将来の航空構造物の生産のための圧縮RTM
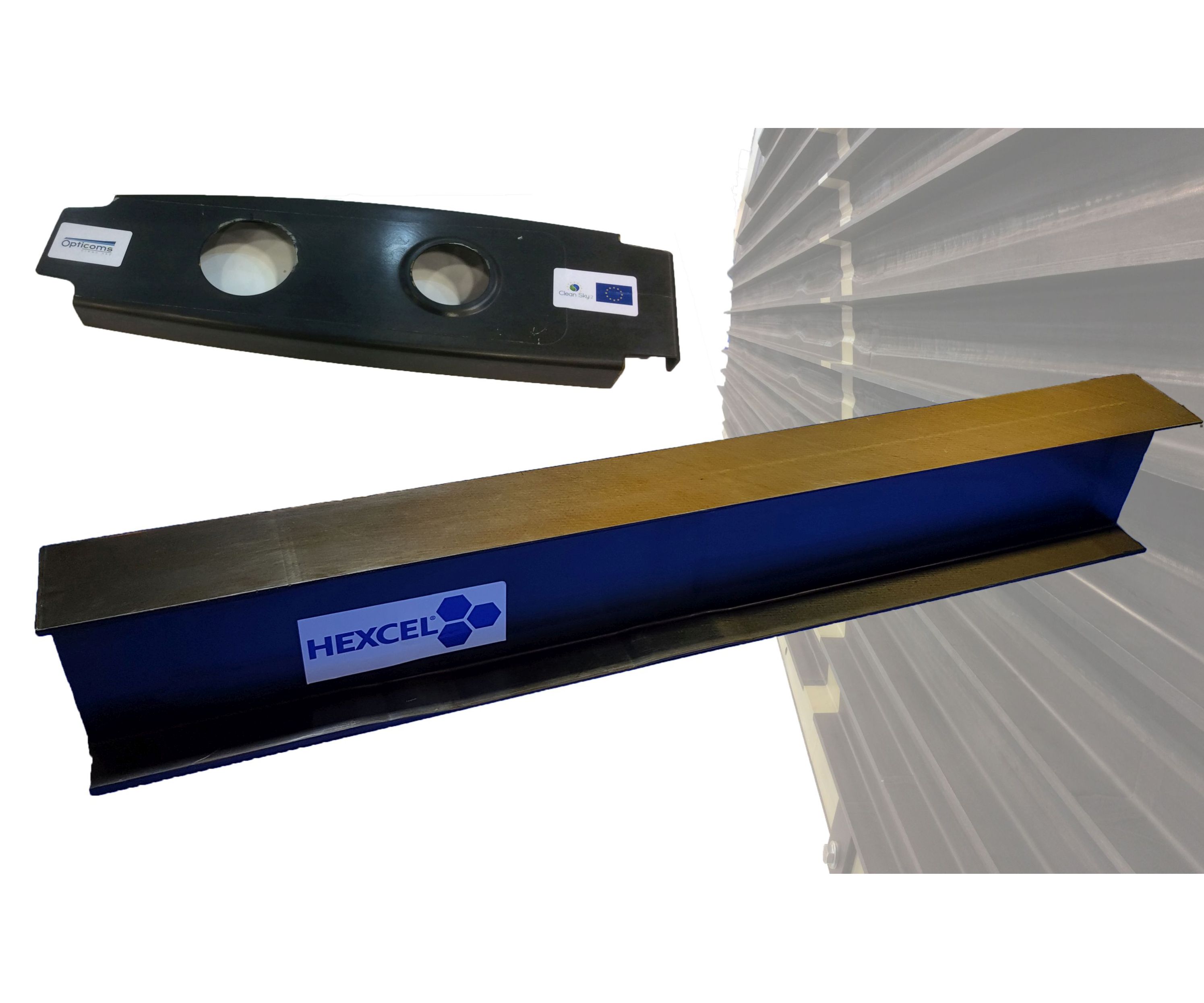
複合材は、金属に比べてメンテナンスコストが低く、高強度で軽量の構造を可能にするため、民間旅客機の機体で恒久的な地位を確保しています。ワイドボディ機とナローボディ機の両方の次世代の現在の予測は、複合機体の継続的な成長を示していますが、それは、材料とプロセスが低コストと高生産率という困難な目標を達成できる場合に限られます。オートクレーブ硬化エポキシプリプレグは、これまで炭素繊維強化ポリマー(CFRP)エアフレームで最高の地位を占めてきましたが、次世代航空機の開発者は、自動化とインライン検査を統合したアウトオブオートクレーブ(OOA)テクノロジーを積極的に追求しています。将来のインダストリー4.0の生産。
機器および自動化のサプライヤーであるTechni-ModulEngineering(Coudes、France)およびその米国子会社であるComposite Alliance Corp.(Dallas、Texas、US)は、先進材料サプライヤーであるHexcel(Stamford、Conn。、US)の英国およびフランスのビジネスユニットと提携しています。 CFRPリブとストリンガーの自動OOA生産を実証するため。部品は、Hexcel乾式炭素繊維強化材の自動予備成形とHexcel HexFlow RTM6液体エポキシ樹脂の高速浸透を提供する圧縮樹脂トランスファー成形(C-RTM)プロセスで作られ、繊維体積が60%、ボイドが1%未満の部品を製造します。 2.5〜3.0時間のサイクルで、高速生産用に複数の部品を生産するようにスケーリングできます。
乾式補強材の開発
「液体複合成形(LCM)は、コストを削減し、レートに対応し、一次構造のパフォーマンスを提供するという3方向の課題に対する答えを提供するものと考えています」とRémyPagnacは説明します。 液体複合成形用のHexcelテクニカルサポートエンジニア。 Hexcelは、LCMプロセスを使用する際の一次構造のパフォーマンスのニーズに対応するために、HiMaxノンクリンプファブリック(NCF)およびHiTape一方向(UD)炭素繊維材料を開発しました。 HiMaxを使用すると、ウィングスキンなどの大きくて平らな構造物をすばやくレイアップできます。一方、HiTapeを使用すると、無駄を最小限に抑えて、大きくて複雑な構造物に合わせたレイアップを行うことができます。 「最新世代のUDプリプレグと同等の特性を実現できます」とPagnac氏は付け加えます。
