オイルパッチのパーツ作りの新たな試み
フラッキングは、オイル パッチに大きな変化をもたらし、部品加工に大きな変化をもたらしました。
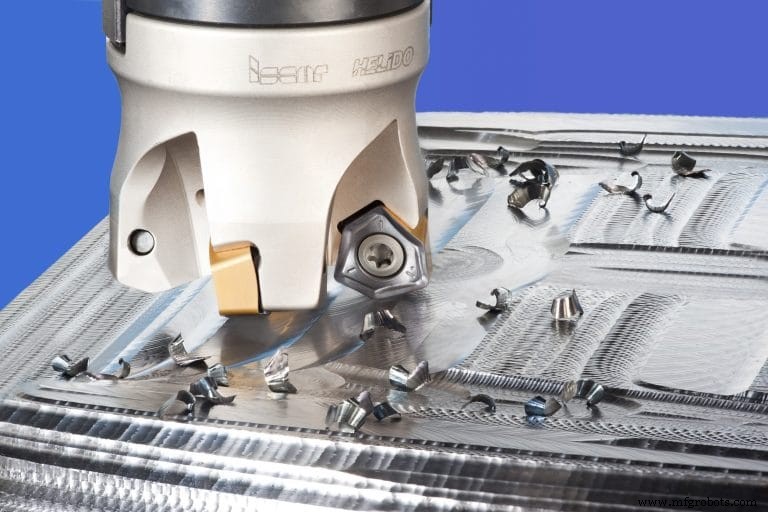
切削工具メーカー Iscar Metals の Rod Zimmerman は、フォート ワース郊外の快適な緑地帯に住んでいます。しかし、彼の家から 0.5 マイル (0.5 マイル) 以内に、ある石油会社が深さ 7,500 フィート (2,286 m) の垂直の穴を掘り、そこから 9 本の横線を広げ、それぞれ約 0.5 マイル (0.5 マイル) 進んだ.フラッキング液をこれらのラインに 9,000 psi で送り込み、天然ガスを抽出します。これは、フラッキング革命の遍在性と関連する驚くべきテクノロジーと同じくらい良い例です.
革命は文字通り「どこでも」ではないかもしれないが、別の切削工具メーカーである Allied Machine &Engineering のプロダクト マネージャーである Salvatore Deluca 氏は、彼の郡の巨大なフラッキング施設は「都市」と呼ばれていると語った。ダラス・フォートワースとは異なり、これらの「都市」は遠く離れたオハイオ州にあり、以前は石油で知られていなかった.ですから、オイル パッチの大きな変化が、オイル パッチの機械加工部品に大きな変化をもたらしたことは当然のことです。
フラッキングブロックへの取り組み
上記で触れたように、水圧破砕 (より一般的にフラッキングと呼ばれる) は、地中を掘削し、水、砂、化学物質の混合物を非常に高圧で岩石に注入することにより、頁岩層からガスと油を回収します。その圧力を生成するには、巨大なポンプが必要です。その重要なコンポーネントは、「フルイド エンド」または「フラッキング ブロック」と、そのバルブ、ピストン、およびライナーです。
これらのブロックを介してポンピングされるスラリーの高圧と研磨性により、急速な摩耗と亀裂が発生します。また、オハイオ州ドーバーにあるアライド マシンの製品スペシャリストであるポール ベスト氏によると、油田のオペレーターは高圧を維持する必要があるため、数日ごとにフルード エンドを交換する必要があります。最良の流体端は鋼の固体ブロックから機械加工され、一般に高さ約 3 フィート、幅 4 フィート、厚さ 2 ~ 3 フィート (0.61 ~ 0.91 m) です。複雑な輪郭、多数のチャネル、3 ~ 5 個の貫通穴 (それぞれ最大直径 8 インチ [203.2 mm])、および 3 ~ 5 個の交差する交差穴を備えたフルイド エンドには、膨大な量のフライス加工、ドリル加工、ねじ切り加工が必要です。 /P>
Iscar の West Zone 販売担当副社長である Zimmerman 氏は、フルード エンドは伝統的に 4000 シリーズの合金鋼で作られていると述べましたが、摩耗に対抗するために、ユーザーは「17-4 PH ステンレス鋼材料、スーパー デュプレックス ステンレス鋼などのよりエキゾチックな合金を試しています。そして15-5ステンレス。 Deluca は、彼が現在目にしているフルイド エンドの約半分は、硬化前のステンレス鋼の変種であり、その割合は増え続けていると推定しています。
