積層造形から射出成形への移行
産業グレードの 3D プリンティングの精度と再現性により、アディティブ マニュファクチャリングは、機能プロトタイピングのための効果的で正確なプロセスとして確立されました。同時に、プラスチック射出成形は、数万個以上の大規模生産用の部品を製造するための、信頼性が高く、コスト効率と時間効率の高い方法として長い間使用されてきました。
その結果、エンジニア、デザイナー、および製品開発者は、これら 2 つのプロセスが製品のライフ サイクルにおいてうまく機能することを発見しました。最初は 3D プリント プロトタイピングによる設計リスクの軽減から始まり、射出成形による製造方法への移行です。ボリュームを上げてください。長年にわたる数百万の部品設計において、これは頼りになる組み合わせでした.
プロトラブズでは、航空宇宙、防衛、医療技術など、いくつかの業界で例が豊富にあります。
完全に機能する生産部品を構築できる 3D プリント プロセスがいくつかあることに注意してください。たとえば、直接金属レーザー焼結では、さまざまな金属を使用して最終用途部品を製造します。ナイロンベースの材料を使用した選択的レーザー焼結により、耐久性の高い最終部品を作成できます。 Multi Jet Fusion は、最終用途のナイロン部品の製造にも使用されています。
とはいえ、3D プリントのプロトタイプから最終部品の射出成形への移行は、主に言及したように、依然として頻繁に使用されるオプションです。なぜなら、成形はより多くの部品を生産するためのコスト効率と時間効率の高い方法だからです。
このオプションを選択するときは、留意すべき独自の設計上の考慮事項がいくつかあります。この投稿では、その変化を乗り切るためのアドバイスを提供しています:
- 部品を設計する前に部品を定義する
- 複数のプロトタイプの使用
- 成形による操縦
- 材料の選択
- コストとタイムラインの軽減
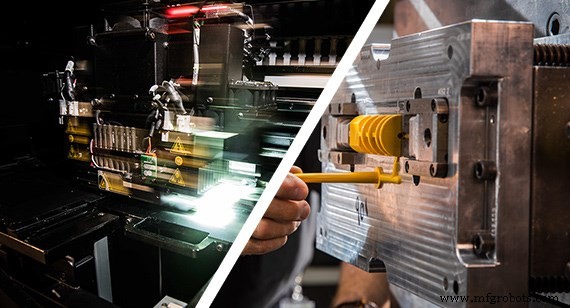
設計リスクの軽減:部品を設計する前に部品を定義する
3D プリントまたはアディティブ マニュファクチャリングによるプロトタイピングは、設計リスクの軽減がすべてです。部品の設計を改善する方法を検討します。部品の形状、適合性、および機能にどのような潜在的なリスクがあるかを調べます。さまざまなデザイン コンセプトを試して吟味する。部品の製造可能性を考慮せずに自分自身をコーナーに設計しないように注意してください。実際、3D プリントでは、パーツを作成する際に問題を引き起こす規則や制限はほとんどありません。しかし、成形可能な部品を設計する場合、それは別の話です。機能はあらゆる種類の部品の形状に影響を与えますが、特にプラスチック部品では、仕上げ、さらにはそれらを形作る金型の設計にも影響します.
そこで、当社の自動化されたデジタル見積もりプラットフォームの出番です。この分析は、部品が成形されることを念頭に置いている場合、または少なくとも試作段階を超えて多少大量に生産されることを念頭に置いている場合に特に重要です。 3D プリント パーツの場合は、材料、解像度、仕上げに基づいたインタラクティブな価格設定で即座に見積もりを取得できます。さらに、社内のアディティブ マニュファクチャリング エンジニアから設計に関するフィードバックをいつでも得ることができます。成形部品の場合、数時間以内にインタラクティブなオンライン見積もりに加えて、DFM 分析と、数量、仕上げ、およびリード タイムに基づくリアルタイムの価格設定を入手できます。
しかし、リスク軽減の例に戻りましょう。自動車業界では、SUV のエンジンのコンポーネントとして適合する部品設計は、高温多湿への暴露に耐えなければならない可能性があります。これにより、使用する材料や選択する製造方法などの重要な選択が促進されます。選択的レーザー焼結 (SLS)、機能的な生産部品を製造できる 3D 印刷プロセスの使用が必要になる場合や、成形部品または機械加工部品が必要になる場合があります。あるいは、医療技術会社が新しいハンドヘルド手術器具のプロトタイプを作成しているとしましょう。その場合、3D プリントされたプロトタイプは、診療所や診療所での販売デモンストレーションやユーティリティ テストで問題なく機能するツールになります。
この初期のフロントエンド段階での最善のアドバイスは、 定義 に役立つ適切で健全な設計原則を使用することです。 設計前のパーツ 一部。これは次のセクションにつながります:反復または複数のプロトタイプの役割.