Hexcelは、HiMax NCFを使用して、かさばりを減らし、ドレープ性を向上させるために取り組んできました。これには、細い20dTexステッチヤーンが含まれます。 HiMaxの材料は、Hexcelが2016年に買収した英国レスターの以前のFormax施設で製造されています。この施設で製造された軽量のスプレッドトウ多軸は、レーシングヨット、スーパーカー、フォーミュラなどの要求の厳しいアプリケーションにソリューションを提供してきた長い歴史があります。 1台のレースカー。現在、NCF材料は、エアバスディフェンスアンドスペース(エアバスDS、カディス、スペイン)とダノバット(エルゴイバル、スペイン)が、後者の自動乾燥材料配置(ADMP)テクノロジー(自動繊維配置の一種)を使用して完了した翼デモンストレータープロジェクトで使用されています。 (AFP)NCF(「大型航空構造物の乾式布地注入の実行可能性の証明」を参照)—およびエアバスが後援するストリンガー補強ウィングスキンなどの欠陥ゼロCFRP構造物のZAeroプロジェクト(「複合部品のゼロ欠陥製造」を参照) 」)。
Hexcelは、HiMaxとHiTapeの両方を使用して、バインダーとして機能する薄い、低面積の熱可塑性フィラメントベールの層を統合し、予備成形や液体成形用の乾燥材料でこれまで使用されてきた粉末バインダーの必要性を排除します。 HiMaxの場合、このベールはNCFプライの間に挿入されます。 HiTapeの場合、ベールはカーボンファイバーユニテープの両側に適用されます。 「これにより、UD層を所定の位置に保持するために粉末バインダーを使用する必要がなくなります」とPagnac氏は説明します。 「HiTapeはキャリブレーションされており、スリットテープではないため、毛羽立ちがなく、幅のばらつきが少ないため、AFP処理が向上します。熱可塑性ベールはまた、最終的なラミネートに靭性を追加し、次世代のAFPマシンで高い材料堆積率を達成できることを実証しました。」 2015年5月のSAMPEの論文で、Hexcelは、レーザーを備えたCoriolis Composites(Quéven、フランス)AFPマシンをレイアップ速度1メートル/秒で適用した幅0.25インチのHiTapeを使用して製造された単一湾曲プリフォームについて説明しています。また、Electroimpact(Mukilteo、WA、U.S。)AFP機器と連携して、フルサイズのスパー航空構造で最大150キログラム/時間の堆積速度を実証しました。
図。 1圧縮RTM
C-RTMでは、ドライプリフォームはRTM金型に配置されますが、金型は部分的にしかありません。 閉じて、乾燥したプリフォームと上部の金型表面の間にギャップを残します。次に、真空が適用され、樹脂が注入され、プレスによって金型のギャップが閉じられ、液体樹脂が部品全体でz方向にプリフォームに押し下げられます。ソース|ヘクセル

