板金溶接:溶接の一般的な方法とヒント
金属片を希望の大きさに切断した後、希望の形状や仕様に合わせて接合する必要があります。したがって、板金溶接は金属加工の重要な側面です。
さまざまな板金溶接技術がありますが、産業用途に最適なものを知っていますか?
この記事では、板金の溶接に使用されるさまざまな方法の詳細を、その利点と用途を含めて説明します。また、最良の結果を得るために薄い金属シートを溶接するときに注意する重要なヒントも提供します。
6つの方法 板金溶接
それでは、金属板を溶かすためのいくつかの方法を包括的に見てみましょう。
1。 MIG溶接
ガスメタルアーク溶接としても知られるメタルイナートガス溶接(MIG)。これには、溶接ガンを使用して連続した単線電極を溶接パドルに供給することが含まれます。プール内の溶けたワイヤーは、金属片の接合を引き起こします。溶接ガンのシールドガスは、溶接パドルの大気汚染を防ぎます。
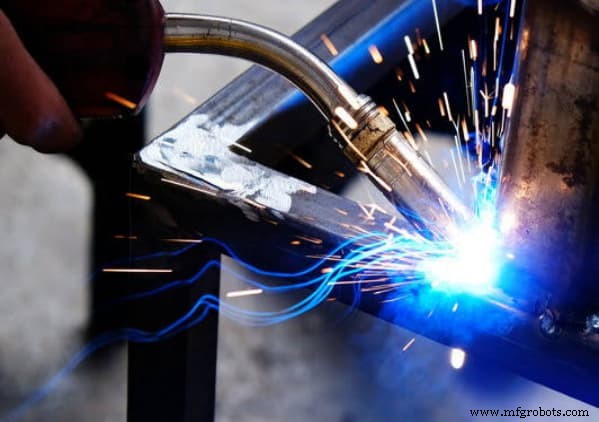
MIG溶接は最高品質の溶接を作成し、アルミニウム、鋼、ステンレス鋼などのほとんどの板金に適しています。
この溶接方法は、自動車および住宅改修業界で頼りになる技術です。また、高度な機械を必要としないため、費用対効果の高い手法です。
TIG溶接
タングステンイナートガス(TIG)は、DCまたはAC下で非消耗性のタングステン電極を使用して溶接を行うアーク溶接です。 MIG溶接と同様に、不活性シールドガス(アルゴンまたはヘリウム)を使用して、大気汚染物質や電極および水たまりの酸化を防ぎます。
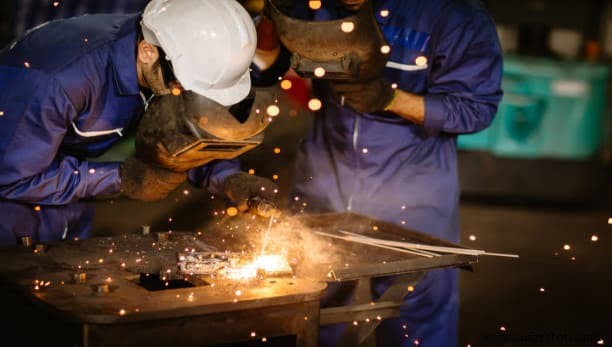
TIG溶接は、アルミニウム、チタン、銅、ニッケル、マグネシウム、クロムなどの非鉄金属の溶接に適しています。これは、航空および航空宇宙産業にとって貴重な技術です。また、オートバイ、ドア、フィーダーのフレームの製造にも最適です。
この溶接方法は、溶接工に優れた制御を提供し、きちんとした強力な溶接を実現します。ただし、時間がかかる場合があり、溶接工側の専門知識が必要です。
[参考資料:ミグ溶接とティグ溶接のどちらかを選択するためのガイド]
スティック溶接
スティック溶接は、被覆アーク溶接と呼ばれます。これは、フラックスで覆われたスティックを電極として使用する手動アーク溶接プロセスです。溶接電源からの電流は、金属を接合する部品と電極の間にアークを形成します。鉄や鋼などの強靭な金属に適しています。
このプロセスでは、シールドガスを使用しません。熱が発生すると、電極を覆っているフラックスが崩壊し、溶接プールを汚染から保護するスラグが形成されます。
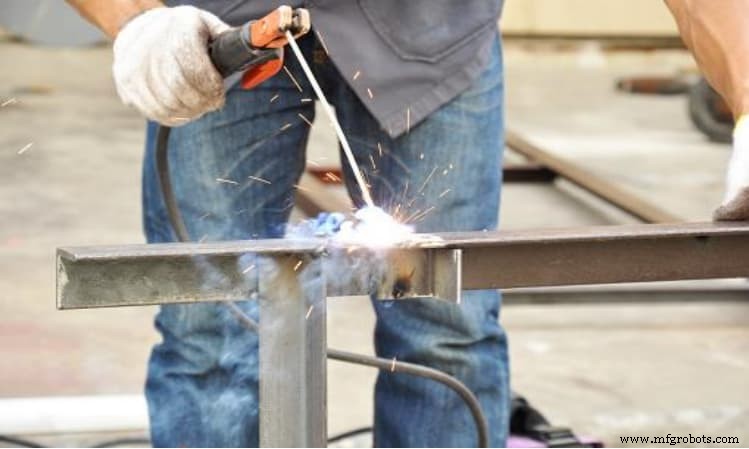
この溶接技術は、その装置がコンパクトで持ち運びが簡単で、持ち運びが簡単なため、おそらく最も便利です。これは、建設、造船、および製鉄業で一般的な技術です。
プラズマアーク溶接
