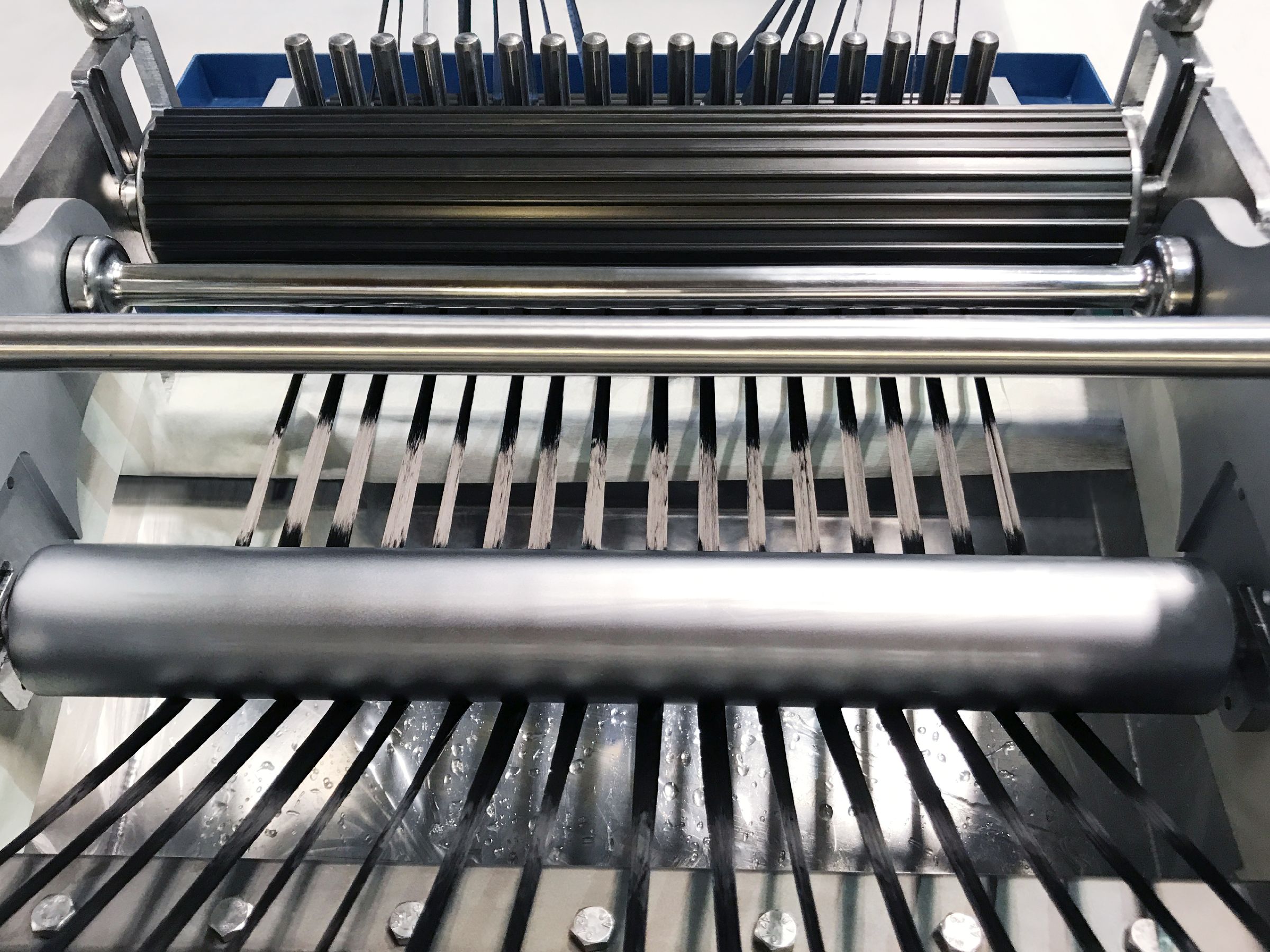
Dynexaは、ウェットフィラメントワインディングプロセスを使用しています(「自動車の試験場に対応する複合出力シャフト」を参照)。重要なステップは、樹脂のピックアップです。コンパクションローラーの前に座っているのはドクターブレードで、乾いたフィラメントを巻く前に組み合わせる樹脂の量を決定します。 「樹脂を取りすぎると、指定されたチューブの直径を超える可能性があります。ただし、樹脂が少なすぎると、許容される最小直径を下回るリスクがあります。」
「測定せずに、すべての価値が投資されたとき、あなたは硬化後の最終的な直径しか知りません」と彼は指摘します。 「したがって、オペレーターは機械を停止し、部品を測定し、書き留めてから再起動する必要があります。長年の経験から、巻線の各段階でのラミネートの厚さはどのくらいであるかがわかります。したがって、オペレーターは測定値を比較し、必要に応じて樹脂のピックアップを修正するためにドクターブレードを調整しますが、これは非常に手動であり、オペレーターのスキルと経験に依存します。」
これをデジタル化するために、Dynexaは無数のレーザーおよびカメラメーカーと話をしました。 「彼らは「私たちは解決策を持っている」と言うでしょうが、それでは誰もそれを機能させることができませんでした」とコッペンベルグは述べています。しかし、ダルムシュタット大学のチームは、濡れた表面からの光の反射など、特定の物理的要因のために必要な補正を把握することで、カメラの使用を可能にしました。 「これで、非常に標準化された方法で動作する巻線機が測定装置に接続されました」と彼は付け加えます。
チームは、修正テーブルと決定アルゴリズムのデータベースを開発しました。これにより、フィラメントワインディングマシンは、巻き付けられる特定のチューブの各ステージでターゲットが何である必要があるかを知ることができます。 「測定装置の入力により、樹脂のピックアップが本来あるべき場所にないことが示された場合、フィラメントワインディングマシンは、ドクターブレードを調整して、測定のための巻き取りを停止せずに、ドクターブレードを仕様に戻すことで応答します。」
>現在、すべての巻線機にはデジタル測定システムがあり、および イーサネットカード。 「最も費用のかかる部分は、サーバーへのケーブルの設置と配線でした。しかし、今ではすべてのマシンと通信して、すべてのデータを収集できます」とKoppenberg氏は言います。そして、別の利点があります。 「以前は、オペレーターはマシンでプログラミングを行っていましたが、サーバーに接続すると、任意のデスクトップまたはラップトップコンピューターでプログラミングできます。これにより、ダウンタイムがさらに短縮され、別の生産のボトルネックが解消されました。」
