リニア パレット システム:収益性へのまっすぐな道?
改善されたソフトウェアにより、リニア パレット システムが大幅に強化されます
DMG Mori (イリノイ州ホフマン エステート) の最高システムおよび販売責任者である Adam Hansel 氏は、次のように完璧にまとめています。自動化したいかどうかを尋ねます。答えはイエスです。 100%」しかし、どのような自動化ですか?そして、どのマシンとプロセスですか?さまざまな企業にとって、論理的な答えは、複数の金属切断機と、場合によっては追加の操作を統合するリニア パレット システムです。一方、「論理的」とは必ずしも「簡単」または「心配いらず」という意味ではありません。
FMS とパレット プール システムを混同しないでください
フレキシブル マニュファクチャリング システム (FMS) とも呼ばれる基本的なリニア パレット システムは、1 つまたは複数のマシニング センターへのワークピースのロードとアンロードを中央保管場所から自動化します。工作物は直線レール上を移動し、追加の運動軸を備えた車両によって運ばれます。これにより、工作物を機械に移動し、そのテーブルに移動して、完成したら再び取り出すことができます。オペレーターは、個々のマシンではなく中央ステーションでジョブを設定し、中央コンピューターが作業の分散と実行を制御します。
最も一般的な構成では、ワークピースは固定具にボルトで固定され、固定具は均一なパレットにボルトで固定されます。これにより、機械がその標準パレット用に構成されている限り、いつでもどのジョブもどの機械にも移動できるため、システムの柔軟性が最大化されます。リニア パレット システムのもう 1 つの重要な機能は、最初の設置後に追加の工作機械、より多くのストレージ、さらには検査などの非機械操作を含めるように拡張できることです。一部のシステムには、10 台以上のマシニング センターと、3 段に積み上げられた数十台のパレット棚があります。
このように、リニア パレット システムはパレット プール システムとは異なります。後者は、システムおよび大型機械のスペシャリストである Bob Baldizzi 氏のように、「マシンのインテリジェントでない拡張」と考えることができます。Doosan Machine Tools America (Pine Brook、 NJ)が説明した。 「パレットプールシステムでは、マシン自体に追加のソフトウェアがシステムを実行します。通常、プール内のどのパレットにどのプログラムが関連付けられているか、およびそれらのパレットがマシンを通過する順序をソフトウェアに伝えることに制限されています。それでおしまい。生産スケジュールはありません。データ管理なし。報告なし。これは、機械に対するより大きなパレット システムの拡張にすぎません。」パレット プール システムは、通常は円形の配置ですが、線形の場合もあり、混乱を招く可能性があります。
Fastems LLC (オハイオ州ウェストチェスター) の David Suica 社長は、次のように述べています。 「パーツを変更したい場合は、通常、マシン内のツール、パーツ プログラム、および各パーツに必要なオフセットを変更する必要があります。パレット プールは、一連の同じ部品に適しています。しかし、販売できる量で必要なものだけを作りたい場合は、通常、リニア パレット システムの方が適しています。」
スピンドル使用率 90% 以上
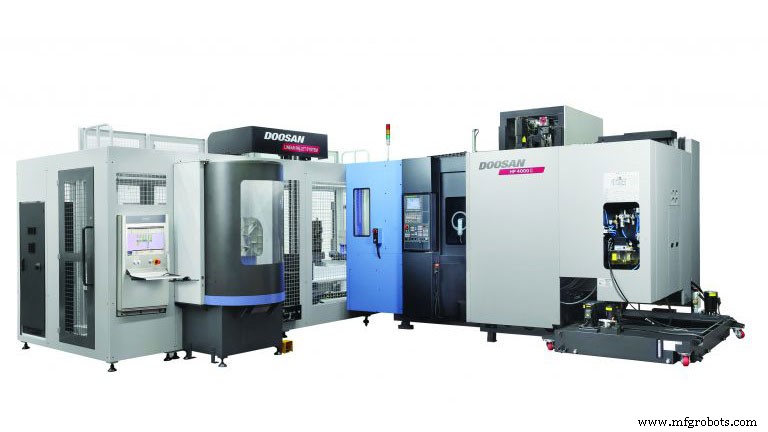
