スペインのCleanSky2向けの熱可塑性複合材料とRTMの進歩
EURECATCentroTecnológicodeCatalunya(EURECAT Technology Center Catalonia、バルセロナ、スペイン)は、11の施設、650人の従業員、5,000万ユーロの年間収益を誇る民間の非営利R&D組織です。 「スペインで2番目に大きいR&Dセンターです」と、EURECATの航空宇宙市場のプログラムディレクターであるAngelLagrañaHernandezは説明します。 EURECATの収入の一部はカタロニア政府からのものであり、残りの半分は民間企業(主に中小企業(SME))からのものでなければならず、残りの半分は欧州連合が資金提供するなどの公的企業である可能性があると彼は説明します。クリーンスカイ2プログラム。 「現在、18のClean Skyプロジェクトがあります」と、Lagraña氏は述べています。
Clean Sky2の多数の目標と計画されているテクノロジーデモンストレーターでコンポジットがどのように機能するかの例は次のとおりです。
- 次世代の多機能胴体デモンストレーター—熱可塑性プラスチックを活用してよりきれいな空を実現
- サーキュラーエコノミー:リージョナル航空機用の複合胴体が形になります
- CleanSkyのFastCanにモーターレースの専門知識を活用する
「EURECATは非常に横断的であり、航空宇宙での作業に加えて、自動車、鉄道、その他の業界で機能しています」とLagraña氏は言います。 「また、データ分析やブロックチェーンなど、IT分野で多くの活動を行っています。Composites4.0はその戦略分野の1つです。」コンポジット内で、彼はEURECATが主にオートクレーブ(OOA)技術の外で機能すると述べています。 「私たちは、熱可塑性プラスチックと液体圧縮成形に焦点を当てています。これには、処理中の樹脂のガラス転移温度(Tg)の監視を含む、リアルタイムでのプロセス監視が含まれます。」 (このブログの最後にあるCOFRAREのセクションを読み続けて、このTgモニタリングの詳細を確認してください。)
Clean Sky 2におけるEURECATの最新の複合材料関連プロジェクトには、次のものがあります。
- KEELBEMAN 熱可塑性複合キールビームのデモンストレーション(このプロジェクトは、GAP番号785435KEELBEMANに基づく欧州連合のHorizon研究およびイノベーションプログラムに基づくCleanSky 2共同事業から資金提供を受けています);
- WINFRAME 4.0 Clean Sky(2008-2017)のGreen Regional Aircraft(GRA)デモンストレーター用の熱可塑性複合(TPC)ウィンドウフレームを構築し、Clean Sky 2(2014-2024)のRegional Aircraft IADP(Innovative Aircraft Demonstrator Platform)に拡張します。