プラズマアーク溶接は、タングステン電極を使用するという点でTIG溶接に似ています。ただし、小さなアークを使用し、溶接トーチ本体に電極を配置できます。加圧されたガスは高温プラズマを形成し、金属を一緒に溶かして固体溶接を作成します。
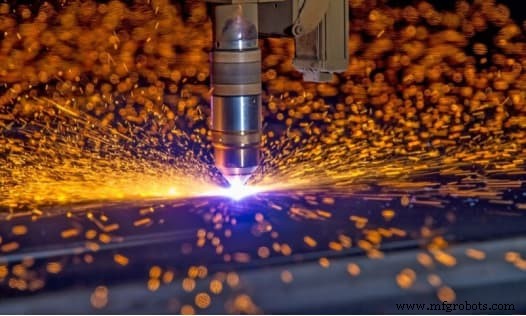
この溶接技術は、低電力を必要とし、高速で機能します。さらに、それは正確な溶接を生成し、航空および海洋産業で広く受け入れられています。
TIG溶接と同様に、プラズマアーク溶接はフィラー材料を必要としません。また、仕上げの必要性が少ない高品質の溶接を生成します。
電子ビームとレーザー溶接
名前が示すように、レーザーと電子ビーム溶接は、金属片を融合して接合するための熱源としてレーザーと電子ビームを使用します。他のほとんどの方法とは異なり、この溶接技術には高度な機械または自動ロボットが必要です。
高精度の溶接技術であり、細部までこだわった作業に適しています。レーザービームは、非常に正確な溶接のために最も小さな物質に焦点を合わせることができます。
さらに、炭素鋼、チタン、ステンレス鋼、アルミニウムなどの強靭な金属の溶接にも適しています。この技術は熱可塑性プラスチックにも適しています。この方法により、美的魅力の高い製品が得られ、ポストプロダクションのニーズが軽減されます。
ガス溶接
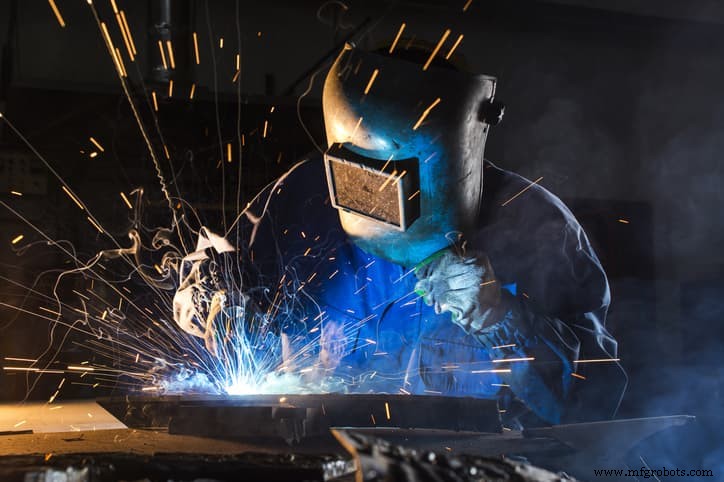
ガス溶接は、熱による溶接の伝統的な形式の1つです。これには、燃料(ガソリン)、酸素、またはオキシアセチレンの燃焼によって発生する熱を使用して、金属片を結合することが含まれます。これらの燃料の燃焼により、接合中に金属表面を溶かす非常に高温の炎が発生しました。
この技術は、業界で最も使用されている溶接方法の1つです。幅広い用途があり、鉄および非鉄金属の両方に適しています。また、パイプやチューブの溶接、換気システムや空調システムの修理などにも効果的かつ効率的です。
他の多くの溶接技術とは異なり、電気を必要としません。また、持ち運びができ、経済性が高く、専門家のサービスを必要としません。
溶接またはリベット留めの技術を使用して板金部品を結合するかどうかわかりませんか?その場合は、溶接とリベットのどちらを選択するかについてのガイドがあります。
選択するときは表面を考慮してください 板金溶接 メソッド
以下は、金属板を溶接するときに遭遇する可能性のある表面と、それらを使用するための最良の方法です。
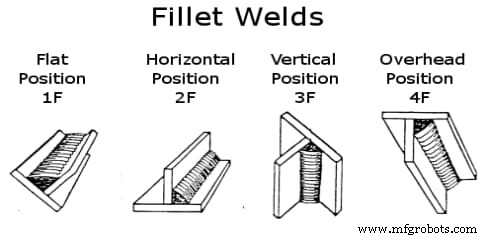
平らな面
平らな面の溶接は、フラット溶接と呼ばれます。溶接機はジョイントの上側からこの表面に近づき、重力が溶融流を補助できるようにします。
平らな面で良好な溶接を行うには、溶接工は先端の角度を金属面に対して45度に配置し、炎を接合点に向けて慎重に向ける必要があります。
MIGおよびTIG溶接法は、平坦な表面に最適です。ワイヤーフィードとガスフローは、フラットなセットアップで優れたパフォーマンスを発揮します。
水平面