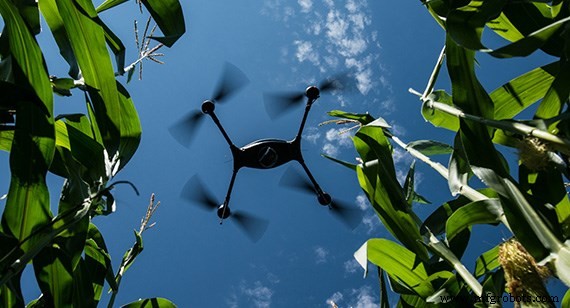
マルチプロトタイピングは生産方法の決定に役立ちます
前述のように、アディティブ マニュファクチャリングでパーツを作成する際の規則や制限はほとんどありません。それは祝福と呪いです。設計者が印刷されたプロトタイプのデザインを成形部品または別の製造方法に移行したい場合、これは特に困難です。なんで?成形の場合、厚い断面、オーバーハング、コアと編み物の周りを流れる流れ、複雑な形状、内部のチャネルまたはチャンバー、有機的な形状などは「嫌い」です。つまり、3D プリントできるからといって、成形できるとは限りません。
その結果、クロス クォーティング (複数のプロセスにまたがる、または複数のプロセスに対して引用する) と、反復的なプロトタイピングを組み合わせることで、パーツ設計の審査プロセスを行うことができます。これを並行して行うことで、部品が機能するかどうかを示し、次のステップ、つまり成形、鋳造、機械加工、板金などの大量生産を可能にする方法にうまく変換する方法を示すのに役立ちます。製作、または他のプロセス。この複数のプロトタイピングは、価格と時間に関する考慮事項を把握するのにも役立つでしょう。
射出成形の場合、金型を作成できなければ部品を作成できないため、成形できるものとできないものに関するより多くの制限が発生します。射出成形では、多くの成形技術と要素を使用または追加する必要があります (成形による操作に関する次のセクションを参照してください)。
このマルチクォート プロセスの航空宇宙業界の例は、ロッキード マーチンのクアッドコプター ドローンで発生しました (サイドバー ボックスを参照)。プロジェクト デザイナーであり、ロッキード マーチンのエンジニアであるミゲル ペレスは、プロトラブズの DFM 分析自動見積システムを使用して、さまざまな部品の反復をガイドし、最終的に 3D プリントによるプロトタイプ作成から、プロトタイプ作成と少量生産の両方に移行するように導きました。射出成形で。
彼は修正されていないモデルを見積もりシステムに提出し、たとえば、金型の半分がどのように機能するか、提案されたサイド プル、成形できなかった機能のハイライトなどについてフィードバックを得ました。次に、Perez はこの情報を使用して、3D プリントされたパーツを、設計意図を維持する複数の成形可能なインターフェース パーツにします。その後、彼は修正した部品を再提出し、見積もりシステムから金型の作成方法についてさらに多くのフィードバックを受け取り、たとえば、必要なドラフトを適切な方向に見落としている可能性があることを示しました。
医療業界の例としては、シリンジの端にねじ込んで取り付けるルアーロックなどの部品に 3D プリントが提供する検証テストがあります。コストを節約するためにこれらのロックを成形する特定の方法がありますが、最初に 3D プリントを使用して設計を検証し、成形に進むのに十分機能するかどうかを判断する前に、たとえば、シールを作成するのに十分なほど締まっていることを確認できます。
最終的に、設計中の部品によっては、複数のプロトタイプをテストして使用することで、何かが機能するかどうかを検証し、成形に移行する前にプロトタイプに自信を持つことができます。
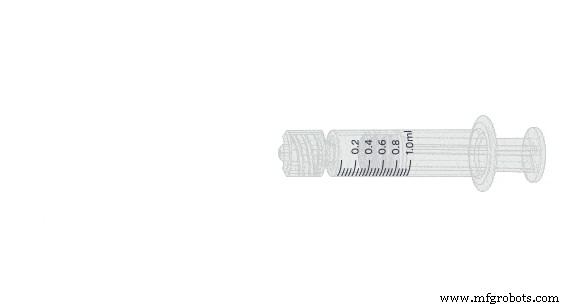
