押し出しとは何ですか?さまざまなタイプの押し出しプロセス?
押し出しプロセスは、ワークメタルをダイホールに押し込むか圧縮して特定の必要な断面形状を実現するバルク成形プロセスの一種です。
簡単に言えば、押し出しは、金属を高圧下でダイホールに押し込み、その断面を圧縮する金属加工手順です。
押し出しプロセスの進化以来、世界は押し出しに依存して、中空または中実の任意の形状のバー、チューブ、およびセクションを製造するようになりました。
この操作では、ビレットをダイに押し込んだり引っ張ったりする必要があるため、ビレットを押し出すのに必要な力はかなり大きくなります。高温での金属の変形抵抗は低いため、熱間押出しが最も一般的な方法ですが、冷間押出しは一般に軟質金属でのみ実行されます。
履歴:
押し出しの概念は成形のプロセスから生まれますが。 1797年に、ジョセフ・ブラマーという名前のエンジニアが押し出しのプロセスの特許を取得したことが記録されています。
この試験では、金属を予熱してから、ビレットからパイプを作るためにダイキャビティに金属を押し込みました。彼は手動のプランジャーを使用して金属を押し出しました。
ブラマーは、押し出しの発明後に油圧プロセスを発明しました。次に、トーマス・バーは、油圧プレスの技術と基本的な押出技術を使用して、個々の技術を組み合わせてパイプ(中空)を製造しました。その後、1820年に特許を取得しました。
その後、この技術は成長する世界で基本的なニーズとなりましたが、プロセスは硬質金属では機能しませんでした。 1894年、トーマスバーは銅と真ちゅうの合金を使用した押し出しを導入し、押し出し技術に進化をもたらしました。
押し出し技術の発明以来、このプロセスは、複雑な構造を持つ幅広い製品を可能な限り低いコストで製造できるさまざまな技術に進化しました。
押し出しプロセスの分類またはタイプ:
さまざまなタイプの押し出しプロセス :
- 熱間押出し
- 冷間押し出し
- 温かい押し出し
- 摩擦の押し出し
- マイクロ押し出し
- 直接押し出し
- 間接押し出し
- 静水圧押出および
- 衝撃押し出し プロセス。
#1。ホット押出プロセス:
この熱間押出プロセスでは、ビレットは再結晶温度を超えて加工されます。 この熱間加工により、ワークピースが加工硬化するのを防ぎ、ラムがワークピースをダイに簡単に押し込むことができます。
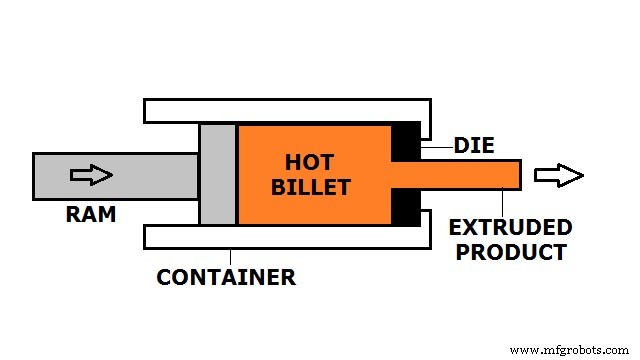
熱間押出しは、通常、水平油圧プレスで実行されます。このプロセスに含まれる圧力は、30MPaから700MPaまで変化する可能性があります。高圧を損なわないように、潤滑が採用されています。低温押出成形では潤滑剤としてオイルまたはグラファイトが使用され、高温押出成形ではガラス粉末が使用されます。
ビレットには、高品質の動作を得るために0.5 Tm〜0.75Tmの熱が供給されます。
一般的に使用されるいくつかの材料の熱間押出し温度は、次のとおりです。
