ギアカッティングとは何ですか?さまざまな種類の歯車切削プロセス?
こんにちは、お元気ですか。この記事では、さまざまな種類の歯車切削プロセスについて説明します。詳細に。まず、はじめに、少し歴史を見てから、さまざまな種類の歯車切削プロセスをすべて学習します。
最初に紹介を始めましょう
歯車切削の概要:
歯車は機械の重要な構成要素です。これは、機械の一方のシャフトからもう一方のシャフトに動力または運動、あるいはその両方を伝達することを唯一の目的とする硬い剛性の要素です。
それは、その周囲に沿って数えられる数の歯を備えた丸いブランクホイールです。ギアは厳しい使用条件を通過します。機械の分野での広範な要求を満たすために、歯車を堅牢で信頼性が高く、効率が高く、経済的なものとして設計することが重要です。
歯車の設計の細部は、それらの製造を特別なものにします。歯車の製造は、もっぱら正確な仕事です。ギアの設計は、世界中の何世紀にもわたって標準のままです。
歯車の切断は、歯車のみを切断するように設計された特殊な機械で実行されます。何年にもわたって、歯車の切断以外の多目的操作を実行できるが、歯車の大規模生産には適していない、まだ時代遅れではないフライス盤があります。
歯車切断の歴史:
古代には、動きと力を伝達するために一種の丸いブランクホイールが使用されていました。フリクションホイールは図1に示すようなシンプルなデザインでした。 1.0。
ホイールは、各シャフトの端に固定された単純な丸いディスクでした。動力の伝達は、一方のシャフトの面をもう一方のシャフトの面の上に転がすことによって達成されました。
嵌合部品は、それらの間に生じる摩擦によって互いに回転しました。その後、1897年の発明として、Herman Pfuaterは、歯車と呼ばれる歯車の土台となる歯車を切断できる機械を発明しました。
それから今まで歯車切断技術が実践されています。
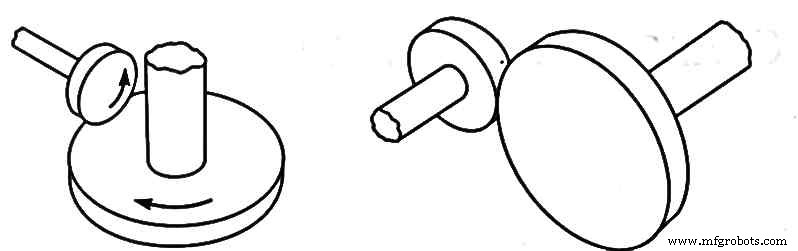
歯車の製造方法:
自動化の世代では、歯車は3つの主要な方法で製造されています。
- キャスト
- フォーミング
- 金属の除去
1。キャスティング:
歯車はさまざまな鋳造プロセスで製造できます。最も一般的で経済的なプロセスは砂型鋳造です。大型の歯車やモジュールを低コストで製造できます。
これらの歯車は一般に粗く不正確であり、動作音と動きの精度が許容されるアプリケーションも同様です。砂型鋳造は、1回限りまたは少量のバッチに適しています。インベストメント鋳造で作られた歯車は、より高い寸法精度と優れた表面仕上げを備えています。
これらは、砂型鋳造で作られた歯車と比較して、大きな負荷に耐える強力な材料を使用して製造できます。
射出成形はまた、より高い精度と動きで低負荷に使用できる熱可塑性プラスチックの歯車を生成します。