この最初のデジタルステップにより、Dynexaはプロセス制御、品質、効率を改善し、費用対効果を高めることができました。それはまた、さらなる変革に拍車をかけました。
コンポジットのパラダイムの変更
「私たちは、お客様に新しいエコシステムを提供する段階的なプロセスにあります」と、Dynexaの販売およびマーケティング責任者であるMatthiasBruckhoffは述べています。彼は例を挙げています。「Amazonでは、購入したものと時期、および提案された新製品を確認できます。以前は、顧客の要件を取り入れてから、計算ツールとエンジニアリングツールを使用して数日で対応していました。今、これはオンラインになります。お客様は製品を見て、必要なもの、コスト、納期を数分で計算します。これは新しいものではありませんが、 私たちの業界のために。機械オペレーターを解放して、より多くの機械とより高いレベルのタスクに集中できるようになりました。これから、エンジニアリングチームを解放して、より専門的で洗練された製品に集中できるようになります。」
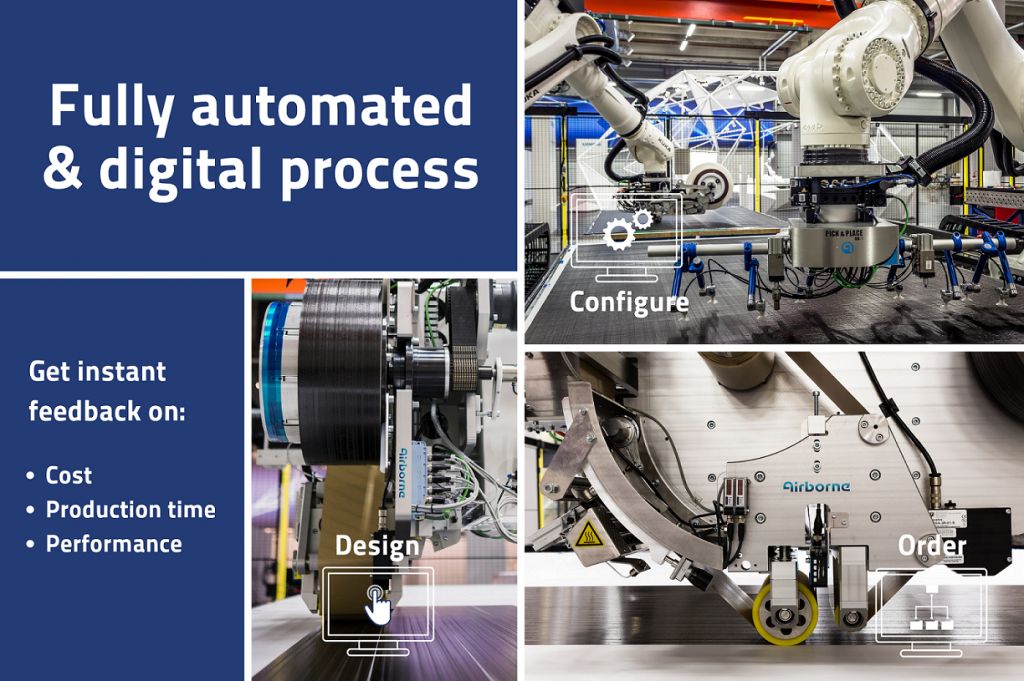
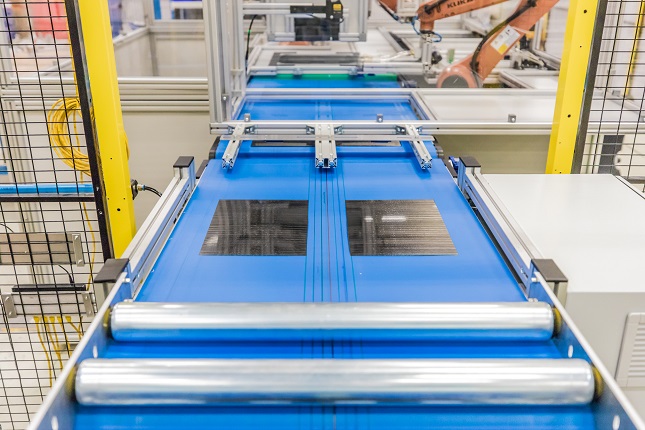
Airborne(オランダ、ハーグ)は、2019年9月に複合材料の自動製造のためのオンデマンド製造ポータルを立ち上げました(「Airborneが複合印刷ポータルを立ち上げました」を参照)。このツールを使用して、顧客はWebベースのプラットフォームにデザインを入力します。次に、システムはその場でマシンコードを作成し、生産期間とコストを決定します。その後、製品をカスタマイズして、注文すると自動製造セルで製造できます。ポータルは、熱硬化性プリプレグを処理するためにAirborneの自動ラミネートセル(ALC)を使用して起動されました。これは他のプロセスにも拡張されます。たとえば、SABIC(サウジアラビア、リヤド)のスペシャリティビジネスユニット向けに開発された大量の熱可塑性複合材料(TPC)の生産ラインです。
「このポータルは、複合材料製造のデジタルの未来をどのように捉えるかを示す重要な構成要素です」と、Airborneの最高技術責任者であるMarcusKremersは述べています。 「5年前、私たちは部品製造のビジネスモデルから、自動化とデジタル化で顧客を支援することに変わりました。お客様がコンポジットを使用して簡単に構築できるようにするソリューションのポートフォリオを開発しています。」このポートフォリオには、ALC、自動ハニカムポッティング、自動プライキッティング、およびSABICのDigital Composites Manufacturing Line(DCML)およびAirborneのFalconと呼ばれるTPCテープを使用した大量生産ラインが含まれます。後者は、Airborneの特注ソリューションの例です。 「私たちは、複合材料と部品製造の知識をこれらの自動化システムに組み込んでいるため、顧客は専門家である必要はありません」とクレマーズ氏は言います。