(このプロジェクトは、GAP番号821323 WINFRAME4.0に基づく欧州連合のHorizon研究およびイノベーションプログラムに基づくCleanSky 2共同事業から資金提供を受けています。) - COFRARE 2020 TPCせん断タイを備えた樹脂トランスファー成形(RTM)を使用して製造された熱硬化性胴体フレーム用。
(このプロジェクトは、GAP番号821261 COFRARE2020に基づく欧州連合のHorizon研究およびイノベーションプログラムに基づくCleanSky 2共同事業から資金提供を受けています。)
熱可塑性複合キールビーム
クリーンスカイ2-JTI-CS2-2017-CFP06-LPA-02-20。プロジェクト期間:2018年3月から2019年12月
KEELBEMANプロジェクトの目的は、A320タイプの航空機向けに製造指向のキールビーム構造を開発することです。これにより、航空機の高い生産率を実現しながら、熱可塑性複合材料を介して手頃なコストで製造できます。プロジェクトコーディネーターとしてのEURECATに加えて、パートナーには次のものが含まれます。
- エアバス (フランス、トゥールーズ)トピックマネージャーとして
- CETMA (欧州技術設計材料研究センター、ブリンディジ、イタリア)
- CTエンジニアリンググループ (CT Ingenieros、マドリッド、スペイン)、ドイツのハンブルクオフィスを介した胴体、翼、リアエンドの研究などの航空機開発についてエアバスと複数年契約を結んでいる多数のグローバルオフィスを持つ会社。後部の研究(スペイン);胴体および発電所に関連する構造(フランス、トゥールーズ)および翼の開発(英国、ブリストル)に関する研究
- ソフィテック (スペイン、セビリア)、複合材料の専門知識と生産能力を備えた航空構造物の製造と組み立てのスペシャリスト。
CTエンジニアリンググループは、トゥールーズのオフィスを介してキールビームの形状の完全なモデリングを提供し、ソフィテックは非破壊検査(NDT)検査を開発しました。 「これは、このような閉じたボックス構造では非常に困難です」とLagraña氏は指摘します。
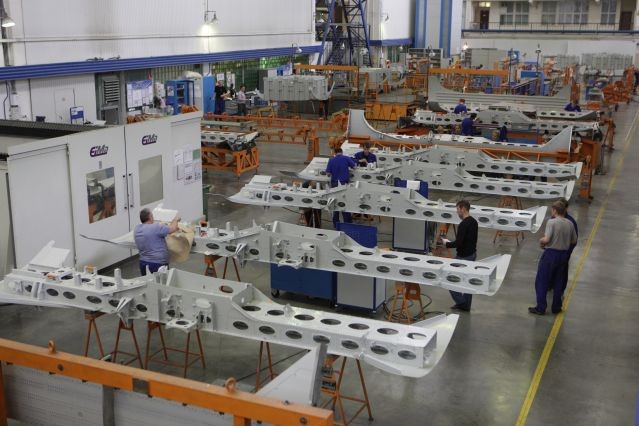
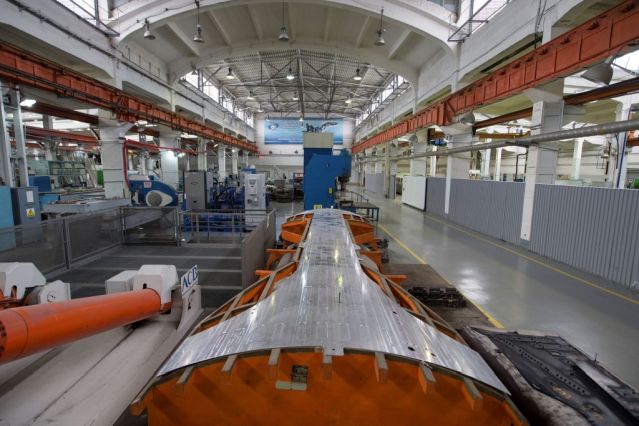
ここに示されているのは、Irkut Corporation(モスクワ、ロシア)によって金属で作られたA320キールビームアセンブリです。イルクートは2004年にエアバスと契約を結び、前脚ベイ、キールビーム、フラップトラックなどのコンポーネントを、平均して3機に1機のA320ファミリー航空機に搭載していると報じられています。ソース|イルクート
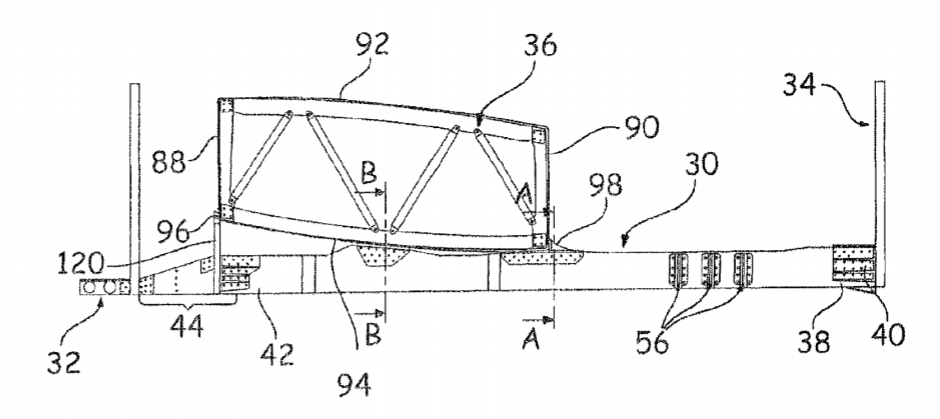
キールビーム構造の開発
「今日、エアバスを除いて、ほとんどの航空機のキールビームは金属で作られています