シェルモールドは、最も安価であるため、小さな歯車の製造にも使用されることがあります。ただし、鋳造は歯車の大量生産の要件を満たしていません。
2番目の方法は成形プロセスです
2。フォーミング:
成形法による歯車の製造は、ロール成形、押出成形、および冷間引抜プロセスを実行に移します。
2.1ロールフォーミング:
このプロセスでは、ギアブランクがシャフトに取り付けられ、ローリングダイに対して強制的に回転させられます。いくつかの回転数が与えられます。このダイをブランクホイールに押し付けると、歯付きホイールがしっかりします。
この工程で作られた歯車は、強度と精度に優れています。ロールフォーミングは、用途に応じてホットとコールドの両方で実行されます。
この方法で製造された歯車は、仕上げ作業を必要としません。この方法でも多くの材料を節約できますが、この歯車の製造方法に使用される機械は非常に高価です。
この方法の注目すべき利点は、圧延プロセス中にホイールと歯に発生する塑性ひずみにより、引張と圧縮の両方で歯車が強くなることです。
2.2押し出しとコールドドローイング:
押し出しは、正確な寸法の小さな歯車を作るための最良の方法です。
この製造方法では、図1に示すように、ロッドを成形ダイを通して冷間引抜して、ロッドの長さに沿ってロッドの表面全体に歯車を作成します。 1.1。次に、バーの刻まれた長さから短い長さが切り取られます。
それぞれの小さな長さは、必要なギアの厚さに等しくなります。作業を完了するために必要なのは、仕上げ研削のみです。以前は、アルミニウム、真ちゅう、青銅、およびマグネシウム合金が押し出されていました。
しかし今では直径60mmまでの棒鋼。製造業で押し出されています。この方法で製造された歯車は、時計、時計、プリンター、タイプライターなどで最も一般的に使用されています。
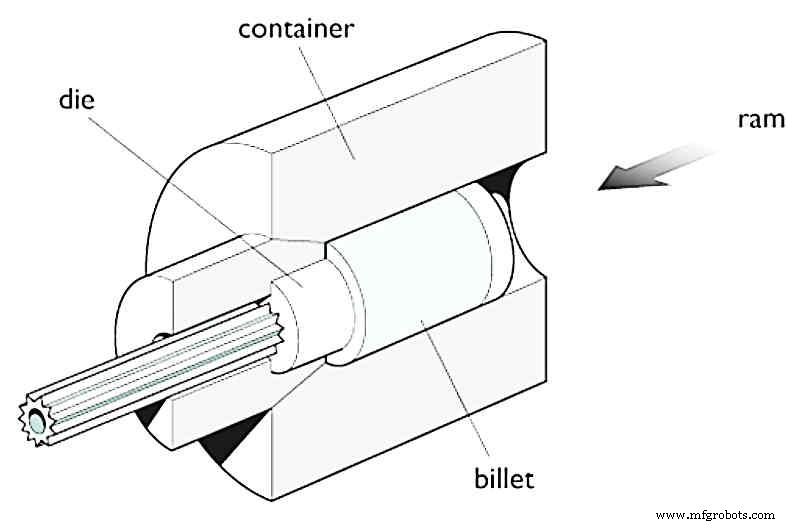
3。金属の除去:
名前自体が示すように、この方法では、ブランクホイールを機械加工してワークピースから金属を除去し、その周囲に沿って歯車の歯を生成します。
この歯車の切断方法では、主な方法は次のとおりです。
- プロファイリングまたはフォームカッター法。
- 生成方法。
3.1プロファイリングまたはフォームカッター法による歯車の切断:
この方法では、カッターを使用してブランクホイールから金属を除去します。多くの場合、カッターの厚さは同じで、歯車の各歯の間にスペースがあります。操作には、平削り盤と形削り盤に一点切削工具を使用します。
一方、フライス盤では、丸い多歯工具を使用してワークピースの歯車のプロファイルを作成します。この方法では、製造するギアプロファイルごとに特別なカッターが必要であり、大量生産には適していません。