ヒューストンにある Hartwig のエンジニアリング サービス (地域のオークマのディーラー) の Gayle Vollmer 氏は、フラッキング ブロックの最も摩耗しやすい部分に、より硬い材料を使用する動きもあり、より多くのコンポーネントを使用できるようにフラッキング ブロックを再設計する試みもあると述べました。簡単に交換できます。しかし彼は、大量生産に対する現在の需要により、そのような研究は「後回しにされている」と推測しました。
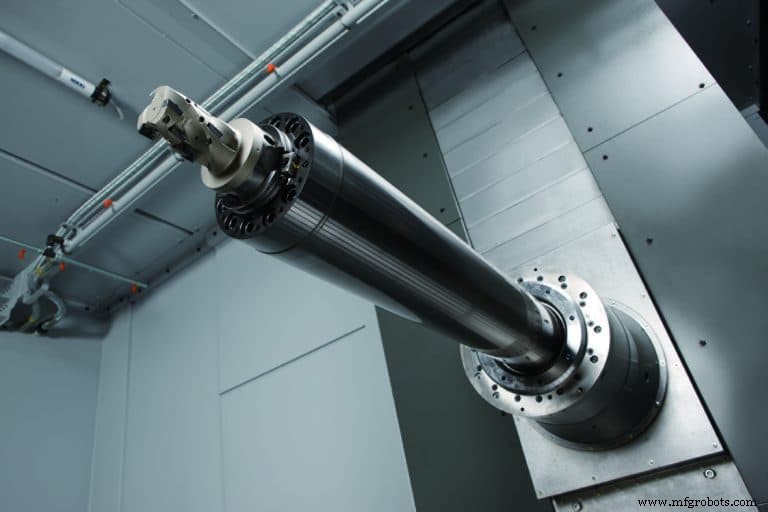
材質が 4340 鋼であろうと、より硬いステンレス鋼であろうと、フルイド エンドに取り組むには、実質的に大型のボーリング ミルまたは横型マシニング センターが必要です。イリノイ州アーリントンハイツにある JTEKT Toyoda Americas の地域セールス マネージャーである Jason Schooley 氏は、目標は 1 台の機械でできるだけ多くの操作を実行することであると述べました。>
Schooley 氏によると、ボーリング ミルは通常、さらに大きな部品用に大きなテーブルを備えていますが、Toyoda の FH1250SX のような水平型ミルはほぼ 4 倍高速です。これは、ギア駆動の 6,000 rpm スピンドル (オプションで 8,000 rpm または 15,000 rpm の高トルク スピンドル) と 1,654 ipm (42 m/分) の高速送り速度によるものです。この機械はミーハナイト鋳鉄ベース上に構築されており、剛性を最大限に高め、シリンダー ローラー ガイドを使用して速度を高めています。また、Y 軸と Z 軸のデュアル ボールねじ駆動により、重切削時の機械加工の安定性が向上しています。
FH1250SW には、深穴加工および中ぐり加工用の W 軸クイルもあります。近年、「多くの工作機械製造業者が組み込みの U 軸ヘッド」または W 軸を選択しており、これらはそれぞれ X 軸または Z 軸に平行に乗ります。これにより、固定旋削工具の回転中心を変更できます。これは、大きなボアやその他の大きな輪郭を切削する場合に便利な機能です。これは、液体の端に大きな穴があるだけでなく、穴が内部で「ボトルの形」になっていることが多いため、単純にドリルで穴を開けることができないためです。 U 軸が組み込まれていないマシンの場合、ユーザーは同じ機能を実行する「フィードアウト」ヘッドを追加できます。D'Andrea はそのようなサプライヤの 1 つです。
大きなヘッドを回転するスピンドルに取り付けることには、部品の干渉の可能性やスピンドルを介したクーラント供給との非互換性などの欠点があります。アフターマーケット オプションには専用の外付けドライブも必要であり、他のツール交換のようにリグを自動的に切り替えることができない場合があります。
しかし、スクーリー氏によると、マシンの Z 軸の移動距離が十分に長く、アドオン ヘッドがゲージ ラインを超えないようにすれば、フラック ブロック アプリケーションでは干渉は問題になりません。 1,850 mm の Z 軸移動量と、スピンドル ノーズからテーブル センターまでの 200 mm のデッド バンドを備えた 1250 マシンは、干渉することなくフラック ブロックに取り組みます。彼は、豊田がコンタリングヘッドの自動交換機能をさらに開発し、「石油のように不安定な業界でお客様が先を行くのを支援する」と付け加えました.