モールディングによる操縦
印刷されたプロトタイプから成形部品への移行を行うには、多くの成形設計方法を検討し、必要に応じて適用する必要があります。これらの手法の上位 2 つは均一な肉厚と抜き勾配ですが、他にもいくつかあります。簡単な要約は次のとおりです。
均一な肉厚。 均一な肉厚を維持することは、良好な成形部品を得るためにおそらく最も重要な設計要件です。均一な肉厚を持つことで、溶融プラスチックが金型に均一に充填されるため、反り、ヒケ、薄いニット ライン、またはその他の欠陥のある部品が作成されません。
下書き 成形品の垂直壁に抜き勾配または勾配を追加すると、金型からの成形品の取り出しまたは取り外しが容易になります。主な規則は、金型キャビティの深さ 1 インチあたり 1 度の抜き勾配を適用することです。
半径 丸みを付けたり角を丸くしたりして、金型へのプラスチックの流れを改善し、部品の完全性を向上させます。鋭い角はあなたの部分にストレスを与え、溶けたプラスチック (樹脂) の流れを妨げます。
リブ、マチ、ランプ リブと支持ガセットを含めると、構造部品の強度が向上し、反り、ヒケ、ボイドをなくすことができます。リブは、隣接する壁の厚さの 40 ~ 60% にする必要があります。鋭い階段ではなく傾斜をつけた方が、厚い壁部分と薄い壁部分の間の移動における応力を減らすことができます。
ボス。 ねじを受けるボスまたは取り付け機能の薄い壁を設計すると、ヒケとボイドがなくなります。
部品サイズや材料の推奨事項など、射出成形の設計ガイドラインの詳細については、プラスチック射出成形の設計ガイドラインを確認してください。これには、最大サイズの寸法、一般的に使用されるプラスチックと表面仕上げのリスト、カスタム カラー マッチングと二次仕上げオプションが含まれます。液体シリコーン ゴム (LSR) の設計ガイドライン。オーバーモールドおよびインサート成形のガイドライン。
射出成形の材料に関する考慮事項
プラスチック材料の 2 つの大きなカテゴリは、熱可塑性樹脂と熱硬化性樹脂 (LSR など) です。材料の選択は、さまざまな考慮事項に基づいています。材料の機械的、物理的、熱的、および電気的特性は重要です。冷却中の変形に対する抵抗力や、金型の小さな特徴をどれだけうまく満たすかなど、樹脂 (生の形のプラスチック材料) の特性など、製造可能性は不可欠です。部品の機能によっては、外観も重要な場合があります。材料費はまた別の問題です。 FDA または UL 評価の必要性など、その他の特別な考慮事項もある場合があります。
コストとタイムラインの軽減
確かに、タイムラインと期限とともに、全体的なコストと予算も重要な考慮事項です。また、場合によっては、特にコストが部品や製品開発の最大の影響力であると感じることがあります。しかし、成形などのより手頃な製造方法を使用することで、コストを抑えることができます。
これらの線に沿って、迫り来る締め切りもトップインフルエンサーのように感じるかもしれません.しかし、製品開発を加速できるデジタル マニュファクチャリング手法のおかげで、部品や製品の試作と生産を大幅に短縮できます。
Gus Breiland は、ミネソタ州にある Protolabs のシニア テクニカル エンジニアです。
Eric Utley は、ノースカロライナ州にある Protolabs のアプリケーション エンジニアです。
産業技術