状況は異なりますが、FMS なしでスピンドル使用率が 50 ~ 60% を超えるマシン ショップはないようですが、FMS を適切に使用している場合は、90% 以上の率が見られます。そして、場合によっては格差がさらに大きくなります。 Hansel 氏は次のように述べています。ワークピースの交換、治具の交換、およびクリップボードで効率的に多くのリソースをスケジューリングすることはまったく不可能です。」 Suica は次のように説明しています。その時間のセットアップが費やされると、本番環境に戻すことはできません。」
これは、過去数年間のリニア パレット システムにおける最大かつ最も重要な改善であるソフトウェアを示しています。多かれ少なかれ、すべての FMS プロバイダーは、システムのスループットを最大化できるキャパシティ プランニング ソフトウェアを提供しています。ヘンゼルは典型的なシナリオを次のように説明しています。ジョブの優先度や特定の時間までに必要な数などのパラメーターを設定します。または、車を作っているとしましょう。 2 つの車軸と 3 つの車輪を製造することはありません。 4つの車輪が必要です。したがって、ソフトウェアにロットサイズを生成するように指示できます。どちらの場合でも、ソフトウェアはリソースを適切に使用して必要な生産を得る方法を自動的に計算します。適切に計画して固定具と工具を準備し、ソフトウェアに作業を任せれば、90 ~ 95% の稼働率を完全に達成できます。」
ジョブ ショップなどに最適
FMS の恩恵を受けるのは誰ですか?小さなジョブ ショップから、場合によっては 100,000 個以上の部品を製造するオペレーションまで、あらゆる人が対象です。マキノ社 (オハイオ州メイソン) の製品ライン マネージャーであるジョン・アインバーガー氏は次のように述べています。マシニング センターからワーク セッティングを行うことで、スピンドルの使用率が向上します。
「しかし、季節生産を行う人々の間で、より多くの生産量を求めるアプリケーションもあります」と彼は続けました. 「たとえば、彼らが年間 80,000 個の製品を製造しているが、それを 3 か月間しか製造せず、次の 4 か月間は別のバリエーションまたは別のものを実行するとします。レクリエーショナル ビークルのパワートレイン業界は、この種の生産スキームに適合します。オフシーズンには、スノーモービルが売れるときはボートのモーター、ボートが売れるときはスノーモービルのモーターなど、シーズンに必要なものを作っています。当社の FMS は、このような大量の状況にあるお客様にとって非常に便利なツールです。」
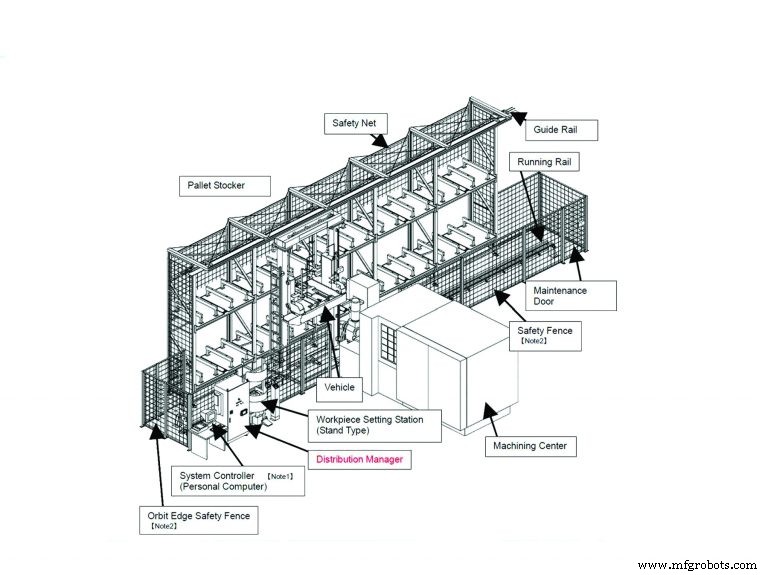
Hansel 氏は次のように付け加えています。これは、そのようなシステムには多くの冗長性があるためです。ホリゾンタルには通常、大きなツール マガジンがあり、冗長なツールをマガジンに配置してより長いシフトを実行できます。ツールが壊れたり摩耗したりした場合は、次のツールに進むことができます。」一方、Liebherr (ミシガン州サリーン) の人々は、特定のパレット上のすべての部品のサイクル時間が合計で 5 分を超える場合に、パレット ハンドリング セルが最も費用対効果が高いと指摘しました。そうしないと、車両がパレットを切り替えるのを待つ時間が無駄になります。
これらのシステムがどれほど普及しているかを理解するために、Einberger 氏によると、Makino は過去 20 年間に北アメリカだけで 575 台のリニア パレット システムを設置したとのことです。
横向きだけじゃない
