表面仕上げを改善するための5つの研削上の考慮事項
表面仕上げの改善は、操作パラメーター、ホイールドレッシング、グリットサイズ、クーラント供給、および機械の状態の1つ以上のポイントを調整することで実行できます。
精密CNC生産研削は、部品に厳しい幾何公差と高品質の表面仕上げが必要な場合に役立ちます。通常、32マイクロインチRaから4.0マイクロインチRaまでの範囲の表面仕上げは、達成する必要のある数値です。比較すると、従来のフライス盤または旋削加工では、約125マイクロインチから32マイクロインチのRaの仕上げが得られる可能性があります。
現在の表面仕上げを20マイクロインチRaから17マイクロインチRaに改善することが目標である場合は、ホイール速度を上げるか、送り速度をわずかに下げるだけで十分な場合があります。ただし、より細かい表面仕上げが必要な場合は、これらの5つの要素に対処する必要があります。
1)操作パラメータの粉砕
研削パラメータを調整することは、部品の表面仕上げを改善するための最も簡単で最速の解決策になります。これを成功させるための重要なパラメータと推奨されるアクションは次のとおりです。
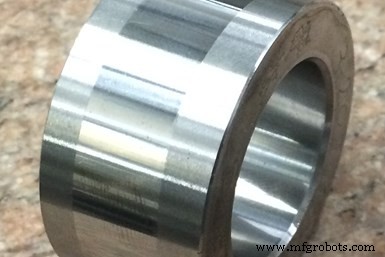
クリープフィード/表面研削:
- ホイール速度を上げます。 これは良い出発点です。ただし、ホイールが新しい速度で動作するように定格されていることを確認してください。最大動作速度(MOS)は、ホイールの側面に記載されています。
- 送り速度を下げます。
- 切り込みの深さを減らします。
- スパークアウトパスの数を増やします。
外径(OD)/内径(ID)研削:
- ホイール速度を上げます。前に述べたように、ホイールは新しい速度で動作するように定格が定められている必要があります。最大動作速度はホイールの側面に記載されています。
- 1回転あたりの切り込みの深さを減らします。
- 作業速度(rpm)を下げる:1回転あたりの深さを維持するために、送り速度を調整する必要がある場合があります。
- 滞留時間/スパークアウト時間を増やします。
- オシレーションを使用します(プランジID研削の一般的な方法)。
今日の多くの研削盤には可変速度コントローラーが搭載されているため、CNCプログラムを編集するか、スピンドル速度コントローラーを調整するだけで、ホイールの速度を変更できます。他のマシンでは、プーリーとベルトを手動で交換する必要がある場合があります。