モノリシック炭素繊維複合材であるA350」とLagrañaは言います。 「これには、多数のリベットと組み立てにかなりの時間が必要です。」キールビームは胴体の重要な構造であると彼は説明します。「着陸中にキールビームが破損し、胴体全体がひび割れて破損する場合があります。
スティーブウィルヘルムによる2011年の記事によると、A350キールビームは70%複合材で、長さ54フィート(16.5メートル)、10,000個の留め具を組み合わせ、重量は1.2トンで、航空機のバックボーンを形成しています。ウィルヘルム氏は、競争力のあるボーイング787航空機は、「船体の強度の多くは、エンドツーエンドで固定された複合バレルに由来するため、このような堅牢なキール構造に依存していません」と述べています。次に、この記事では、G2 Solutions LLC航空宇宙コンサルタント会社(米国ワシントン州カークランド)のマネージングパートナーであるMichel Merluzeauを引用しています。彼は、エアバスの設計を「より従来型」で「リスクが少ない」と説明していますが、キールビームは「その航空機の構造的完全性。」
エアバスは実際に2001年にA340用の複合キールビームを開拓しました。しかし、前述のように、必要なリベットの数が多いと、複合材を使用することで可能な軽量化に逆行します。したがって、KEELBEMANプロジェクトの主な目標は、互いに溶接された熱可塑性複合部品を使用してファスナーを最小限に抑えることです。
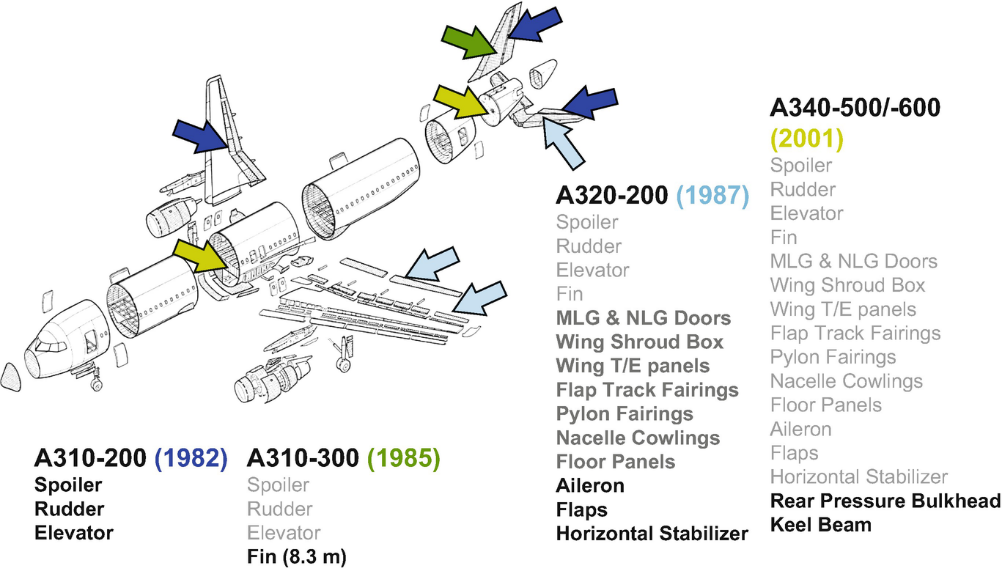
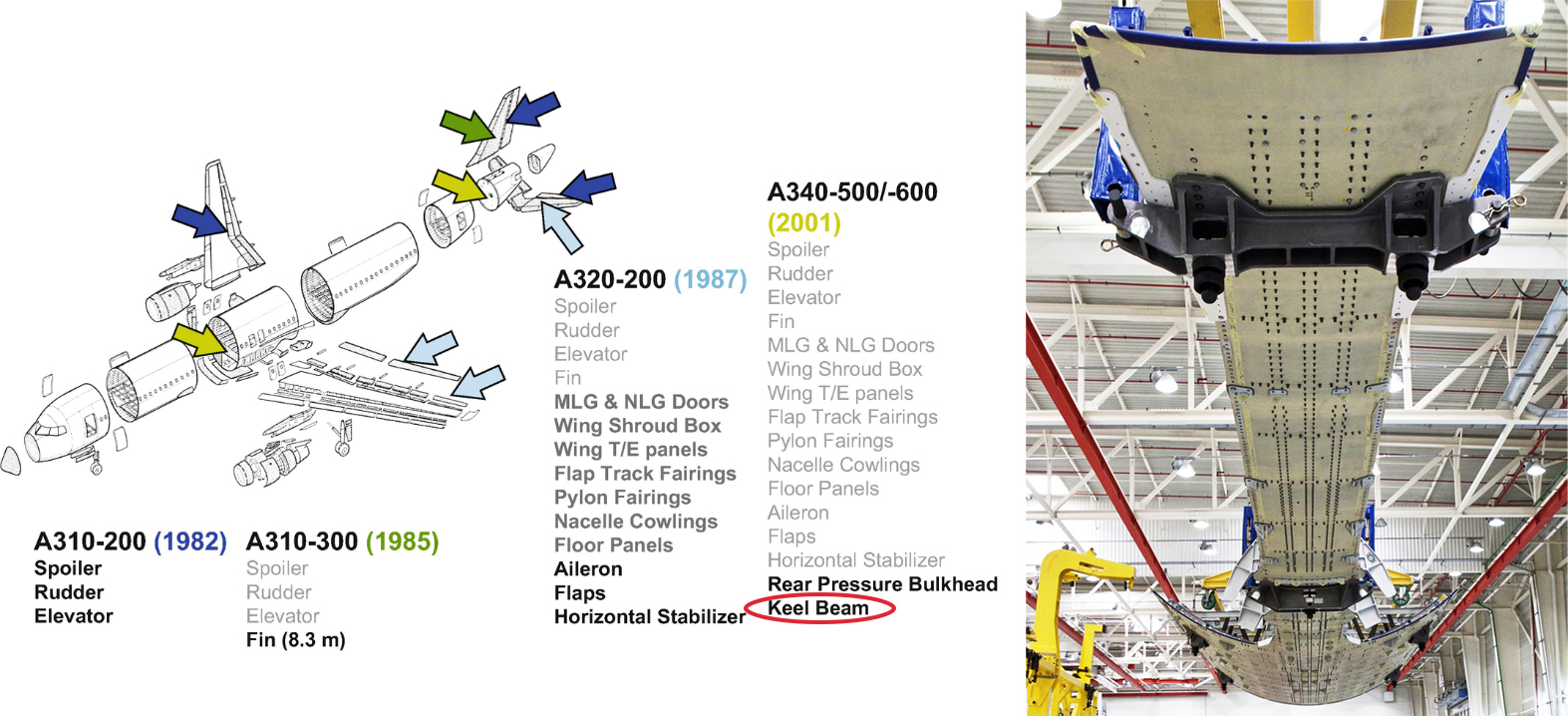
TPCキールビーム
「組み立てに溶接を使用した熱可塑性複合キールビームの開発は、エアバスによる明日の航空機の開発の一部であり、これには、明日の翼や明日の胴体などのプログラムが含まれます」とLagraña氏は言います。 「KEELBEMAN内で、ストリンガーを備えたキールビームの250ミリメートル×500ミリメートル×1メートルの長さのデモンストレーションセクションを作成し、可能な限り自動化してこの構造を溶接する可能性を実証しました。」
Lagrañaは、デモンストレーターのウォールプレートとストリンガーは、CETMAによって開発された連続圧縮成形(CCM)プロセスで炭素繊維/ポリエーテルケトンケトン(PEKK)一方向(UD)テープを使用して作成されたと述べています(「航空宇宙グレードの圧縮成形」および「PEEKvs.PEKK」を参照)対PAEKおよび連続圧縮成形」)。 「EURECATによる従来の非等温圧縮成形を使用して作成された横方向補強材用のリブもあります」とLagraña氏は付け加えます。
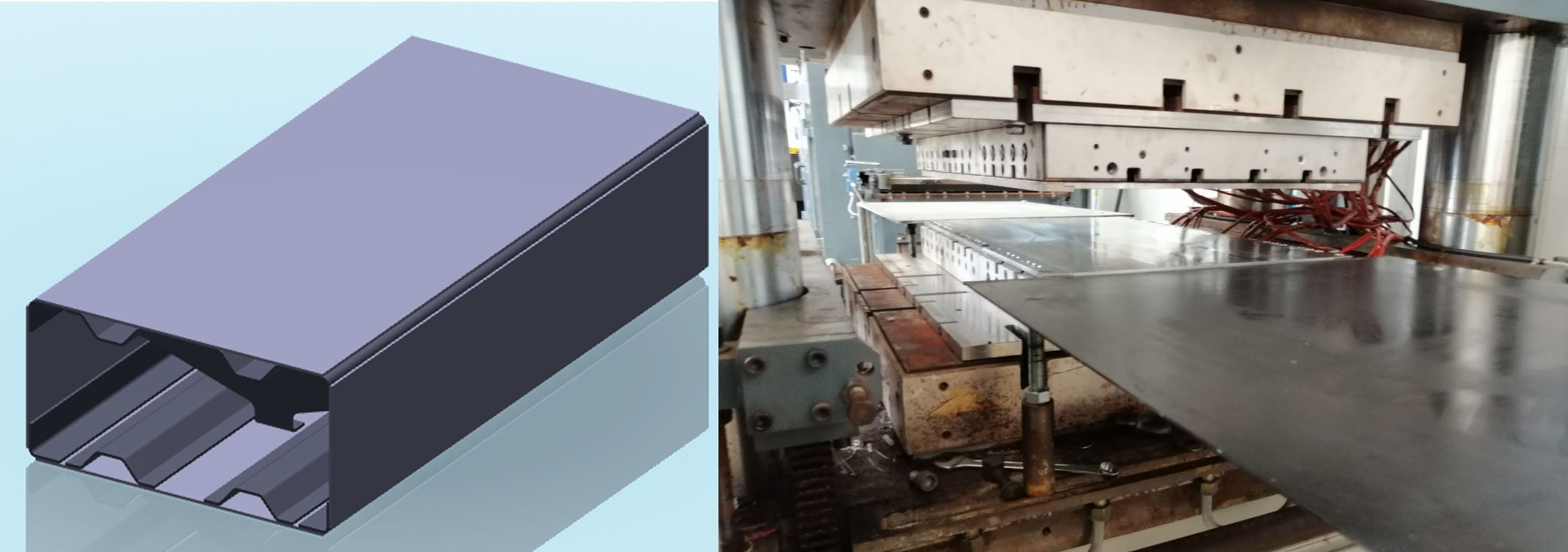
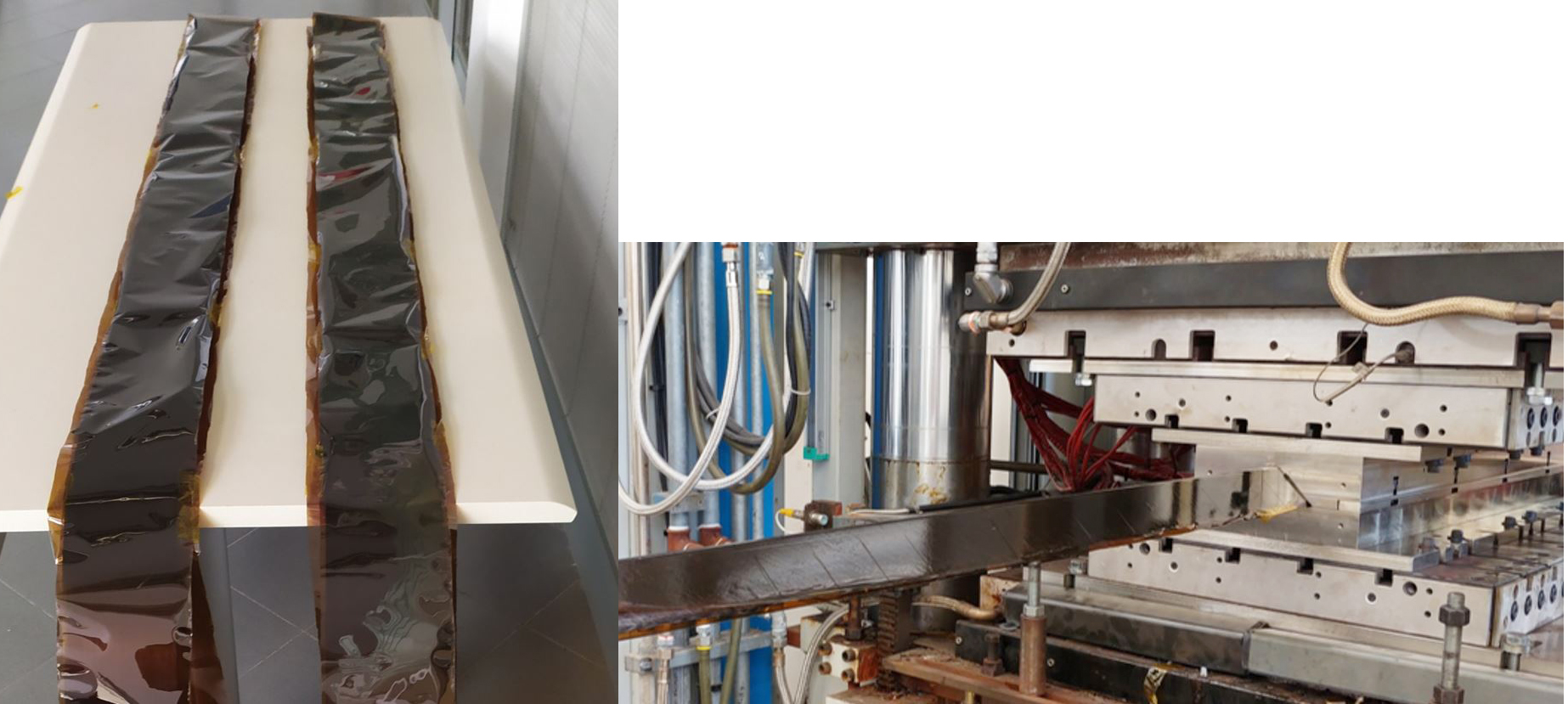
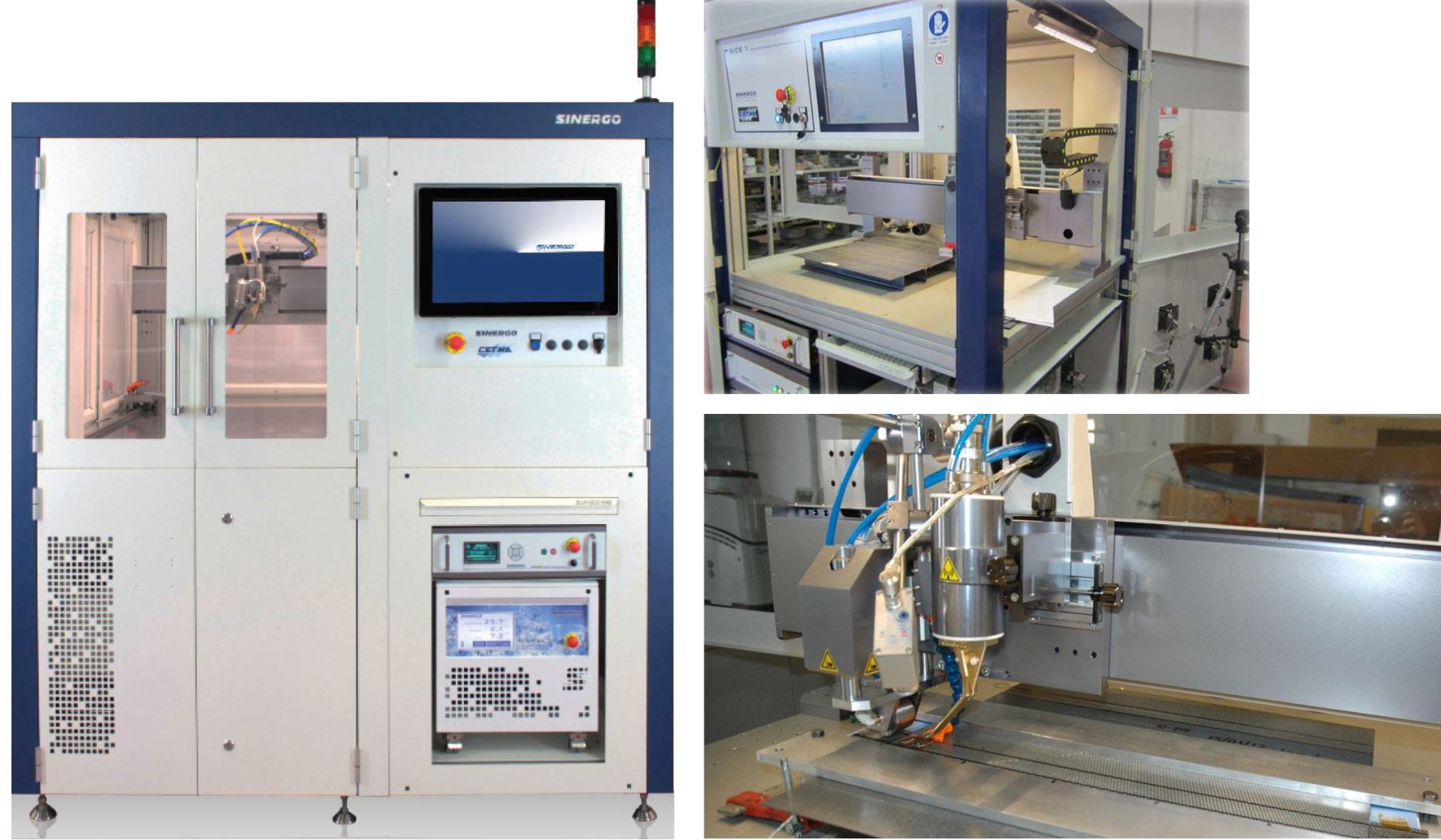
キーイネーブラーとしての誘導溶接
