Stratasys、チャンピオンモータースポーツがチームを組み、3Dプリントされたコアテクノロジーをテスト
6月27日、チャンピオンモータースポーツ(米国フロリダ州ポンパノビーチ)の911ポルシェGT2 RSクラブスポーツカーが、99回目のタイムアタック1部門で最初にフィニッシュしました。 米国コロラドスプリングズのパイクスピークインターナショナルヒルクライム
チームの成功の秘訣の1つは、車の空力構造でした。翼、足回りのストレーキ、ディフューザーなど、車の運転中に空気をより効率的に移動させるコンポーネントです。これらのコンポーネントの多くは、パートナーのStratasys(Rehovet、イスラエル、Eden Prairie、ミネソタ、米国)によって3D印刷されました。これには、新しいツールレスの炭素繊維で包まれたサンドイッチコアテクノロジーの最初のアプリケーションの成功も含まれます。
3Dプリントされたツールとコアテクノロジーの証明
チャンピオンモータースポーツは数年前からStratasysの顧客でしたが、「パートナーシップは通常のベンダーと顧客の関係以上のものになりました」とStratasysのシニア戦略アプリケーションエンジニアであるAllenKreemerは述べています。たとえば、StratasysとChampionは以前、Stratasysが3Dプリントの可溶性工具用に開発した新しい技術をテストするために協力していました。この技術により、ダクトやその他のチューブ状の部品用に成形された可溶性プラスチックコアが印刷され、炭素繊維プリプレグで包まれます。可溶性サポート除去タンクを使用すると、印刷された工具が溶解し、シームレスで完成した中空の複合ダクトが残ります。
「これは、Champion Motorsportとのパートナーシップの始まりでした。そこでは、CNC機械加工や成形のような境界のない、従来とは異なる方法でこの非常に複雑でシームレスな炭素繊維ダクトを作成するために協力しました」とシニアVPのPatrickCareyは述べています。 –アメリカ大陸、Stratasysの製品とソリューション。