送り速度を下げるには、CNCプログラムを編集するか、送り速度制御を調整することもできます。ただし、このアプローチではサイクルタイムが長くなる可能性があります。これは、特にサイクルタイムが重要な実稼働操作では、常に適切なオプションとは限りません。サイクルタイムが重要ではないアプリケーションでは、送り速度を下げることは、ワークピースの表面仕上げを改善するための良いオプションかもしれません。
ホイール速度を上げ、切込み量と送り速度を下げると、ホイールが鈍くなることがあります。これにより、ワークピースへの熱損傷の可能性が高まり、研削力が増加する可能性があります。したがって、これらのパラメータを調整するときは、プロセスに他の問題が発生しないように注意する必要があります。
2)砥石ドレッシング
従来の砥石と超砥粒砥石の両方のドレッシング条件を操作して、表面仕上げを改善することができます。これは通常、ドレスのトラバース速度を遅くしたり、ドレッシング中のパスあたりの深さを減らしたりすることで実現されます。ドレッシングの深さを減らすと、ドレッシングの動きが弱くなり、ホイールフェースが滑らかになります。これにより、通常、ワークピースの表面仕上げが向上します。ドレストラバース速度を下げると、ドレスリードが減ります。これは、ホイールが1回転するときにホイールが移動する距離です。ドレスリードは、ドレッシングツールがホイール面を横切るあらゆるドレッシングプロセスに適用できます。ただし、ドレスリードはプランジドレッシング操作には適用されません。リードを調整することは、既存のプロセスの表面仕上げを改善するための良い方法です。
新しいプロセスを開発したり、ドレッシングツールの種類を変更したりする場合は、ドレッシングのオーバーラップ率(ドレッサーの幅を考慮)を計算することをお勧めします。オーバーラップ率は、ドレッサーがホイールを横切って移動するときに、砥石面の任意の1点がドレッサー面に接触する回数です(表1)。
ドレッシングオーバーラップ率は、ホイール面の表面状態を決定します。これにより、ワークピースの表面粗さが決まります。オーバーラップ率が高くなると、ドレッサーはホイールの同じグリットに何度も当たって、ホイールの表面に細かい地形を作成します。これにより、ホイールフェースが鈍く閉じて、ワークピースの表面仕上げがより細かくなります。
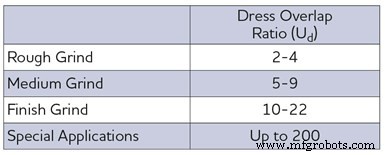
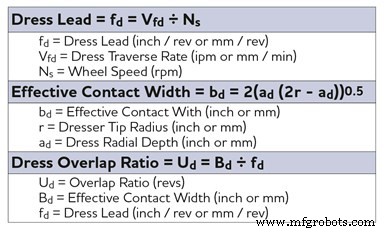
ただし、非常に細かいドレッシングを行った後、ホイールフェースが閉じすぎないように注意する必要があります。ホイールフェースを閉じると、ホイール表面が鈍くなり、ワークピースの熱損傷を引き起こす可能性があるため、研削力が高くなる可能性があります。表2に、リードとオーバーラップの比率を決定するための式を示します。