この方法で歯車を切断するさまざまな方法は次のとおりです。
- 成形ディスクカッターまたはエンドミルカッターを備えたフライス盤での歯車切削。
- シングルポイントフォームツールを使用したシェーパーまたはプレーナーマシンでの歯車の切断。
- ブローチ盤でのギアカット。
- せん断速度プロセスによるフォームツールブレードを使用した歯車の切断。
3.1.1成形ディスクカッターを使用したフライス盤での歯車の切断:
平歯車はユニバーサルフライス盤で簡単に製造できます。この歯車切断の原理では、中実のブランクホイールが分割ヘッドに接続されたマンドレルに取り付けられます。カッターはアーバーに取り付けられています。
図1.2に示すように、カッターの軸は常にギアブランクの軸に垂直です。次に、ブランクホイールの垂直軸がカッターの水平軸と適切に一致します。
次に、カッターのノーズがギアブランクホイールの周囲にちょうど触れるまで、テーブルを垂直移動クランクを使用して上方に移動します。インデックスの動きは事前に計算され、それに応じて決定されます。
次に、必要な高さ、つまり歯の深さに等しい高さで膝を上げ、垂直方向のゼロを設定します。同時に、カッターに電力が供給されます。
1回のパスで、1つの歯が完成し、テーブルが元の位置に戻ります。歯車を2回以上のパスで切断する場合は、この垂直方向の動きが少なくなる可能性があります。次に、ギアブランクは次の歯のためにインデックスが付けられます。
ギアブランクホイールの周囲に必要な数の歯がカットされるまで、同じ操作サイクルが繰り返されます。
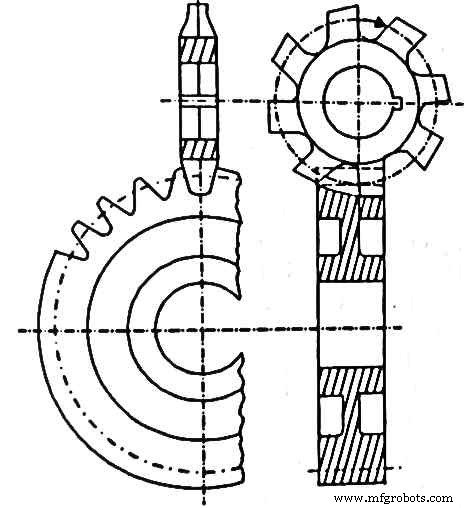
ユニバーサルフライス盤ではすば歯車やウォームを作成する場合は、スパイラルフライス盤 使用されている。
ねじれ角は、カッターとギアブランクホイールを互いに傾斜させるためのアタッチメントを使用して得られます。はすば歯車の切削では、2つのカッターのセットが使用されます。
1つは荒削り用、もう1つは仕上げ用です。これらの歯車も、上記と同じ一連の操作で切断されます。
大ピッチのピニオンを製造するために、ディスクタイプのカッターの代わりにエンドミルカッターが使用されます。 エンドミルカッター チャックを介してフライス盤のスピンドルに取り付けられています。

フライス盤で歯車を製造することは、最も簡単で経済的な方法の1つです。平歯車、斜角、はすばタイプの歯車、およびラックも歯車フライス盤方式で作成できます。
インデックスの動きが正確ではないため、製造された歯車の品質は正確であるとは見なされません。
3.1.2シングルポイントフォームツールを使用したシェーパーまたはプレーナーマシンでの歯車の切断。
