レーザー溶接:可能性は無限大
高性能産業用ロボットは、製造現場での生産性をさらに高めるために (従来の信頼性の高いロボット溶接プロセスよりも) 優れた精度と柔軟性を製造業者に提供します。さらに、かつて産業部門で溶接不可能と見なされていた材料は、現在では容易に製造され、廃棄物を削減しながら独自の製品を生み出すことが多い.
航空宇宙、自動車、および重機メーカー、リモート レーザー溶接 (RLW) – 非接触レーザー溶接技術 – は、さまざまな業界、特に大量生産において、より複雑な用途での利用が増加し始めています。従来のロボット溶接は依然として幅広いタスクに適した方法ですが、最高の精度と速度を必要とするアプリケーションには、リモート レーザー溶接ヘッドを装備した産業用ロボットが適しています。 RLW について学び始めたばかりであるか、ロボットの購入に近づいているかに関係なく、次の情報は意思決定プロセスに役立つ場合があります。
リモート レーザー溶接を使用する理由
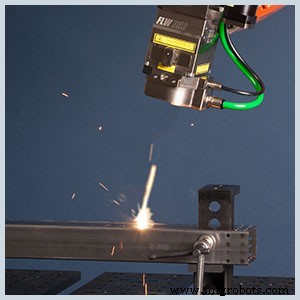
これにより、ロボットの精度が二次的な要因になり、メーカーは従来のSP165 や GP180 などの重いペイロード ロボットをヘッドの位置決めに使用します。 MC2000 II のような高精度ロボットではなく、このような従来型のロボットを使用する方が、多くの場合、安価であり、目標投資回収期間の短縮につながります。
同様に、リモート レーザー溶接ヘッドにはロボットの移動中にプログラムを動作させることができる特別なソフトウェア。これは一般に「オンザフライ」溶接として知られています。少数のアプリケーションでは「オンザフライ」構成が使用されていますが、Yaskawa は、ロボットの位置に基づいて出力を開始する機能を提供し、ロボットの動きとレーザー ヘッドの動きを毎回同じポイントで同期させます。
RLW は費用対効果が高いですか?
レーザー溶接は、依然としてレーザー、ヘッド、チラーに多額の設備投資を必要としますが、価格は下がり続けています。この種の初期設備投資を正当化するには、十分なボリュームを確保してコストを相殺することが重要です。大量生産が懸念される場合は、ロボット レーザー溶接の長所と短所について、評判の良いロボット サプライヤに相談することと、特定の用途に合わせてスポット ガンとタイマーを備えた溶接ロボットを設置することが有益な場合があります。同様に、ロボットによるレーザー溶接では通常、YAG レーザー (イットリウム、アルミニウム、ガーネット結晶の組み合わせ) が使用されますが、このレーザーは有害な光を発するため、遮光エンクロージャが必要です。これには追加の費用がかかり、大規模な場合は非現実的かもしれません
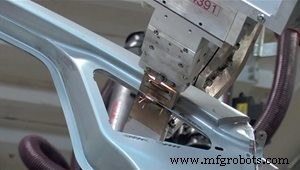
RLW はレーザー溶接の唯一の方法ですか?
リモート レーザー溶接ヘッドは、ビームを広範囲にすばやく移動できるという利点があり、特定の領域で複数の溶接を実行する際にロボットの動作を必要としない場合があります。ロボットは、パーツを静止した RLW ヘッドに提示することもでき、「レーザー オン」時間を高く保つ負荷を分担するのに役立ちます。 RLW ヘッドは、部品洗浄のためのアブレーションなど、溶接以外の用途でビームを操作するためにも使用できます。固定ヘッドをロボットの端に取り付けて、ロボットの動きを動かすことができます。ビーム。固定ヘッドでさえ、ビームを揺動または振動させてより広い溶接を行い、熱を分散させ、より多くの接合部の変動を処理し、蒸気のガス抜きを行うビーム操作を組み込む場合があります。ペイロードが小さいアーク溶接クラスのロボットは、小型部品用の小型で低コストのワークセルでウォブル ヘッドと組み合わせることができます。
他に考慮すべきことは?
材料前述のように、レーザー溶接は次世代材料の溶接への扉を開きつつあります。よく聞かれる材料の 1 つは、自動車に使用される新しい超高強度鋼と、それがレーザー溶接と抵抗スポット溶接のどちらに適しているかということです。強度の高い鋼の冶金学により、これは間違いなく良い候補であり、レーザー溶接の急速な加熱/冷却サイクルに対応できます (遅い抵抗加熱よりも優れています)。
製造のためのアルミニウムの使用トラックの軽量化や、自動車の電子バッテリー トレイなどの自動車部品の製造も急速に成長しています。その結果、後者へのレーザー溶接の使用が注目を集めています。レーザー溶接の低入熱、高い溶接速度、優れた柔軟性により、メーカーは自動車バッテリー部品の溶接プロセスに関する厳しい要件を満たすことができます。
メソッド
抵抗スポット溶接から摩擦攪拌溶接まで、ロボット レーザー溶接が特定のプロセスを置き換え、品質とスループットを向上させています。さまざまなロボット溶接アプリケーションで非常に注目されている特定の種類のレーザー溶接プロセスには、熱線およびハイブリッド レーザー溶接が含まれます。同様に、ワイヤと粉末によるクラッディングのレーザー溶接は、速度と低入熱により関心が高まっています。
ジョイント設計
ぴったりとはめ込まれた重ね継ぎは、レーザー溶接に最適です。表面間のわずかな隙間により、レーザー溶接がレーザー切断にすぐに変わる可能性があるため、レーザー溶接用治具は強力なクランプを使用します。レーザー溶接では、スポット溶接とは異なり、片面からアクセスするだけで済みますが、下部にはクランプ力に抵抗するためのサポートが必要です。
表面
溶接する製品の表面にも配慮が必要です。製品にレーザーを使用する場合、理想的には、クラス A の表面 (美的な形状と最適な表面品質を備えた自由曲面) を使用する必要があります。これは、小さな熱影響ゾーンが非常にきれいになるためです。このため、従来の抵抗スポット溶接 (RSW)、ガス メタル アーク溶接 (GMAW)、またはタングステン イナート ガス (TIG) 溶接に代わるレーザー溶接の使用は、ステンレス鋼が使用されている家電業界などの業界で拡大しています。
熟練したリソース
ロボットをプログラミングするときは、オペレータがロボットに教えるプロセスを理解することが重要です。アークまたは抵抗溶接の経験を持つ熟練したロボット オペレーターは、レーザー プロセスを完全には理解していない場合があります。このため、部品の完全性を維持しながらプロセスを最大限に活用するために、企業はレーザー溶接技術を理解するための人員の雇用またはトレーニングを検討する必要があります。ボルト、アンペア、ワイヤ供給速度は、潜在的に使用されるシールドガスと溶加材の違いは言うまでもなく、レーザーの出力と速度に置き換えられます。レーザーの安全性も、工場の担当者が責任を負う重要な要素です。
ジョイントの形状から部品のはめあいまで、ロボット レーザー溶接ではさまざまな側面を考慮する必要があります。ロボット レーザー溶接によって提供される堅牢な品質とスループットの向上が自社に適しているかどうか疑問に思っている場合は、希望するロボット サプライヤーに連絡して、特定のアプリケーションに関する質問への回答を求めることが賢明です。
産業用ロボット