水平構成では、金属シートは溶接機に対して水平に見えます。ただし、2つの形式で存在する可能性があります。
- フィレット溶接:溶接は、水平面の上端で垂直面に対して行われます。接合領域は、「L」字型に互いに垂直な2つの金属片の接合部のように見えます。
- 開先溶接:溶接面は垂直面にあります。結合される両方の金属片は同じ平面上にあります。
スティック溶接は、TIG溶接とMIG溶接の完璧なバランスをとることが難しい水平面での作業に最適です。
垂直面
溶接シャフトの垂直位置は、基本的に直立した表面に面した溶接機です。溶湯は溶接時に下向きに流れて堆積する傾向があります。したがって、溶接工は金属の流れを制御する必要があります。これには、溶接ガンをプレートに対して45度の角度で向け、電極を炎と溶接プールの間に保持することが含まれます。
垂直面の最良の方法はスティック溶接です。多くの場合、溶接工は、利便性を高めるために、溶接軸を平らまたは水平に見えるように調整しようとします。
オーバーヘッドサーフェス
頭上の表面での材料の溶接は最も困難です。名前が示すように、それはあなたの頭の上に置かれたワークピースを溶接することを含みます。溶接しようとすると、溶融金属が脱落する傾向があります。
オーバーヘッド溶接の難しさを緩和するために、溶接パドルを最小限に抑えます。また、良好な溶接を行うために十分なフィラー材料を使用するようにしてください。
この構成には、スティック溶接が最も適切な方法です。カスタム板金製造施設では、オーバーヘッド表面の溶接は比較的まれです。
8板金を溶接するためのヒント
金属板を結婚式にするときの目的は、溶接部品が用途に十分な機械的特性を維持することを保証することです。以下は、溶接を実行するときに覚えておくべきヒントです。
1。 フィラーメタルを選択
製造の機械的特徴に適合する適切な溶加材を使用することが不可欠です。フィラーは板金よりも薄くする必要があります。たとえば、1 mmの薄い金属を溶接する場合は、0.6mmのフィラーが最適です。
ワイヤーが細いほど、溶かすのに必要な熱は少なくなります。したがって、過度の熱の蓄積のリスクが少なくなり、溶接から最良の結果が得られる可能性が高くなります。
また、溶加材を正しく選択することで、錆び、ひび割れ、その他の考えられる欠陥のリスクを減らすことができます。
2。 スキップ溶接技術を使用する
スキップ溶接技術では、重要なポイントで一連のステッチまたは短い溶接を使用して、薄い板金を所定の位置に保持します。数分間冷却した後、溶接工は以前にスキップした場所を溶接し続けることができます。
スキップ溶接は、不均一な熱分布によって引き起こされることが多い金属の歪みや反りを回避するのに役立ちます。
また、溶接するときは、溶接トーチを織らないでください。これも過度の熱を引き起こす可能性があります。代わりに、トーチをまっすぐな道に沿ってすばやく動かしてください。
3。 タック溶接技術を使用する
タック溶接は、過度の熱の蓄積と溶け落ちのリスクを減らすためのもう1つの優れた技術です。
