油圧システムの溶接の種類
溶接 は、油圧シリンダーの修理からフレームやサポートの製造まで、油圧システムに関連して定期的に使用されます。アーク溶接、スティック溶接、固相溶接など、使用できる溶接プロセスも多種多様です。ただし、油圧修理および製造で最もよく使用される 4 つの特定の溶接プロセスがあります。MIG、TIG、スティック、および摩擦溶接です。それぞれに長所と短所があり、最適な状況もあります。
MIG 溶接
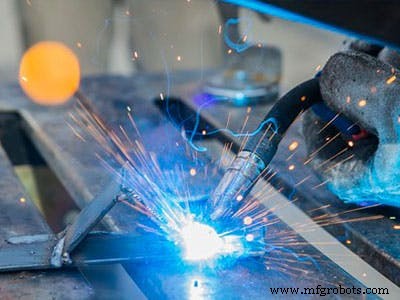
金属不活性ガス溶接の略である MIG 溶接は、サブディビジョン GMAW、またはガス金属アーク溶接です。アーク溶接では、電極と金属ワークピースの間に電気アークが発生します。そのアークは、ワークピースの金属を溶かすために必要な局所的な熱生成を提供します。
MIG 溶接の場合、電極は裸の金属ワイヤです。溶接ガンは消耗ワイヤ電極に継続的に供給し、アークを維持します。同時に金属アークをシールドガスで覆います。 MIG 溶接で使用されるシールド ガスは、不活性ガス (アルゴン) と活性ガス (二酸化炭素または酸素) の組み合わせです。このシールドガスと消耗品の裸線の組み合わせを使用することで、スラグは生成されません。
MIG 溶接にはいくつかの利点があり、それがなぜ一般的に使用されるのかを説明しています。これは、同じジョイントで複数の溶接パスを作成する機能をサポートし、溶接後のクリーンアップをほとんどまたはまったく行わないようにします。精度の高い使用が可能で、非常に薄いワークピースにも適しています。さらに、MIG 溶接のアーク時間は、金属ワイヤの連続供給を使用するため、他の多くの溶接プロセスよりも短くなります。実際、多くの溶接工は、これを最速の溶接方法の 1 つと考えています。厚い部品に頑丈な溶接を行う必要がある場合、MIG 溶接は優れたオプションです。
MIG 溶接には、検討する際に留意する必要がある欠点があります。溶接が適用される表面は、完全にきれいにする必要があります (錆、塗料、またはその他の汚染がない)。そうしないと、溶接が不十分になる危険があります。このプロセスは風に非常に敏感です。扇風機でさえ、シールド ガスを乱して溶接部を危険にさらす可能性があります。それに加えて、加圧されたガスのボトルを使用する必要があるため、現場での使用が難しく、携帯性もあまり高くありません.
TIG 溶接
TIG 溶接は、ガス タングステン アーク溶接 (GTAW) のカテゴリに分類され、タングステン イナート ガス溶接の略です。 MIG 溶接と同様に、電極とワークピースの間に電気アークを発生させて金属を溶かします。 TIG との違いは、電極材料としてタングステンを使用していることです。タングステンは融点が非常に高いため使用されます。
MIG 溶接と同様に、TIG 溶接でもシールド ガス (アルゴン、ヘリウム、またはその 2 つの混合ガス) を使用する必要があります。 TIG 溶接ではフィラー メタルを使用する必要はありませんが、フィラーを使用する場合は、別のワイヤーまたはロッドから溶接プールに追加されることに注意してください。
TIG 溶接の主な利点は、ほぼすべての金属と厚さのワークピースを接合できることです。これには、MIG 溶接では処理できない厚さが含まれます。 TIG溶接は、飛散がなく、溶接後の洗浄がほとんどまたはまったくない高品質の溶接を生成できます。鋳鉄および錬鉄の溶接は非常に困難ですが、TIG を使用する経験豊富な溶接工はそれを行うことができます。また、異種金属 (アルミニウムやステンレス鋼など) を接合することもできます。