航空宇宙向けのC-RTMの適応
C-RTMは、自動車用複合材料用の高圧RTM(HP-RTM)で最初に導入されました。従来のRTMと同様に、C-RTMでは、乾式繊維プリフォームを対応する金型に配置し、液体樹脂をプリフォームに注入してから、作動プレスを使用して熱と圧力を加えます。ただし、C-RTMでは、カビは部分的にしかありません。 閉じて、乾いたプリフォームと金型上部の表面の間に隙間を残します(図1)。次に真空が適用され、正確な量の混合樹脂が注入され、プレスによって金型のギャップが閉じられ、液体樹脂が部品全体でz方向にプリフォームに押し込まれます。 「これは、部品から面内に樹脂を注入するよりもはるかに高速です」と、Techni-ModulEngineeringのプロセスエンジニアであるThomasChevallet氏は説明します。
Techni-Modul Engineeringは、Clean Sky2の「OptimizedCompositeStructures」(OPTICOMS)プロジェクトのパートナーとしての役割の中で、C-RTMを航空宇宙に適応させる機会を見ました。作業パッケージB-1.2(「より手頃な複合構造」)内で編成されたOPTICOMSは、統合構造と自動製造により小型航空機(地域のジェット旅客機など)の製造コストを削減し、プリプレグと液体樹脂の両方の方法を検討することを目的としています。 OPTICOMSは、3つのスパーを備えた上部翼スキンで構成される複合翼デモンストレーターを設計し、ワンショットプロセスで統合された構造として製造されました。実物大の翼(図2)は、2025年以降に生産される次世代航空機の技術準備レベル(TRL)6に向けて技術を評価および成熟させるための、AIRFRAME Innovative Technology Demonstrator(ITD)の一部です。イスラエル航空宇宙産業(イスラエル、ロード)は、2016年7月にOPTICOMSのコーディネーターに選ばれました。このコンソーシアムには、小型航空機OEMピアジオエアロスペース(イタリア、サヴォーナ)、Techni-Modul Engineering、AFP機器サプライヤーのCoriolisCompositesとDanobatも含まれています。
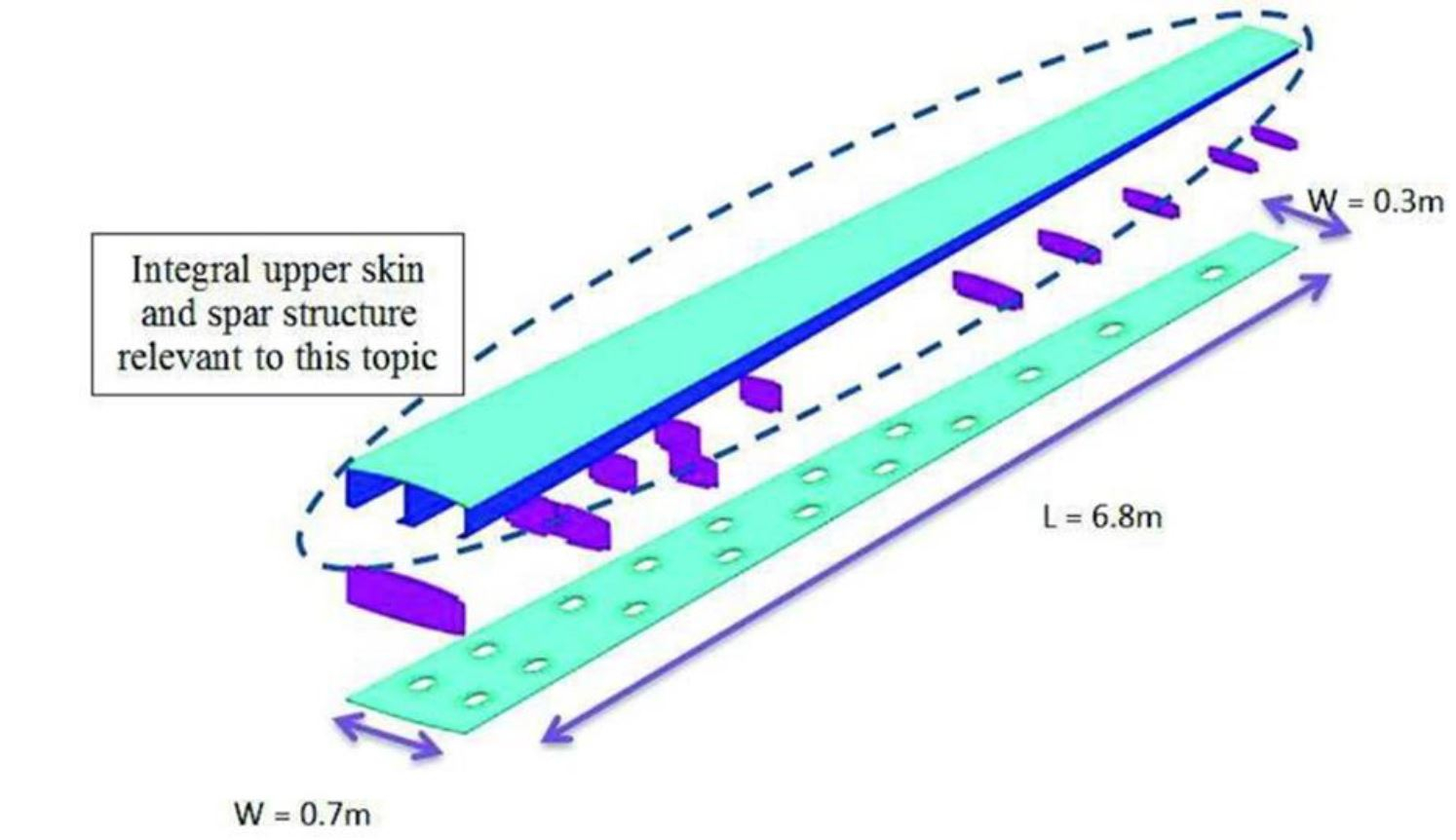
図。 2 Clean Sky 2OPTICOMSリブ