Airborneには3つのビジネスモデルがあります。自動化を購入するか、レンタルするか、Airborneに任せて、サービスとしての製造(MaaS)を介して運用します。空中自動セルには、顧客が定義した欠陥と許容範囲のデータベースに基づいてアラートを生成するセンサーとインライン検査システムがあります。 「ファルコンラインは、視覚的な品質の欠陥に対する許容度が非常に低いです」とクレマーズ氏は述べています。「しかし、航空宇宙の自動化は、構造的な許容範囲によってさらに推進されています。また、自己学習と自己適応を実現するために、テクノロジーを継続的に進歩させています。たとえば、ALCテープ敷設用の次のソフトウェアバージョンには、欠陥を特定し、その場で生産プログラムを修正する機能があります。」
長期的には、オンデマンドポータルを拡張して、複数の企業や地域に分散している複合部品の生産能力を収集することがビジョンです。 Kremersは、Protolabs(Maple Plains、Minn。、U.S。)を引用しています。これは、射出成形、板金、CNC機械加工、または3Dプリントのプロトタイプをわずか1日でオンデマンドで提供します。同様に、Plyable(英国、オックスフォード)のオンラインアプリは、複合材料を製造するための金型を提供し、複合材料や3D印刷ツールを含むポリウレタンボードから鋼までの材料を提供します。 「これは、バリューチェーンを整理するための別の方法です」とKremers氏は言います。 「私たちは、複合部品でこれを可能にする機械とソフトウェアを作っています。」
AZL Aachenは、5秒未満で多層TPCラミネートを製造するために開発された、超高速コンソリデーターマシンでもこの目標を追求しています。 2019年に商品化され、Conbility(アーヘン、ドイツ)のロボット、レーザー支援AFPアプリケーター、25 mm幅のUDテープ、およびピースフローの原理(高速印刷業界の最先端)を使用しています。局所的な補強材を使用して、さまざまな厚さで、単純にタックまたは完全に統合されたTPCラミネートを製造します。 「私たちのビジョンは、オンラインプラットフォームを可能にするスケーラブルなマシンを提供することです」とEmonts氏は言います。 「回線には複数のステーションを含めることができ、それぞれに複数のAFPアプリケーターがあります。顧客は要件を入力し、プライブック、コスト、および配送のオプションを取得します。完成すると、アプリケーターはオペレーターではなく、生産を整理するために互いに通信します。これは、テーラードコンポジットの完全にインテリジェントな製造です。」