3)砥石構成:グリットサイズ
砥石のグリットサイズは、表面仕上げに直接影響します。グリットサイズが大きいほど、仕上がりは粗くなります。ワークピースの仕上げ要件に基づいて、正しいグリットサイズを選択することが重要です。表3に、グリットのタイプ、サイズ、およびさまざまな仕上げ要件の提案を示します。
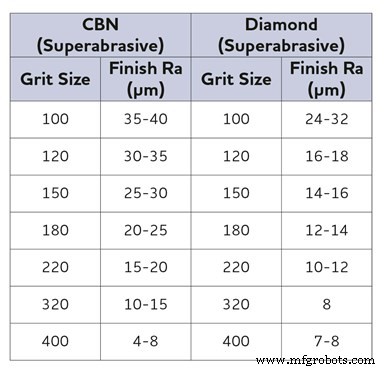
グリットサイズを変更する前に、攻撃性の低いパラメータを使用してホイールをドレスアップすることをお勧めします。グリットサイズを小さくすると、送り速度を下げる必要があり、その結果、サイクルタイムが長くなる可能性があります。グリットサイズが小さいと、グリットサイズが粗いほど高い除去率で材料を除去できません。また、小さいグリットサイズを使用すると、ワークピースに熱損傷が発生する可能性があります。
従来の砥粒の組成には、砥粒の種類とサイズ、砥石構造(結晶粒間隔)、グレード(ボンド硬度)、ボンドタイプがあります。超砥粒砥石の構成には、砥粒の種類とサイズ、砥粒濃度、接着グレードと種類が含まれます。従来の研磨剤には、酸化アルミニウム、炭化ケイ素、セラミック研磨剤が含まれます。超研磨剤には、ダイヤモンドと立方晶窒化ホウ素(cBN)が含まれます。
より小さなグリットサイズのホイールを注文する前に、アプリケーションに最適なホイール構成を見つけるために、砥石の製造業者/販売業者に連絡することをお勧めします。
4)クーラントの供給
クーラントの塗布が不十分な場合は、研削チップを研削ゾーンに再導入できます。切りくずは、ID研削でよく見られるワークピースの引っかき傷を引き起こす可能性があります。クーラントノズルが研削ゾーンに適切に向けられ、チップをその領域から洗い流すのに十分なクーラントの流れと圧力があることを確認することが重要です。研削ゾーン全体を正確にターゲットにすることは、パーツ全体で一貫した表面仕上げを実現するための鍵となる可能性があります。一部の高除去率プロセスでは、部品の焼損を防ぐために、ホイール速度に一致するようにクーラント圧力を調整する必要がある場合があります。これは、研削ゾーンから切りくずを取り除くのにも役立ちます。
場合によっては、切りくずが砥石に付着することもあります。これは、より積極的な研削や、砥石に付着する傾向のある特定の金属を研削するときに発生する可能性があります。これらのアプリケーションでは、スクラバーノズルを実装する必要がある場合があります。スクラバーノズルは通常、高圧(500〜1,000 psi)の低流量デバイスであり、ホイール構造から切りくずを除去するために研削ゾーンの後でターゲットにされます。