資料 | 温度(℃) |
アルミニウム | 350〜500 |
銅 | 600〜1100 |
マグネシウム | 350〜450 |
ニッケル | 1000〜1200 |
鋼 | 1200〜1300 |
チタン | 700〜1200 |
PVC | 180 |
ナイロン | 290 |
熱間押出プロセスの利点:
- 変形は要件に応じて制御できます。
- 加工硬化のため、ビレットは強化されていません。
- 押すのに必要な力は少なくなります。
- 時期尚早の亀裂のある材料も加工できます。
熱間押出プロセスのデメリット:
- 表面仕上げが悪い。
- 寸法精度は妥協できません。
- コンテナの寿命が短くなります。
- 表面酸化の可能性。
#2。冷間押出し:
金属をナメクジで叩いて成形するプロセスです。この打撃は、閉じた空洞内のパンチまたはラムで達成されます。ラムは金属をダイキャビティに押し込み、中実のビレットを中実の形状に変換します。
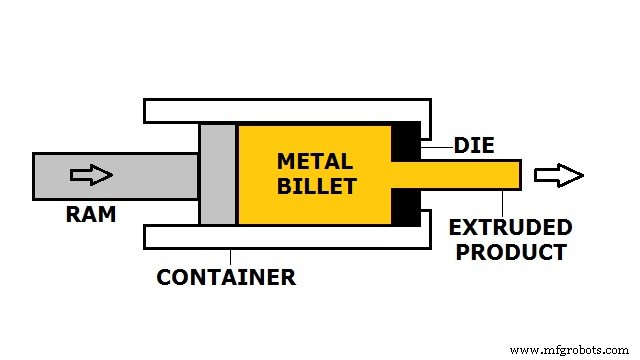
このプロセスでは、ワークピースは室温または室温よりわずかに高い温度で変形します。
必要な力が高すぎる場合は、この手法で強力な油圧プレスを使用します。圧力範囲は最大3000MPaです。
利点:
- 酸化なし。
- 製品の強度が向上しました。
- より厳しい公差。
- 表面仕上げの改善。
- 硬度が向上します。
短所:
- より高い力が必要です。
- 動作するにはより多くの電力が必要です。
- 非延性材料は加工できません。
- 押し出される材料のひずみ硬化は制限です。
#3。温間押出成形プロセス:
温間押出しは、ビレットを室温より高く、材料の再結晶温度より低く押し出すプロセスです。このプロセスは、押し出しプロセス中に発生する微細構造の変化から材料を防止する必要がある場合に使用されます。
このプロセスは、必要な力と延性の適切なバランスを実現するために重要です。この操作で使用される金属の温度は、摂氏424度から摂氏975度の間です。
ウォームプロセスの利点:
- 強度の向上。
- 製品の硬度が向上しました。
- 酸化の欠如。
- 非常に厳しい公差を実現できます。
短所:
- 非延性材料は押し出しできません。
- 暖房設備が追加されます。
#4。摩擦押し出し:
摩擦押し出し技術では、ビレットとコンテナを互いに反対方向に回転させ、同時にビレットをダイキャビティに押し込んで目的の材料を製造します。
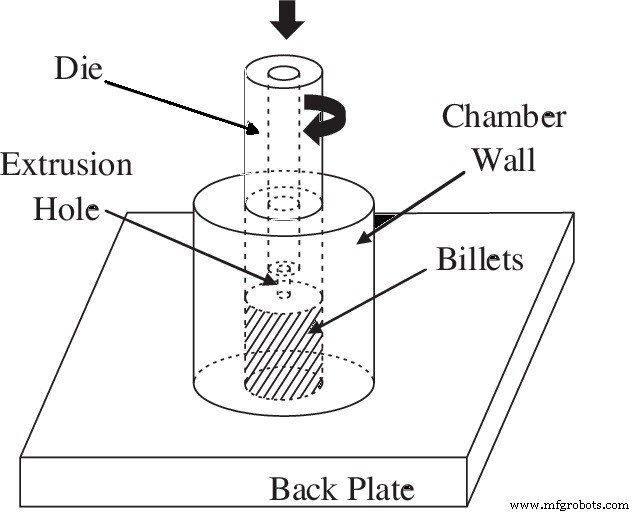
このプロセスは、ビレットとダイの間の相対回転速度の影響を受けます。チャージとダイの相対的な回転運動は、プロセスに大きな影響を及ぼします。
第一に、それはビレットを塑性変形させる多数の剪断応力の発生をもたらす。第二に、ビレットとダイの間の相対運動中に大量の熱が発生するため、予熱が不要であり、プロセスがより効率的になります。
