ソリューションベースのデジタル複合材料の製造
自然は、驚くほど強く、用途が広く、適応性があり、環境に応じて成長し機能する構造を構築します。木、骨、キチンについて考えてみてください。後者はハードシェルとの両方を形成します 甲殻類の柔軟な関節。自然の構造物は、廃棄物をほとんどまたはまったく生成せず、エネルギーをほとんど必要とせず、機能寿命の終わりにリサイクルされます。対照的に、人工建造物は通常、規範的であり、大量のエネルギーを消費し、有毒な廃棄物を生成し、ほとんどがリサイクルされません。米国環境保護庁の2018年のデータによると、リサイクルされる材料の割合は、プラスチックで9%(2010年以降変化なし)、ガラスで25%、金属で33%(どちらも2010年から減少)です。デジタル設計と製造は急速に進歩し、洗練された多機能の構造とコンポーネントの生産を可能にしていますが、これらの技術はまだ持続可能性に同じように浸透していません。
これは、2013年にマサチューセッツ工科大学(MIT、ケンブリッジ、マサチューセッツ州、米国)メディアラボのMediated Matter Groupによって開発された水ベースのデジタル製造プロジェクトのインスピレーションと目的でした。このイニシアチブは、新しいデジタル製造を開発しました。地球で最も豊富な天然素材と、さまざまな濃度のバイオコンポジット溶液を堆積させるロボット制御のマルチチャンバー押出システム(最初は甲殻類の殻からのキチンと酢酸)を組み合わせて、異方性のある構造を作成する技術。機械的、化学的、光学的特性の勾配は、ミリメートルからメートルまでの長さスケールで生成され、独自の形状と多機能性だけでなく、構造的自己組織化の可能性も実現します。たとえば、湿式堆積物は、多層複合材料内の方向性蒸発応力に応答して、乾燥時に形状(たとえば、円柱)を形成するように設計できます。
このソリューションベースのデジタルファブリケーションは、持続可能な建築パネル、リサイクル可能なパッケージ、消費財、または軽量の生分解性自動車部品に応用できる可能性のある、生物学的環境と構築環境の間の架け橋として構想されました。 MITは最終的に、セルロースマイクロファイバー、ペクチン、藻類、セラミックナノプレートレットを使用した複合材料を調査しました。しかし、この水ベースのデジタル蒸着と、今日の3D印刷複合材料で急速に進歩している連続的で短い繊維強化添加剤押出技術を組み合わせることができたらどうでしょうか?