Lagraña氏は、CETMAは、KEELBEMANの部品製造だけでなく、特許取得済みの誘導溶接機と技術を使用したデモンストレーターの組み立てにおいても重要な役割を果たしたと述べています。この溶接は、元々、最初のCleanSkyプログラムのECOFAIRSプロジェクト(2011〜 2014年)で、上記のTPC構造の等温および非等温圧縮成形とともに開発されました。 ECO FAIRSでは、CETMAはこれらすべての技術を使用して、アグスタウェストランドヘリコプターテールの既存の上部パネル(ストリンガー補強スキンパネル)と湾曲したスポンソンフェアリングデモンストレーターに基づいたプロトタイプデモンストレーターを作成しました。これらはCETEX(TenCateが提供、現在はToray Advanced Compositesが提供)T300 3K 5HS炭素繊維繊維と両面PPS(ポリフェニレンサルファイド)フィルムを使用して作成されましたが、CETMAはPEEKおよびPEI複合材料による誘導溶接も証明しました。
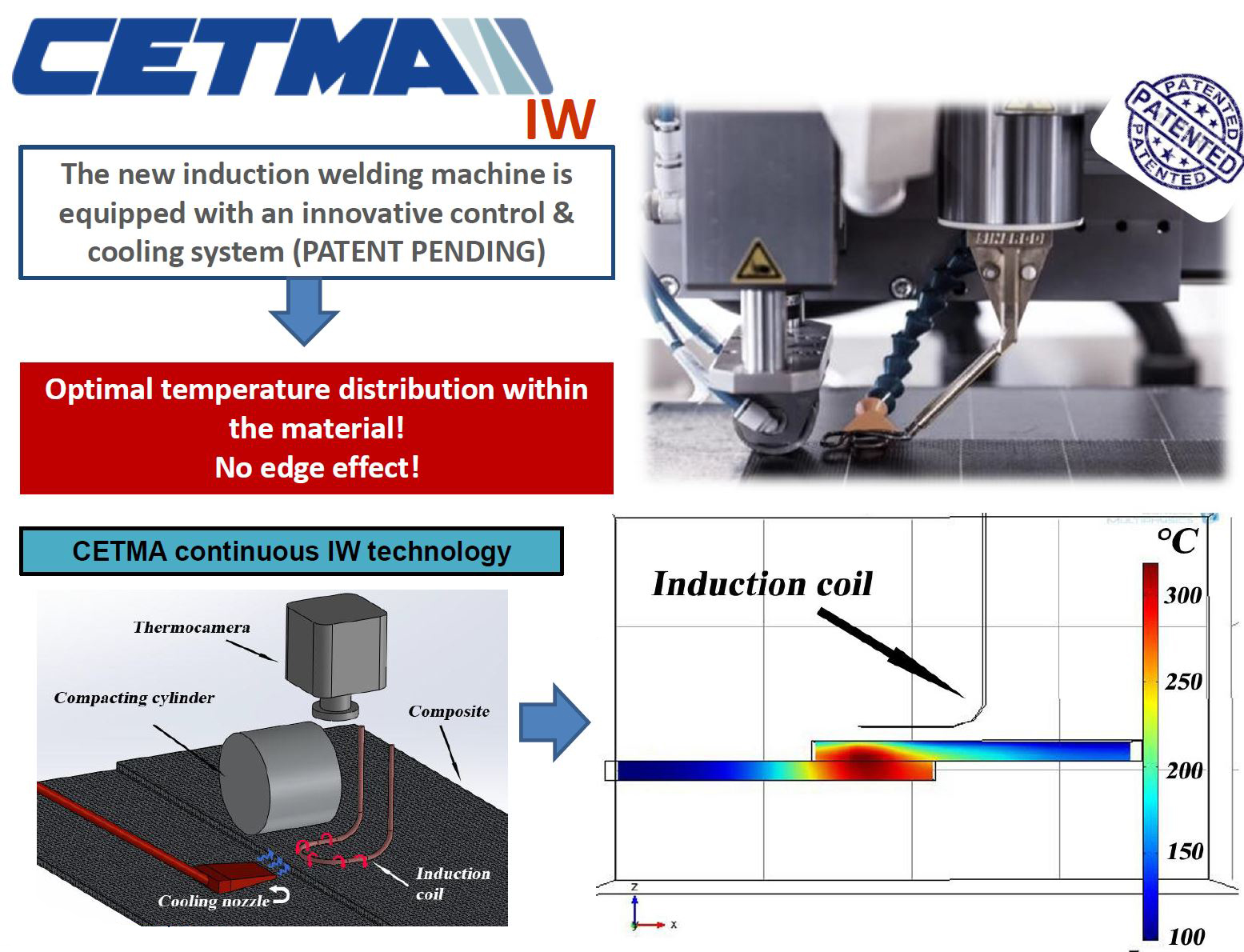
CETMAは、熱可塑性複合溶接技術の中で最も有望なものとして誘導溶接(IW)を選択し、溶接および電子工学のスペシャリストであるSINERGO srl(Valdobbiadene、トレヴィーゾ、イタリア)と協力して新しい誘導溶接機を開発しました。 SINERGOが提供するガントリーベースのSICE1 WIDEマシン(下の画像を参照) 最大1メートル×1メートルの航空宇宙品質の部品の連続溶接が可能です。これには、溶接される材料内で最適化された温度分布が確実に達成されるようにするための堅牢な制御システムが含まれています。機械には、圧密圧力を加えるための冷却シリンダーと、誘導された渦電流の流れが制限されているエッジなど、必要に応じて熱を除去するための空冷システムが装備されているため、電流密度が高くなり、過熱します。 。幾何学的に複雑な形状を溶接するために、CETMA誘導溶接ヘッドを6軸ロボットアームに取り付けることも可能です。
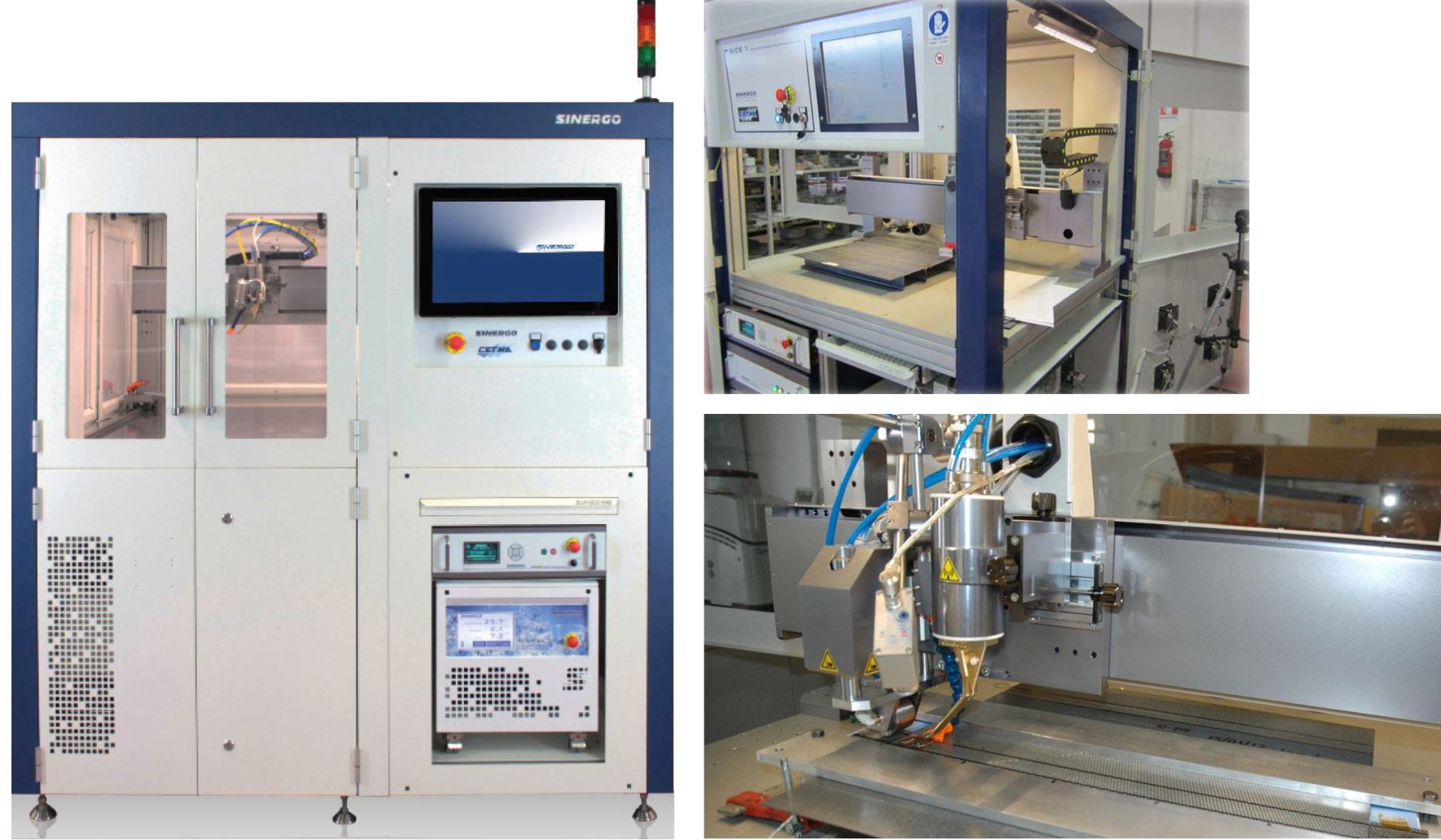
CETMAは、シミュレーションツールを使用し、COMSOL Multiphysics(COMSOL Inc.、マサチューセッツ州バーリントン)の有限要素モデリング(FEM)ソフトウェアを使用して数値解析を実行することにより、誘導溶接プロセスを最適化する機能も開発しました。多数の物理テストを通じてこれらのモデルを検証しました。 CETMAは、溶接クーポンのシングルラップテストによって最適化されたプロセスパラメータを確認しました。このテストでは、せん断強度の値が文献で報告されている最大値に非常に近かった。特に、これらは構造用接着剤を使用した場合の最大値よりもはるかに高かったとCETMAは言います。
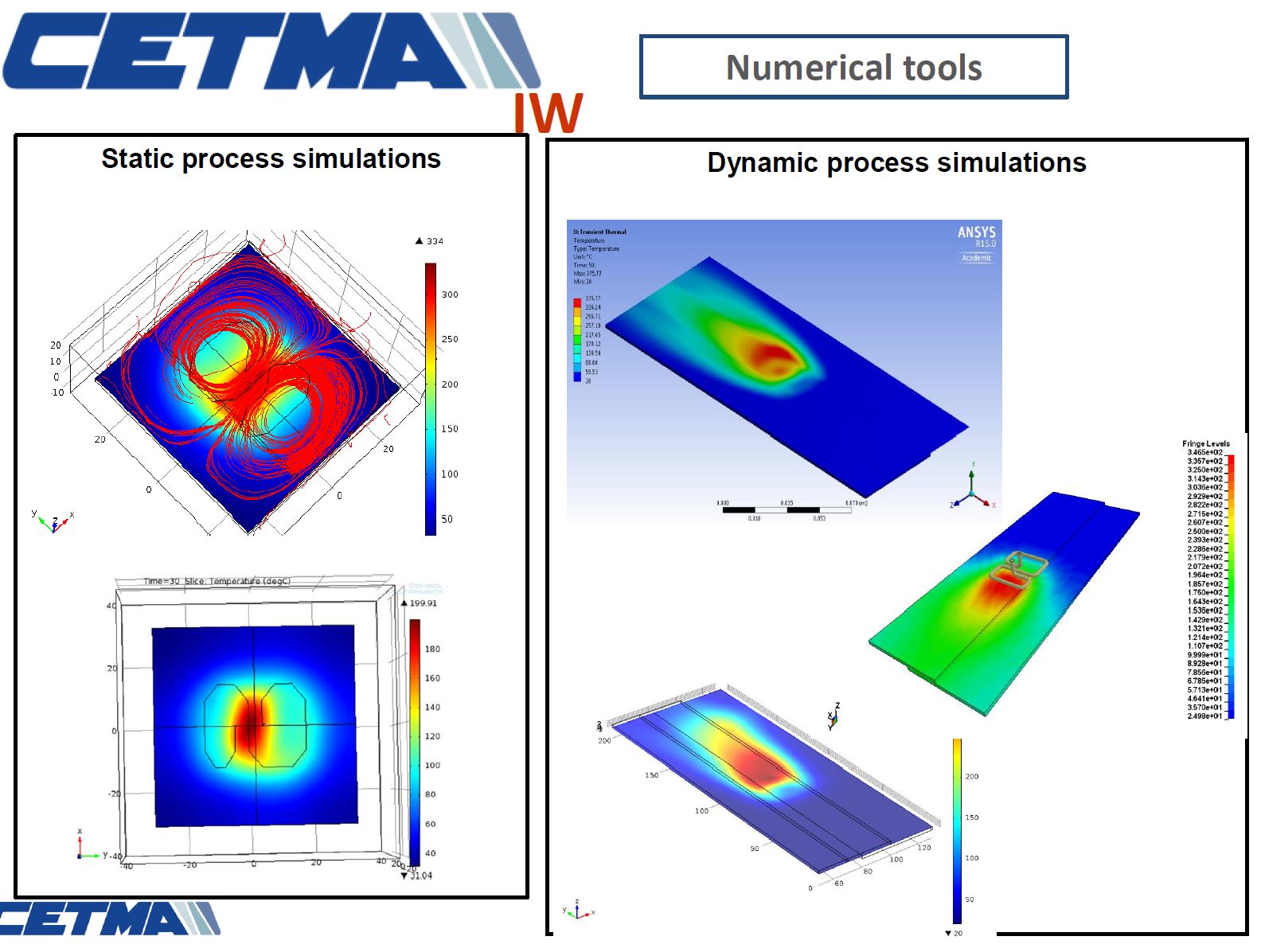