歯車は、シェーパー、プレーナー、またはスロッティングマシンで製造することもできます。この製造方法では、図1.3に示すように、シングルポイントフォームツールを使用してブランクホイールの歯をスクライブします。
これらのすべての機械では、ギアブランクは心押し台と発端者の間にあるマンドレルに取り付けられています。フライス盤の分割ヘッドは、これらの機械のテーブルに直接ボルトで固定できます。小規模生産では、ギアブランクは図1に示すようにチャックに直接取り付けられます。 1.4。
ツールはツールヘッドにしっかりと取り付けられています。これらの各マシンでは、工具をワークピースに対して往復運動させるか、ギアブランクホイールを一点切削工具を通過させて往復運動させることにより、歯車の切削を実現します。
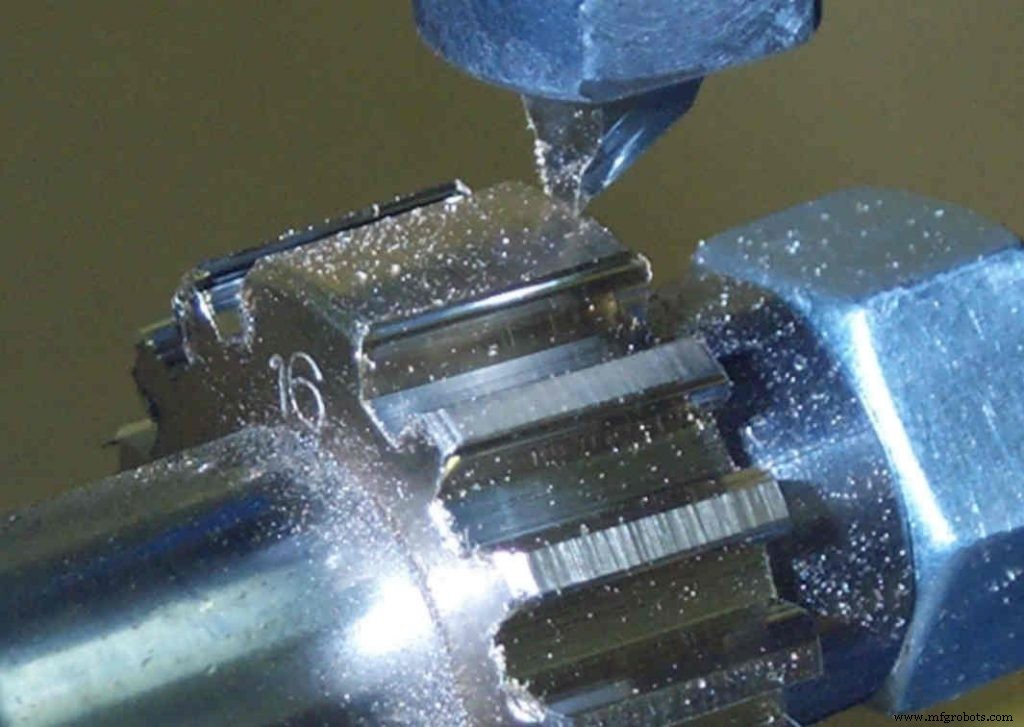
シェーパーマシンとスロッターマシンの両方の場合、ギアブランクホイールはチャックとフィクスチャでそれぞれ静止したままですが、シングルポイント切削工具はワークピースを通過して往復します。図に示すように、どちらの場合も工具は機械のラムに取り付けられています。 1.4。
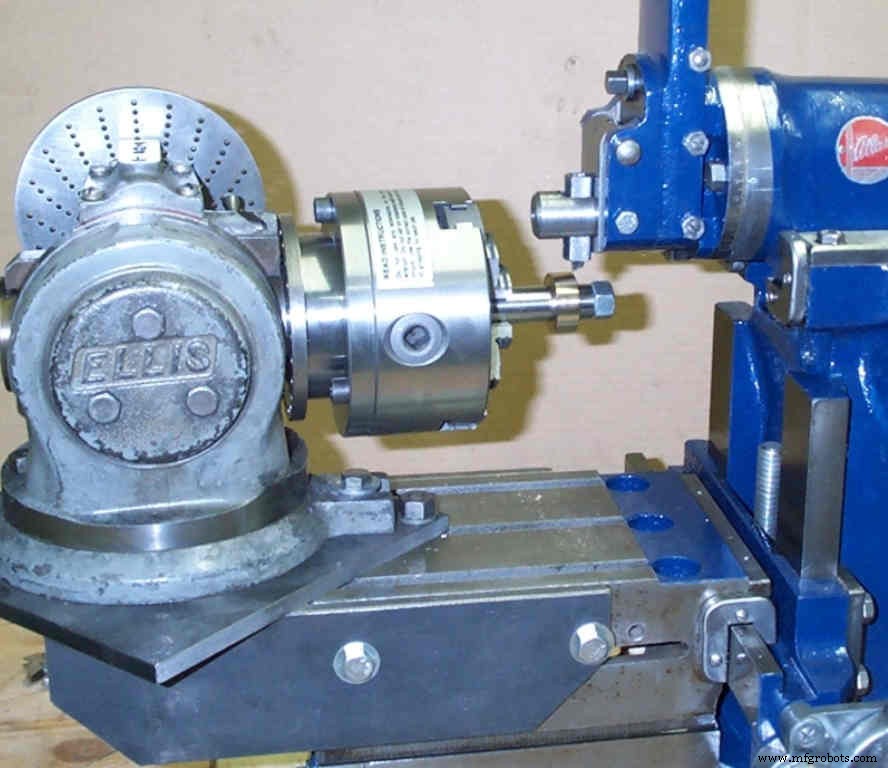
平削り盤の場合、ブランクホイールを保持しているテーブルが工具を通過して往復する間、一点切削工具は静止したままです。歯の深さは、垂直軸に沿ったツールヘッドの動きによって調整されます。各歯をカットした後、インデックスを付けてホイールを一方向に回転させます。
このように、工具またはブランクホイールを往復運動させる操作を繰り返すことにより、新しい歯が切断されます。このシーケンスは、必要な数の歯がブランクホイールの周囲に沿って製造されるまで繰り返されます。
この歯車切断方法は費用効果が高く経済的ですが、主な欠点は、切断動作が遅いため、大量生産には適していないことです。したがって、この方法は歯車の製造には広く使用されていません。
シェーパーマシンとプレーナーマシンとスロッターマシンのギアカットの比較:
シェーパーマシン | プレーナーマシン | スロットマシン |
ギアブランクホイールは静止したままです | ツールは静止したままです | ギアブランクホイールは静止したままです |
ツールは空白のホイールを通過して往復します | ブランクホイールはツールを通過して往復します | ツールはブランクホイールを通過して往復します |
ブランクホイールはチャックに取り付けられています | ブランクホイールは作業台に固定されています | ブランクホイールは固定具に固定されています |
切り込みの深さが浅い | より深い切り込み | 切り込みの深さが浅い |
3.1.3成形カッターを使用したブローチ盤の歯車切削:
ブローチ加工は、ブローチ盤で行われる機械加工です。ブローチ加工に使用される工具は「ブローチ」と呼ばれます。これは非常に迅速なプロセスです。ここでは、図に示すように、歯車の厚さのブローチがワークピースの内面または外面を越えて押したり引いたりします。 1.5。
このプロセスには、内部か外部かに関係なく、シングルパスで歯車を製造する機能があります。この方法は経済的で迅速で、優れた表面仕上げが施されています。
この方法の唯一の制限は、高価な工具のために小規模な生産には採用できないことです。
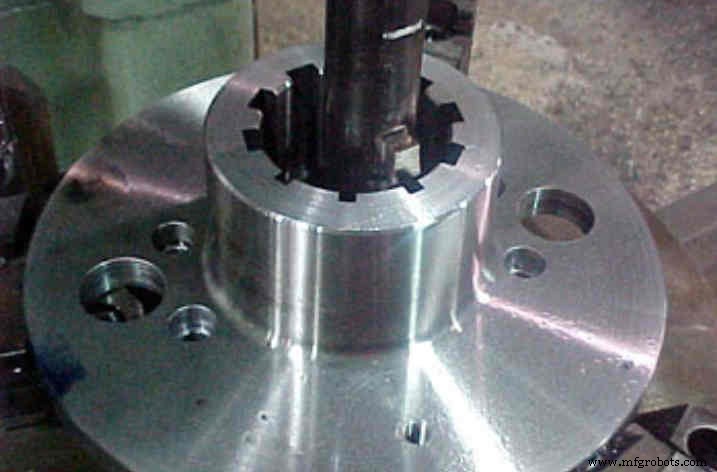
3.1.4せん断速度プロセスによるフォームツールブレードを使用した歯車の切断:
メソッドのタイトル自体が示すように、これは迅速なプロセスです。 1回のパスまたは2〜3回のパスですべての歯を切断すると、この方法は非常に高速になります。
この方法はブローチ加工に似ていますが、ここでは、一点切削工具の代わりに、ブランクの周囲に必要な切削歯数に応じて、多数の切削工具を放射状に配置します。
このプロセスでは、内面と外面の両方に歯車が生成されます。外歯車を切削する場合、ラジアルツールは中空ヘッドの周りに取り付けられます。ストロークごとに、工具は段階的な切り込み深さで送り込まれます。
ツールのすべてのリタードストロークに沿ってクリアランスが提供されます。この方法は、内外の平歯車、スプライン、クラッチ歯、特殊歯車を大量に切削する場合に採用できます。
ブローチ加工とせん断速度法による歯車切削の比較:
ブローチ方法 | せん断速度法 |
1つのシングルポイントツールのみが使用されます | 同じ寸法の複数のツールが使用されています |
ブローチ盤が使用されています | ラジアルフォームツールを使用 |
1回のパスで1本の歯がカットされます | すべての歯が1回のパスでカットされます |
クイックプロセス | より迅速なプロセス |
比較的低コスト | 比較的高コストの工具 |
3.2ギアの生成:
この自動化された時代では、「歯車生成プロセス」によって最も多くの歯車が製造されています。基本的で重要な歯車生成プロセスは次のとおりです。
- シェーパープロセスによる歯車の切断。
- ラック計画プロセスによる歯車の切断。
- ギアホブ切りプロセス。
3.2.1。シェーパープロセスによる歯車の切断:
ギアシェイパーの操作は、2つの異なる方法で実行できます。 1つは「ロータリーギアシェイパーカッター」方式で、もう1つは「ラックタイプシェイパーカッター」方式です。歯車の切削の基本原理は、どちらのプロセスでも同じです。
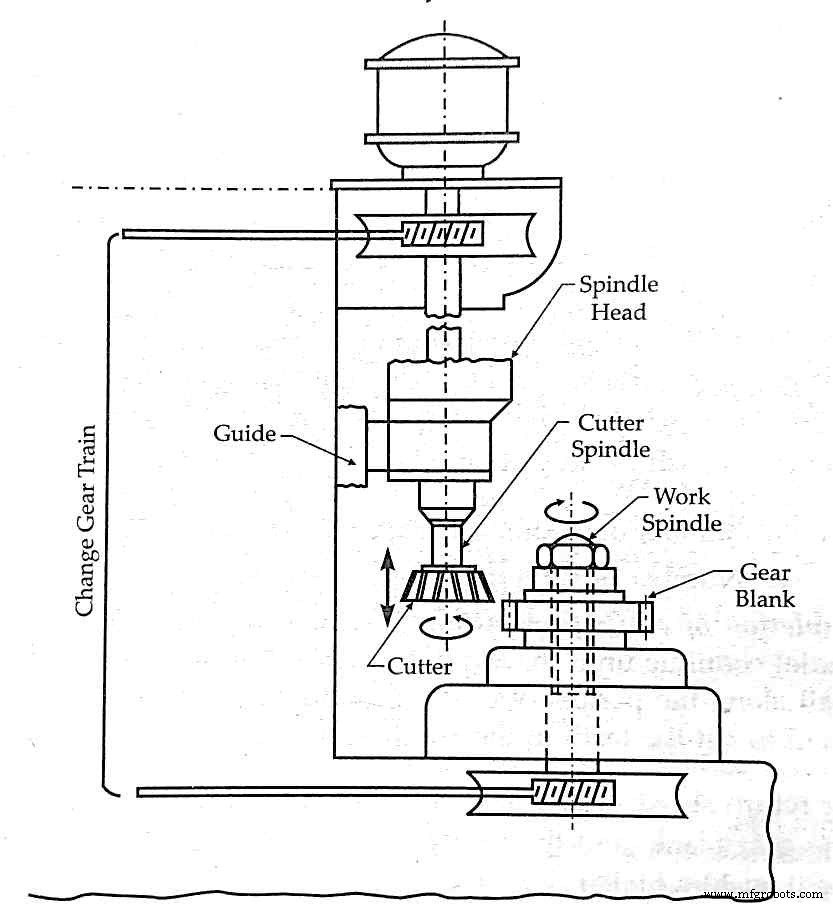
このプロセスでは、カッターがスタブアーバーに取り付けられている間に、ギアブランクがスピンドルシャフトにボルトで固定されます。この機械のアーバーには2つの運動軸があります。 1つは垂直または往復運動で、もう1つは回転運動です。