なぜキトサン溶液なのか?
水ベースのデジタル製造プロジェクトの最初の実験では、キチンに由来するキトサンを使用しました。セルロースに次いで地球上で2番目に豊富な天然高分子であるキチンは、セルロースと同様の化学構造を持ち、甲殻類や昆虫の高弾性、高靭性の殻だけでなく、それらの関節に見られる強力でありながら柔軟な組織も含みます。天然素材、特にキチンやセルロースなどのポリマーや多糖類は、人工合成ポリマーよりもはるかに高い速度で生産される膨大な再生可能資源を提供します、とこのプロジェクトの主要なMIT研究者の1人であるLaiaMogas-Soldevilaは説明します。彼女は、多糖類誘導体が既存の石油化学ベースのポリマーに取って代わり、新しい特性の組み合わせを提供し、より持続可能な製造を可能にする可能性があると主張しています。
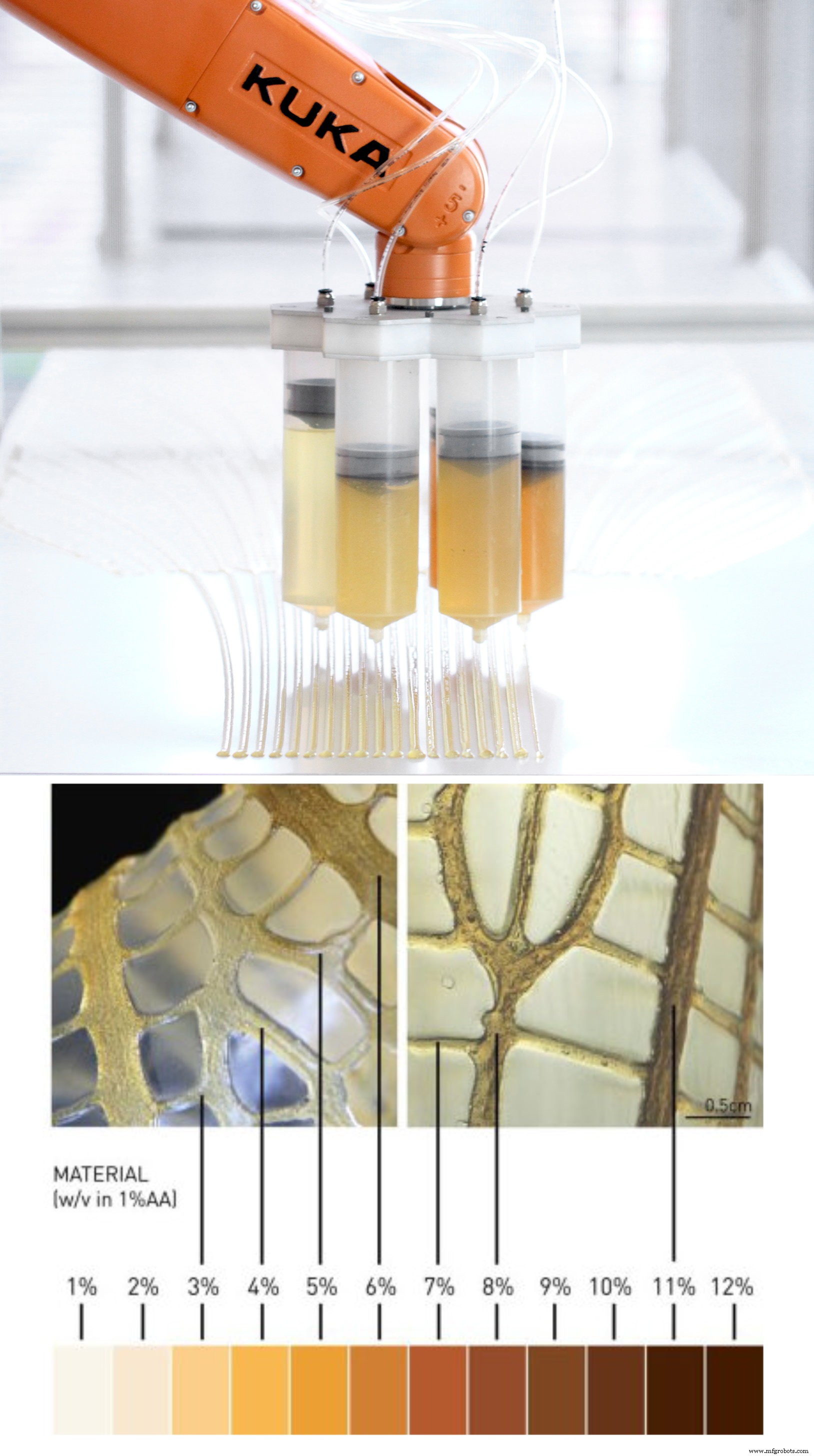
Mogas-Soldevilaは、2015年の論文「水ベースのデジタル設計と製造:キトサンとその複合材料の印刷における材料、製品、およびアーキテクチャの調査」で、MIT技術開発の優れた概要を説明しています。彼女は、ソリューションベースのデジタルファブリケーションを使用するというアイデアは、インクジェットおよびノズルベースのバイオファブリケーション手法を研究して、組織成長の足場として柔らかい材料を製造することから生まれたと説明しています。
水溶液中の4%w / v酢酸を使用して、1〜12%の重量対体積(w / v)濃度でゲルに加工されたキトサン粉末を使用して、ノズルベースの3D堆積を試みることにしました。これらのヒドロゲルは、3%の濃度で水っぽい蜂蜜のような粘度を持つ半透明の液体から、12%の濃度で天然ゴムの粘稠度を持つ不透明な材料までの範囲でした(図1)。堆積および乾燥の初期結果 キトサンフィルムは、40メガパスカルの極限引張強さを示しました。これは、Mogas-Soldevilaが、繊維の方向でナイロンポリマーまたは木材に匹敵すると説明しています。 構造物は室温で製造および硬化されました。
新しいデジタルマニュファクチャリングプラットフォーム