自動化の自動化
ZLPの主な焦点は、CFRP構造の自動生産です。 「一部またはプログラムの自動化を正当化するのは困難です」と、柔軟な自動化のZLPチームリーダーであるFlorianKrebs氏は述べています。 「しかし、タスク固有のマシンを超えて、追加のセットアップをほとんど行わずに再構成可能な自動化プラットフォームに移行すれば、ビジネスソリューションが得られます。プラットフォームの柔軟性が高いほど、投資収益率は速くなります。」
冒頭の画像に示されているワークセルは、ZLPプロジェクトPROTEC NSRの一部として設計されており、同じプロセスルート(乾燥したノンクリンプファブリックのピックアンドプレースレイアップと樹脂注入)に従うパーツのファミリーを構築します(オンラインサイドバー「いいえロボットを教えるためのビジネスケース」)。 「このプロセスはエアバスA350後部圧力隔壁用に設計されましたが、手順が類似しているため、このラインで胴体パネルまたは翼カバーを作成することもできます」とクレブス氏は言います。
「柔軟な自動化プラットフォームを実現するには、ロボットのアルゴリズム、センサー、およびロボットが生成するデータを理解する方法など、特定のテクノロジーブリックが必要です」とKupke氏は言います。 「たとえば、PROTEC NSR生産ラインは、最大のモジュール性を目指して設計されています。すべてのモジュールが相互接続され、サイズと複雑さがスケーラブルな自己構成、修正、最適化システムを実証します。」
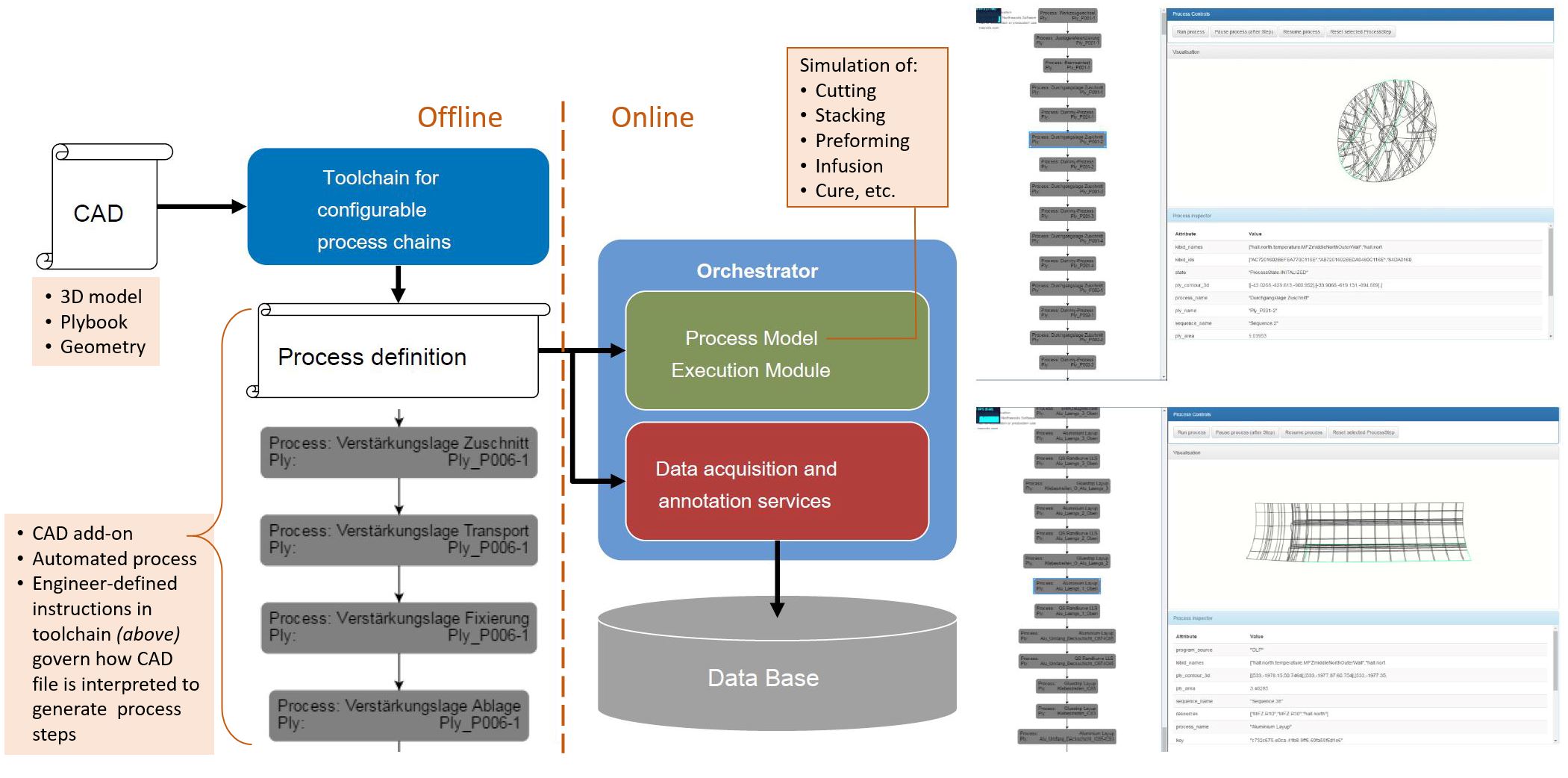
彼は、図5に示すように、CADモデル、プロセス定義、プロセスのシミュレーションと実行を可能にするプロセスモデル、製造実行モジュール、データを取得するセンサー、データに注釈を付けるソフトウェア、およびストレージ用のデータベースを含むモジュールについて説明します。
「この図の左側で、計画を立てます。次に、実行モジュールがその計画を実装します」とKupke氏は言います。 「プロセスステップでは、カッター、ロボット、建物(温度、圧力、湿度)、ピックアンドプレース中のカメラなど、関連するすべての機械とプロセスからデータを取得します。データを分析します。プロセス中にリアルタイムで、また収集されたデータにメタデータで自動的に注釈を付けてデータベースにフィードします。これは、プロセスのデジタルツインの基礎を形成します。デジタルツインの最も重要なポイントは、1つの中央リポジトリと1つの信頼できる情報源を持つことです。各パーツのCADモデルとプロセス定義は、信頼できる唯一の情報源の一部です。」