ただし、部品のボア内のスペースが限られているため、スクラバーノズルがID研削の答えになる可能性は低いです。このような場合は、フラッドクーラントを使用する必要があります。ただし、ODおよびクリープフィード/表面研削の場合、スクラバーノズルは、多くの場合、部品または固定具に干渉することなく実装できます。
クーラントのフィルタリングが不十分だと、表面仕上げに悪影響を及ぼしたり、成形品の表面に引っかき傷を付けたりする可能性もあります。粒子がろ過されない場合は、クーラントと一緒に粉砕ゾーンにポンプで戻すことができます。引っかき傷や仕上がり不良の原因としてフィルタリングが疑われる場合は、より小さなミクロンのフィルターを使用する必要があります。たとえば、超硬研削の一般的な経験則は、少なくともホイールのグリットサイズの10%を超える粒子をろ過するフィルターを使用することです(表4を参照)。
展開展開展開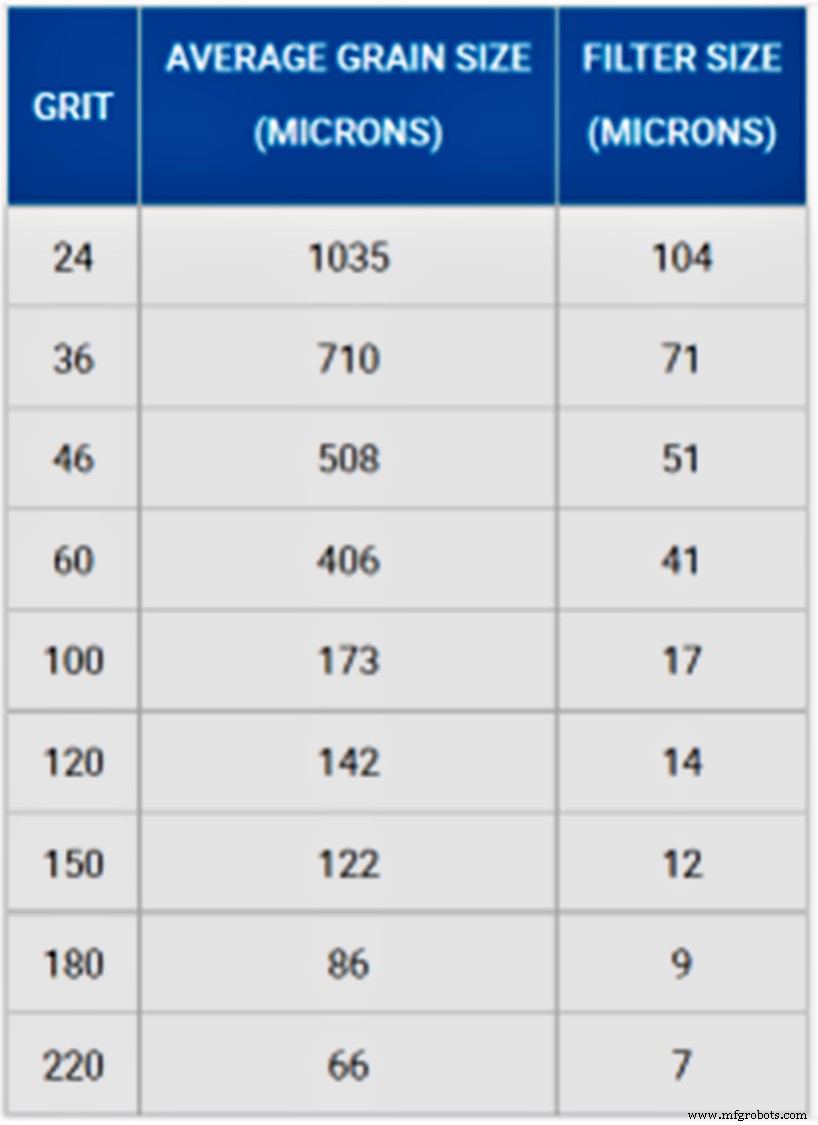
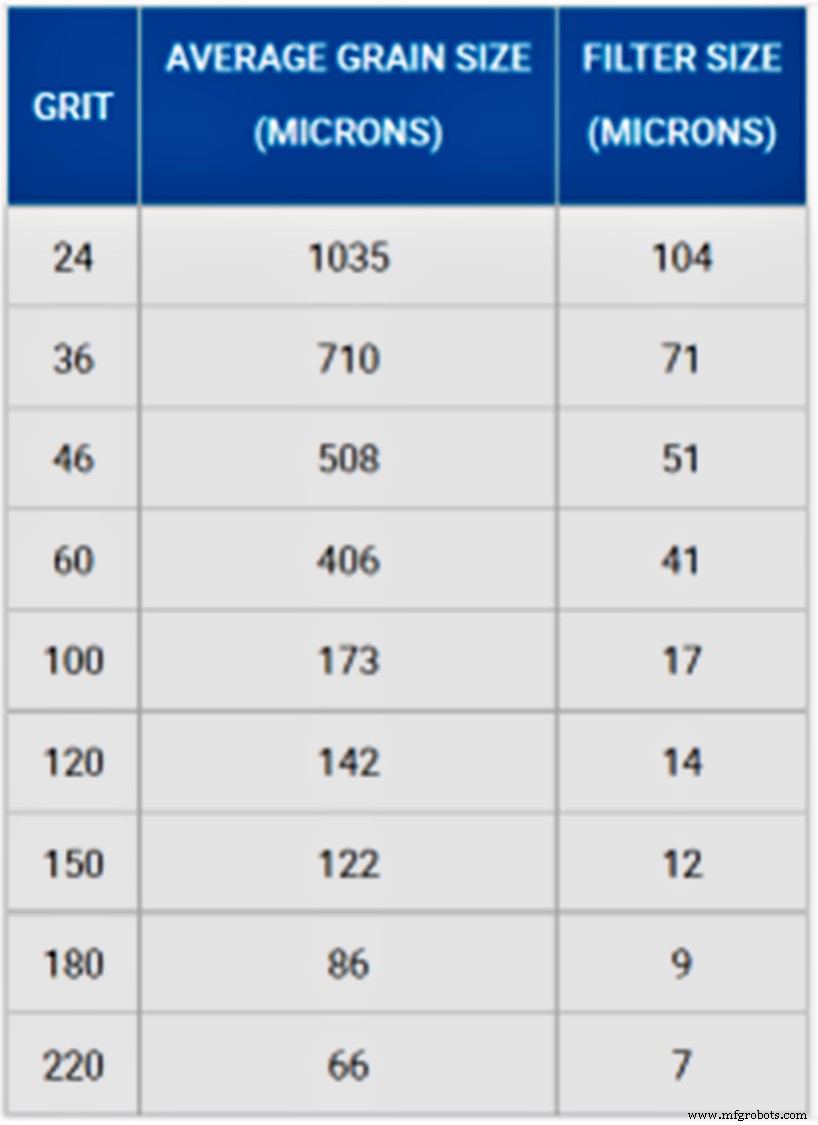
クーラントの種類も、通常、潤滑性がホイールの摩耗に影響を与えるため、表面仕上げに影響を与える可能性があります。ストレートオイルクーラントは通常、ホイールの摩耗を減らし、したがって、より一貫した表面仕上げを促進します。
5。機械の状態
研削盤に関連する要因は、ワークピースの表面仕上げに影響を与える可能性があります。これらには以下が含まれます:
ホイール/ハブアセンブリのバランス: 砥石アセンブリのバランスが許容レベルに達していない場合、びびりや表面仕上げの低下を引き起こす可能性があります。バランシングは、静的バランサー、動的/手動バランサー、またはマシンに取り付けられたオートバランサーなどの機器を使用して実行できます。必要なワークピースの精度と表面仕上げによって、使用する機器のタイプが決まります。
研削スピンドルに直接取り付けられたオートバランサーシステムは、最良のバランシングオプションです。このシステムは、ホイール/ハブの不均衡を打ち消すために、ハブ内でウェイトを自動的に移動します。オートバランサーは、クリープフィードやODタイプの機械などの大型の機械に限定されているため、小径のホイールには実用的ではありません。
バランシングの次善の方法は、すべてのタイプのマシンで使用できる動的/手動タイプのバランシングシステムです。ホイール/ハブアセンブリを機械上で直接バランス調整しますが、バランス調整ウェイトを手動で移動する必要があります。
