スプレー溶接とは - プロセスとテクニック
スプレー溶接とは?
スプレー溶接は、溶射の形でのいくつかの溶接プロセスを指します。これは、粉末またはワイヤを圧縮ガスで高速で噴霧し、金属表面に噴霧する産業活動です。
スプレー溶接では、産業用プラズマ、火炎、デトネーション ガン、アーク スプレー、および高速酸素燃料を使用します。スパッタ溶接によって発生するかなりの熱のため、人と環境への害を避けるために、手順と規制に注意深く一貫して従う必要があります。
関連: 溶接とは?
スプレー溶接の仕組み
溶射とは、複数回のコーティング工程を表す総称です。溶接全体には、さまざまなエネルギー源によって溶融されるロッド、粉末、ワイヤなどのコーティング材料の使用が含まれます。
簡単に言えば、熱源と、高速で噴霧される液滴に溶けたコーティング材料からなる工業用コーティングプロセスとして定義できます。スプレーは、噴霧ジェットまたはガスによって基板に向かって推進されます。
溶射は非常に用途の広いプロセスであり、非常に効率的であることが知られています。これは、熱処理または窒化処理プロセス、クロム、ニッケルメッキ、陽極酸化などの方法を含む、いくつかの表面処理の優れた代替手段となります。
コーティングの厚さは、個人の好みによって異なります。コーティングは、摩耗したコンポーネントと基本的な機械部品を修復します。また、エレメントの性能と耐久性を向上させるために適用することもできます。適切に処理すれば、これは最大 70% 長く続く可能性があります。
関連: 溶射とは
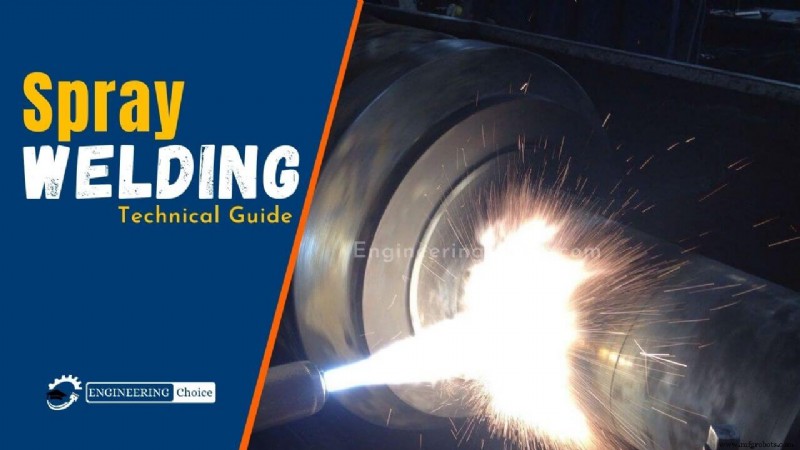
さまざまなタイプのスプレー溶接技術
1.スプレーアーク溶接
スプレー アーク溶接は、溶加材の直径よりも小さい直径の多数の小さな液滴の形で溶融材料を移送する方法の 1 つです。短絡がないため、アークが安定し、スパッタが発生しません。
スプレーアーク溶接を成功させるための前提条件は、電流と電圧の値が特定の制限を超えていることです。その結果、ショートアーク溶接よりも多くの熱がワークピースに供給され、5 mm 以上の厚さの材料のみがスプレー アーク溶接に適しています。
入熱量が多いため、溶融池も大きくなるため、溶接は水平位置で行う必要があります。純粋なスプレー アークは、CO2 をシールド ガスとして使用すると実現できないことに注意してください。
シールドガスは、できれば少量の CO2 (最大 25%) または O2 を含む純粋なアルゴンでなければなりません。スプレー アーク溶接は、シールド ガスが主にアルゴンであるアルミニウムとステンレス鋼の MIG 溶接に特に適しています。
スプレー アーク溶接は、太いフィラー ワイヤよりも細いフィラー ワイヤを使用して、より低い電流で正常に実行できます。
アーク電圧は、短絡のないアークを維持するのに十分な高さに設定する必要があります。通常、フィラー ワイヤーは正極に接続されます。
メリット
スプレーアーク溶接は非常に効率的なプロセスです。このプロセスの主な利点は次のとおりです。
- 高い入金率、
- 優れた融合と浸透
- 良好な溶接外観
- より大きな直径の電極ワイヤを使用する能力
- 飛び散りがほとんどない
制限事項
スプレー アーク溶接の制限は次のとおりです。
- 厚さ 1/8 インチ (3mm) 以上の素材 (ハンドヘルド) にのみ使用され、
- フラットおよび水平フィレット溶接位置に限定されます
- オープン ルート機能がないため、適切な調整が常に必要です。
2.溶射プロセス
フレーム溶射は、酸素/アセチレン燃焼溶射とも呼ばれ、約 100 年前に開発されたオリジナルの溶射技術です。これは、溶接トーチの基本原理に高速気流を加えて、溶融粒子を基材上に推進させます。