鋼に使用する場合、TIG 溶接は棒溶接や MIG 溶接よりも時間がかかり、費用が高くなる可能性があります。このルールの唯一の例外は、薄肉セクションを使用して高品質の溶接を作成する場合です。また、同様の金属を溶接する場合でも、TIG 溶接では使用する電流、圧力、およびタイミングを慎重に制御する必要があります。
スティック溶接
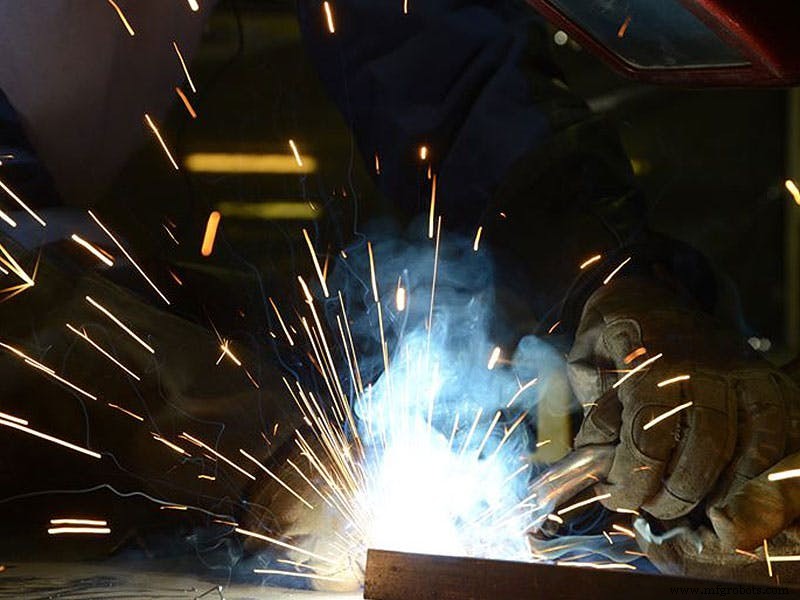
シールド メタル アーク溶接 (SMAW) としても知られるスティック溶接は、別のアーク溶接プロセスです。異なるのは、電極として消耗性のフィラー金属棒を使用していることです。溶接棒と呼ばれるこの棒は、フラックスとシールドの両方をサポートする材料でコーティングされています。溶接棒の裸の金属端は、絶縁ハンドル付きの電極ホルダー内に固定されます。電極ホルダー自体は電源に接続されています。
棒溶接で使用される装置は持ち運び可能で低コストであるため、現場での溶接作業に最適です。 MIG や TIG 溶接とは異なり、溶接点の塗装や腐食を除去する必要はありません。スティック溶接は、風や温度の影響を受けない十分な大きさのアークも生成します。スティック溶接は、屋内、屋外、風通しの良い場所、限られたスペースなど、使用できる場所に関しても非常に柔軟です。これにより、現場での修理に最適です。
棒溶接の主な欠点は、消耗棒を使用することにあります。プロセス中にロッドを交換する必要があるため、スティック溶接に時間がかかる場合があります。溶接プロセス中に電極の長さが変化するため、ロッドの抵抗も変化します。これは、特に新しいスティックを使用する場合に、過熱や早期溶融につながる可能性のある電流の変動につながります.
また、関係する熱により、金属の薄さにも限界があります (通常は 18 ゲージより薄くなりません)。最後に、スラグとスプラッターの生成は、塗装またはさらに溶接する前に溶接面をきれいにする必要があることを意味します.
摩擦圧接
摩擦溶接 (FRW) は、MIG、TIG、スティック溶接とは異なり、固体溶接プロセスです。固相溶接プロセスでは、溶融を伴わずに 2 つの母材間に冶金学的結合が作成されます。特に摩擦圧接は、摩擦熱と圧力を組み合わせて結合を実現します。
ほとんどの場合、1 つのパーツを別のパーツに対して相対的に回転させながら、高い軸力でパーツを接触させます。このような大きな力の下での相対運動は、摩擦につながります。この摩擦により、2 つの表面間に強力な金属結合を形成するのに十分な熱が発生します。
回転摩擦圧接を使用する場合、ワークピースの選択は制限されます。少なくとも 1 つのワークピースは、チューブやパイプなどの円筒形でなければなりません。一方、線形摩擦溶接では、回転運動ではなく往復運動を使用して、必要な摩擦と熱を生成します。直線運動を使用すると、少なくとも 1 つのワークピースが円筒形である必要がなくなります。
摩擦溶接は、TIG、MIG、または溶接シームへの接触を制限するスティック溶接とは異なり、完全な界面接触を実現できます。摩擦圧接は、異種金属の溶接も容易にします。また、フラックス、シールド、フィラー メタルも必要なく、正しく行われると、気孔のないしっかりした溶接が生成されます。