金属粉末、フレーク、機械加工廃棄物(チップまたは削りくず)、固体ビレットなどのさまざまな前駆体チャージから直接、実質的に統合されたワイヤー、ロッド、チューブ、およびその他の非円形の金属形状を生成できます。
摩擦プロセスの利点:
- 加熱は必要ありません。
- せん断応力が発生すると、製品の疲労強度が向上します。
- あらゆる種類の素材をビレットとして使用できるため、このプロセスが経済的になります。
- 低エネルギー入力。
- 耐食性が向上します。
摩擦のデメリット プロセス:
- 予想される酸化。
- 高い初期設定。
- 複雑な機械。
#5。マイクロ押出プロセス:
このプロセスはサブミリ波範囲の製品の製造を扱っていることがその命名法によって理解されています。
マクロレベルの押し出しと同様に、ここのビレットはダイオリフィスを通過して、ビレットに期待される形状を生成します。出力は1mmの正方形に収まります。
前方または直接および後方または間接のマイクロ押出しは、マイクロエレメントを製造するためにこの時代に使用されている2つの最も基本的な技術です。
前方マイクロエクストルージョンでは、ビレットを前方に駆動するラムがあり、ビレットは同じ方向に移動しますが、後方マイクロエクストルージョンでは、ラムとビレットが反対方向に移動します。
マイクロエクストルージョンは、生体吸収性ステントから制御された薬物放出システムに至るまで、吸収性および埋め込み型医療機器のコンポーネントの製造に広く使用されています。
一方、機械分野では、小さな歯車や小さなパイプなどの製造での用途が広く見られます。
マイクロプロセスの利点:
- 非常に複雑な断面を作成できます。
- 小さな要素を作成できます。
- 幾何公差の改善。
短所 :
- 私たちのニーズを満たすために小さなダイとコンテナを作成することは挑戦です。
- 熟練した労働者が必要です。
#6。直接または前方押し出し:
直接押出プロセスでは、最初に金属ビレットが容器に入れられます。コンテナには輪郭のあるダイホールがあります。ラムを使用して金属ビレットをダイホールに通し、製品を製造します。
このタイプでは、金属の流れの方向はラムの移動方向と同じです。
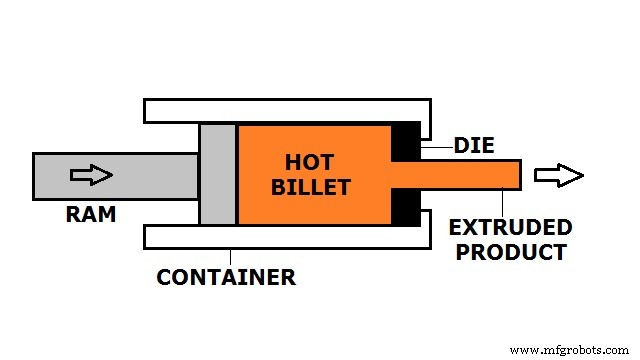
ビレットがダイ開口部に向かって移動するように強制されると、ビレットの表面と容器の壁との間に大きな摩擦が発生します。摩擦が存在すると、ラムの力を大幅に増加させる必要があるため、より多くの電力を消費します。
このプロセスでは、タングステンやチタン合金などの脆い金属は、プロセス中に破壊されるため、押し出すのが困難です。プロセス全体の引張力により、微小亀裂が急速に形成され、破壊が発生します。
タングステンやチタン合金などの脆い金属は、プロセス中に破壊されるため、押し出しが困難です。引張力により、微小亀裂が急速に形成され、破壊が発生します。
また、ビレットの表面に酸化物層が存在すると、摩擦が激しくなります。この酸化物層は、押し出された製品に欠陥を引き起こす可能性があります。