コーティング材料は、ワイヤまたは粉末のいずれかの形態にすることができます。火炎溶射コーティングは、多くの場合、塗布後に溶融して接着性とコーティング密度を向上させます。
利点
- 高い入金率
- 低表面加熱
- 万能
- プロセスはシンプルで使いやすい
デメリット
- 粘着力が比較的低い
- 暖房効率の向上
- 融点が 2,800°C を超える金属には対応していません
3.高速酸素燃料 (HVOF)
HVOF (High-Velocity Oxy-Fuel) プロセスは、酸素と、プロパン、プロピレン、または水素を含む選択された可燃性ガスのグループを燃焼させます。 HVOF システムは燃焼の基本原理を使用しますが、スプレーガンは標準の酸素燃料スプレーガンとは異なる設計になっています。
HVOF ガンの違いにより、火炎温度が高くなり、速度が速くなります。その結果、粉末がより完全に溶融し、コーティング材料の溶融粒子を「平らにする」ためにより多くの運動エネルギーが利用可能になります。 HVOF プロセスは、優れた接着強度とコーティング密度を生み出します。
HVOF プロセスは、タングステンカーバイドやクロムカーバイドなどの高融点金属および金属合金の堆積に最も一般的に使用されます。
利点
- 厚塗りにも対応
- 低空隙率
- 高い接着レベル
- 火炎溶射またはプラズマと比較して、より多くのカーバイドが保持されます
デメリット
- 騒音レベルが最大 130 dB の比較的大きな音
- 低い入金率
- 少し高い
4.プラズマ溶射プロセス (PTA)
プラズマ スプレー プロセス (非転送アーク) では、ガスの「プラズマ」状態を誘導する電極を通過して供給される不活性ガスが使用されます。ガスがガン装置のノズルから出て通常の状態に戻ると、膨大な量の熱が放出されます。
粉末コーティング材料がプラズマ「炎」に注入され、基板上に推進されます。
セラミックコーティングは、溶融温度が高いため、プラズマスプレーを使用して適用されることが最も多いです。 (多くの場合> 3500 F)。プラズマ スプレーを使用して、数種類のセラミック コーティングを施すことができます。
利点
- 簡単に適用
- サーメット粒子はサイズが大きい
- 耐摩耗性
- 気孔率が非常に低いかゼロ
- 厚いコーティング
- GTAW と比較して低い基板加熱
デメリット
- 溶射材料の高酸化
- 1mm 以下の薄層を得ることは難しい
5.爆破スプレー
デトネーション溶射は、材料の表面特性を変えるために、材料に超音速で保護コーティングを施すために使用される溶射技術の多くの形態の 1 つです。これは主に、コンポーネントの耐久性を向上させるためのものです。
1955 年に H.B. によって最初に発明されました。サージェント、R.M. Poorman、および H. Lamprey と特別に設計された起爆銃 (D ガン) を使用してコンポーネントに適用されます。溶射されるコンポーネントは、強力に結合されたデトネーション溶射コーティングを実現するために、すべての表面油、グリース、破片を除去し、表面を粗くすることによって、適切に準備する必要があります。
このプロセスには、他のすべての形式の溶射技術と比較して、コーティング材料の速度 (コーティング材料を推進する約 3500 m/s の衝撃波) と温度 (約 4000 °C) が最も高くなります。
これは、デトネーション スプレーが低多孔性 (1% 未満) および低酸素含有量 (0.1 ~ 0.5% の間) の保護コーティングを適用できることを意味し、低負荷下での腐食、摩耗、および付着から保護します。