2019年に、両社は同じテクノロジーの新しいイテレーションをテストするプロジェクトで提携することを決定しました。3D印刷され、炭素繊維で包まれたコアは ありません。 水に溶かします。これは、完成した部品またはプロトタイプの構造コアです。
Kreemerは、サンドイッチコンポーネントの場合、柔軟なアルミニウムハニカム、剛性のある構造用フォームなど、コアマテリアルの操作と成形は困難で費用がかかる可能性があり、成形または機械加工してから、専用の金型で炭素繊維複合スキンを使用して成形する必要があると説明しています。 Stratasysは、SABIC(サウジアラビア、リヤド)Ultem1010高温プラスチックを使用して剛性ハニカムコアを印刷します。 「私たちは車に合うように正確な形状を印刷し、型を使わずに炭素繊維で包み、バッグに入れて硬化させます」とKreemer氏は言います。 「私たちは、お客様が今でも使用している可溶性コアから始めましたが、今ではこれらのサンドイッチコアに移行しました。これは、航空宇宙および自動車で幅広い用途があります。」
「私たちはそれを「ツールレス」と呼んでいます。それが本当に重要です」とCarey氏は付け加えます。 「このアプリケーションを作成したのは、金型を作成してから金型に配置するプロセス全体をスキップするためです。」彼は、工具をなくすことで、必要に応じて形状を簡単に変更できると述べています。
3Dプリントされた受賞歴のある空気力学
チャンピオンモータースポーツプロジェクトでは、Stratasysがレース車両へのプロトタイピングまたは最終設置のために構築した合計16の空力部品に、3つの異なるテクノロジーが組み込まれたとCarey氏は説明します。 「Ultem1010 [カーボンファイバーラップ]コアを印刷し、カーボンファイバーを充填したナイロン12を使用して一部のパーツを3D印刷し、柔軟性と衝撃強度が必要な場合はナイロン6を使用してパーツを印刷しました。」
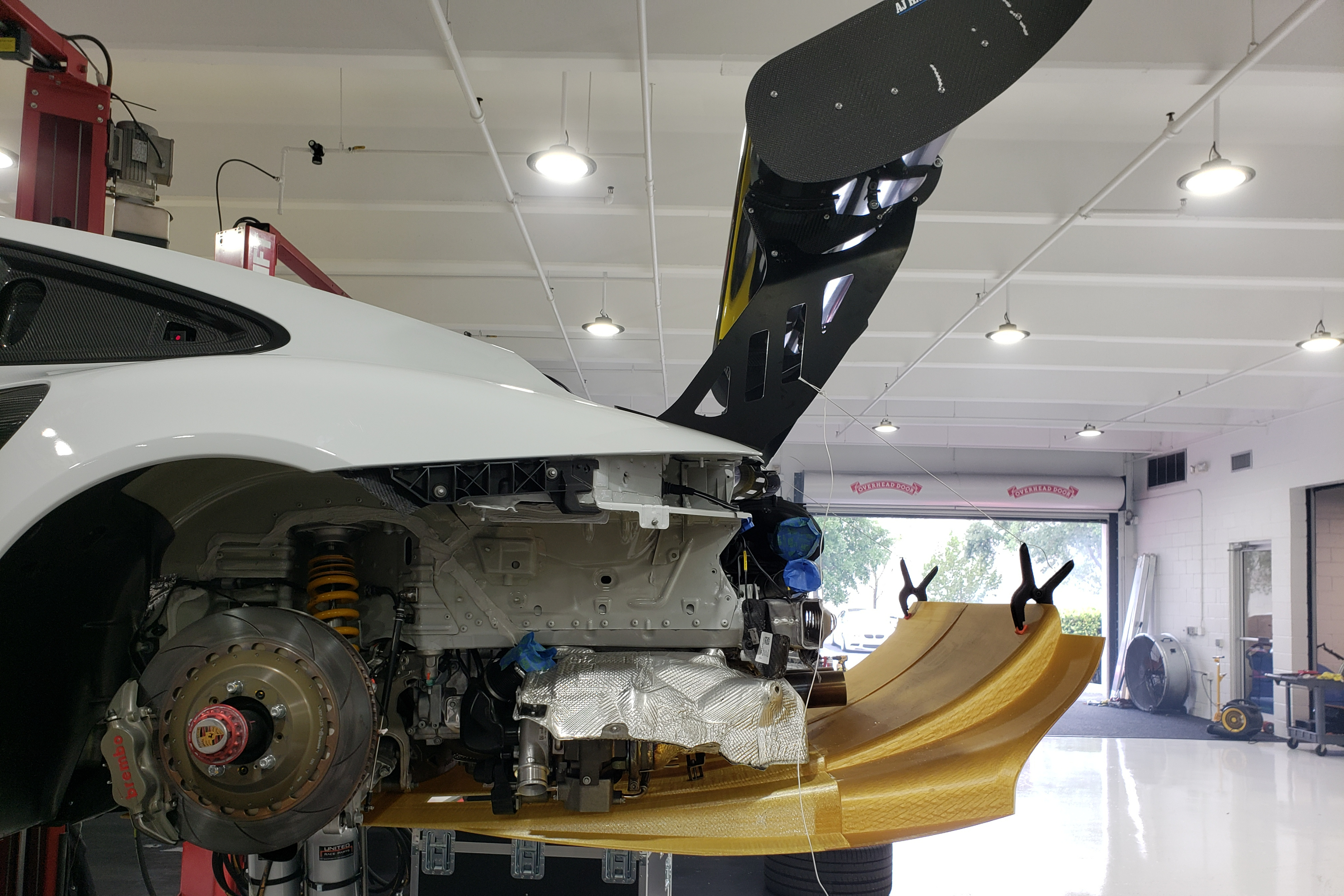