ここでは、ピニオン型のカッターを使用して、ブランクホイールから金属をスクライブします。カッターは、歯面と側面に隙間があるように設計されています。
歯を切るために、カッターはブランクホイールと接触する垂直軸に沿って往復運動し、ブランクホイールから金属が除去されます。金属が切断されるカッターの下向きの線形運動は、切断運動と呼ばれます。 後者を引き抜くためのカッターの上方への直線運動は、戻りストロークと呼ばれます。 。
戻りストロークで金属が除去されることはありません。すべてのカットとともに、カッターとブランクホイールに相対回転速度が与えられます。それらの間のゆっくりとした相対回転は、インデックスフィードと呼ばれます。 。
アーバーのシャフトとスピンドルシャフトの間に接続された歯車列は、図1.6に示すように、カッターとブランクホイールを互いに反対方向にゆっくりと回転させて、インデックス動作を実現します。
必要な数の歯がブランクホイールでカットされるまで、カッターのインデックス作成と往復動作が継続されます。
ロータリーギアシェイパーカッターの場合 、ブランクホイールの周囲に沿って歯車を装飾するために使用されるカッターは、図1.7に示すように回転ピニオンです。
カッターの歯は、ブランクホイールでカットされるのと同じ数です。この方法は、出力が高く、ウォームとウォームホイールを除くすべてのタイプの歯車を切断できるため、歯車の生成に広く使用されています。
ロータリーギアシェイパーの切断は、同じ動作原理で内歯車の切断にも適合させることができます。ロータリーギアシェイパーマシンは、垂直スピンドルタイプと水平スピンドルタイプの両方で広く利用できます。
通常、水平回転ギアシェイパーカッターマシンには2つの強力なアーバーがあります。それぞれが互いに向かって往復します。
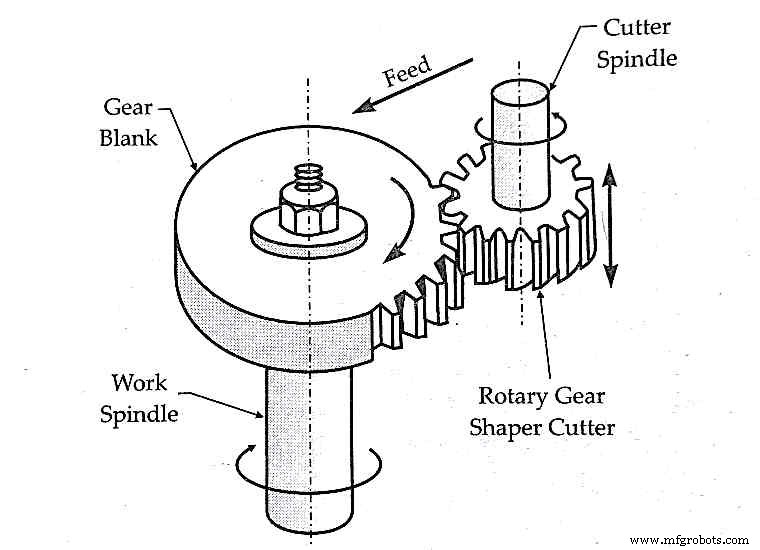
ラックタイプのギアシェイパーカッター 方法では、ラックタイプのカッターを使用してブランクホイールから金属を取り除き、歯を作ります。動作原理はギアシェイパーカッターの基本原理と同じです。
これは、図1に例示されているように、ラックタイプのカッターが垂直軸に沿って往復運動する間にギアブランクホイールを回転させることを含みます。 1.8。
このラックタイプの歯車生成方法の最大の制限は、ラックの全長、つまりカッターのすべての歯を使用して位置をカッターの最初の歯にリセットするたびに、加工を一時停止する必要があることです。最大の利点はそれですが、任意の数の歯の任意の歯車を作成できます。
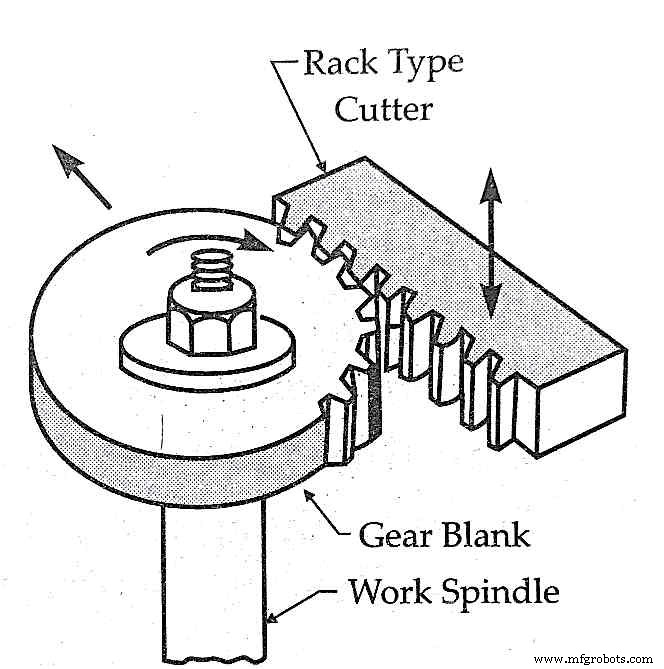