従来、リニア パレット システムは一般に横型マシニング センターに接続されていました。これは、「横型機械にはほとんどの場合、パレット チェンジャーが付属しているからです」と Doosan の Baldizzi 氏は説明します。 「ロード ステーション エリアには常に 2 つ目のパレットがあり、独立型の設定では、機械の稼働中にオペレーターが部品の積み降ろしに使用します。機械加工サイクルを中断することなく、クレーンがロード ステーション エリアから積み降ろしできるため、これは FMS の利点です。典型的な縦型マシニング センターにはそれがなく、ほとんどの 5 軸加工機にもありませんが、Doosan のようなメーカーは現在、FMS に接続できるパレット チェンジャーを 5 軸加工機に装備しています。」
さまざまなタイプのマシニング センターを混在させるだけでなく、他の機能を FMS に統合することも可能です。異なるメーカーのマシンを統合することもできますが、その場合、Fastems のような「不可知論者」の自動化会社と協力する方が良いかもしれません。アプリケーション、チップへの自動ツール オフセット書き込みを備えた Zoller、CMM、ウォッシュ ステーション、およびバリ取りシステムがすべて完全に統合されています」と Suica は述べています。 「私たちのソフトウェアは、ツールのオフセットと検査データも自動的に管理します。」
これらのオプションの一部では、1 つまたは複数のステーションにロボットを配置したり、従来の FMS 車両をレール上のロボットに置き換えたりする必要があります。アインバーガー氏によると、マキノは後者のハイブリッドを「主に航空宇宙構造分野におけるいくつかの要件への回答として提供しています。これらの顧客の中には、部品を平らな面にロードすることから始めて、サブフィクスチャを取り、横型マシニング センターにロードできるという利点を求めて、レール上のロボットを使用して機械に部品を自動ロードしたいと考えている人もいます。
「このアプローチは、同じマシニング センター内で最初の操作が 4 軸操作で、2 番目の操作が 5 軸操作である複数操作部品でも非常に有利です。」と彼は続けます。 「したがって、マシニング センターのパレット 1 は、サブプレート上の部品を受け入れる 4 軸のトゥームストーンであり、同じマシニング センターの 2 番目のパレットは、同じサブプレート上の同じ部品を受け入れる 5 軸テーブルにあります。その後の 5 軸操作。ロボット オン レール システムは、パレット ハンドリング FMS とディスクリート パーツ ハンドリング ロボットの間のギャップを埋めます。」
一方、バルディッツィ氏は、ある種の柔軟性を得ると、別の柔軟性を失うことになると警告しています。 「いくつかの機能を水平で実行し、別のパレットを必要とする旋削機能を備えた 5 軸マシンで他の機能を実行するなど、さまざまなパレットに適応する需要が見られ始めています。さらに、操作を実行するために必要なこれらすべてのマシンを FMS に置くことができます。欠点は、FMS の柔軟性の一部が失われることです。これは、ソフトウェアが、この特定の時間にこの特定のマシンにのみこのパレットが移動することを確認する必要があるためです。一方、FMS に複数のマシンがあり、すべて同じである場合、パレットにボルトで固定された作業は、いつでもどこでもどこへでも移動できます。」
コストと課題
Einberger 氏によると、レール システム、車両、ワークセット ステーション、パレット ストッカー スタンドを含む初期 FMS のコストは、固定具を除いた特定のマシニング センターのコストの約 3 分の 2 です。したがって、スループットを 2 倍にするという約束を考えると、それは良い見返りです。しかし、Hansel 氏は次のように述べています。そのため、どのマシンを購入するかを決定する際に、設備の実際のコストが含まれていないことがあり、システムを完全に使用できなくなる可能性があります。たとえば、機械を 8 時間以上稼働させ続けるのに十分な作業を積み込める場合にのみ、完全自動運転または 3 番目のシフトをなくすというメリットが得られます。」