Schooley の経験では、Innovative Tooling Solutions などから入手可能なモジュラー ボーリング ツールには、標準機能としてスルー スピンドル クーラントが付属しており、フラック ブロックを製造する多くのショップは、コンタリング ヘッドを備えた専用の水平ボーリング ミルを使用してボアを仕上げています。また、Toyoda は、重負荷作業向けに 1,560 フィートポンドのトルクを備えたクイル スピンドル横型マシニング センターも提供しています。 Schooley 氏によると、4,000 rpm のクイル スピンドルは、中ぐりと深穴あけに必要なリーチと強度を兼ね備えており、以前は 2 回の作業が必要だったワークピースを 1 台の機械で完了することができます。マシンのロータリー 360,000 ポジション パレットは、さまざまなワークピースの重負荷加工に最大限の柔軟性を提供します。
Okuma America Inc. (ノースカロライナ州シャーロット) は、U ヘッドを使用せずに大型でバランスの取れていない部品の円形および角度のあるフィーチャを切削する際に、横型マシニング センターが旋盤を模倣できるようにする Turn-Cut と呼ばれるプログラミング オプションを開発しました。オークマのヒューストン テック センター コーディネーターである Ted Winkle 氏は次のように説明しています。また、U ヘッドが工具を回転軸の中心から外に移動する代わりに、Turn-Cut は X と Y でこれらの軸を補間しながら、Z で単一点の旋削工具を供給します。」
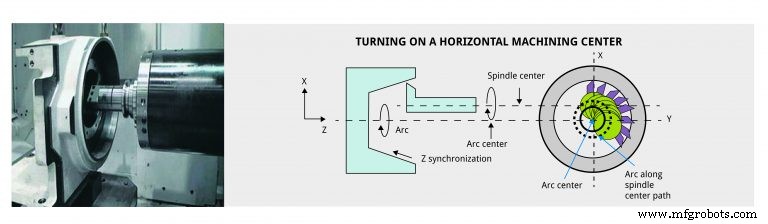
Winkle 氏は、Turn-Cut がフラッキング ブロックなどの部品の石油およびガス産業でより大きな役割を果たすと考えています。 U ヘッドとそれに関連するすべての高価なツールとは対照的に、ターンカット機能があることは利点です。」
一方、Turn-Cut は、特殊な加速、減速、および同期のための追加のソフトウェアと、ガラス スケールおよびボールねじ冷却が必要なため、安価ではありません。しかし、これらの機能を使用すると、さまざまなパーツの精度が向上し、1 回のセットアップでパーツを仕上げることができる可能性が高くなります。
Schooley は、この技術はボールねじとガイドウェイの同じ領域で多くの反復運動を必要とし (直径が小さいほど、これはより多く発生する)、これにより機械の寿命が短くなる可能性があると反論しました。
繰り返しになりますが、同じサイズのパーツでこの機能を頻繁に使用しない限り、同じ領域で過度の動きが発生することはないと Winkle 氏は言います。また、この機能を頻繁に必要としない場合、U 軸の多額の費用を正当化することはできないため、ターンカットはより論理的なオプションになります。工作機械の機能と同様に、トレードオフがあります。