MITがキトサンゲルを堆積させるために設計したカスタムロボット積層造形プラットフォームは、KUKA(ドイツ、アウグスブルク)Agilus KR1100 6軸ロボットアーム(10キログラムのペイロードと±0.03ミリメートルの再現性/精度を備えた54キログラムのプラットフォーム)を組み合わせたものです。押し出しベースのエンドエフェクタ。新しいエンドエフェクターには、デジタルPSIレギュレーターと押し出しを制御するツインステッパーモーターを備えた正(圧縮空気タンク)と負(真空ポンプ)の空気圧を含むコンピューター制御の空気圧システムに接続されたキトサンヒドロゲル用の6つのバレルが含まれていました。
このエンドエフェクターの重量は、装填された注射器と沈着物を含めて4キログラムでした。典型的な流量は、内径が0.5〜8ミリメートルに及ぶノズルを使用して、毎秒8〜4,000立方ミリメートルの範囲でした。システムの線形運動は、毎秒10〜50ミリメートルの範囲で変化しました。堆積領域は長さ1,000ミリメートル、幅500ミリメートルでしたが、長さの制限は後でスライド式のプリントベッドを介して取り除かれました。
ステッパーモーター、空気圧システム、ロボットアームはデジタル制御され、供給/速度比を調整し、可変混合比と押出速度を可能にし、必要な押出形状と材料特性に基づいて堆積圧力と速度をオンザフライで調整します。ロボットの動きと押し出しは明示的にリンクされていませんでした。つまり、両方の機能が互いに独立していたため、各モーター駆動シリンジの独立した制御と、ロボットアームのエンドエフェクターの変位が可能になりました。このシステムは、型を使わずに大規模な3D形状を作成することに成功し、さまざまな構造特性を備えたさまざまな幾何学的形状を実現しました。
デジタル設計から堆積まで
最初の製造試験は、葉やトンボの羽などの生物学的構造に基づいていました。主要な縦方向の構造は、より厚い直径の堆積物とより高い剛性のための材料濃度で作られた全体的な形状を提供しました。次に、二次構造は、より薄い直径およびより低い濃度の材料の堆積されたネットワークによって形成された。製造システムは、これらの構造を構築するためにいくつかの技術を使用しました。特定の経路に沿って異なる濃度の溶液を適用し、堆積中の圧力をデジタル制御して材料の幅と高さを制御し、層状化を繰り返します。これらの戦略は、位置、速度、圧力、および材料の指示にエンコードされ、KUKAロボット(位置決め)および押し出しエンドエフェクター(堆積)にリアルタイムで送信されました。