タックは、最終溶接まで金属部品を一緒に保持するために使用されるマイナーな一時的な溶接です。穴が焼けるのを防ぐために、金属片を1mmの間隔を空けて密接に突き合わせてください。次に、ジョイントが完全に覆われるまで小さな仮付け溶接を作成します。
4。 細い線径を使用
MIG溶接のように、単線電極で溶接する場合は、可能な限り最小の直径のワイヤを使用してください。ワイヤーが小さいと、溶接機の制御が向上し、堆積物が少なくなるため、ミスを修正できる可能性が高くなります。
また、ワイヤーが小さいほど、溶解に必要な熱が少なくなります。したがって、過度の熱の問題は少なくなります。
一般に、ライトゲージの板金を使用する場合は、0.023インチまたは0.024インチをお勧めします。ただし、18ガレージ以上の金属を溶接する場合は、0.030インチのワイヤーが理想的です。
5。 小さな電極を使用する
金属よりも太くないロッドを使用してください。 ⅛インチよりも小さい電極を使用してください。より小さな電極は、より低い熱と電流で優れた性能を発揮し、それによって溶け落ちを減らし、電極を小さな領域に粉砕してタイトなアークを実行することができます。
6。 バッキングバーを固定する
バッキングバーをワークメタルにクランプすると、単に冷却するのを待つよりも迅速に熱を放散できます。バッキングバーは金属から熱を奪うため、反りや焼け落ちのリスクが軽減されます。
金属棒は、熱伝導率が高いために熱を最もよく放散するため、通常は銅またはアルミニウムの材料でできています。適切な熱伝達のために、バッキングバーがワークピースにしっかりと固定されていることを確認してください。
7。 高アルゴンベースのシールドガスを使用
溶接の際は、アルゴンの割合が高いシールドガスを使用してください。その一例は、それぞれ75対25の比率のアルゴンと二酸化炭素の典型的な組み合わせです。
アルゴンは発熱が少ないため、アルゴン含有量の高いシールドガスが好ましい。アルミニウム金属のTIGまたはMIG溶接を行う場合、シールドガスとして純アルゴンを使用する必要がある場合があります。
8。 フィットアップとジョイントデザイン
薄い板金の溶接には注意が必要な場合があります。エラーの余地がほとんどないため、しっかりとしっかりと調整する必要があります。穴が熱を吸収する可能性があるため、溶け落ちを防ぐために、2つの接合金属間のスペースを最小限に抑えてください。
経験則として、溶接工は2回測定し、1回切断する必要があります。場合によっては、耐熱性を高めるためにジョイントを再設計する必要があります。
バットジョイント
突合せ継手とは、溶接のために並べて配置された2つの金属片を指します。
接合面は、溶接中に溶ける領域です。溶接強度を上げるには、表面のエッジ準備を行うことが重要です。溶接工は、強力な溶接を行うために、側面の1つを曲げて、それらを互いにうまく適合させる必要がある場合があります。
突合せ溶接は、準備が比較的簡単で、他の溶接継手よりも応力に耐えることができます。そのため、構造物の製造で最も一般的な溶接継手です。ただし、他のタイプの溶接継手があります。
ラップジョイント