馬力天国
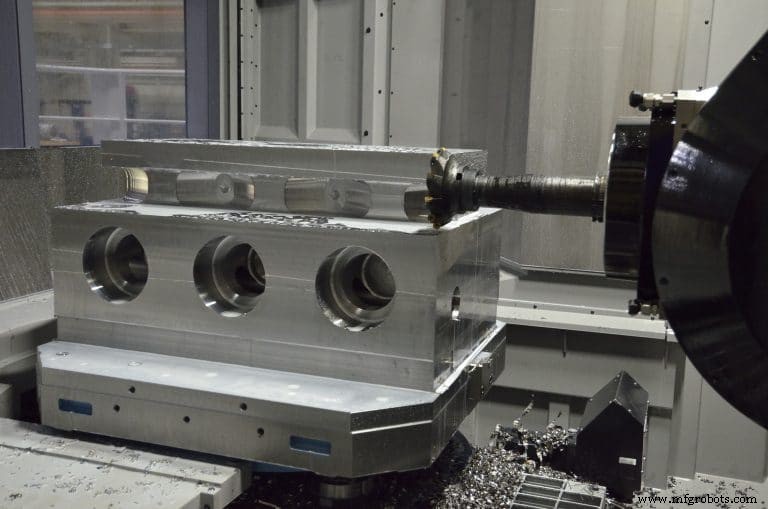
オハイオ州メーソンのマキノ社にとって、フラッキング ブロックなどの部品の「頼りになる」プラットフォームは、T1 および T2 5 軸横型マシニング センターです。プロダクト マーケティング マネージャーの David Ward 氏は、両方のマシンにダイレクト ドライブ スピンドルが搭載されており、「この業界で使用される困難なステンレス鋼や高合金鋼に最適です」と述べています。
T1 には、HSK100 12,000 rpm スピンドルがあり、143 馬力と 740 フィートポンドの定格トルクがあります。大型の T2 スピンドルは、ラジアル剛性のために HSK125 インターフェースを使用しています。 4,000 rpm の T2 スピンドルは、200 HP と 1,107 フィートポンドの負荷定格出力とトルクを提供します。
Ward 氏は、両方のスピンドルが 1,000 rpm まで最大トルク値を維持していると付け加えました。 「この時点まで最大トルク値を実行することで、スピンドルは、高温インサート コーティングなどの切削工具技術の新しい進歩を利用できるようになります。」
Winkle 氏は、オイル パッチが CAT 50 マシンによって支配されていることを観察しましたが、HSK および BIG Plus インターフェースによって提供されるフェース コンタクトは、「長いオーバーハングがある場合」に有利になることに同意しました。しかし、ほとんどの機械加工力は軸方向であるため、どちらのスピンドル タイプを選択しても大きな違いはありません。がっしりしている限り。 「ISO 40 スピンドル マシンでフラック ブロックにアプローチするのは無駄な作業です」と彼は言いました。
情報源は、高圧クーラントは、多くの石油およびガス用途での熱と切りくずの除去に不可欠であることに同意しました。フルイドエンドの穴の奥深くで作業する場合、切粉を洗い流すことが重要ですが、そうするのは困難です。クーラント供給フライス工具は、このような用途に最適です。」
そのため、マシンにこの機能が搭載されていない場合、ユーザーは ChipBLASTER などのサプライヤからのユニットを追加しています。 「スルーザスピンドルの高圧クーラントなしでは、今日フライス盤を購入することさえ考えません」とジマーマンは言いました。 「フライス加工と穴あけ加工の両方を一変させるものです。」唯一の例外は、クーラントを刃先に向けることができない状況です。その場合、クーラントは「時々あなたに逆らうので、インサートの熱亀裂を避けるために機械で乾かした方が良いです」と彼は言いました.