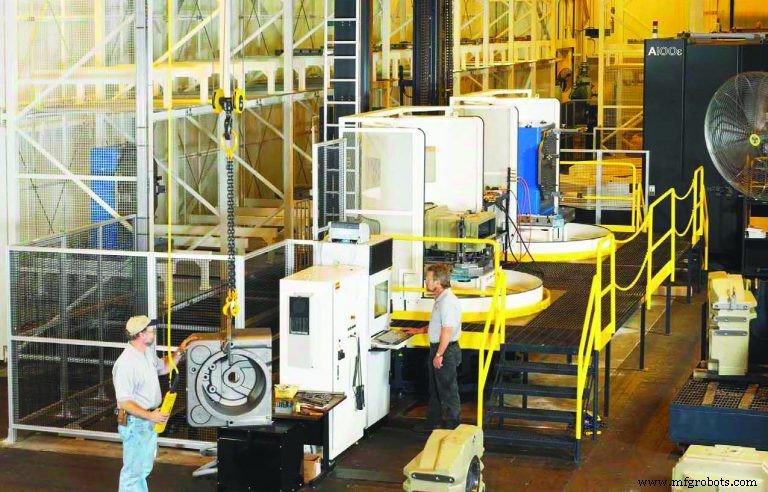
ただし、FMS の最大の課題は操作であることに誰もが同意します。 Suica は次のように述べています。優れたプログラムを使用している場合、ツール オフセットはわかっています。スケジュールがうまくいっていれば、それは非常にうまく機能します。ほとんどの企業にとって最大のことは、準備ができていることを確認するために必要な規律です。これは、すべての企業が経理部門に課している規律と何ら変わりはありません。請求書を照合し、それらが正しいことを確認し、税金を支払うことを確認します。簡単ではありませんが、ぴったりと並んで完成です。同じことを製造現場で行って統合することで、エラーの原因となる人的要素を取り除くことができます。」
Suica はまた、「世に出回っているリニア パレットとロボット システムのほとんどは、自動化されたアイランドである傾向があります。彼らは自分が知っていることを知っており、あなたのオペレーション内の他の何にも接続されていません.注文や原材料の摂取などを追跡する ERP [エンタープライズ リソース プランニング] パッケージがあるかもしれません。工具、工具オフセットの決定、および測定システムに多額の費用を費やしてきました。しかし、これらすべてのシステム間の情報の流れは依然として手動のままです。」この統合の相対的な欠如により、企業は人員の大幅な節約を達成できません。
Suica によると、これらのシステムを完全に統合すれば、8 ~ 9 台のマシンがわずか数人で稼働することも珍しくありません。 「私たちは現在、3 人が担当する 8 台のマシンを備えたシステムに取り組んでおり、そのうちの 1 人はチェックを自動化したくなかったためにチェックを行っているだけです。 2 交代制なので、ラインには 6 人がいますが、現在は 14 人です。しかし、それを行うには高レベルのシステム統合が必要です。そうでなければ、自動化に何をすべきかを伝えるために多くの人が必要です。統合とソフトウェアが鍵です。」トレーニングとサポートも同様です。そのため、DMG 森、マキノ、およびその他の企業は、専用の自動化チームと施設を持っています。
ただし、ソフトウェアがすべてを解決するわけではありません。 Baldizzi 氏は、機械の信頼性が絶対的に最優先事項であると指摘しました。オペレータが横型マシニングセンタに積み込むために立っていた場所は、現在は FMS に囲まれています。押しボタンがなくなりました。その機械に部品を手動で効率的にロードおよびアンロードできる可能性はほとんどありません。そのため、ボンネットの下を調べて、FMS が機械的に 90% のアップタイムを実現できることを確認してください。」
高品質のビルダー向け。これには、地下鉄の 3 番目のレールのように、接触点以外に可動部分がない、車両の上のバス バーを介して 3 相の高電圧電力を流すことが含まれます。 「堅牢性の低いシステムでは、車両が前後に移動する際に、ケーブル トラック内の一連のケーブルに車両をつなぎます。これは、ケーブルが絶えず曲がっているため、疲労点を引き起こします」と Baldizzi 氏は述べています。 「第二に、サーボドライブ、モーター、制御などの間で発生する必要があるデータ通信のために、トンネルに囲まれた光学アイを使用して、これらのケーブルの必要性をミックスから取り除きます。
「FMS にクーラント チャネル、ダクト、配管があるかどうかも調べて、パレットが保管されたときにパレットに残っているクーラントが回収され、機械のクーラント タンクまたは中央リポジトリに戻されるようにします。床がぐちゃぐちゃになってしまいました」と Baldizzi 氏は締めくくりました。
自動制御システム