Techni-Modulは、Clean Sky 2の「OptimizedCompositeStructures」(OPTICOMS)プロジェクトのパートナーです。このプロジェクトでは、下部ウィングスキン、複数のリブ、および3つのスパーを備えた上部ウィングスキンで構成される複合翼デモンストレーターを設計しました。後者は、ワンショットプロセスで統合された構造として生成されます。デモンストレーターは、2025年以降に生産される次世代航空機について評価されます。ソース|クリーンスカイ2
「C-RTMは業界でよく知られていました」とChevallet氏は説明します。「しかし、HP-RTMでは、依然として大きな報道機関が必要です。私たちの開発は、C-RTMを低圧を使用した高速射出に適合させ、高繊維量、繊維配列、および低ボイドの非常に厳しい要件を備えた航空宇宙部品の低コスト生産を可能にすることでした。 OPTICOMSプロジェクトでは、長さ0.7メートル×幅0.2メートルのウィングリブの注入時間が40分から5分に短縮されました。長さ900ミリメートル、高さ150ミリメートルのIビームストリンガーの別のテストプログラムでは、注入時間が1時間から5分未満に短縮されました。

「C-RTMによって提供されるこの射出時間の短縮は、フルウィングスキンやヘリコプターのローターブレードなどの大きな部品ではさらに大きくなります」とChevallet氏は付け加えます。彼は、C-RTMは、高粘度樹脂の射出、低圧射出システム、低トン数のプレスも可能にし、コストを削減できると述べています。 「C-RTM中の金型圧力はわずか6バールで、HP-RTMで使用される圧力よりもはるかに低くなっています」とChevallet氏は説明します。 「このプロセスにより、航空宇宙品質の複合材料が実現されますが、大きくて薄い部品や、小さくて複雑な形状の部品にも適しています。」
自動プリフォーム
より高速で低コストの樹脂射出とOOA成形は、より手頃なエアロコンポジット生産のためのこのアプローチの重要な部分ですが、プロセスチェーンでは、材料の切断とレイアップ、および予備成形に複数のステップが必要です。 「私たちにとって、OPTICOMSは自動化にも関わっていました」とChevallet氏は言います。 Techni-Modul Engineeringは、OPTICOMSプロジェクト用のC-RTM噴射システムだけでなく、ピックアンドプレースロボットとホットドレープフォーミング(HDF)マシンも提供し、すべて完全に自動化された生産セルに統合されました。
2016年にOPTICOMSが開始された直後、Techni-Modul Engineeringの子会社であるCACは、CAMX 2016(9月26〜29日、米国カリフォルニア州アナハイム)で、自動3Dプリフォーミングセルの製造部門でACE Equipment and Tooling InnovationAwardを受賞しました。