重ね継手は、突合せ継手の典型的な変更です。これらは、さまざまな厚さの板金を溶接するための頼りになるジョイントです。
重ね継手では、2つの金属片が重なり合って結合します–一方が他方の上に配置されます。重ね継手の主な欠点は、2つの金属の接合部が錆びやすいことです。
T-ジョイント
名前が示すように、Tジョイントは、2つの金属片が垂直に交差し、「T」字型に直角を形成する場所で発生します。それらはすみ肉溶接の形式と見なされます。
このジョイントを使用するときは、溶接ルーフに十分に浸透していることを確認してください。また、接続ポイントで頻繁に発生するジョイントの制限を減らすために、ストッパーを追加する必要がある場合もあります。 Tジョイントは、配管およびチューブシステムを備えた構造で一般的です。
コーナージョイント
コーナージョイントは、両方とも垂直な角度を形成するという点で、Tジョイントにいくぶん似ています。ただし、接合金属の向きは異なります。コーナージョイントでは、金属がコーナーで合流し、「L」字型の形で単一の直角を作成します。コーナージョイントは、標準的な部品製造、特にフレームとボックスです。
エッジジョイント
エッジジョイントでは、板金を並べて配置し、同じエッジに溶接します。これは、フランジエッジのあるワークピースで発生します。溶接工は、どちらかの金属片の端を適切な角度で曲げて、それらがもう一方の金属片にうまくフィットしてしっかりと溶接できるようにする必要がある場合があります。
RapidDirect:カスタム 板金溶接 パートナー
カスタム板金製造のために一流の溶接作業が必要ですか? ?または、製造ニーズに合わせて板金を溶接する方法がわかりませんか? RapidDirectはまさにあなたが必要とするものです。溶接からレーザー切断、その他の関連技術に至るまで、業界で最高のサービスを提供しています。
RapidDirectは、卓越したプロフェッショナルな板金サービスを提供します。デザインファイルをアップロードするだけです。板金部品の製造に関する無料のDfM分析レポートを入手できます。そのうえ?競争力のある価格設定と迅速なリードタイムで高品質を保証します。
よくある質問
薄い金属に適した溶接はどれですか?TIG溶接は、薄い金属板の溶接に最適です。 TIG溶接プロセスは非常に正確であり、溶接の焦点を合わせる必要がある場所から逸脱することはありません。その結果、溶接部品は滑らかで繊細な仕上がりになります。
ACまたはDCを使用してアルミニウムをMIG溶接できますか?交流と直流の両方のMIG溶接がアルミニウムに適しています。ただし、MIG溶接の典型的な形式である直流溶接は、ACおよびDC仕様の機械を必要としないため、はるかに高速です。
溶接できる最も薄い板金は何ですか?非常に薄い金属を溶接するには、金属にかかる熱を最適に制御できる専門家が必要です。優れた熱制御により、MIG溶接で0.8mmの薄さの板金を溶接することが可能です。さらに、TIGを使用すると、0.6mm以下の厚さまたはそれ以下の厚さで溶接できます。
産業技術