これらのモジュールを配置すると、ボタンを押すだけで回線が自律的に動作します。 CADモデル、生産計画、カメラから、ロボットは次に来るカットピースを推測し、テーブル上でそれを探します(たとえば、他の100個のカットピースから)。 「彼らは、グリッパーを持ち上げて工具に置くようにグリッパーを構成する方法を決定し、それをどこに配置するかを知っています。」ロボットは、生産計画に基づいて、すべてのプロセスステップの各開始/終了パスを決定し、それぞれがいつ完了するかを認識します。 「通常、これらのパスは人間によって教えられます」とKupke氏は述べています。 「しかし、私たちのシステムでは、各パスは自動的に、衝突がなく、リアルタイムで定義されます。 CADモデルまたはプロセス定義を変更すると、ロボットは追加の教育作業なしで適応します。しかし、パーツを完全に変更するとどうなりますか?このタイプの自動化を使用すると、その変更を非常に迅速に行うことができます。これがフレキシブル生産への道です。 ZLPでの私たちの役割は、テクノロジーブリックを開発し、それらをリンクすることによって、このルートを開くことです。」
機会とオントロジー
COVID-19のパンデミックは、柔軟な生産の価値を浮き彫りにしました。また、ますます予測不可能なビジネス環境を生み出しています。 「過去2〜3年で、すべてがより不安定になりました」とDynexaのBruckhoffは述べています。 「私たちの顧客は、顧客に対応するために、非常に迅速な回答を求めています。新しいオンラインエコシステムを提供することで、サプライチェーン全体の競争力を高めます。」
これは、航空業界でよく知られています。 「水平統合と垂直統合の両方を可能にする生産ラインとサイト全体のデジタル基盤が必要です」と、VDIの航空宇宙技術技術部門の議長であるドイツエンジニア協会および複合技術センター(CTC、COO)のMarcFetteは述べています。シュターデ、ドイツ)、エアバスのR&T子会社。 Composites 4.0のCTCプロジェクトには、材料と資産の追跡、協働ロボット、高度なプロセスチェーンなどが含まれます。しかし、Fetteは、オントロジーの必要性を強調しています。これは、デジタル通信とデータ交換のための用語と一般的なプロトコルです。 (オンラインサイドバー「Composites4.0アーキテクチャとオントロジー」を参照してください。)