ドライファイバーまたはプリプレグから3Dプリフォームを製造できるこのセルは、真空吸引グリッパーを使用して、カットされたプライをピックアップし、配置して、加熱されたプリフォームモールドに折り畳みます。 Techni-Modul EngineeringとCACは、複雑で可展面に成形するための2D材料のカットプライを準備するソフトウェアを開発しました。このセルは、OPTICOMSおよびIビームテストプロジェクトでさらに開発されました。
ステップ1
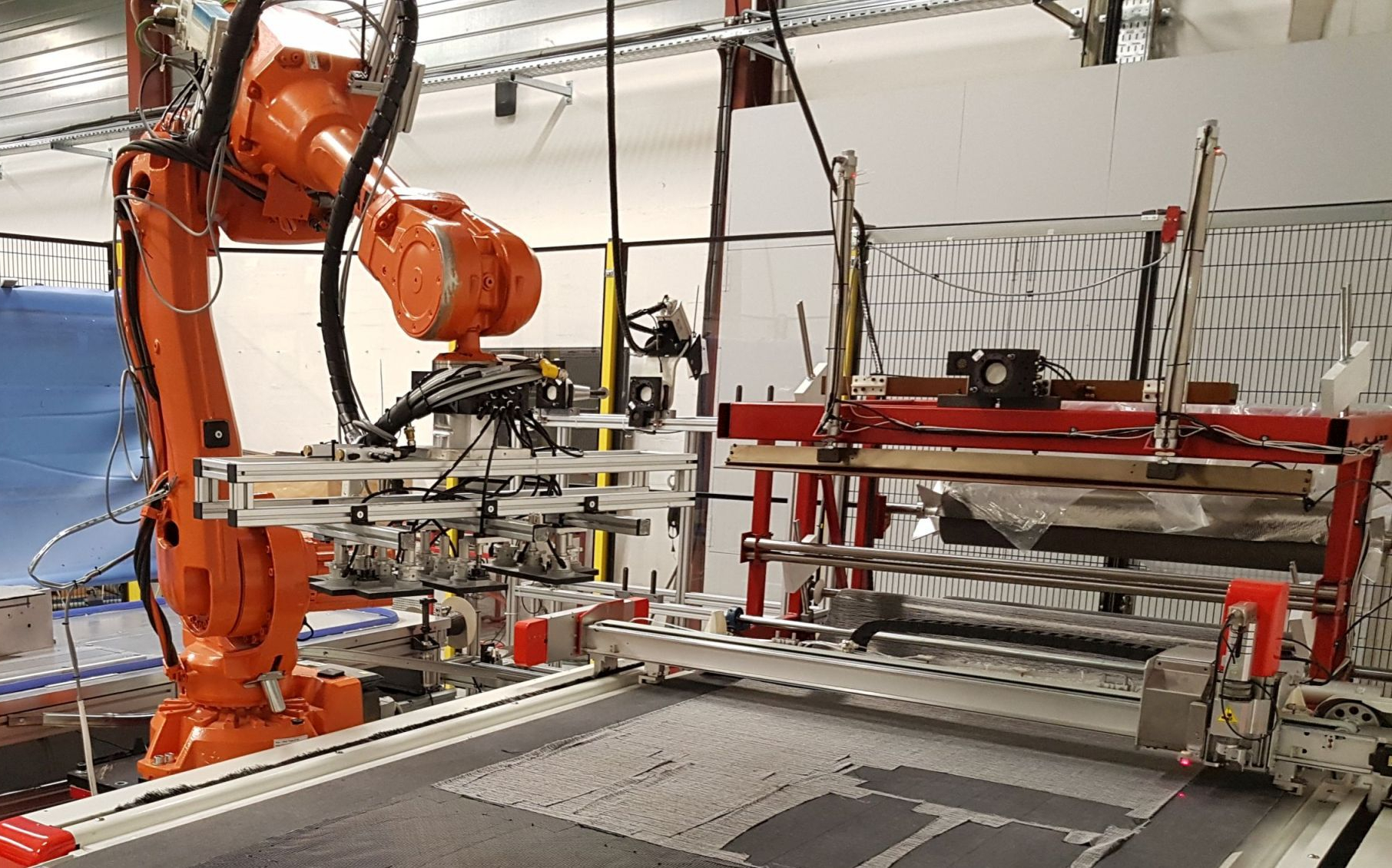
ソース、すべてのステップ画像| Techni-Modul Engineering
Techni-Modul Engineering自動セル内で、ピックアンドプレースロボットが自動カッターからプライを取り出し、加熱された予備成形ツールに適用します。
ステップ2

予備成形ツールは、レイアップ中に5〜8プライごとに加熱されたデバルクを完了するために使用されるヒンジ付きの再利用可能な真空膜(左側の青)を備えた圧縮テーブルに配置されます。
ステップ3
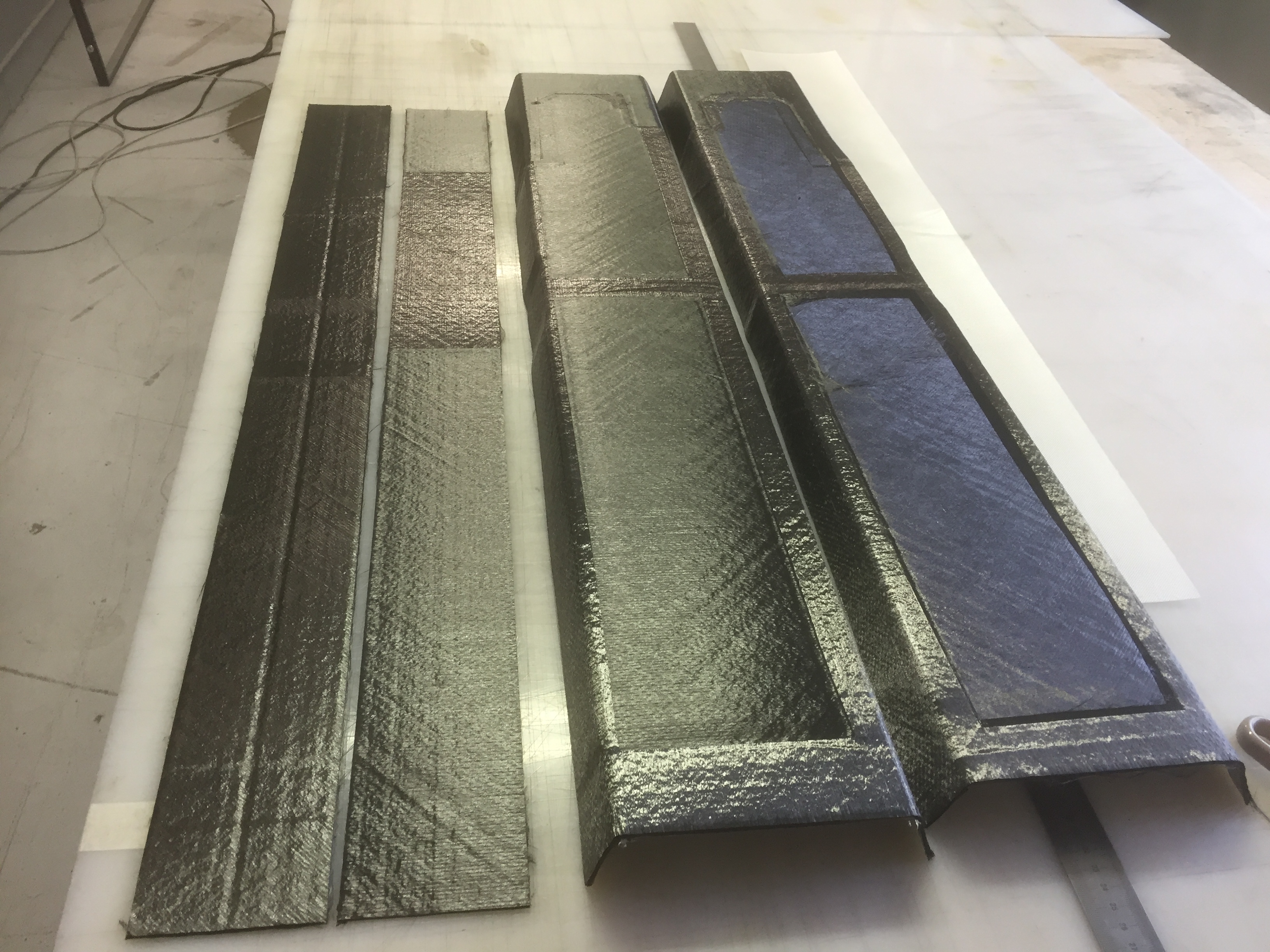
各ストリンガープリフォーミングサイクルは、1つのCビームプリフォーム(2つはIビームウェブを構成します)と1つのフラットフランジプリフォームを生成します。各Iビームストリンガーに必要な2つのセットをここに示します。
ステップ4
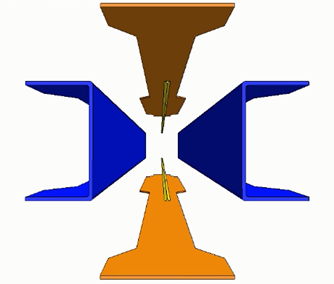
4つのIビームストリンガープリフォームをRTM金型に配置し、真空を適用して、樹脂の射出を5分で完了します。
ステップ5
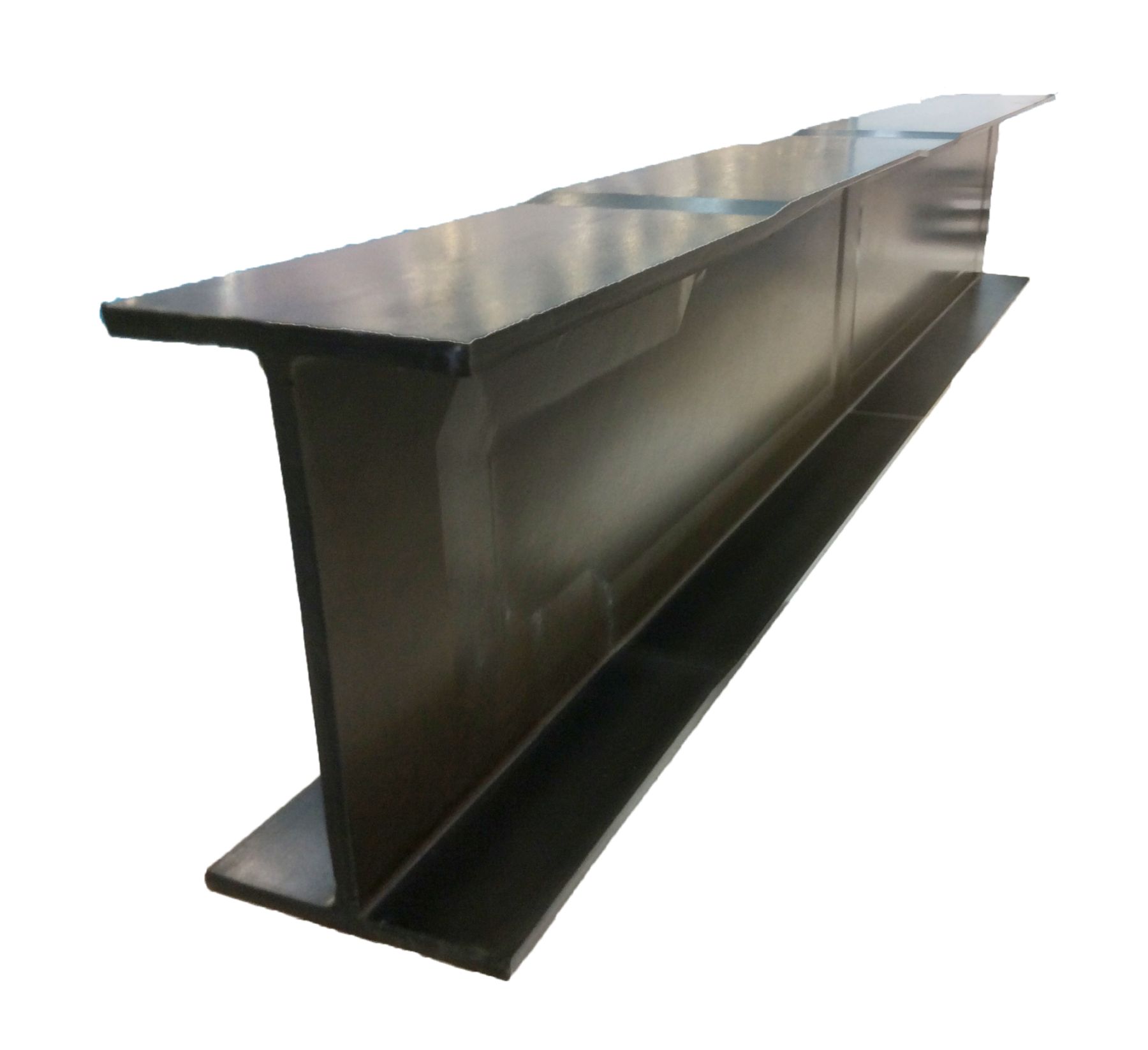
90分間の硬化後、ストリンガーを型から外し、樹脂フラッシュを4.5時間の完全なパーツサイクルでトリミングします。

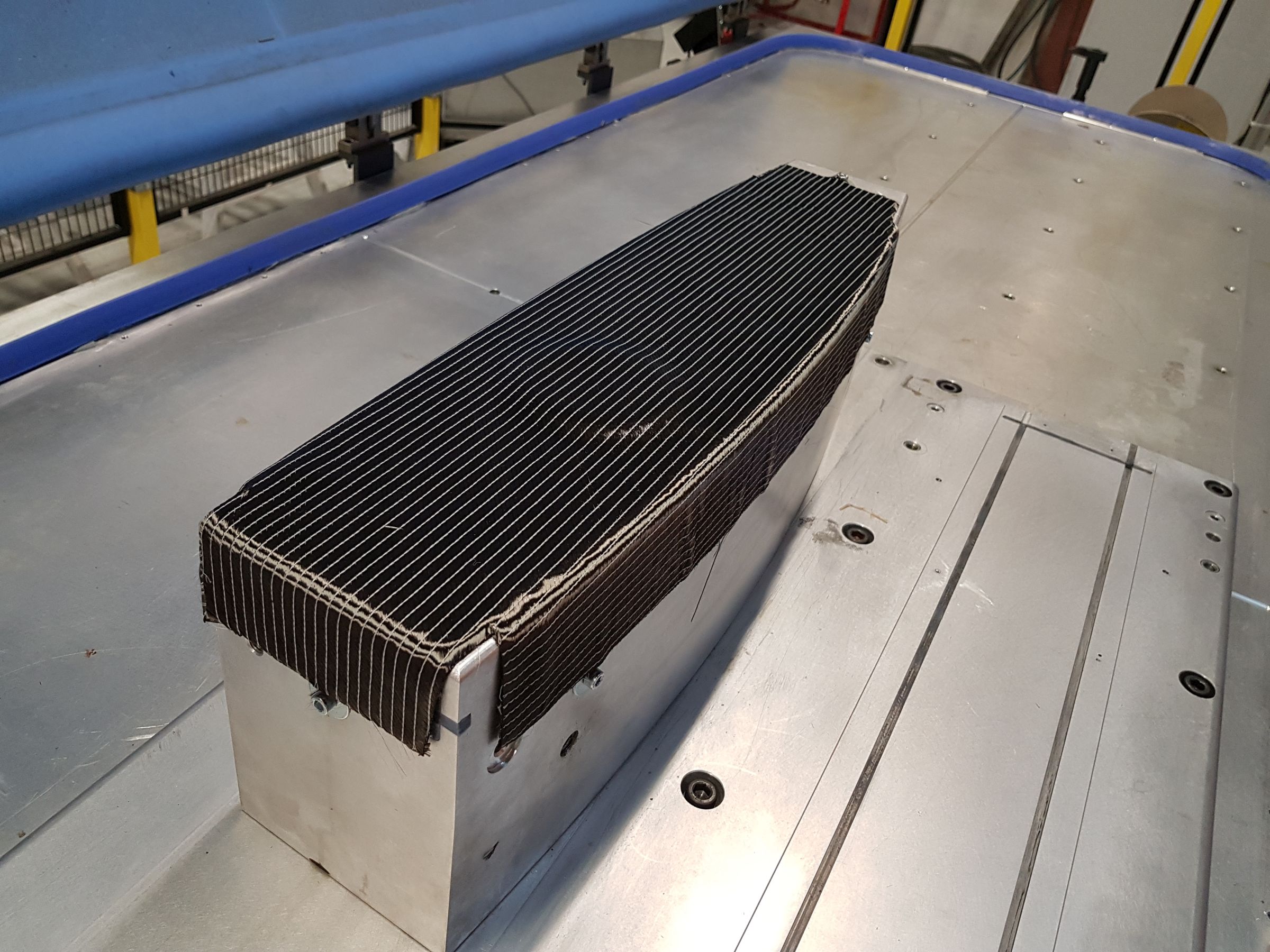
ロボットは、加熱されたプリフォームツールにカットプライを配置します。 5〜8層ごとに、プリフォームを圧縮するために加熱されたデバルクが完了します。

減量する前に、青いリリースフィルムが適用されます。
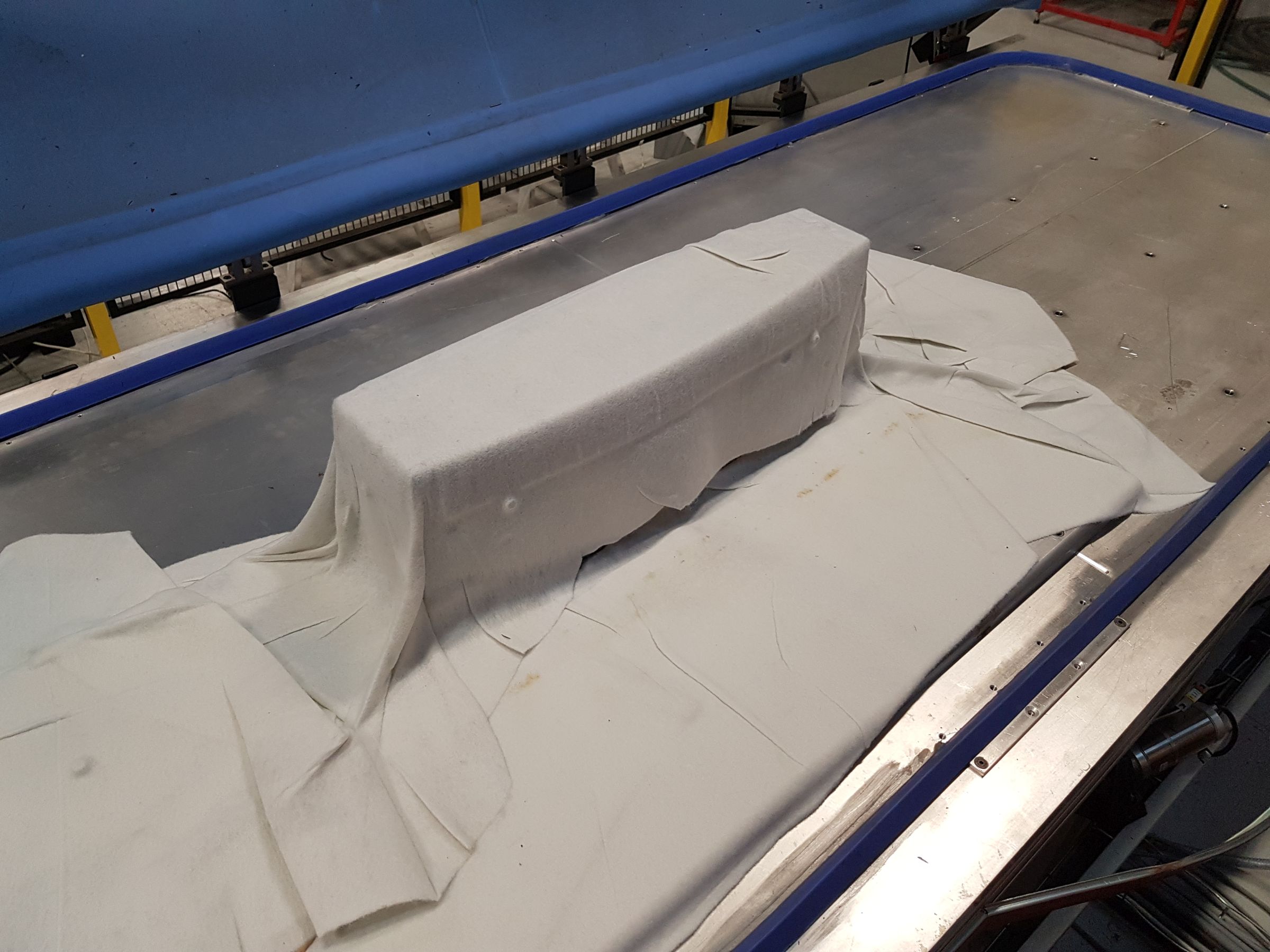
ブリーザーは、プリフォーム全体の空気を抽出するために使用されます。
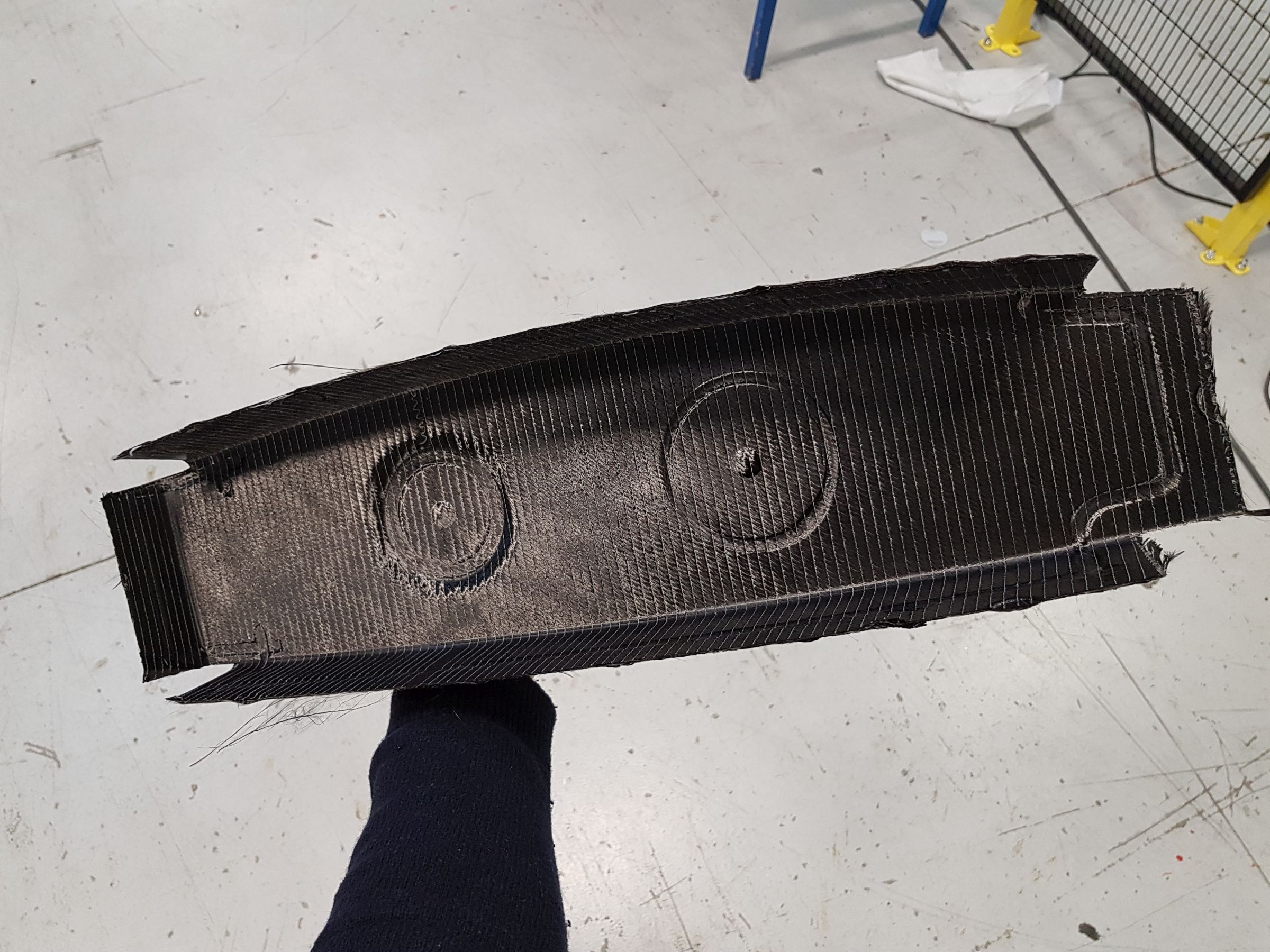
最後のデバルク後、プリフォームはツール上で冷却され、カットアウトがトリミングされます(下)。
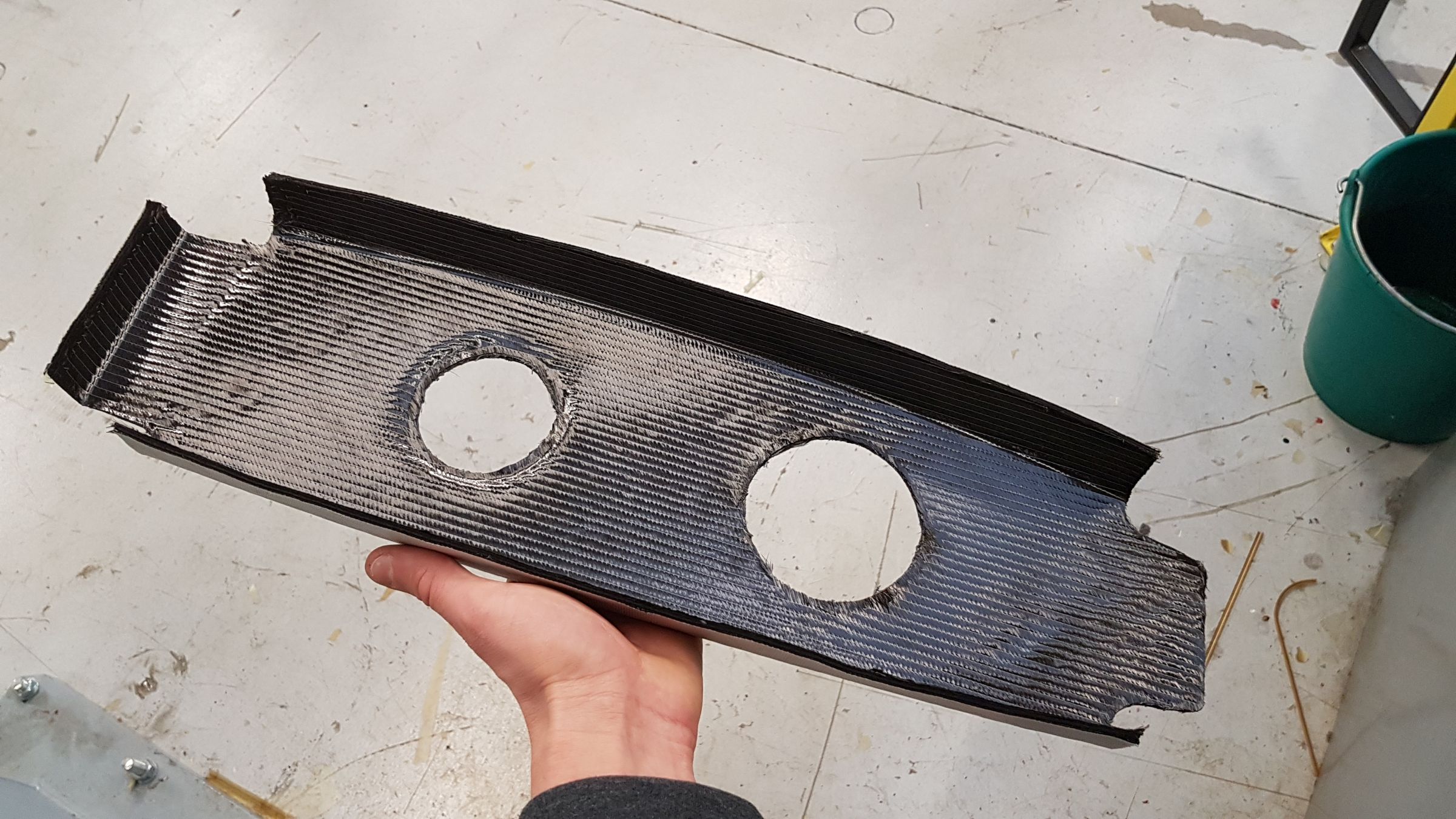