この問題を解決するために、ラムと作業ビレットの間にダミーブロックを配置して、摩擦を軽減します。
チューブ、缶、カップ、小型ギア、シャフト、その他の押し出し品がその例です。
ビレットの一部は、常にすべての押し出しの最後に残ります。それはお尻と呼ばれます 。ダイの出口を過ぎてすぐに切断することにより、製品から除去されます。
直接プロセスの利点:
- このプロセスでは、より長いワークピースを押し出すことができます。
- 材料の機械的特性の改善。
- 良好な表面仕上げ。
- 冷間および熱間押出しが可能です。
- 継続的に運用する能力。
直接プロセスのデメリット:
- 脆い金属は押し出すことができません。
- 大きな力と高い電力要件。
- 酸化の可能性。
#7。間接または後方押し出し:
この後方押し出しプロセスでは、ダイは静止したままですが、ビレットとコンテナは組み合わせて移動します。ダイは、コンテナではなくラムに取り付けられています。
金属は、ラムによって圧縮されるときに、ラムの動きとは反対の方向にラム側のダイ穴を通って流れます。
ビレットが圧縮されると、材料はマンドレル間を通過するため、ダイ開口部を通過します。
ビレットとコンテナの間に相対運動がないため、摩擦は記録されません。これにより、直接押し出しプロセスよりもプロセスが持ち上げられ、使用されるラム力が直接押し出しよりも小さくなります。
ダイを静止状態に保つために、コンテナの長さよりも長い「ステム」が使用されます。ステムの柱の強度によって、最終的な最大押出長が決まります。
ビレットはコンテナと組み合わせて移動するため、すべての摩擦力を簡単に排除できます。
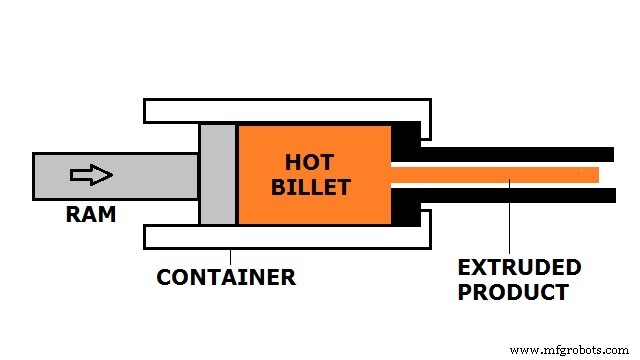
間接プロセスの利点:
- 必要な押し出し力は少なくて済みます。
- より小さな断面を押し出すことができます。
- 摩擦を30%削減します。
- 動作速度の向上。
- 摩耗はほとんど記録されていません。
- 金属の流れがより安定しているため、押し出し断層や粗粒リングゾーンが発生する可能性は低くなります。
間接プロセスのデメリット。
- 押し出される材料の断面は、使用するステムのサイズによって制限されます。
- 押し出し後の残留応力の可能性。
- 不純物や欠陥は表面仕上げに影響を与え、製品を危険にさらします。
#8。静水圧押出:
静水圧押出プロセスでは、ビレットはコンテナ内の流体に囲まれ、ラムの前進運動によってビレットに押し付けられます。流体による容器内の摩擦はなく、ダイホールでの摩擦はほとんどありません。
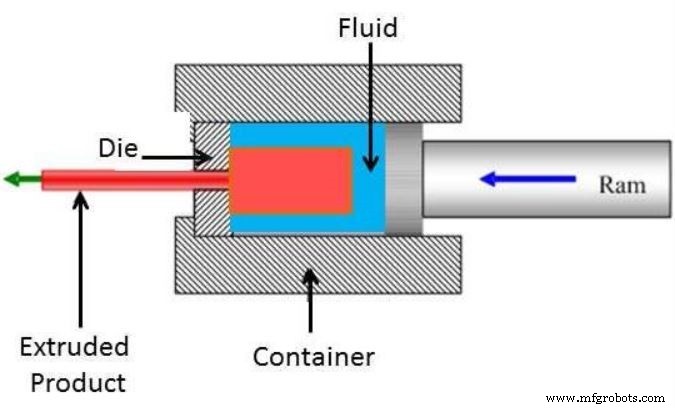
ビレットは均一な静圧にさらされているため、コンテナのボアを充填するときに邪魔になりません。これにより、長さと直径の比率が非常に大きいビレットが得られます。ワイヤーのコイルでさえ、完璧に押し出されたり、断面が不均一になったりする可能性があります。