「特定のプラントのすべての機械と生産システムに総合的なネットワークが必要です」と彼は説明します。「しかし、これはエンジニアリング、調達、ロジスティクス、材料、プロセス認証などの分野を含む、価値創造チェーン全体にも及ぶ必要があります。 、 一方では。一方、サプライヤなどのすべての利害関係者は、この変更プロセスを考慮して関与する必要があります。多くのパイロットプロジェクトがありますが、詳細に見ると、企業または生産チェーンごとの全体的なアプローチの戦略がまだ不足しています。」
彼は次のように続けています。「当社には非常に大規模なグローバルなサプライヤーネットワークがあり、デジタル接続されたサプライチェーンとして機能するためには同じ要件があります。当社のサプライヤーのほとんどは、エアバスとボーイングの両方の航空機メーカーで働く中小企業です。共通の基準についての議論がない場合は、これらの課題をサプライヤーに伝えます。ほとんどの場合、ドキュメント、データの評価、サイバーセキュリティなど、すべてのマシンについて2セットの異なる標準に準拠する余裕はありません。」
Fetteは、これらは大きなアイデアであると認めており、航空機のOEMはこれらの課題に対処するための計画を作成していると述べています。 「しかし、このような多くの障害があり、テクノロジーだけでなく、社会的、経済的、人間工学的、法的な問題を含む非常に複雑です。これは精神的な変化のプロセスです。まだ始まったばかりです。しかし、成功するには、これらの新しいシステムは人に依存しており、これらの人はOEMだけでなく、グローバルネットワーク全体に参加している必要があることを理解する必要があります。」
「市場はすべての業界で細分化されており、誰もがパラダイムシフトに直面しています」とZLPのKrebs氏は述べています。 「多くの人はそれをチャンスとは考えていません」とZLPのKupkeは付け加えます。しかし、その機会を見た人は、Composites 4.0によって可能になったコンポジットへの民主化されたアクセスを想定しており、それにより、私たちが考え始めたばかりのアプリケーションを含む、はるかに広い市場が生まれます。
樹脂
- CPG製造におけるデジタルトランスフォーメーションの最適化
- デジタルトランスフォーメーション戦略には新しい才能のアプローチが必要
- データ駆動型デジタルトランスフォーメーションがエアバスを新たな高みへと駆り立てる
- デジタルトランスフォーメーションの新時代は、公益事業セクターをどのように変えていますか?
- エボニックが新しいPA12生産施設を建設
- デジタルトランスフォーメーションの成功を計画する
- 製造業におけるデジタルトランスフォーメーションとは何ですか?
- デジタルトランスフォーメーションの7つの推進要因
- 製造業におけるデジタルトランスフォーメーションの課題
- デジタルマニュファクチャリングの変革:新年の抱負
- GE Digital:進行中のデジタルトランスフォーメーションの旅