「ロボットによるピックアンドプレースを使用して、従来の手動によるプライの積み重ねを自動化しました」とChevallet氏は言います。 「ロボットは自動カッターからプライをピックアップし、圧縮テーブル上にある加熱されたプリフォームツールに転送します[ステップ1および6]。」ピールプライ(ステップ6の青いフィルム)、ブリーザー(ステップ6の白い素材)、ヒンジ付きの再利用可能な真空メンブレン(ステップ2と6の左側の水色)を適用し、真空と加熱を行って事前に成形し、空気を取り除きます。薄い熱可塑性ベールを溶かして圧縮されたプリフォームを作成しながら、テキスタイルスタック(ホットドレープフォーミング、HDF)。
「一度に圧縮できる層の数は、部品の材料と形状によって異なります」とChevallet氏は説明します。 「ウィングスキンのように曲率の低い部品の場合、50プライごとに圧縮できる可能性があります。ただし、OPTICOMSリブの角度は90度で、テスト用のIビームストリンガーはT字型であるため、予備成形中にプライにシワが形成されないように注意する必要があります。」彼は、このような複雑な形状では5〜8プライごとに圧縮が必要になる場合がありますが、それでも大量の工業化されたプロセスの一部である可能性があると付け加えています。スタックプライ、2分間のHDF 圧縮し、再度開いて再度スタックし、続いて圧縮サイクルを繰り返し、RTM金型に移す前にツールのプリフォームを最後に冷却します。
「当社の自動セルは、1プライあたり15秒の速度で配置できます」とChevallet氏は述べています。 「合計20プライ未満のOPTICOMSリブのレイアップは、20分で完了しました。」 Iビームストリンガーのレイアップが長くなりました—45分 その複雑な形状と1.2から6ミリメートルまでの厚さの変化を含むラミネートスタックのため。 「これは手動プロセスよりもはるかに高速であり、エラーリスクを減らし、再現性と品質を向上させ、コストを削減します」と彼は付け加えます。
ステップ7
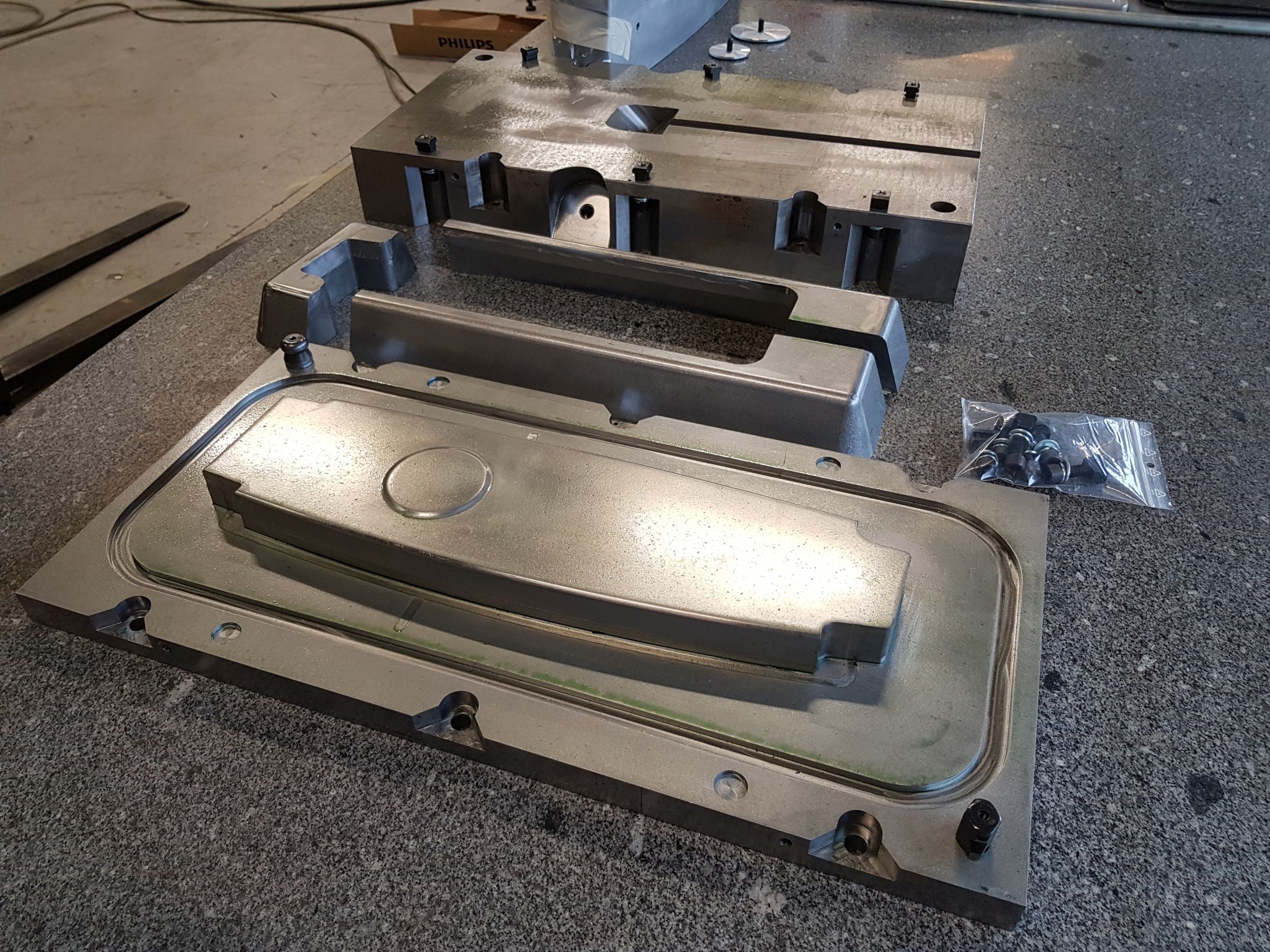
OPTICOMSリブのRTMツールは複数のパーツで構成されています。
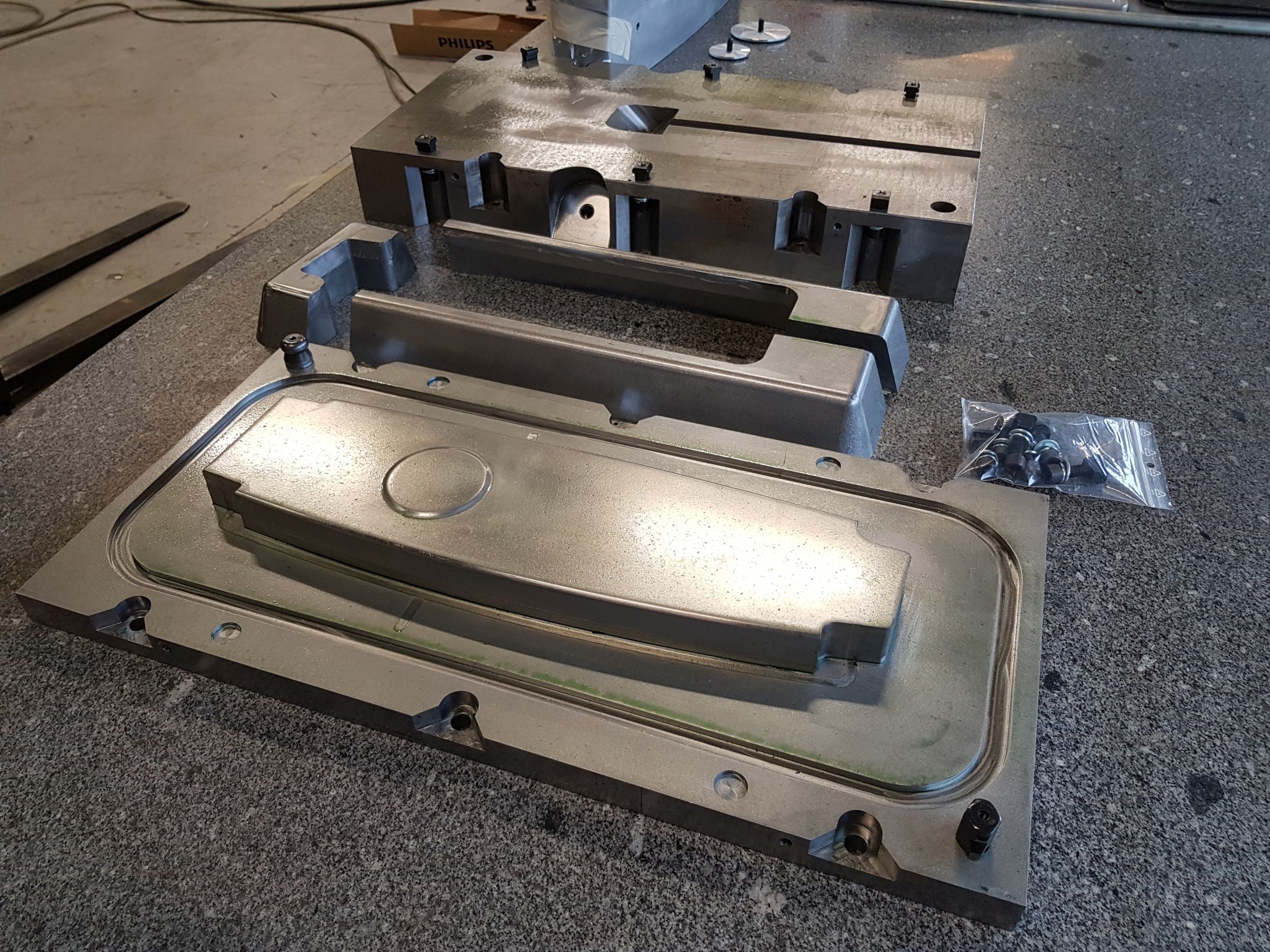
ステップ8
リブプリフォームはRTMツールに配置されます。
ステップ9
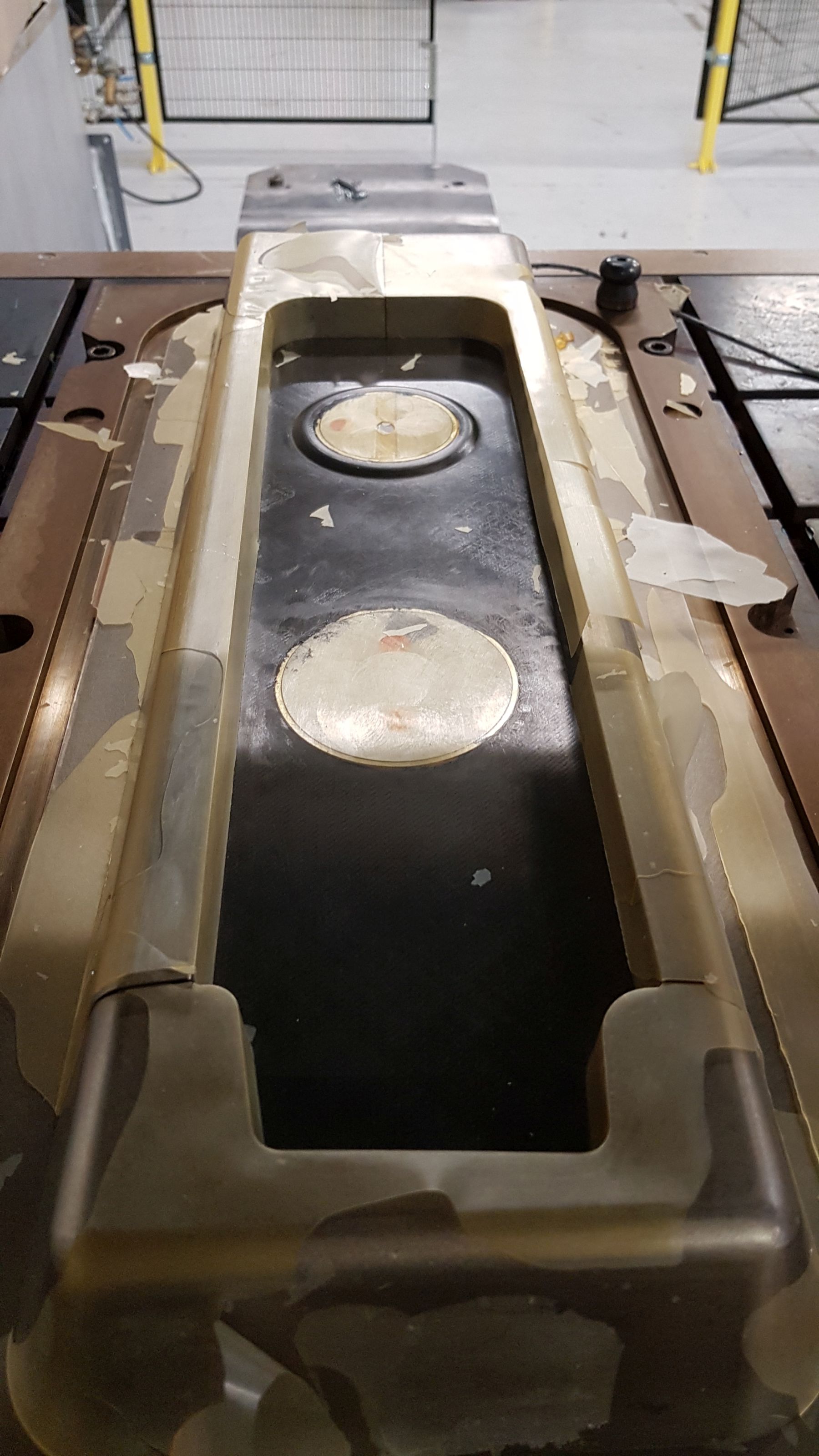
真空を適用し、樹脂を注入してプリフォームに浸透させた後、90分間硬化させます。ここでは、プレスが開かれ、硬化した部分が表示されています。
ステップ10
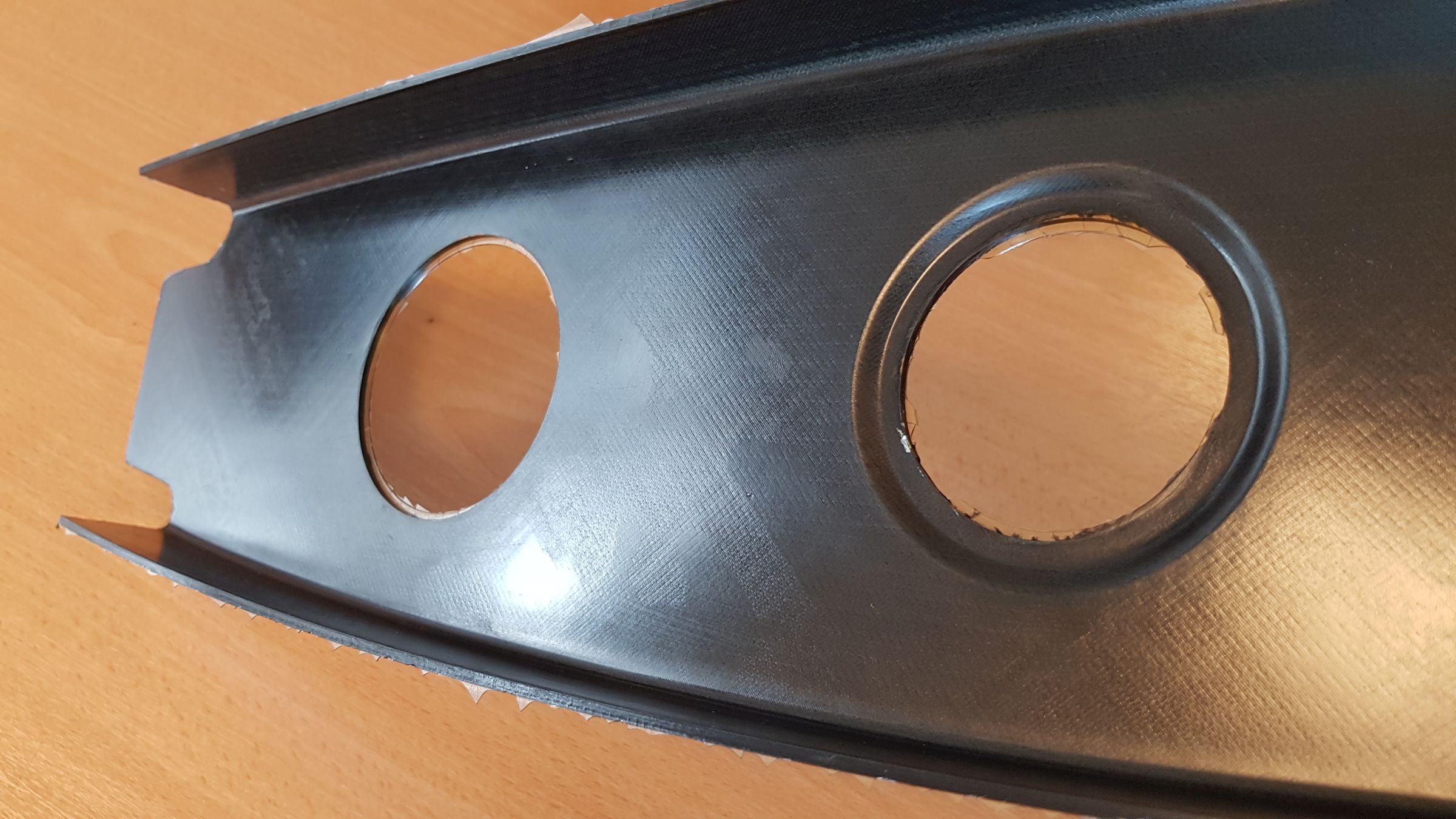