3.2.2ラックプレーニングプロセスによる歯車の切断:
このプロセスは、主にインボリュート歯の歯車を作成するために使用されます。平歯車とはすば歯車は、この方法で製造できる歯車の種類です。
このプロセスによる歯車は、2つの異なるマシンで作成できます。サンダーランドとマーグ。構造は異なりますが、両方のマシンは同じ切断原理で動作します。
ラック計画プロセスでは、ブランクホイールは水平軸のスピンドルにボルトで固定され、ラックタイプのカッターはアーバーにボルトで固定されます。ブランクホイールのインボリュート歯をカットするために、カッターが前後方向に往復運動している間、ブランクホイールは静止状態に保たれます。
図1.9に示すように、カッターは2つの完全な歯と2つの部分的な歯をスクライブします。および1.10。
前後のストロークごとに少量の金属が除去されます。このタイプの不適切な歯のスクライビングは、インボリュートプロファイルの歯を生成します。その後、ギアブランクがラックタイプのカッターに向かって徐々に送られ、この動きによってカッターの歯がブランクホイールの周囲を貫通します。
それらがブランクに侵入すると、低速の回転送りまたはインデックス送りがブランクホイールに与えられ、これにより歯が生成されます。インボリュートプロファイル歯の生成原理は図1のようになります。 1.9。
ブランクホイールの周囲に必要な数の歯ができるまで、同じ一連の操作が繰り返されます。

3.2.3サンダーランドプロセスでのギアカット:
このプロセスは、その発明者である「サンダーランド」にちなんで名付けられました。このプロセスは、上記と同じ原則であるラック計画プロセスで機能します。また、ここでは、この過程で、カッターもギアブランクに沿って移動し、突然後退し、1ピッチ距離まで等量後退します。
この動きは、必要な歯の深さが達成された後に発生します。カッターの動きとブランクの回転を同期させるために歯車列の配置が行われます。
カッターが元の位置に戻ると、同じ往復動作が繰り返され、続いてブランクのインデックスが作成され、工具が突然引き抜かれます。
サンダーランドプロセスの動作の概略原理を図1.10に示します。および1.11。
この歯車生成方法では、オペレーターは材料に応じてカッターの往復速度を自由に調整できます。
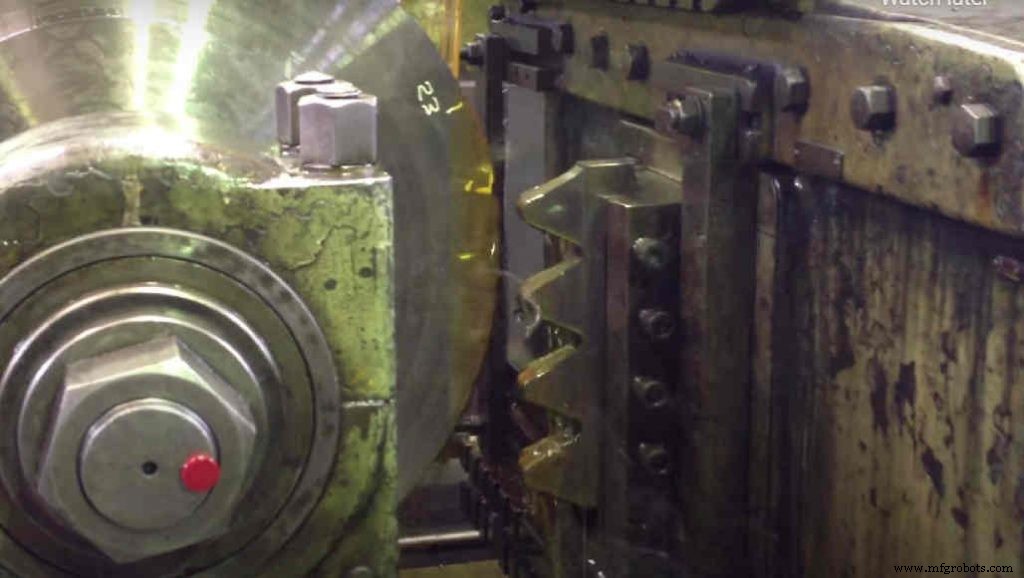
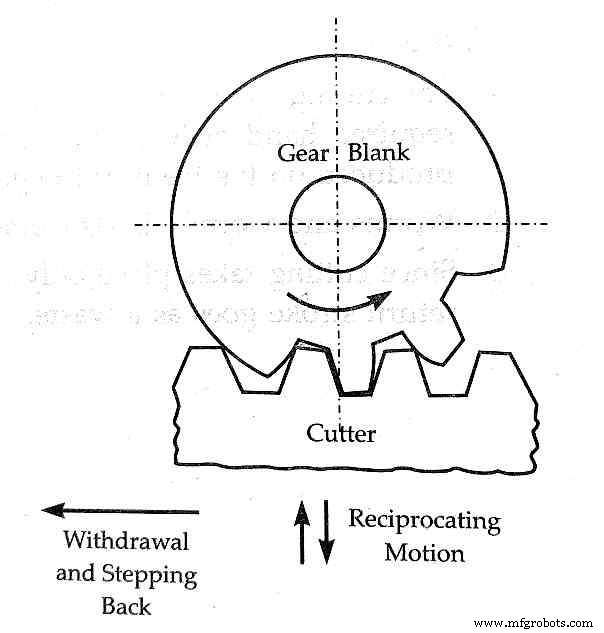
3.2.4 Maagプロセスでの歯車の切断:
この工程では、ブランクホイールを軸を垂直にしてワークテーブルに取り付け、ラックタイプのカッターをスライドに取り付けます。スライドは、その軸に沿って自由に往復運動を行うことができます。