まず、構造をCADプログラムでモデル化し、カスタムスライシングソフトウェアがこれを印刷レイヤーに変換しました。デジタル制御システムは、堆積経路をテストして最適化しました。押し出しシステムの制御と操作を提供する幾何学的なツールパスは、Rhino3Dモデリングソフトウェア(Robert McNeel and Associates、米国)とそのスクリプトプラグインGrasshopperを使用して設計されました。
次に、システムは、デジタル設計に関連する一連の独立したパラメータと、基本的な機械的および化学的材料特性をエンコードしました。また、粘度、せん断速度、バレルタイプ、ハードウェア応答時間、エンベロープサイズなど、製造システムによって与えられるプラットフォームに依存する制約を緩和しました。次に、これらすべてのパラメータをデザイン固有と組み合わせました。 ノズルタイプ、材料組成、時間依存の圧力マップなどのバリエーション。結果として得られる計算は、必要な流量、バレルの補充パターン、および位置決め速度を出力します。最後に、カスタム製造命令が生成され、モーションコマンドと押し出しコマンドがそれぞれ位置決めシステムと堆積システムにエンコードされました。
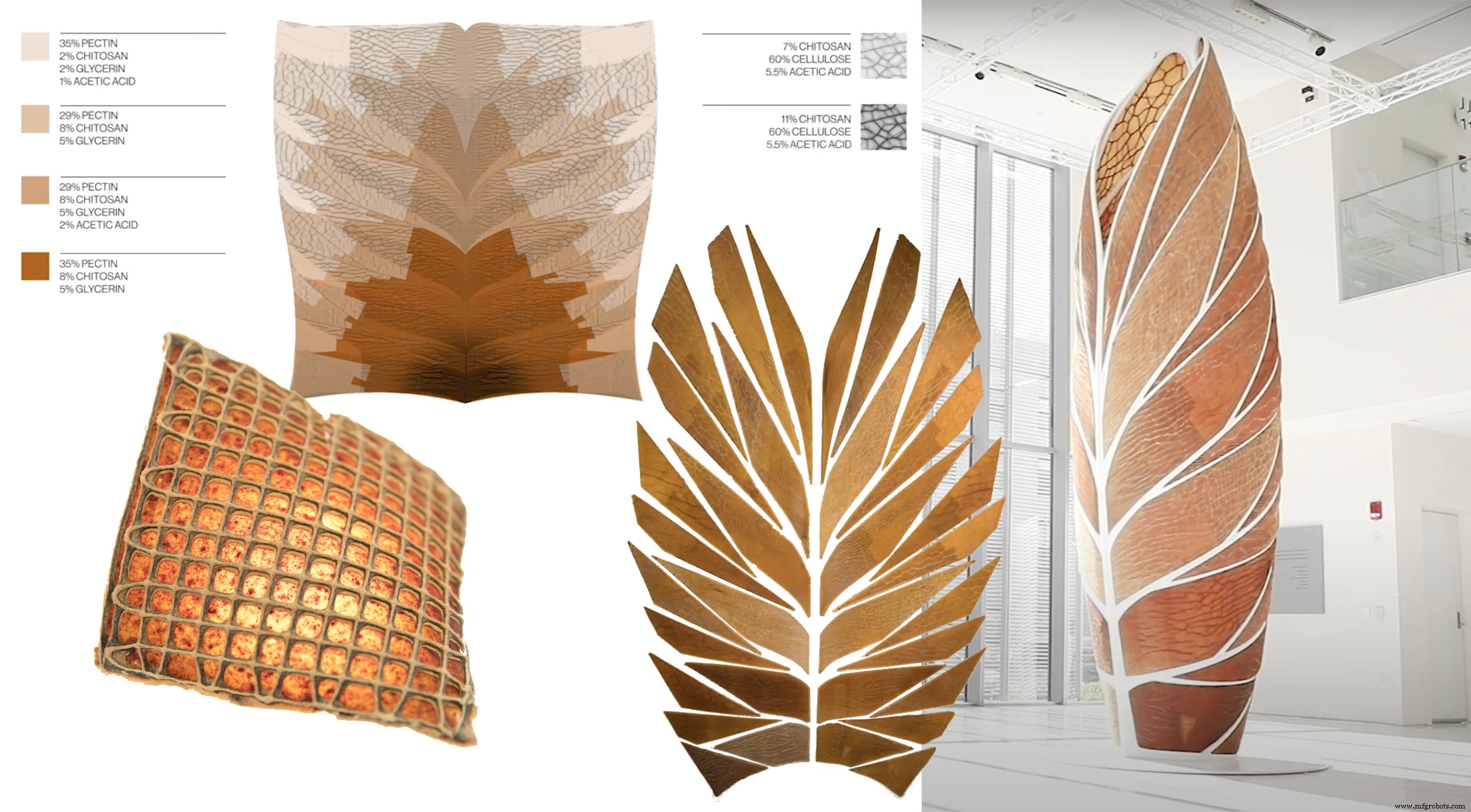
新しい構造の探索
Mogas-Soldevilaによって記述された製造試験には、トンボの翅に触発された長さ50センチの構造が含まれています。その構造上の「静脈」は、天然のアルギン酸ナトリウム粉末で増粘されたキトサンゲルから作られ、その上に3%キトサンゲルの透明な耐張力膜が重ねられています。材料の自己修復特性により、膜は堆積中に静脈に結合しました。この概念は、長さ3メートルまでのさまざまな葉のような構造でさらに探求されました。別の例では、2%キトサンゲル中のセルロースマイクロファイバーの溶液を使用して、5 x15ミリメートルのグリッドを平らに堆積させました。乾燥すると、前述のように内部蒸発応力を設計する機能を使用して、長さ50センチメートルのシリンダーが形成されました。
この技術は、ネリ・オックスマン教授の下でMIT Mediated MatterGroupの建築家兼エンジニア兼主任研究員であるJorgeDuro-Royoによって開拓され、皮膚のような構造(「hojas」)が作成および成形されたAguahojaプロジェクトでさらに開発されました。水ベースのソリューション(「アグア」)。 