離型が完了すると、樹脂フラッシュは4時間の完全な部品サイクルで除去されます。
スマートコントロール
Techni-Modul Engineeringの自動プリフォーミングセルのもう1つの重要な機能は、統合制御システムです。 SMART CONTROLと呼ばれるそのバックボーンは、処理中に撮影された写真を部品のCADデータベースと比較するカメラシステムと多目的ソフトウェアであり、プリフォームの形状認識、繊維配向制御、層の位置決め、および欠陥や異物の破片(FOD)の検出を可能にします。 )。 SMART CONTROLフィードバックは、正しい順序とタイミングでプライをピックアップして配置する方法をロボットに指示しますが、エラーを検出するとセルオペレーターに警告します。 「システムは、オペレーターが手動でプライを取り外し、システムを再起動して交換するように構成できます。または、お客様と協力して、欠陥のあるプライを除去し、エラーを修正するための自動ソリューションを作成できます。」
層のエッジと輪郭を検出するために使用されるのと同じ光学画像が、繊維の配向を制御するためにも使用されます。 Chevalletは、パーツが非常に大きい場合(たとえば、200 x 200ミリメートルに対して2メートルの長さ)、「プライのエッジを検出するために、より高い垂直位置から写真を撮るカメラが必要になる場合があります。その後、に近づきます。繊維配向をチェックするための部品。このシーケンスは、パーツのタイプごとに調整します。しわやFODを検出するために、さまざまな欠陥のデータベースがあり、これに追加できるため、深層学習アルゴリズムは時間の経過とともに向上します。アイデアは、適応性のあるシステムを持つことです。」
サイクルタイムと将来の生産
OPTICOMSリブのプリフォームはHiMaxを使用して作成され、IビームストリンガーはHiTapeを使用しました。両方の樹脂システムは、HexcelのHexFlow RTM6 1成分(1K)液体エポキシで、180°Cで90〜120分の硬化サイクルがあります。この硬化は、表1に示すように、OPTICOMSリブとテストIビームストリンガーの両方の部品サイクル時間の中で最も長いステップです。
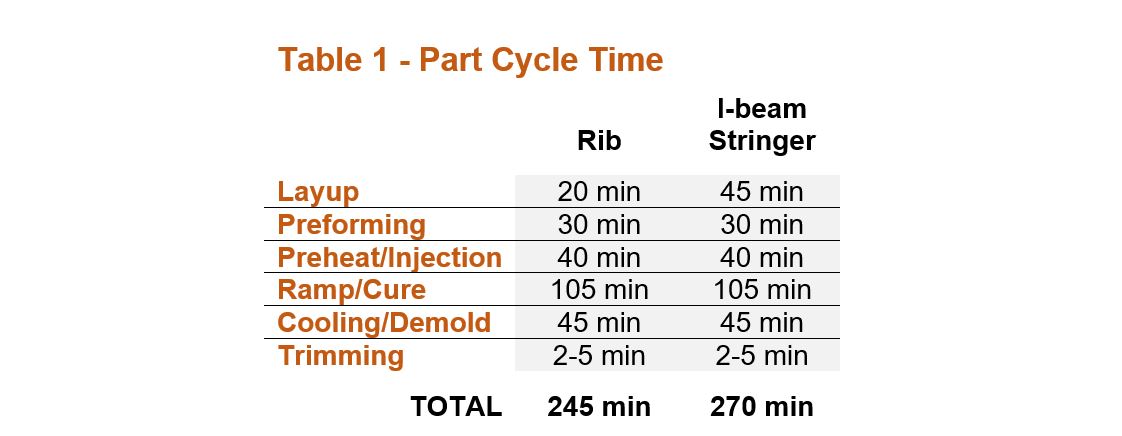
ソース| Techni-Modul Engineering
現在まで、これは航空宇宙構造物のRTMに認定された唯一のエポキシです。ただし、射出ヘッドで混合される2成分システムの認定への関心が高まっており、硬化サイクルの柔軟性が向上し、予混合されたRTM6の早期反応を防ぐために必要な冷蔵輸送と保管の必要性がなくなります。