Maagプロセスは、ラックプレーンの原理でも機能します。さらに、カッターは垂直面で任意の傾斜に設定できるため、カッターは任意の方向に歯車を切断できます。工業写真を図1.12に示します。
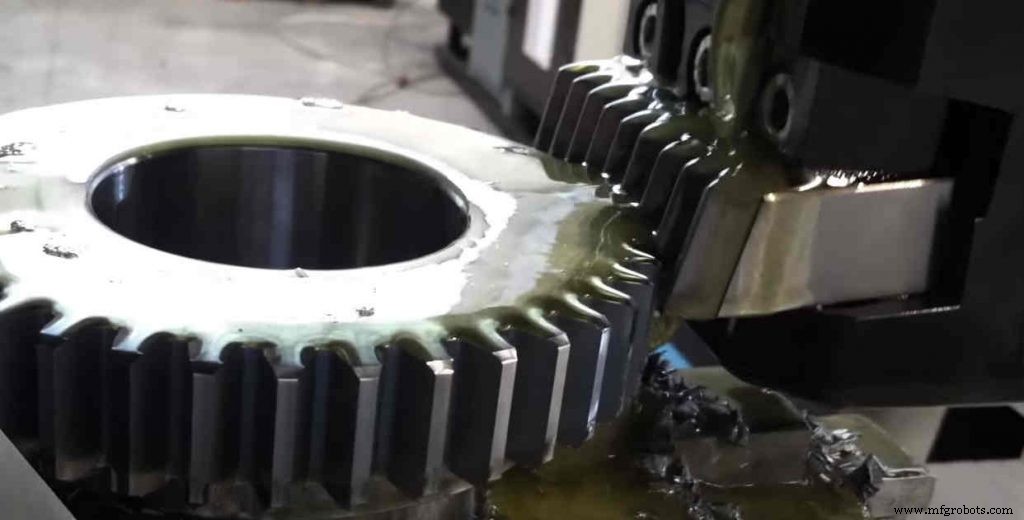
3.3.1ホブ盤でのギアホブ盤プロセスまたはギアカット:
このプロセスでは、ギアブランクホイールがホブと呼ばれるローリングカッターに対して回転します。 。ホブは、ワームのように見えますが、いくつかのまっすぐなフルートが全体にカットされているツールです。
ホブはアーバーに取り付けられ、ブランクホイールはスピンドルに取り付けられています。スピンドルには、図1.13に示すように、垂直方向に移動したり、中心軸を中心に回転したりする自由があります。
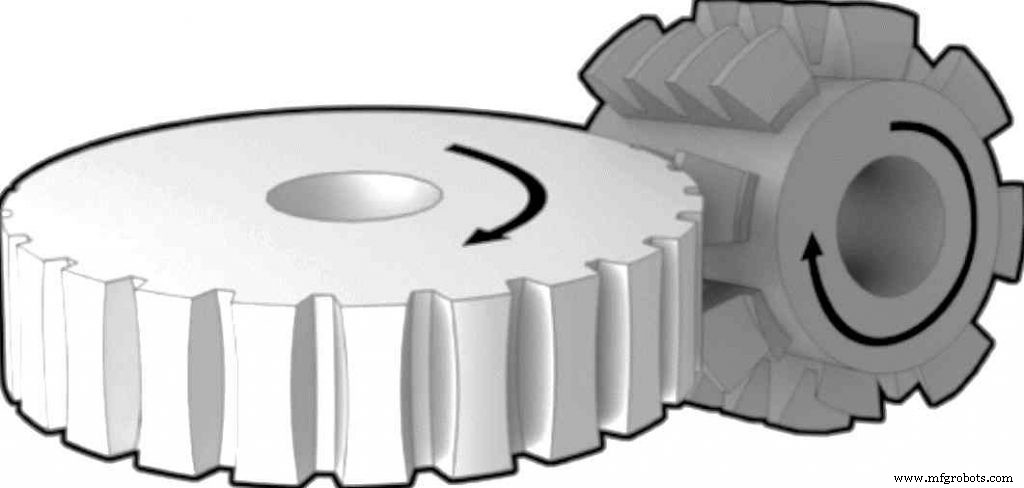
このプロセスは主に、すべてのタイプのインボリュート歯車を製造するために使用されます。この操作では、ホブに適切な回転速度が与えられます。同時に、歯車列の配置により、ブランクもその軸を中心に回転するように作られています。
ホブの切削歯は、ブランクから金属をスクライブします。ブランクが完全に回転するたびに、均一な深さの歯がカットされます。ブランクの回転が終了すると、歯の深さが増し、ホブ切りが繰り返されます。
この一連の操作は、希望の切込み深さが達成されるまで繰り返されます。ブランクも上下に動かされ、ホイールの厚さとともに均一な深さのカットを生成します。
歯車ホブ盤の工業写真を図1に示します。 1.14。
このプロセスでは、すべてのホイールを互いに取り付けることにより、複数のブランクホイールに同時に歯車を製造できます。
ホブ切りは、すべてのホイールでギアが生成されるまで、ブランクホイールのセットで継続的に操作されます。はすば歯車を切断するには、ブランクホイールのスピンドルシャフトを適切な角度に傾けます。
歯車ホブ盤法は、あらゆるタイプの歯車を短時間で大量に製造できるため、世界中で広く使用されています。ギアホブ盤の唯一の制限は、内歯車を製造できないことです。
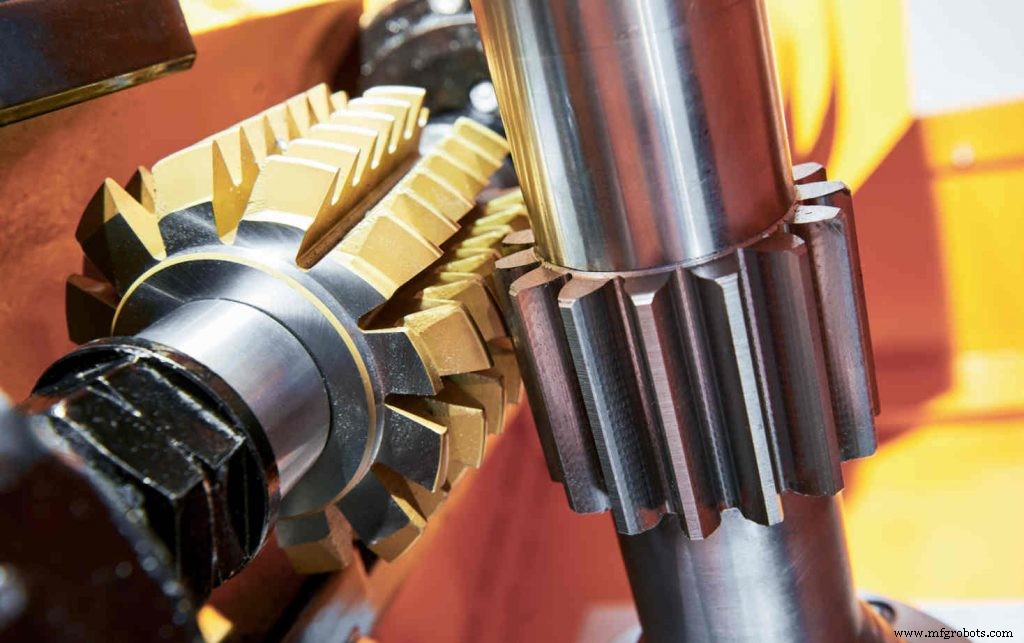
ギアホブ切りプロセスが広く使用されているのはなぜですか?
- この方法は、他の生成プロセスと比較して経済的です。
- これはより高速で継続的なプロセスです。
- あらゆる種類の歯車を製造できます。
- 正確な寸法が達成されます。
- 複数のブランクをすべて互いに取り付けることにより、同時に加工することができます。
- 同じホブを使用して、任意の数の歯をカットできます。
鋳造、成形、切断、生成のすべてのプロセスで製造された歯車は、機械に適合する前に、シェービング、バニシング、研削、仕上げに送られます。
産業技術