最大の部品は、最終部品の設計をテストするために構築された、長さ7フィート、幅5フィートのリアディフューザープロトタイプ部品でした。これは、Ultem 1010ポリエーテルイミド(PEI)ポリマーを使用して、F900溶融堆積モデリング(FDM)Stratasysプリンターで7枚に印刷され、結合され、炭素繊維プリプレグで包まれ、袋に入れられ、オーブンで硬化されました。パーツの所要時間は、印刷に約5日、レイアップと硬化に24時間強でした。「非常に高速で、当時必要だったものです」と、チャンピオンモータースポーツの機械エンジニアであるクリスリューは述べています。
>COVID-19により、今年の夏に対面式のイベントを開催できるかどうかの不確実性が原因で、「プロジェクトは土壇場でオンラインになり、同時に多くのシステムに対処する必要がありました」とLyew氏は説明します。 「空気力学はその1つであり、通常、コンポーネントの設計、テスト、反復のプロセスは非常に時間のかかるものです」と彼は言います。従来の方法では、金型の作成、金型へのハンドレイアップ、コアの切断と取り付けが必要でした。 「このプロセスがなければ、トラックで車をテストするための目標日を達成することはできませんでした」とリューは言います。
車のフロントスプリッターも同様の方法でプロトタイプを作成し、テストしました。プロトタイプであるパーツの場合、最終的な生産パーツは従来のツールで作成されましたが、プロトタイプパーツは、さまざまな反復をテストするためのパターンとして使用されました。 Carey氏は、次のように述べています。「ツールレスプロセスを使用すると、より高速に反復してテストし、次に高速に反復してテストすることができます。従来のツールでは、反復することはできません。ツールを作成するだけで、それを使い続けることができます。ここで、実際の部品を作成し、テストして、そこから学ぶことができます。」
いくつかの小さな生産部品もStratasysによって生産されました。たとえば、車のフロントバンパーの両側にあるウィングレットは、35%の炭素繊維を充填したナイロン12で印刷され、車両のサイドスカートも、ハニカム内部充填を備えたUltem 1010で印刷され、炭素繊維でオーバーラップされました。