Airbus Helicopters(Donauworth、Germany)は、SPARTAプロジェクトでAlpex Technologies(Mils、Austria)と協力して、HexFlow RTM6の2コンポーネントバージョンを使用したHP-RTMプロセスを実証し、A350ドアの180°Cで30分の硬化を達成しましたフレームは、高さ2メートル、幅200〜250ミリメートル、厚さ8〜10ミリメートルの複雑な形状の主要構造です(「費用対効果の高いCFRPエアロ構造の連続生産のためのHP-RTM」を参照)。エアバスはまた、複合技術センター(CTC、Stade、ドイツ)の子会社がHP-RTMを使用して製造した1.5メートル×0.5メートルのCFRPリブを実証し、繊維量が60%で2未満の部品の成形サイクルを20分に達成しました。 %ボイド。昨年、CTCは多くのティアサプライヤーと協力して、ハンドレイアッププリプレグ部品をA320用のHP-RTMに移行しました。ただし、2K樹脂システムは航空構造物の製造に適格である必要があり、CTCは、2K樹脂システムの混合品質を現場で継続的に保証できるかどうかを懸念しています。 Alpexは、これを実現するためにNetzsch(Selb、ドイツ)とKistler(Winterthur、スイス)のインモールドセンサーを使用しており、他のソリューションが開発されています(「複合エアロストラクチャーの生産を増やすための2液型エポキシ」を参照)。
>2Kシステムがなくても、より多くの生産量が可能になる可能性があります。 SPARTAプロジェクトのドアフレームは、180°Cでの最初の30分間の硬化後に取り外され、熱応力を除去して機械的特性を確保するために、真空下でプレスから後硬化されました。 AlpexのR&D Bernhard Rittenschoberの責任者によると、これには追加のツールセットが必要ですが、プレスと射出ユニットは1つだけです。彼は、余分な工具コストはプロセスとプレスのコストの削減によって相殺され、500〜1,000パーツ/年の少量でも迅速に回収できると説明しています。
「これらのデモンストレーターの主な成果は、UD炭素繊維強化材を使用して樹脂をこのような大きな部品に浸透させることが困難で長いプロセスであった従来の航空宇宙RTMプロセスと比較して、短い樹脂注入で一次航空構造を作成できることです」とPagnac氏は述べています。 。 「私たちは、このタイプのインテリジェントな自動プリフォーミングとC-RTM処理で達成できることのほんの始まりに過ぎません」とChevallet氏は付け加えます。 「将来の航空機で想定されている、補強材が組み込まれたスキン構造のより費用効果が高く、持続可能な生産を実現する可能性があります。」
樹脂