静水圧押出と直接押出の主な違いは、静水圧押出中にコンテナとビレットが直接接触しないことです。
高温で作業するには、特殊な液体とプロセスを使用する必要があります。
材料が静圧にさらされ、摩擦がない場合、その延性は増加します。結果として、この方法は、一般的な押し出し方法には脆すぎる金属に使用される可能性があります。
このアプローチは延性のある金属に使用され、高い還元率を可能にします。
利点:
- 押し出された商品は、優れた表面研磨があり、寸法が正確です。
- 摩擦の問題はありません。
- 最小化された力の要件。
- プロセスにビレットの残留物は残っていません。
- 材料の流れは均一です。
短所:
- 高温で操作する場合は、特殊な液体と手順を使用する必要があります。
- 各ビレットは、作業前に片方の端を準備して先細にする必要があります。
- 液体を封じ込めるのは難しいです。
#9。衝撃押し出し:
衝撃押し出しは、金属押し出しプロファイルを作成するためのもう1つの主要な方法です。材料を柔らかくするために高温を必要とする従来の押し出しプロセスとは対照的に、衝撃押し出しはしばしば冷たい金属ビレットを使用します。これらのビレットは高圧と効率で押し出されます。
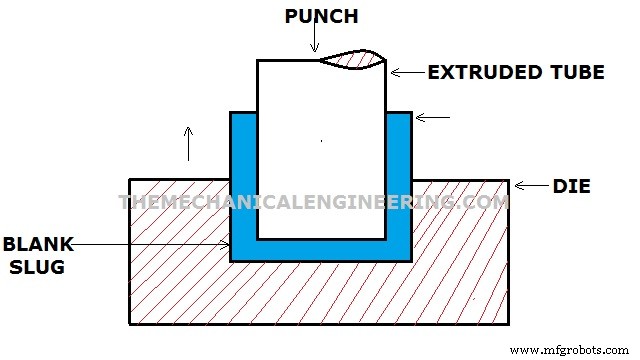
適切に潤滑されたスラグがダイキャビティに配置され、従来の衝撃押出操作中にパンチで一気に打たれます。これにより、金属がダイとパンチの間の隙間を通ってパンチの周りに逆流します。
このプロセスは、鉛、アルミニウム、スズなどのより柔らかい材料でより効果的に機能します。
このプロセスは常にコールド状態で実行されます。後方衝撃プロセスにより、非常に薄い壁が可能になります。たとえば、歯磨き粉のチューブやバッテリーボックスを作ります。
それはより速い速度でより短いストロークで実行されます。圧力をかける代わりに、衝撃圧力を使用してビレットをダイから押し出します。一方、インパクトは、前方または後方への押し出し、あるいはその2つの組み合わせによって実行できます。
利点:
- サイズの大幅な縮小。
- クイックプロセス。加工時間を最大90%短縮しました。
- 生産率の向上。
- 許容範囲の整合性が向上しました。
- 最大90%の原材料節約。
短所:
- 非常に高い圧縮力が必要です。
- ビレットのサイズには制限があります。
押し出し力に影響を与える要因:
押し出し力に影響を与える次の要因は次のとおりです。
- 動作温度。
- 水平または垂直の機器の設計。
- 押し出しのタイプ。
- 押し出しの比率。
- 変形の量。
- 摩擦パラメータ。
押し出しプロセスのアプリケーションまたは用途:
- チューブや中空パイプの製造に広く使用されています。また、プラスチックオブジェクトの製造にも使用されます。
- 押し出しプロセスは、自動車産業でフレーム、ドア、窓などを製造するために使用されます。
- 金属アルミニウムは、多くの産業で構造工事に使用されています。
産業技術