CETMAは、PEEK、PEI、PEKK、PP、PA6、PA12、さらには熱可塑性PVB(ポリビニルブチラール)ハイブリッドを使用したCF /エポキシへの溶接など、さまざまな材料の溶接能力を証明しています。溶接用の熱硬化性基板から熱可塑性面への移行用の層。 (このセクションの詳細の多くは、CETMAコンピテンシーのプレゼンテーションとから引用したものです。 CORDIS最終レポート ECO FAIRSの場合。) CETMAは2014年にヨーロッパ特許を申請し、発明者のSilvioPappadaとAndreaSalomiは2016年に特許EP2801472A1を取得しました。CETMAはこの技術に関する多数の論文とプレゼンテーションを公開しています。
- 「オートクレーブ外技術の開発をサポートする有限要素シミュレーション」、A&D、2012年10月11〜12日
- 「PPS-炭素複合材料の連続誘導溶接をサポートする有限要素シミュレーション」、SEICO 13、2013年3月11〜13日「パリ」
- 「航空宇宙セクターにおける熱可塑性複合材料用の新しい誘導溶接機の開発」、イタリア航空宇宙工学協会XXII会議ナポリ、2013年9月9〜12日
- 「航空宇宙分野での誘導溶接」、TPRC、熱可塑性複合材料ヨーロッパコンソーシアム、Webミーティング、2013年12月。
- 「航空宇宙分野向けの熱可塑性部品の実物大試験」、SEICO 14、2014年3月10〜11日「パリ」
- 「航空宇宙分野向けの新しい誘導溶接装置」、JECマガジン、No。87、2014年3月、89〜91ページ。
KEELBEMANのステータスと今後の進路
エアバスは12月にCETMAを訪れ、1メートルのデモンストレーターセクションの最終溶接を見ました。また、KEELBEMANチームは、技術準備レベル(TRL)の最終レビューも行いました。 「私たちは良い結果を得ており、技術をTRL3からTRL4に成熟させています」とLagrañaは言います。次のステップには、TRL 6のさらなる開発と、WP2.3.2フルサイズ下部中央胴体などのCleanSky2のデモンストレーターの1つに設置されるフルスケールキールビームの製造が含まれる可能性がありますが、これはまだ行われていません。決定しました。
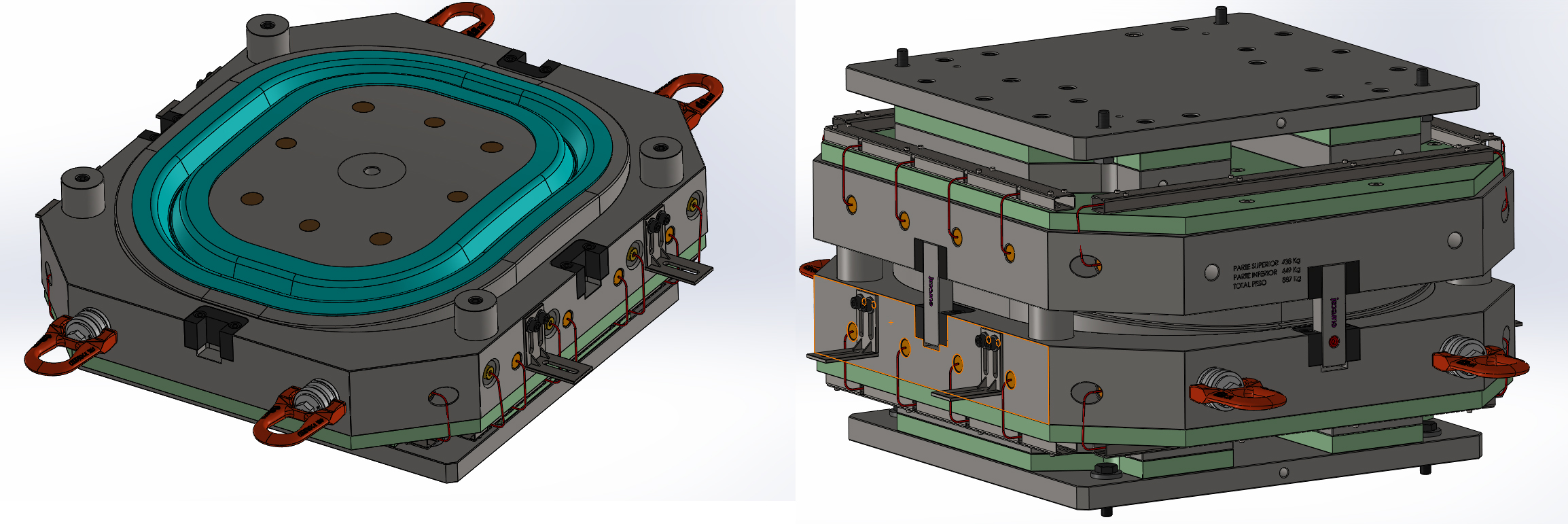
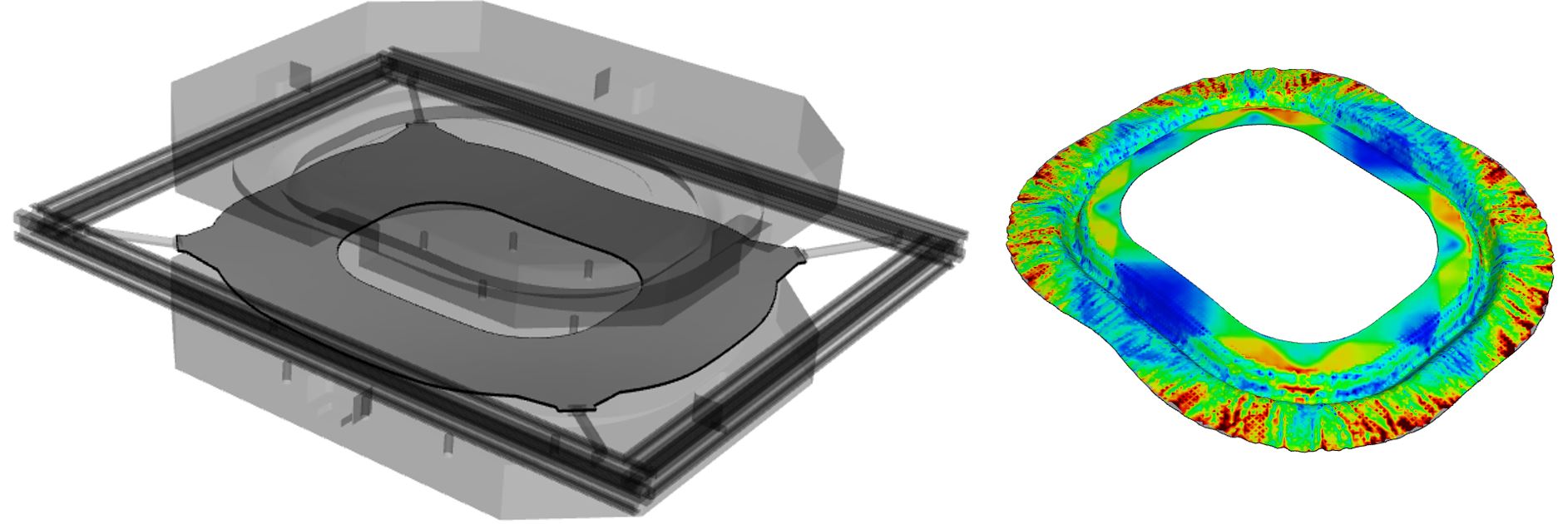
TPCウィンドウフレーム用のWINFRAME4.0プロジェクト
EURECATのもう1つの熱可塑性複合(TPC)プログラムはWINFRAME 4.0であり、リージョナル航空機の胴体/キャビン統合地上デモンストレーター用の24個のウィンドウフレームを開発および製造することを目的としています(リージョナル航空機およびフル向けのClean Sky2の開発の説明を参照) -規模の革新的な胴体および客室のデモンストレーター 下)。 WINFRAME4.0パートナーには次のものが含まれます。
- 多国籍航空宇宙会社レオナルド (イタリア、ローマ)トピックマネージャーとして
- EURECAT
- ソフィテック。