Deluca 氏によると、工作機械メーカーはこの需要に応えており、現在では、20 gpm で 1,000 psi を供給する OEM 供給のポンプを備えた機械をよく見かけるようになっています。 Ward 氏によると、Makino の T1 は 1,000 psi で 26 gpm を供給し、T2 はこれと同じ圧力を 53 gpm で供給します。
切削工具の進歩
フラッキング ブロック用に高馬力のモンスターが欲しいと思うかもしれませんが、Allied Machine の Deluca は、逆の課題にますます直面していると述べています。それは、スピンドル速度がより高いが、馬力が 40 で最大になるフライス加工に焦点を当てた機械で大きな穴をあける必要性です。 50まで。
「これらの部品を製造している会社は通常、小規模から中規模であり、通常、フラックブロックの製造に専念していません」と彼は言いました. 「そして多くの人々は、この市場に焦点を当て、ジェットコースターのように動く業界の機械に 50 万ドルを費やすことをためらっています。そのため、
従来の穴あけ製品よりもはるかに高速なスピンドル速度とはるかに低い送り速度で直径 4 インチの穴を切削できる工具を開発する必要がありました。」
フラッキングブロックを掘削する際の課題は、必要な穴のサイズを超えています。 「クロスホールは既存の穴に対して垂直にドリルで開けられるため、中断されたカットは流体エンドブロックの製造に固有のものです」とAllied Machine's Bestは述べています。 「交差する穴の結果として得られる形状のため、ドリルの外側のエッジは引き続き切削に関与しますが、内側のエッジは関与しません。これによりドリルが不安定になり、ツールが破壊され、フラッキング ブロックの完全性が損なわれる可能性があります。」
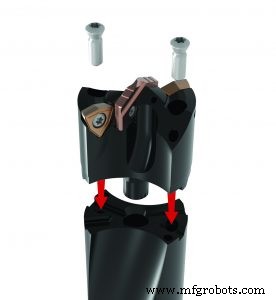
また、顧客が熱処理されていない材料を使用して節約している場合、ドリルは大きな変動に遭遇する可能性があります. Allied の Deluca は通常、これはオペレータがプロセスを常に監視しなければならないことを意味すると述べています。そうしないと、鋳物のポケットに衝突してから数秒以内に壊滅的なドリルの故障の危険にさらされ、何時間も費やした部品が壊れる可能性があります。ショップはまた、ブロックごとに材料の違いを経験しており、完璧なドリルと操作パラメータを選択することを困難にしています.
Allied は、APX と呼ばれる「次世代」ツールでこれらの課題に対応しました。より丈夫な超硬基板と独自のコーティングが特徴で、ポケットにぶつかったときの衝撃に耐えます。 「工具が欠けると、きしむ音がするかもしれません」とデルーカは言いました。「それでも、穴を仕上げることはできます。」
彼は、Allied が安定性を向上させるためにインサートにワイパーを追加し、パイロットが空のスペースまたはクロスホールに出たときに追加の安定性を提供するために摩耗パッドを追加することにより、クロスホール掘削の難しさに対処したと付け加えました。 「また、角度の付いた出口穴をあけるときは、送りを軽くして同じ速度を維持することをお勧めします。これにより、工具が押し出されたり移動したりしなくなります。通常、メイン ラインやクロス ホールをドリルで穴を開けるときは必要ありませんが、角度の付いた穴の極端な断続切削を補正するためにツールに投入できるエンジニアリングは限られています。」
Zimmerman 氏によると、フライス加工については、Iscar の HeliDo H600 両面 6 コーナ チップがこの種の被削材に非常に適しているとのことです。 「Mill 4 Feed も提供しています。これは、より少ない馬力でよりソフトに切削できるように、より積極的な形状を備えた正方形の片面インサートです。」
彼の主なメッセージは、Iscar は石油およびガス産業に長年取り組んできており、経験豊富な機械工のみを雇用しているため、顧客にとって最適なプロセスを開発し、さまざまなツールから選択できるということです。 「当社には多くのスタイルの飼料ミルがあり、剛性、馬力、トルクを考慮して、用途、材料、機械に基づいて飼料ミルを最適化できます。」
マルチタスクと自動化