最後に、マシン外で実行される静的バランシングには、達成できるバランシングレベルの点で制限があります。ただし、バランスをとらないよりはましであり、一部のアプリケーションでは正常に機能します。
とはいえ、すべてのホイールがバランスを取る必要があるわけではありません。質量の小さい一部の小さなホイールには、問題のある不均衡を生み出す重量がありません。したがって、これらの小さな車輪が非常に高速で動作している場合、または機械/システム(羽ペン)が硬くない場合を除いて、バランスを取る必要はありません。また、精度の低いアプリケーションや荒削りアプリケーションに使用されるホイールは、バランス調整を必要としない場合があります。
機械の剛性: 機械の剛性が低いと、ワークの品質が低下する可能性があります。時間の経過とともに、スピンドルベアリングが摩耗して緩む可能性があります。機械がクラッシュした場合、ベアリングも損傷する可能性があります。可能な場合は、振動解析装置を使用してスピンドルベアリングを定期的または継続的にチェックする必要があります。この装置は、ワークピースの品質を低下させる可能性のあるスピンドルベアリングの今後の問題を予測するのに役立つ優れたツールです。固定方法やクランプ方法が不十分だと、振動やたわみが発生し、最終的には表面仕上げが悪くなる可能性があります。
ドレッシングシステム: ホイールを正しくドレッシングすることは、良好な表面仕上げを達成するために重要であるため、ドレッシングシステムは良好な状態でなければなりません。固定工具は、損傷または摩耗している場合は交換する必要があります。研削スピンドルなどの回転工具は、過度の振動、振れ、および動きがないかチェックする必要があります。
工作機械のメンテナンス: スケジュールされた機械の潤滑、圧縮空気の品質の監視、フィルターの交換頻度などについては、工作機械のサプライヤーの指示に従うことが重要です。ホイールハブとアーバー、フィクスチャー、ステディレスト、テールストックセンターなどの損傷を検査する必要があります。これらの機械部品の検査は、ショップの毎日の予防保守ルーチンの一部である必要があります。
現在、多くの企業が定期的なメンテナンスに加えて、加速度計、温度計、圧力計などのセンサーによって機械を監視する状態ベースの監視(CBM)などの保守プログラムを実施しています。この予知保全は、センサーから収集されたデータを使用して、傾向を確立し、障害を予測し、ベアリングなどのコンポーネントをいつ変更する必要があるかを判断するのに役立ちます。
以前はノートンのブログで取り上げられました。
産業技術