「私たちが使用している方法では、10分ごとに1つのウィンドウフレームを生成できます」とLagraña氏は言います。製造ステップには、オーブンでTPCラミネートブランクを加熱し、型に変換し、プレスで型を閉じ、10〜20分間熱と圧力を加え、完成した部品を型から外します。 「このアプローチは、液体成形よりも短いサイクルを実現するだけでなく、はるかに安価な金型も実現します」と彼は付け加えます。 「このプロセスは自動車業界でよく知られており、高度に自動化された構成での圧縮成形により部品の品質が向上しますが、使用される航空宇宙材料は異なります。この場合、炭素繊維強化PPSと東レの炭素繊維です。 Advanced Composites(以前のTenCate)。このプロジェクトの終わりまでに、これらのテクノロジーのTRL6を達成する予定です」とLagraña氏は述べています。
COFRAREプロジェクト:RTMCフレームと熱可塑性せん断タイ
COFRARE 2020プロジェクトは、最初のCOFRARE2.0プロジェクトの拡張です。
Clean Sky 2 COFRARE 2.0プロジェクトの目標は、地域の航空機用の複合パネルベースの胴体で使用される炭素繊維複合フレームの競争力のある実行可能な製造プロセスを開発することでした。含まれるパートナー:
- ナポリを拠点とするTier1航空宇宙サプライヤーおよびエンジニアリング/工業化会社 DEMA (Design Manufacturing SpA、Somma Vesuviana、イタリア)
- EURECAT
- Applus + Laboratories の一部門であるLGAITechnological Center S.A. スペインのバルセロナでテストを提供しました。
次世代のCOFRARE2020プロジェクトの目標は、Clean Sky2胴体/キャビン統合地上デモンストレーターで使用される実物大の複合フレームとせん断タイを製造することです。このデモンストレーターは、Clean Sky 2のリージョナル航空機IADP(革新的な航空機デモンストレータープラットフォーム)内で編成され、2015年3月の共同技術プログラム文書のセクション5.2.2で詳しく説明されています。
2015年の合同技術プログラムでは、2つの飛行テストベッドと5つの大型統合地上デモンストレーターを含むリージョナル航空機開発の概要を説明しています。後者には、本格的な革新的な胴体と客室のデモンストレーターが含まれます。 :「胴体は、複合材料、構造、製造の技術の本格的なデモンストレーションになります。 ライフサイクル全体にわたって(影響ゼロに向けて)エコデザインとエネルギー消費の最適化を通じて、重量とコストの削減を[達成]し、環境への影響を最小限に抑えることを目的としています。」
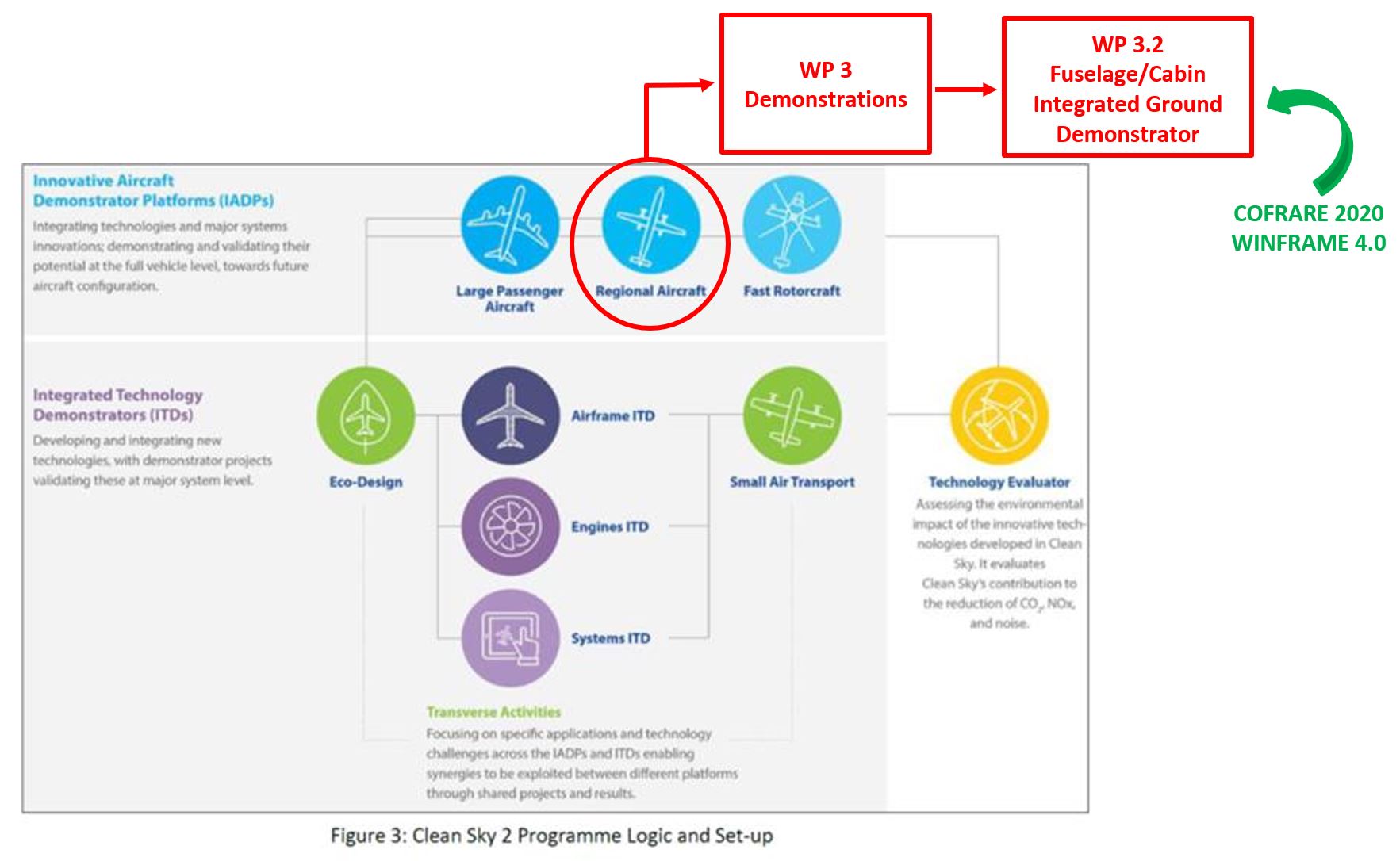
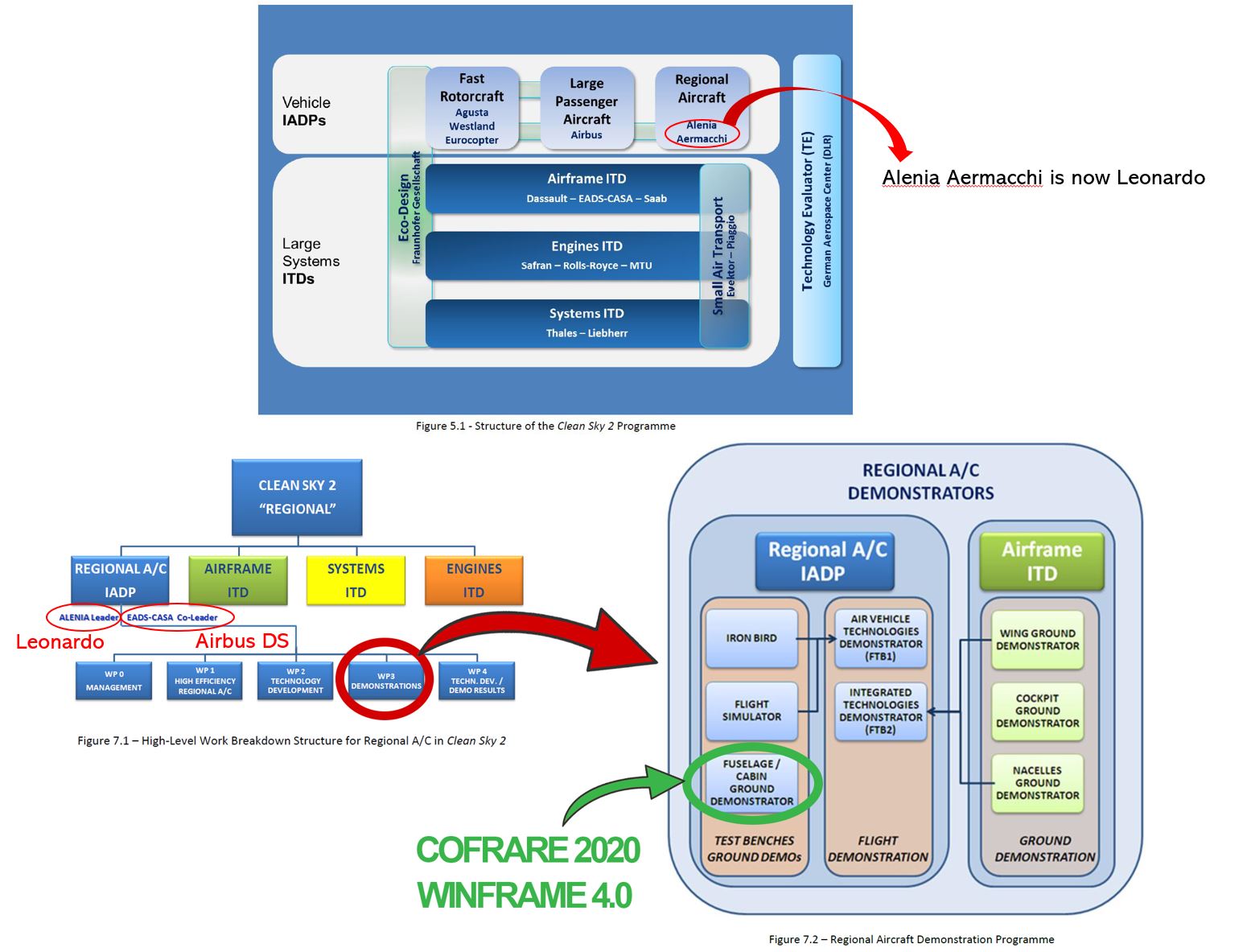
COFRARE2020プロジェクトパートナーには次のものが含まれます。
- レオナルド トピックマネージャーとして
- EURECAT
- DEMA