9,500 ポンドのフラッキング ブロックを「自動化」と考える人はいないかもしれませんが、Makino と他のビルダーは、1 人のオペレーターが複数のマシンを実行できるようにするソリューションを提供しています。フラック ブロックの場合、これは通常、生の鋳造品と完成品を 1 分以内に切り替える回転パレット チェンジャーを意味します。その後、オペレーターは完成品を取り出すための十分な時間があります。
数分のサイクル時間で、フラッキング ガン チューブはスペクトルの反対側にあります。また、それらは「1 回限りの使用アイテム」であるため、Vollmer 氏は次のように述べています。毎日何千個も作られています。」
その結果、この部品は自動化に最適であり、Hartwig と Okuma は協力していくつかのオプションを提供しています。これらには、スイス式旋盤で小さな部品に使用されるようなロード/アンロードおよびバーフィード タイプのシステム用のロボットが含まれますが、ここでは 2 ~ 4 インチの直径を処理します。最速のアプローチは、素材をツイン スピンドル マシンに供給し、一方の端を機械加工してから、もう一方の端で作業するためにサブスピンドルに部品を直接送り込むことです。
Vollmer 氏によると、部品には旋削、ねじ切り、フライス加工が必要であり、後者にはライブ ツールを使用するのが理想的です。Winkle 氏は、この機能を「近年の業界における最大の変化の 1 つ」と呼んでいます。フラッキングと指向性掘削は、この移行の大きな理由です。
しかし、今日の「ダウンホール」操作で必要とされる大部分が円筒形の部品の多くにとって、理想的な旋盤は、ライブ ツーリングと 1 つまたは 2 つのタレット以上のものを備えています。オークマの MULTUS ミルターン シリーズと同様に、スイベル ヘッドと多軸フライス加工機能を備えています。
「掘削と完成段階の両方に必要な部品は、従来の垂直坑井よりもはるかに複雑です」と Winkle 氏は説明します。 「生産ゾーンを変更するには、バルブを開閉できなければなりません。パーツには油圧配管と電子監視装置が通っています。」
これには、外径と内径に交差穴と複雑なフライス加工が必要なため、機械には 5 軸の位置決めと、一方の端で部品を切断し、もう一方の端で作業するスピンドルを切り替えるための 9 軸程度の機械移動が必要です。
スレッドは別の課題です。 Winkle 氏によると、文字どおり何百もの種類があり、許容範囲は厳しいとのことです。その理由は、石油やガスでは、ねじ山が部品を一緒に保持するだけでなく、「ねじ山は完全に密閉し、穴の奥深くまで進む巨大な一連の部品からの膨大な引張応力に耐えなければならないからです」と Winkle 氏は述べています。 「そして、熱膨張と衝撃荷重に対処する必要があります。この密閉性と耐荷重性を備えたコンポーネントは、他の業界には存在しません。」
これらのねじを切断するには、剛性の高い機械とびびりに強いセットアップが必要です。イリノイ州ホイーリングにある SMW Autoblok のプロジェクト管理およびマーケティング担当ディレクターである Kyle Downs 氏は、「入ってくる資料は非常に一貫性がない」という事実によってすべてが複雑になっていると述べています。フック付き、曲がった、および/または長円形のパイプのセンタリングの自動化は、3+3 自動センタリングおよび補正チャック、または補正チャックとテールストックに取り付けられたセンタリング ソリューション (通常はチャックでもある) のいずれかの 2 つのシナリオで実現できます。 .」
最後に、金属除去装置にレーザー金属蒸着機能を追加すると、オークマの新しい LASER EX シリーズに例示されるように、新しい可能性が追加されます。たとえば、突き出た形状がわずかしかないパーツがある場合、大きなストックから形状を切り取るのではなく、それらの形状を本体に追加できます。これにより、加工時間が大幅に短縮される可能性があります。
ウィンクル氏は、たとえばインコネルとステンレス鋼を組み合わせて、異種材料を融合することもできると付け加えました。ジョイントは、ソリッドから機械加工された場合と同じか、より強力です」と彼は言いました.
これは、石油およびガスで、ドリル アセンブリに必要な摩耗パッドを追加したり、パイプが指向性井戸の曲がりを通過するときにパイプが井戸ケーシングの ID をこすらないようにするために使用されるサイド フィンを追加したりするための即時の可能性を秘めています。オークマは、同じレーザーを異なるアパーチャで使用して、最大約 50 ロックウェルまでの材料のゾーンを肌焼きする機能も提供しています。
自動制御システム