摩擦圧接の欠点の 1 つは、2 つの部品が接合された場所で避けられないばり材料が発生することです。最終アセンブリからトリムするには、旋削操作を使用する必要があります。ばりの存在は、ワークピースの元の長さの一部が失われることも意味します。この損失は、設計プロセスの早い段階で簡単に見積もって説明することができます。
さらに、摩擦圧接による高品質の溶接には、旋盤に似た大型で強力な設備が必要です。このため、摩擦溶接の機器は、MIG、TIG、スティック溶接のように携帯できません。
一般的な溶接の問題
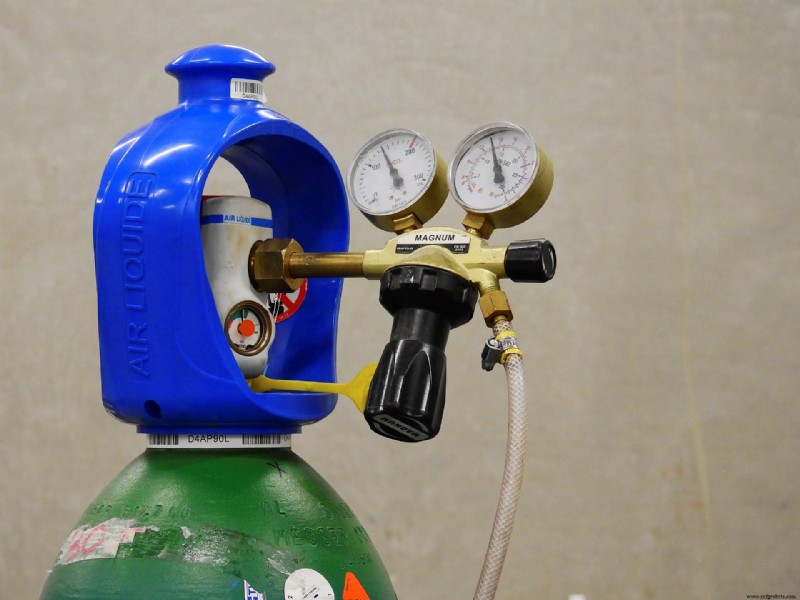
油圧コンポーネントと機器は高圧で動作するため、しっかりとした溶接が重要になります。溶接が正しく行われていない場合、非常に危険な場合があります。このコンテキストで考慮すべき 2 つの点は、溶接欠陥、歪み、および残留応力です。
溶接欠陥には次のようなものがあります:
- 不完全な融合
- 虫歯
- クラック
- 貫通力の欠如 (融合が関節の根元に達していない)
- 融合の欠如 (関節断面全体で融合が達成されていない場合)
- 介在物 (非金属粒子が溶接部に閉じ込められている場所)
- 過剰な飛び散り
- 溶接プロファイルが悪い
これらの欠陥のない溶接を実現するには、トレーニングと経験が必要であり、結果は溶接工が使用するプロセスに大きく依存します。
溶接におけるもう 1 つの大きな懸念事項は、2 つの異なる金属を接合することです。 MIG、TIG、またはスティック溶接を使用する場合は、相対的な熱伝導率と膨張を考慮して、冷却時の歪みと残留応力を回避する必要があります。たとえば、溶接アセンブリ全体に収縮が発生する可能性があります。これは、突き合わせ溶接 (エンドツーエンドの溶接) で特に一般的です。この収縮は冷却時に発生し、反りや残留応力につながる可能性があります。実際、局所的な熱の問題と溶接部品の形状により、同様の金属が使用されている場合でも発生する可能性があります.
プロの溶接工は、残留応力と歪みの可能性を最小限に抑えるためにどのような対策を講じるべきかを知っています。熱を逃がすためのヒートシンクの使用、溶接プロセス中の部品の動きを再調整するための溶接治具、残留応力を最小限に抑えて歪みを除去するための応力除去熱処理など、さまざまなアプローチがあります。
認定された溶接工は、溶接欠陥のない強力な溶接を実現するために、適切な溶接プロセス パラメータ (速度、電流、溶加材の量、シールド ガスなど) を選択するための知識と経験を持っています。
結論
油圧アプリケーションが MIG、TIG、スティック、または摩擦溶接を必要とするかどうかにかかわらず、実際の溶接プロセスは多くの場合、専門家に任せるのが最善です。溶接には、使用する金属とその厚さだけでなく、多くの変数が関係しています。欠陥のない強力な溶接、または 2 つの異種金属間の効果的な溶接を実現するには、認定された経験豊富な油圧機器の溶接工が必要です。
MAC 油圧
MAC Hydraulics では、認定された溶接工が自分の仕事に大きな誇りを持っています。彼らは溶接領域を準備して溶接を実行するだけでなく、プロジェクトに最も適したプロセスを選択し、複数の非破壊検査方法を通じて溶接の完全性を検証します。 MAC Hydraulics の経験豊富な溶接工は、ステンレス鋼、炭素鋼、さらには鋳鉄を扱うことができ、最も困難で複雑な製造と修理を行うことができます。 今すぐお問い合わせください 当社の溶接サービスの詳細をご覧ください!
機器のメンテナンスと修理