- 航空機のコンポーネントとアセンブリは Aを製造します。アベテ (ノラ/マリリアーノ、イタリア)。
「COFRARE2020では、胴体デモンストレーターに統合されるRTM(樹脂トランスファー型枠)を使用して胴体フレームを作成しています」とLagraña氏は説明します。 「私たちは、樹脂の射出に適したプリフォームを製造するシキボウ(大阪、日本)のZiplusテクノロジーを使用しています。」 Shikibo Ltd.は、Composite Alliance Corp.(米国テキサス州ダラス)の一部であり、さまざまな繊維予備成形技術を提供しています。
このプログラムの興味深い側面の1つは、Synthesites(Uccle、ベルギー)のセンサーを使用して、樹脂の到着、温度、圧力、Tg、および硬化をリアルタイムで監視することです。 「センサーは、樹脂注入戦略を最適化するために、複合部品とRTMツールの特定の領域に配置されています」とLagraña氏は述べています。注入は、Composite Alliance Corpの一部でもあるISOJET(Corba、France)が提供する高度に自動化されたシステムを使用して実現されます。合成センサーは誘電体センサーですが、交流(AC)に基づくほとんどの誘電体分析(DEA)とは異なります。 、Synthesitesは直流(DC)を使用します。 「当社のセンサーは、樹脂などの高抵抗率の材料で良好に機能します。単一の電圧を印加するため、複数の周波数を分析する必要はありませんが、硬化の最後でも高精度を実現します」とSynthesitesのディレクターであるDr. NikosPantelelis。
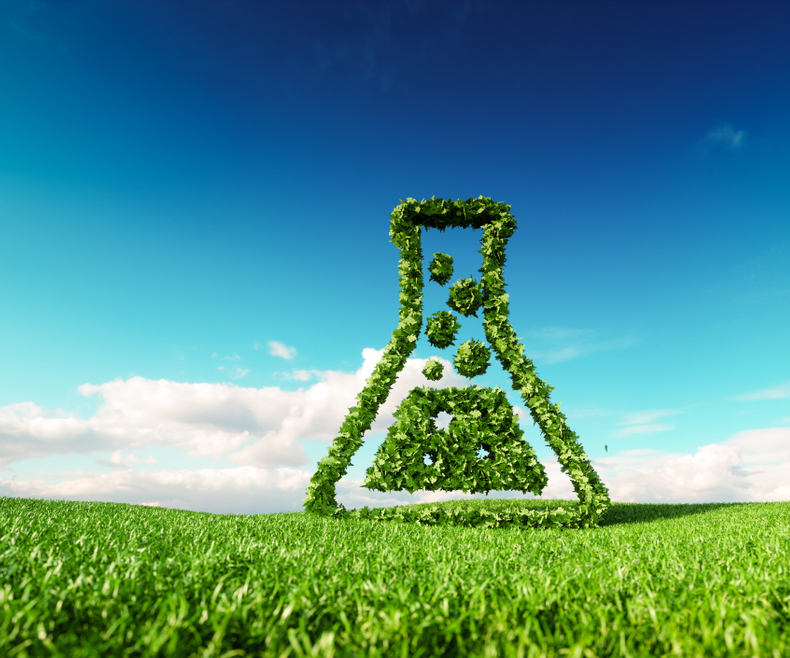
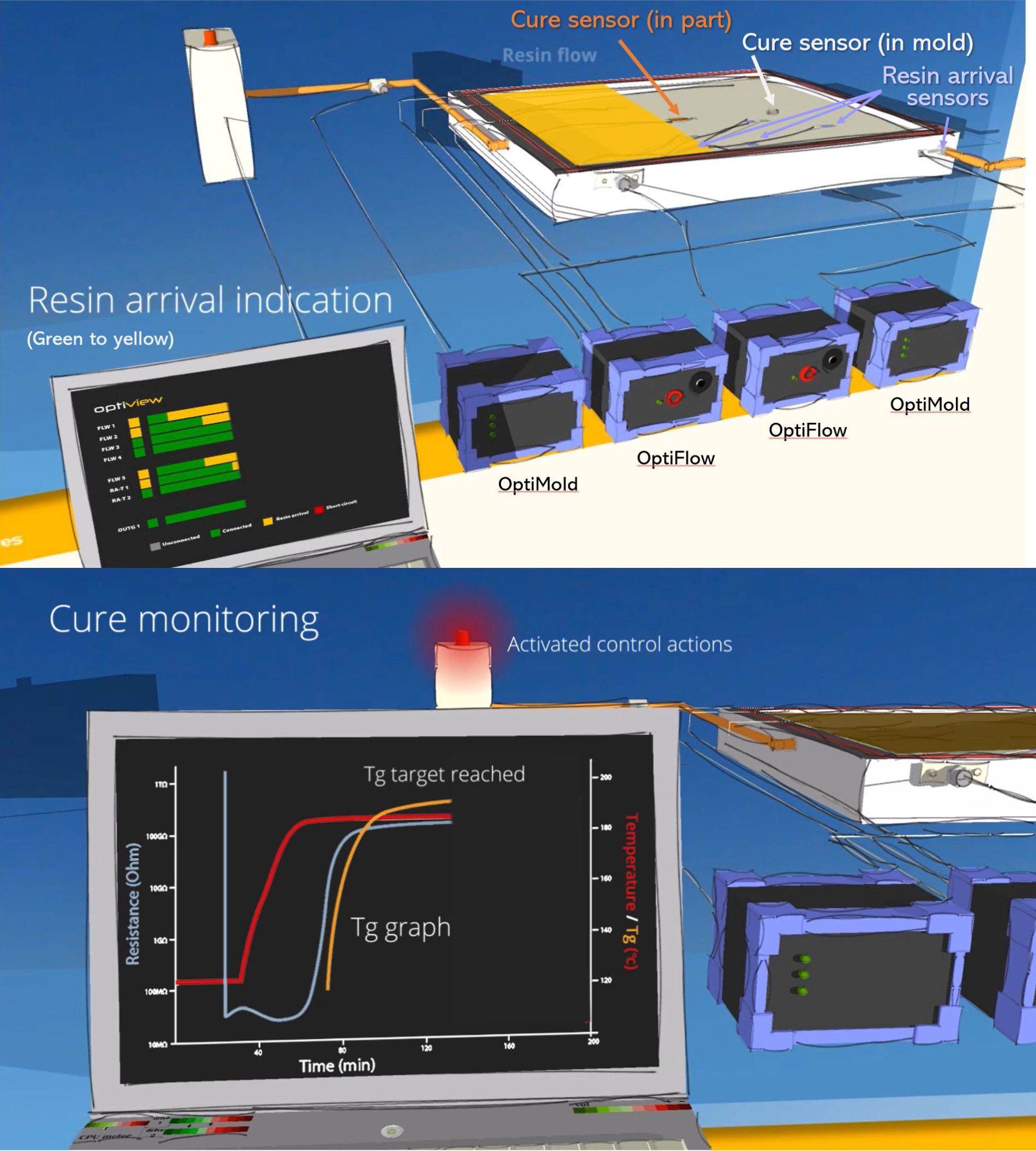
「2011年のSAMPEカンファレンスでSynthesitesに会いました」とLagrañaは回想します。 「硬化サイクルを短縮するためのセンサーについての理論。胴体フレームのプリフォームを自動化する方法を模索しており、HP-RTM(高圧RTM)でより高速な処理を使用することもできますが、それでも処理時間は3〜4時間です。ただし、Synthesitesでは、Tgを監視することで硬化サイクルを50%短縮しました。現在、プロパティのテストを行っています。これらのセンサーは高圧で動作しますが、RTM処理では、8バールの圧力しか使用していません。」
Synthesites DC誘電体センサー、OptiFlow液体樹脂流量監視システム、およびOptiMold硬化監視システムは、さまざまな風力ブレードメーカーによって製造されています。また、ボンバルディア航空宇宙(ベルファスト、英国)は、Cシリーズの現在のエアバス220用の液体複合成形翼を製造するために使用しています。ドイツ航空宇宙センター(DLR、スタッド、ドイツ)は、両方で最大50%の硬化サイクルの短縮を実証しました。オートクレーブプリプレグとRTMは、National Composites Center(NCC、ブリストル、英国)が、反応性の高い樹脂の場合でも、樹脂の温度と抵抗率のセンサー測定から行われるリアルタイムのTg計算が、硬化パネルから測定されるTgと同じくらい正確であることを示しました。微分走査熱量測定(DSC)を使用します。