Aquahoja Iには、高さ5メートルの建築パビリオン(図2)と、2018年に展示され、サンフランシスコ近代美術館(SFMOMA、カリフォルニア州、米国)が永久コレクションとして取得した材料実験のライブラリが含まれていました。 。 Aguahoja IIは、Cube Design Museum(オランダ、ケルクラーデ)とCooper Hewitt、Smithsonian Design Museum(ニューヨーク、ニューヨーク、米国)が共催した2019年の展示会の一部でした。
Aguahojaプロジェクトのロボット製造プラットフォームは、ロボットベースのシステムとガントリーベースのシステムの両方を含むように進化しました。パビリオンは、95の個別の3Dプリントセグメントで構成されていました。白い背骨は、既製のF900溶融堆積モデリング(FDM)システムとアクリロニトリルスチレンアクリレート(ASA)熱可塑性プラスチックを使用して印刷されました。複数のバイオコンポジットパネルは、構造、窓、環境フィルターとして機能する領域を作成するために、さまざまな程度の剛性、柔軟性、不透明度で設計されました。アグアホジャの素材の中には、湿気や熱に反応して変化するものもあれば、季節の変化に応じて暗くなったり明るくなったりするものもあります。材料は、もろくて透明なものから柔軟で革のようなものまでさまざまですが、すべてが水中で劣化するようにプログラムでき(雨など)、それによって構成要素の構成要素を自然の生態系に復元します。
Mogas-Soldevilaはその後、タフツバイオメディカルエンジニアリング(米国マサチューセッツ州メドフォード)内のThe Silklabで博士号を取得し、MITで働いていたものを含め、シルクやその他の天然繊維や素材の使用方法を検討しています。彼女は現在、ペンシルベニア大学スチュアートワイツマンデザイン大学院の建築助教授であり、持続可能性と最先端のライフサイエンスの交差点で材料駆動型デザインを教え、研究しています。彼女の最近の作品のいくつかはdumolab.comで見つけることができます。 「これらは自然から生まれた素材であり、非常に簡単に機能させることができます。私たちはそれらを混ぜ合わせ、ドープし、変形させることができます。実際に特定の製造能力に合わせて調整することができます。明日は何を考えていますか。」
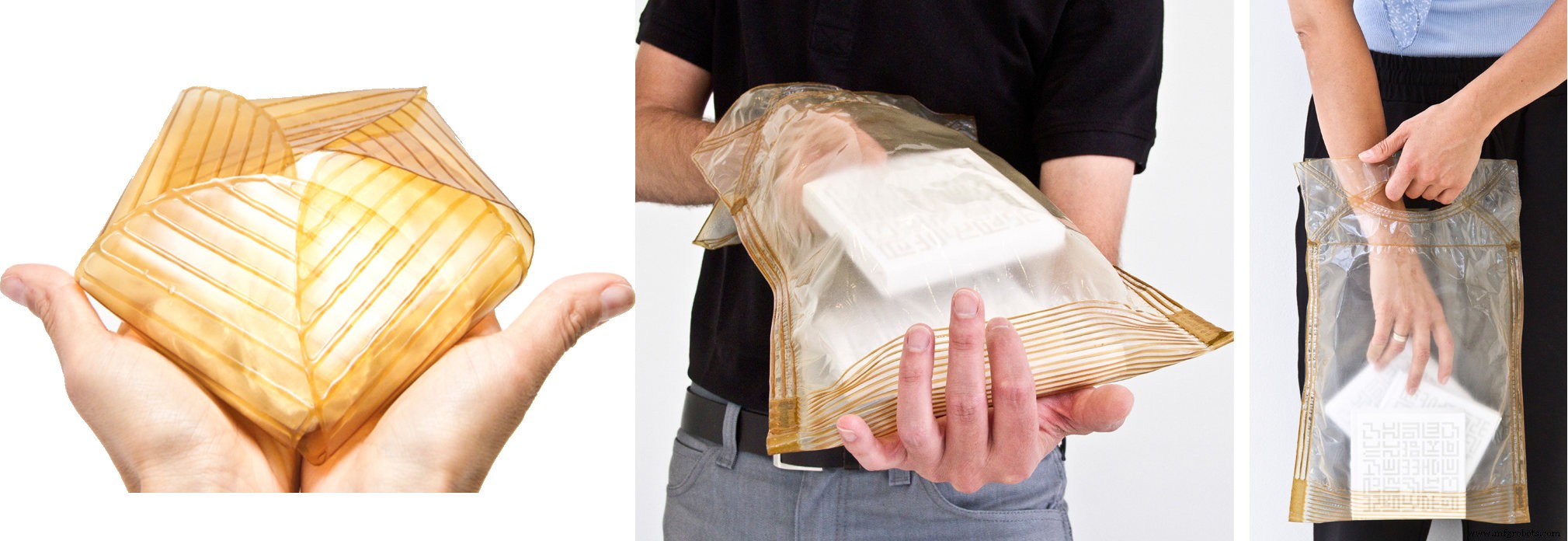
複合材料