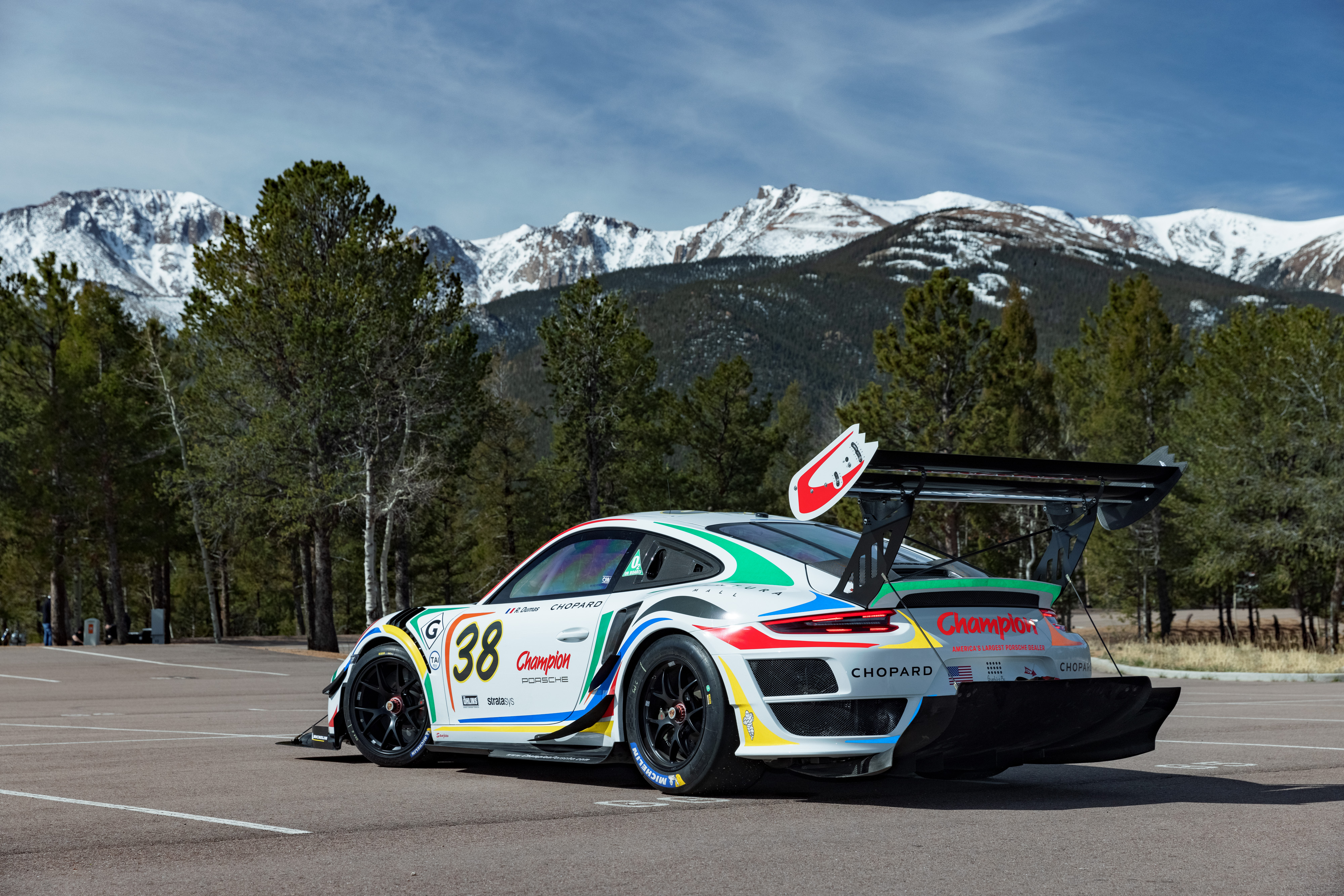
車の空力的な「ストライク」(車の周りの空気の流れを制御するのに役立つ戦略的なポイントで車の外側にボルトで固定される小さなフィンのような部分)の多くも、炭素繊維を充填したナイロン12または非強化ナイロン6のいずれかから印刷されました。部品は、損傷や摩耗により、必要に応じて簡単に再設計または交換できるように設計されています。 「パイクスピークには、損傷を引き起こす可能性のある起伏の多い地形がかなりあります。そのため、[ストレーキ]を簡単に交換できることが重要でした」とLyew氏は付け加えます。レース中に必要に応じて簡単に交換できるように、いくつかのスペアセットも印刷されて納品されました。
パイクスピークを超えて
パイクスピークは、最高地点で標高14,000フィートで開催されるこのイベントに特有の独特の環境のため、このテクノロジーをテストするための理想的なレースになりました、とKreemerは言います。 「すべてのレースカーはダウンフォースを使用して車をトラックに押し込み、トラクションを獲得しますが、パイクスピークのこれらの特定の車は、車をトラックに固定するために非常に誇張された空力効果が必要なため、世界の他のモータースポーツとは異なります。その高度で]。」その結果、他のタイプのレースカーで使用されるよりも大きな翼や他の空力コンポーネントが得られます。
今後、Stratasysは、同様の空力部品について、ツールレスのプリントコアテクノロジーを他のレーシング企業に導入する予定です。キャリー氏によると、将来的には、少量の自動車、レクリエーション用の船舶、さらには航空宇宙の内装部品にも、他にも多くの潜在的な用途があるとのことです。 「イテレーションやカスタムデザインが必要なアプリケーションであれば、そこに付加価値を付けることができると信じています」と彼は言います。
樹脂