TPCせん断タイを使用したフレームの結合
COFRARE 2020のもう1つの重要な部分は、RTM胴体Cフレームを複合胴体パネルに結合するために必要な数百のせん断タイとブラケットを製造するためのより大量生産方法です。 「圧縮成形によって製造された熱可塑性複合ブラケット用に255の異なる形状を開発しています」とLagraña氏は言います。 (注:GKNFokkerには複数のCleanSky 2プロジェクトがあり、大型旅客機IADPの多機能胴体デモンストレーター用のTPCブラケットを製造します。COFRARE2020でのこの作業は、小型のリージョナル航空機向けです。) マッチしたスチールツールと加熱プレスを使用した基本的な方法を以下に示します。 「このような圧縮成形ツールのコストはわずか2,000ユーロで、RTMツールと比較して非常に手頃な価格です」と彼は付け加えます。 「スタンピングはまた、非常に短いサイクルタイムを達成します。」
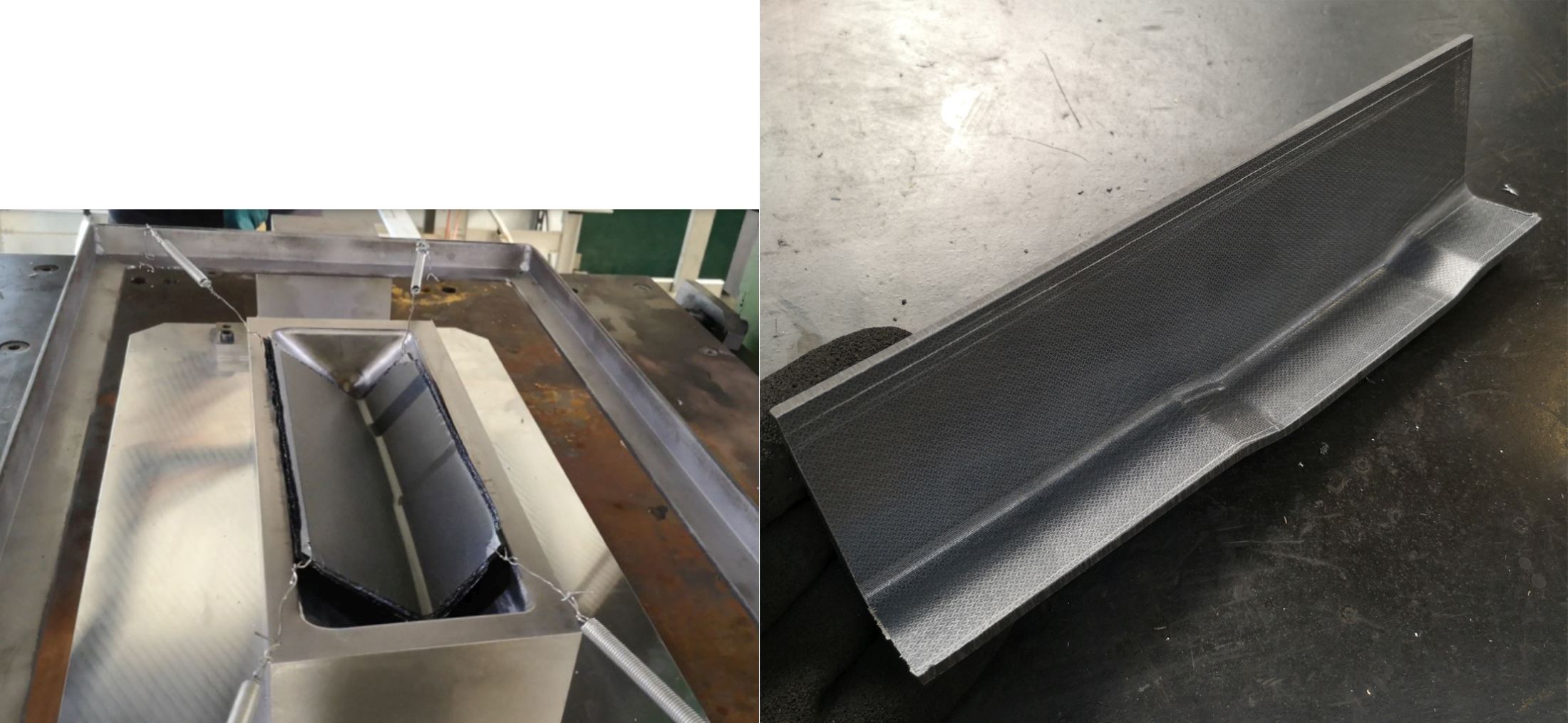
EURECATは、複合材料技術開発の最前線にとどまることに投資しています、とLagrañaは言います。 「クリーンな環境への圧力により、すべての輸送で複合材料の使用が劇的に増加し、手頃な価格とパフォーマンスが両立すると信じています。これが、お客様に提供するオートクレーブ外の自動化テクノロジーに焦点を当てている理由です。」
Clean Sky 2 STUNNINGおよびMECATESTERSプロジェクトに関する今後のブログにご注目ください。このブログでは、多機能胴体デモンストレーター用の溶接TPCブラケットの開発と、このプロジェクトのPAEKの完全な特性について説明します。また、Synthesitesについて、またCETMAの複合材料の開発についてさらに詳しくブログを書きます。 2020年はコンポジットにとって非常に興味深い年になるでしょう!
樹脂
- より薄い軽量複合材料にオーバーモールドするための熱可塑性ハニカムサンドイッチ
- 複合材料プロセスの最適化と制御のための超音波センサーのカスタマイズ
- 複合材料用の再処理可能、修理可能、リサイクル可能なエポキシ樹脂
- 複合材料の硬化監視のためのACおよびDC誘電測定の組み合わせ
- ソルベイ、レオナルドが熱可塑性複合材料の共同研究ラボを立ち上げる
- より民主的な複合材料のための多層熱可塑性テープ、AFPおよび樹脂注入
- 自動車用複合材料の最初の熱可塑性ドア
- ランクセスは、連続繊維強化熱可塑性複合材料の生産能力を拡大します
- TPACとTPRCは、熱可塑性複合材料のリサイクルプロセスを開発しています
- 熱可塑性複合材料の溶接
- 熱可塑性複合材料コンソーシアムは、自動車および航空宇宙向けの大量生産を目指しています