このプロセスにより、耐摩耗性コーティングとして有用な非常に硬く緻密な表面コーティングを施すことができます。このため、デトネーション スプレーは、航空機エンジン、プラグおよびリング ゲージ、カッティング エッジ (スカイビング ナイフ)、管状ドリル、ローターおよびステーター ブレード、ガイド レール、または摩耗の激しいその他の金属材料の保護コーティングに一般的に使用されます。
通常、爆発溶射中にコンポーネントに溶射される材料は、金属、金属合金、およびサーメットの粉末です。およびそれらの酸化物 (アルミニウム、銅、鉄など)。
デトネーション スプレーは、正しく安全な環境で行わないと危険な産業プロセスです。そのため、この溶射技術を使用する際には、遵守しなければならない多くの安全上の注意事項があります。
6.コールド スプレー プロセス
コールド スプレー (CS) は、コーティングの堆積方法です。固体粉末 (直径 1 ~ 50 マイクロメートル) は、超音速ガス ジェットで最大約 1000 倍の速度まで加速されます。毎秒1200メートル。基板との衝突中に、粒子は塑性変形を起こし、表面に付着します。
均一な厚さを実現するために、スプレーノズルは基板に沿ってスキャンされます。金属、ポリマー、セラミック、複合材料、およびナノ結晶粉末は、コールド スプレーを使用して堆積できます。
ガスの膨張によって供給される粒子の運動エネルギーは、結合中に塑性変形エネルギーに変換されます。プラズマ溶射、アーク溶射、火炎溶射、高速酸素燃料 (HVOF) などの溶射技術とは異なり、粉末は溶射プロセス中に溶融しません。
スプレー溶接の利点
- スプレー溶接でスムーズな溶接
- 浸透性が高く、3/16 より厚い金属に適しています
- 溶着率が高く、生産性が向上します
- 飛沫がほとんどない
- 安価:安価な材料を使用し、スプレーで強化
- スプレー溶接は用途が広く、ほとんどの金属、セラミック、プラスチックを溶射できます
- さまざまな厚みに対応
- 処理速度が速い:スプレー時間は 3 ~ 60 ポンド/時 (使用する処理によって異なります)
スプレー溶接の欠点
- 溶射には溶接工の特別な訓練が必要
- アルゴン濃度が高いため、ガスのコストが高くなります (>85%)。
- フラット ポジションと水平フィレットにのみ推奨
- 高熱は溶接作業者を不快にさせる可能性があります
- 特に溶接の端でのアンダーカットの可能性
- コーティングは冶金学的ではなく、機械的に結合されています
- 見通しのプロセス
- 正確な負荷に対するコーティングの抵抗の低さ
よくある質問
スプレー溶接とは?スプレー溶接は、溶射の形でいくつかの溶接手順を分類するために使用される用語です。これは、粉末またはワイヤーを圧縮ガスで高速で金属表面に噴霧および噴霧する産業活動です。
スプレー アーク溶接とは?スプレー アーク溶接は、溶加材の直径よりも小さい直径の多数の小さな液滴の形で溶融材料を移送する方法の 1 つです。短絡がないため、アークが安定し、スパッタが発生しません。
スプレー アークを設定するにはどうすればよいですか?生産速度を上げるには、スプレー転写を使用します。 80% 以上のアルゴン混合物は、電圧を 23 ~ 4 ボルトに設定して開始します。アンペア数を約 300 ~ 400 インチのワイヤ送り速度に設定します。 150 アンペアに達するまで、ワイヤー送り速度を再び上げたり下げたりします。
どのくらいの厚さで溶射できますか?溶射は、電気メッキ、物理蒸着、化学蒸着などの他のコーティング プロセスと比較して、高い堆積速度で広い領域に厚いコーティング (およその厚さの範囲は、プロセスと原料に応じて 20 ミクロンから数 mm です) を提供できます。 .
製造プロセス